How to protect your business with inventory planning
Are you tired of playing hide-and-seek with your inventory? Do you feel like you’re constantly in a race with stock either running out or overflowing your spaces? Well, fear not! Inventory planning is here to save the day (and your sanity). With forecasting and strategic ordering, you can say goodbye to the chaos and hello to an organized supply chain. So make inventory planning your new favorite game and enjoy a winning streak!
What is inventory planning?
Inventory planning is the process of managing and tracking the inventory of a business. It involves tracking the quantity, type, and value of items in stock while also planning for future needs and ordering new supplies when necessary.
Inventory management planning can be done manually using spreadsheets and files, but more and more businesses are opting for software and online solutions. They’re more reliable as they offer real-time updates on stock levels and automatic analytics.
What are the biggest challenges in inventory management planning?
Inventory planning can be a complicated process, but there are several key challenges that should be addressed to make your daily work that much easier. These include:
- Accurate forecasting
- Supply chain visibility
- Managing multiple locations
- Seasonal fluctuations
1. Accurate forecasting
It can be difficult to accurately forecast demand for inventory items, which can lead to stock shortages or overstocking. Forecasting can be improved by using the correct tools and specialty software.
2. Supply chain visibility
Having visibility into your entire supply chain is essential to ensure that stock levels are always accurate. Tracking your inventory from raw materials to manufacturing to sales leaves minimal room for errors or theft.
3. Managing multiple locations
When operating in multiple locations, stock-level tracking and efficient inventory management across all those locations can be challenging. Once you have an overview of your entire inventory, it is easier to move stock from one warehouse to another and make overall better business decisions.
4. Seasonal fluctuations
Seasonal changes can have an impact on inventory levels, and it’s important to plan accordingly for these fluctuations in demand. Working with past data will give you insights into trends that you can take into consideration when planning ahead.
What are the benefits of planning inventory management?
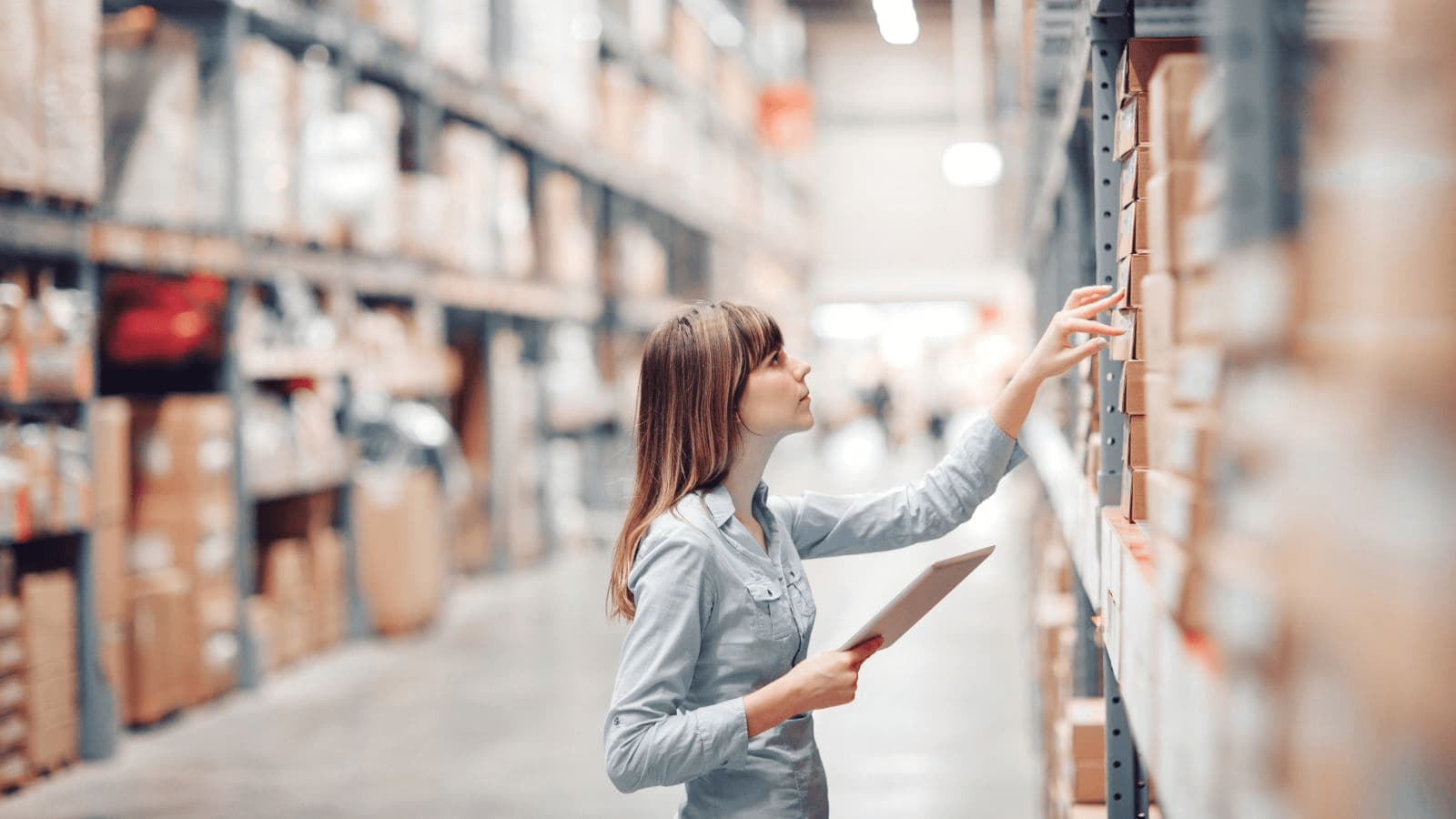
Overall, stock planning makes managing inventory easier for you and your teams. As with anything else, creating a plan to work things out ahead helps avoid having to fix them afterward.
Some of the main benefits of inventory planning include:
- Overview of stock levels
- Better customer relationships
- Insights into inventory data
1. Overview of stock levels
By taking a proactive approach to inventory management, businesses are able to plan ahead for future orders and ensure they have the right items in the right quantities at the right time. That helps them avoid overstocking or understocking, resulting in reduced costs.
2. Better customer relationships
