10 manufacturing best practices for 2023
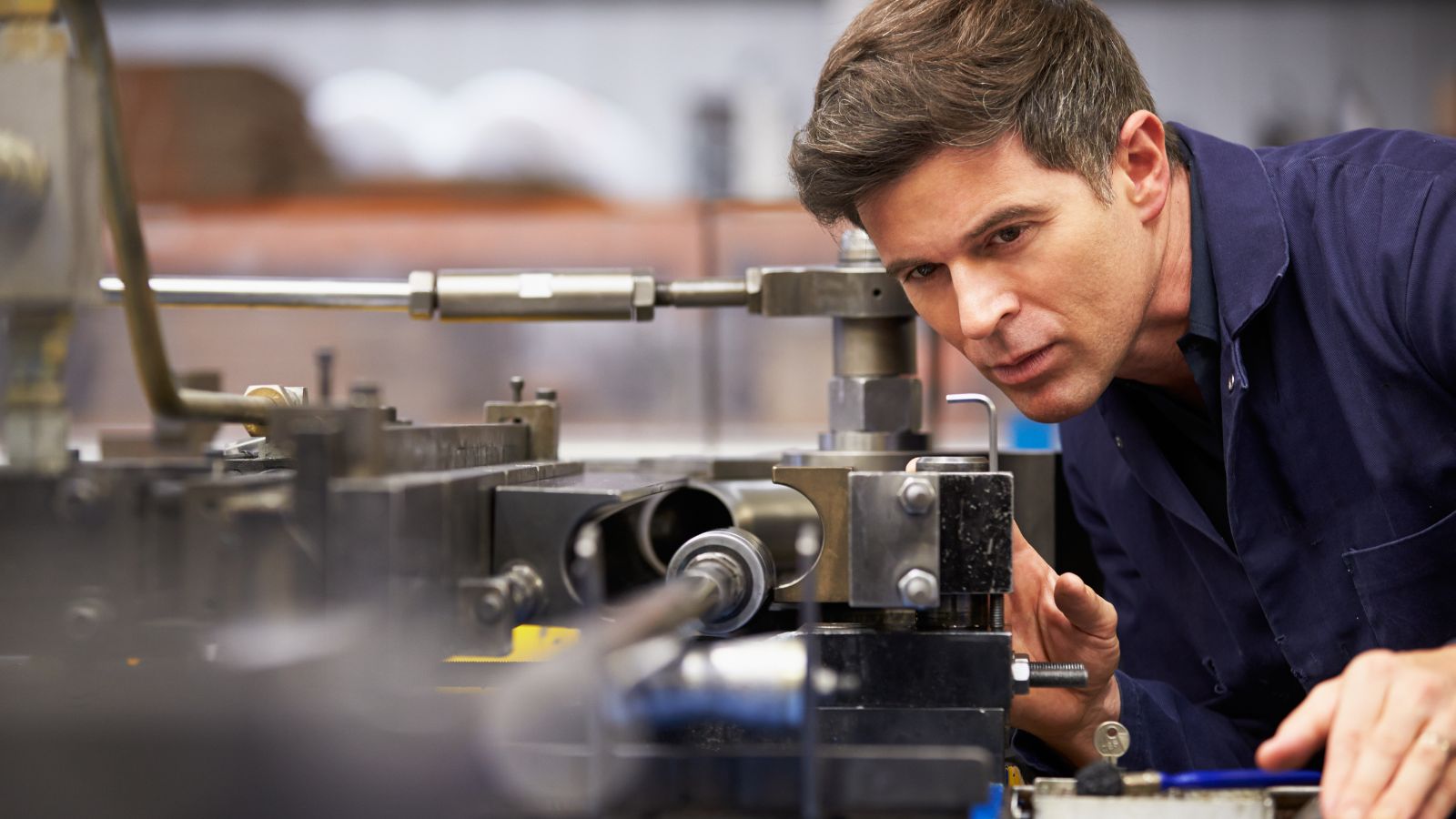
In 2023, the manufacturing industry experienced several nearly unprecedented roadblocks, from supply chain disruptions to workforce shortages.
As the industry continues to evolve, manufacturers must be proactive with their business practices to prevent such issues from having catastrophic effects on their operations. What worked in the past may not be enough to remain competitive in the years ahead, so companies need to stay on top of the latest manufacturing best practices. Continuous improvement, frequent communication, and a focus on sustainability will be key components moving forward.
