Streamline your work in process inventory management
You’ve probably heard of work in process or work in progress, but what does it actually mean in manufacturing?
You’re correct if you guessed it’s a way to refer to unfinished business. But since unfinished business sounds a bit too ominous, manufacturers have decided to use the term work in process instead. You may also hear the term work in progress, but generally, that’s used more in the construction industry when talking about unfinished projects.
Below, we’ll get into more details about what work in process exactly is, the benefits, and how you, as a manufacturer, can manage work in process inventory efficiently.
What is work in process?
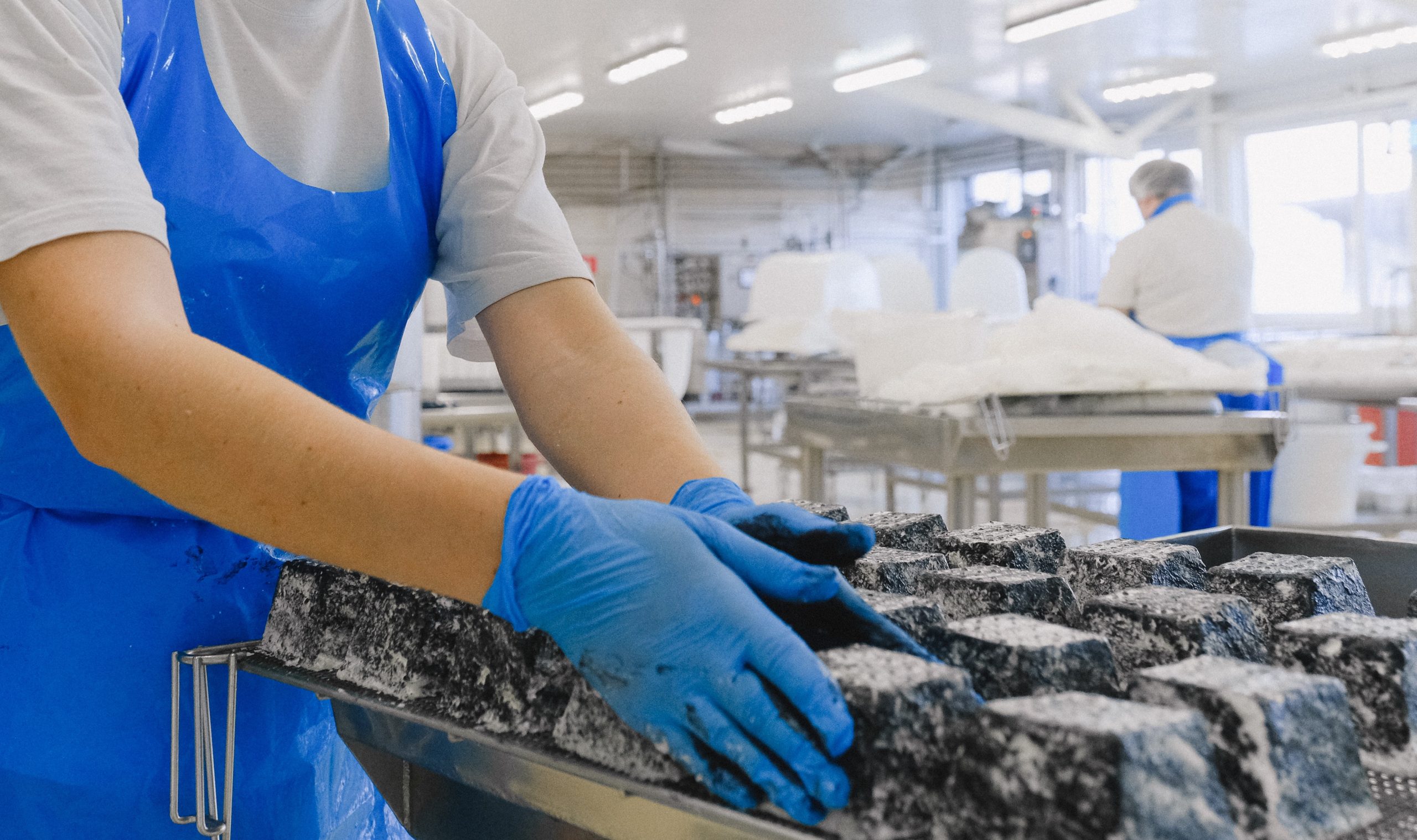
Work in process (WIP) is inventory being worked on but isn’t ready to be shipped out yet. In other words, it’s goods that are in the middle of the production process. Work in process can also be used to refer to the total value of these goods.