Businesses gain a higher customer satisfaction rate due to the timely delivery of products and more accurate lead times. A good inventory plan streamlines the manufacturing and sales flows, which is only good news for your buyers as more optimized processes mean lower costs and more wallet-friendly prices.
3. Insights into inventory data
Supply chain management becomes more efficient when businesses use inventory planning as they gain better insights into their inventory data, enabling them to adjust production schedules or promotional campaigns accordingly.
Take control of your stock
Try inventory planning in Katana and lower your costs while increasing efficiency.
What are the key elements of inventory planning?
An inventory plan is essential for any business that needs to keep track of its stock. It involves forecasting demand and deciding how much, when and how often to order materials and products. This helps companies meet customer demands while keeping costs low. The key elements of inventory planning include:
- Demand forecasting
- Budgeting
- Trend analysis
- Inventory control
1. Demand forecasting
Predict your customers’ demand for a product or service based on past sales data and market trends. Relying on previous experiences is always a good way to predict the future behavior of your buyers. Also, try putting yourself in your client’s shoes — what would you want and expect when purchasing this item?
Another aspect to look into is seasonality — weather, holidays, and significant events often impact customer behavior, so being prepared for that gives you a significant advantage before the competition.
2. Budgeting
Budgeting helps ensure the company has enough funds to keep operating. Whether it’s to purchase necessary supplies, pay the salary of warehouse workers, or upgrade tools, being in control of the financial aspect of your business helps every other part of it function smoothly.
Having a live overview of your current inventory levels will help you save on costs as you’ll know the exact quantities you have in stock and won’t have to make more “just in case.” The same applies to supplies — if you plan accordingly, you can optimize your resources to reduce waste and use all your raw materials to the maximum benefit.
3. Trend analysis
Take a look at past sales data to identify patterns in consumer behavior. This can help you make future decisions about which products should be stocked and when they should be ordered. It is similar to predicting demand but focuses more on the analytical aspect of it, deep-diving into past trends and how they have affected sales and inventory.
Common data points to track include:
- Customer demand
- Seasonal fluctuations
- Supply chain disruptions
- Economic factors
- Effects of prices on customer behavior
4. Inventory control
Controlling inventory levels, so there is neither too much nor too little on hand at any given time means keeping costs at a minimum while still being prepared for a sudden spike in demand. Real-time inventory count and automatic stock balance changes give you the security you need to always be in the know while not having to tumble around the warehouse, clipboard in hand, pointing at each individual shelf.
How do you develop an inventory plan?
