15 reasons designers need apparel inventory management
Between designing and making apparel items, it’s easy to lose focus when managing inventory. Here are 15 reasons you need to optimize your inventory management.
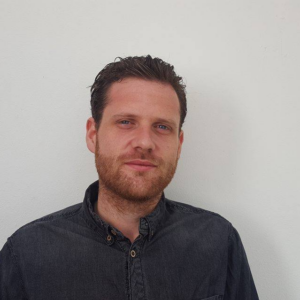
James Humphreys
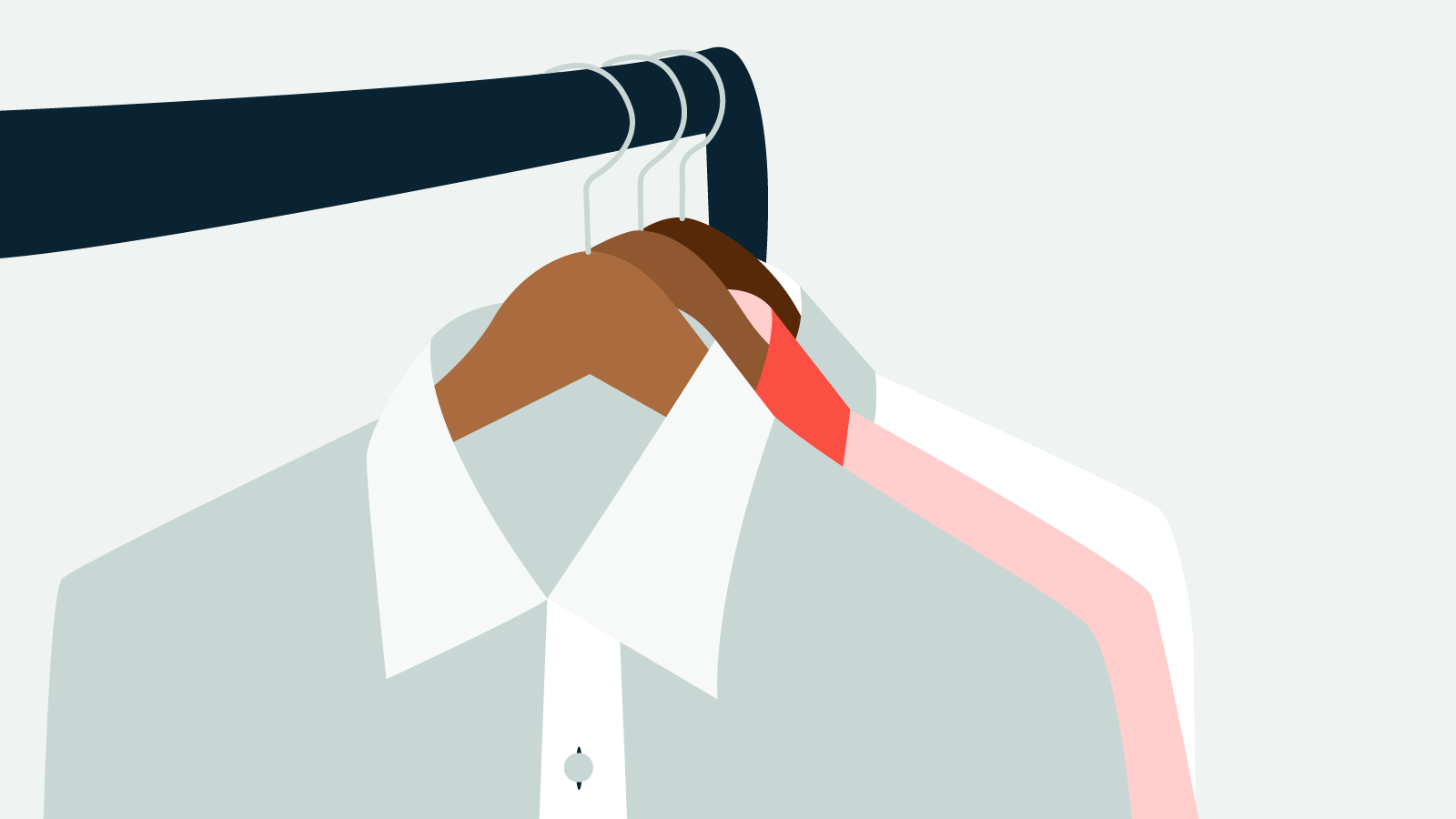
According to research published on Statista, in 2022, global retail sales of apparel reached $1.53 trillion — that’s a lot of cheddar.
