A complete guide to the four types of inventory in manufacturing
How you manage your inventory can either make or break your manufacturing operations.
Moreover, the complexity of dealing with your inventory grows dramatically with every additional product or product variant you add to your catalog. Hence, it is worthwhile to understand fundamental questions related to inventory and inventory management — exactly what this guide covers.
We’ll define what inventory is and explain the different types you will encounter in your manufacturing business — to support these definitions, we’ll look at the fictional Acme Corporation of Warner Bros fame and the different types of inventory they hold at their factory.
So without further ado, let’s dive right in.
Get the ultimate guide to inventory management
A comprehensive ebook that covers everything you need to know about inventory management.
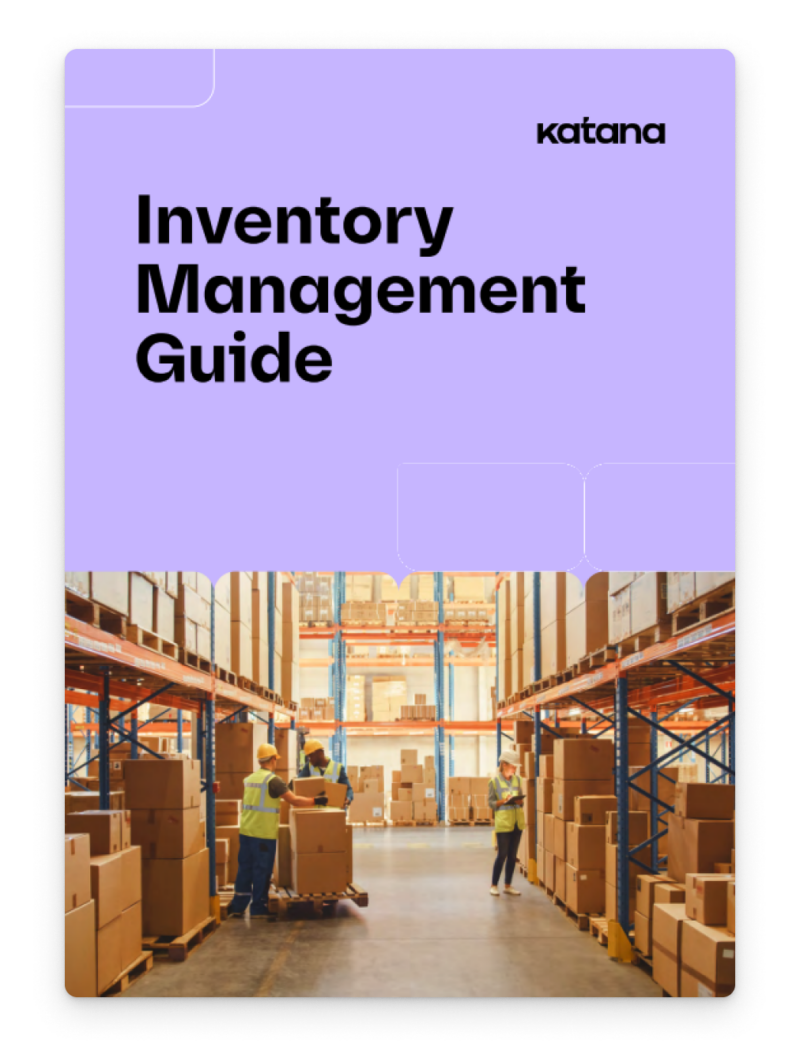
What is inventory?
