Warehouse layout: The crossroads between design and efficiency

Ioana Neamt
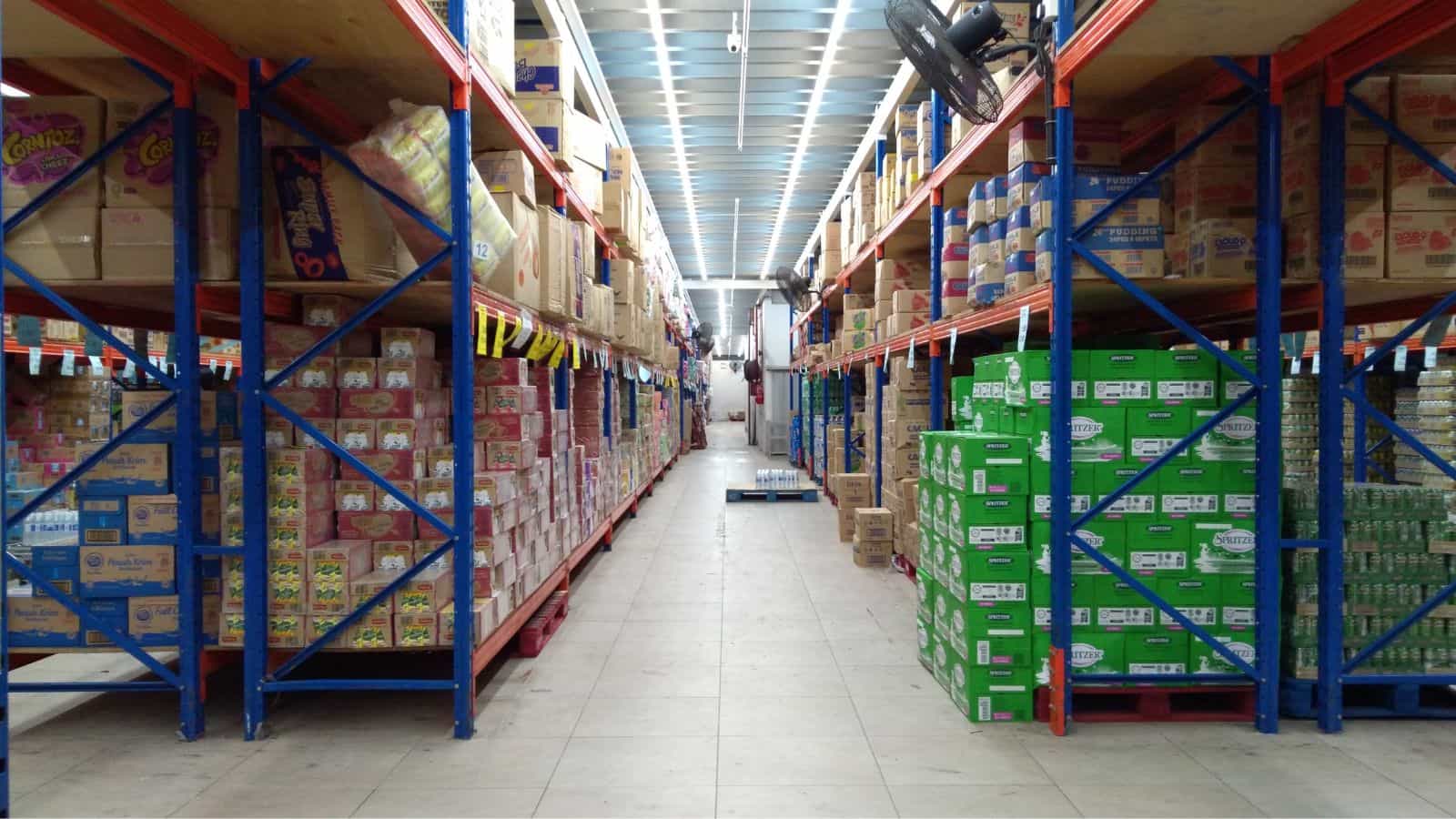
Business is all about being at the right place at the right time — as long as that right place is optimized to the max. Which is where warehouse layout design comes in.
