Rough Cut Capacity Planning: Is it right for you?
Rough cut capacity planning will be essential in balancing your production capacity against customer demand. But is it good for your manufacturing business?
Team Katana
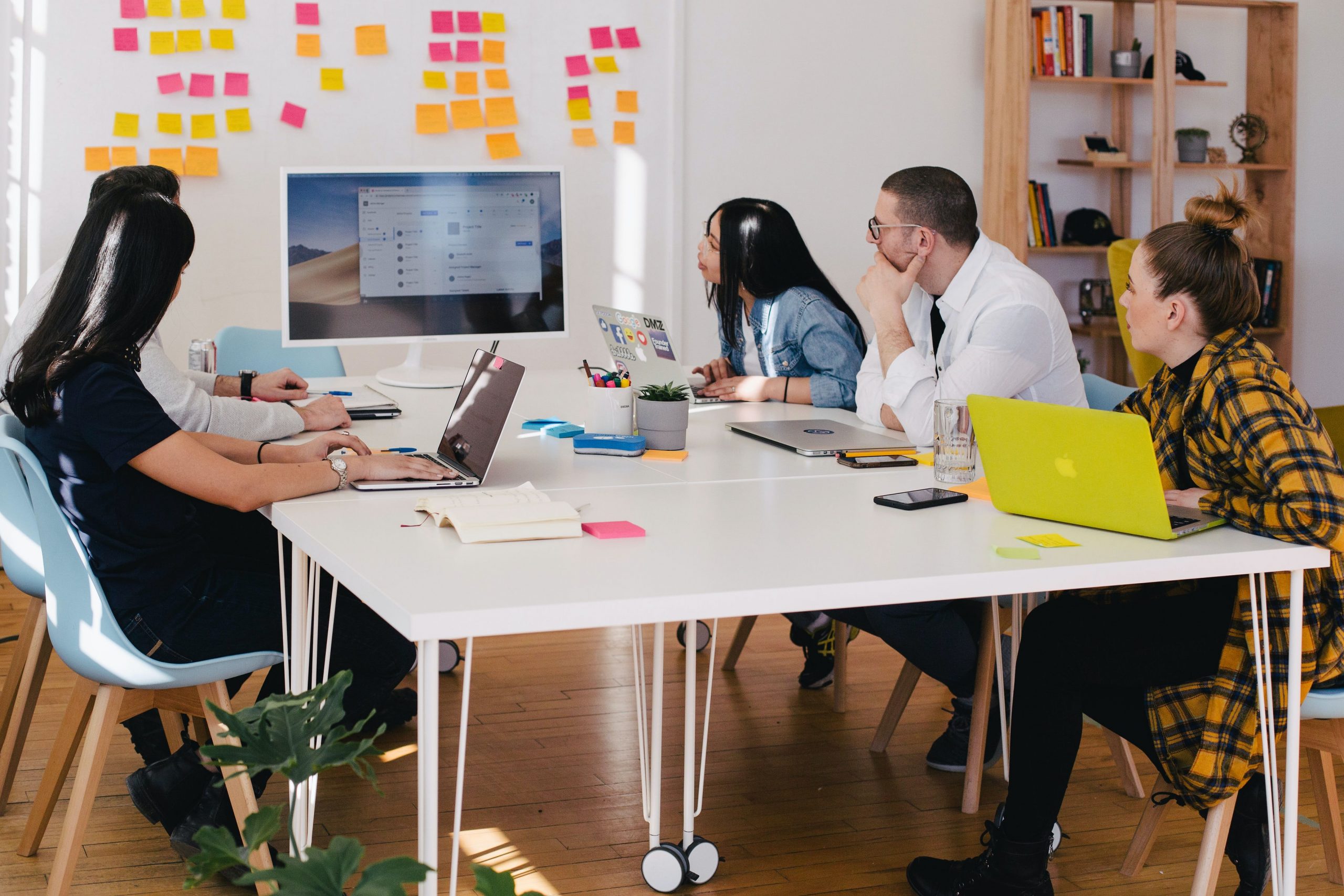
If you’re running your production lines day-to-day, you’re going to constantly run into problems or even completely stop production from unforeseen issues.
That’s why it’s extremely important to work out your rough cut capacity planning, that will help you convert your master production schedule (MPS) into production requirements for key resources, such as:
— Direct labor; and
— Machine time.
Many manufacturers believe capacity planning is a close relative to supply chain optimization, as you’re planning production based on what you have, and what you’ll need in the future.
In this article, we’ll be looking into capacity planning, but mostly focusing on the rough cut capacity planning process, and if it’s right for you.
What is Production Capacity Planning?
Capacity planning is the goal of figuring out the realistic capacity of the shop floor to meet the demand for products within a certain period, to increase your profits and minimize your costs.
These plans can be developed for short- or long-term goals.
When you look at what is production capacity planning, you can think of it as something that’s put together based on:
— The number of workers on your shop floor;
— The skill of your workers;
— The number of machines;
— Wastage;
— Your scrap;
— Defects;
— Mistakes;
— Your productivity levels;
— Suppliers;
— Governmental regulations; and
As you can already see, designing your capacity planning is going to take a lot of time.
And if there are discrepancies between the capacity of your production and the demands of your customers in your planning, it’ll lead to inefficiencies, such as under-utilized resources or unsatisfied customers.
Here’s the basic formula for calculating your productions capacity:
Number of machines or workers x number of shifts x utilization x efficiency
In a nutshell, that’s a breakdown of what is capacity planning. But, what is meant by long term and short-term capacity planning?