As a work in process inventory example, let’s say your company manufactures bicycles. The process of creating each bike might look something like this:
- Frames are built in the welding department
- The frames move to the painting department, where they’re painted
- Then, they go to the assembly line, where all the other parts are added
- Finally, the bikes are inspected and packaged for shipping
The inventory is considered work in process at each stage of this process, except the last because it hasn’t been completed yet. When the bike is finally inspected and packaged, it’s considered finished goods and ready to be shipped out.
Want to see Katana in action?
Book a demo to get all your questions answered regarding Katana’s features, integrations, pricing, and more.
Work in process inventory calculation
To calculate WIP, you’ll need to know your beginning WIP inventory, manufacturing costs, and cost of goods manufactured (COGM). Your manufacturing costs include the direct raw materials, direct labor, and overhead associated with making your product.
Work in process inventory formula:
WIP = beginning WIP inventory + manufacturing costs – COGM
As a work in process inventory example, let’s say your company starts the year with $100,000 in WIP inventory and adds $200,000 in direct labor and materials during the year. If the cost of goods manufactured and shipped during the year is $300,000, then your WIP at the end of the year would be:
WIP = $100,000 + $200,000 – $300,000
This means that you ended the year with no WIP inventory, which is ideal. In reality, most companies will have some WIP inventory at the end of the year, but the goal is to keep it as low as possible.
The cost of the beginning WIP inventory is the cost of the unfinished goods that were in production at the beginning of the period. It’s worth pointing out that this year’s beginning WIP is last year’s ending WIP inventory. Therefore, you can just look at the previous period’s ending WIP.
What are the benefits of work in process?
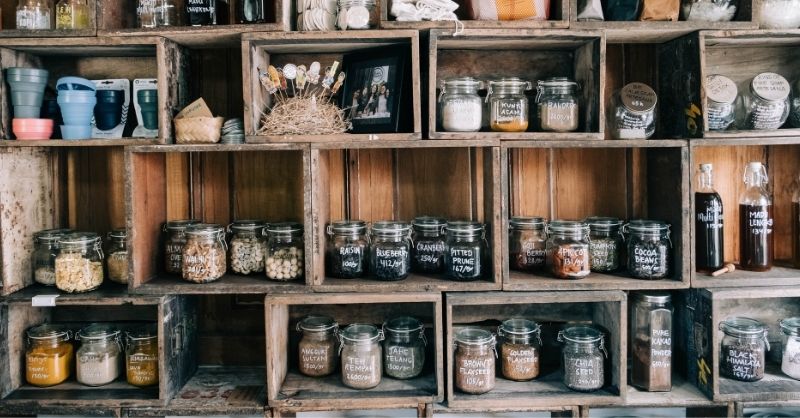
There are a few reasons why WIP can be beneficial for manufacturers. Let’s take a look at each of these benefits in more detail.
WIP can help even out production
If a manufacturer is constantly starting and stopping production, it can be costly and inefficient. With some WIP on hand, manufacturers can keep the assembly line moving even when disruptions or slowdowns occur. This helps to even out production and make the manufacturing process more efficient.
WIP can provide a cushion if there are delays
If there are delays in the production process, having some WIP can help to keep things on track. For example, if the painting department is behind schedule, the frames that are already painted can be moved to the assembly line so that they’re not sitting idle. This helps to keep production moving even when there are delays.
WIP can help you take advantage of economies of scale
If you have a lot of WIP on hand, you can take advantage of economies of scale. This means you can buy raw materials in bulk, saving you money. Additionally, you can utilize assembly line workers more effectively since they’ll always have something to do.
WIP and the balance sheet
The work in process inventory account and the finished goods inventory account are both classified as current assets on the balance sheet. The main difference is that WIP is considered to be a short-term asset while finished goods are considered to be long-term assets.
The reason for this is that WIP is in the process of being turned into finished goods. Once the goods are completed and packaged, they’re considered finished goods. However, if it’s taking longer than a year to turn WIP into finished goods, it might be classified as a long-term asset.