Planning a warehouse layout is much like designing the blueprint for a huge library with intertwining similar rows. Just as a library’s layout determines the ease of access to books, a strategically planned warehouse layout is essential for a business to store, organize, and manage various items and raw materials.
The most optimal warehouse layout focuses on maximizing space and productivity, as well as ensuring safety. However, the best warehouse layout designs are always tailored to the specific needs of the business. And, at the end of the day, the key to unlocking the potential of a business may lie in something as simple as how its warehouse space is utilized.
What is warehouse layout design?
An efficient warehouse layout demands meticulous planning and a structured approach. To make the most out of our library metaphor, a well-thought warehouse layout ultimately contributes to the success of the business — just as a well-organized library makes it easy to find books and enhances the reading experience.
Effective warehouse operations begin with the optimal use of space. Being heavily reliant on its floor plan, a carefully crafted warehouse layout should ensure seamless movement of goods and materials. Devising an effective warehouse layout takes into account business needs, as well as an intuitive flow of both goods and people working on location. The process includes creating schematics, optimizing space, implementing workflow strategies, and even conducting traffic flow tests.
Essentially, businesses should consider the following factors when looking to streamline warehouse operations:
- Space utilization
- Storage options
- Productivity equipment
- Aisle layouts
- Production area workflows
Just as a library’s layout reflects its collection and reader needs, a good warehouse layout should align with your business’ inventory management systems to ensure efficient inventory control.
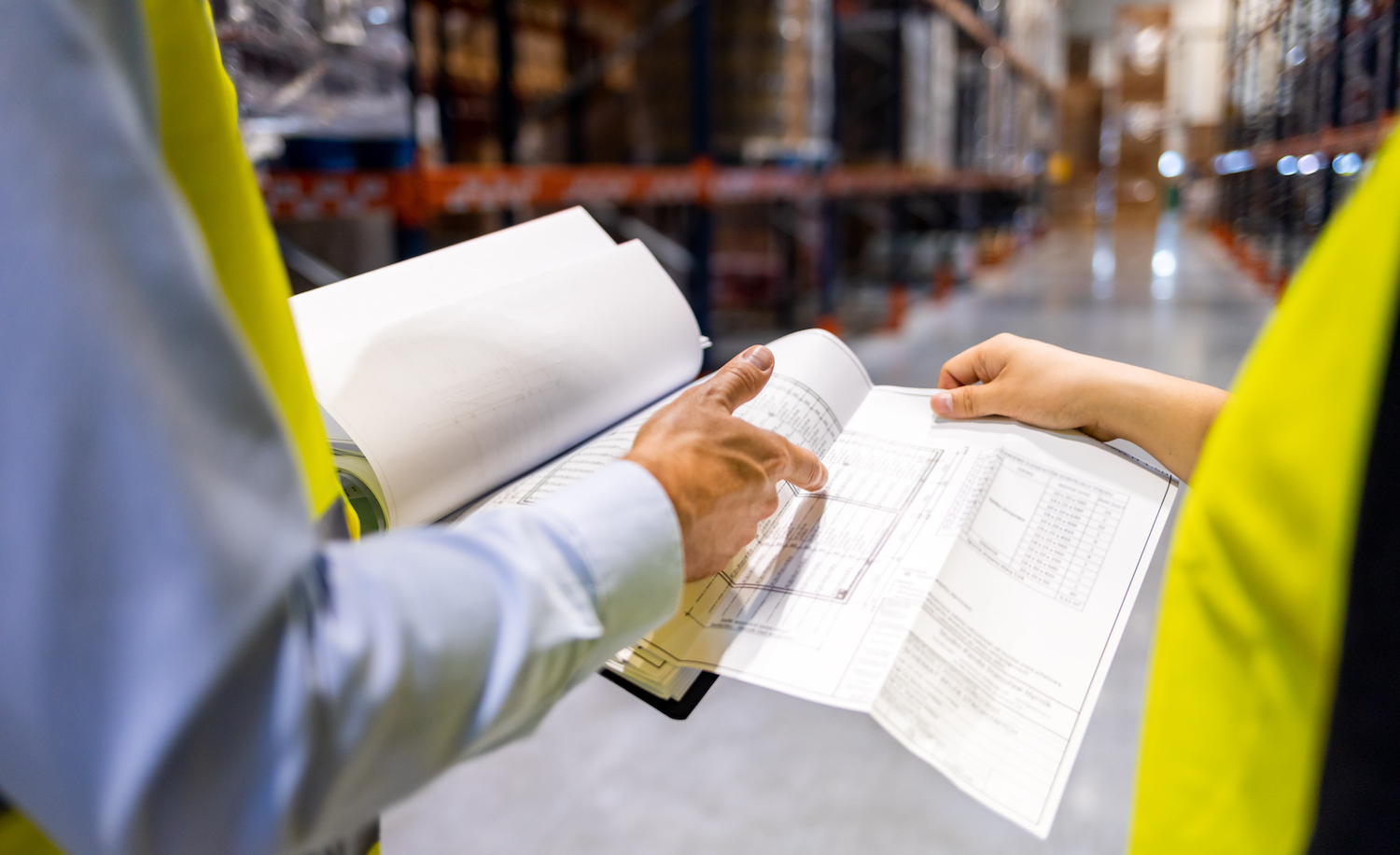
Benefits of designing a warehouse layout
A well-planned layout of your storage facility aims to facilitate smoother production and distribution processes. Before you know it, this ends up enhancing overall operational efficiency.
Without an efficient layout, valuable time is wasted on basic tasks like searching for items, navigating through aisles, and keeping track of inventory. This inefficiency can lead to higher operating costs and disrupt the smooth flow of the supply chain, delaying deliveries to customers.