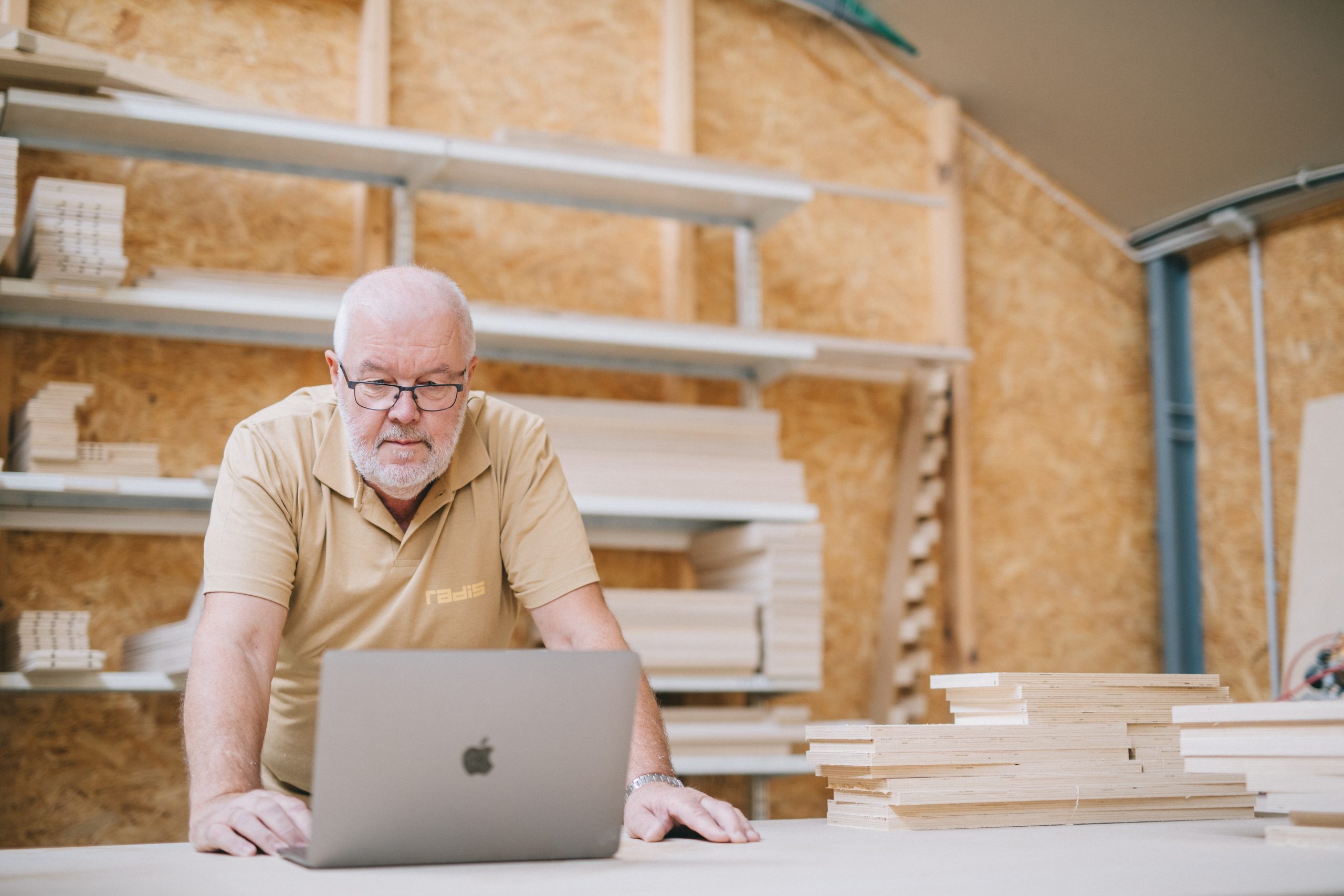
Long-Term Capacity Planning
Long term capacity planning refers to the grand scheme of things, and that is developing plans strategically for all your major production lines.
These long-term capacity plans will include:
— Plans made for specific locations; and
— Technology and transferability of your processes to other products.
Long-term capacity planning isn’t set in stone. It’s something that may change over time when you discover short-term capacity plans are inefficient.
A scenario where long-term capacity planning would take place is when implementing a new shift pattern into your production line, which, unfortunately, doesn’t increase productivity. If you’re unable to subcontract tasks, maybe your best alternative is to modify your routing manufacturing.
Redesigning your factory’s route is an example of a long-term capacity plan to improve productivity.
Short-Term Capacity Planning
You can think of your short-term capacity planning as any plans that are implemented now. Examples of short-term capacity planning issues are things such as:
— Production planning and scheduling;
— Labor shifts; and
— Balancing resource capacities.
The time frame in which your short-term capacity planning runs could be anywhere from a few days to six months.
Your short-term capacity planning is concerned with addressing unexpected demand spikes and drops, efficiently and economically.
An example, and a commonly used example of short-term capacity planning, is offering overtime to your workers. Overtime is a flexible and inexpensive solution to addressing high demand since you won’t need to:
— Hire;
— Train; or
— Add additional benefits.
You can think of your short-term capacity planning as the goal of increasing and decreasing demand, but also assigning resources to meet the demand requirements.
That’s everything you need to know about capacity planning. There are many techniques you can adopt to put together these plans, but for this article, we’re going to focus on rough cut capacity planning.