It would be a shame to realize how much money you could stand to make, only to then hemorrhage money out of your company due to some unforeseen issue with their inventory. After all, a report by Coresight Research and Celect revealed that roughly $300 billion in revenue was lost due to markdowns in 2018. Figures of this size are enough to make your head spin.
That’s why we’ve put together this article highlighting 15 reasons why apparel businesses need to optimize their fashion inventory management.
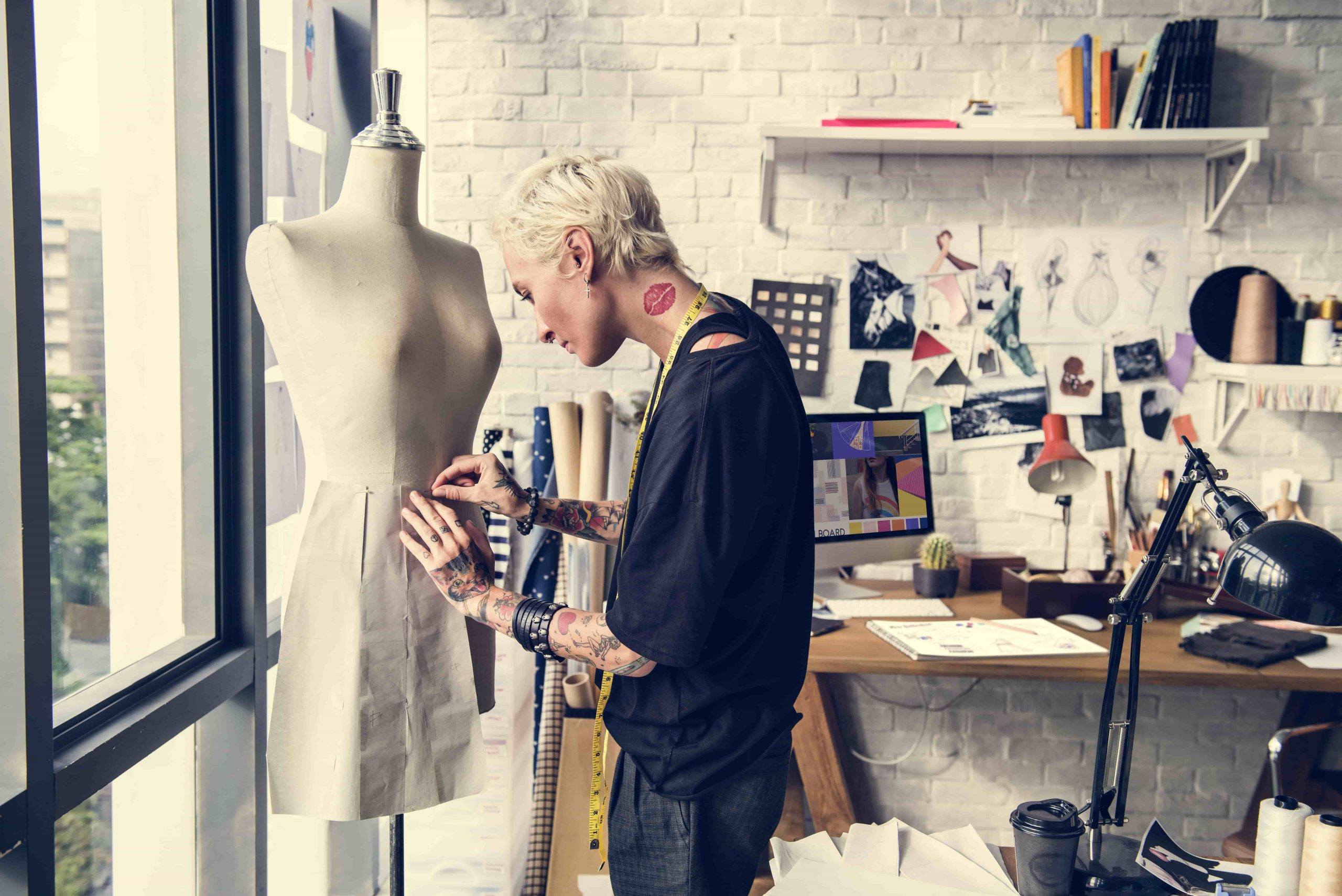
Why do you need apparel inventory management in your business?
