11 Warehouse mistakes and how to fix them
Discover 11 costly warehousing mistakes and how to prevent them. Learn about common inefficiencies and strategies for efficient warehouse management.
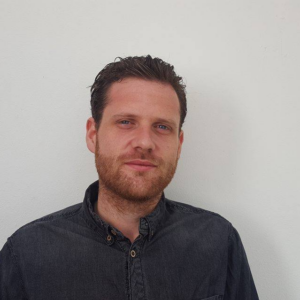
James Humphreys
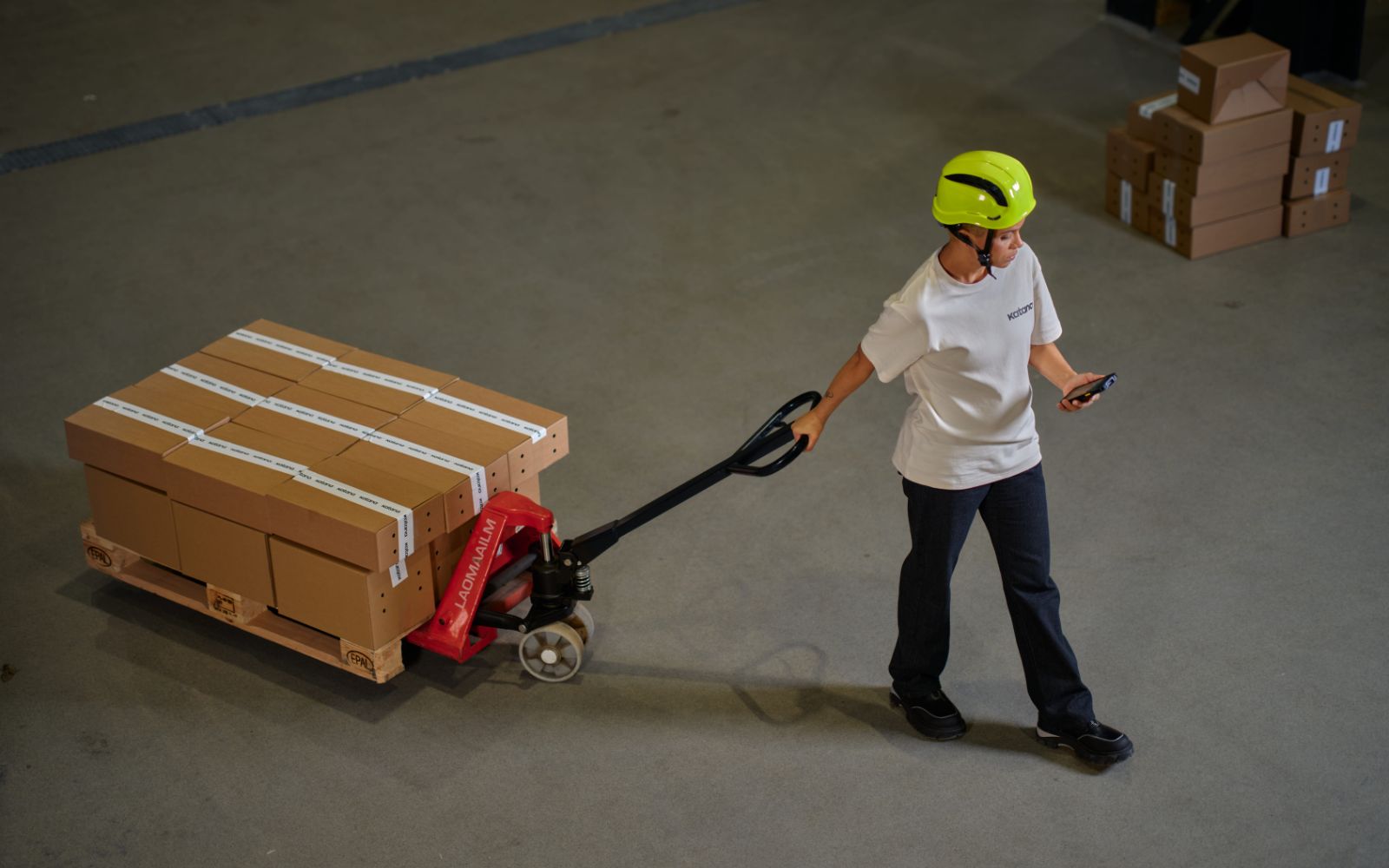
Regardless of whether you’re just getting started or your warehouse has been in operation for several years, it can be difficult to see where warehouse mistakes occur.
