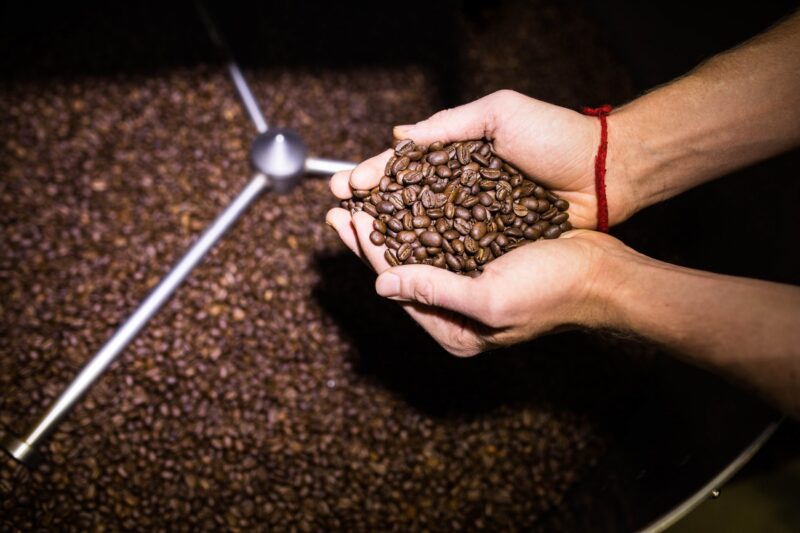
Track your perishable stock and order fulfillment with coffee roasting software
Katana gives coffee roasters the real-time insights they need to manage manufacturing and sales order fulfillment. Features like batch and expiry date tracking help you meet coffee roasting industry regulations, giving you total visibility when it comes to tracking your perishable stock, from green coffee beans to roast coffee, and optimizing your inventory.
Features
Getting your products to customers faster
Katana supports your workflows no matter your industry with the features and seamless integrations you need to manage your business how you want.
Inventory management
Get real-time inventory insights of all your items and optimize your inventory levels based on demand.
Purchase management
Issue purchase orders for supplies and materials in Katana that are delivered directly to your warehouse or contract manufacturer.
Sales order management
Consolidate all your online and offline sales channels and data into a single view for total omnichannel support.
Planning and forecasting
Make better data-driven decisions as Katana automates your inventory planning — using historical data to predict future demand.
Production management
Optimize your production and decrease lead times based on your bill of materials and operations data.
Cloud accounting
Get your inventory and accounting data in sync to better understand your business’s finances.
Warehouse management
Our Warehouse add-on provides all the tools and real-time insights to improve picking routes and manage receiving, mobile scanning, and printing — all from a mobile device.
Integrate Katana’s coffee roasting software with the other tools you know and love
Create custom API integrations
Use Katana’s open API to create custom workflows and connect your coffee roasting software to apps beyond our list of integrations. Automate data transfers between the services you use to level up efficiency. Take a look at our API documentation to learn more.
Coffee roasting software which puts you in control from green beans to roasted, packed, and shipped
If you’re in the coffee roasting business, quality and consistency are absolutely crucial. However, keeping track of different roast profiles in your product variants, which roasting machines are used for different products, while keeping order fulfillment on time is a challenge — especially when your business is growing.
As a coffee roaster, you also need to know what you have in stock, how soon it needs to go in the roasting machine, what’s committed to orders, and when they need to be shipped. In short, you don’t want to be managing it all in poor software, or even worse, a spreadsheet!
Katana cloud manufacturing software offers support for batch manufacturing, so each bean in a batch can get the same roasting quality, batch tracking, so you can follow the progress of each batch of roast coffee, and product recipe, so you’ll always have control over what’s required for every specialty coffee product you stock and sell.
You can also keep track of your outgoings, with our moving average cost feature, which will help you track your spending on green beans over time.
How Katana can help you maintain quality control over your roasting process, and minimize waste
Consistency in production is crucial to maintaining product quality and customer loyalty, and this is where well-structured product recipes are key in Katana. Your staff will know the make up of every coffee product, and you can maintain the roasting quality of every bean.
You can also use batch tracking and expiry date tracking to know when beans need to be roasted, and when products are nearing their sell by dates. This will help you know when you need to place new orders with your coffee importers so you’re not out of stock.
