From chaos to order: A guide to warehouse order picking

Ioana Neamt
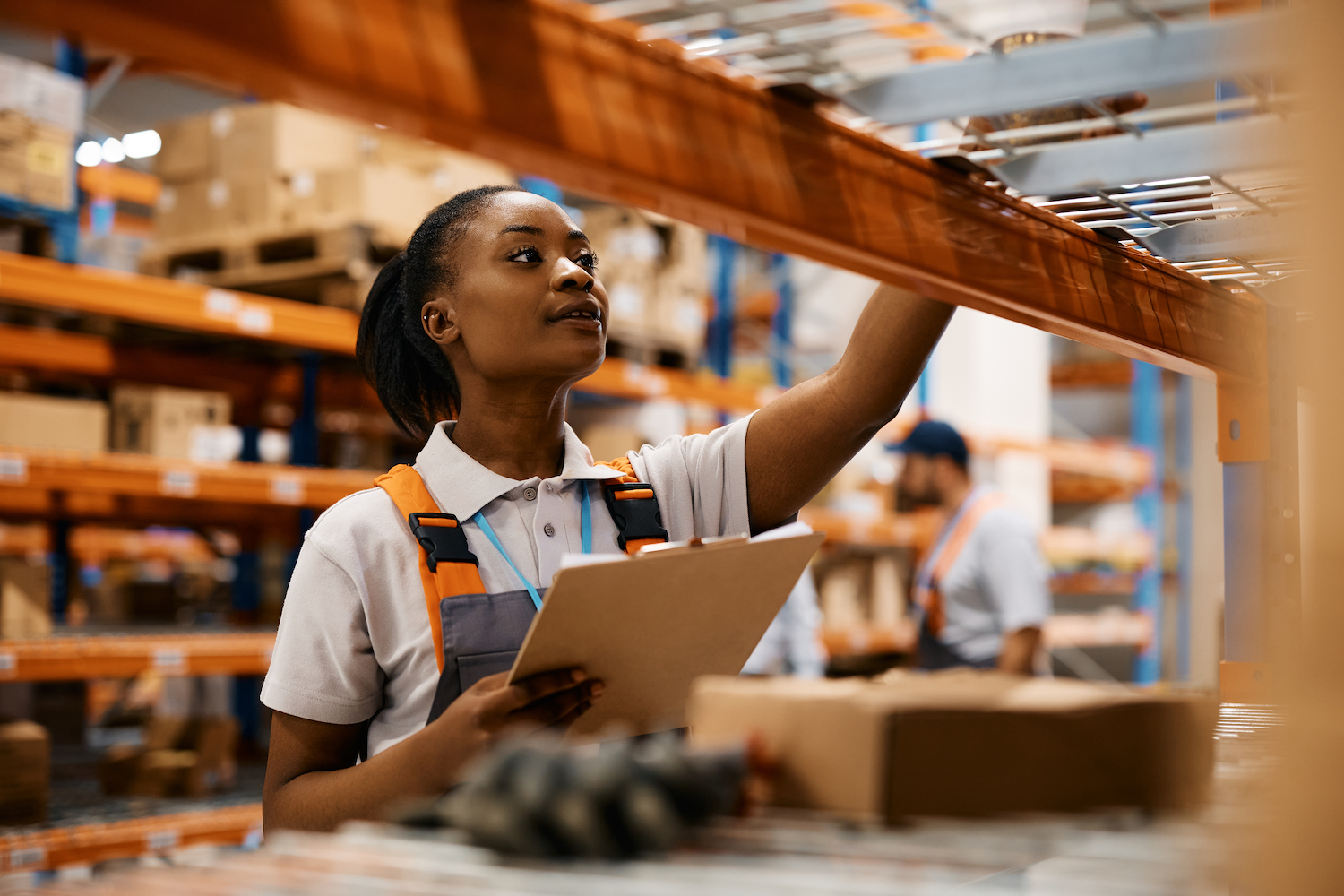
If you thought warehouse order picking is just a mundane and unexciting process, think again. It’s actually an art form! It’s where precision meets thrill and where every aisle holds a potential adventure. You could say that it’s almost a carefully choreographed dance, as teams strategically navigate the aisles, picking and packing with the precision and care of a well-experienced choreographer.