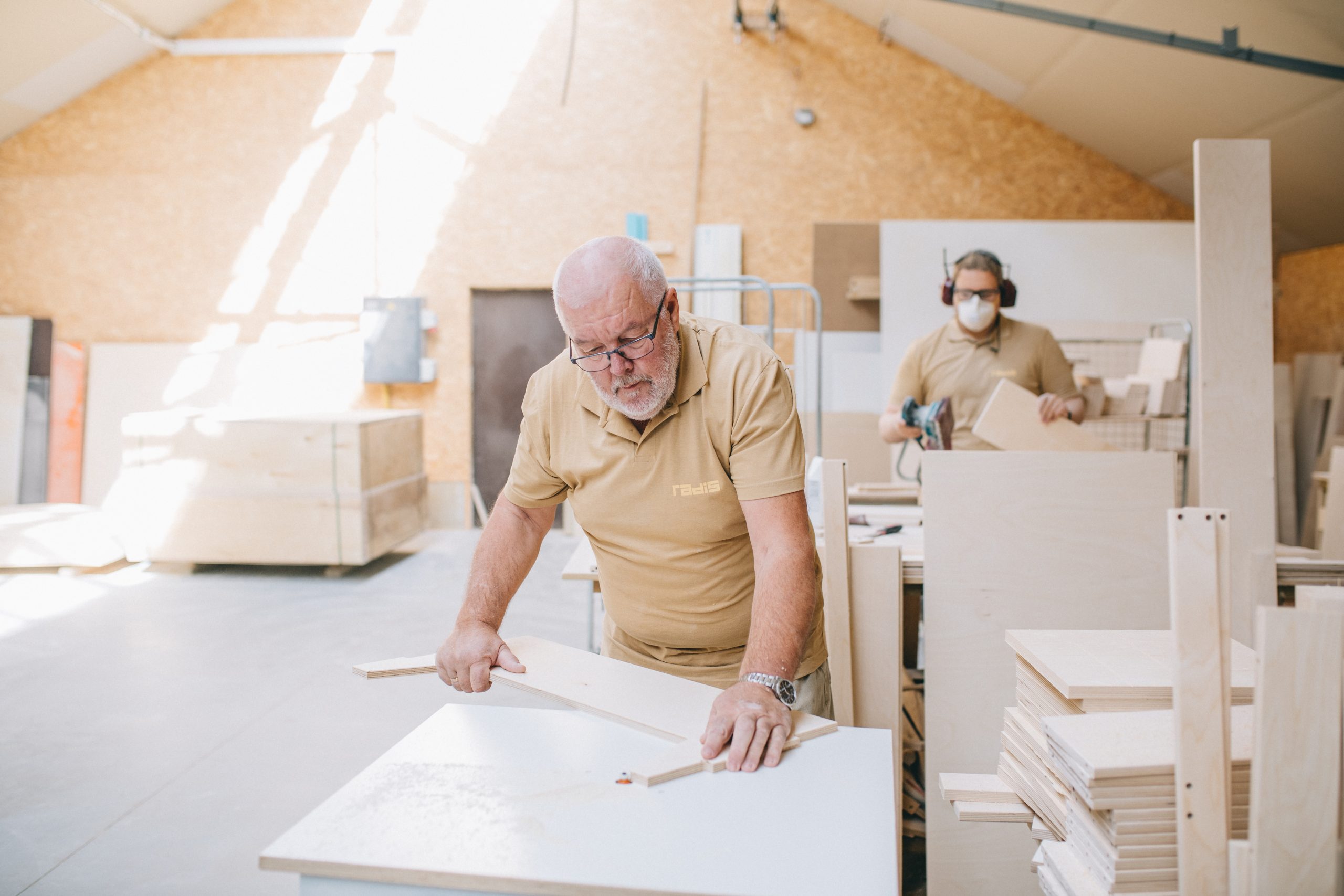
What is rough cut capacity planning?
RCCP process is verifying that you have sufficient capacity available to meet the requirements of your master production schedule.
Rough cut capacity planning is a long-term technique that your marketing and production departments use to balance the available capacity and capacity required so that you can make changes to your production schedule or available capacity.
Traditionally, many manufacturers would adopt MRP software to pull off their rough-cut capacity planning, as it’s a manufacturing execution system that gives you the tools for:
- Production planning and scheduling
- Raw material and finished goods inventory management
- Calculating manufacturing costs
When you’re working out your rough cut capacity planning, it can be done at two levels:
Routing-Based RCCP
Routing-based rough cut capacity planning shows your resource availability. For this, you’re going to look into the required and available capacity in hours per week per resource.
Rate-Based RCCP
This is where you measure your rough cut capacity by production lines. For this, you’ll need to figure out your required and available capacity per week per production line.
So, to quickly summarize, your rough cut capacity planning will look into how much you need to produce, how much you can produce, and how you can find a balance between the two.
