Production quality control checklist for manufacturing
In this competitive world, keeping your business standing out is vital. While excellent marketing strategies can go a long way, it is still your products that help you make a name for yourself.
Whether you produce your products from scratch or have supply partners — issues and defects should be avoided or eliminated as soon as possible. That’s where a manufacturing quality control checklist comes to the rescue.
Luckily for you, we have put together a detailed description of what a quality control checklist should entail and how it will benefit your business.
What is a manufacturing quality control checklist?
A quality control checklist for manufacturing includes all the requirements for a product, both visual and physical.
It is a beneficial tool to ensure all parties are on the same page about the demands for the parts, materials, and final product. It outlines the standards your suppliers and manufacturers should meet and describes the “ideal” product that your customer expects from you. You can think of a quality control checklist as guidelines for all teams to follow when making and selling your products. It streamlines the cooperation process and helps eliminate any possible errors occurring along your entire manufacturing workflow.
A production quality control checklist for manufacturing can entail all product features, including (but not limited to):
- Size
- Color
- Functionality
- Branding
- Packaging
- Defects
- Manufacturing flaws
Why does your business need a quality control checklist?
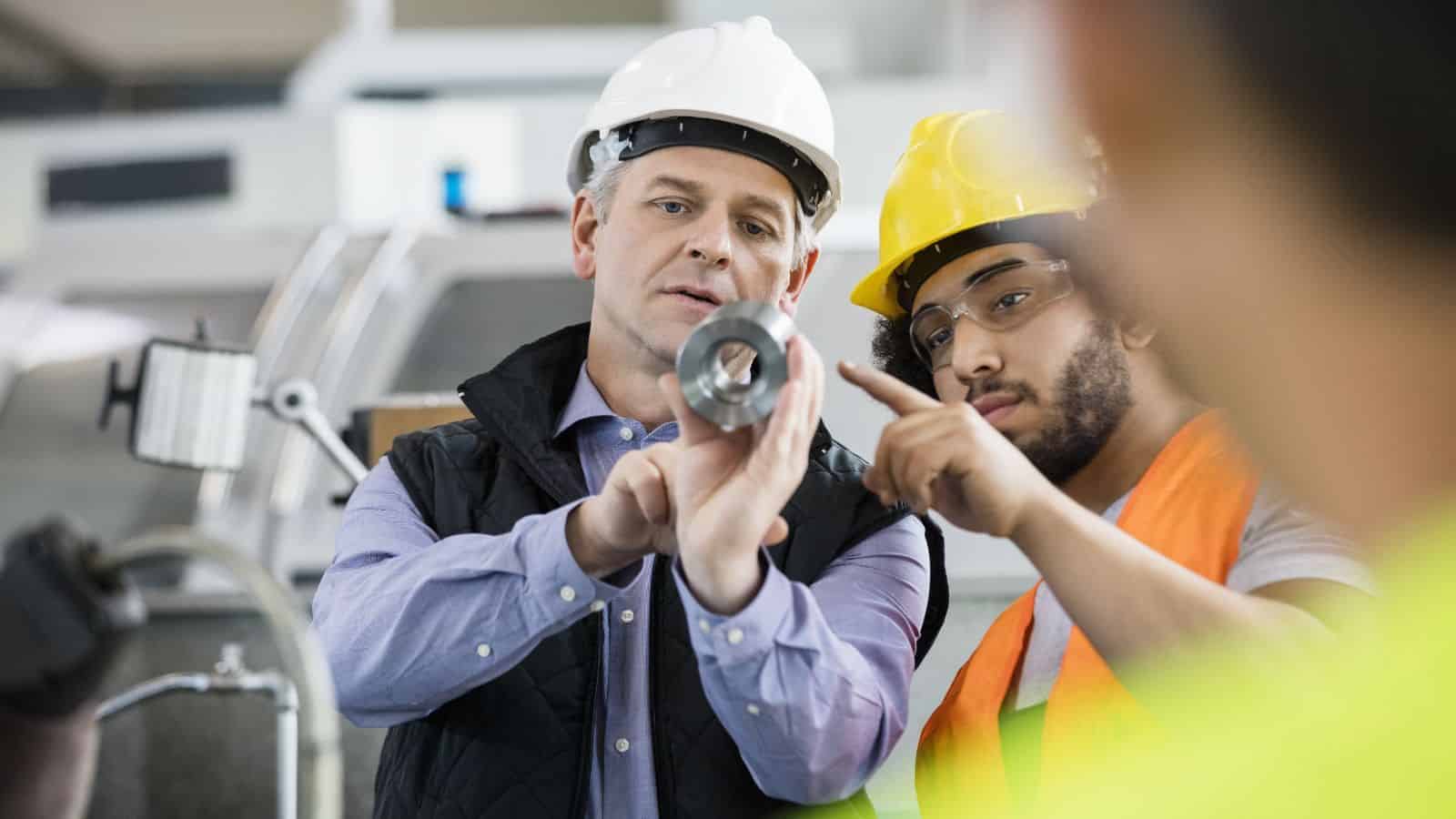
Imagine a situation where your supplier delivers parts with defects, some are visual while others have also left the materials unfit for use.