In this tech-driven era, order picking is about mastering the art of efficiency, turning the mundane aspect of order fulfillment into a streamlined and nuanced process. So, let’s learn more about it and find the best picking strategy for your business.
What is order picking in a warehouse?
Order picking is the process of picking the right products from a warehouse to fulfill an order. It’s a crucial step in the order fulfillment process within a warehouse or distribution center.
For business owners, mastering warehouse order picking is essential. It means efficiently and accurately assembling customer orders to meet expectations and maintain a positive reputation. The ultimate goal? To fulfill customer orders while providing them with a seamless experience and keeping them happy and loyal.
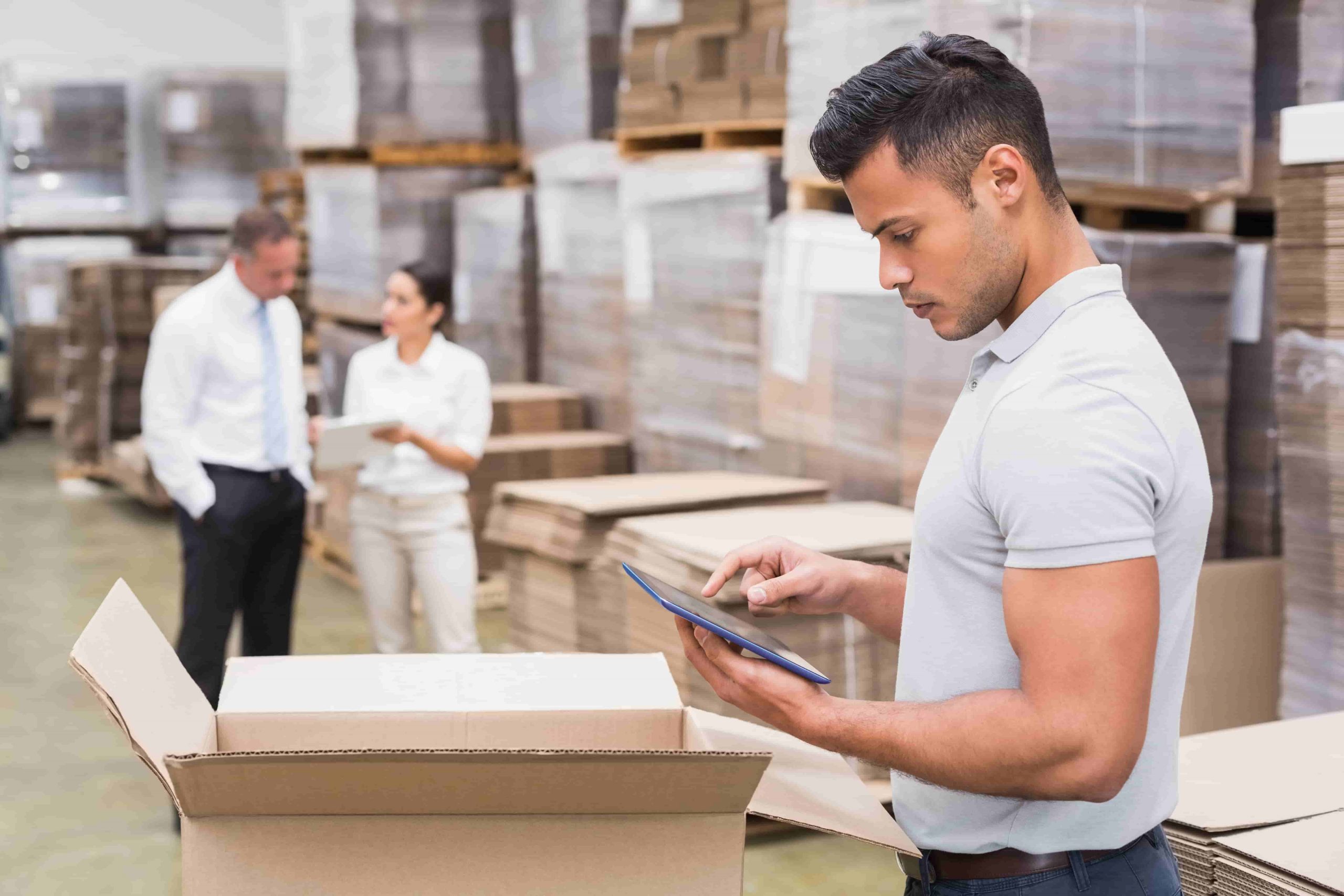
Why is a warehouse order-picking system important?
