MRP systems for manufacturers: the ultimate guide
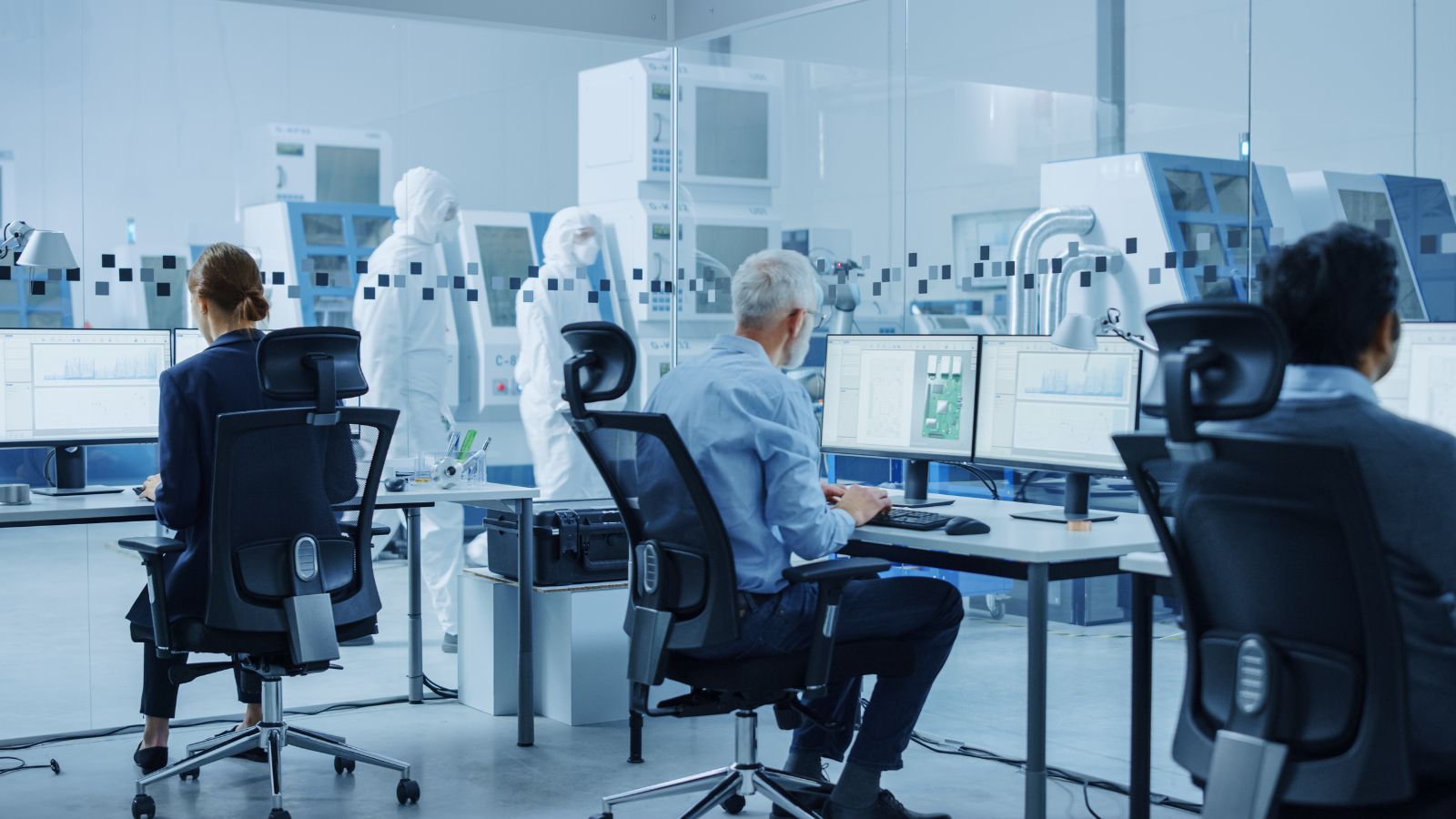
A common denominator for most businesses is aiming for growth.
As soon as the business is sustainable, the next plan is to increase sales, expand to new markets, or add new products to the range. But as your business grows, so does the challenge of keeping up with customer demand. You need to find ways to streamline processes and make your operation more efficient in order to meet the needs of a larger customer base.
Your sales are increasing, but so is your workload.
Times are great, but with sales and manufacturing orders piling up, you realize that manually tracking your inventory, production, and sales will not cut it anymore. It’s probably a good time to check out how you can leverage software to streamline your processes and keep up with the demand. That’s why we’ve put together this epic guide on what is an MRP system, which is the best software for you, and how to choose between MRP and ERP systems.
What is an MRP system?
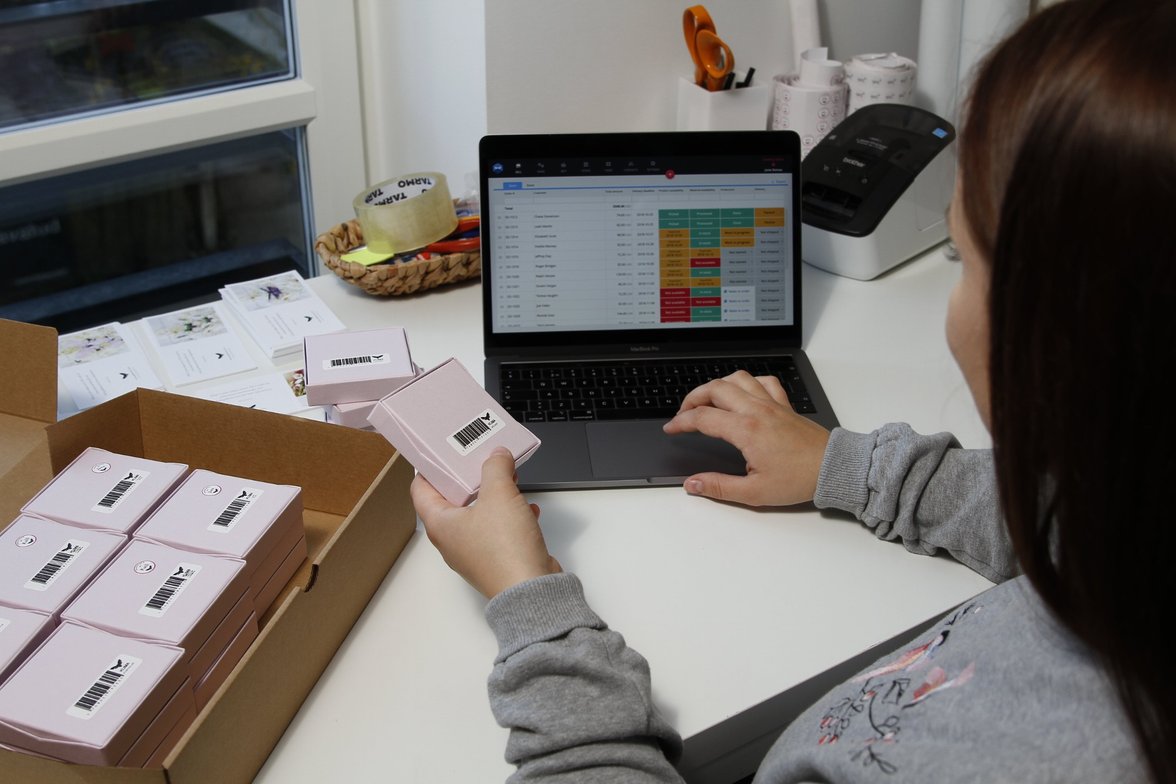
MRP, or material requirements planning systems, are tools for calculating the raw materials, sub-assemblies, and components a manufacturer needs to create a product.