What options does a manufacturer have in this instance? Well, they might have to order new pieces or even fix the existing ones to make them fit for purpose. Either way, this serves only to raise the costs for the manufacturer as they now have to pay more in time and money. This scenario could have easily been avoided if they’d had a quality control checklist in place, so all parties understood what was expected with the delivery.
Whether your business deals with clothes, pet toys, or custom alarm clocks, one thing is for sure – you attract customers by being the best at what you do. A client base does not come easy, and you must ensure your business is delivering high-quality services to support and grow it.
Using a manufacturing quality control checklist can help you streamline two essential processes.
1. Reviewing of incoming materials and parts
Any deviations can cost you time, money, and potentially business. Mark down all your requirements as precisely as possible so your suppliers also know what is allowed and what is not.
What looks like a minor defect to the supplier can take you a long time to fix or might eventually prove to be unusable. If you receive a whole shipment of defective items, your manufacturing might fall behind, and it will start impacting not only production but also sales.
2. Inspection of finished products
A QA team should review every batch of products, ensuring the final product matches the design.
Your clients expect and deserve a certain level of quality, so before shipping out an order, verify that all items meet the required standards and show your business in the best light. Remember:
Free quality control checklist for manufacturing
Download a production quality control checklist to improve communication and reduce delays while maintaining a high standard for your operations.
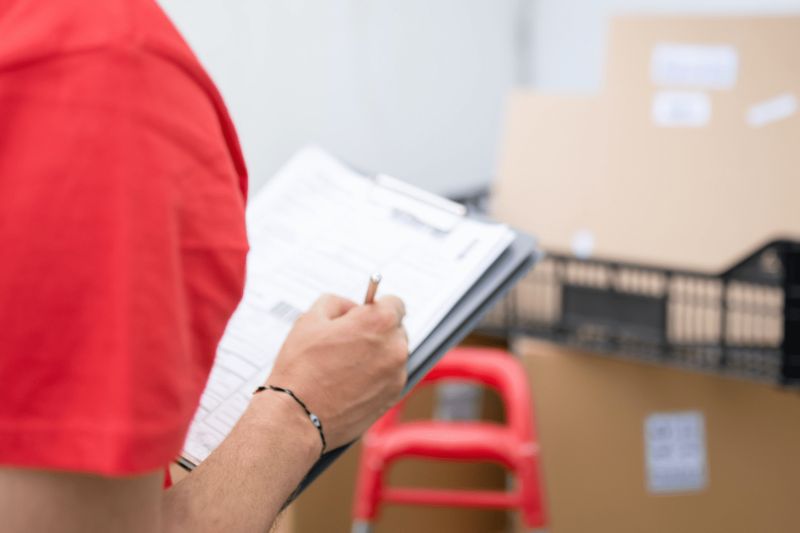
What are the 5 essentials of a quality control checklist for manufacturing?
When putting together a manufacturing quality control checklist, there are a few points to keep in mind.
The main goal of this type of list is to avoid as many mistakes and points of miscommunication as possible. Keep in mind that it needs to be specific and elaborate while also understandable for all parties. The five essentials are:
- Agreed upon requirements
- Collaboration between all parties
- Testing and inspections
- Proper documentation of defects
- Continuous quality checks
What exactly do these points mean?
1. Agreed upon requirements
All parties must understand the requirements for the product.
A slight misunderstanding can become unnecessarily expensive and time-consuming. Therefore, make note of all requirements as precisely as possible — including color codes, dimensions, weight, materials, and anything else you think is relevant. It may sound like tedious work to write every little detail down, but it will save you a lot of hassle and headaches in the long run, making it definitely worth it!
Your suppliers are not mind readers and “make sure it looks good and feels good” can mean vastly different things to different people or parties.
Once all the requirements have been written down, and all teams are aware of the demands they must meet, communication and sticking to the guidelines becomes much easier.
2. Collaboration between all parties
As always, communication is key!