In this article, we will examine 10 industry best practices that are geared toward the future, not the past. By implementing these strategies in their operations, manufacturers can maximize their profits for years to come.
1. Invest in automation
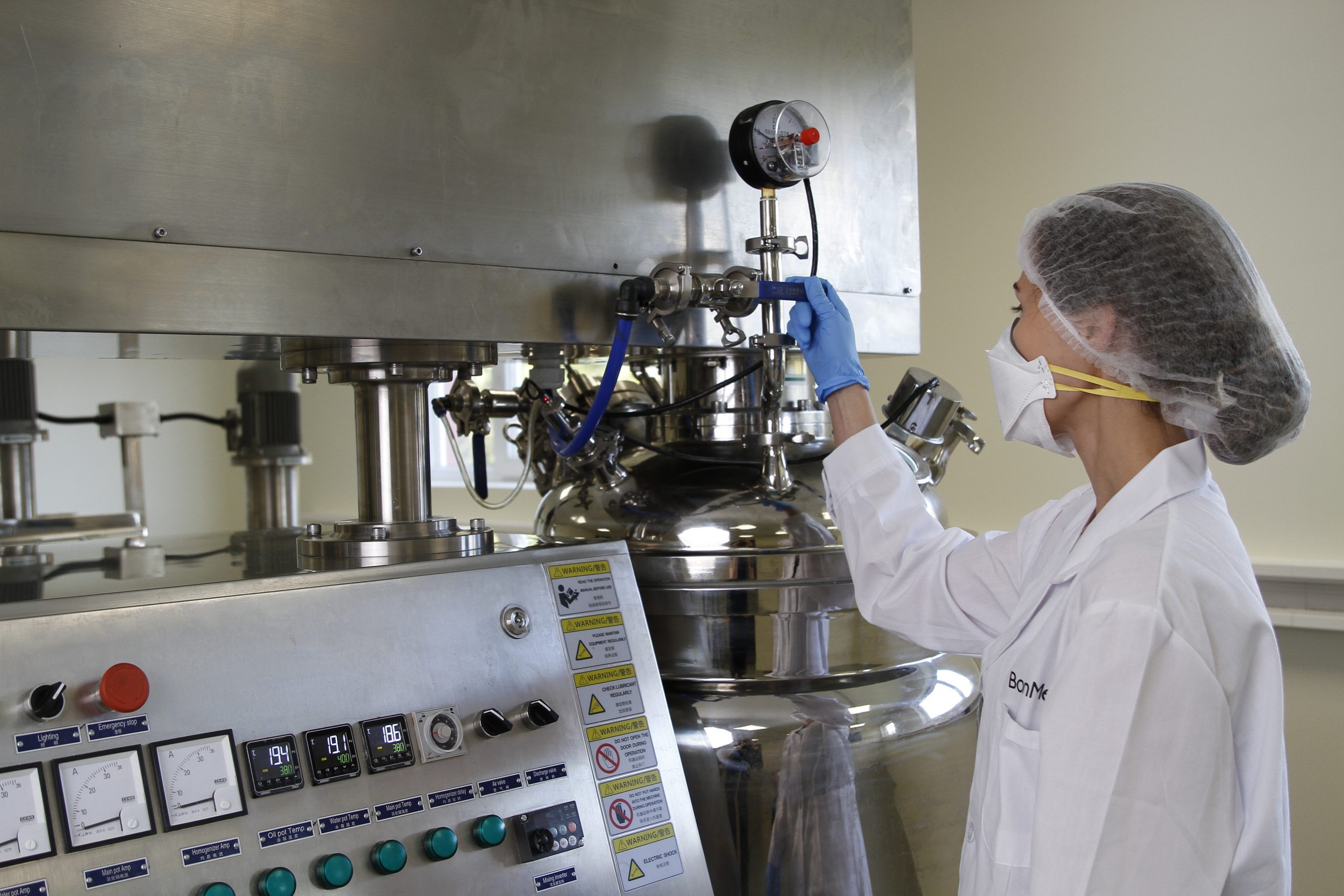
Through increasingly-rapid technological leaps, automation has become one of the most cost-effective solutions for manufacturers.
Because of this, the industrial automation market size is expected to rise from $189.7 billion in 2021 to $430.0 billion by 2030. This massive rise in the market is reflective of the advantages automation can bring to a manufacturing business.