Whether setting up new warehouses, expanding, or reorganizing current ones, designing a warehouse boils down to optimizing the space you have. At the foundation of every good warehouse layout lie concrete principles that aim to:
- Control inventory effectively
- Maximize use of space
- Minimize handling of goods
- Ensure easy access to goods
- Create product placement flexibility
Challenges of warehouse layout design
A good warehouse layout comes with a ton of benefits, but designing it has its share of challenges. While a well-designed layout can help alleviate many issues, preparation is key. Like in life, the key to addressing potential challenges is proactive preparation. But what is there to fear when discussing warehouse layout design?
Here are four main challenges businesses often come across during warehouse design planning:
- Keeping things safe — Safety is a top priority. Make sure there’s plenty of room to move around safely and keep an eye on equipment to ensure it’s in good working order.
- Planning for the future — It’s important to think ahead. Make sure to create adaptable designs for order changes, like reserving some shelving space for expected shifts in orders. This helps you adapt as your business grows.
- Making the most of your space — Don’t let any space go to waste. It’s important to use every available warehouse surface with a clear purpose, so make sure every nook and cranny is used efficiently to maximize your storage capacity.
Wasting space — Too much stuff in small areas risks injuries and mess, so preventing clutter and crowding is a must. It can lead to accidents, confusion, and items getting lost or damaged.
Where to start with warehouse layout design
Before embarking on the layout planning journey, it’s crucial to assess your needs. A well-planned warehouse layout should meet these set goals, starting from deciding the necessary warehouse zones, the shape of the storage facility, and the flow you need it to have.
A warehouse usually consists of several main areas, each serving a specific purpose in managing inventory and facilitating the movement of goods. Let’s take a look at the key warehouse areas that can simplify both stock management and shipping.
Reception area
Where new stock arrivals and incoming shipments are unloaded and logged into the warehouse inventory system. This is where staff checks the contents of every package and ensures they are all correctly accounted for.
