Advanced manufacturing — costly gimmicks or the way forward
As long as humans have existed, we’ve always looked for ways to simplify different processes and become more efficient.
Manufacturing is one industry where these improvements have been especially noticeable. But does it make sense to keep up with these innovations as a business, or should you take a step back and wait for new technologies to be tried and tested before implementing them yourself?
In this article, we’ll look at advanced manufacturing and try to answer these exact questions.
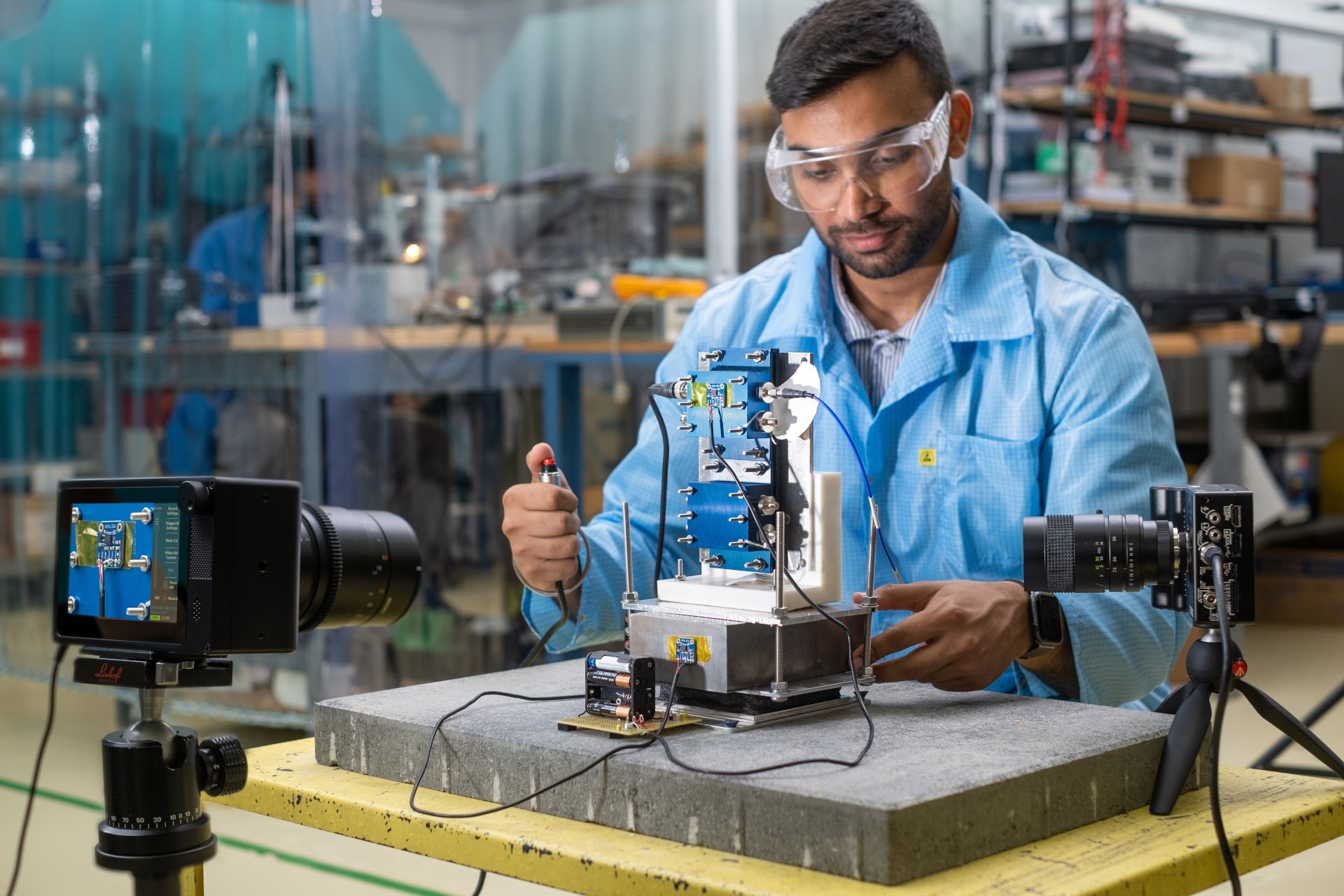
What is advanced manufacturing?