MRP systems perform this task following three steps:
- Monitoring the current level of raw materials and components on hand
- Understanding which inventory is low and needs reordering
- Scheduling the production or purchasing of those materials
When it comes to answering the question of what MRP software is and how it works, that’s it in a nutshell. However, although it appears to be this way, MRP systems aren’t considered lean production and are considered by many practitioners to be antithetical. But that doesn’t mean they don’t go hand-in-hand!
So that’s the general definition of an MRP, but what does it mean in manufacturing?
What is MRP in manufacturing?
An MRP system for manufacturers is a piece of software used to automate production, scheduling, and inventory.
Though this definition, especially for MRP systems in manufacturing, has changed over time since there have been big strides in technological advancements in this area. Traditionally, MRP systems used to be considered a pull production system. However, as the software and technology improved, capable MRP systems became able to support all types of production workflows:
- Make-to-order (MTO)
- Make-to-stock (MTS)
- Assemble-to-order (ATO)
That means the MRP systems of today allow growing manufacturers to be flexible with their production lines and change their production speed depending on the different challenges they encounter.
So, we’ve already touched upon this a little bit. But how exactly does an MRP system work in manufacturing?
How does MRP work?
The way earlier MRP system iterations automate these areas and meet demand efficiently is by following the bill of materials (BOMs) of a manufacturers product, which details:
- The raw materials, subassemblies, and components used
- The quantity of these items
- Total costs
- Operational steps
The BOMs will highlight the relationship of the items that go into making your product as either parent or child. As the parent item, the finished goods are at the top of the hierarchy.
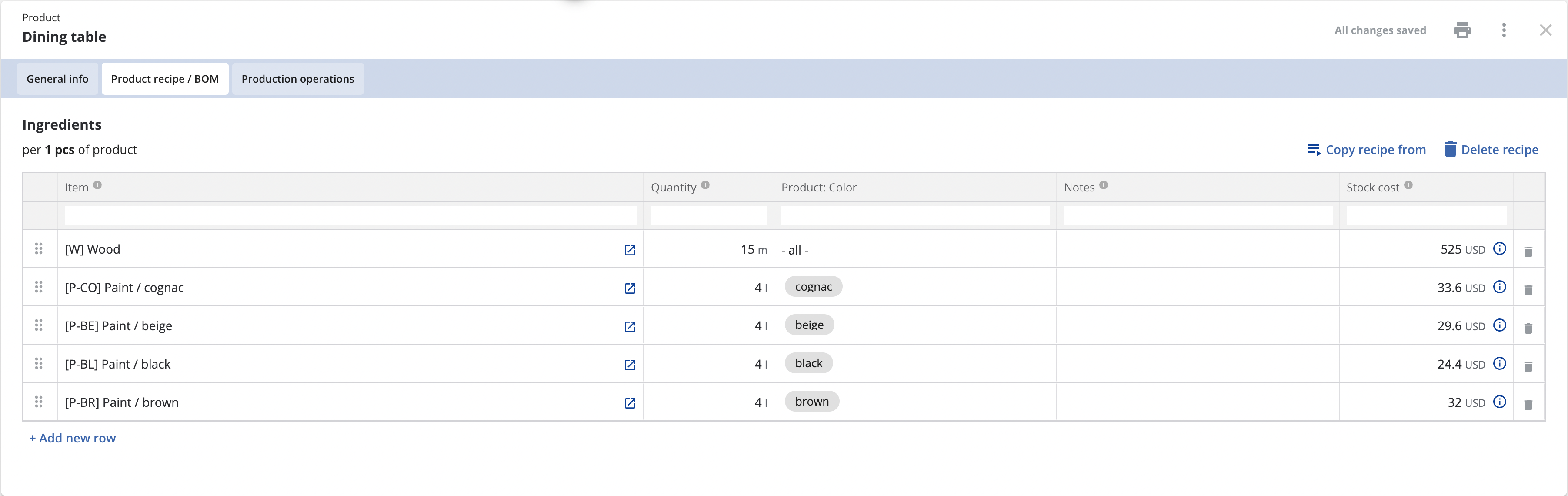
But, the MRPs of today use inventory data and your master production schedule (MPS) to automatically calculate how much material you need and how much your manufacturing process will use. However, back to inventory types, as the inventory items within your BOM are classified as one of two things:
Dependent demand
These are the items you need to make your finished goods — the raw materials and the components. The demand for these items will depend on how much is needed to make the next-level component in the BOM hierarchy.
Independent demand
This is essentially your finished goods, as the amount you need is all determined by several factors such as:
- Market demand
- Sales history
- Forecasted demand
To help manufacturers track and manage all these dependencies and figure out how many items are needed by the specific dates within the master production schedule, most turn to MRP systems to achieve this task.
Another element of understanding what an MRP system is is how they track lead time. There are two common types of lead time manufacturers concern themselves with, and that’s:
- Material lead time — The ordering and delivery time of materials
- Manufacturing lead time — The time it takes to make finished goods and ship them to the customer
Material requirements planning systems automatically estimate these lead times for you by using the information provided with your BOM and MPS.
What Are MRP I and MRP II Systems?
Let’s cut straight to the chase. Everything we’ve mentioned above is MRP I, but let’s break down the different MRP systems further.
What is an MRP I system?
MRP I (or Material Requirements Planning) is a tool for using different inputs, like:
- Material costs
- Material availability
- Expected demand
- Forecasted demand
- Staffing ability
- Machinery capacity
And using the data to calculate if you have adequate material, labor, and machinery levels to meet market demand or reach company production goals.
MRP I System Features:
- Inventory control
- Bill of materials (BOM)
- Master production scheduling (MPS)
But as the technology improved, the functions of an MRP system increased, leading the way to a robust system dubbed an MRP II system.
MRP and ERP systems come from the same software family but perform different functions.
What Is an MRP II System?
An MRP II system, unlike its predecessor, stands for Manufacturing Resource Planning as this improved system includes the original functions of MRP I, but integrates other business applications too, including:
- Advanced demand forecasting
- Machinery capacity scheduling
- Quality assurance
- General accounting
The MRP II system quickly replaced the MRP I system as it provides the same features but also incorporates real-time functionalities, giving you a tool to centralize your logistics, marketing, and financing.