Managing work in process inventory
In any manufacturing or production process, keeping track of WIP is essential. The most effective way of doing it is utilizing a software system like an ERP that allows you to track WIP inventory.
With Katana, you can track WIP inventory levels at each stage of the production process. This information is updated in real time, showing exactly how much WIP you have on hand, where it is located, and what stage of the production process it is in. Katana’s manufacturing ERP also provides tools to help you manage your WIP inventory effectively, such as the ability to set reorder points, so you know when WIP levels reach a certain threshold.
Katana’s ERP is the perfect solution if you want to improve your WIP tracking and management. Get a demo to see Katana in action.
Table of contents
Inventory management guide
Get visibility over your sales and stock
Wave goodbye to uncertainty by using Katana Cloud Inventory for total inventory control
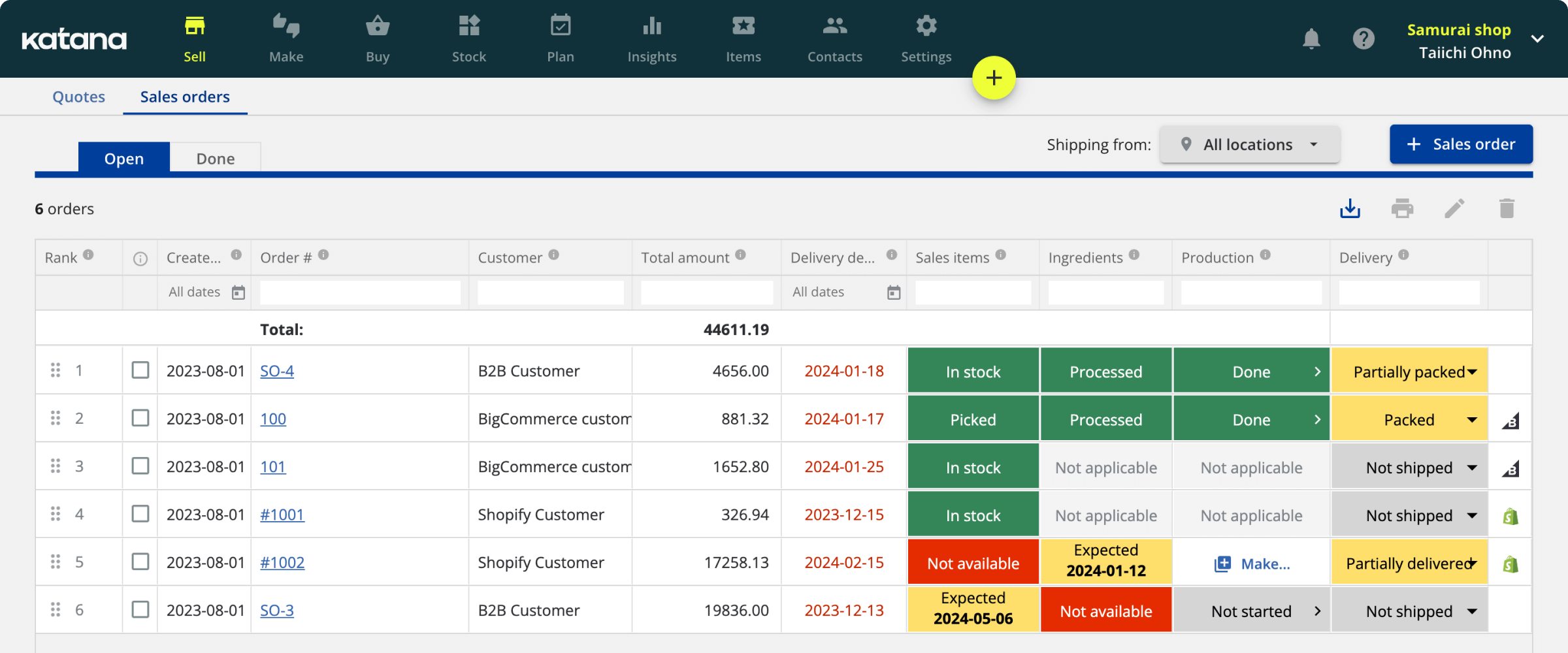