Nowadays, designers and retailers aren’t limited to selling from a physical inventory location.
The rapid growth of e-commerce means fashion inventory management helps merchants manage their clothing, apparel, and jewelry inventory at physical locations like brick-and-mortar stores or marketplaces and manage clothing stock levels from their online sales channels.
Without the proper solutions for apparel in place, it won’t take long before there are problems understanding where your clothing stocks are at any given time. Aside from being able to manage inventory for your clothing business better, optimized fashion inventory management helps you:
- Track your sales orders
- Track your manufacturing orders
- Track your purchasing orders
- Manage your bill of materials
- Gather analytics on inventory
- Improve your bottom line
- Keep transactions secure
How exactly do other manufacturers set up and organize their apparel inventory management? The three most common methods are:
- Paper-based system
- Spreadsheet system
- Apparel inventory software
Paper-based system
All inventory information is written down on paper, which is great for micro-businesses or individual sellers handling stock at one location.
One of the biggest time wasters when depending on paper is that the information on the document itself may be outdated or incorrect. This creates “the paper chase,” where workers spend hours looking for the most recent information instead of getting their work done. In addition, having everything written down on paper makes it difficult to track changes or modifications to the inventory.
Spreadsheet system
A clothing inventory spreadsheet is a type of system that allows users to create and edit data tables.
This makes spreadsheets the perfect tool for tracking inventory, as it allows users to track an item of clothing by category, quantity, and other criteria. There are numerous benefits to using a spreadsheet for inventory management solutions since spreadsheets are easy to use and can be customized to fit the needs of any company or organization.
They are also versatile, meaning they can be used for various tasks beyond just inventory management. Additionally, spreadsheets are free and can be accessed from any computer with internet access.
There are also a few drawbacks to using a spreadsheet for inventory management:
- Spreadsheets can be difficult to learn and use for those unfamiliar with them
- They can be time-consuming to set up and customize
- If not used correctly, spreadsheets can be prone to errors
Solutions for apparel inventory management
Many manufacturers use apparel inventory management solutions made for retailers to track and manage their inventory.
These types of software include:
- Inventory reports
- Backorders
- Inventory optimization
- Multichannel sales
- Order management
- Sales reports
Apparel inventory management helps businesses keep track of their stock count to ensure they always have enough products on hand to meet customer demand. Additionally, this type of clothing inventory management app can help companies save money by reducing the need for excess or overstocked inventory.
This software typically works by tracking stock levels and sales data. Then, these data is used to generate reports that help businesses understand:
- Their current inventory levels
- What products are selling well
- What needs to be reordered
Apparel sales revenue increased by 29.8% in 2022
From 2021 to 2022, the fashion industry experienced 18 months of robust growth. However, how does that look now, and will it be the case in 2024? Download the State of Inventory Management report.
The reasons why manufacturers and designers need to optimize their apparel inventory management
We’ve looked at the three different apparel inventory management methods sellers can use. Depending on which you use, some require a lot of manual intervention from yourself or staff to keep updated to avoid problems, while others are better suited for larger SMB companies. Regardless of the method, each has its own pros and cons.
However, the biggest difference between the three methods is how apparel management software automates a lot of your day-to-day activities.
With that said, here are the 15 reasons designers and manufacturers need to optimize inventory for their clothing business.
1. Reduce inventory errors
By implementing an improved inventory of merchandise, you can reduce the number of inventory errors in your business.
A good solution will automate many of the tasks involved in managing inventory, making it easier and less error-prone. It will also provide you with detailed reports and analytics that can help you track your inventory levels and performance over time. You can set up alerts and notifications to remind you when to order more merchandise or restock your shelves with an automated system.
2. Reduce carrying costs
By keeping track of inventory levels and efficiently using available clothing inventory storage space, businesses can minimize the cost of holding onto unsold merchandise.
Apparel businesses can also use inventory management software to help keep track of stock levels and reduce carrying costs. This type of software can automate many tasks associated with managing inventory, including order tracking, stock level alerts, and reordering merchandise.
By using these tools and strategies, apparel businesses can effectively reduce their carrying costs and keep more of their inventory in stock.
3. Reduce out of stock
Reducing stockouts is essential for any retailer, as it can lead to lost sales and unhappy customers.