A warehouse order-picking system is essential for improving things like efficiency, accuracy, and customer satisfaction. But don’t take our word for it, let’s go through some of the reasons why this system is not just a cog in the machine but an actual crucial part of business operations.
Helps reduce costs
An optimized order-picking system helps your business save money by reducing labor hours, minimizing operational errors, and overall improving inventory management. It serves as a linchpin for cost reduction and the result is simply a leaner, more agile operation that adapts and minimizes unnecessary expenses.
Leads to higher customer satisfaction
Using a picking system is like offering customers a first-class flight experience. Think of it as the diligent and always available flight crew making sure they’re having a smooth journey. With meticulous planning, the system acts as the navigational compass by guiding each delivery through the skies of the supply chain. It also minimizes turbulence and ensures each package arrives at its destination with the precision of a scheduled flight. What more could you want?
Better optimizes staff’s jobs
Your staff should be able to efficiently manage their time and a picking system is the perfect tool to help achieve that. It can strategically organize and assign tasks based on their skills and availability, which leads to enhanced coordination and, overall, a well-functioning team.
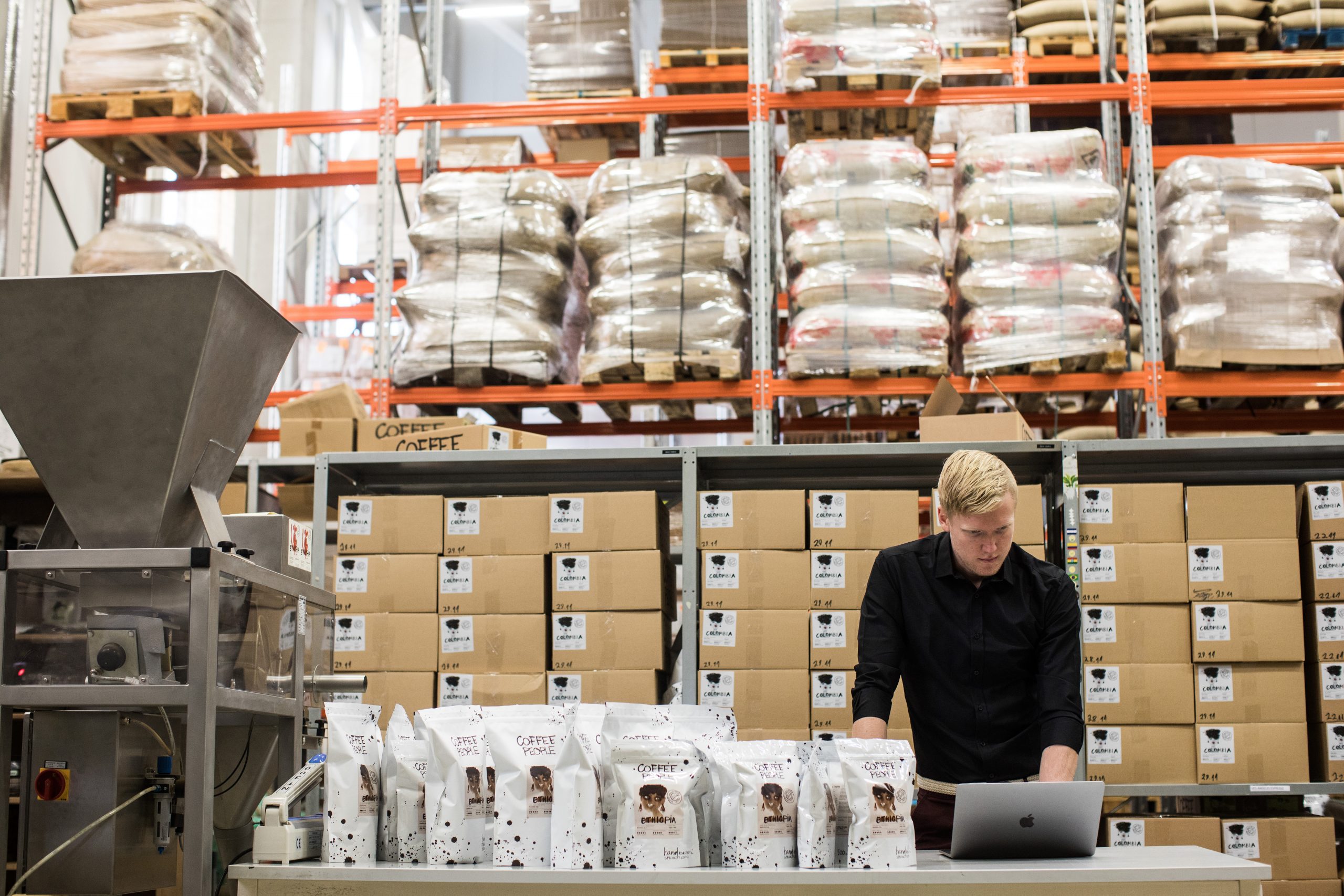
Top strategies for effective warehouse order picking
There are several strategies that can lead to effective warehouse order picking, and if you want to make the best of them, you can consider using each individually or a combination of two. Here are the most popular warehouse order picking methods for improving efficiency.