No longer does this refer to robotic arms on a factory floor. Automation now also includes software-driven solutions, such as predictive analytics and machine learning tools used to optimize production processes or monitor inventory levels in real time.
As more money flows into automation, the potential outcomes only improve as artificial intelligence scales more and more effectively.
The benefits of investing early in automation technology can be measured in both cost savings and new opportunities. Things like:
- Reduced labor costs
- Reduced downtime, errors, and waste
- Improved product quality and consistency
- Increased productivity
Automation will be the cornerstone of future success with the rapid movement toward a digital-first world.
2. Move toward digital
Digital manufacturing is a process of creating, developing, and producing products in a virtual environment. This includes everything from engineering products to designing production facilities, sales funnels, and marketing materials.
Manufacturers can greatly minimize initial costs and future risks by leveraging digital assets instead of investing in physical production.
It allows manufacturers to quickly test and iterate on products, helping them stay agile in the face of ever-changing customer needs. It’s also possible to track customer feedback, analyze data trends, and use machine learning tools to improve production cycles.
The combination of automation and digital manufacturing is a powerful one that can help companies stay competitive in an increasingly-connected industry.
3. Focus on talent management
In the face of a global pandemic, many manufacturers had to adjust their talent management strategies quickly. These changes included everything from remote working policies to virtual onboarding and training sessions.
As industry best practices continue to evolve in 2024 and beyond, manufacturers need to focus on talent management as a way to stay competitive. This includes recruiting top-tier employees with the skills necessary for success in this new landscape.
It also means finding ways to retain existing personnel through flexible work arrangements, attractive compensation packages, and other benefits that make them feel valued.
Additionally, effective communication should be a priority at all levels of the organization. This means engaging with employees regularly, offering feedback and recognition when appropriate, and providing the necessary resources to ensure that everyone is working together toward shared goals.