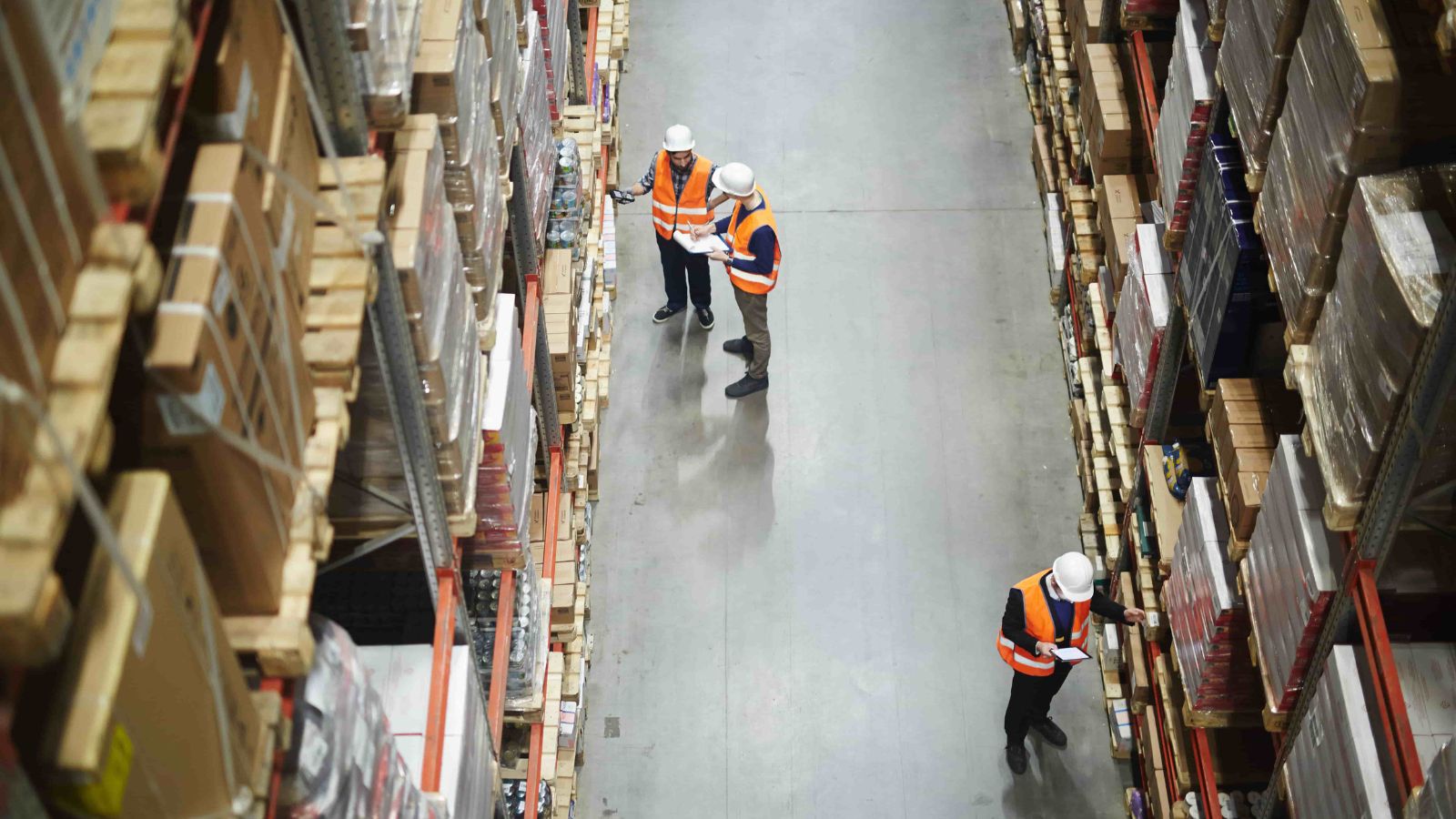
Planning inventory management requires a comprehensive understanding of the present and future needs of your business. Once these elements are determined, it is possible to develop a complete inventory plan that can be used to track progress toward reaching goals.
Analysis of demand
Determine your buyers’ expectations and purchasing trends to meet their expectations and keep up with demand. By analyzing previous purchasing behavior, you can determine trends within a month as well as a year.
The beginning of a month can be a busier time when people get their salaries and are more eager to make purchases. Respectively, the end of the month may be slower and lower in demand as people make more practical decisions on where to spend their money.
