End-to-end traceability with batch tracking
Get the free guide to batch production
Download our free ebook guide on batch production to learn more about the benefits, workflows, and software you need to get started.
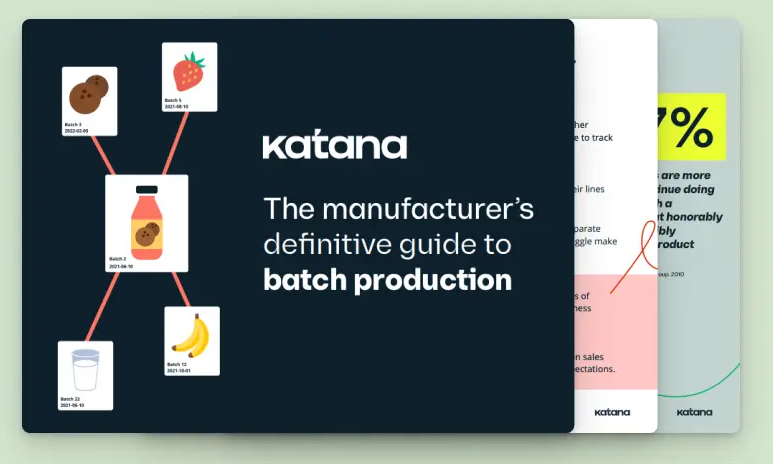
Efficiency is one of the key metrics in the business world. Whether you’re a small-scale artisanal baker or a multinational pharmaceutical giant, the ability to track and manage your products in batches is essential for maintaining quality, compliance, and overall operational excellence.
This article looks into batch tracking, exploring its importance and providing valuable insights into how it can improve your business processes.
What is batch tracking?
Batch tracking, often referred to as lot tracking, is a way to monitor and manage products in discrete groups, known as batches or lots, throughout their lifecycle within a business. This method allows businesses to trace the origin, production, and distribution of each batch, ensuring quality control, regulatory compliance, and improved operational efficiency.
In essence, batch number tracking involves assigning a unique identifier, often in the form of a batch or lot number, to a group of products or materials that share common characteristics or were produced together. This identifier is then used to record and track various aspects of the batch’s journey, from its inception to its final destination.
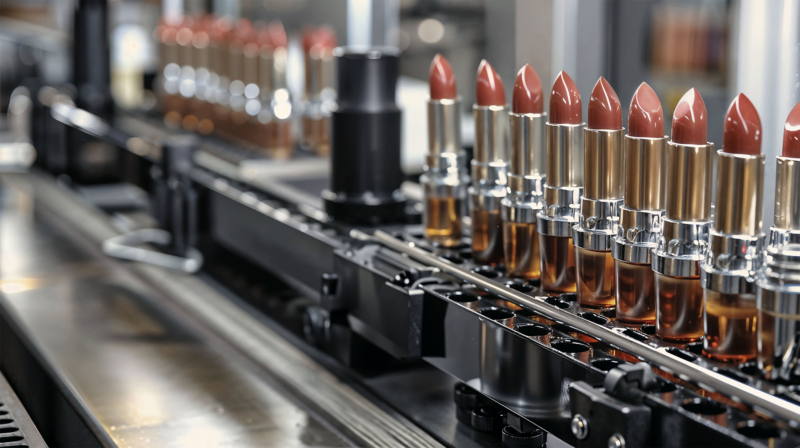
What is a batch management system?
A batch management system is a software or technology solution that allows you to monitor, control, and track batches of products or materials within a manufacturing or supply chain environment.
Production tracking is not limited to batch manufacturing. It’s equally essential for discrete manufacturing and businesses with diverse manufacturing processes that handle perishable inventory.
Using batch management software with batch number tracking allows you to:
- Track the expiry date of items
- Track defective items back to the production batch
- Enable an efficient product recall process
- Comply with legislation and requirements for your industry
An example of a business or industry that uses a batch tracking system is a company that makes beauty products.