4. Create supply chain redundancy
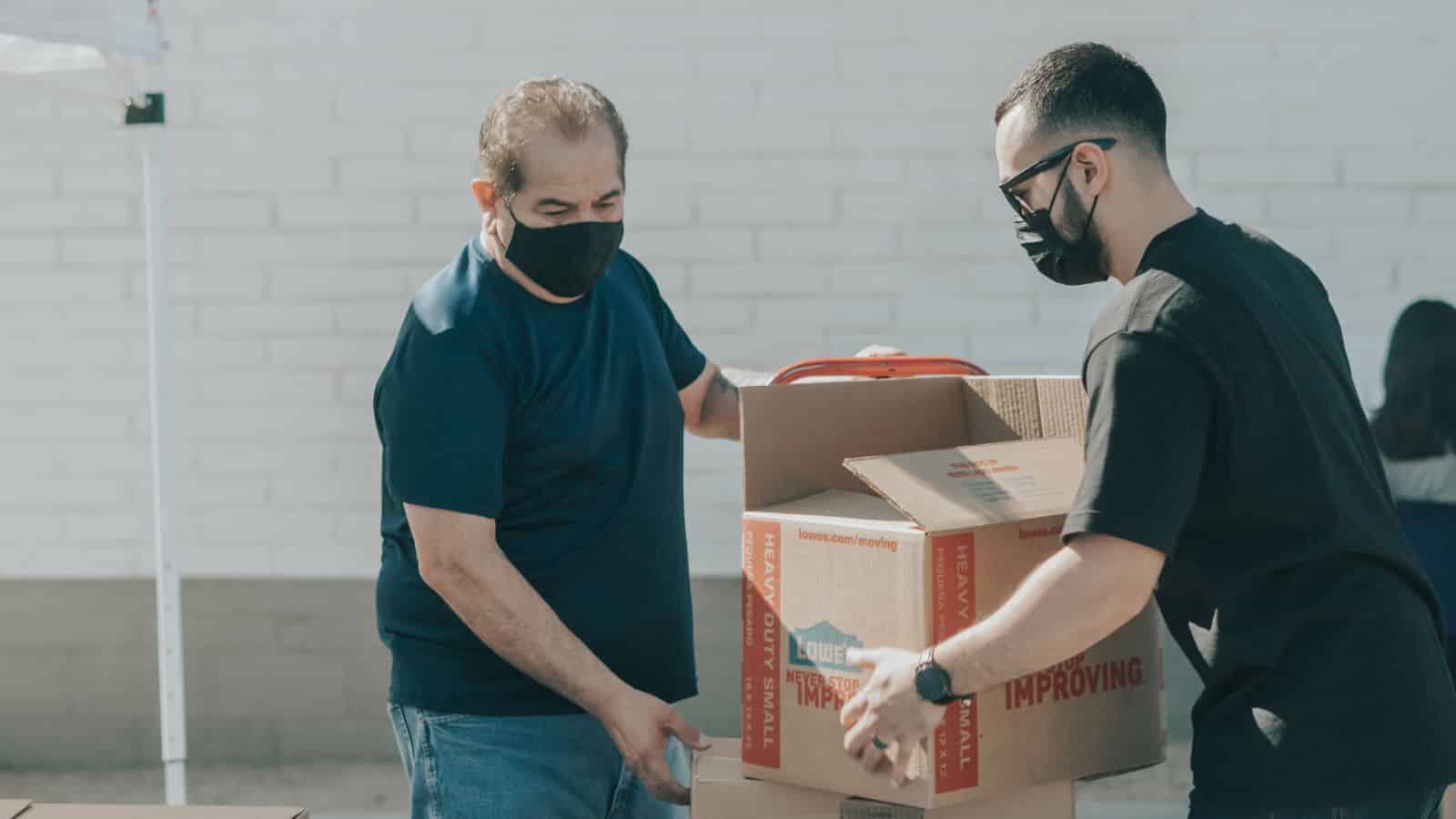
More than 80% of respondents to a McKinsey survey reported raw material shortages over the past year as supply chains continue to be disrupted.
Manufacturers must be prepared for these types of supply chain crises by creating redundancy in their systems. This means having multiple sources for raw materials, components, or subassemblies that can quickly step in to fill any gaps due to a disruption.
For example, an automotive manufacturer could create relationships with different steel suppliers worldwide so that if one could not deliver, another could take its place without too much disruption.
5. Begin preventive maintenance
Preventive maintenance is the practice of proactively maintaining equipment and systems rather than waiting for them to fail. This strategy includes regularly inspecting and testing machines for signs of wear or malfunction before any serious issues can arise.
By using predictive analytics, manufacturers can monitor the condition of their equipment in real time and use that data to schedule regular maintenance tasks. This will help prevent downtime due to unexpected malfunctions and increase machinery’s life expectancy, which can lead to significant cost savings.
6. Improve lean techniques
With the right information and technology, manufacturers can more efficiently manage their operations and reduce waste. Lean principles provide a framework for doing just that.
Lean manufacturing is the practice of reducing resource consumption while still producing high-quality goods. It’s based on the idea of “continuous improvement,” or Kaizen in Japanese culture, which encourages businesses to focus on making small changes over time instead of large leaps all at once.
Applying lean techniques to a business requires an understanding of each activity involved in the production and how they interact with one another. This helps identify areas that need improvement, such as eliminating unnecessary steps or using fewer resources.
7. Take sustainability seriously
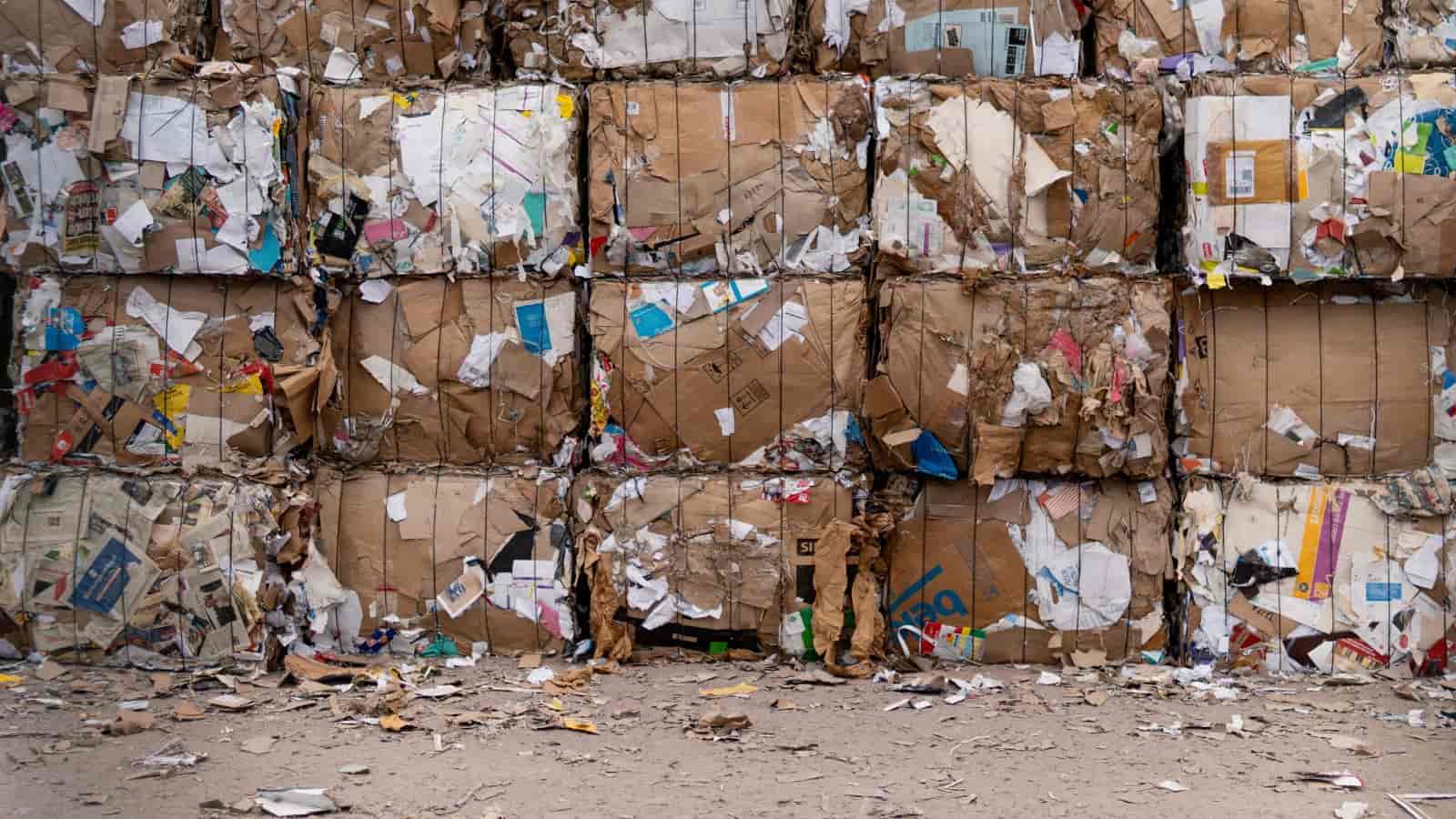
The environment has become a major factor in the success of any business. Consumers are increasingly demanding that companies reduce their carbon footprints and adhere to sustainable practices, no matter which industry they’re in.