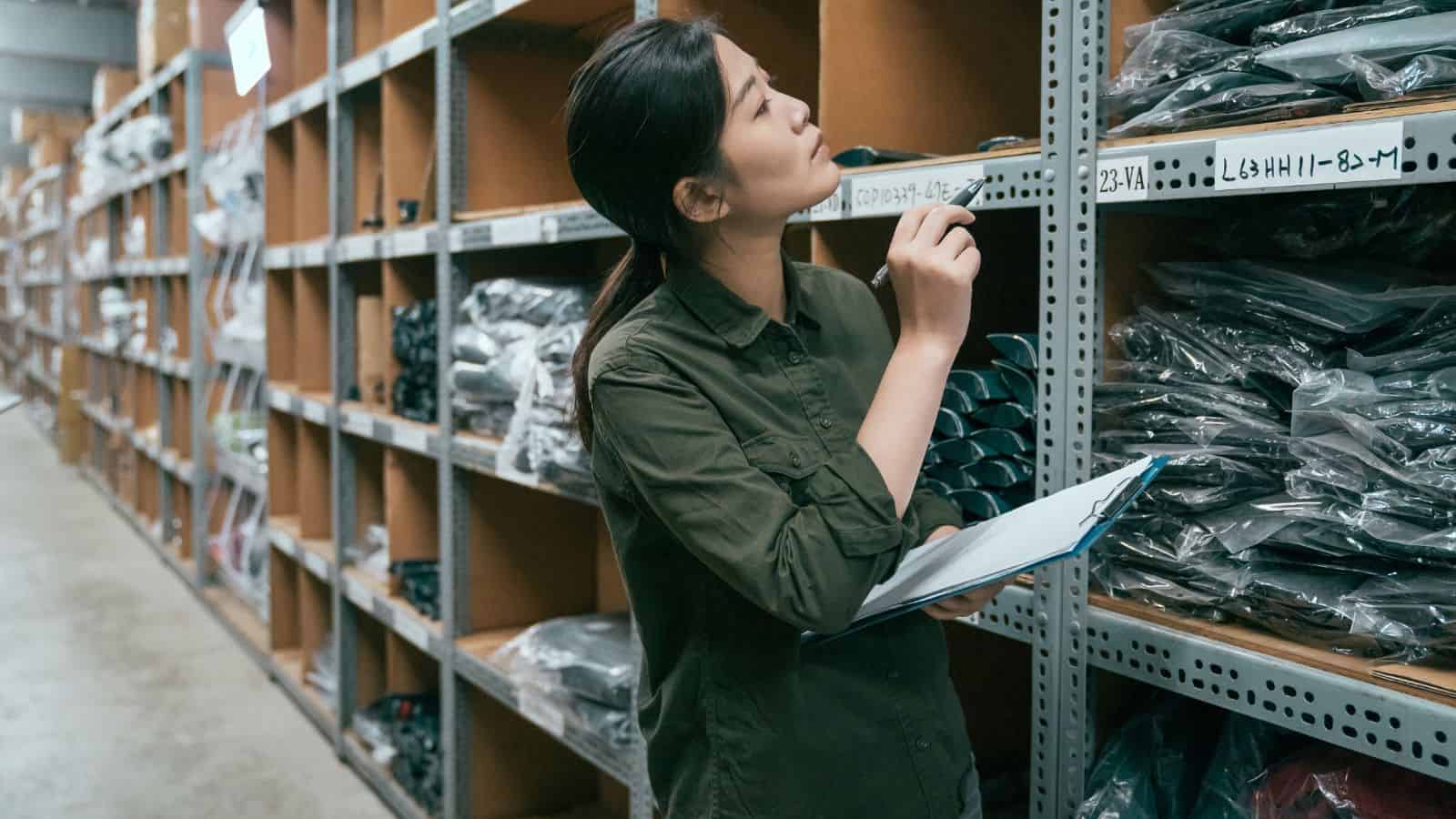
Inventory is the sum of all items intended to be sold by your business.
This constitutes a strict definition and only includes everything from your raw materials to finished goods that will eventually end up in your customers’ hands.
While this definition is of the most practical importance, it is useful to expand our definition a little bit to include materials and goods that are essential to your production process. This expansion allows the inclusion of materials that will never reach your customers but are vital for your business and hence should be part of your inventory.
Ultimately, inventory is the sum total of all the goods and materials that your business holds for either resale, production, or utilization.