The reception area should ideally be positioned separately from the main warehouse space to serve multiple purposes, including receiving goods, conducting quality control checks, and sorting items. Keep in mind that, in certain warehouse settings, there may be a need to modify the received units. For businesses dealing with this, it’s essential to designate a suitable area for this purpose.
Storage area
To make the most of your storage space, it’s helpful to split it into dynamic and static areas.
Dynamic storage
Dynamic storage houses high-demand goods that don’t have an established place within the warehouse. Because things are always changing in the world of supply and demand, the contents of dynamic storage are ever-shifting, too. These items usually need to be easily accessible near packing stations and change based on supply and demand.
Think of this section of the warehouse as the quick-access zone, where popular products are kept nearby for speedy fulfillment. This setup ensures that your team can easily grab what they need to pack orders efficiently and keep your customers happy with prompt deliveries.
Static storage
If dynamic storage is formed by hot-ticket items that fly off the shelves, static storage is represented by items that hang out for a bit before they’re ready to be sent out to customers. These items have permanent places that rarely change and are organized on racks to maximize space use. Keeping these two areas separate can prevent mix-ups and ensure your inventory stays accurate.
Staging area
The staging area is like the heart of the warehouse. It’s where incoming and outgoing packages are prepared for shipping or integration into inventory. Here is where orders get packed for pickup before shipping, as well as where received packages are unboxed and sorted to determine their placement within the warehouse inventory system.
When it comes to preparing orders, there are two main ways to do it. First, you can do it within your storage areas, which is common when picking items directly from racks. Alternatively, you can have separate picking areas. These spots are designed just for that task, and they often come with cool automated systems to make the picking process a whole lot smoother.
Shipping area
It’s in the name as these areas are well-oiled waiting rooms for goods ready to be sent out. However, it can also double as the spot for items that need to be assembled and packaged before being loaded onto delivery vehicles. For smooth movement in the warehouse, these spaces need to be in specific locations and clearly separate from the rest of the setup.
Arranging and combining these specific areas can help reduce points of congestion, facilitate movement and maintenance tasks, as well as reduce runtimes. This is why each and every one of them must be perfectly defined when creating a warehouse layout.
Widely-used warehouse layout designs
According to business needs, every company must establish a floor plan that best suits their profile. Here are the top three most common types of warehouse layout designs:
- U-shaped — This design resembles a semicircle, forming a shape similar to the letter U. Receiving and shipping areas are positioned at the ends of the U, while storage occupies the space in between. These types of layouts are well-suited for smaller warehouses, but there may be issues with truck congestion if shipping and receiving bays are located too closely.
- I-shaped — In this layout, the warehouse is shaped like a straight line, similar to the letter I. Shipping operations are situated at one end, receiving at the other, and storage is centralized in the middle. This simple design facilitates a streamlined flow of goods, ideal for warehouses handling high-volume orders.
- L-shaped — This design follows an L shape, with shipping and receiving areas occupying the two ends, while storage is located in the corner. These layouts are beneficial for businesses involved in cross-docking, where items are swiftly transferred from inbound to outbound trucks. They are common in companies that prioritize rapid shipment and do not use extensive storage racks.
10 warehouse layout tips to boost efficiency
Once your areas are clearly outlined, try implementing a few tested tips and tricks. They can optimize your warehouse layout and save time and resources.
Designing an efficient warehouse layout is one of those business decisions that can make a difference from the get-go. But it can also set the stage for long-term savings, finances, and operational complexity. Sure, it takes a lot to put in the effort, manpower, and necessary resources to craft an effective warehouse. However, the manner in which this simple initial step can bolster overall profitability cannot be overstated.
Here are 10 practical warehouse layout tips to boost efficiency while enhancing productivity and profitability:
- Go up — Make use of the vertical space in the storage facility. Stack items on tall shelves, pallet racks, and ceiling racks to maximize storage capacity.