Manufacturers should take this demand seriously by focusing on reducing energy consumption and waste production throughout their operations. This includes investing in renewable energy sources, utilizing recycled materials, and implementing efficient processes to avoid unnecessary consumption or emissions.
In that way, a focus on sustainability can go hand-in-hand with lean techniques that focus on producing high-quality output with the least amount of resources.
The good news is that sustainability efforts can be rewarded. These days, companies are increasingly rewarded for their commitment to environmental impact reduction and sustainable practices. This includes tax incentives, grants, and other financial benefits from government programs or private organizations.
8. Build resilience with sophisticated technology
Manufacturing is becoming increasingly complex with the integration of new technologies. As such, manufacturers need to be prepared for unexpected disruptions and must develop a strategy that accounts for them.
One way to do this is by investing in sophisticated technology to help build their operations’ resilience. This includes systems like artificial intelligence (AI), blockchain platforms, and predictive analytics tools.
AI can be used to identify potential hazards before they happen, while the blockchain provides an immutable record of events that can be tracked over time. Predictive analytics tools allow manufacturers to plan more effectively, so they are better equipped when something does go wrong.
By having this level of control and foresight, manufacturers can reduce risk and make better decisions.
9. Partner with experts
To get the most out of this tech, consider partnering with the right external teams with access to specialized knowledge and skills that are otherwise unavailable in-house. This can be especially helpful when implementing new or making changes to existing processes.
Not only will these experts have a better understanding of how different systems work together, but they’ll also be able to offer insights into areas where improvements could be made.
The best manufacturing practices mean nothing if you are trying to execute them without the right help. Partnering with experts in their respective fields can provide manufacturers with valuable guidance and support when introducing new technologies.