MRP II system features include:
- Inventory control
- Bill of materials (BOM)
- Master production scheduling
- Equipment maintenance scheduling
- Accounting and financial planning
- Forecasting demand
So, there you have it, the differences between MRP I and MRP II system.
Next, let’s examine MRP systems’ importance for your business.
Why is an MRP system important?
Now that you know MRP system meaning and everything there is to know about MRPs, let’s delve into why it’s important for manufacturing businesses (especially direct-to-consumer manufacturers) to get set up with an MRP.
But, firstly, what is the purpose of adopting an MRP system into your business?
Well, the goal of MRP systems is to:
- Minimize manufacturing lead times
- Optimize inventory levels
- Maximize service levels to boost business efficiency
An MRP system will give your business the real-time visibility you need to see inventory requirements to meet demand, help you maintain optimal inventory levels, and design the best production schedules. Without these functions, your business is going to be playing catch up from having the adopt manual systems instead, such as inefficient Excel spreadsheets, which will lead to issues such as:
- Ordering too many raw materials that will increase carrying costs and tie up capital from overstocking
- Stockouts from underordering materials and components will make you miss deadlines and driveaway sales
- Create bottlenecks and cause disruptions, increasing your manufacturing costs and decreasing your output
At first, handling your production planning and scheduling will be fine as you’re just starting out. But as companies begin to grow and start manufacturing on a larger scale, many turn to MRP systems, not just in manufacturing but in over industries too, to create a perfect balance between supply and demand.
A scenario of the importance of MRP systems in manufacturing
Let’s imagine you’re a bicycle manufacturer. Your MRP system basically performs like an inventory management system which will streamline your production schedules and help you place orders for your dependent demand. A bicycle manufacturer needs to keep track of multiple dependent demand items, including aluminum pipes, tires, seats, bicycle gears, etc.
An MRP system steps up by being able to answer questions automatically and immediately to help you know when you can initiate a production run, such as:
- The components you need in terms of inventory
- The quantity you’ll need
- When the components are needed
For the bicycle manufacturer, the MRP system matches the flow of materials and, in the order they follow along the manufacturing route, depending on the availability of the preceding dependent demand. This allows the manufacturer to understand what’s missing, the lead time for each product, and any bottlenecks forming on your production line.
The benefits of adopting an MRP system
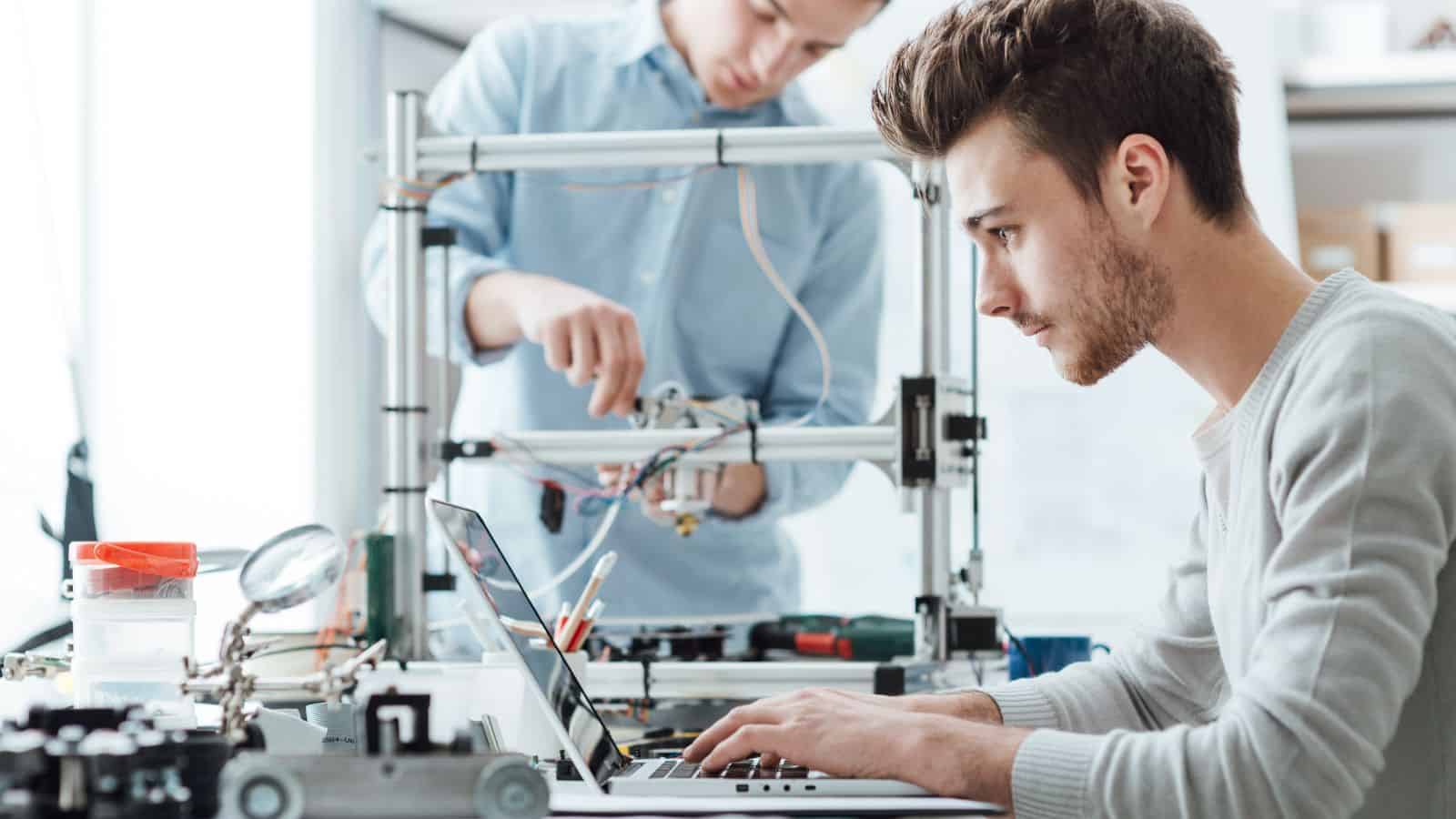
So, as you can see, the importance of an MRP system is to automate your production flow and to have your lead times calculated, and scheduling completed automatically.
But MRP systems don’t stop there.
Stock ideal inventory levels
Reduce the amount of inventory you hold while tracking your production. An MRP system allows you to avoid holding the materials and components that are rarely used in production. Providing you with more space to store your more important items gives you peace of mind knowing you can easily avoid stock shortages.