Just like driving a car — you learn how to drive and pass your exams, and once you’re on the highway, a bad habit becomes standard practice, and your car’s performance decreases. When this happens, it’s time for a refresher course. And that’s why we’ve put together this article on the 11 most common warehouse mistakes businesses make and how you can fix them.
1. Too much inventory
“It’s better to have it and not need it than to need it and not have it” certainly does not apply to keeping inventory.
Probably the most common warehouse mistake all businesses face is holding excess inventory in their storage. This is an easy mistake to make, especially for wholesalers, as their business model is all about buying one particular product in bulk for a discount. Before you know it, what seemed like a great way to save money is now driving up costs as you have items clogging up inventory space and running the risk of becoming obsolete.
Ultimately, it doesn’t take a lot for you to lose control over your inventory if you don’t have the space or staff to manage it — not only will it slow down your supply chain, but it will also create a hazardous environment for your workers.
Doing more with less
When it comes to inventory management, the name of the game is balance.
To avoid the warehouse mistake of overstocking, you’ll need to watch how your inventory levels and customer demand change over time. Sure, you could do it manually, but even that is prone to mistakes and increases labor costs. Your best bet if excess inventory is a problem for you is to adopt solutions that can automate inventory management and demand planning.
For example, Katana’s Planning and Forecasting add-on makes demand predictions by processing real-time sales data and analyzing historical trends — preventing inventory errors and enabling strategic growth planning.
According to Zak Genefaas¹, Sales and Operations Lead at Wabanaki Maple, “It would require a full-time person just doing documentation in Excel to match what is automatically taken care of in Katana.”
What is Katana?
Katana Cloud Inventory is a solution that facilitated a total customer revenue of $2 billion from sales in 2023. From large multi-million-dollar enterprises to small-scale entrepreneurs, Katana assists SMBs in effectively managing their sales and inventory. Katana boasts an average customer rating of 4.8 out of 5 — recognized by reputable review platforms such as G2, Capterra, and Software Advice as an industry-leading inventory management solution.
2. Too complacent
According to the US Bureau of Labor Statistics², there were nearly 3 million recorded cases of nonfatal injuries and illnesses in the private sector throughout 2022 — and an unfortunate 5,486 fatalities.
As you can see from the statistics, a common warehouse mistake is that businesses assume that because there hasn’t been an accident, they’re meeting health and safety requirements and drop their guard. However, during these times, warehouse managers must stay vigilant for health and safety violations or assess where risks are likely to come next. Otherwise, without due diligence toward health and safety, an accident is just a matter of time.
And the consequence of a worker becoming injured can lead to downtime, the worker suing, or your business getting into trouble with the Occupational Safety and Health Act (OSHA).
What is OSHA?
OSHA is a federal agency in the United States that falls under the Department of Labor. OSHA’s primary responsibility is to ensure safe and healthy working conditions for employees across various industries.
Keeping your workers safe
You’re going to have to ensure that your staff knows, understands and follows safety protocols to the T.
To avoid warehouse mistakes that cause injuries leading to increased costs and litigation, you and your managers need to perform regular risk assessments to perform preemptive and corrective measures. Then, once risks have been identified and protocols have been put in place, it’s time to get your staff on board. Including them in the following health and safety guidelines will mean giving them proper training and monitoring adherence to these rules.
Insider tip: One way to make sure employees follow the rules is to introduce an award system.
3. Inefficient picking path
Now we head into the first issue caused by warehouse setup mistakes — and considering picking and packing is a huge responsibility for warehouse workers, optimizing your picking path is important.
And even though this might seem obvious, many businesses fail to keep looking for the most optimal routes in their warehouse. Failing this task can increase labor costs and supply chain cycle times. Ultimately, your profitability all depends on how efficient your operations are.
Insider tip: Finding the optimal picking path will require continuous analysis. That’s why many businesses turn to real-time inventory management solutions to collect data to understand how to improve warehouse order picking.
Finding the quickest path
Warehouse setup mistakes cause inefficient picking paths and need to be reconfigured to fix.