When your business is small, you often don’t even need to think about inventory management. However, as your business grows, so does your inventory and the need to manage it efficiently. Inventory management systems evolve along the following lines in general:
- Mental notes and intuition
- Simple paper-based solutions (Sticky notes, notepads, etc.)
- Excel-based management
- Dedicated inventory management software
Each step improves on the previous ones and attempts to equip you with the best tools to tame the complexity of managing your workflows and inventory. Of course, your business could have already grown to the point where you’d have to skip a step or two to use manufacturing software with built-in inventory management features.
However, let’s return to the task of classifying inventory.
What are the 4 types of inventory?
The four types of inventory are raw materials, work-in-progress (WIP), finished goods, and maintenance, repair, and overhaul (MRO) inventory. Knowing which items belong to which category allows you to optimize your operations and account for each step of the production process more efficiently.
Now that different types of inventory have been laid out, let’s dive deeper into what each category consists of and what to keep in mind when managing them.
Raw materials
Raw materials are all the items that your business uses to manufacture finished products.
These materials can be sourced, produced by your company, or procured from a supplier. Raw materials can be further classified into two categories:
- Direct raw materials
- Indirect raw materials
Direct raw materials
Direct raw materials are the components that are used directly in the final product. These materials are easy to quantify and account for per unit or per batch basis.
Indirect raw materials
Indirect raw materials are the components that are not part of the final products but are used during the production process. Indirect raw materials are harder to identify and account for since they can’t be traced to specific batches or units. However, these are essential for the production process.
For instance, one of Acme Corp’s top-selling products is its Plush Couch 5000. To manufacture each Plush Couch 5000, Acme Corp requires high-quality metal frames, foam, and leather as raw materials. However, the main component of the Plush Couch 5000 happens to be one ridiculously large spring that can shoot your target to the stratosphere. These are the components that it can easily quantify and price.
So Acme categorizes these as its direct raw materials.
Of course, making a couch isn’t as simple as throwing foam and leather on top of a frame. The company also requires tools, screws, glue, staples, and leather wax to manufacture the couches. However, it is pretty hard to quantify how much leather wax or how many staples are used on each couch.
So these raw materials are categorized as indirect raw materials.
Would you like to know more?
There are more intricacies in raw material inventories, so if you’d like to learn more about raw material inventory management, you can look at the raw materials inventory management guide.
Work-in-progress (WIP)
All the materials that your factory floor has started working on, but the product isn’t quite finished yet, consist of your work-in-progress (WIP) inventory.
It can comprise direct and indirect raw materials — the only thing to note here is that the product is not complete and is a work in progress.
Continuing with the Acme Corp example, let’s assume that every couch has a production time of one week. So once the metal frames, foam, and leather has been cut to size and the factory has started working on a couch, those materials stop being part of the raw materials and should be considered WIP inventory.
Finished goods
All the items ready to be sold are considered part of your finished goods inventory.
Of course, depending on the workflow you adopt, this could mean slightly different things.
If you follow a make-to-order workflow, then the final product is made and can already be shipped to your customers. Whereas, if you follow the make-to-stock workflow, the inventory will have to be stored in a warehouse until an order comes through. In either case, your finished goods inventory should be pretty clear and straightforward to account for and track.
In the case of Acme Corp, once the couches are ready, they are stored in a warehouse until a shipping company picks them up and delivers them to customers. The finished couches are part of Acme’s finished goods inventory.
Maintenance, Repair, Operations (MRO)
As the name suggests, maintenance, repair, and operations (MRO) inventory is essential to keep your factory operational. MRO inventory is strictly for your consumption and is not available for customers to purchase.
For example, Acme Corp maintains extremely clean and safe working environments for its employees.
So every day the facilities are cleaned by a team of janitors. All the equipment and materials required to accomplish this job, like vacuum cleaners and cleaning supplies that the janitors use, are part of the MRO inventory. Similarly, the tools and spare parts required to repair and fix broken machinery are also part of the MRO inventory.