Purchase planning
While we’re on the topic of maintaining ideal inventory levels, the benefit also passes over to your purchase planning. An MRP system will tell you exactly what you need to order and when you need to order it. Knowing this information in real time allows you to improve your supply chain management. It also gives you and your managers the information needed to meet product demand and plan future expansions.
Production planning
As we have explained, keeping track of your production flow and dependent demand inventory levels is tricky. MRP systems highlight stock shortages and reorder points so you can order materials immediately and reallocate your machinery or labor for alternative jobs in the meantime.
Work scheduling
MRP systems save you the headache of figuring out production schedules by automatically doing it for you. This allows you to delegate work easily, increase or decrease your workforce, and understand the deadlines of all your projects.
Reduced costs
With improved analytics, MRP systems can help to reduce your carrying costs and save money by avoiding overtime. With an MRP system, you can save money across the board as it allows you to better understand your cost of goods sold and manufacturing costs.
Better service to customers
Finally, by using MRP systems to improve all of the above, you’ll be able to better deliver on your deadlines, and the reduced costs allow you to pass those savings on to your customers. And that’s everything you need to know about what is an MRP system and the importance of getting it up and running in your business.
However, earlier in this article, we briefly touched on another system known as ERP. So, before we move on to how to choose the right system for your business, let’s look into a comparison of MRP and ERP systems.
Differences between ERP and MRP systems
When manufacturers realize they need to incorporate some sort of process automation software into their business, they come across ERP and MRP systems. We’ve outlined the differences below to make it easier to choose between the two.
What is an ERP system?
An ERP (enterprise resource planning) system is a tool for manufacturers looking to take control and integrate the important areas of their business. Before even coming across the term MRP, people often come to ERP first. It can be confusing to get to grips with when pitting ERP vs. MRP systems. Conventionally ERP systems were aimed at larger corporations with over 500 employees. However, as technology has evolved, there are now ERP systems fit for small and even micro businesses.
ERP systems allow users to implement improved resource planning by centralizing all their important processes onto one piece of software. Meaning if you adopt an ERP system into your business, you’ll be able to integrate your:
- Planning
- Purchasing
- Sales
- Marketing
- Finance
- Human resources
Are your eyebrows furrowed yet?
We understand your confusion, as the borders between the systems have melted away. But not to worry, we’ll try to clarify everything in the following few chapters.
The main differences between MRP and ERP systems
In order to make a decision between ERP vs. MRP, you’ll need to understand what your manufacturing business needs are.
ERP systems offer much more comprehensive solutions that go way beyond resource planning and management. With an ERP system in place, businesses can unify all their departments and data, automate processes, and get real-time insights into how the company is performing. On the other hand, MRP systems are focused solely on managing material resources and inventory levels. They don’t offer the same breadth of features as ERP systems and lack integration capabilities.
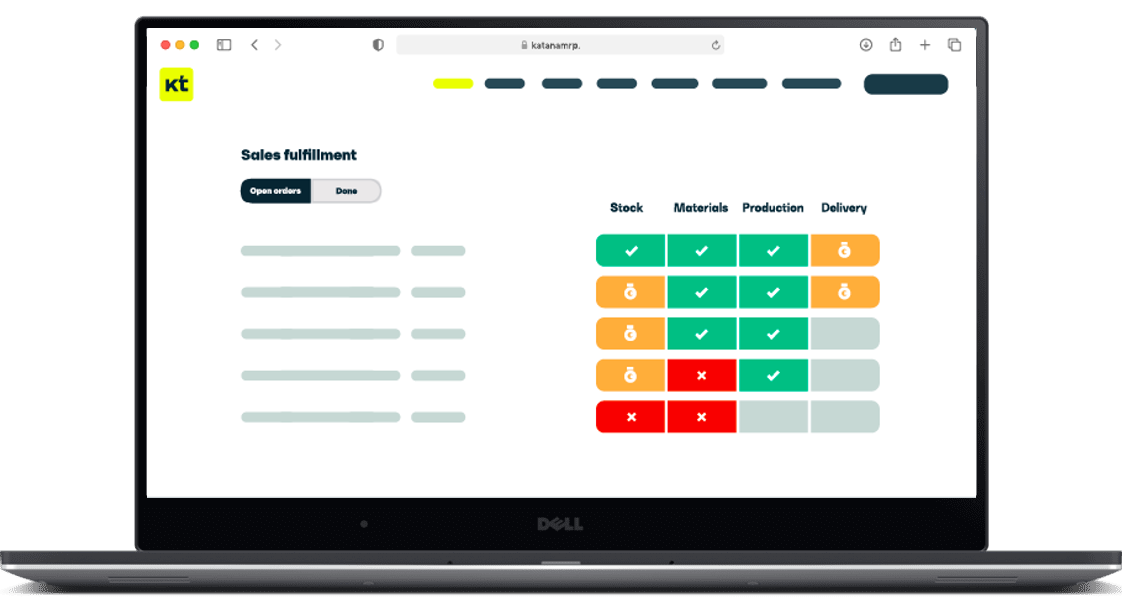
ERP vs. MRP: Which one is right for you?
As mentioned before, traditionally, manufacturing ERP systems were only targeted at larger corporations. They also required a large initial investment in terms of time and money to get everything set up. Nowadays, however, things have changed. ERP systems have become more user-friendly and affordable. They can be implemented in phases, which makes the transition smoother, and they offer a lot of value for small and medium-sized businesses.
Many manufacturing businesses start off with an MRP, but once the business outgrows its capabilities, they realize they need to switch to an ERP system.
Swapping out all your existing systems can take quite some time and effort. In addition, it can also slow down your production. To avoid such problems down the road, it’s better to be prepared by implementing a system that is able to grow with your business.
Katana’s manufacturing inventory software is designed for small and medium-sized businesses. It’s cloud-based and can be scaled up or down according to your needs. You can see Katana in action by requesting a demo.
How to choose the right system
Here are the key factors you should consider when choosing the right system for your manufacturing business. Until recently, manufacturers had been stuck between a rock and a hard place. On the one hand, was the choice of working with overly complex webs of inefficient Excel spreadsheets, and on the other were the expensive ERP systems of the big players.
It’s not been an easy ride.
Thankfully there are now affordable ERP and MRP systems available to meet the needs and budgets of growing manufacturers. These systems can offer benefits ranging from optimal inventory control to better production planning strategies. That doesn’t mean that all the systems on the market are worth your time, though.
Here are seven key factors you should consider when choosing the right MRP for your manufacturing business.
1. Taking control of your inventory should be a priority
A good MRP keeps track of your stock. An exceptional MRP gets your inventory to optimal levels. What you want is software that will provide live inventory control to guide you in purchasing at the ideal times. This way, the benefits of achieving optimal inventory are twofold:
- Excess stock is reduced, which cuts carrying costs
- You won’t run out of stock, so there will be no more delayed deliveries
That means you need to look for software that manages raw materials and products, sets reorder points for when they are low, and can make stock adjustments in real time. If all these features are present, you’re onto a winner.