Apparel inventory management is one way that retailers can help avoid running out of stock. Here are a few ways that inventory management can help to reduce stockouts:
- Automated stock replenishment
- Accurate inventory tracking
- Seasonal stock planning
- Buying in bulk
- Planning for peak demand periods
- Use of drop shippers
- Outsourcing order fulfillment
These methods can help ensure that retailers have the right amount of stock on hand and that they are not running out of product or overstocking. By using these methods, retailers can minimize the chances of experiencing a stockout.
4. Increase supply chain accuracy
Apparel inventory management can help to ensure that all items in the supply chain are accounted for and tracked.
This means that if there is ever a problem or discrepancy, it will be easier to identify and resolve. Inventory management can also help to streamline the overall supply chain by reducing waste and improving efficiency. By having better control over inventory, businesses can avoid overstocks and stockouts, leading to lost sales and disruptions in the supply chain.
5. Improve demand planning
Having an accurate forecast of customer demand allows you to meet that demand better while also reducing operational costs.
To do this, businesses need to clearly understand their customer base and what they are likely to purchase in the future. Additionally, businesses need to have visibility at their inventory levels so they can adjust their production accordingly. By considering these factors, businesses can ensure that they are able to forecast customer demand more accurately and ultimately improve their bottom line.
6. Optimize fulfillment
The most important thing is making sure your stock inventory is correctly categorized and organized.
You can easily identify what needs to be restocked and ensure that you always have the right items available for customers. Additionally, keeping track of inventory levels and ordering new stock can help avoid unnecessary delays or out-of-stocks. Using an automated system can make managing your apparel inventory much simpler and more efficient.
7. Streamline production
An effective clothing inventory management system can help to streamline operations and improve profitability.
By ensuring that accurate measurements and specifications are entered into the system, ordering materials and supplies in a timely manner, tracking finished goods, and providing accurate reports on inventory levels and stock turnover, an effective inventory management system can help to ensure that your production process is as efficient as possible.
8. Increase customer satisfaction
Apparel inventory management is crucial to maintaining customer satisfaction, especially regarding product returns.
If a product is returned because it is damaged or defective, you can arrange with the manufacturer for an instant swap to keep the customer happy. In addition, having a good inventory management system in place will help you keep track of stock levels and ensure that products are available when customers need them. This can help reduce frustration and increase satisfaction levels overall.
9. Keep investors happy
By analyzing inventory ratios over time, investors can better understand the company’s overall financial health now and into the future.
Inventory management is an important aspect of any business, but it’s especially important for companies in the apparel industry. Apparel companies must be able to move quickly to keep up with fashion trends and prevent their inventory from becoming outdated. Efficient inventory management can help a company avoid these problems and keep investors happy.
10. Loss prevention
A National Retail Federation report claims that the U.S. retail economy lost $112.1 billion in 2023.
One of the benefits of tracking retail inventory throughout its journey is that it helps prevent loss due to theft from warehouses or storefronts.
Understanding where inventory is at every step of the supply chain makes it easier to identify when and where theft is happening so that proper steps can be taken to stop it. This can result in a reduction in losses for both retailers and suppliers.
In some cases, it may even be possible to track down the individuals responsible for the theft and bring them to justice.
11. Better space management
Warehouse management system (WMS) is an important part of apparel inventory management and fashion warehouse organization.
Routing manufacturing helps to optimize the pick path for workers, schedule docks, and manage cross-docking. This ensures that goods are managed properly from receipt to shipping. Ultimately, this helps to improve the efficiency of the warehousing of clothes and ensure that the correct goods are shipped out to customers.
12. Remove administrative errors
There are many ways that a clothing inventory management system can help remove administrative errors from your day-to-day activities.
It can automate taking inventory so that you don’t have to rely on your staff to adjust inventory manually. Additionally, it can keep track of your inventory levels in real time to always know exactly what you have in stock. This way, if something does go wrong, you’ll be able to catch it quickly and correct the issue before it causes any major problems. Overall, using an inventory management system is the best way to ensure that your business runs smoothly and efficiently.
13. Remove dead stock
One of the most important ways to remove dead stock is through efficient inventory management from day one.
If you can manage your inventory effectively, you’ll be able to identify and remove dead stock before it becomes a problem. By doing this, you’ll be able to improve your bottom line and keep your business running smoothly.
