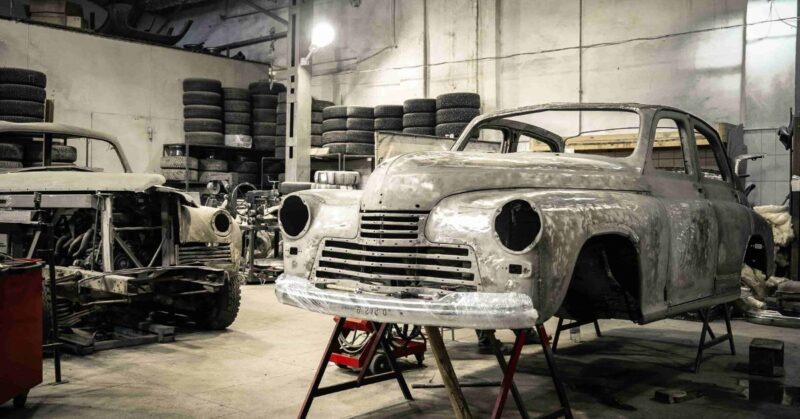
Automotive inventory management software
Katana helps you get ahead in the automotive industry by minimizing waste and effort while maximizing profits, quality, and customer satisfaction
Features
Automotive inventory management software helps you work smarter
Katana offers the ideal features of automotive inventory management software, with inventory management, live planning, and integrations for all your needs from sales to shipping.
Automotive inventory management software helps reduce waste, supercharge production, and maximize profit
You can use Katana as automotive, auto parts, or even auto dealer inventory software. Use Katana’s array of features for raw materials and stock inventory tracking as well as to gain an end-to-end overview of completed and shipped products. If you’re linked to a dealership then you can keep track of which vehicles are in stock and when a car is sold. It’s an ideal overview of your whole business, with live data thrown in.
Make bills of materials to perfect your products
Well-written bills of materials (BOMs) can play a crucial role in inventory management, as the finer details of each of your products are kept within them.
By accurately capturing every component and material required in the production process, BOMs provide a comprehensive overview that is essential for efficient planning and execution.
This level of detail ensures that you can manage resources effectively, reduce waste, and maintain quality control.
Katana allows you to:
- Create BOMs and share them with your team
- Include variations for different products
- Add notes for special cases and custom details
- Calculate lead times and plan product lifecycles
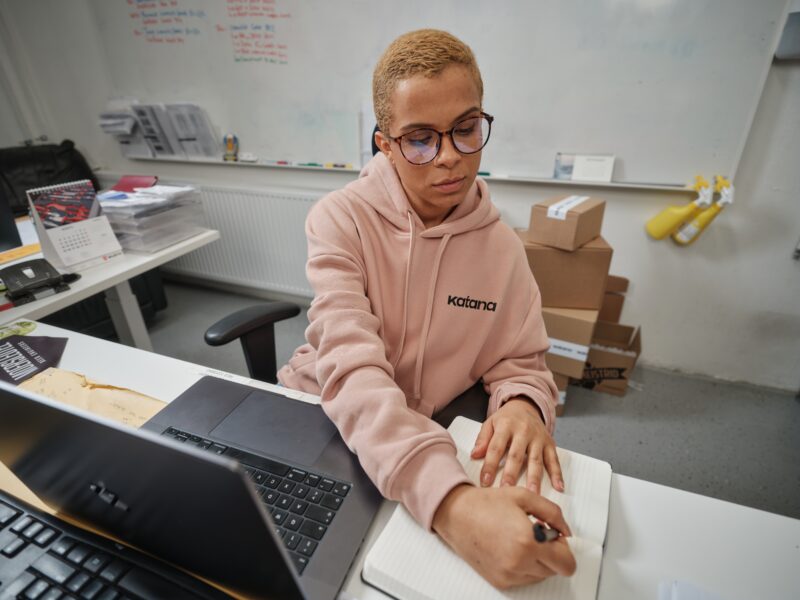
Optimize your logistics and operations with integrations
Katana has a growing list of native and third-party integrations to streamline your operations and centralize day-to-day tasks in one comprehensive platform.