2. Strong production planning capabilities are key to MRP
Production planning processes and resources is a two-sided coin — both heads and tails must be balanced to achieve maximum efficiency.
One side of the coin is finding an MRP to help you schedule your operational and human resources. This means that your teams are focused and do not get overwhelmed, while your machinery won’t be double-booked. Scheduling tasks for your team might not be something you expect from an MRP, but human resources are as critical to your operations as your material resources.
The other side of the coin is prioritizing your productions.
Smart production scheduling software allows you to rank manufacturing jobs while automatically considering the material availability. Make sure that both sides are covered. That way, you can save money by keeping an efficient schedule and are also able to make changes to your production according to demand.
3. Find software that gives you accurate costing
One of the most desirable features of MRPs is production cost reporting, and there’s a good reason too. Keeping track of your costs can be mission impossible using spreadsheets, especially if the cost of raw materials is not consistently stable. Finding the right MRP can help you gain accurate costing, allowing you to make better pricing decisions based on actual product margins.
There are two key aspects to look for:
- The capability to create multilevel product recipes with sub-assemblies
- Product recipes that track manufacturing costs as well as the cost of materials
Having both elements will give you a complete and up-to-date bill of materials so you can sell products at the right price.
4. Get a complete order fulfillment cycle
MRP systems should make your life easier. The more elements your order management system covers, the better. Look for software that makes sales, production, and inventory one seamless flow. This will maximize the system’s use and reduce the amount of work you have to do as more features will be automated.
MRP systems with a complete order fulfillment cycle will give you the flexibility to make-to-order or make-to-stock, depending on your manufacturing needs.
So, if you have a dedicated sales team, they can use these tools to create orders themselves. On top of that, they will know the completion dates without having to be in constant communication with your production team. The perfect solution is a system that integrates your entire workflow from a single platform.
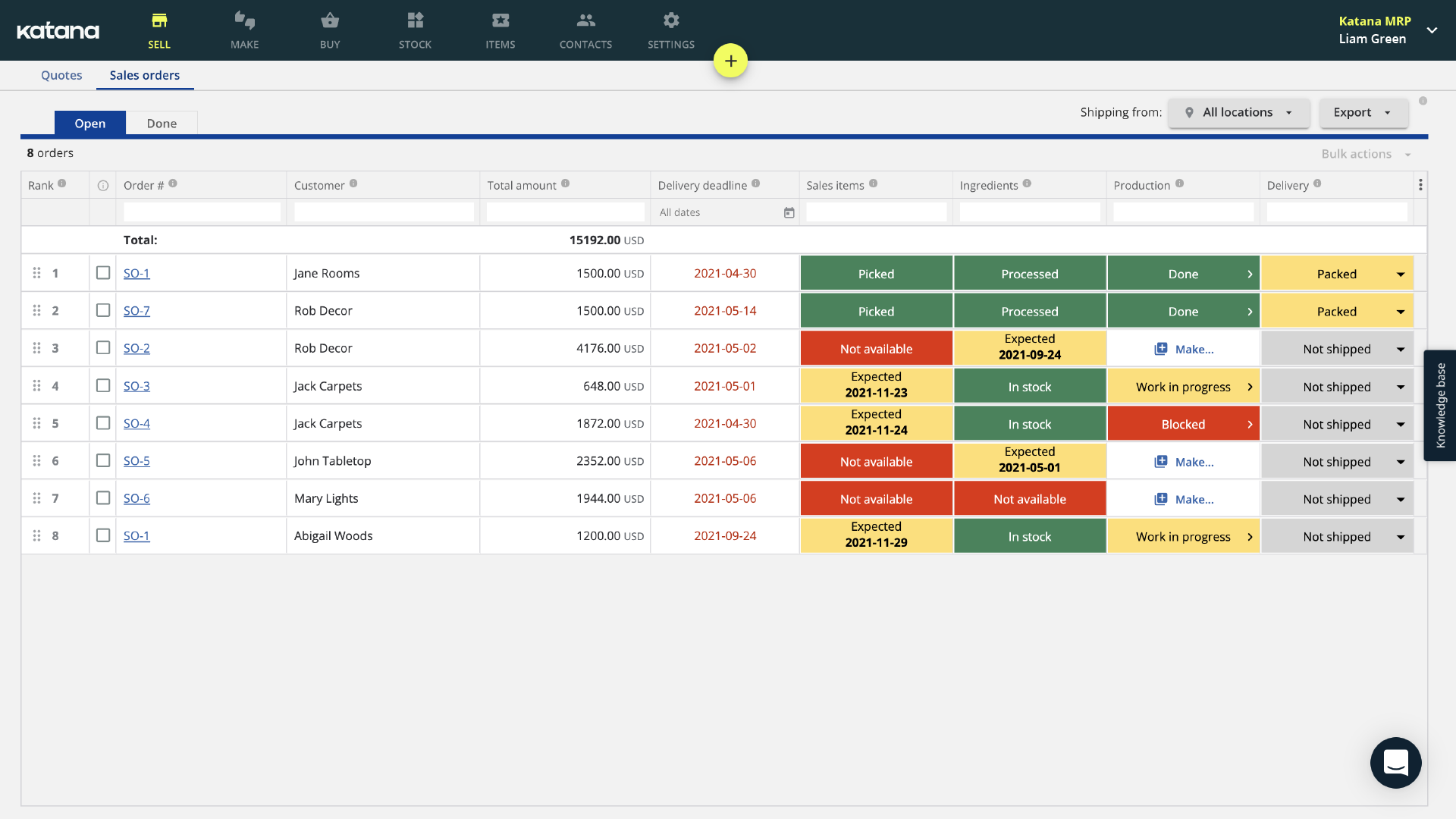
5. Look for the important integrations
Most scaling manufacturers use multiple online services to meet their needs, whether it be for accounting or sales. Ideally, you want to find software that integrates with popular e-commerce platforms like Shopify or WooCommerce and accounting software like QuickBooks Online or Xero. That’s going to make a critical difference to the manufacturing seller, as it means that you have full visibility of stock, production, and sales.
6. Friendly face matters
One of the beauties of having an MRP system is that it can be used by different team members while reducing miscommunications. That’s why you want software that’s understandable by everyone who uses it. Whether you’re someone that uses it every day or only needs to check on things once in a while, the interface should be friendly enough to be accessible to both.
This might seem superficial, but the reality is that if a system looks simple, then there’s probably been effort put in to make it easy to use as well. It will greatly reduce anxiety amongst employees if you go for a modern, intuitive solution rather than a mind-numbing program that looks like it jumped out of the ’90s.
7. Cloud-based software is where it’s at
As well as it being user-friendly, you also want your software to be accessible anywhere by anyone.