Picture a cosmetics manufacturer producing a face cream that fights off the onset of wrinkles. It’s wonderful! But one day, a customer contacted them saying they bought a cream that contained a cornflake.
As the company waits for the cream to be returned, they use their cosmetics production software to track down the batch and remove it from inventory to avoid more faulty products going into circulation and damaging their reputation.
Besides the beauty industry, let’s see who else benefits from batch management systems.
Who needs to use batch tracking?
Batch management systems are essential to streamline tracking, allowing you to monitor your inventory efficiently, but finding inventory management software with batch number tracking is especially important for industries such as:
These industries often need to keep track of perishable raw materials or perform product recalls should something go awry. That’s why they require end-to-end traceability. The simplest, fastest, and most reliable way of tracking the location of your products is through the use of traceability software.
Next, let’s take a look at the benefits batch tracking brings to your operations.
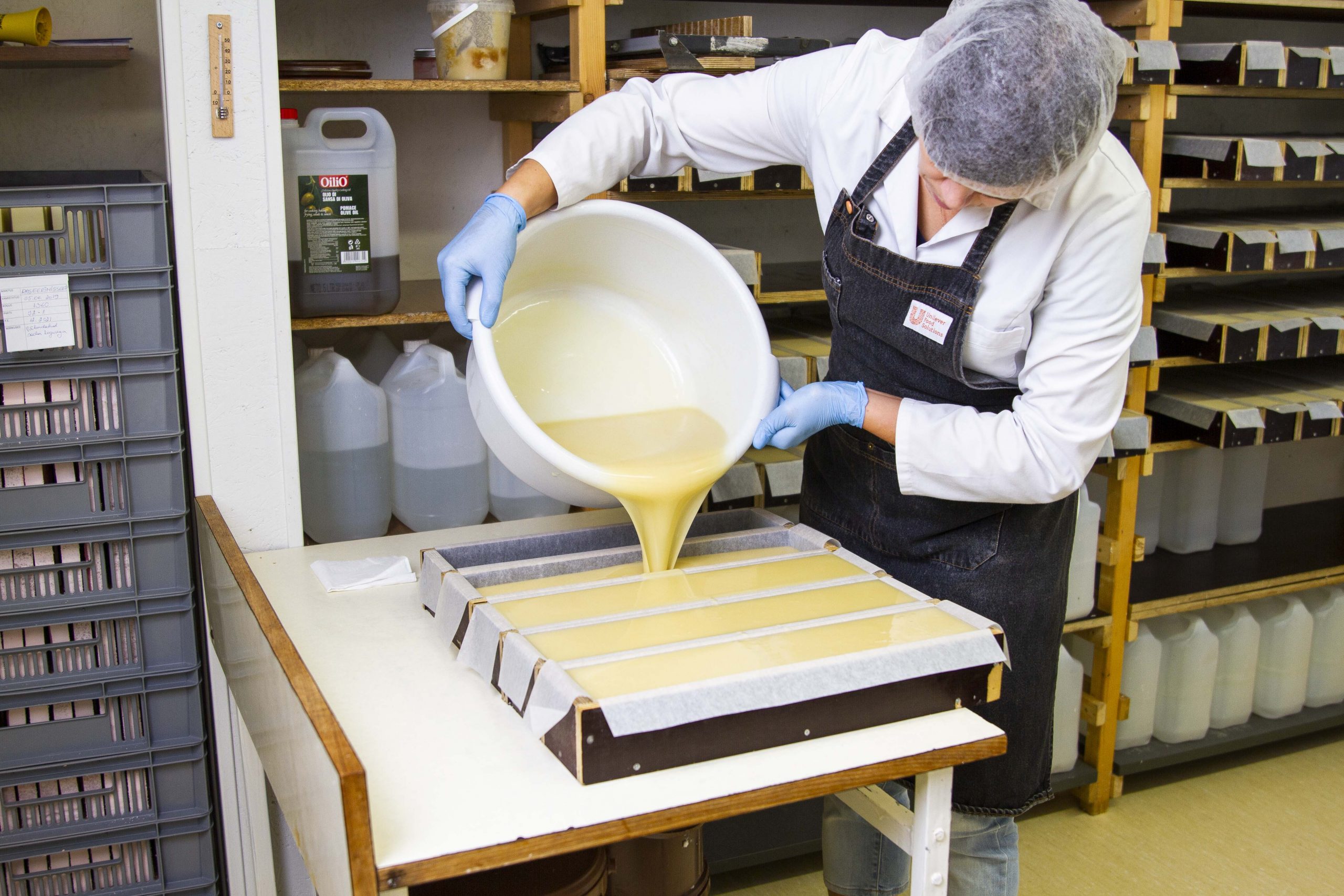
Benefits of batch tracking
Batch tracking can greatly improve your business operations and introduce a wide range of benefits. It can help you achieve consistently high product quality, increase efficiency, and allow you to fix issues a lot quicker. Here is a list of the benefits you can expect when implementing batch tracking:
- Improved quality control — Batch tracking can greatly help in maintaining product quality. Businesses can quickly identify and isolate batches that don’t meet quality standards. This increases customer satisfaction and reduces the risk of product recalls and related financial losses.
- Regulatory compliance — Many industries are subject to strict regulations regarding product traceability and safety. Batch tracking systems help businesses meet these regulatory requirements, avoiding fines, legal consequences, and damage to their reputation.
- Efficient recall management — In the unfortunate event of a product recall, batch tracking allows you to pinpoint affected products. This targeted approach reduces the scope of recalls, minimizes losses, and preserves customer trust.