To improve your picking routes, you should analyze your warehouse layout, considering where your shipping areas are and where you store your SKUs. Make sure your warehouse operators can complete picking runs close to your shipping location and that products regularly purchased together are stored close to each other. Adopting solutions where warehouse operators can quickly scan barcodes to update inventory movements and picking status will help greatly reduce the lead time of getting products to customers.
Katana Warehouse app
The Warehouse app in Katana is a mobile-friendly web-based application that warehouse teams can use to help fulfill sales orders.
4. A waste of space
More warehouse setup mistakes include not fully utilizing your space.
Many businesses have become comfortable and primarily have a static storage layout. This means that wherever products are stored, they’ll always be stored there. You would think that this would make things easier since it won’t take operators long to learn where everything is.
But, this oversight leads to underutilizing storage space, such as storing half-pallets in bays meant for full pallets.
Freeing up more space
Regularly review your warehouse layout and stock composition to optimize space.
Adjust the layout based on the product mix, ideally on an annual basis. Pay particular attention to racking to maximize space utilization for height, length, and width. Generate a report of processed cargo over the past year and categorize it by dimensions for better insight.
5. Poor planning
Warehouse mistakes don’t have to be complicated — they could be as simple as not planning operations and inventory management properly.
What worked yesterday might not work today. Covid-19 and many other external factors have highlighted how things change quickly, and businesses need to adapt new processes, procedures, and technology to thrive. Without planning your workflow based on current and future circumstances, you’re dooming your business to fail in the long run.
Insider tip: Download the free ebook on inventory management and learn all about proper inventory planning techniques here.
Planning the right way
The first step is planning for your plan — okay, that’s a bit tongue in cheek, what we mean is to schedule some time in your warehouse for evaluations.
You could set this time aside once or twice a year to analyze your warehouse processes. The intervals you choose are up to you, but the idea is to review the efficiency of your warehouse based on your inventory management KPIs and see if there’s room for improvement. If your business is performing these audits, but warehouse mistakes keep occurring, it might be time to consider hiring a consultant to help you create a new plan.
Using a perpetual solution for planning
Hiring a consultant may not be necessary if your data collection is inefficient. Katana Cloud Inventory collects and updates data in real time, so you can get an understanding of your business’s performance whenever you need it.
6. No spring cleaning
With a surge of orders, everyone is running every which way but loose to keep the lead time low, and maybe some steps to get things packed and shipped as soon as possible have been skipped.
Now you’re staring at a messy warehouse — which is fine if it’s all cleaned up at the first opportunity. For some businesses, the mess is a symptom of warehouse mistakes due to poor efficiency. Besides the potential to cause injury, mess obstructs routes and reduces the productivity of your workers.
Even worse, if it gets too bad, you’ll be forced to shut down operations to clean up — costing your business and damaging your reputation with your customers.
Getting everything spick and span
You will need to enforce a strict regime to correct this warehouse mistake.
First, you should start having your warehouse operators inspect unused materials and get into the habit of moving items to the trash bin if they have passed their usefulness. Another thing to consider is to schedule in a daily clean-up time. For example, at the end of every shift, your workers clean and prepare the warehouse for the next shift workers so they can get started with their tasks.
7. Not giving staff the opportunity to grow
2022 was known as the Great Resignation — as governments lifted Covid-19 restrictions, a record was broken, as over 50 million Americans³ quit their jobs to find something better.
If you’re not giving your employees incentives or opportunities to grow, then you run the risk of them leaving for a company that can. Even if it’s just regular training sessions on workplace safety, this will show them that you care for their well-being. If you’re a business already experiencing a high turnover rate, you don’t need to be told how much it costs to replace and train new joiners, so it might be time to try a different approach.
Nurturing your employees
First things first, establishing regular health and safety training for your staff will keep them safe and your operations moving.
But, talk with your staff about their ambitions. Most people want career growth, to develop new skills, and refine their existing abilities. Have a discussion with your people to understand if there’s something that you can facilitate to help them strengthen these areas.
You might think you can’t spare the time or budget for these endeavors, but not investing in your staff will cost you much more once you start losing your best workers.
8. You can’t tell your bolt from your nut
Warehouse mistakes are tenfold because of this one bad practice — inaccurate inventory tracking.