This allows users to elevate operational efficiency and drive business growth without having to switch between platforms, leaving you plenty of time to enjoy the results of your work.
Katana enables automotive businesses to:
- Manage e-commerce channels with Shopify and WooCommerce
- Keep your finances in check with accounting tools like Xero and QuickBooks Online
- Discover tools for automation, CRM, shipping, and more
- Create custom workflows based on the specific needs of your business
See Katana in action
- Manage production planning, resource allocation, and scheduling in real time
- Issue purchase orders based on precise material requirements and reorder points
- Implement Katana on your own or with a team of experts that will set you up for success
Learn more about our plans and the features they come with
- Plans starting from $179 / month
- Annual and monthly billing options
- Add users and warehouses as you grow
Integrate with the best e-commerce, accounting, reporting, and CRM software out there
Create custom API integrations
Use Katana’s open API to create custom workflows and connect to apps beyond our list of integrations. Automate data transfers between the services you use to level up efficiency. Take a look at our API documentation to learn more.
Automotive inventory management software FAQs
Inventory management in the automotive industry refers to ordering, storing, and utilizing a company’s inventory, which includes both vehicle parts and completed vehicles.
This enables automotive businesses, dealerships, and parts suppliers to effectively balance supply with demand, minimizing surplus inventory while ensuring products are available when needed. The goal is to maintain optimal stock levels to meet consumer demands efficiently while avoiding overstocking or running out of goods.
Effective inventory management is crucial for reducing costs associated with excess inventory and for maximizing sales and profitability.
Many businesses in the automotive sector now rely on automotive inventory management software or systems. These technological solutions automate key processes and manage the flow of goods from warehouses to sales points or the end consumer, ensuring the timely availability of the right products.
Here are the key elements of automotive inventory management.
- Implement an automotive inventory management system — Utilize software to automate the tracking of stock levels, orders, sales, and deliveries. This software can provide real-time data, helping make informed decisions about stock levels, reordering, and storage.
- Categorize inventory — Organize inventory into categories based on demand, value, or frequency of use. This can include separating fast-moving items from slow-moving ones and keeping critical parts always available.
- Use demand forecasting — Analyze past sales data and market trends to predict future demand for parts. This helps maintain optimal inventory levels, reducing the risk of stockouts or excess inventory.
- Establish reorder points — Set minimum stock levels that trigger the automatic reordering of parts. This ensures a continuous supply without the risk of running out of essentials.
- Regular inventory audits — Conduct physical counts of inventory periodically to verify stock levels and identify discrepancies early. This can be done through cycle counting, where a portion of the inventory is counted on a regular basis.
- Optimize inventory layout — Organize the warehouse logically to ensure fast-moving and frequently used items are easily accessible. This can reduce picking and packing times and improve overall efficiency.
- Build strong supplier relationships — Collaborate closely with suppliers to ensure fast delivery of parts. Good relationships can lead to better terms, such as volume discounts or more flexible delivery schedules.
- Leverage just-in-time (JIT) inventory — Adopt a JIT inventory strategy to reduce inventory holding costs by receiving goods only as they are needed in the production process. This requires precise coordination with suppliers and accurate demand forecasting.
- Implement quality control measures — Ensure that all received parts meet quality standards to avoid the cost and inconvenience of returning defective items and dealing with replacements and delays.
- Utilize data analytics — Analyze inventory data to identify trends, inefficiencies, and opportunities for improvement. This helps make better decisions about inventory levels, ordering practices, and suppliers.
The just-in-time (JIT) inventory technique is one of the most popular and widely implemented inventory management strategies in the automotive industry.
Originating from the Toyota Production System, JIT focuses on reducing waste and increasing efficiency by ordering and delivering components just in time to be assembled rather than keeping large stocks of parts or finished products.
JIT requires precise coordination between suppliers, as well as accurate demand forecasting, to ensure that parts arrive exactly when they are needed, minimizing the need for storage space and reducing inventory carrying costs. This approach not only optimizes inventory levels but also enhances production efficiency, reduces waste, and can lead to significant cost savings.