Ensuring quality control is critical, with the visibility Katana’s coffee roasting software gives you, ensuring quality and consistency in your products is easier than ever. Here are few features that coffee roasters that use Katana benefit from:
- Accurate product recipes — Ensure your shop floor staff know what’s needed for every product, from roast profile to coffee bags
- End-to-end production management — Combine roasting process, order scheduling, and resource management in one intuitive platform
- Smart inventory management — Automate inventory transactions and set reorder points to prevent running out of beans
- Accurate costing — Moving average cost helps you track money spent on coffee beans, coffee bags, and other inventory, so you remain in the black
- Integrations and custom workflows — Sync your inventory data with hundreds of e-commerce, shipping, accounting, and reporting platforms
Roasting software like Katana gives you a visual overview of ingredients and production statuses, helping you stay on top of inventory, sales orders, and production at all stages of your product lifecycle.
Get a demo and see Katana in action
- Eliminate stockouts with Katana
- Easily manage incoming orders from all your sales channels
- Track products available for sale
Learn more about our plans and the features they come with
- Plans starting from $179 / month
- Annual and monthly billing options
- Add users and warehouses as you grow
Get visibility over your sales and stock
Wave goodbye to uncertainty by using Katana Cloud Inventory for total inventory control
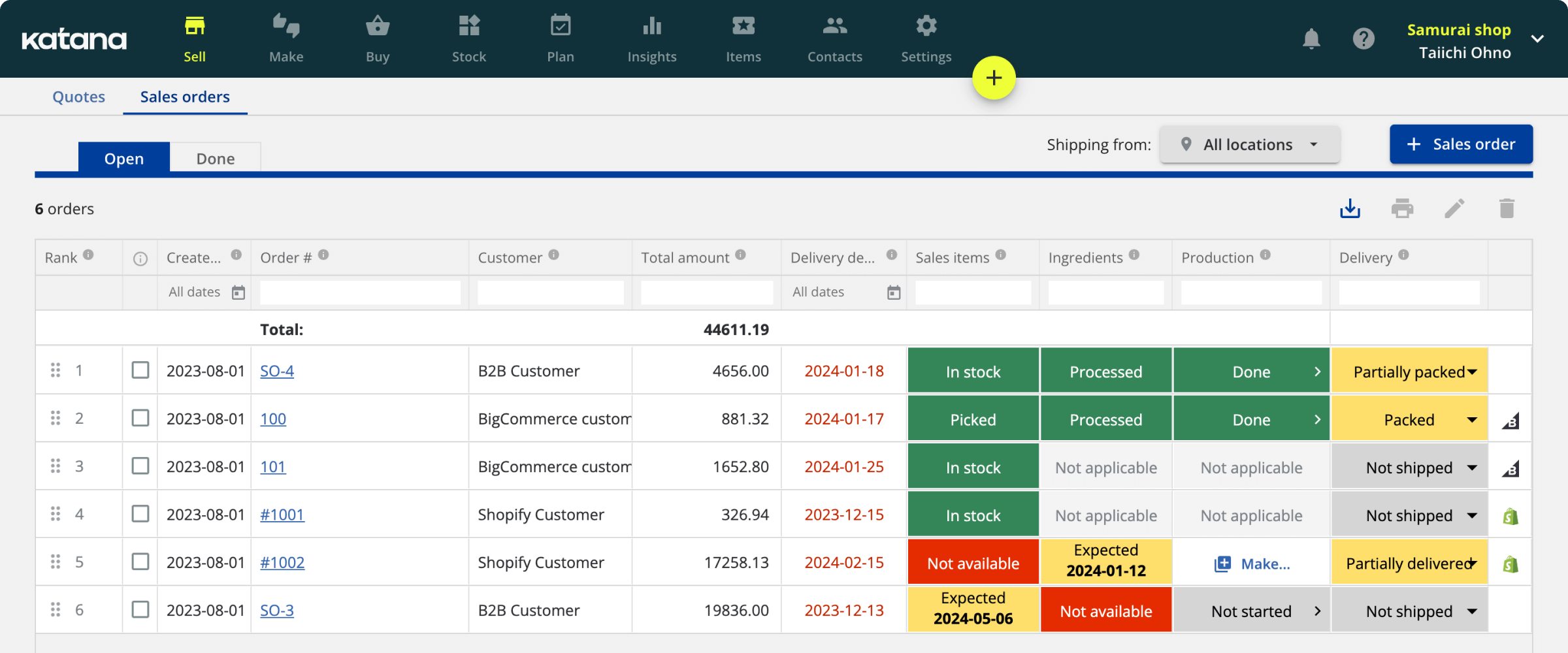