In a year, you may notice trends around holidays, especially those that have gifting associated with them. Valentine’s Day, Christmas, and even Black Friday — depending on your products, these may be the busiest times of the year for you.
Reviewing stock levels
Keep up with your inventory count to avoid unexpected stock-out or even negative stock. Unexpectedly low supply levels can cause manufacturing delays, meaning that everything else starts slowing down too. This will ultimately lead to extended delivery times for customers.
Track the shelf life of a product or ingredient for as long it is in your possession. This can provide an idea of how long you will need to order supplies and products ahead of time. Also, it might help you develop a better inventory management system and figure out how to store your stock more efficiently.
Creating and maintaining supplier relationships
Having reliable partners can take a huge weight off your shoulders and give you peace of mind and time to spend on more important things. When putting together an inventory plan, also consider your cooperations and partnerships.
Regular conversations about trends, demand, and business strategies will help create a better understanding between you and your suppliers. Set clear expectations for delivery times and quantity of goods, so both sides know what is expected from them.
Monitor potential issues such as pricing changes and quality discrepancies at an early stage to prevent delays or disputes down the line. Also, establish backup arrangements with other suppliers to keep stock levels consistent despite unexpected issues. Create emergency plans on both sides so that you and your suppliers can feel safe in this partnership.
At the end of the day, it’s all about communication, and as long as both sides are open to each other and follow the inventory plan, you will benefit equally from it.
Production costs
Creating and following a clear budget that each team sticks to will help you optimize costs and avoid unexpected expenses. Outline your whole production process and try to find areas that you could optimize and streamline to cut down on expenses.
One way to reduce costs is to build a stock reserve during the off-season when supplier prices are also lower. This strategy will only work if you work with non-perishable materials that won’t spoil by the time you need them.
Invest in quality control. In the long run, it will be more beneficial than having to restock at the expense of unsuitable or defective supplies. As a rule, cheaper things prove to be more expensive in the end. You may have a large stock, but if only a part of it is usable, then it’s actually useless.
Available resources
A big part of creating an inventory plan is your input and analyzing your past stock management. There are, however, several different resources available that you could highly benefit from, such as:
- Forecasting software: There are various programs out there that can help you make predictions about customer demand, allowing you to plan your purchases more efficiently.
- Inventory tracking systems: Automated inventory tracking systems can help you keep tabs on current stock levels, enabling you to make decisions about purchases quickly and accurately.
- Supplier networks: Having access to a network of reliable partners is essential for maintaining steady supply chains and getting the best deals on materials.
- Consultants: Working with professional consultants can help you identify opportunities to improve your inventory management processes and reduce costs. Don’t waste time inventing the bicycle when there are people who have already done it and who now share their experiences.
Monitor inventory systems
Ensure your stock management methods are up-to-date and can keep up with changes in demand or supply conditions.
By establishing metrics and benchmarks, you can measure the performance of your inventory systems and identify areas for improvement. Regular audits ensure your systems are running smoothly and can help identify any potential issues in advance.
Make the most of the systems and software you use. Automations are your friend. They can save you time that can be used more practically in other areas and processes.
What are the different inventory planning methods?
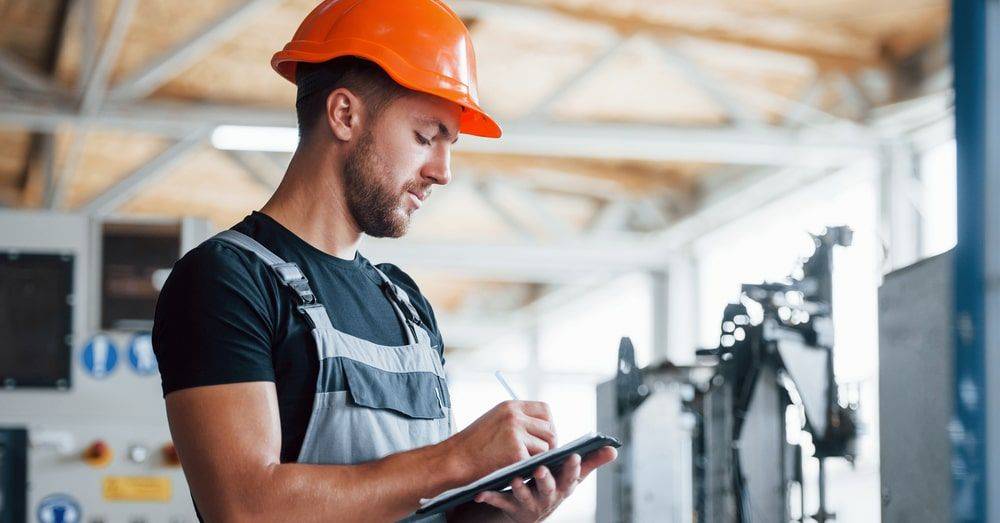
You can choose from various methods of inventory planning depending on your specific business needs.