And it turns out that this issue is self-inflicted in some cases, as 43% of small businesses don’t have inventory tracking in place⁴, and 24% that do track inventory use tools like QuickBooks Online — accounting software that does have basic inventory tracking but lacks features necessary for warehouse workers. Without proper inventory tracking in place, items and orders are destined to become as lost as the Ark of the Covenant in Hanger 51 from Indiana Jones.
Insider tip: In the beginning, starting with a tool like QuickBooks Online is normal since it gives you a solid accounting solution and other benefits. But, as you grow, the other benefits struggle to keep up. At that point, it’s time to upgrade your QBO with an inventory management integration like Katana Cloud Inventory.
Demystifying your item’s movements
Many claim perpetual inventory to be the way forward in this area, and a warehouse management system (WMS) will give you exactly that by integrating inventory management and tracking, order fulfillment, shipping, receiving, and more, all centralized in one place.
Katana’s Warehouse app is designed to facilitate warehouse operations and streamline the fulfillment of sales orders, giving you:
- Sales order fulfillment — The app helps plan and execute sales orders by enabling warehouse teams to pick and pack items efficiently
- Live production status updates — It provides real-time updates on production status directly from the shop floor to Katana’s main platform, ensuring that all stakeholders are informed promptly
- Paperless operation — Eliminates the need to print sales order packing lists, contributing to a more environmentally friendly and efficient workflow
You can read more about the Katana Warehouse app add-on here.
9. Papers, Please
It’s not just the risk of paper cuts you’re increasing, but having your operations reliant on paper documents means you’re playing with fire — and paper is highly flammable.
Hyperbole aside, many small businesses often make the mistake of not using technology and sticking to good old-fashioned paper-based methods to manage their warehouse. Even though you might believe that keeping things simple is best for your logistics or warehousing, using paper can slow down your processes and lead to delays due to lost or misplaced documents. Getting rid of your paper-based processes will save you money on supplies and also benefit the environment.
Saving the trees
Going paperless could be adopting software into your business or simply finding another system to replace paper, like whiteboards or spreadsheets.
Transitioning to paperless operations in a warehouse starts by evaluating current paper usage and identifying areas where paper can be reduced or eliminated. Replace all paper-based forms, reports, and manuals with digital documents and utilize cloud-based storage solutions for easy access and sharing. Just make sure to train employees to help them adapt to the new digital processes and continuously monitor and optimize to improve efficiency and sustainability over time.
10. Focusing on the wrong metrics
Another common warehouse mistake is not understanding what KPIs you should be tracking within your business.
Focusing on the wrong ones in your warehouse can lead to inaccurate evaluations, misguided decisions, wasted resources, lack of improvement, and loss of competitive advantage. It’s crucial to align KPIs with strategic goals to ensure meaningful insights and effective decision-making. If you don’t address this issue, you’re likely to drive your business into the rocks, as the data you’re collecting is not helping you properly navigate challenges in your warehouse.
Using the right KPIs
There are many inventory management KPIs out there that you can use within your warehouse.
However, collecting the data, that’s the big challenge in overcoming these warehouse mistakes. Using a platform that can give you real-time business analytics will help you get the information you need to understand how your business is performing. For example, Katana has the Sales Insights and Purchasing Insights dashboards to help you track orders, costs, and inventory status and understand what’s underperforming in your operations with historical data.
11. Technophobia
Inventory management tools are getting better day after day, and with AI being the latest craze every business is jumping on, holding off on adopting some form of automation in your operations is actually detrimental to your ability to keep up with competitors.
Not adopting technology and neglecting data collection and analysis leads to inefficiencies. Without tracking business trends or responding to market changes promptly, your business will struggle to stay agile and meet evolving customer needs. On the other side of the coin, it’s important to avoid investing heavily in the latest technology without considering its suitability for your warehouse operations.
Getting started with the right software
Katana Cloud Inventory Software is a comprehensive solution designed to optimize inventory levels, manage sales channels in real time, and seamlessly integrate with your favorite ecommerce, accounting, reporting, and CRM tools.
Begin simplifying your warehouse inventory management now using Katana. Monitor and control your entire setup seamlessly from one platform. Gain real-time insights into stock levels and inventory requirements.
Contact us for a demo and experience Katana firsthand to see how it can help you fix your warehouse mistakes.
