The ultimate guide to what is manufacturing
Download the manufacturing ebook for small manufacturers
Learn how to organize and scale your manufacturing.
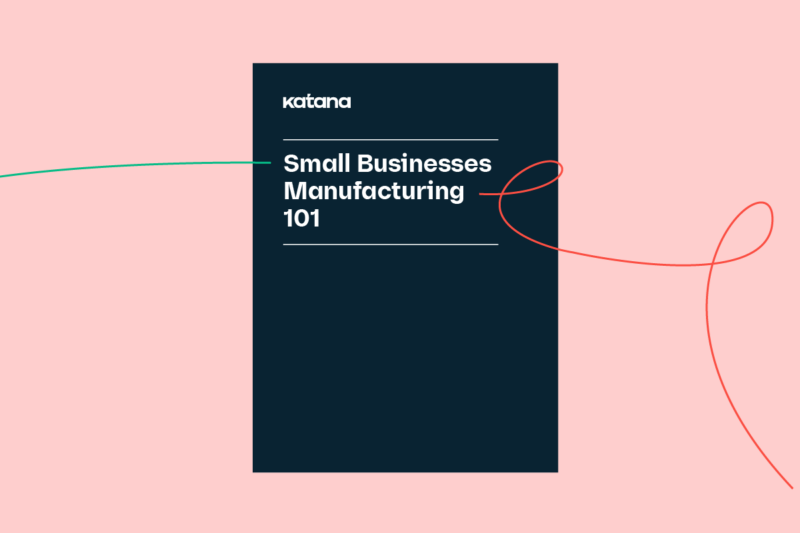
Are you someone who lies awake at night, being pestered by an innovative and brilliant idea for a product that will change the world, but you’re unsure how to make this dream a reality? Or are you someone who has taken the plunge and already delved into the industry but needs a helping hand running your business? Perhaps you’re an expert and just want to refresh your knowledge with some easy-to-follow literature to keep your business running at 100% efficiency.
Whoever you are, an ambitious hopeful, a newbie, or a seasoned veteran, here is our comprehensive mini-encyclopedia on the manufacturing industry — easily broken down for manufacturers. The guide will cover the industry and explore the nitty-gritty details of running and organizing a manufacturing business.
So, let’s get started!
What is manufacturing?
Manufacturing involves converting raw materials, parts, and components into a finished product using labor, tools, and machinery.
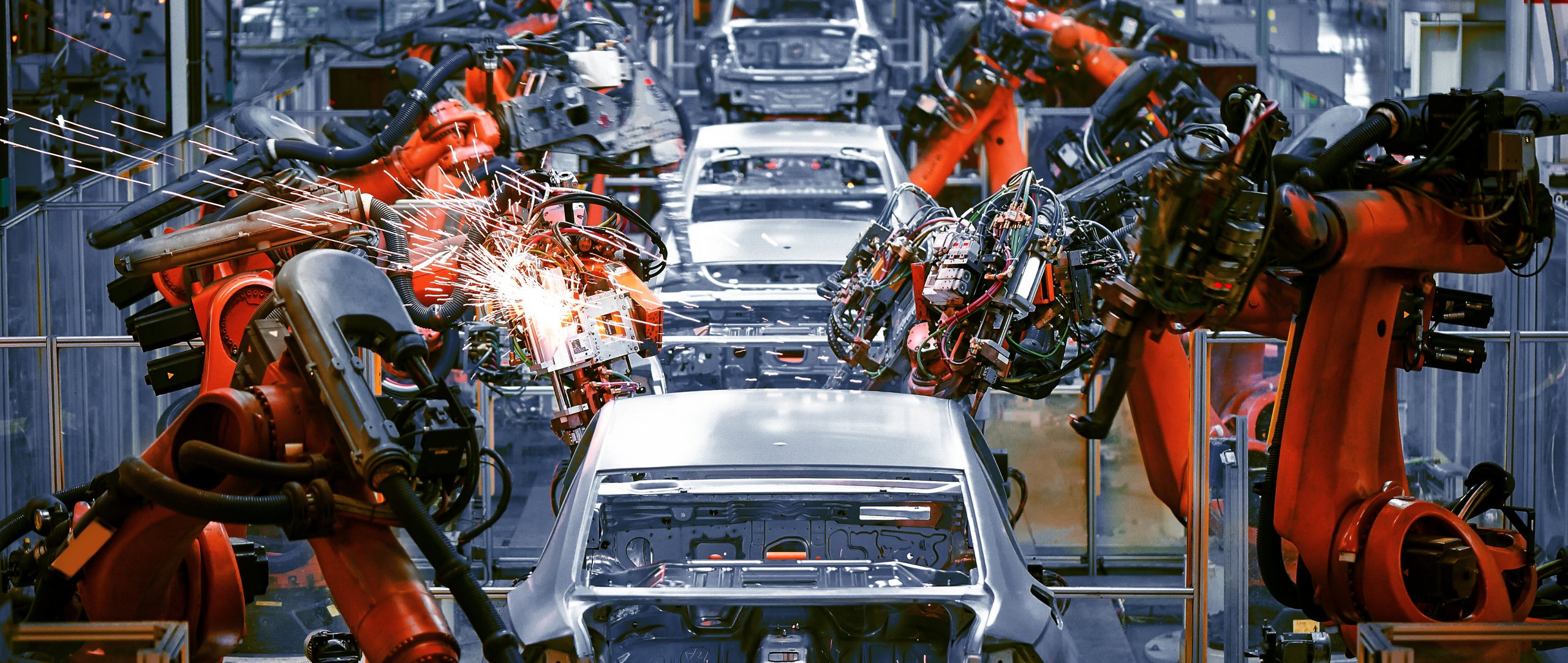
Traditionally, and according to Dictionary.com, manufacturing refers to making goods on a large scale. But that isn’t always necessarily the case. Manufacturing encompasses not only factories but also the butcher, the baker, and the candlestick maker.