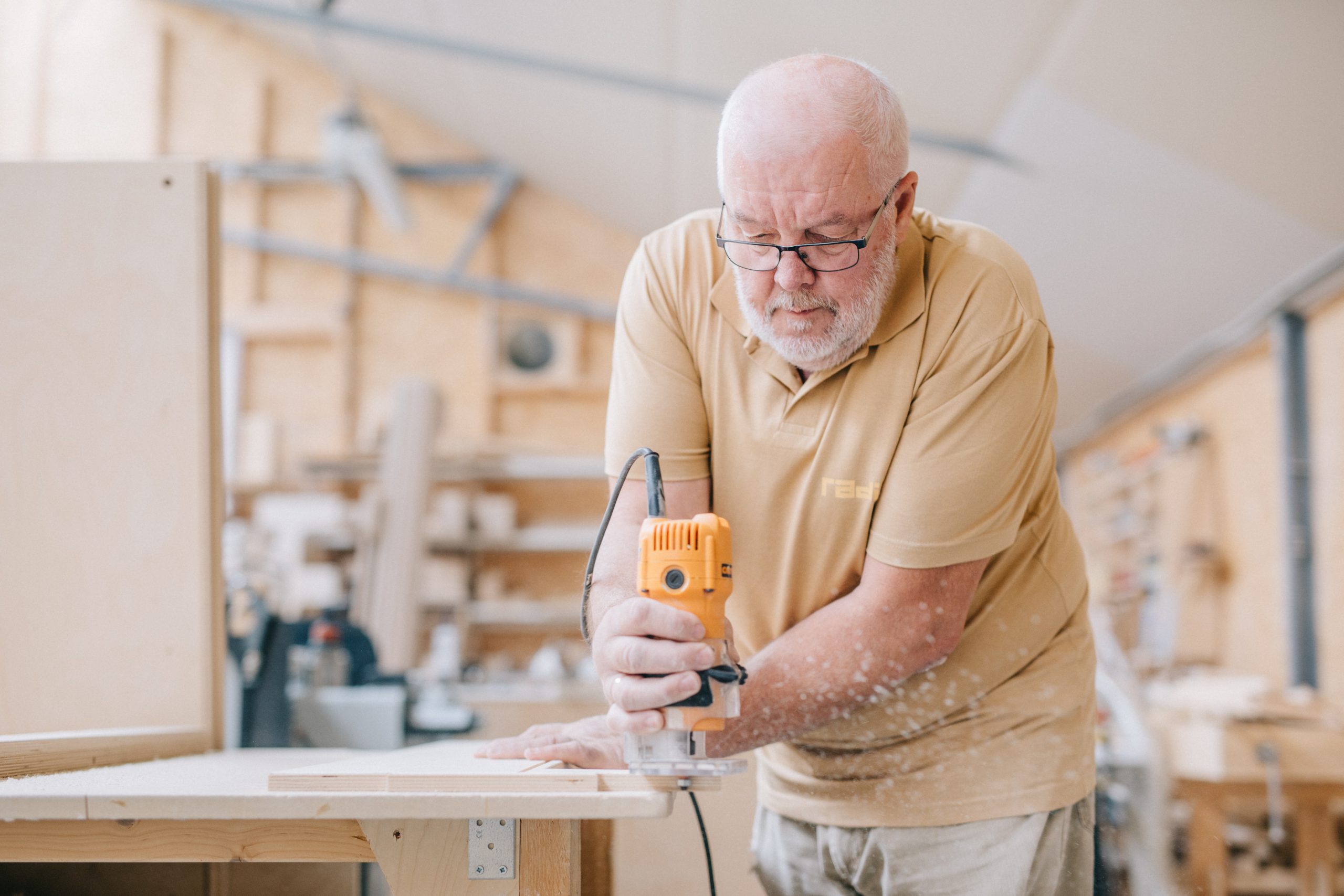
Capacity Planning Example for Rough Cut
Let’s try and better understand how to do a capacity analysis of your production line.
Let’s say you’re a manufacturer who makes skateboards and rollerblades, and you have an estimated demand for your quarters as follows:

To keep it simple, let’s assume production takes place at one factory for both products, and the factory itself is one capacity unit.
And at this factory, the available capacity for each quarter is:

And within this factory three production lines produce skateboards and two production lines produce rollerblades:

The manufacturer must make a plan for production runs, that will decide the ideal number of products to produce for each quarter. In this instance, the manufacturer takes the total demand, and divides it by each quarter to meet demand:

Rough cut capacity planning allows the manufacturer to see the impact on:
— Meeting demand;
— Available capacity; and
— Inventory levels.
This allows them to see the relationship between their supply and demand:
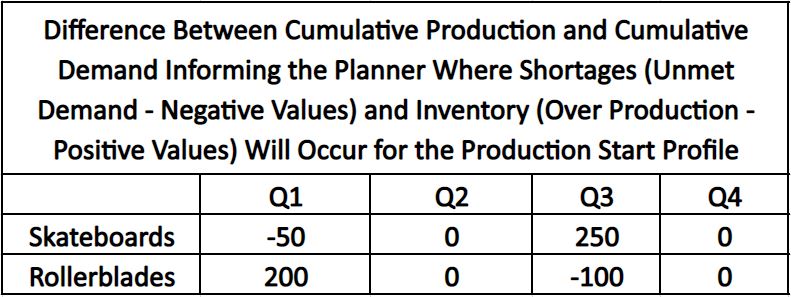
With all this information collected from rough cut capacity planning, the manufacturer can finally put together a production plan across the year to effectively meet their demand:
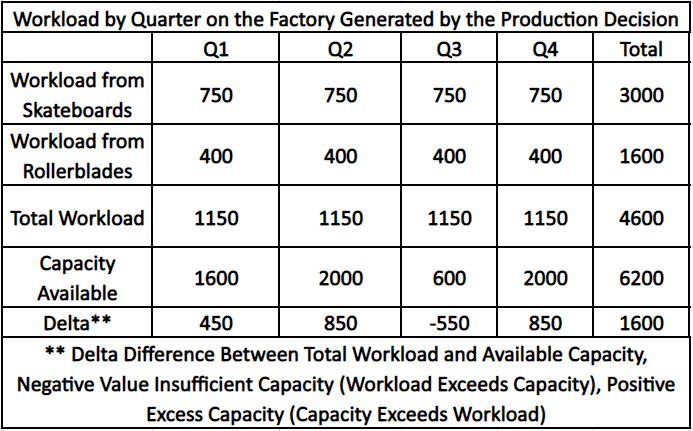
So, that’s a capacity planning example. But, what are the benefits of adopting rough cut capacity planning into your business?