Advanced manufacturing uses cutting-edge technologies and processes to improve manufacturing efficiency.
This can include anything from nanotechnology and robotics to artificial intelligence (AI) and laser beam machining. Advanced manufacturing aims to create a more streamlined production process that requires less input in terms of time, labor, and resources but still produces high-quality output.
What are the differences between advanced and traditional manufacturing?
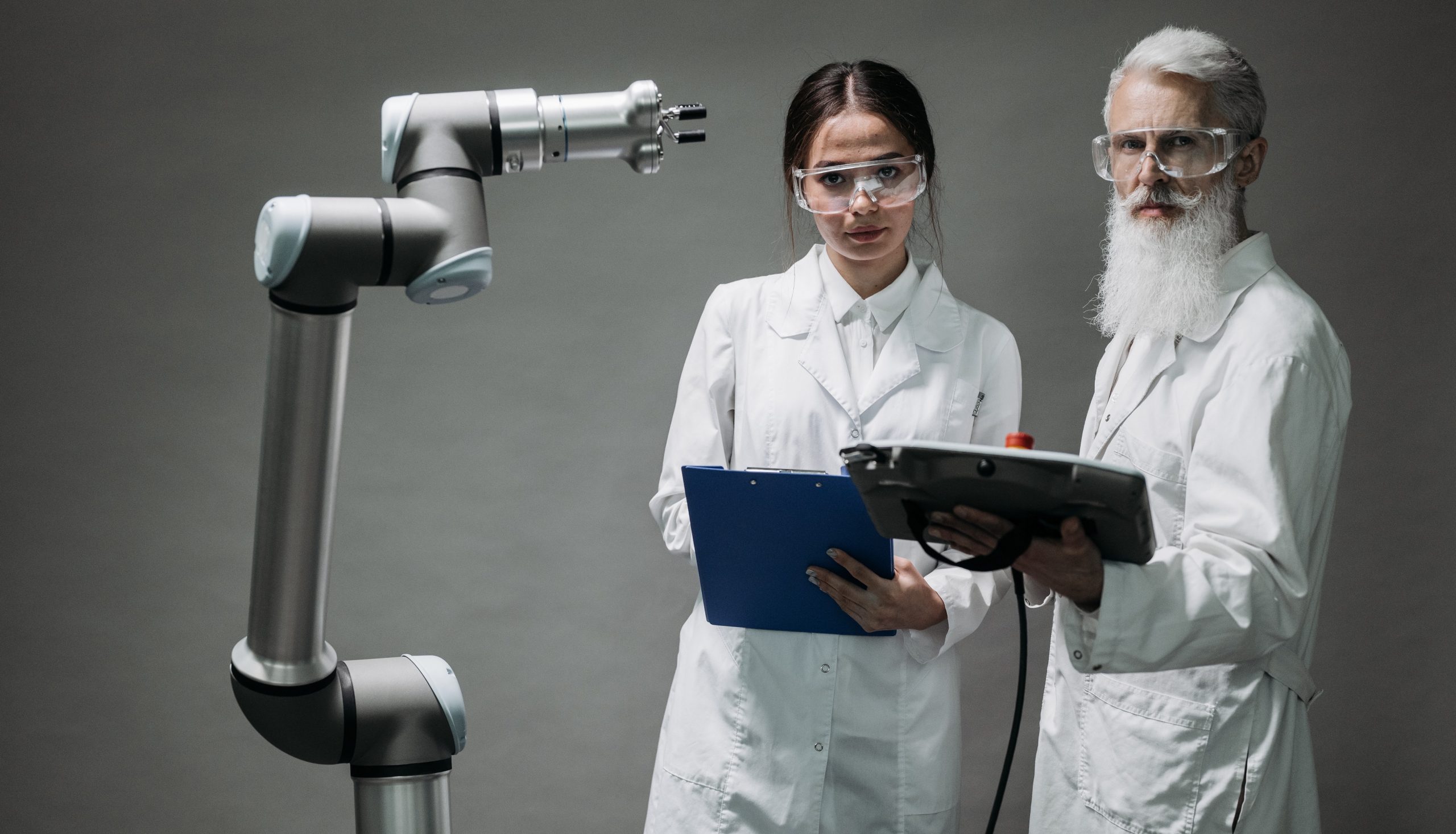
Advanced manufacturing generally refers to any type of manufacturing that uses cutting-edge technology and processes in order to improve efficiency, quality, or speed. Advanced manufacturing is built on a foundation of continuous innovation to develop new ways to create products and improve efficiency.