- Zone order picking — Dividing the warehouse into zones and assigning specific staff or teams to each zone helps streamline the picking process. With this approach, each team is responsible for picking items in their designated area, reducing congestion and improving efficiency.
- Discrete order picking — This particular strategy fits almost any business. A picker focuses on one product at a time until the entire customer order is a perfectly curated package of goodies. Now, the cool part is that this strategy creates a straightforward and easily manageable system. It’s a bit like having a clear view of the puzzle pieces and fitting them into place with precision.
- Batch order picking — Grouping multiple orders together for simultaneous picking can reduce travel time and increase efficiency at the same time. This strategy is particularly effective when orders share common items. For example, if multiple orders include the same popular product or frequently requested items, the picker can gather all these items at once rather than making separate trips for each.
- Wave order picking — Similar to batch picking, wave picking involves picking multiple orders in a predefined sequence or wave. This strategy optimizes the route for pickers by minimizing unnecessary movement and increasing overall speed.
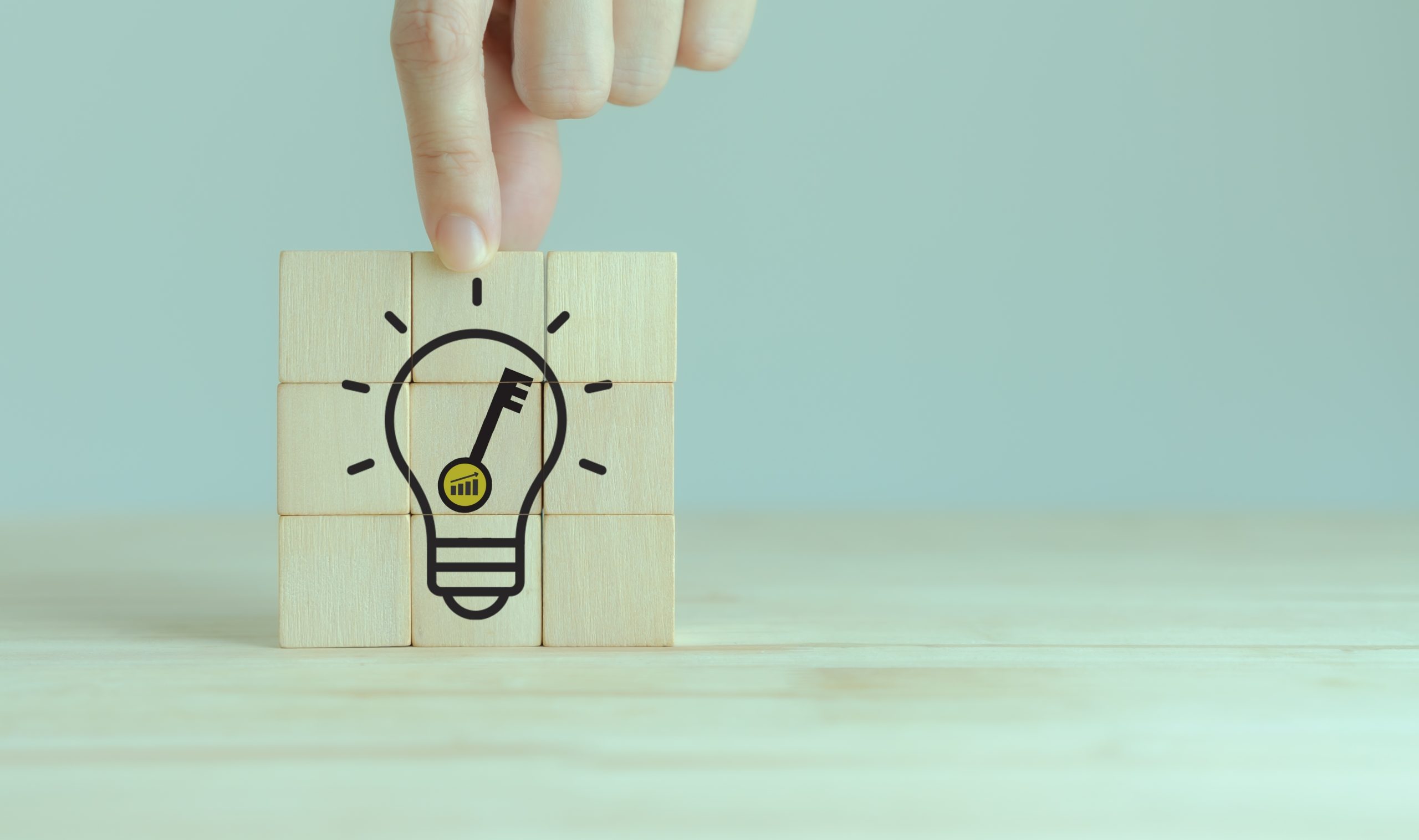
Best practices to enhance warehouse picking efficiency
Efficient warehouse picking is key to successful order fulfillment, and implementing best practices can significantly boost operational performance. Take a look at the best practices for enhancing your business’ warehouse picking efficiency.
Keep a steady supply in stock
Your inventory is almost like the lifeblood of your operation. You have to regularly tune into demand patterns, replenish your stock strategically, and let the rhythm of just-in-time inventory management be what keeps your warehouse dance floor bustling.
Use automation and warehouse management tools
Say hello to the future! Inventory automation and warehouse order-picking management tools can turn your warehouse into a world of unparalleled efficiency. Think robots, conveyor belts, and cutting-edge software working in unison to reduce manual load and streamline the entire process.
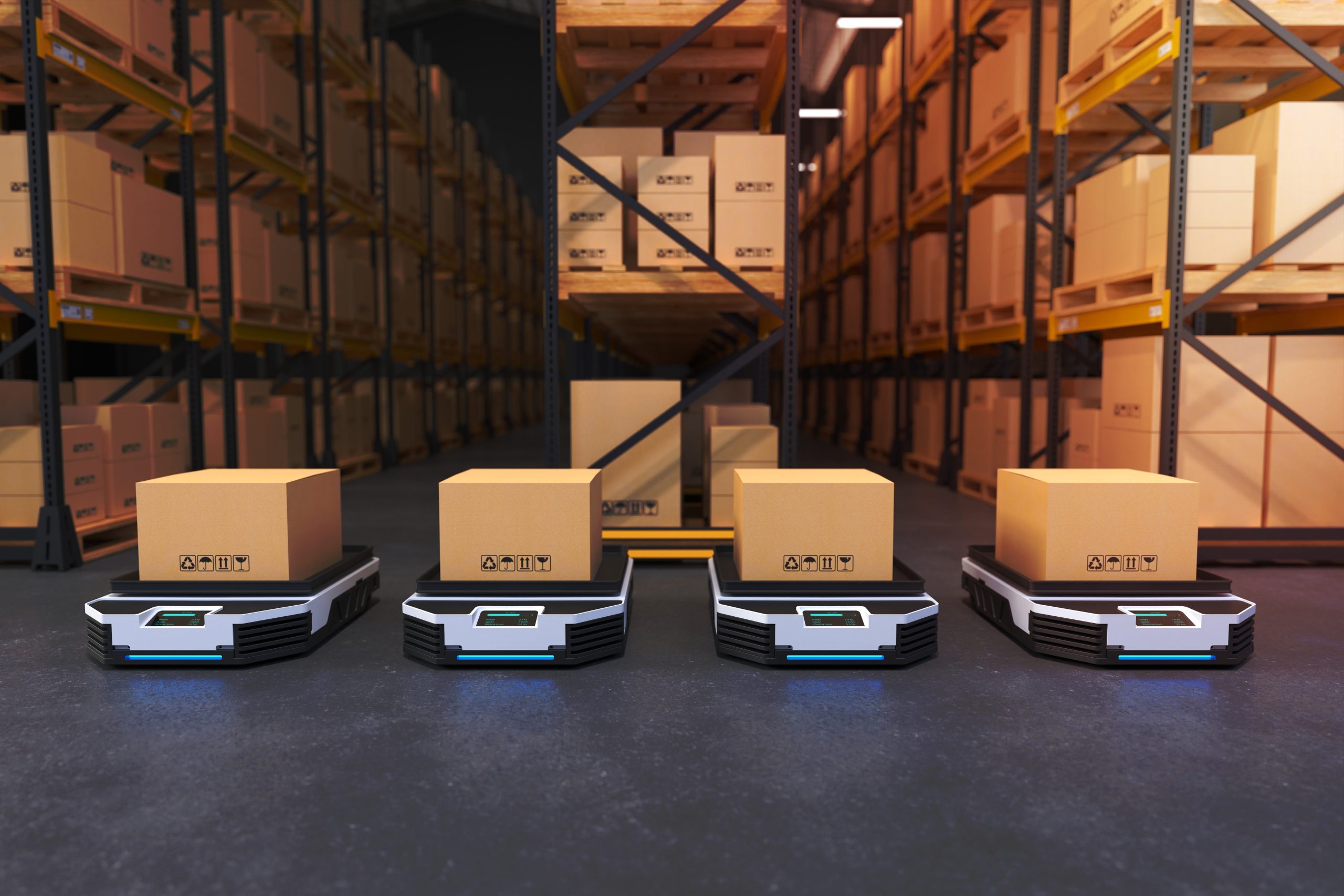
Choose the right equipment
On top of your regular heavy-duty equipment (forklifts, pallet jacks), it might be a good idea to also add collaborative mobile robots that can work alongside your staff and help guide them through tasks. Find also some voice-picking equipment like headsets and hands-free systems that can give your pickers instructions in real time. To avoid things like over- or under-packaging, make sure you use smart scales which will help predict changes in shipping costs.
Optimize the warehouse layout
Your warehouse layout is what sets the tone of efficiency. You have to regularly fine-tune it and adjust it based on the patterns of demand. A strategic layout can turn any warehouse into an efficient space. And practice makes perfect so try several layouts out before deciding on one. Just to see what works best.
Make workplace safety a priority
Provide training, create well-lit and marked pathways, and ensure your warehouse runs smoothly and without any mishaps. Regular safety audits are essential for identifying and addressing potential risks. Keep in mind that workplace safety is not only a compliance measure but a crucial aspect of creating a secure and productive setting where your employees can do their jobs with confidence.