This means that manufacturing products can be mass-produced or customized as one-of-a-kind items.
Regardless of the manufacturing process, once a final product finishes production, it’s sold to a business or directly to a consumer. Normally, manufacturers would sell their wares through a wholesaler. But, if you’re a small business manufacturer, this can be extremely counter-productive and expensive since a wholesaler is likely to buy in bulk and have their own fees for selling your wares.
What does that mean? Many forward-thinking manufacturers are cutting out the middleman — nothing personal middleman. It’s just business.
If this is a move that you would consider making with your business, then you’ll be glad to know that getting set up and selling independently nowadays it’s pretty straightforward — especially with the emergence of e-commerce websites such as BigCommerce, WooCommerce, and Shopify.
The manufacturing industry is constantly expanding, and so are the methods of getting your products in front of buyers.
Using your wits, you can seize this opportunity because, as demand increases for skilled workers and customers seek bespoke options on their products, it’s quickly becoming a profitable market to start operating within. However, demand is one thing. If you can’t efficiently organize and maintain your business, you won’t be able to tap into the potential this market offers and risk going under.
Now that we know what is manufacturing, let’s see if small workshops have any business in the sector or if manufacturing is only for large enterprises.
Small scale manufacturers
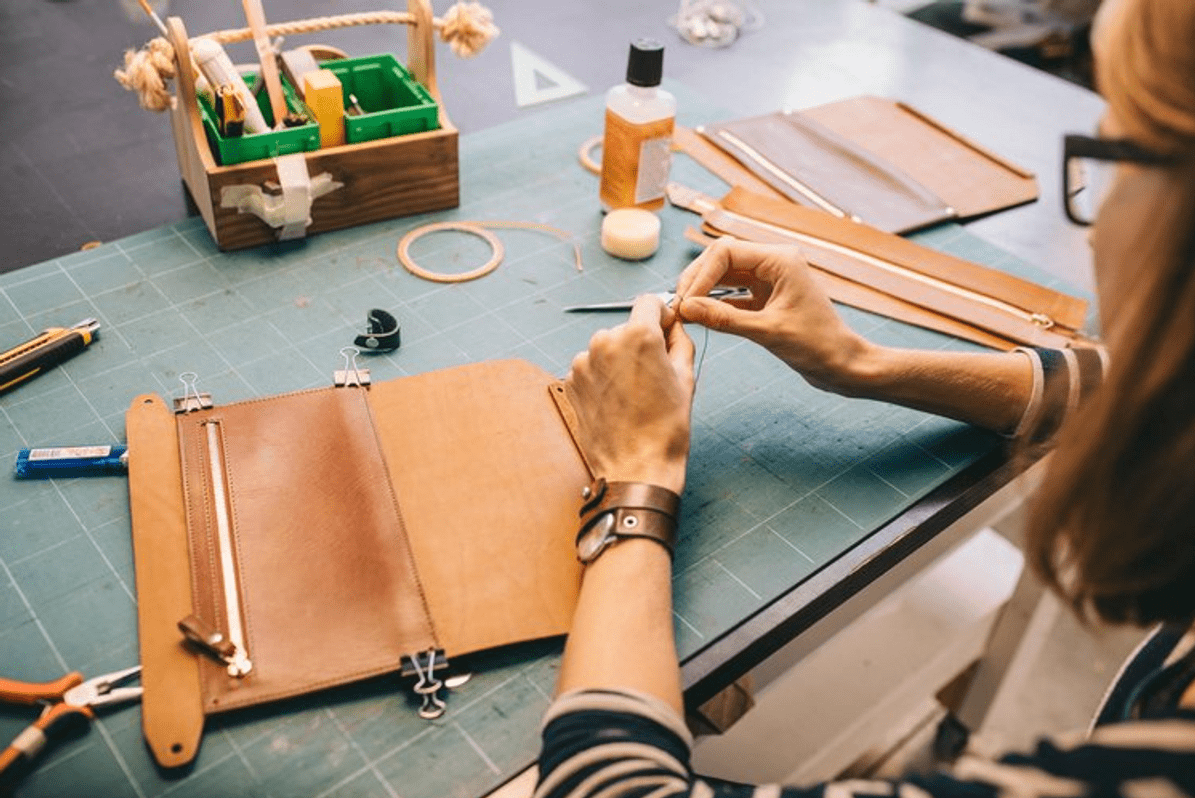
In September 2022, there were a total of 12.8 million manufacturing jobs in the US alone. Manufacturing makes up 8.2% of the total workforce in the United States.