Inventory management
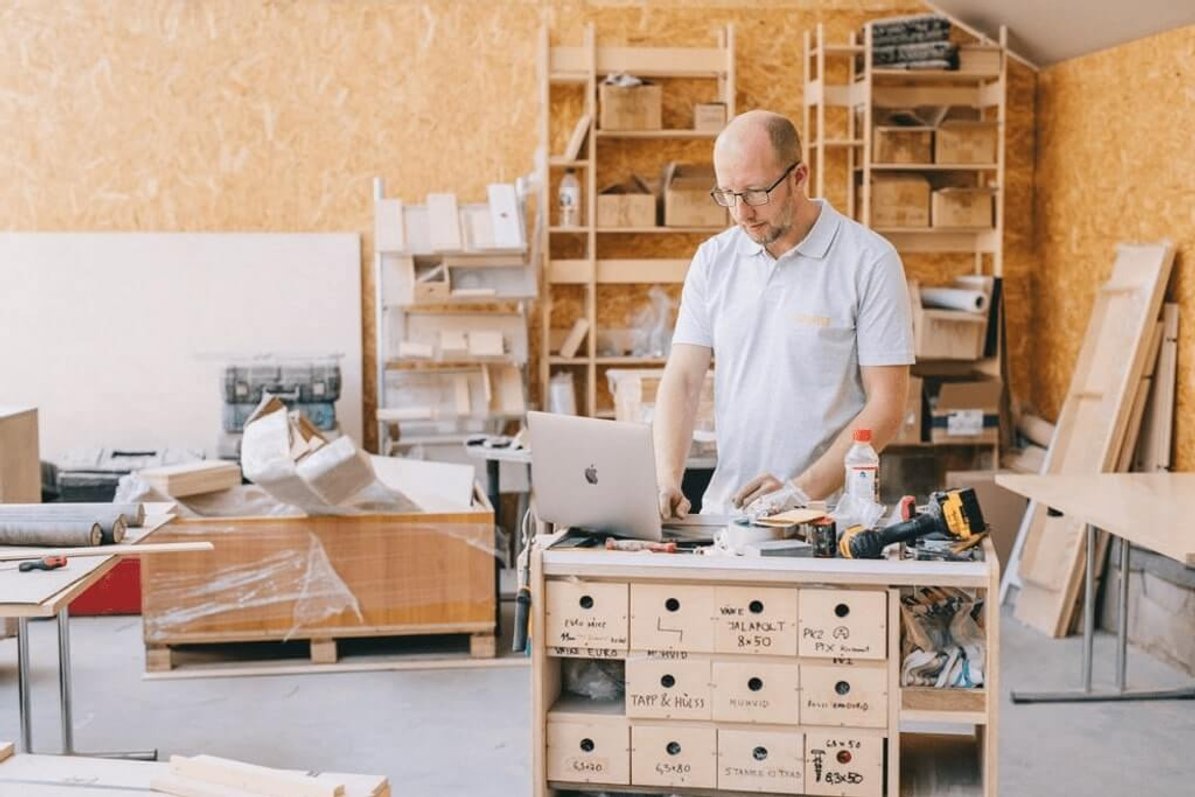
With the classification of inventories down, the natural question that arises is how to manage them effectively.
There are plenty of strategies when it comes to managing your inventory. However, it is becoming increasingly easy to implement perpetual inventory systems with the rise of manufacturing software like Katana.
A perpetual inventory management system automatically maintains inventory counts through live systems that record and account for sales and orders in real time. This greatly simplifies maintaining stock by drastically reducing the need to perform expensive inventory audits.
For instance, Katana’s live inventory management features allow you to keep track of materials across multiple warehouses and bring all your teams on the same page. Give Katana a try and send your inventory management problems to the stratosphere with a riskless 14-day free trial.
Would you like to know more?
If you’d like to learn more about the other inventory management approaches, here is a detailed guide for you: Inventory management guide.
A breakdown of the key points of the types of inventory
To recap what you’ve learned, here is a short summary of the key points from the guide.
Inventory: The total of all the goods and materials your business holds for resale, production, or utilization.