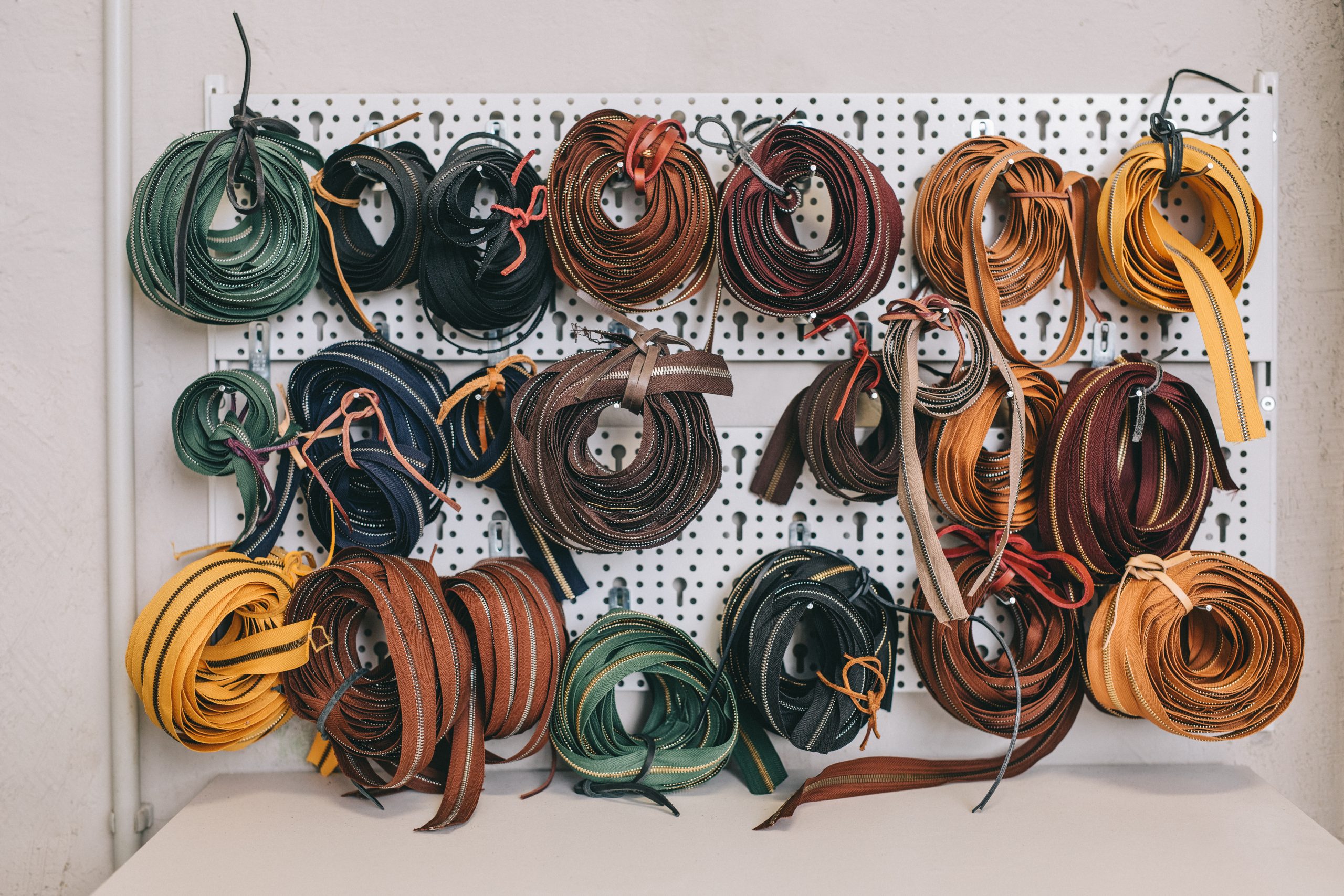
What Are the Benefits of Using Rough Cut Capacity Planning?
It’s worth reiterating that rough cut capacity planning allows you to understand how much supply you’re going to need to meet demand, but also give you a schedule that is flexible (as things happen on the shop floor which disrupts production).
But, other benefits of rough cut capacity planning includes:
Improved Project Management
Understanding all your operations and outstanding job operations means you can improve your project management.
For example, you can see which operations should start by a specific date, and which jobs you can start later because they have a short turnaround.
Essentially, your team will be able to easily prioritize operations by their start date.
Better Resource Management
Rough cut capacity planning allows you to understand the total number of hours of work for each week by each manufacturing process.
For example, knowing how much work is passing through a workstation can help you determine if too much or not enough workloads are being processed, which will allow you to adjust the capacity by:
— Changing the number of shifts;
— Changing the number of workstations in operation; or
— Passing operations onto a contract manufacturer.
Improved Manufacturing Lead Time
The transparency offered by rough cut capacity planning allows manufacturers to easily identify areas along their production lines that are being overworked or are prone to other issues such as a bottleneck in production.
With this overview, it’s easy for you to see an area of concern and make important business decisions immediately to address the problem, which is going to:
— Reduce your manufacturing lead time;
— Reduce costs; and
— Improve customer satisfaction by finishing projects on-time.
As you can see, the benefits of rough cut capacity planning are numerous. But, as you may have already noticed, to pull off RCCP, you’re going to need to develop your planning and forecasting.