When people think about manufacturing, they usually picture large factories, warehouses, heavy machinery, and the like. But you don’t need to be an industrial powerhouse to produce products. Maybe you’re a baker with a small local business who makes customized cakes for special occasions. You can corner the market by designing personalized treats for your customers, as opposed to them just getting a generic pumpkin pie from the supermarket that some large-scale, faceless manufacturer produced.
That being said, there’s a reason that a large-scale business can produce such quantities of their cakes. Having an assembly line as a manufacturing process is a viable option for you, only if there is demand for your pies and your available resources can cope with that method. If this surprises you, maybe you have a hobby that can make you money, but you just never realized it.
Do small manufacturers earn megabucks?
Honestly, it’s difficult to say just because of the industry’s size — it’s hard to quantify that information. Certainly, as a whole, the industry has a lot of potential for someone to make a decent living because, in 2021, manufacturing contributed $2.3 trillion to the economy. But, obviously, you can imagine that if you’re mining coal, your profits are going to be significantly higher than someone who produces tortillas.
IRS figures show that, in 2008, the average revenue of a sole proprietorship ranged from approximately $11.9 thousand for unclassified establishments to $1.1 million for coal mines.
All this being said, in 2017, the average manufacturing worker in the United States earned $84,832 annually. Or, if you have the time, you could look across each sub-sector to get a better understanding of the potential for earning money in that field. For example, we could look at the fashion industry, which in 2015 was calculated to be a 1.2 trillion global industry, with more than $250 billion spent annually on fashion in the United States. Around 17,000 fashion designers are operating in the industry, each earning, on average, $73,600.
The money is out there, it’s just figuring out how to tap into it.
What is lean manufacturing?
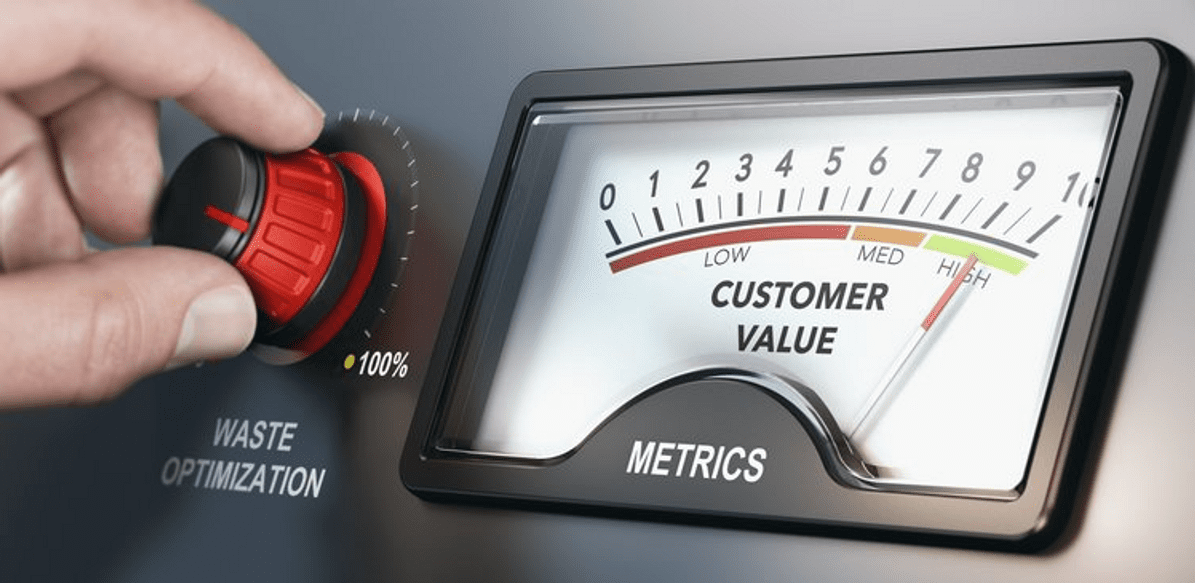
Lean manufacturing is the technique of eliminating waste from the manufacturing process and giving the customer the biggest bang for their buck. It’s important to note that lean manufacturing does not make any sacrifices when it comes to quality. The production quality control checklist is strictly followed, so there is no cutting corners.
The concept originated from Japan, and the idea was that by eliminating muda (futility, uselessness, wastefulness) from your business, the value of your products is increased due to it being made strictly for the customers’ requirements. Those who practice lean manufacturing will look to remove waste from their business by examining the seven types of mudas:
- Transport — Moving products costs money and adds no value
- Inventory — Products take up space, need to be moved, and can become damaged
- Motion — Getting to work or moving equipment around wastes time
- Waiting — Waiting for repairs or waiting for a delivery of material
- Overproduction — Making too much product and/or making it too soon
- Overprocessing — Using a machine or methods that take longer and don’t add value
- Defects — Products being replaced, repaired, or worse, recalled
Lean manufacturing can be achieved by viewing your production from the consumer’s point of view. Lean manufacturing allows you to identify where your production methods can improve. You will always be examining and changing approaches to your process as maybe you’re not operating at your most efficient or an external factor has affected your business, and you need to adapt to survive.