- Improved inventory management — Batch number tracking provides real-time data on the status and location of products. You can use that for inventory management, helping you to optimize stock levels, reduce carrying costs, and prevent overstocking or stockouts.
- Streamlined production processes — With batch tracking, you can monitor the entire production process, from raw materials to finished products. Having this visibility enables you to identify bottlenecks, optimize workflows, and increase overall efficiency.
- Cost reduction — Although implementing batch tracking may require an initial investment, the long-term benefits often result in cost savings. Fewer recalls, optimized production, and reduced waste all contribute to a healthier bottom line.
- Supply chain visibility — Batch tracking extends beyond the boundaries of your business. It provides insights into your supply chain, allowing you to track the movement of products from suppliers to customers, facilitating a more agile and responsive supply chain.
- Quick issue resolution — In the event of product issues or disputes, batch number tracking allows businesses to resolve problems more efficiently. The ability to trace products back to their source can help clarify the cause of issues and identify responsible parties.
These benefits are not limited to a specific industry or business size. Whether you’re a small manufacturer or a large-scale distributor, implementing a batch tracking system can have a positive impact on your operations and overall success.
The benefits are clear, so let’s see what steps you need to take to implement batch tracking into your business.
How to set up batch tracking
To set up batch tracking, you need to assign unique identifiers to groups of products or materials and record relevant data to track their journey. Let’s go over the process step-by-step.
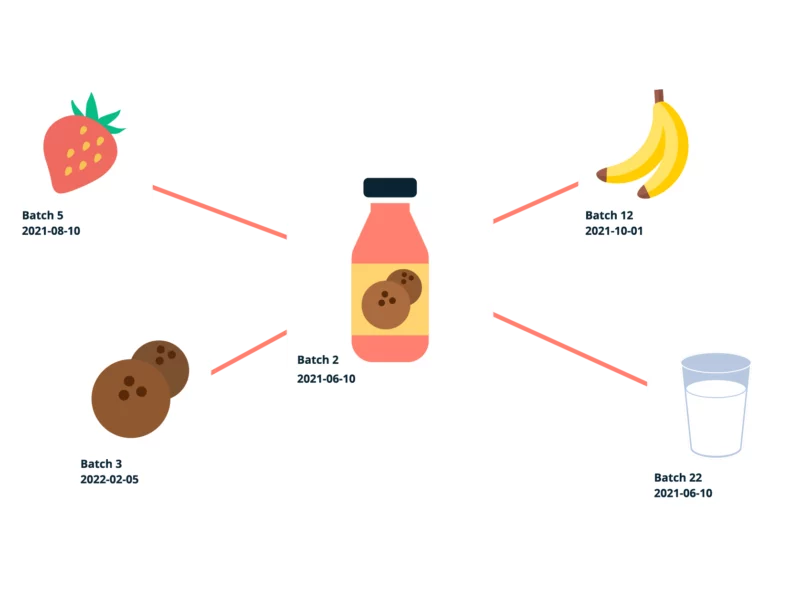
1. Define a standard format
Decide on a standard format for your batch numbers. This format should be consistent and easy to understand. It may include letters, numbers, or a combination of both.