It’s always easier preventing issues rather than fixing them, which is why all parties must be on the same page about standards. From supplier to manufacturing to the quality check team — if everyone works towards the same end goal and meets the exact requirements, this helps avoid unnecessary issues overall.
A minor flaw in the supplier’s eyes may be a significant issue for production. A manufacturing defect might end up annoying a customer who finds it visually unappealing or cheap.
Remember, perceived quality leads to purchase, so make sure your product not only performs well but also looks good.
3. Testing and inspections
It is vital that your product meets every single requirement for yourself and the customer.
That is why a thorough evaluation of the components and products must be conducted before sending it to the client. While visual features can be inspected mainly by looking at the piece, extensive testing is still necessary.
Testing and inspection in the real world
Imagine that your business produces locks for front doors.
Locking and unlocking them 1000 times may work fine with zero issues at all. However, weather conditions change. The lock will have to endure temperature changes from 20° in summer to -15° in winter or be rained on for a week straight. Consider different weather and environmental conditions when conducting tests on your product, depending on the functionality and type of items you make.
4. Proper documentation of defects
A detailed report of possible defects can help your team identify which are minor and which are major.
Some minor flaws can be ignored. They do not affect the end-user or the product’s functionality. As long as the item’s quality is not impacted, the customer might not even be aware of any issues. The problem arises once the defects are major or even critical, causing the elements to:
- Be visually unappealing, such as dents or faulty mold injections
- Physically prohibit further production due to using a defective part
- Render the final product unusable
Trust but verify
Let us imagine that your company produces organic orange juice.
Your supplier sends you a shipment of bottle caps that, for some reason, are smaller than you previously agreed upon. You will be unable to use them as they do not fit on the bottle. Visually you might not even notice the difference, but once it is time to use the caps, they will end up being completely useless, stopping production, stopping sales, and stopping everything!
5. Continuous quality checks
Just because you created a perfect batch of products for sale doesn’t mean you can rest on your laurels and start easily making money.
Once you’ve delivered superior quality, your clients will keep expecting it. Make a habit out of regular inspections and randomized testing. This way, you may find room for improvement or fix accidental hiccups before they become customer complaints.
People say, “cheap is expensive,” and it’s almost always related to the quality of the products they buy. Why spend money on new boots twice a year if you can buy a pair that will last you for a few years or more? Now, it is your job as a business to make sure the boots will actually last that long.
How do you ensure quality control in manufacturing?
Many businesses have assigned quality control officers (QC officers) or inspectors within the company who conduct the tests and inspections.
These people are deeply involved in:
- Creating checklists
- Developing quality assurance procedures
- Performing audits
- Running tests and assessments
The first thing that QC officers need to figure out is how to run inspections that accurately represent the quality of the whole batch. Testing too many samples wastes time and might damage too many items in the process. Not testing enough might give an inaccurate representation of the quality, and significant issues may be overlooked.
Another element that QC officers need to cover is the packaging.
While most businesses rely on a shipping company to deliver their products, it is still their responsibility to ensure that the items arrive at the client’s doorstep in one piece. Packaging quality includes characteristics such as material, labels, method, etc. While just a piece of paper, labels can make or break if the package is delivered or even shipped to the customer.
Quality control officers also classify defects and decide which are critical, major, or minor issues.
For example, untrimmed threads in an article of clothing can be classified as a minor issue. At the same time, if you forget a needle in the fabric during production — this is critical and should be avoided at all costs. Classification of defects can also help plan solutions to issues and develop ways to prevent them from occurring in the first place.
Inspections are not only essential to guarantee high standards in the visual appearance and functionality of the product. But, sometimes they also ensure that the product is safe to use. Children’s toys are a type of product that requires extensive testing to eliminate any life hazards, including suffocation or swallowing of tiny objects.
Tests may reveal unexpected results
In 2013, British supermarket chain Iceland tested positive for horse meat in some of their beef products. CEO of Iceland, Malcolm Walker, responded to the scandal. “Did we test for horse? No, but we haven’t tested for dog or cat either. I mean, there might be dog or cat. You can’t test for everything.”
How does a manufacturing quality control checklist help your business?