There are 4 types of inventory. These are:
- Raw materials (direct materials and indirect materials)
- Work-in-progress (WIP)
- Finished goods
- Maintenance, Repair, Operations (MRO)
For your business to be successful and efficient, it is important to manage inventories well.
Perpetual inventory management systems provide many benefits, and implementing them is getting increasingly easy due to cloud systems like Katana.
And there we have it! Everything you need to know about the different types of inventory and how to utilize them in your business. Take it away, Porky Pig:
Table of contents
Inventory management guide
More from Katana
Get visibility over your sales and stock
Wave goodbye to uncertainty by using Katana Cloud Inventory for total inventory control
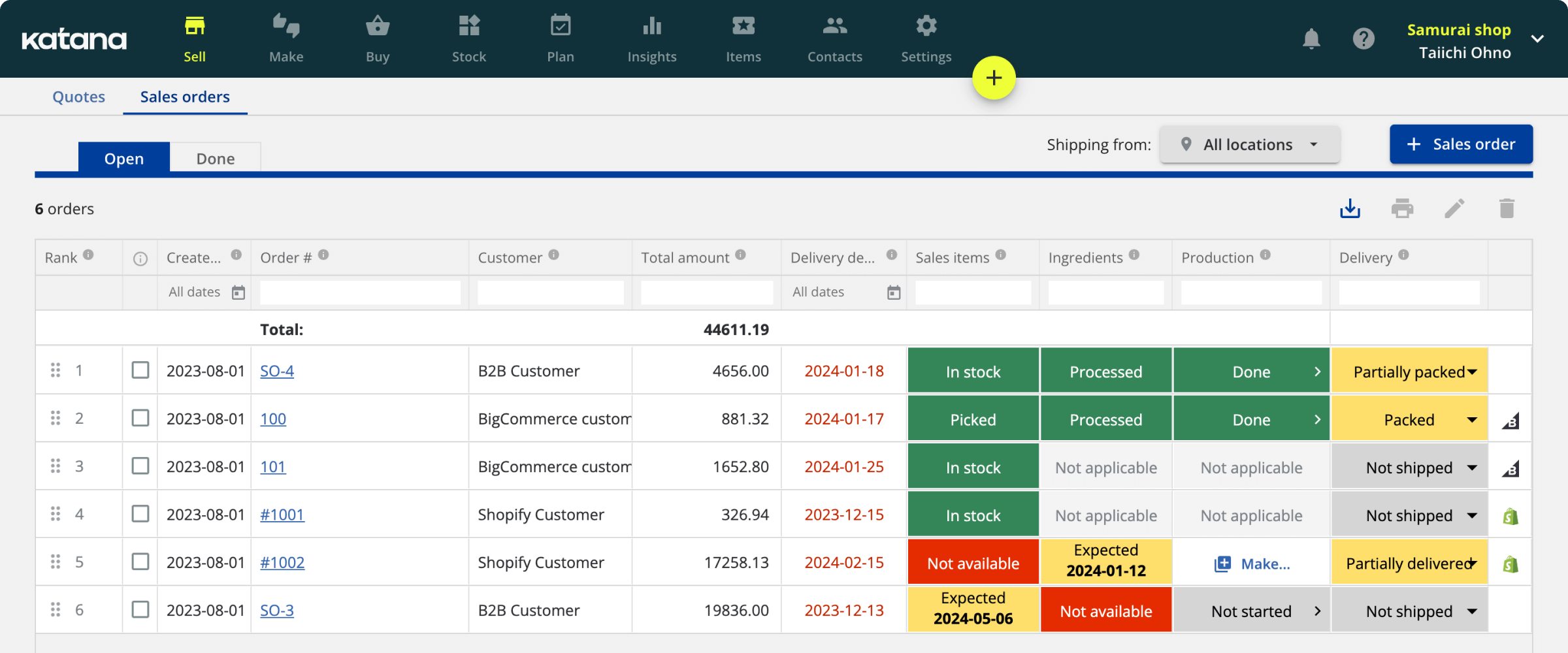