Common formats include date-based codes (YYMMDD), sequential numbers, or a combination of product type and production date.
2. Invest in technology
To efficiently manage batch numbers, consider using warehouse inventory management software. These tools can automate the process and ensure accuracy.
3. Assign unique batch numbers
For each batch of products or materials, assign a unique batch number. This number should be specific to the group and not repeated for other batches.
Make sure the numbering system you choose is easy to read, with no room for confusion or duplication.
4. Record batch information
Create a batch tracking record for each batch. This record should include details like:
- Batch number
- Date of production
- List of ingredients or materials used
- Production location
- Personnel involved
- Quality control checks
Make sure this information is accurate and consistently recorded.
5. Label products
Attach batch number labels to the products or materials in the batch. These labels should be easily visible and scannable if using barcode scanners.
6. Implement a tracking system
Use a tracking system that allows you to record the movement and status of each batch as it progresses through your business. This can be a combination of software, hardware, and manual record-keeping.
Update the system in real time or at regular intervals to ensure accurate tracking.
End-to-end traceability with Katana
Adopt Katana’s batch tracking software to ensure regulatory compliance and consistently high quality standards for all batches.
7. Training and education
Train your staff on the importance of batch tracking and how to correctly assign and record batch numbers. Ensure they understand the significance of accurate data entry.
8. Data Security
Protect the data associated with batch numbers. Use secure storage and access controls to prevent unauthorized changes or data breaches.
9. Regular audits
Conduct regular audits to verify the accuracy of your batch tracking system. Ensure that batch numbers match recorded data and that the system is functioning correctly.
10. Document retention
Maintain batch tracking records for a specified period in compliance with any regulatory requirements. Archived records can be essential for historical analysis and addressing quality control issues.
11. Scalability and flexibility
Ensure that your batch numbering system can scale as your business grows. It should accommodate new products, increased production volumes, and changes in production processes.
12. Continuous improvement
Regularly review and improve your batch tracking processes. Seek feedback from your team and incorporate best practices as you identify them.
As discussed in the previous section, setting up batch tracking offers numerous benefits for quality control, compliance, and operational efficiency. It’s an investment in the long-term success and reliability of your business, no matter the industry you operate in.