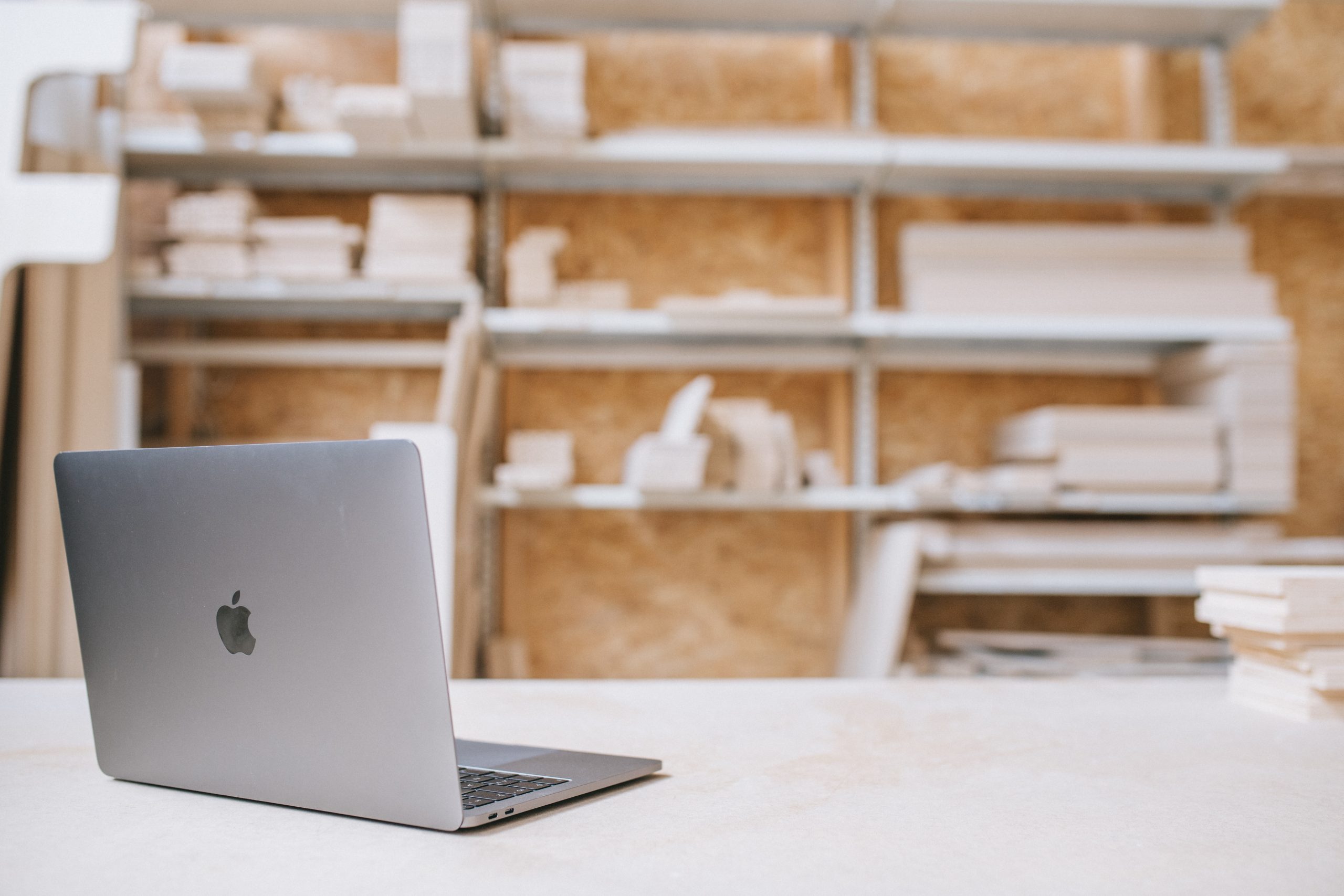
The Importance of Planning and Forecasting
Rough cut capacity planning is going to be essential in helping you achieve your goals over a defined period, but also allow you to understand the issues that might be befalling your production line.
And this is why demand planning is important for rough cut capacity planning because, without a prediction of what future sales might look like, it’s going to be difficult to determine how much you’re going to need to produce.
However, the best planning and forecasting techniques are ones in which you can integrate your financials too.
Without the knowledge of financial outcomes, your capacity planning could fall short from poor cash flow management.
That’s why it’s important to find a tool that can help you manage your manufacturing business, but also track costs and integrate accounting software too.