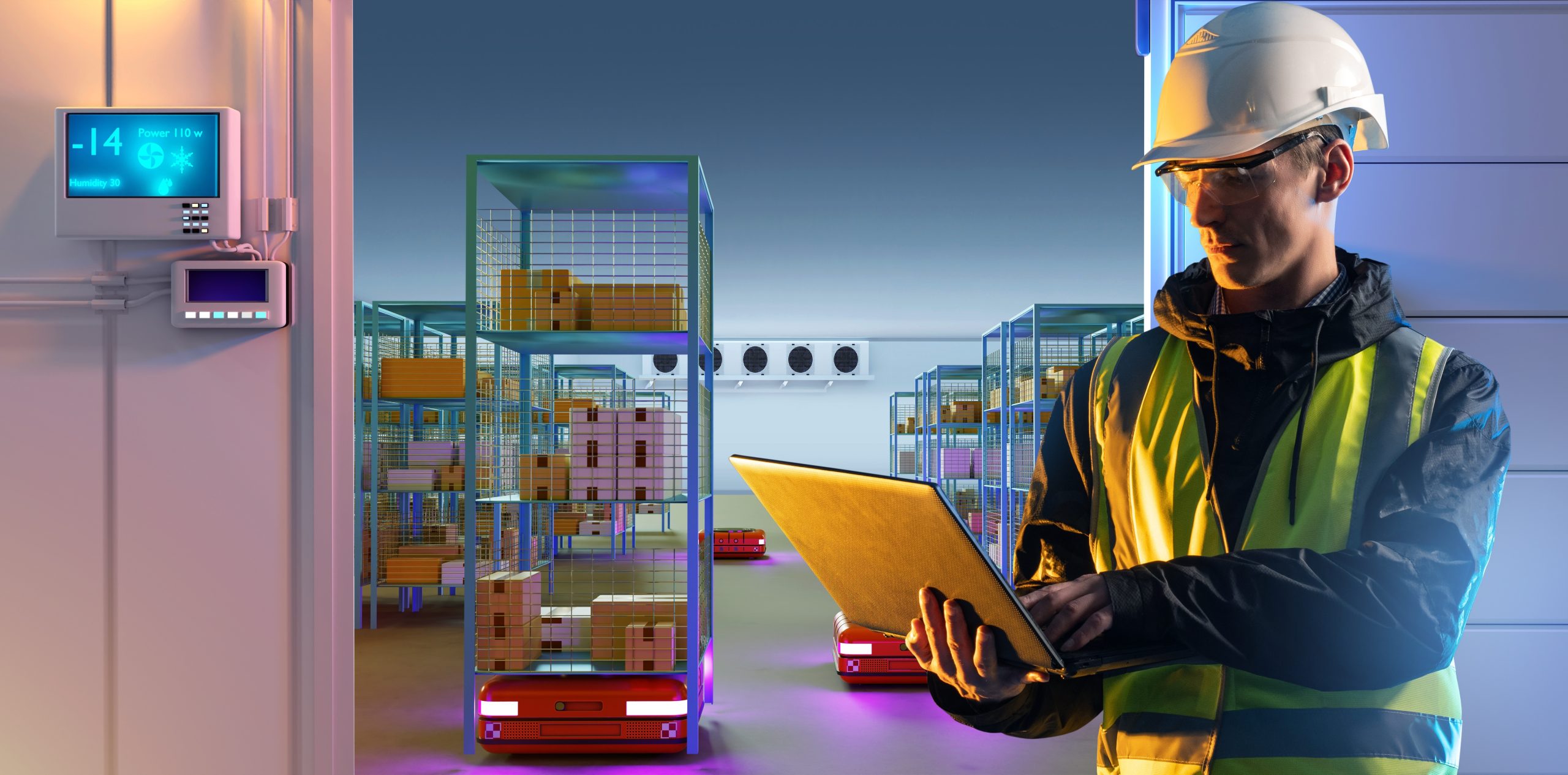
Common challenges with order picking
Of course, every business journey comes with its own set of challenges. Yet, fear not, as challenges are but mere stepping stones to fine-tune your business operations and emerge stronger than before. Understanding them will ensure a smoother and more efficient warehouse order-picking process. Here are some common challenges warehouses can encounter.
High volume orders: Navigating the rush
Dealing with a sudden influx of high-volume orders can be challenging. Pickers may face increased pressure to fulfill orders promptly, leading to potential bottlenecks and longer processing time. This requires strategic planning to make sure your resources are optimized during peak periods.
Slow-moving products: The tortoise in the race
Every warehouse has its tortoise products — the slow-moving items that seem to take a very leisurely pace in terms of demand. Implementing strategies like batch picking or revising your storage locations can help address this challenge.
Inaccurate inventory counts: The numbers game
Keeping accurate inventory counts is a perpetual challenge, often resembling a complex game of numbers. Discrepancies between physical stock and recorded inventory can lead to errors, delayed orders, and, ultimately, client dissatisfaction. To avoid this, try leveraging technology such as barcode scanning or RFID systems.
Seasonal demand: Riding the waves
Seasonal fluctuations in demand can create waves that warehouses have to ride strategically. Peaks in orders means you should find a flexible picking process that can adapt to varying workloads. Otherwise, it can result in overworked staff, storage challenges, and difficulties meeting customer expectations during peak periods.