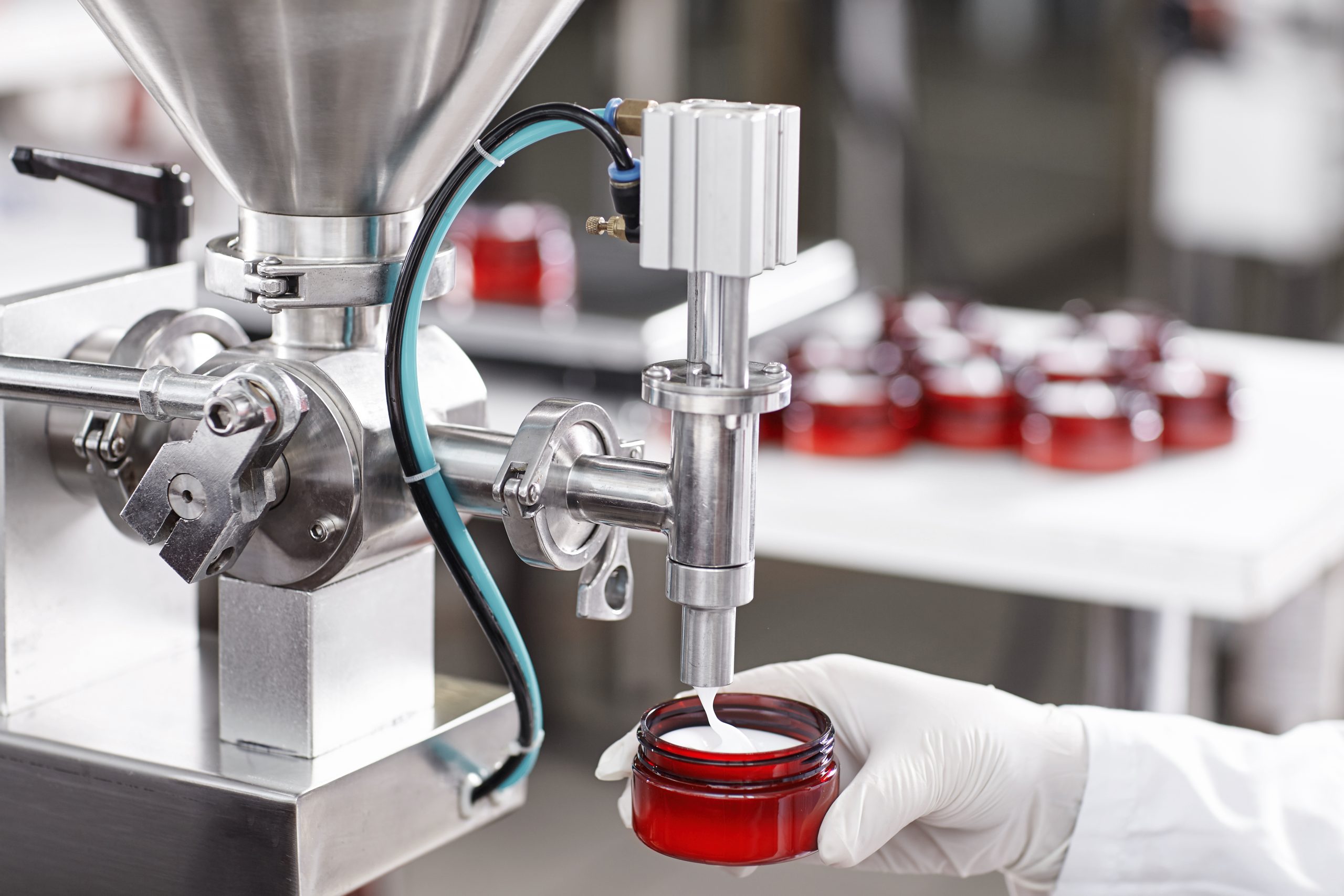
Batch tracking inventory strategies
This section explores three main inventory management strategies that utilize batch tracking:
- FIFO
- LIFO
- FEFO
Each of these methods offers distinct advantages and is tailored to specific business scenarios. Whether dealing with perishable goods, managing costs, or prioritizing product safety, understanding these strategies is crucial for streamlining your inventory management and achieving compliance with industry standards.
FIFO (first-in, first-out)
FIFO is a widely adopted batch tracking strategy that operates on the principle that the first batch of products received or produced is the first to be used or sold. In other words, older batches are utilized before newer ones.
This method is particularly valuable for industries dealing with perishable goods, such as food, cosmetics, or pharmaceuticals, as it minimizes the risk of spoilage. FIFO ensures that products are distributed in the order they were obtained, which can be crucial for quality control and adherence to expiration dates.
LIFO (last-in, first-out)
Conversely, the LIFO strategy dictates that the most recently acquired or produced batches are the first to be consumed or sold. LIFO can be beneficial for businesses in situations where there is a steady increase in product costs over time.