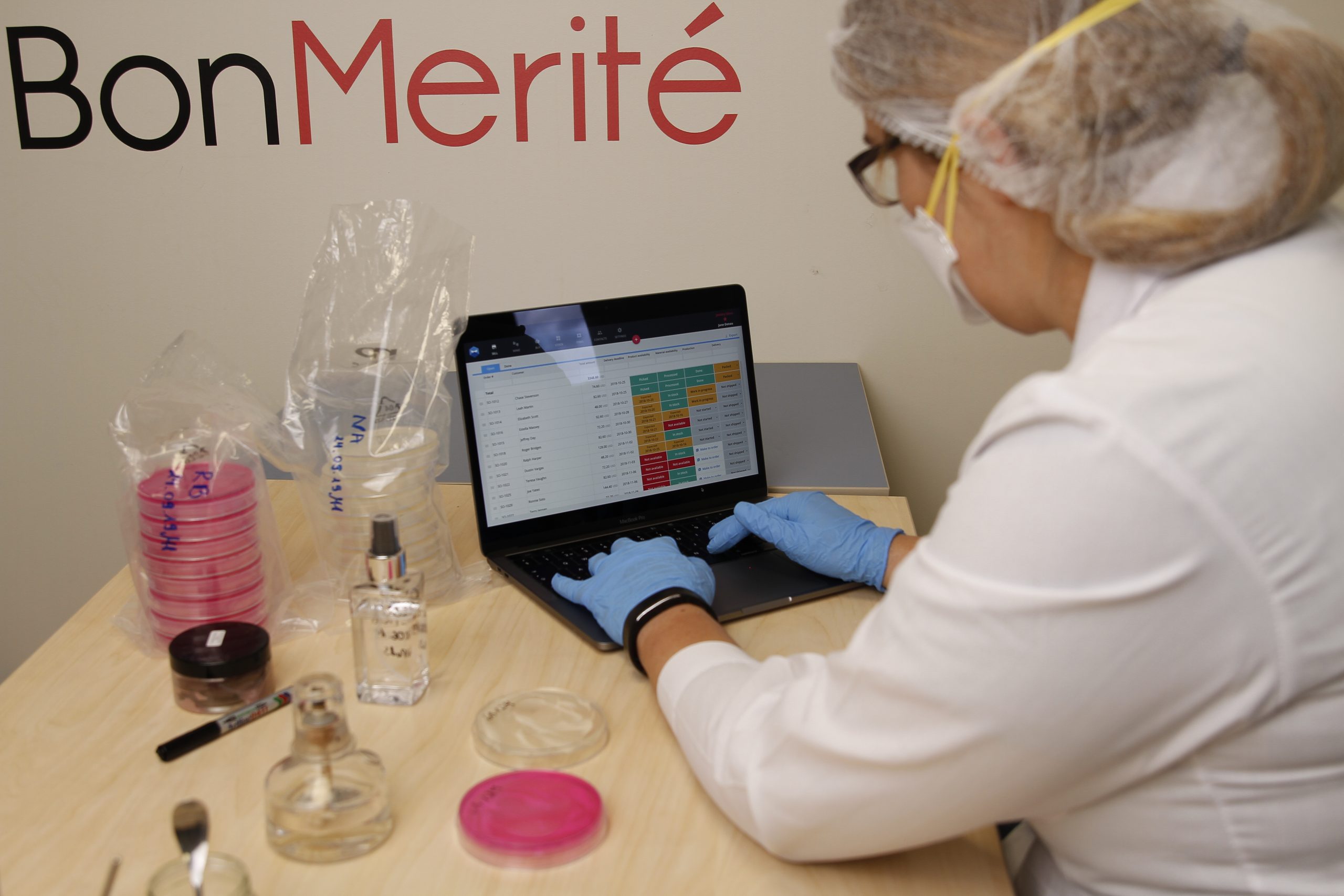
Katana Cloud Inventory Software
Katana Cloud Inventory is the ultimate tool for manufacturers looking for help with their rough cut capacity planning, by streamlining:
— Inventory management;
— Sales orders; and
— Your overall business management by integrating with your favorite tools.
But not only that, Katana gives you the power to track your businesses performance to help you put together your rough cut capacity planning, such as:
— Real-time and historical stock data;
— Priority-based production scheduling;
— Shop floor control management; and
— Inventory buffers from setting safety stock and using reorder points.
Check out the video below to better understand how Katana performs:
Want to see it for yourself? Request a demo today, so you can see how it’s an important ally for increasing your company’s productivity.
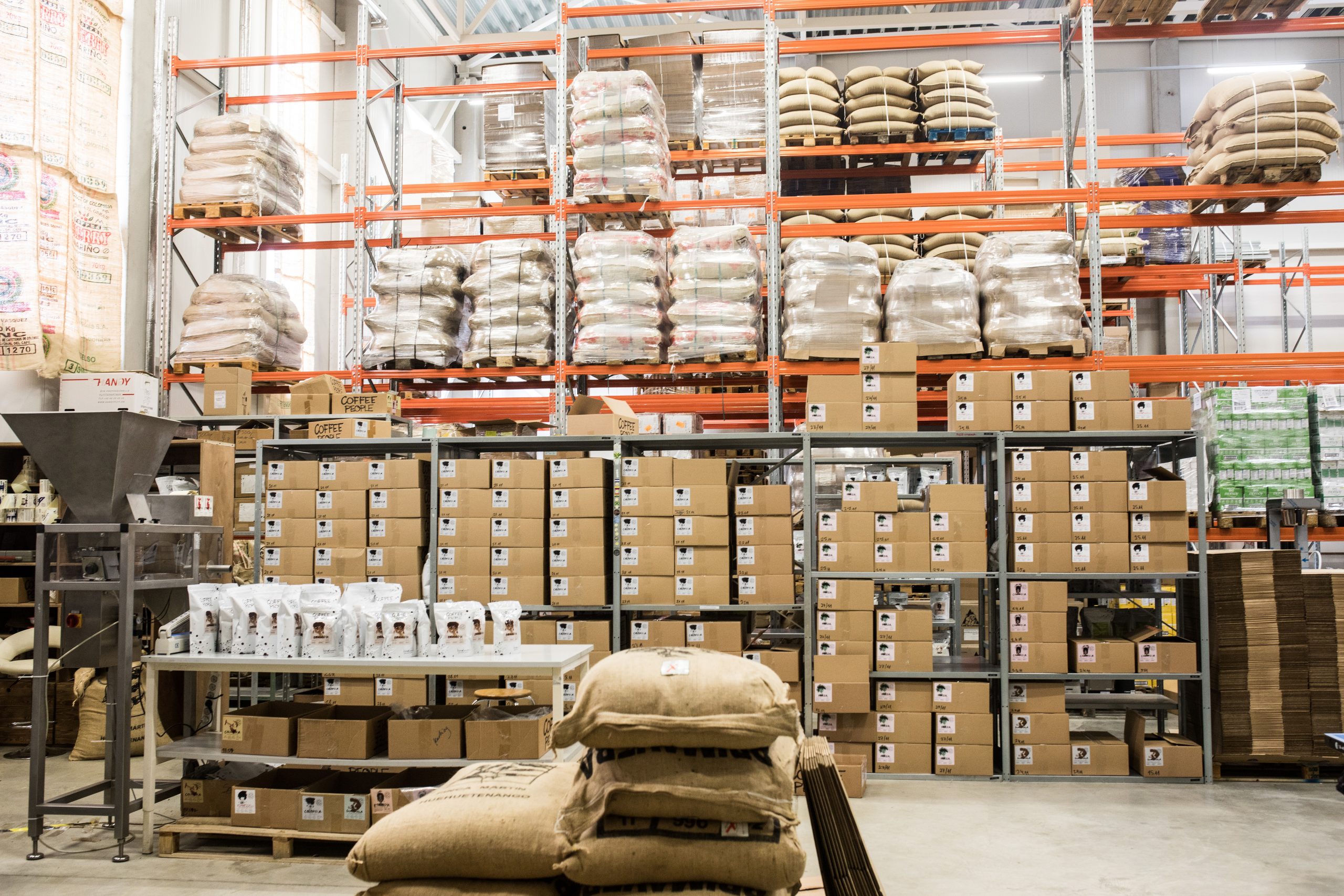
Conclusion: Is Rough Cut Capacity Planning Right for You?