10. Increase visibility
The most important of the manufacturing best practices is visibility. Manufacturers must have access to accurate, real-time data to make informed decisions.
This means having a comprehensive view of the entire supply chain, from raw materials and components to finished products and customer orders. This can be achieved through connected systems that share information across departments and stakeholders.
The data collected should also include key performance indicators (KPIs) that measure progress towards goals such as cost reduction, efficiency gains, or improved quality standards.
By tracking KPIs over time, manufacturers gain valuable insight into their operations and quickly identify areas for improvement. Additionally, increased visibility will help them respond faster to customer needs and stay ahead of the competition.
Want to see Katana in action?
Book a demo to get all your questions answered regarding Katana’s features, integrations, pricing, and more.
The easiest way to implement manufacturing best practices
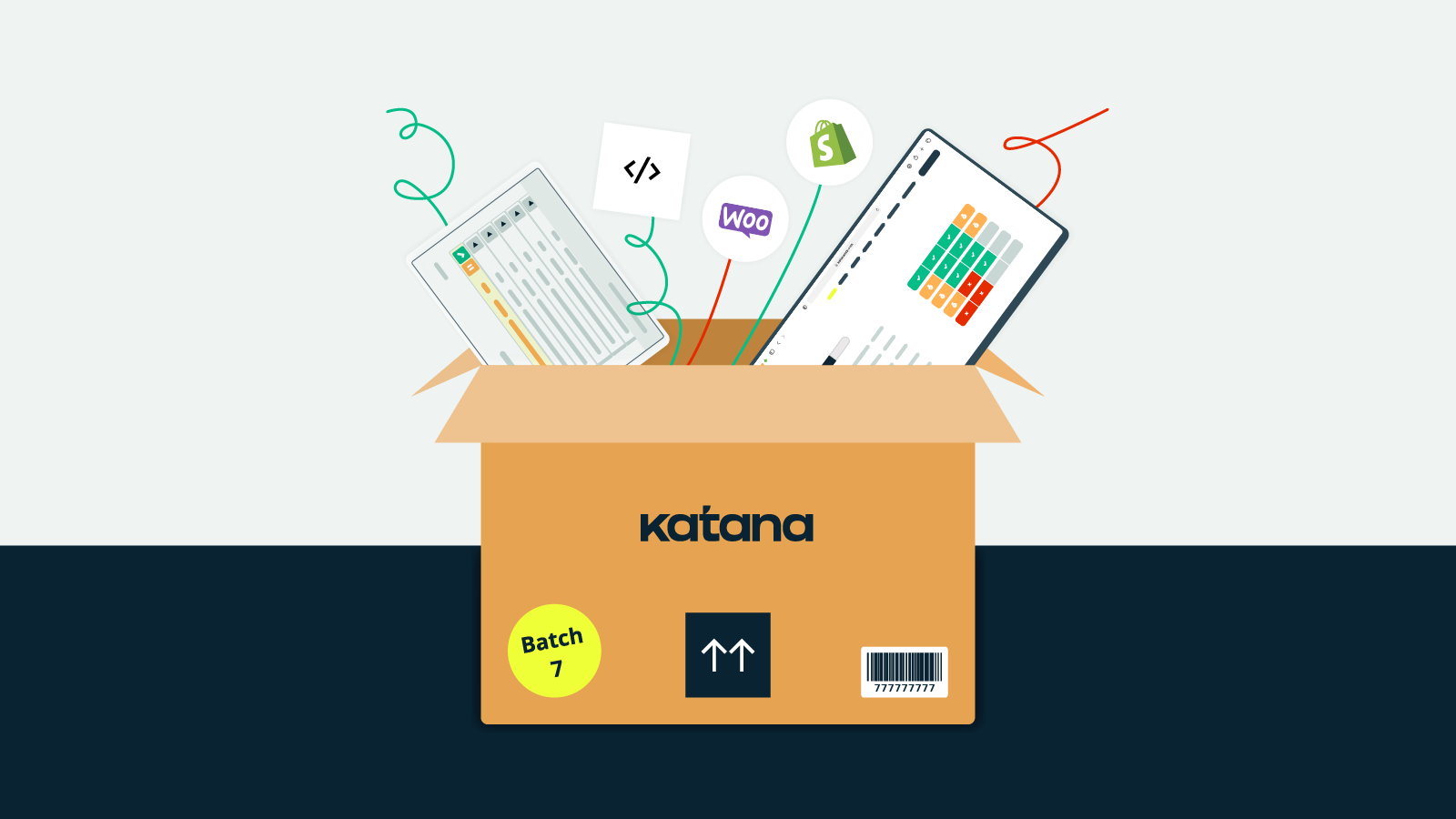
Using platforms like Katana’s cloud system, manufacturers can access the insights and technologies needed to remain competitive in the years ahead. By leveraging these manufacturing best practices, they can reduce risk and create a more resilient operation that is better prepared for whatever disruptions may come along.