Cloud inventory software means that anyone in the business, including yourself, can have full visibility no matter where they are. Let’s say your production manager goes away for a week-long conference. As long as they have internet access, their trip will not disrupt your business workflow. Remote work is on the rise, and this solution gives your team the flexibility to work away from the office.
MRP system implementation for small businesses
The big decision for small manufacturers is how do you choose from a large collection of small business manufacturing software available today?
Well, first things first, you want to research the market to determine which software gives you the tools you need to manage your business. To get you started, review sites, such as Capterra or Software Advice provide ratings of software based on customer reviews and even have their own top choices lists. For example:
- Capterra’s top 20 MRPs list
- Software Advice’s top manufacturing software
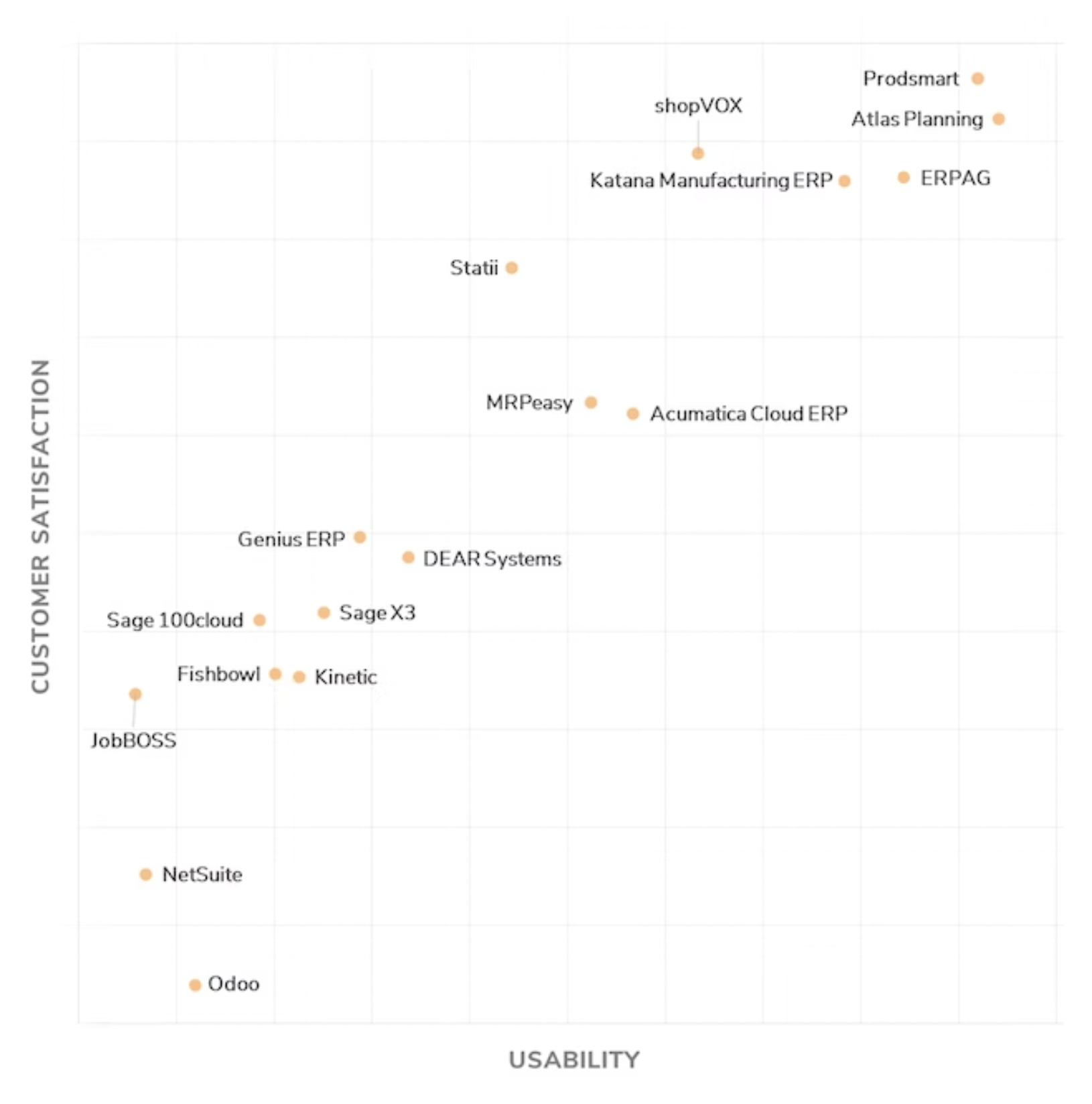
But that’s just the beginning of a long journey. Here are our 9 Insider tips for a smooth implementation of MRP systems for small businesses.
1. Know your needs
Whether you’ve already chosen the software you want to go with or still browsing, it is vital to know your reasons.
Otherwise, you’re going to lose focus very quickly. To stress this point — you need to know your needs and the problems you’re trying to solve. If it’s a large-scale inventory you’re struggling with, then find out if the system can handle your number of products.
If you need raw material inventory booking, check if there’s support for that before you start implementing.
If you’re unsure, an excellent place to start is to look at where you’re currently using the greatest number of spreadsheets. Those are the elements you must ensure the MRP of your choice can take care of. It’s the tediousness and inefficiency you want to eliminate, so make it the focus when finding and implementing your chosen software.
2. A live demo or a free trial is everything
You can read about all the millions of features that software offers and still not know what it’s like until you see it in action yourself.
It’s often the case that a business buys into a great sales pitch and finds that the system is much more difficult to use than expected. Or it doesn’t even match their needs. For example, a website may list a feature that their MRP software tracks your stock, so you know when you are low on materials.
However, it may not tell you that there is no visual cue for this, so you need to check the system manually every day to find out what you’re missing.
This means your workload has not been reduced that much, and sadly, you wouldn’t know until you had already bought it. That’s why you should look for MRP that offers a demo or a trial.
3. Prime your data
One of the major speed bumps in MRP implementation is the lack of organized and accurate data.
Firstly, that means ensuring that your inventory lines up with the reality of your stockroom. You can give your new system a head start by doing a thorough stock check at this time and updating your numbers.
Secondly, you need to get your spreadsheets in order regarding materials and products. That means having your inventory matched with their SKUs, variants, costs, and categories so you can import your data as soon as needed.
Katana offers a data import template, which makes transferring your inventory from your spreadsheets effortless. If you already have a Shopify store, you can use the integration to bring your finished products over with one touch of a button.
4. Do an integration checklist
Most cloud inventory software works with other online applications to give you broader options for areas like accounting and online sales.
That’s why you must consider the current and future integrations of the system. Make sure you can connect to your favorite business tools like CRM platforms or accounting software. But even more importantly, you need to know how far the integrations go and what the limitations are.
Just because there is an integration in place doesn’t mean you can do everything you imagined. There could be workarounds involved, and you want to know that before investing your time.
5. Look for expert support
Every discipline has its guru, and MRP implementation is no different.