Now you know everything you need to know about rough cut capacity planning. But, one question remains unanswered.
Is rough cut capacity right for your business? Well, it all depends.
For any manufacturer who follows a make to stock workflow, it’s a match made in heaven as you can figure out the ideal quantity of finished goods you should be producing.
But, for make to order and bespoke manufacturing, it’s not so useful as your manufacturing is triggered as soon as a customer has expressed interest.
Rough cut capacity planning works better for manufacturers who have a standardized workflow because if you make customized goods, there’s no way of knowing in advance what it is you’ll even be making.
And that’s it for today, we hope that you enjoyed this article, and if you have any questions, please don’t hesitate to get in touch.
And until next time, happy manufacturing.
Table of contents
Get inventory trends, news, and tips every month
Get visibility over your sales and stock
Wave goodbye to uncertainty by using Katana Cloud Inventory for total inventory control
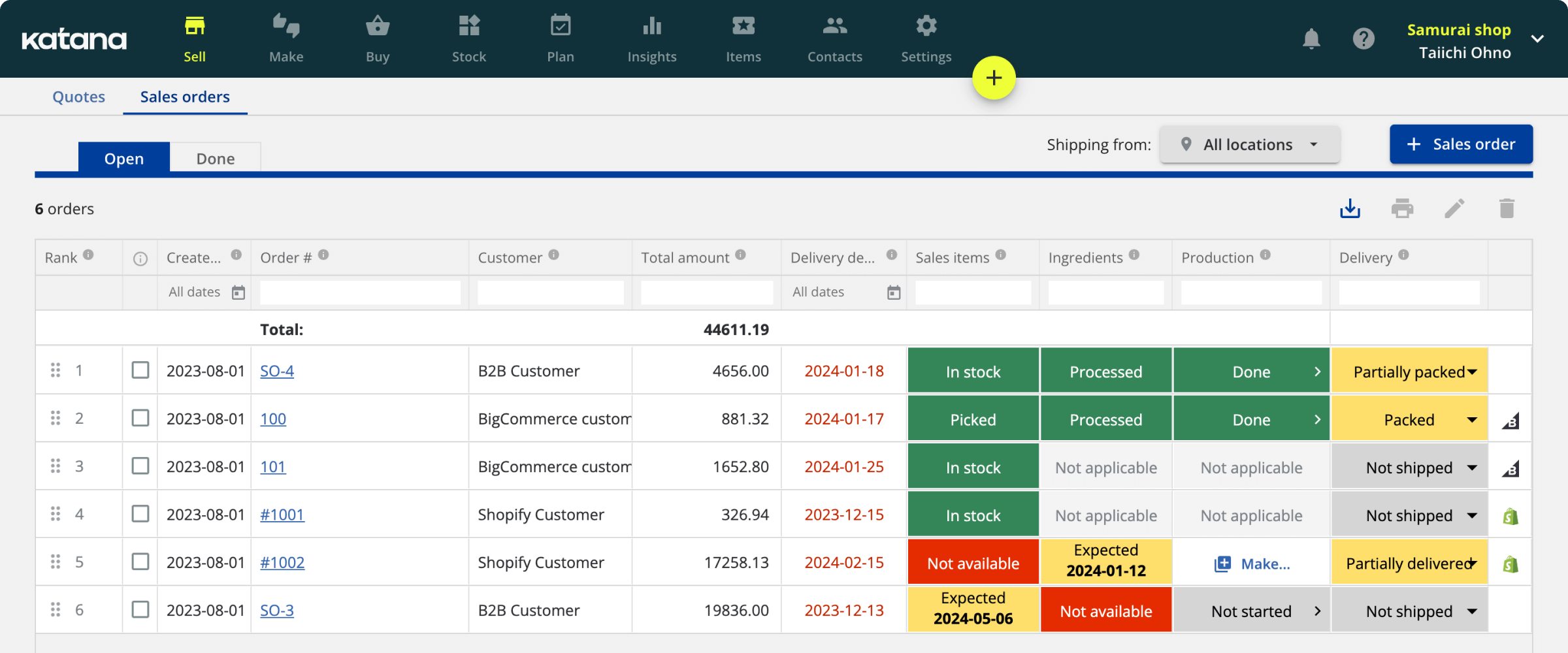