Sources used in this article
¹ How Wabanaki Maple solves sticky problems — a tech stack that increases sales without hiring, Katana (2023)
² Injuries, Illnesses, and Fatalities, US Bureau of Labor Statistics (2023)
³ The Great Resignation Is Over: Quits Return to Pre-Covid Level, Statista (2024)
⁴ 18 STUNNING SUPPLY CHAIN STATISTICS [2023]: FACTS, FIGURES, AND TRENDS, Zippia (2022)
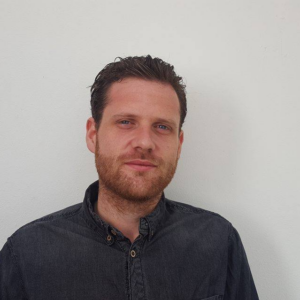
James Humphreys
Table of contents
Get inventory trends, news, and tips every month
Get visibility over your sales and stock
Wave goodbye to uncertainty by using Katana Cloud Inventory for total inventory control
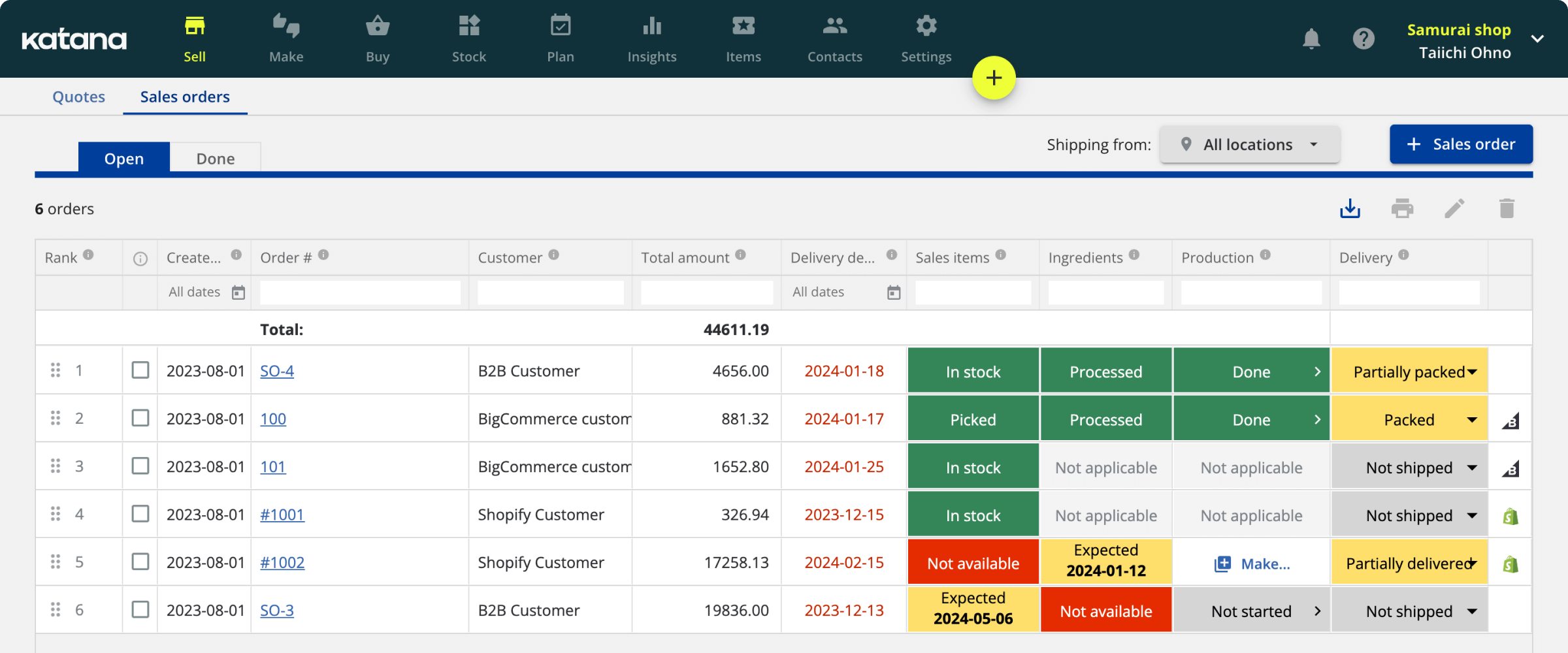