See if the company you’re signing up for offers an implementation meeting. Having a guru by your side to set things up (even virtually) can make a huge difference in the time you save working it out yourself. You also want to find out if demo videos are available to give you an idea of how the whole system works.
6. Separate testing and MRP implementation
You want to know how your new system works before you go all in, right?
That’s why starting with a testing period where you can play around and iron out the details is useful. You could start with one product to keep the process simple. Probably best to go with your key product if you have one that can serve as the centerpiece to work around.
Once the tests are completed successfully, you can move on to implement your system to its full capacity.
If you’ve already run your tests properly, you shouldn’t be overwhelmed by any unexpected jabs. But even then, you want to constantly review your processes to ensure you’re getting the most out of it, especially in the first couple of months.
7. Get everyone in the loop
It becomes a lot easier to make sure your MRP implementation goes to plan if you have your team to support you.
Doing the whole thing alone just means you’ll have to go back on yourself later. Better to get it right on the first run, right? MRP implementation can be a lengthy process. Depending on the complexity of your business, it could be a matter of weeks, but more realistically, it’s a matter of months.
Still not bad, considering legacy ERPs take an average of 6-24 months to implement.
But that’s why it’s important to keep all stakeholders up to date with the potential changes. This also means that any training should be provided ahead of time. This is a significant incoming change and should be treated as such. It will make the transition a lot smoother if the team is less resistant and more receptive to the change.
Give regular updates regarding at what stage you are.
Even more importantly, use the opportunity for feedback, especially from those who will be using it most frequently — like the production planner. Your team can give insight into the nuances and details you might miss. Remember — Team effort is required.
8. Be prepared for change
Your processes might have to be slightly adjusted when executing MRP software.
Each system works differently, so your workflow could be affected by features like reorder points and perpetual inventory. Take this as a positive step and run with it. Otherwise, you’ll be fighting against the system you’re trying to implement. That’s only going to slow things down.
Understanding the benefits and spreading the love to your team is much better.
Pro tip: There should always be someone with executive decision-making power involved so that the MRP implementation can be as effortless as possible.
9. Set aside sufficient time and resources
Failing to plan is planning to fail. So, make sure you set the time aside to develop a detailed plan and checklist of your MRP implementation process. It’ll be worth the effort.
The process of MRP implementation could be one of the biggest projects you embark on. A common mistake is underestimating the time and energy it takes to set up. The implications are wide-spanning, so at least one person should be wholly responsible for the implementation. That means taking the time to get things right, understanding the system, and swinging into action.
It can be a great idea to have an implementation plan written out, which you update every time you take the next step. Here’s an example list of steps:
- Analyze requirements
- Confirm that MRP has the capacity for requirements
- Ready the test data
- Go into testing
- Ready the full data
- MRP implementation with full data
- Run integrations
- Make adjustments for optimization
- Review progress and whether requirements reached
Upgrade to the ultimate manufacturing ERP
So, that’s everything you need to know about the world of MRP and ERP systems.
Using this guide, you should better understand if you should get set up with ERP and MRP systems or if you should stick it out for the time being by manually tracking your business’s processes. However, if you’re considering adopting a future-proof system or want one on your wish list for later, which is the best for your business?
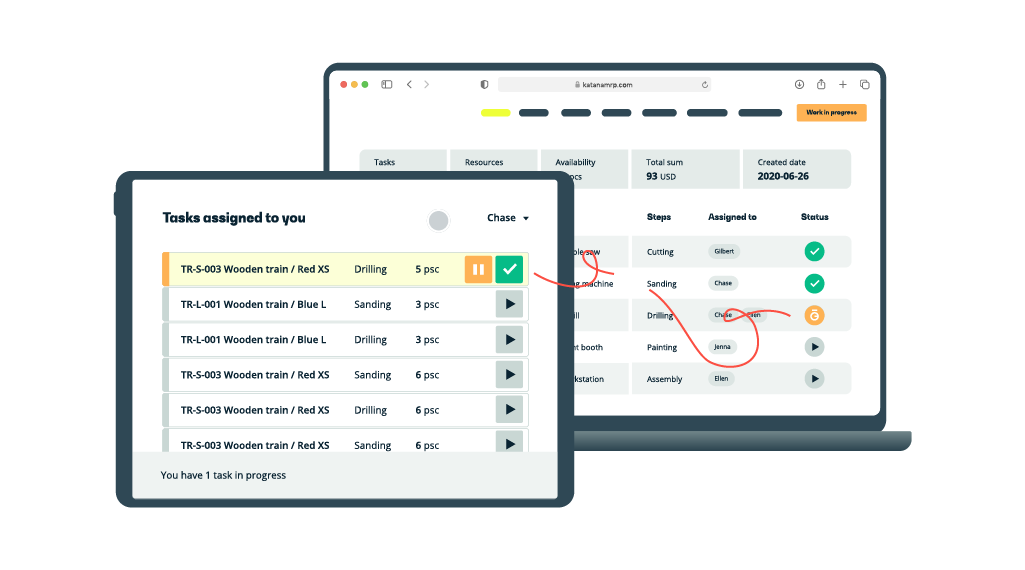
Katana’s manufacturing ERP — smart manufacturing software
Katana’s ERP is an all-in-one industry-agnostic platform for SMB manufacturers offering:
- Enhanced inventory and order management
- Access from anywhere with an internet connection
- Priority-based production planning
- Multichannel sales management
- Manufacturing floor-level control
- Product traceability
This ERP system is designed with the modern manufacturer in mind, as it can handle your regular B2B e-commerce platform orders but also gives you the power to implement a direct-to-consumer business model.
So, how exactly will Katana help you improve your production lines?
Inventory and order management
Katana supports all your different manufacturing processes, from how you manage your stock to if you use forward or backward scheduling for your production.
The automated inventory management feature can track and monitor all your different inventory types, including raw materials, work-in-progress inventory, and finished goods. Integrations with your favorite business apps like Shopify, WooCommerce, Xero, and QuickBooks Online allow you to create a smooth workflow and a centralized point to handle your sales and manufacturing orders.
Accessible on the move
Katana is accessible from any location with an internet connection, meaning if you or a manager have to step out of the office, you can still check in and monitor the status of tasks (something that can’t be offered by localized ERP and MRP systems).
Manufacturing trends indicate a shift in the industry landscape, with many businesses ditching the traditional workshop setup and working from the comforts of their own home. An online small business manufacturing software like Katana supports you and your team when someone needs to do remote work. If you take commissions or outsource manufacturing, providing partners or freelancers access with their own account to your contract manufacturing software allows you to have a clear communication channel with not only employees but other individuals from anywhere around the world.