In advanced manufacturing, a large part of the profits is reinvested in research and development to maintain a competitive advantage.
In contrast, traditional manufacturing typically relies on older, more established methods and technologies. In traditional manufacturing, investments in new technology are often incremental, and the focus is on optimizing existing processes.
As a result, traditional manufacturing is often less nimble and adaptive than advanced manufacturing.
What are some examples of advanced manufacturing technologies?
The list of advanced manufacturing technologies is quite long and gradually grows as new emerging technologies are developed — below we look at the ones that have found wider applications within the manufacturing industry.
Additive manufacturing or 3D printing
This technology can be used to create prototypes or finished products from a digital file. 3D printing is often used in a product creation’s design and development stage, as it allows for quick and easy iterations.
Robotics and automation
Robotics are often used in manufacturing to automate repetitive tasks. For example, a robot arm could be used to weld components together or apply sealant. Automation in manufacturing can also be used to manage the flow of materials through the production process.
Nanotechnology
Nanotechnology is the manipulation of matter on an atomic or molecular level. This technology can be used to create advanced materials that are stronger and lighter, as well as to develop new methods of manufacturing.
In chemical manufacturing, nanotechnology is often used to create more efficient catalysts that require less energy for the same reaction and produce less waste.
AI and data science
AI can be used in manufacturing to predict failures, optimize production schedules, and even control robotic arms. Big data analytics can be used to analyze large data sets generated by manufacturing processes to identify trends and improve efficiency.
What industries can benefit the most from advanced manufacturing?
Most manufacturing companies can benefit from these advanced technologies and processes. However, certain manufacturing industries are more inclined to take advantage of these technologies and, in return, may see particularly big improvements.
Aerospace
The aerospace industry is one that has historically been at the forefront of advanced manufacturing. This is due in part to the stringent safety requirements of the industry, as well as the need to produce highly complex products. 3D printing is often used in aerospace to create prototypes and small production runs of parts and components.
Medical
The medical industry is another field that greatly benefits from additive manufacturing. In particular, this technology is used to create prostheses specific to a patient cost-efficiently. The use of 3D printing has also allowed for the development of new implantable devices, such as cardiac stents.
Automotive
The automotive industry is another major beneficiary of advanced manufacturing technologies. In particular, robotics and automation have improved production lines and created higher-quality products. These technologies are also used to create new automotive components, such as lightweight aluminum chassis.
In addition, the automotive industry has also benefitted from nanotechnology, which has made it possible to manufacture new, durable, lightweight composite materials, which, in turn, has also changed automotive inventory management.
Should your business adopt advanced manufacturing technologies
Ultimately, the decision of whether or not to adopt advanced manufacturing technologies should be based on a careful analysis of your specific business needs.
Implementing advanced manufacturing technologies may be a good idea if you are in an industry subject to high safety standards or require complex products. These technologies can also be beneficial if you want to improve your production process’ efficiency or create new and innovative products.
That being said, unless you’re involved in one of the abovementioned industries, you probably shouldn’t try to adopt every new technology that you read about. Most of the time, it’s better to wait for the technology to mature and for bigger flaws and wrinkles to be ironed out.
The most valuable company in the world by a solid margin — Apple Inc. — is not known to be the first to the marketplace with new technologies. It is well-known, however, for meticulously selecting the right technology at the opportune moment and making it work in a way that greatly benefits its customers.
This is not to say that you should never be the first to enter the market with a product built with new and innovative technology. But unless you have a clear competitive advantage, it’s usually best to wait until technology matures before you adopt it.
Advanced manufacturing technologies can be costly and may require significant changes to your existing production processes. As such, it’s important to carefully consider whether or not these technologies are right for your business before making any investments.
How to manage advanced manufacturing?
Considering how reliant most of these technologies are on computers, the internet, and software, it should be no surprise that before adopting these technologies, you should likely also upgrade your computer systems.