Out of the thousands of examples of a manufacturing business, let’s take Toyota Motor Corporation, which took a make-to-order approach and continuously evaluated its production.
Being more analytical of its manufacturing processes meant it could survive, even in a post-war Japanese economy, by adapting to different trends in demand and the changing climate of the economy. You may not be operating on the same scale as Toyota, but applying lean manufacturing means that you can perform at your most efficient. This increases your company’s chances to grow instead of fizzling away from poor management habits.
Types of manufacturing businesses
While there are many types of manufacturing companies, here are the 20 most popular sectors today:
- Food manufacturing
- Beverage and tobacco products
- Chemical manufacturing
- Electronic equipment
- Textile mills
- Textile product mills
- Apparel manufacturing
- Leather and allied product manufacturing
- Wood products
- Paper manufacturing
- Printing and related support activities
- Petroleum and coal products
- Plastics and rubber products
- Nonmetallic mineral products
- Primary metal manufacturing
- Fabricated metal products
- Appliance and component manufacturing
- Transportation equipment
- Furniture and related products
- Miscellaneous manufacturing
If you’re surprised by this list, let’s look at how the North American Industry Classification System determines if a business belongs in the manufacturing sector:
“The Manufacturing sector comprises establishments engaged in the mechanical, physical, or chemical transformation of materials, substances, or components into new products.
Establishments in the Manufacturing sector are often described as plants, factories, or mills and characteristically use power-driven machines and materials-handling equipment. However, establishments that transform materials or substances into new products by hand or in the worker’s home and those engaged in selling to the general public products made on the same premises from which they are sold, such as bakeries, candy stores, and custom tailors, may also be included in this sector.
Manufacturing establishments may process materials or may contract with other establishments to process their materials for them. Both types of establishments are included in manufacturing.”
These sub-sectors can be broken down even further as one will encompass companies that use different manufacturing processes. Take, for example, food manufacturing. This covers:
- Animal food manufacturing
- Grain and oilseed milling
- Sugar and confectionery product manufacturing
- Fruit and vegetable preserving and specialty food manufacturing
- Dairy product manufacturing
- Animal slaughtering and processing
- Seafood product preparation
- Packaging, bakeries, and tortilla manufacturing
- Other food manufacturing
Extensive, wouldn’t you agree?
This should cover up any misunderstandings that you may have and give you a better scope of the diversity of the industry. You can explore these categories yourself at the Bureau of Labor Statistics as they will also have the relevant sic codes that you need when incorporating your business (in the USA, that is).
Types of manufacturers and workflows
There are several ways your business can operate when completing the manufacturing of your products. Here are five different types of manufacturing processes that you could adopt:
- Repetitive manufacturing — Uses an assembly or a production line running 24/7 and producing identical items at a high output rate. This type of manufacturing is typically used for products that are in high demand or have a long shelf life, like automobiles or electronics
- Discrete manufacturing — Utilizes an assembly or a production line. However, the difference is products will vary, requiring operations to change to compensate
- Job shop manufacturing — Job shop manufacturing makes use of production areas. This process creates smaller batches that can be manufactured at different and more desirable rates
- Continuous manufacturing — Continuous manufacturing is the same as repetitive manufacturing, using a 24/7 production line. However, its production materials are not countable, like gases, liquids, and chemicals. In mining, the material can be more granule. Instead of assembling the final products, formulas are used, like in the case of making rubber
- Batch manufacturing — The batch manufacturing process produces items in batches to meet customer demand. This can be met with one batch, several, or the batch process can be continuous in nature
MTS, MTO, and ATO
Obviously, with the spectrum of the industry being as large as it is, you can probably imagine that there is more than one way in which a business will organize and manufacture its items.
A lot of these processes or inventory management techniques will depend on the type of business you run and what you find most beneficial. Firstly, how you prepare your product for your customers will depend on your production workflow. Are your products:
- Make-to-stock (MTS)
- Make-to-order (MTO)
- Assemble-to-order (ATO)
Make-to-stock (MTS)
Make-to-stock inventory will be products created based on your company’s forecasts and customer demand. The idea is to have products in stock in preparation for a customer’s order. But this can run the risk of not meeting demands by either producing too much or not enough products. This option doesn’t leave much room for customizing customers’ products.
Make-to-order (MTO)
Make-to-order inventory means that instead of stocking products, a company will begin production on an item once a manufacturing order is received. This technique aims to maximize storage space to avoid ending up with dead stock. This allows for greater personalization. Although, a downside is that a spike in demand could strain your business while trying to fulfill orders.
Assemble-to-order (ATO)
Assemble-to-order means the components to make the final finished product are stocked and ready for assembly when a sales order is received. This means the products might have some customizability, but not to the same extent as make-to-order.
Once you’ve figured out the ideal inventory management method, you will need good manufacturing inventory software that provides you with real-time visibility, freeing up your resources to stay focused on manufacturing your products.