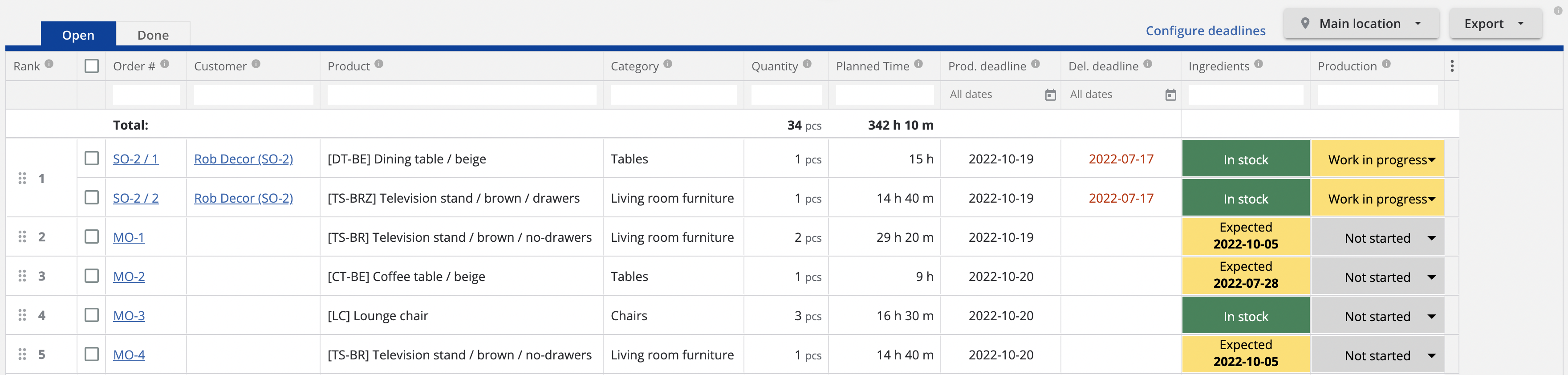
Priority-based production planning
No more sweating trying to design the perfect production plans.
Katana automatically schedules your production based on which orders were created first. However, if you feel the need to rearrange your workflow, you can do so with Katana’s nifty drag-and-drop function. Once you’ve defined your resource capacity with Katana, it can calculate how many resources you need for a project and gives you an estimated deadline. All this information can be used to improve your rough-cut capacity planning.
Integrations with your e-commerce platforms will allow you to generate manufacturing orders from within Katana if you have no finished goods available. Katana will also take care of all the associated scheduling.
Manufacturing floor-level control
Katana comes with an app for complete shop floor control, giving production planners and employees a clear communication channel, so each can update the status of tasks, monitor the progress of operations, and easily assign tasks to available resources.
Katana’s Shop Floor App gives you smooth shop floor planning by taking manufacturing orders from Katana and automatically breaking them down into tasks. The system then assigns them automatically to workers and resources — though managers can easily change the workflow if needed. By improving your shop floor scheduling, you can improve your:
- Production efficiency
- Enhance your capacity planning
- Set accurate due dates
- Prioritize production
- Reduce production setup time by having better planning functions
Product traceability
Katana offers users product traceability, allowing manufacturers to add batch/lot numbers to items to track the best-before dates of products.
These features are essential and can even be a legal requirement in certain industries. This feature also comes with the tools to perform batch tracking, which gives manufacturers the capability of performing track and trace operations on defective or contaminated products — ultimately giving you the power to implement the smoothest product recall possible.
Why not check out Katana’s traceability software and see how it can benefit your business? Request a demo today.
Table of contents
Manufacturing guide
More on MRP Systems
Get visibility over your sales and stock
Wave goodbye to uncertainty by using Katana Cloud Inventory for total inventory control
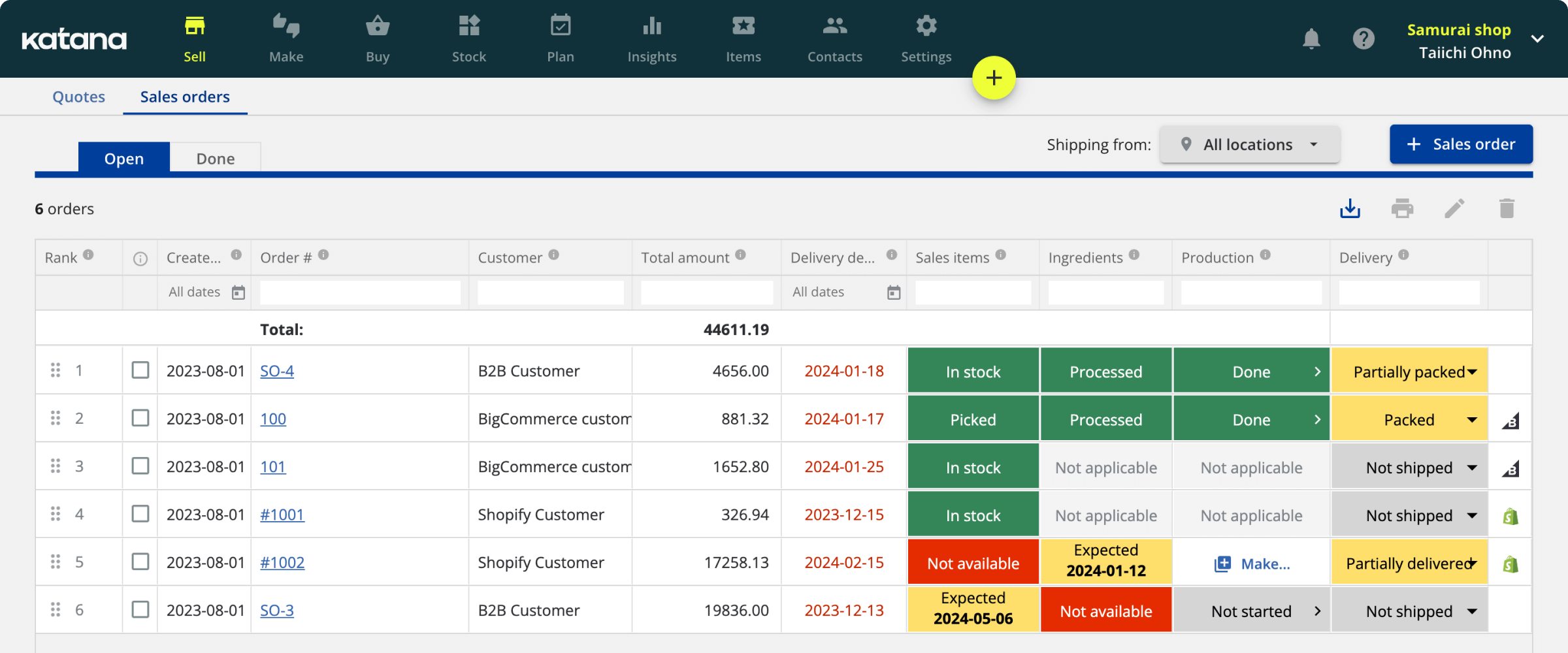