Luckily, that doesn’t necessarily mean additional large investments in hardware and software suites. Enterprise resource planning (ERP) systems have evolved over the last decade, and you can now find comprehensive but affordable solutions that can help manage and automate many of the processes related to advanced manufacturing.
Katana’s enterprise manufacturing software can help you keep track of your inventory, automate the ordering process, manage your supply chain, and much more. This can free up a significant amount of time and resources that can be better spent on other areas of your business.
Additionally, an ERP system can help you integrate your different manufacturing processes and systems, making it easier to take advantage of the benefits of advanced manufacturing technologies. Reach out to our sales team to request a demo and see it in action.
Table of contents
Manufacturing guide
More on manufacturing
Get visibility over your sales and stock
Wave goodbye to uncertainty by using Katana Cloud Inventory for total inventory control
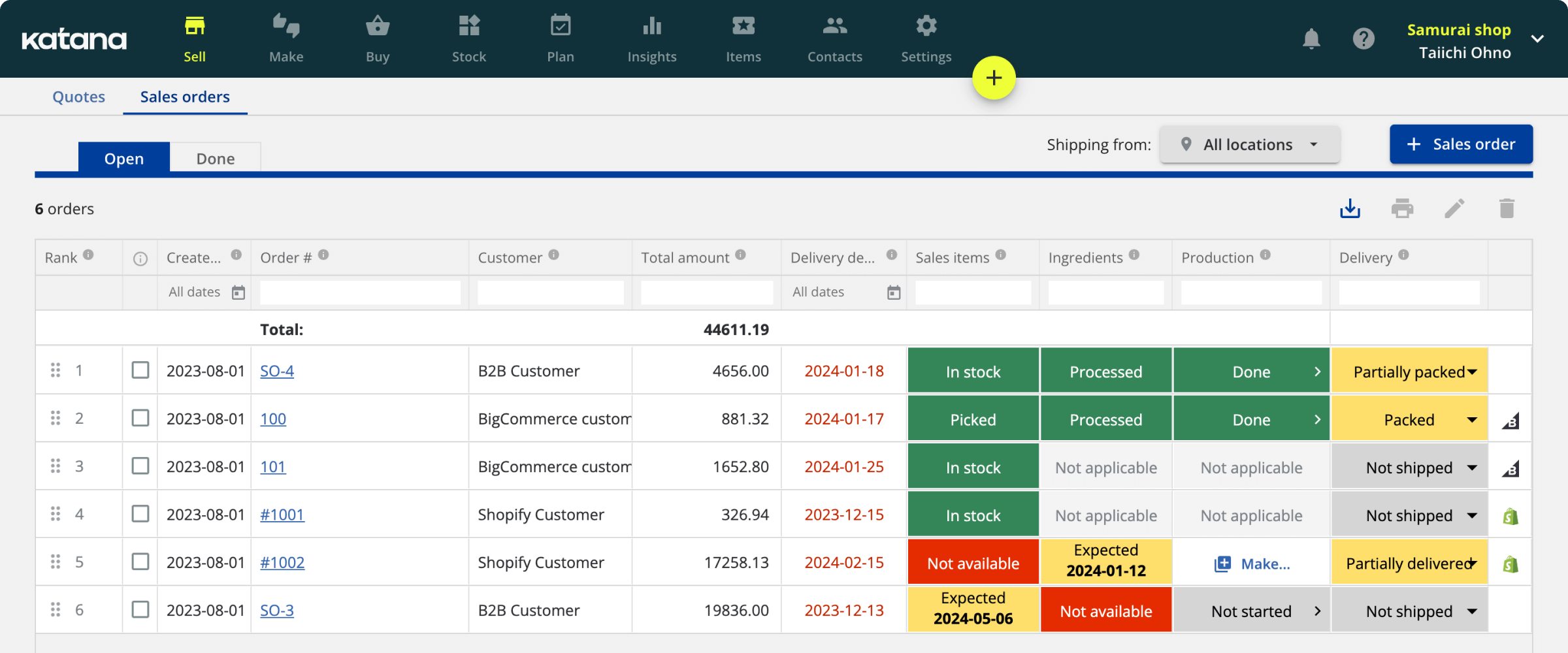