For now, we’re going to investigate the inner workings of a manufacturing business, seeing how they operate and highlighting any areas that will be useful for you.
The narrative of a manufacturer
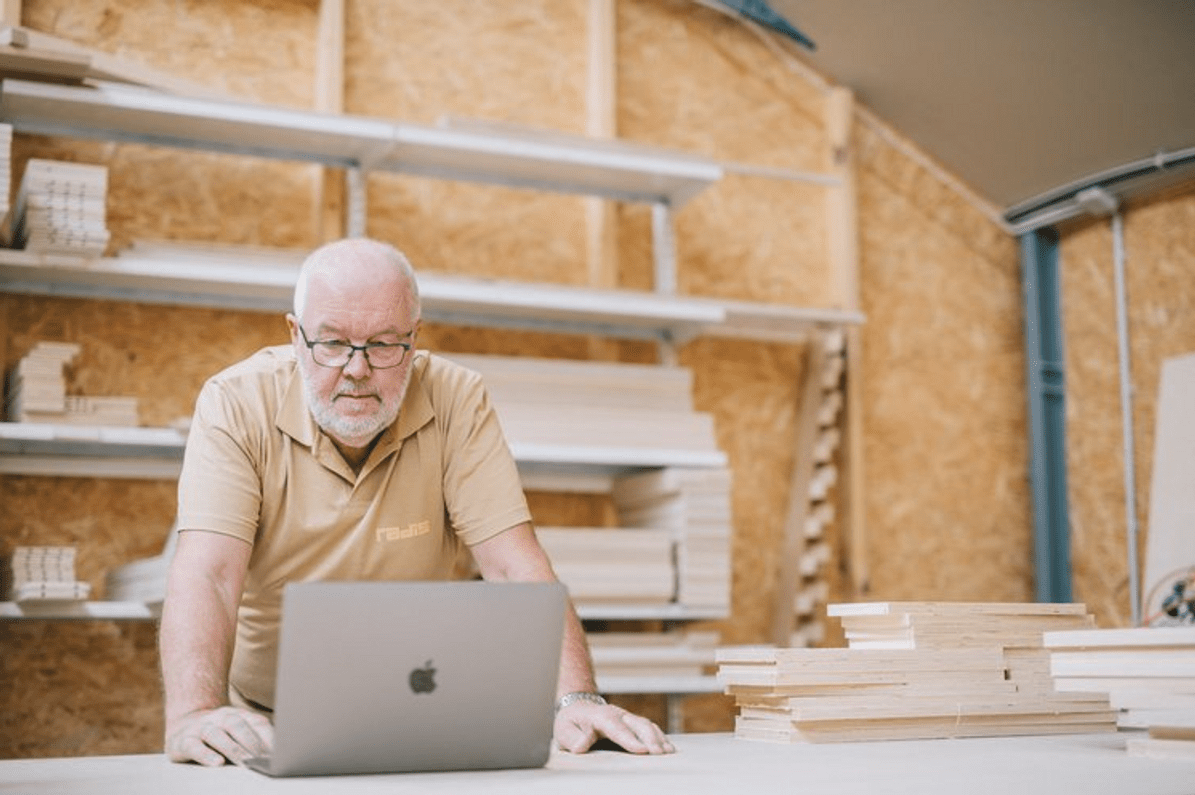
Now that you have a better understanding of the industry and may feel more confident to pursue your fantasy of becoming a manufacturer, where should you start? Or perhaps you’ve already started, but something doesn’t appear to be working, and you just can’t figure out where the issue hides.
In this section, we’ll explain what a manufacturer must do, consider, and, more importantly, how to prepare if they wish to survive in this highly-competitive industry. We’ll also try to achieve this in a logical order, from the very beginning (your idea) to selling your goods.
Prototyping
You have your idea, and even though you’d love to instantly invest everything you have to get this out into the public sphere, you simply can’t.
Maybe it’d be a good idea to attend showrooms and conventions to see if anyone is manufacturing a similar product to you. It might be that you could need to contract a manufacturer, and this would be a good place to look if you’re unable to create a prototype yourself. Either way, as soon as you have the prototype, test, improve, test, improve, test, improve. Don’t forget to receive invaluable feedback from others.
If you’re onto a revolutionary invention, it might also be worth looking into securing a patent on your design.
Bill of materials
Once you have perfected your prototype and have a final product, you’ll be left with a bill of materials (BOM) which is essential for your manufacturing processes. A BOM is a list of raw materials, sub-assemblies, intermediate assemblies, sub-components, parts, and quantities needed to create your product. Depending on your products construction requirements, you’ll be using one of three types of BOMs:
- Modular BOMs — Used for products that require completion through sub-assemblies
- Configurable BOMs — Used in manufacturing industries that have multiple options with customizable goods
- Multilevel BOMs — Contain lists of the components, assemblies, and parts required to make a product. Sometimes referred to as a top-down method as the relation between the finished product and its parts is highlighted
The BOM, just like the prototype, can also go through reiterations as you perfect the process of manufacturing your product.
Routing manufacturing
So you’ve finished your bill of materials. If your items are customizable and have tons of different variations, you’ve probably realized that it will be complicated to manufacture these products since they will be traveling all over the shop floor.