While this approach may not align with ideal inventory turnover practices, it can offer certain tax advantages by reducing taxable income through the use of more recent, higher-cost batches.
Can you use LIFO?
It’s worth emphasizing that LIFO is prohibited under the International Financial Reporting Standards (IFRS), the accounting standards adopted in various countries, including the European Union, Japan, Russia, Canada, India, and many others.
Notably, the United States of America remains the sole exception, permitting LIFO due to its adherence to the Generally Accepted Accounting Principles (GAAP).
If you wish to read more about the subject, check out the article about FIFO vs. LIFO.
FEFO (first-expired, first-out)
FEFO is a strategy that focuses on the expiration dates of products within batches. The primary objective is to make sure products with the earliest expiration dates are used or sold first.
This approach is crucial for industries where product safety and regulatory compliance are paramount, such as pharmaceuticals and food. By prioritizing batches based on their expiry dates, FEFO helps minimize waste and reduce the risk of selling expired products.
Each of these batch tracking strategies has its own set of advantages and is suitable for specific business contexts. Businesses should carefully consider their product type, industry regulations, and cost structures to determine which strategy aligns best with their operational needs.
Properly implementing one of these strategies can lead to more efficient inventory management, better product quality control, and compliance with industry standards.
Batch tracking with Katana
Katana is a cloud inventory software that helps businesses get control over their inventory by helping them trace batch movement and track product development.
Let’s go over some of the benefits a batch tracking system like Katana provides.
Expiration date tracking
Tracking the expiration date of items allows you to implement effective inventory management, reduce spoilage, and increase profitability.
However, expiration dates aren’t only useful for food traceability. With this feature, you can track items that will eventually become outdated or unsellable (depending on trends and technology).
Trace defective items back to the batch
We’ve spoken about product recalls within this article, and although they’re commonplace, the best practice is to avoid them altogether.
A batch inventory management system means if you discover a faulty product, you can trace it back to the batch it came from, significantly reducing the risk of defective products making it onto the market.
Tracing your defective products means better transparency and easier compliance.
Make the product recall process easier
If you need to arrange a product recall, you can track the locations of all your products.
This is important because, according to a study by Motley Fool, 87% of respondents¹ said they would still shop with a company that conducted their product recall honorably and responsibly.
While it is possible to do your production tracking manually, to do so will be a slog and will ultimately cost you:
- Time
- Money
- Your reputation
That’s why it’s important to get set up with a batch inventory management system that can integrate with all your other software to give you an overview of your entire business and get the smoothest workflow.
If you wish to see Katana in action, request a demo and see how it can help you achieve streamlined tracking in your business today.
Batch tracking FAQs
Batch tracking is a systematic process of monitoring and managing groups of products or materials, known as batches, throughout their entire lifecycle within a business.
This method involves assigning a unique identifier to each batch and recording essential data related to its production, movement, and status. Batch tracking is essential for maintaining product quality, ensuring regulatory compliance, and improving operational efficiency.
An example of batch tracking can be found in the pharmaceutical industry. In this context, each batch of medication is assigned a unique batch number, and detailed records are maintained. These records include information about the production date, ingredients used, quality control checks, and distribution.
If a quality issue arises or a product recall is necessary, batch number tracking enables the swift identification and removal of affected medication.
Batch traceability is the ability to trace the complete history and journey of a specific batch of products or materials within a business or supply chain. It involves tracking the batch’s origin, production processes, quality checks, and distribution, often through the use of unique identifiers and detailed records.
Batch traceability is crucial for product quality control, regulatory compliance, and swift issue resolution.
Tracking a batch number involves the following steps:
- Unique identifier — Assign a unique batch number to each group of products or materials.
- Data recording — Maintain detailed records for each batch, including production date, ingredients used, quality checks, and any other relevant information.
- Labeling — Attach batch number labels to the products or materials in the batch. These labels should be easily visible and scannable if using barcode technology.