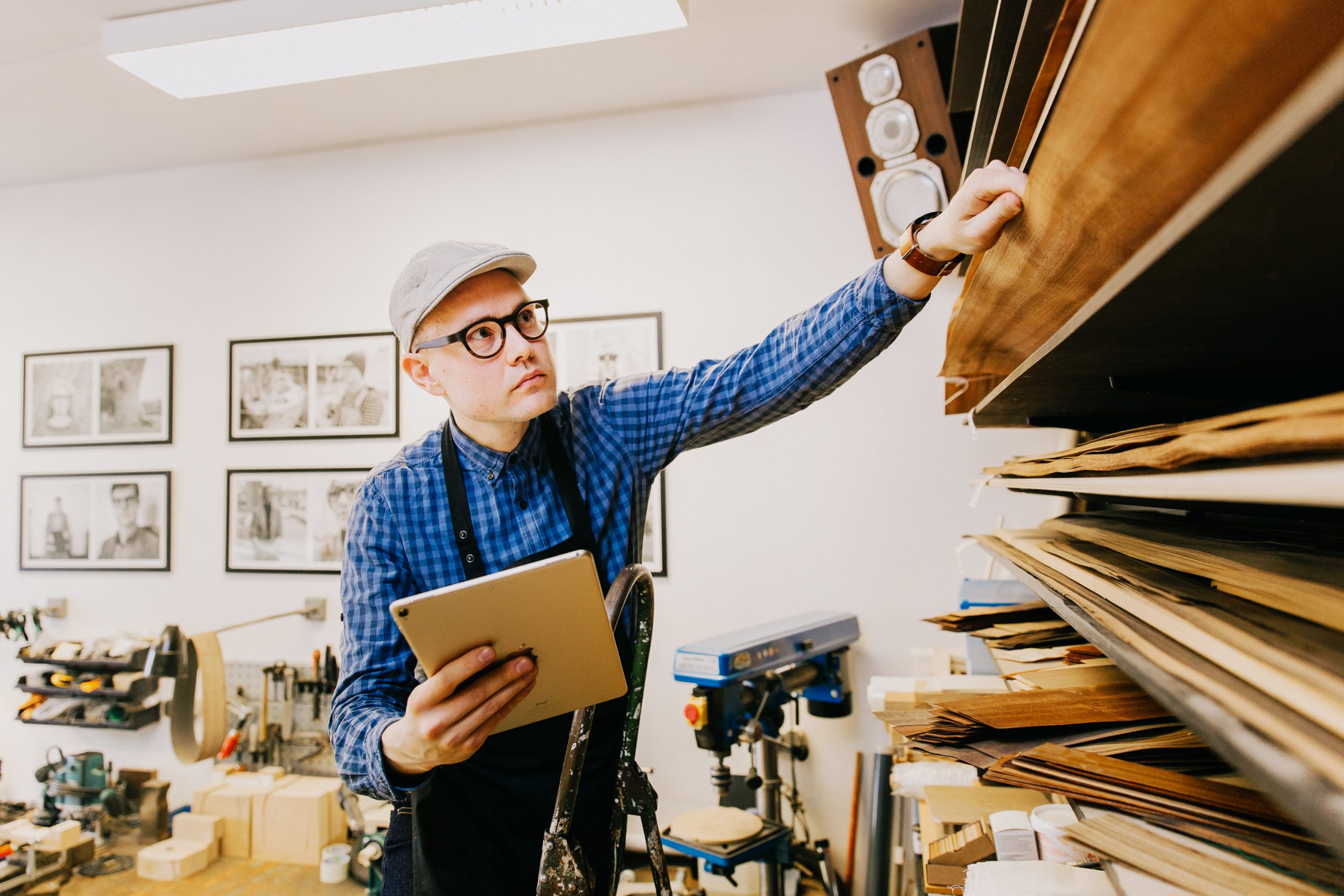
By putting together a quality control checklist for manufacturing, you are essentially setting your team up for success.
There will be no guessing or “winging it” because all requirements have been specifically outlined in a way that all parties understand. The same checklist can be used in various stages of manufacturing:
- Product planning — it is easier to plan and design a product when you know which criteria it must meet. All teams can start managing their workload and tasks accordingly while still working towards the same end-goal
- Quality control — During the manufacturing period, a checklist helps all parties stay focused on what the final product must be like while acting as a guide for all involved teams
- Quality assurance — Using a manufacturing quality control checklist to visualize all the demands for the final product, the QA team can implement different strategies to streamline the quality check process. This includes different types of training, audits, inspection guides, etc.
- Product improvement — Once the final product is finished, it is time to reflect on it and find ways to improve it or implement new and additional features. As a result, you can offer your customers a way to improve or upgrade their product while keeping them loyal to your brand
How can Katana assist in the process?
While you are busy perfecting your product, streamlining workflows, getting teams to work together, and developing a quality control checklist for manufacturing — your business must keep going.