Routing manufacturing is the route or map your products will follow around your shop floor while passing through each process. Your routing manufacturing will depend on what type of production workflow you follow. Once you’ve completed your routings, you’re going to be able to identify the tasks which need to be completed, the order in which those tasks will need to be completed, the processes the item will go through, and the work centers which they will pass through.
Routing — Lists of tasks needed for a manufacturing process that is used in making a product.
Manufacturing cost
From your BOM, you’ll be able to calculate your manufacturing costs (MC). The sooner you calculate this, the faster you can get yourself and your customers a fairer price. It’s worth keeping in mind that there are many different costing methods available and you should consider your specific circumstances when choosing the one that fits best.
The manufacturing cost is determined by the amount of resources spent on creating your wares. This is figured out by looking at two types of expenses. Let’s take a closer look at both of these.
Direct manufacturing cost
These are the direct and variable costs associated with making your product. These include:
- Raw materials
- Labour
- Costs of running machinery
- Consumables (fasteners, glue, paint, etc.)
Indirect manufacturing cost
These are the fixed costs associated with running your business that don’t directly relate to making your product. These can be:
- Utility bills
- Salary of the non-manufacturing staff
- Maintenance and repair costs of machinery
- Factory rent
To calculate your manufacturing costs, you will need to look at the three types of costs:
- Direct materials
- Direct labor
- Manufacturing overheads
Your manufacturing cost formula should look something like this:
MC = Raw Materials + Direct Labor + Allocated Manufacturing Overhead
Figuring out your manufacturing cost is essential to ensure you won’t sell your products at a loss.
What are manufacturing overheads?
The manufacturing overhead costs are indirect factory-related expenses incurred from products being manufactured. Examples of manufacturing overheads are the costs for using machinery during production, rent and property taxes of the business’s premises, workers’ salaries and wages, and the factory’s utilities.
However, it should quickly be mentioned that this does not include administrative costs, salaries, and debts.
Manufacturing overheads are also known as factory overhead, production overhead, and factory burden. It is mandatory to assign manufacturing overhead to the cost of products to report their cost of goods sold and their cost within the inventory asset account (reported on the balance sheet).
Manufacturing order (MO)
You know how to build your product. You’ve completed your BOM and know exactly how much the manufacturing cost will be. Now it’s time to look at your manufacturing order.
Depending on how you prepare your products (MTS, MTO, or ATO), the manufacturing order will come through either due to stock levels or from a sales order and will be prepared as the manufacturing instructions. Manufacturing orders can be classified into an internal order (to be manufactured by the company itself) and a subcontract order (to be manufactured by subcontractors).
But what happens if you create a manufacturing order but don’t have the materials to fulfill the order? The next trick is to stay ahead of your manufacturing orders so as not to create delays and keep your customers waiting.
Throughput time
There’s another metric very similar to manufacturing lead time that can be valuable to the maker. It’s known as throughput time and basically tracks how long it takes to get a product made from when the manufacturing order comes in, to the second it’s ready in the stock room.
lead The main difference with lead time is that it doesn’t include any of the waiting time before manufacturing or the delivery times after it. But getting intimate with this number will let you know how well you’re doing on the production side and even give you some ideas on how to improve efficiency too! Here’s the basic formula to get you started:
Throughput time = The time taken to complete manufacturing / each unit of product
When calculating your throughput time, you should be mindful of the following:
- Processes
- Inspection
- Moving
- Queuing
These all affect how long it will take to manufacture an item.
Manufacturing lead time
The manufacturing lead time is the calculation of the time from when the sales order comes in up until its creation. You can calculate your manufacturing lead time by adding together the different production times for your product:
Order preparation time + queue time + setup time + run time + move time + inspection time + put-away time
The method by which you forecast your lead time will depend on if you’re an MTO or MTS business:
- MTO — Creating manufacturing orders for production and shipment
- MTS — Creating manufacturing orders for production, receiving sales orders, and inventory stock
So, you have a plan of attack formulated, but now it’s time for the execution.
Manufacturing floor-level control
The manufacturing floor-level control is the prioritized task list for every production employee and production line. Consider it like a manager role, where they’ll need to schedule, monitor workflow, and delegate responsibilities to employees. How you implement this is up to you, however, you’ll want to use a system where workers can easily access a schedule calendar so they know exactly where they need to be and what needs to be done.
You can go that extra step by looking into making this easier with shop floor control software.
Manufacturing software
There are multiple ways you can handle your manufacturing floor-level control. To this day, one very commonly used tactic is scheduling timetables through Excel. Which takes time, and resources and, believe it or not, will cost your business money.
Implementing lean manufacturing software means managing your inventory, production processes, and sales orders from one easy-to-use platform. Every little detail in the software has been designed with the precise needs of the growing business in mind.
Master production scheduling
Your master production schedule will inform you what you need to produce, the quantity, the deadlines, everything related to production, and even production lead time. It is crucial to have a master production schedule if you want your business to operate properly. Also, it’s a good habit to instill early as it will help when your business scales up.
