Warehouse inventory management software
Warehouse managers know how important it is to track inventory. Katana’s warehouse stock control software automates your processes so you can see what’s in stock, what needs to be ordered, and when items are due to arrive — all at a glance.
Features
Warehouse management software with the features you need
The best warehouse stock management system is one that takes care of all aspects of your inventory handling.
Control inventory remotely with warehouse management software
Know your stock levels at all times, adjust quantities as needed, and complete inventory transfers between locations. The Stock screen gives you an overview of all your inventory items. Being aware of your inventory status is crucial, and that is why finding the right warehouse inventory management system is important. Stay on top of things and know exactly what you have in stock at all times.
Katana supports tailored shipping workflows
We know that every warehouse is different. That’s why Katana’s warehouse management software is designed to be flexible and adapt to how you work — not the other way around.
Whether managing a single warehouse or multiple across different locations, Katana has the features you need to streamline your operations.
Our powerful software offers shipping workflow features like:
- Search and filter inventory by location, status, or item type
- Track stock levels, inventory turnover, and more
- Set reorder points and safety stock levels to avoid reputation-damaging stockouts
- Picking and packing for streamlined order fulfillment
Katana is a favorite for both sales and warehouse teams
Gain full transparency of what’s in stock and place new orders when items are running low — no more back-and-forth between different platforms. Plus, you can track the status of orders and view past order history. All the data is right there at your fingertips.
If you’re looking for a warehouse inventory management software that’s easy to use and packed with features, look no further than Katana.
Katana allows you to:
- Complete inventory control and sales order management across multiple sales channels
- View stock levels by location and perform stock transfers if needed
- Simple and easy-to-use interface to quickly understand the status of orders
- Centralize all your data and share it with members of the team
Achieve full traceability with Katana
Receiving items and sending goods is now easier than ever with Katana’s warehouse stock management software. Simply scan the item’s barcode, and Katana automatically finds the purchase order it belongs to. You can also view the item’s details, such as its description, unit price, and more.
Plus, you can track where each item is located in your warehouse using bin locations. This is especially useful for those who operate in multiple locations or have a large warehouse.
With Katana, you can:
- Create and track batches of items
- Export barcodes for printing
- Fully or partially receive purchase orders
- Trace the lifecycle of goods across the supply chain
Want to see Katana in action?
Book a demo to get all your questions answered regarding Katana’s features, integrations, pricing, and more.
Integrate with the best ecommerce, accounting, reporting, and CRM apps out there
All your business tools — connected
Optimize your workflow with native and third-party integrations, automating data transfer between systems and reducing errors. Or build your own custom integrations using the open API for seamless data flow with other applications. Check out the API documentation for more details.
We needed help with Shopify inventory control for raw materials, and Katana exceeded our expectations.”
Pablo Baque
Walk With Me CEO
Katana integrates everything, making for effective company-wide resource planning and control of our entire process.”
Danielle Louw
Production Manager at CT LAB
With Katana, we are able to track products, build recipes for materials, and set reorder points for our materials as well.”
Lisa Diep
Chief Operating Officer (COO) at Peace Collective
It’s great to be able to see where inventory faults happen and being able to fulfill orders and where the turnaround happens.”
Alaina Oehrlein
Production Lead at Essence One
Warehouse management software FAQs
A warehouse management system (WMS) is software for managing everything that goes on in a warehouse. Think of it as a digital tool that helps businesses keep track of their inventory, manage their storage space efficiently, and make sure that everything is in the right place at the right time.
Here’s a simple way to understand it:
- Inventory tracking — A WMS keeps tabs on every item in the warehouse. It knows what items are in stock, how many, and where they are located. So, if you need to find a specific product, the WMS can tell you exactly where to look.
- Receiving and putaway — When new products arrive, the WMS helps to check them in, making sure the quantities are correct. Then, it guides workers on where to place these new items so they can be quickly found later.
- Picking and packing — When it’s time to fulfill orders, the WMS directs workers on which items to pick and from where. This ensures they can gather everything quickly and accurately. It also helps with packing the items efficiently for shipping.
- Shipping — The WMS coordinates the shipping process, making sure that orders are packed correctly and sent out on time. It can even print shipping labels and track shipments.
- Space utilization — It optimizes the use of space in the warehouse. By keeping track of where everything is and how much space is available, it helps to make sure the warehouse is not cluttered and items are stored in the most efficient way possible.
- Reporting and analytics — A WMS provides valuable insights and reports on warehouse operations. It can show trends, highlight inefficiencies, and help in making informed decisions to improve productivity.
WMS offers a range of benefits that boost efficiency, accuracy, and overall performance in warehouse management. Here are the key advantages businesses can gain from implementing warehouse management software:
- Improved inventory accuracy — WMS automates data collection and tracking, reducing errors and ensuring up-to-date inventory levels.