- Know where you are — Warehouse layouts can get pretty big. Having detailed maps with the warehouse routes leads to fewer human errors and smoothes out the overall production flow. Floor markings are another great way of in-your-face signaling for certain important areas.
- Wide aisles are your friends — Nothing like wide aisles to ensure easy navigation and traffic flow.
- Automation is your best friend — Industry tech like automated storage systems, digital warehouse management systems, and inventory management software has become essential in streamlining operations and putting your business ahead of the competition.
- Humidity is the enemy — Don’t overlook monitoring warehouse conditions. Temperature and humidity can impact various types of inventory, but mostly electronics, food, and medicine. Start by checking areas near windows or air conditioning units since they are most prone to water damage. Furthermore, you can install sensors and alarms to track the climate throughout the warehouse.
- Pick a sorting system and stick to it — Whether you choose to group similar items together or use color-coded labels for quick identification, a good inventory system goes a long way to facilitate efficiency and ease in finding the goods you need.
- Don’t underestimate good lighting — Adequate lighting throughout the warehouse not only improves visibility but can also reduce errors and unfortunate mishaps or accidents.
- Always separate hazardous materials — One rule of thumb in a warehouse is that dangerous items are to be stored separately. In order to safely store hazardous materials, dedicate them to a specific area and always ensure it is clearly marked.
- Design around your products — Yes, this tip should be a no-brainer. But it’s exactly because of its obviousness that it often gets disregarded. Just like your business, each warehouse is unique. Since a good warehouse layout needs to cater to the items it hosts, its layout must accommodate product sizes, shapes, and various special requirements.
- Security is a must — Keeping the items in your warehouse safe is essential. Your best allies in deterring theft or unfortunate misplacements are CCTV cameras and security alarms. However, you can go the extra mile and add motion sensors, controlled access, and RFID readers.
Planning your warehouse layout design with Katana
From inventory management to manufacturing and all the way through order fulfillment and shipping, a well-planned warehouse layout is instrumental in reducing expenses and optimizing output. And Katana is just as instrumental in designing it.
Katana offers solutions to enhance operational efficiency and improve warehouse performance. It also provides insights and features to streamline all your processes. You focus on growing your company, while Katana helps assess your business needs and select the most suitable equipment to facilitate them.
Reach out to us to request a demo or learn more about our features!
Warehouse layout FAQs
What’s the best warehouse layout out there?
Long story short, there’s no Holy Grail of layouts and no one-size-fits-all solution. A well-designed layout involves implementing strategies such as utilizing innovative storage solutions, optimizing space utilization, prioritizing employee safety, integrating technology for operational enhancements, and maintaining flexibility to accommodate evolving business needs.
How can you identify a bad warehouse layout?
A suboptimal warehouse configuration could mean that you’re not maximizing your available space for crucial tasks such as receiving, storing, picking, packing, and shipping. This inefficiency might lead to increased operational costs, slower processing times, and a decrease in customer satisfaction. Indicators of a less-than-ideal layout include bottlenecks, difficulty locating items, and cramped aisle space, which could pose safety concerns.
What’s the best way to organize a warehouse?
Effective warehouse organization starts with understanding the nature of your inventory, preferred storage methods, available space, and workforce requirements. Customizing your layout to align with these factors ensures optimal efficiency for your specific operation. For example, if your inventory includes perishable items, it’s essential to allocate space for cold storage. Conversely, if you deal primarily with electronics, security, and protection might be higher priorities.
Do I really have to plan my business’ warehouse layout?
Absolutely. The layout of your warehouse can significantly impact various aspects of your business, including productivity, operational costs, lead times, and overall customer satisfaction. A thoughtfully designed layout promotes smoother daily operations, enhances order processing and fulfillment, and contributes to a safer work environment for your team.

Ioana Neamt
Table of contents
Get inventory trends, news, and tips every month
Get visibility over your sales and stock
Wave goodbye to uncertainty with Katana Cloud Inventory — AI-powered for total inventory control