- Economic order quantity (EOQ)
- Reorder point (ROP)
- Safety stock
- Just-in-time (JIT)
1. Economic order quantity
The Economic Order Quantity method seeks to minimize inventory costs by determining the optimal order quantity. By following a mathematical formula, businesses can calculate the optimal count of products to keep in stock while keeping costs at a minimum and still having enough to meet the changing demand.
Q = √[2(DK/H)]
where:
Q=EOQ units
D=Demand in units (typically on an annual basis)
K=Order cost (per purchase order)
H=Holding costs (per unit, per year)
2. Safety stock
The safety stock method protects the business against unexpected changes in demand or supply conditions. As the name states, it’s a safe way to avoid running out of products.
There is, of course, the element of cost when having supplies and items in stock without guaranteeing they will be purchased on time. It may be an inconvenient inventory handling method with perishable products like food and drinks. Still, if you always want to have available stock, it’s the most reliable one. Until everything spoils or ends up as dead stock lying on the shelf for the rest of eternity.
3. Reorder point
The reorder point method establishes minimum and maximum levels of inventory that create notifications for when your supply count is low. With reorder points, you can avoid stock-out or running out of materials for manufacturing. Once you’ve reached the minimum count of allowed stock, you’ll be reminded to order new supplies. ROPs help streamline production, ensure good partner relationships, and create a better customer experience.
ROP = demand during lead time + safety stock
4. Just-in-time
Just-in-time is a method of inventory management to reduce waste and lower costs. In this system, businesses receive supplies as needed instead of stocking up and storing items for later use. This ensures that the company only holds onto what it needs to meet expected customer demand, making it easier to manage inventory levels more efficiently.
JIT inventory also helps reduce excessive labor costs, as there is no need for active stocktaking or storage administration. The downside of a JIT inventory method is the risk of relying too heavily on partners. If the supplies don’t arrive on time, your order fulfillment cycle time suffers. Since you are responsible for customer satisfaction, any delay in delivery time reflects poorly on your business.
How to use Katana for inventory planning?
Katana is a cloud-based inventory planning software that helps you make forecasts based on accurate sales data. It has all you need to forecast demand and plan accordingly.
Barcode systems
Katana allows you to implement barcodes into your inventory system. Whether you want to generate new codes or import your own ones, barcodes will speed up how you handle inventory while providing a real-time overview of your stock.
With the scan of a barcode, you can accept or ship out deliveries, perform inventory controls, and track products from the same batch.
A barcode system helps you:
- Perform inventory checks faster
- Decrease margin for errors
- Track your products from materials to finished goods
- Collect data on purchasing habits
Barcodes also give your team more flexibility, as shop-level workers can use their smart devices for scanning. This means even faster processing of codes and inventory.
Batch tracking
Tracking batches is essential in process manufacturing businesses, where the final product is often made in batches and then divided into smaller packages. Whether you’re active in the food and drink, or cosmetics industry — batch tracking allows you to follow the life of an entire batch even after it has been separated and shipped out to different locations.
While batch tracking may sound like an attachment issue at first, it is highly beneficial in case you receive a complaint from a customer and need to issue a recall.
Batch tracking in emergencies
Imagine getting an angry e-mail from a concerned citizen who purchased a bottle of your craft beer and found a hair in it. A one-time thing or a possible contaminated batch? Following the trail to retailers, you find more complaints about hairy beers. That’s when you issue a recall, and all the beer from that batch is taken off the shelves and returned to you.
Reorder points
We already touched on the subject of reorder points and how it’s a good inventory planning method. That’s why it’s also one of the features that Katana offers on its platform.
Reorder points can be set and edited on the Stock screen in the Reorder point column.
Multilocation stock tracking
Inventory tracking is beneficial, but it’s even better when you have access to all your warehouses. Knowing that you have 20 pairs of socks available in your main warehouse is nice and all, but if you don’t know where the other 300 pairs are, it doesn’t really help you that much.