The popularity of JIT in the automotive industry is attributed to its effectiveness in streamlining processes, reducing lead times, and improving overall quality and customer satisfaction. However, it requires a high level of reliability and quality from suppliers, as well as a flexible warehouse system that can quickly respond to changes in demand.
You should be able to get up and running within a couple of days, as Katana offers a well-presented platform and has an extensive Knowledge Base with lots of video guides to help you get started.
We also have an onboarding program where a dedicated implementation manager guides you through the entire process, showing you all the features and tricks you might need to kickstart your operations in Katana. Customers who enroll in the guided implementation get set up 2 to 3 times faster and need less time to start seeing the benefits.
Get visibility over your sales and stock
Wave goodbye to uncertainty by using Katana Cloud Inventory for total inventory control
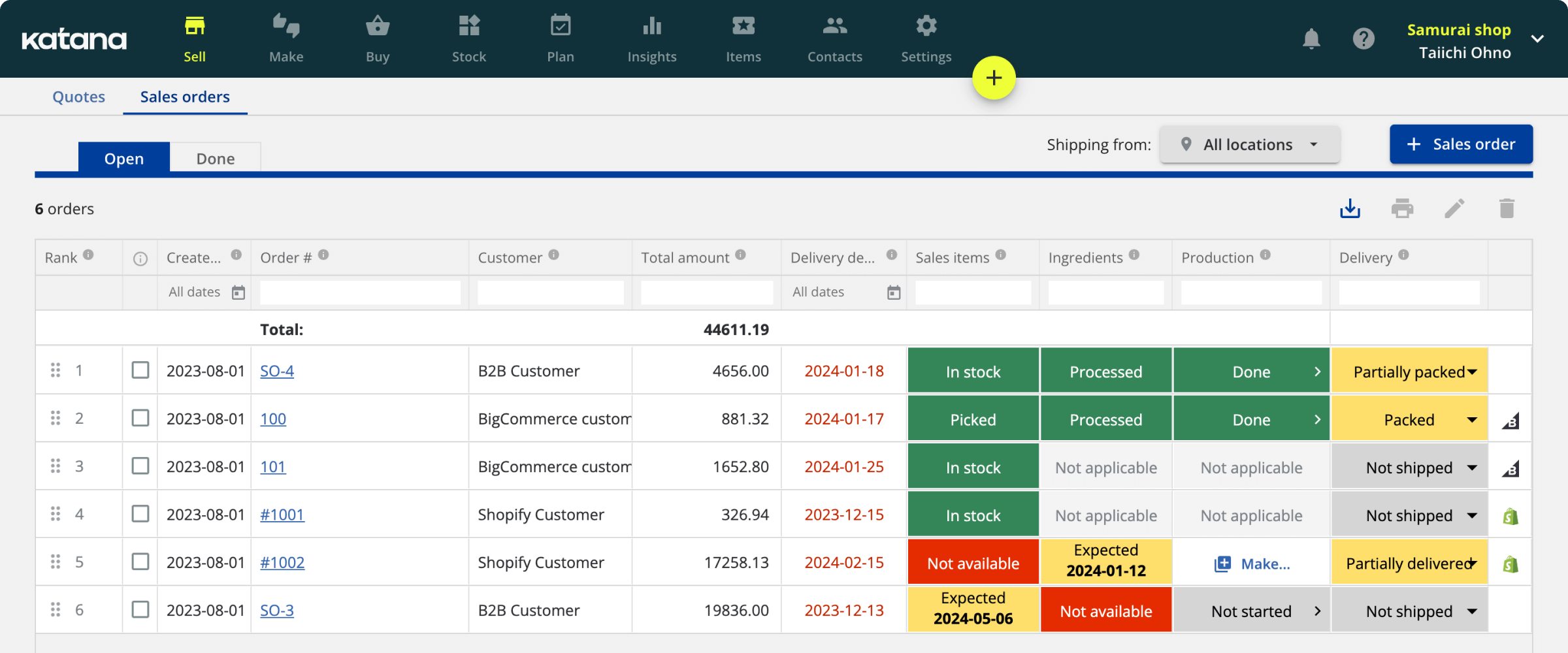