- Tracking system — Utilize a tracking system, which can be a combination of software, hardware, and manual record-keeping. Update the system in real time or at regular intervals to ensure accurate tracking.
- Training — Train your staff on batch tracking procedures and the significance of accurate data entry.
By following these steps, you can effectively track batch numbers, maintain product traceability, and benefit from improved product quality and operational efficiency.
Sources
¹Total Recall: Do Consumers Drop Brands After Products Fail, The Motley Fool (2016)
Table of contents
Inventory management guide
More on inventory management
Get visibility over your sales and stock
Wave goodbye to uncertainty by using Katana Cloud Inventory for total inventory control
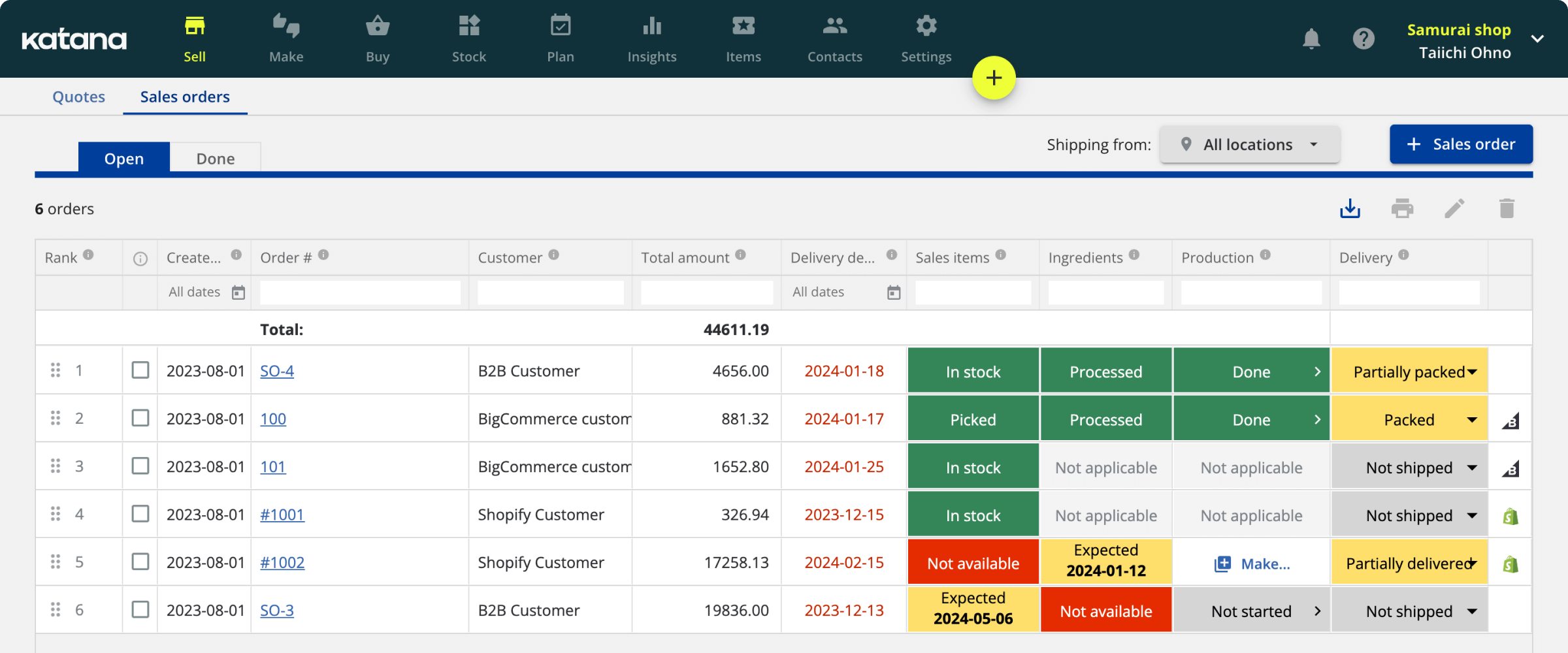