Katana gives you multilocation access to all your locations, giving you a complete overview of your total inventory count. With the click of a button, you can move products from one warehouse to another and ship out deliveries from any suitable location.
This proves especially useful with lean inventory management when production is done in multiple factories, and you’ll need to track the lifespan of a product across different locations.
Shop Floor App
Katana’s Shop Floor App makes it easy to assign tasks and assignments to shop-level employees who can access and update them in a flexible and mobile way. Available on a smart device, the Shop Floor App can change manufacturing statuses and thereby update Katana’s inventory levels.
To give your workers access to the app, you will need to create operator accounts for them. To do that, open the Team page in your Katana space and set up as many operators as you need. Once you’ve created the accounts, you can assign them tasks on the Make screen. Completing a task will automatically change the status or inventory count on the Stock screen, depending on the completed assignment.
Become an inventory planning master
Katana offers you various features and solutions to make your stock management as smooth as butter.
Table of contents
Inventory management guide
More on inventory planning
Get visibility over your sales and stock
Wave goodbye to uncertainty by using Katana Cloud Inventory for total inventory control
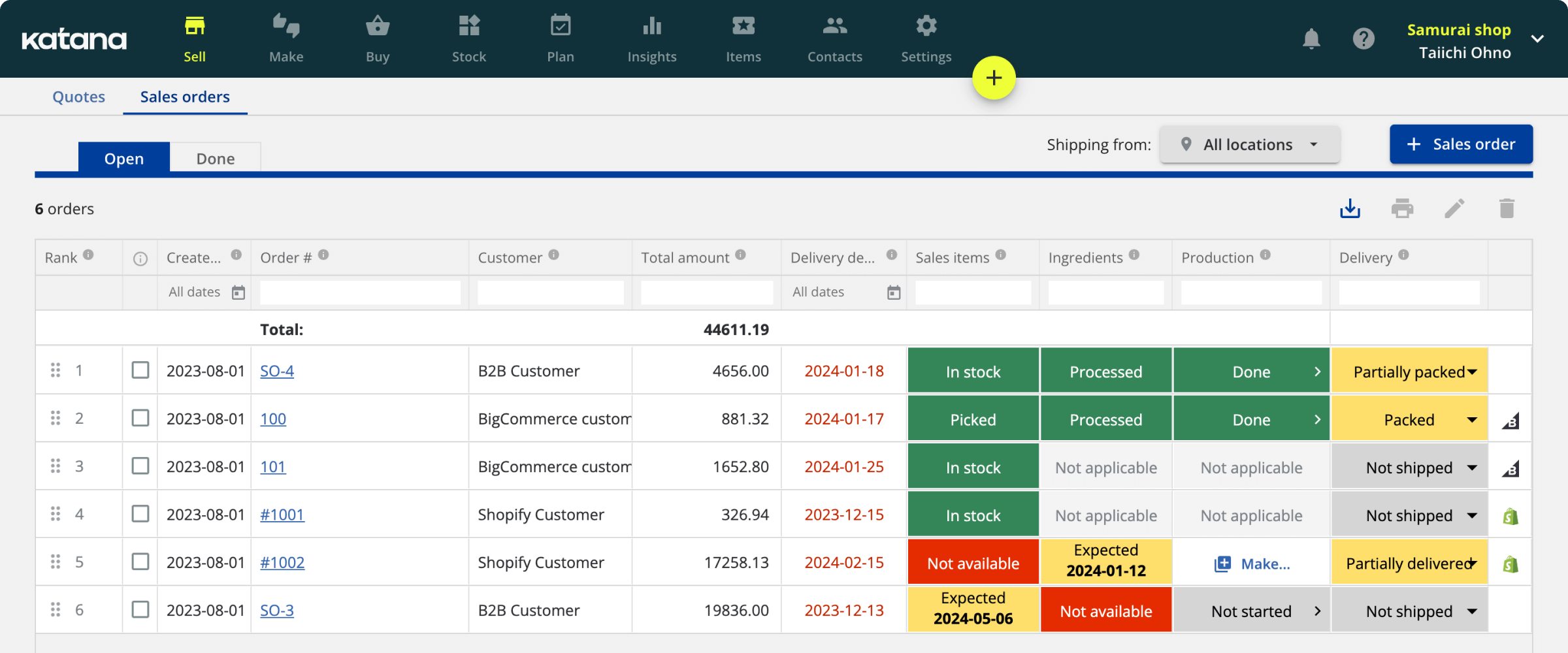