Instead of stressing about all the other things you need to do, let Katana cloud manufacturing software take care of your production processes, handle manufacturing tasks, and keep track of your inventory.
Katana has essential features that your business needs for implementing quality control:
Batch tracking
End-to-end traceability lets you track every item to its original batch, from purchasing to manufacturing to sales. This allows you to distribute food products from one batch across locations and, if necessary, trace items in case of a recall.
Operations management
Create Production operations and assign them for your operators to fulfill. You can change the status of operations, which will automatically also trigger inventory changes. It will streamline manufacturing and create transparency on time and money spent per product.
Shop Floor App
Creating tasks in the Shop Floor App helps plan and conduct inspections and tests. Not only do you have an overview of who and when completes a task, but you also see how much time it takes. This allows you to outline and optimize your future quality check process to identify where defects are occurring and eliminate them from production entirely.
Table of contents
Manufacturing guide
More guides from Katana
Get visibility over your sales and stock
Wave goodbye to uncertainty by using Katana Cloud Inventory for total inventory control
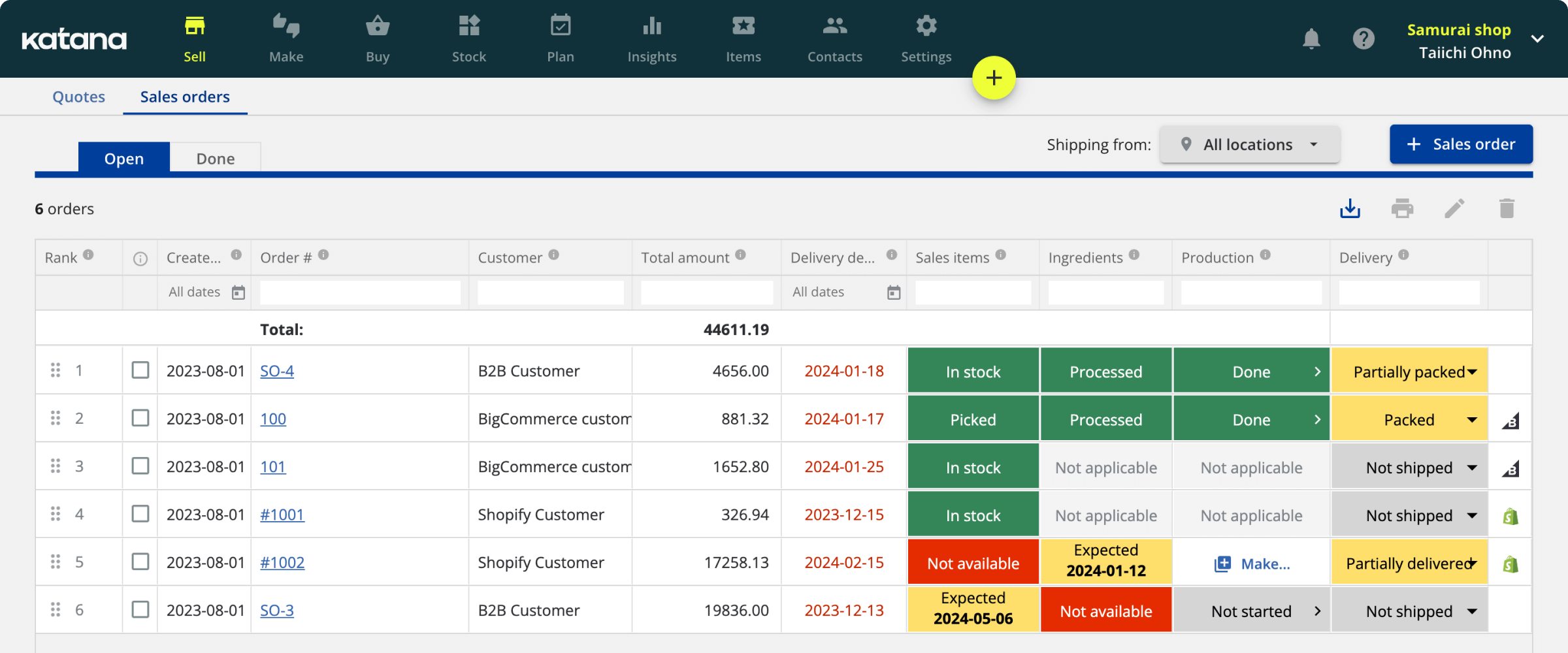
prod-quality-checklist
Free quality control checklist for manufacturing
Download a production quality control checklist to improve communication and reduce delays while maintaining a high standard for your operations.