Other master production schedule objectives are:
- Making your demand flow smoother
- Keeping your lead-time low
- Standardizing communication across your business
- Helping you to prioritize workloads
- Keeping production stable
- Generating workable plans for your manufacturing orders
- Assisting in making an accurate purchase and transfer orders
You can figure out your master production schedule by a product list, variation sub-lists for each product, and production quantities. The sooner you design your manufacturing production schedule, the quicker you can optimize your business workflow and take advantage of the benefits. You can make this job a lot easier by adopting production scheduling software.
Supply chain management
Supply chain management is simply getting your product from Point A to Point B. A supply chain manager is concerned with designing, planning, executing, controlling, and monitoring the supply chain activities to create net value, building a competitive infrastructure, leveraging worldwide logistics, synchronizing supply with demand, and measuring performance globally. Their other responsibilities include negotiating with suppliers to get materials, shipment of materials as effectively as possible, and getting the product on the store shelves as quickly as possible.
Essentially, they make, source, and dispatch products.
If you’re a small business manufacturer, you’re likely doing this yourself, but at least now you know the term of what you’re doing! However, this could be a role for one or more individuals when your business expands into an empire. We hope you’re still with us because we’ll move on to the next thing you should consider, which will help you ensure you don’t under or overprice yourself.
Cost of goods sold (COGS)
The cost of goods sold (COGS) examines how much it costs your business to sell inventory over a given period of time. However, there’s no set time when a business should make these calculations. The frequency is completely up to you. However, it is essential for you to look into your COGS as it can be used in reporting your business income tax and, most importantly, studying your company’s expenses.
When you are figuring out your COGS, you want to include income and expenses.
Income = The sale income from manufactured goods and the sale income from any resold goods
Expenses = Raw materials and direct labor costs
Your formula should look something like this:
COGS = (Beginning Inventory + Additional Inventory) – Ending Inventory
Improve your business with manufacturing software
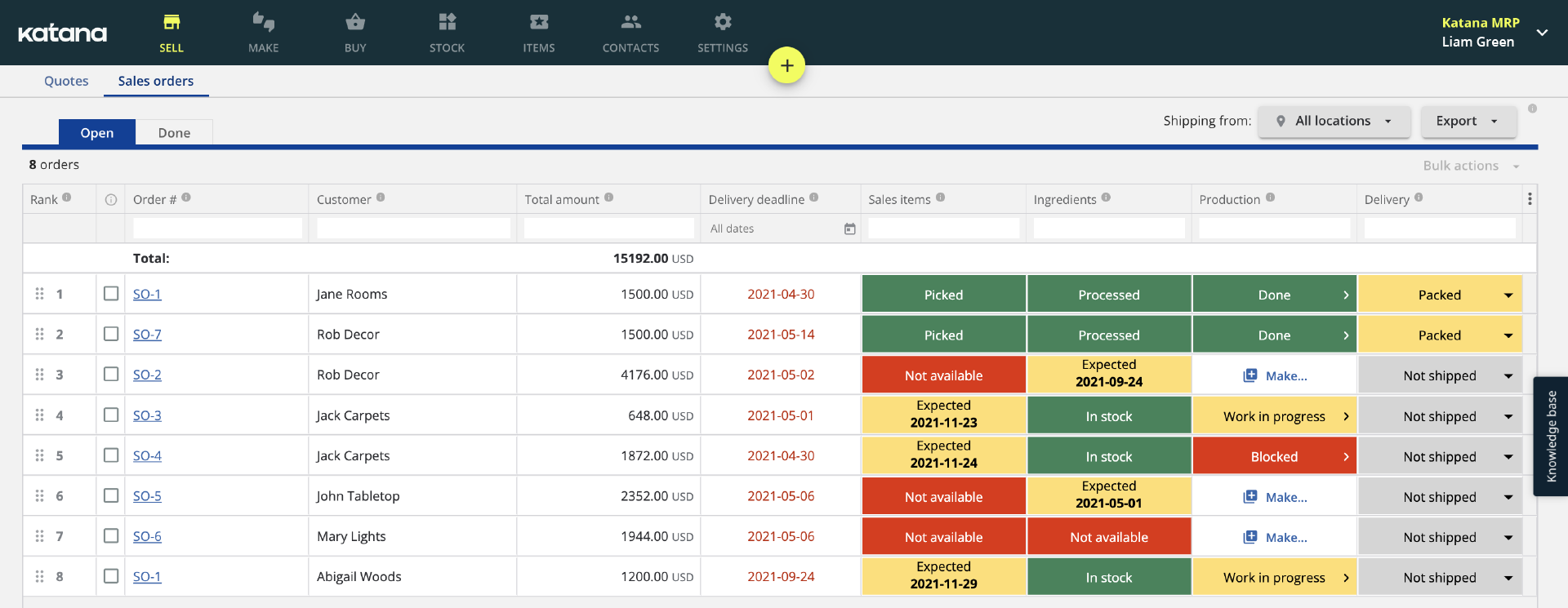
Now that you’ve witnessed how much work one would have to do when running their business, we imagine your head is probably spinning. But not to worry, Katana’s cloud manufacturing software can assist you with all of the points mentioned in this guide. Let’s look at how Katana can help you streamline your business.