- Increased operational efficiency — Automation of tasks such as order picking, packing, and shipping improves efficiency and lowers labor costs.
- Cost reduction — WMS helps in reducing various inventory management costs, including storage, shipping, and handling.
- Enhanced customer service — Real-time visibility into inventory levels and order status improves customer service, ensuring timely order fulfillment and keeping customers informed.
- Streamlined processes — WMS optimizes warehouse processes, leading to smoother operations and reduced operational bottlenecks.
- Space utilization — Efficient inventory management and tracking help in maximizing warehouse space utilization.
- Accurate order fulfillment — Automation in the fulfillment process minimizes errors and ensures accurate and timely order processing.
- Data visibility — WMS provides real-time insights into inventory, allowing for better decision-making and strategic planning.
- Scalability — As businesses grow, WMS can scale to accommodate increased inventory and operational demands.
- Compliance and security — WMS helps ensure compliance with industry regulations and enhances warehouse security through better tracking and monitoring.
There is no limit to the number of warehouses you can manage with Katana. Whether managing a single warehouse or multiple warehouses across different locations, Katana’s WMS system has all the features you need to streamline your warehouse operations.
Get visibility over your sales and stock
Wave goodbye to uncertainty by using Katana Cloud Inventory for total inventory control
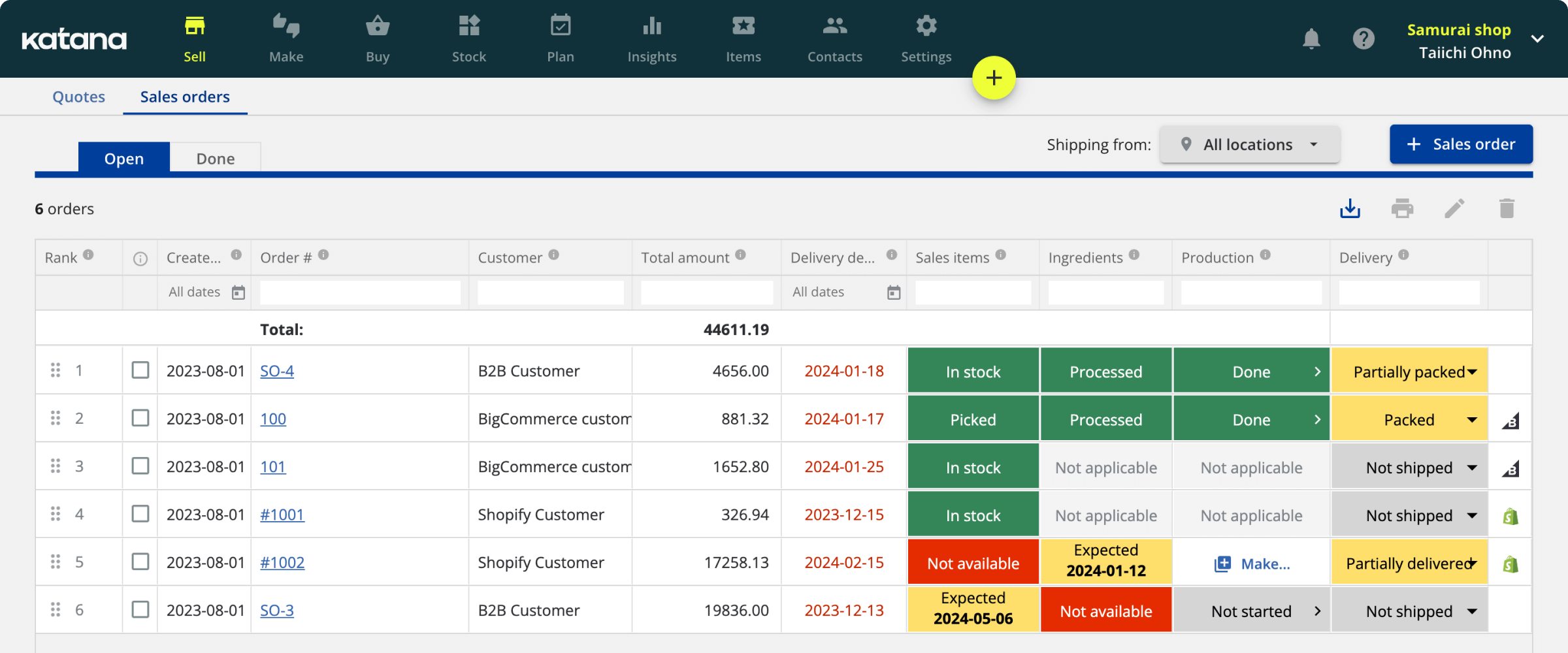