The future of manufacturing will be shaped by those who embrace change and make investments that improve their operations today. With the right tools and strategies in place, they can stay ahead of the curve and maximize their profits in 2024 and beyond.
To get started with some manufacturing best practices, get a demo now!
Table of contents
Manufacturing guide
More essential guides from Katana
Get visibility over your sales and stock
Wave goodbye to uncertainty by using Katana Cloud Inventory for total inventory control
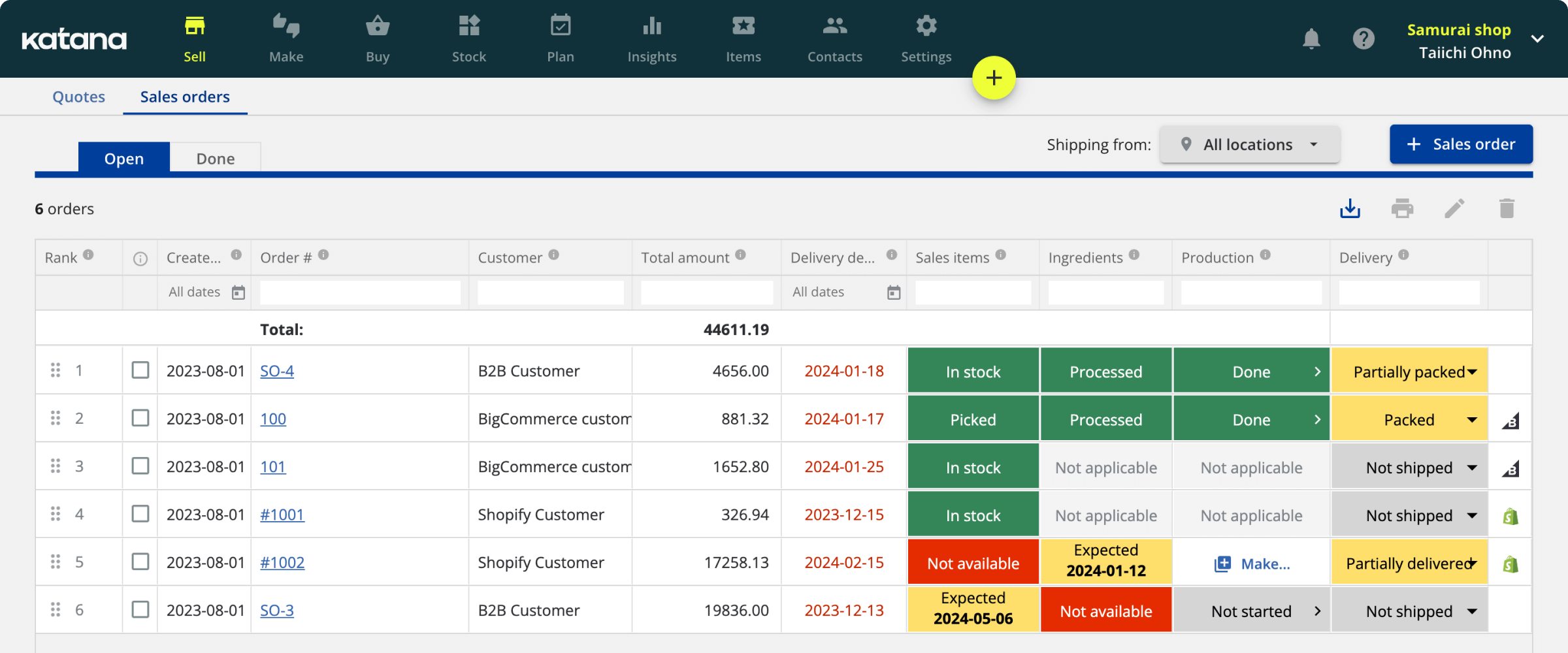