Means of managing inventory
Real-time inventory control and optimization means you can check finished products and raw materials from one platform, and automated inventory transactions give you up-to-date information on the current inventory. With the inventory planning feature, you can ensure you’ll always stay in stock and keep your inventory levels optimal.
Storing your bill of materials
Katana has a page dedicated to your product’s recipes, including all possible variations, with as detailed a breakdown as you wish to specify when adding your own bill of materials (BOMs).
Calculating direct manufacturing costs
Katana keeps track of the moving average cost (MAC), making it easy to track your manufacturing costs based on your BOMs and production operations.
Calculating manufacturing lead time
Katana makes it easy to calculate manufacturing lead time by tracking the availability of required products to decide whether you need to make a manufacturing order or fulfill an order from product stock.
Production scheduling
Get a prioritized task list for every production line and employee with a real-time production status overview from the floor level.
Cost of goods sold (COGS)
Make accurate pricing decisions with Katana based on actual product margins and save your sales history and receipts within the platform.
Single source of truth
Besides the robust set of built-in tools, Katana also connects with the most popular business platforms out there. This means you can connect your accounting tools, CRM software, e-commerce platforms, etc., to Katana and keep everything synced across platforms.
Congratulations! You’ve finally reached the end of this comprehensive guide and have all the knowledge you need to successfully run your manufacturing business. Now, all you need are the tools that allow you to scale without issues while keeping everything running smoothly. Request a demo to see Katana’s enterprise manufacturing software and take your business to the next level.
Table of contents
Manufacturing guide
More on manufacturing
Get visibility over your sales and stock
Wave goodbye to uncertainty by using Katana Cloud Inventory for total inventory control
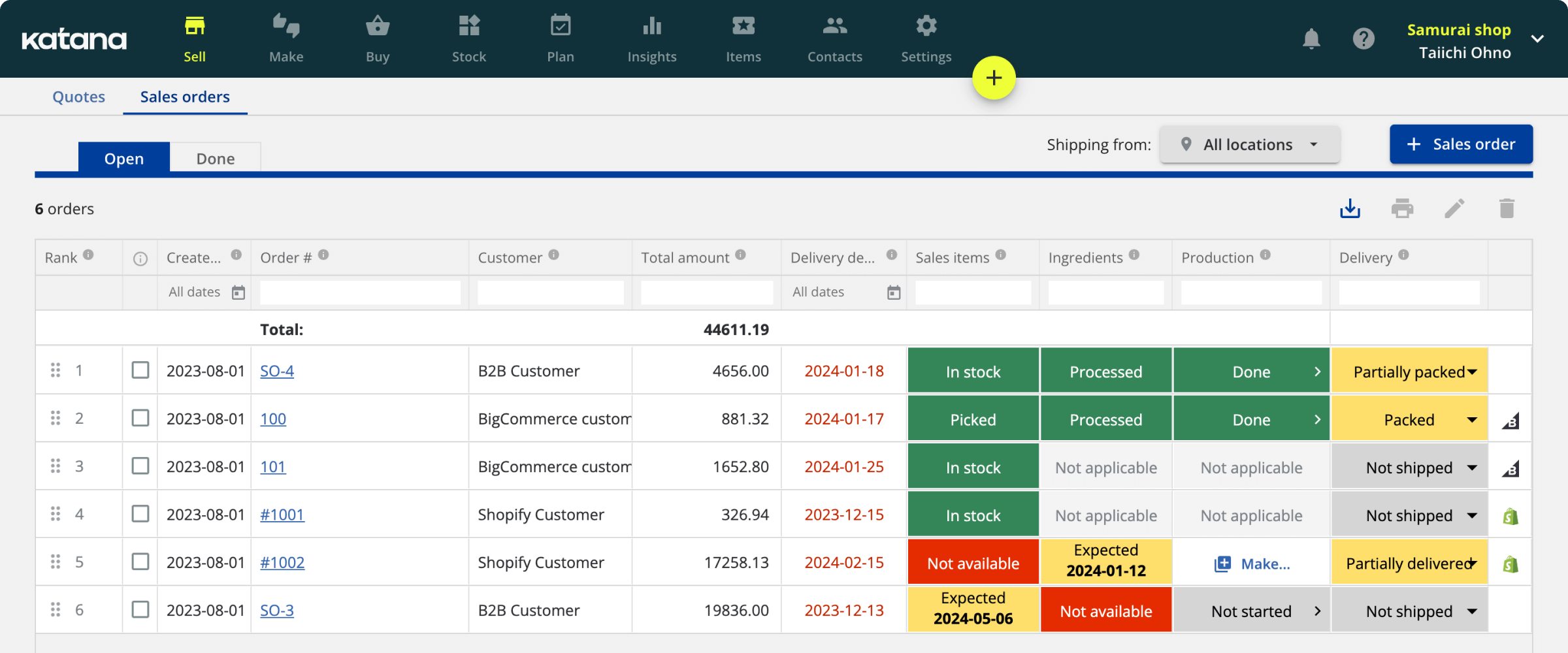