Improve warehouse order picking efficiency with Katana
Need a strategic partner to help enhance your business’ order-picking prowess? Enter Katana. It’s a platform that helps manage inventory and order fulfillment by acting as a support system and helping businesses better optimize their order-picking processes. In a nutshell, it provides insights and tools to manage inventory in a more efficient way so that your business can deliver a positive customer experience and ensure operational efficiency.
Katana ensures accurate real-time stock updates, mitigating the challenge of inaccurate inventory counts. It can also help optimize workflows that allow businesses to implement batch picking and adapt to the unique demands of slow-moving products. With Katana, you can be sure that order-picking becomes a precision-driven task, ensuring efficiency, reducing errors, and contributing to an overall agile and streamlined warehouse ecosystem.
Interested in learning more? Reach out to our team to see Katana in action and decide whether it’s the right fit for you!

Ioana Neamt
Table of contents
Get inventory trends, news, and tips every month
Get visibility over your sales and stock
Wave goodbye to uncertainty by using Katana Cloud Inventory for total inventory control
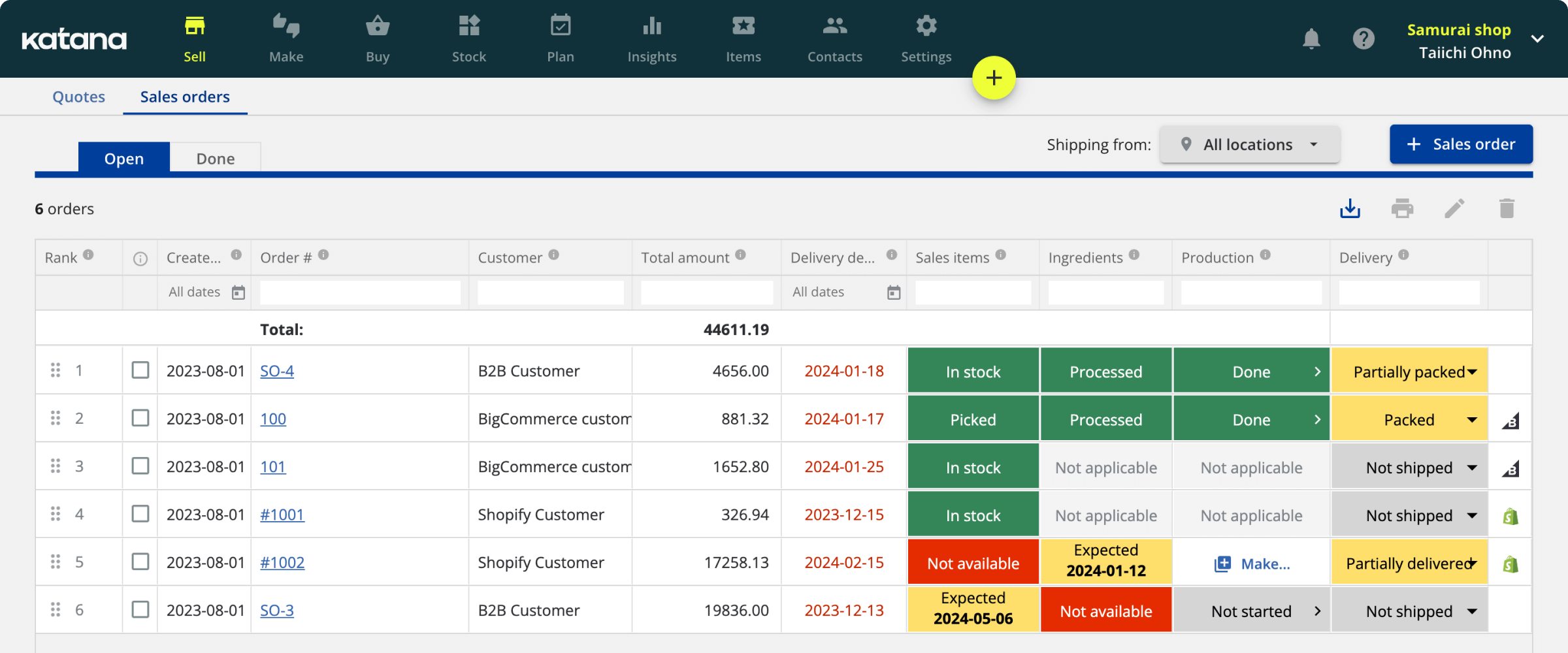