14. Improve bottom line
Apparel inventory management is vital to ensuring that a company’s bottom line is not adversely affected.
Efficient inventory management plays a crucial role in enhancing a business’s bottom line. By monitoring and maintaining optimal stock levels, companies can sidestep the expensive pitfalls associated with overstocking or understocking their inventory.
15. Better product rotation
By keeping track of what items are in stock and where they are located, retailers can ensure that new products are placed in strategic locations.
This might mean putting newer items on shelves near the front of the store or in high-traffic areas. Additionally, retailers can use data from previous sales to predict which items will be popular in the future and make sure those items are well-stocked. By closely monitoring inventory levels, retailers can avoid overstocking their shelves with unpopular items that will eventually need clearance.
By following these guidelines, retailers can keep their products moving quickly and efficiently to meet customer demand.
Download the ultimate guide to inventory management
A comprehensive ebook with everything you need to know about inventory management.
Apparel inventory software for fashion businesses
As earlier mentioned in the article, managing your apparel with an inventory sheet on paper or in spreadsheets is fine — in the beginning.
But, once your business starts to expand, you’ll see how difficult it is to run your business and maintain these documents alongside each other. This is where the power of automation truly shines. Apparel manufacturing software gives you a competitive edge by using a tool to track and help you automatically fulfill repetitive day-to-day inventory management tasks.
Katana is the perfect ally for designers and businesses looking for:
- End-to-end production management
- Real-time automated inventory management
- Automatic and accurate cost calculations
- Seamless integrations with your favorite e-commerce, accounting, reporting tools, and platforms
Katana’s fashion ERP software supports 1000s of businesses. Book a demo and see how you, too, can take your production and operations to the next level.
Apparel inventory management FAQs
What is inventory management in the apparel industry?
Inventory management in the apparel industry involves overseeing the flow of goods from manufacturers to warehouses and ultimately to retail outlets or directly to customers. It encompasses the tracking of physical inventory — such as clothing items and accessories — as well as raw materials required for textile manufacturing, like fabrics and threads, ensuring that there’s enough stock on hand to meet demand without overstocking.
Effective inventory management helps apparel businesses minimize costs, optimize their supply chain, and improve customer satisfaction by ensuring the right products are available when and where they’re needed.
How do you keep track of clothes inventory?
Keeping track of clothes inventory requires a systematic approach, often supported by specialized software. Here are a few key methods:
- SKU system — Implementing a stock keeping unit (SKU) system allows for the unique identification of each item, including size, color, and style, making it easier to track inventory levels
- Barcode scanning — Utilizing barcode scanning can streamline the process of checking items in and out and updating inventory records in real time
- Regular audits — Conducting regular physical counts of inventory ensures that digital records match the actual stock on hand, helping to identify discrepancies and adjust records accordingly
- Software solutions — Inventory management software, like Katana, can integrate these practices into a cohesive system, offering real-time visibility into inventory levels, facilitating easier restocking decisions, and optimizing the supply chain
How do you manage fabric inventory?
Managing fabric inventory involves several specific strategies to ensure that the right materials are available for production without excessive overstock:
- Cataloging materials — Keep detailed records of fabrics, including type, color, weave, and supplier, using a system that allows for easy retrieval of information
- Tracking usage — Monitor how much fabric is used for each product to forecast future needs more accurately and reduce waste
- Storage solutions — Implement effective storage solutions that protect fabrics from damage and make it easy to access and count stock
- Software for raw materials management — Utilize inventory management software, such as Katana, which is designed to handle raw materials like fabric. This can help in accurately tracking material usage per product, predicting future material requirements, and managing supplier relations
Katana offers a solution that is tailored to the needs of the apparel industry, allowing businesses to seamlessly manage both finished goods and raw materials. With features designed to enhance visibility, efficiency, and control over inventory, Katana can help apparel businesses of all sizes stay agile and responsive to market demands.
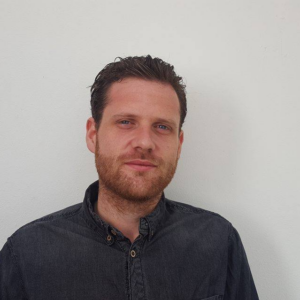
James Humphreys
Table of contents
Get inventory trends, news, and tips every month
Get visibility over your sales and stock
Wave goodbye to uncertainty with Katana Cloud Inventory — AI-powered for total inventory control