Lean manufacturing principles to streamline production and eliminate waste
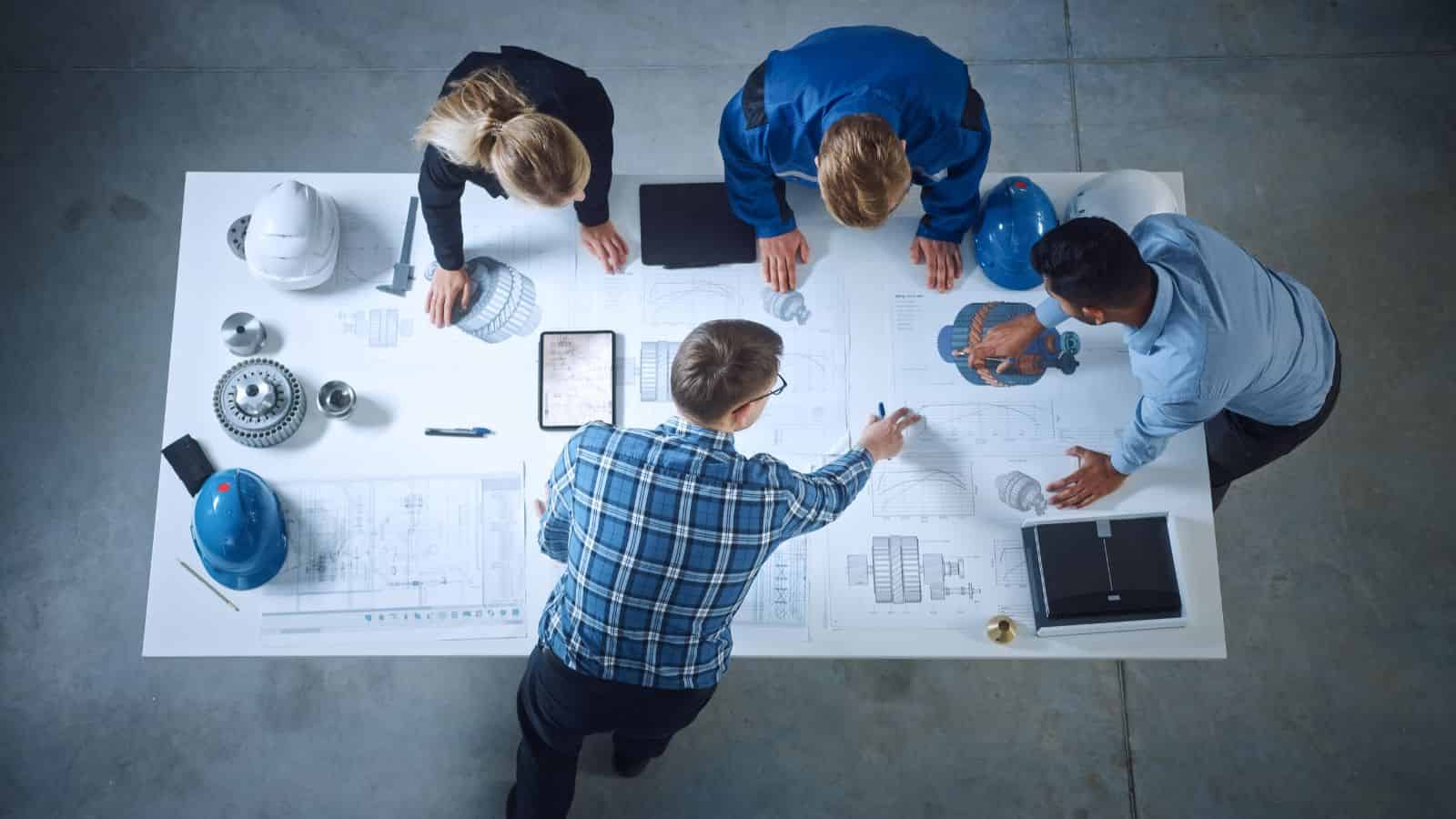
The world went from craft production to mass production with the Industrial Revolution, which was great in many ways. However, mass production wasn’t without problems.
The sole focus of mass production was to produce goods faster and lower the manufacturing cost per unit. As time went by, assembly lines developed a “move the metal” mentality, leading to defective products and higher attrition of assembly technicians. Addressing this issue is how lean manufacturing principles came to be.
The moving assembly line pioneered by Henry Ford in 1913 accelerated the shift from craft to mass by increasing the efficiency of production processes.
It didn’t stop there — a host of other innovations made Ford’s manufacturing system so successful that by 1926, it was producing nearly half of all the motor vehicles in the world. Over time, these process improvements and methods were adopted by other industries. Companies that adopted this production process needed to have dedicated rework areas where the products could be disassembled and repaired. Manufacturing defects and a rapid churn rate among the workforce meant a waste of resources and, ultimately, higher prices for customers.
This was the context that led to the development of lean principles.
History of lean manufacturing
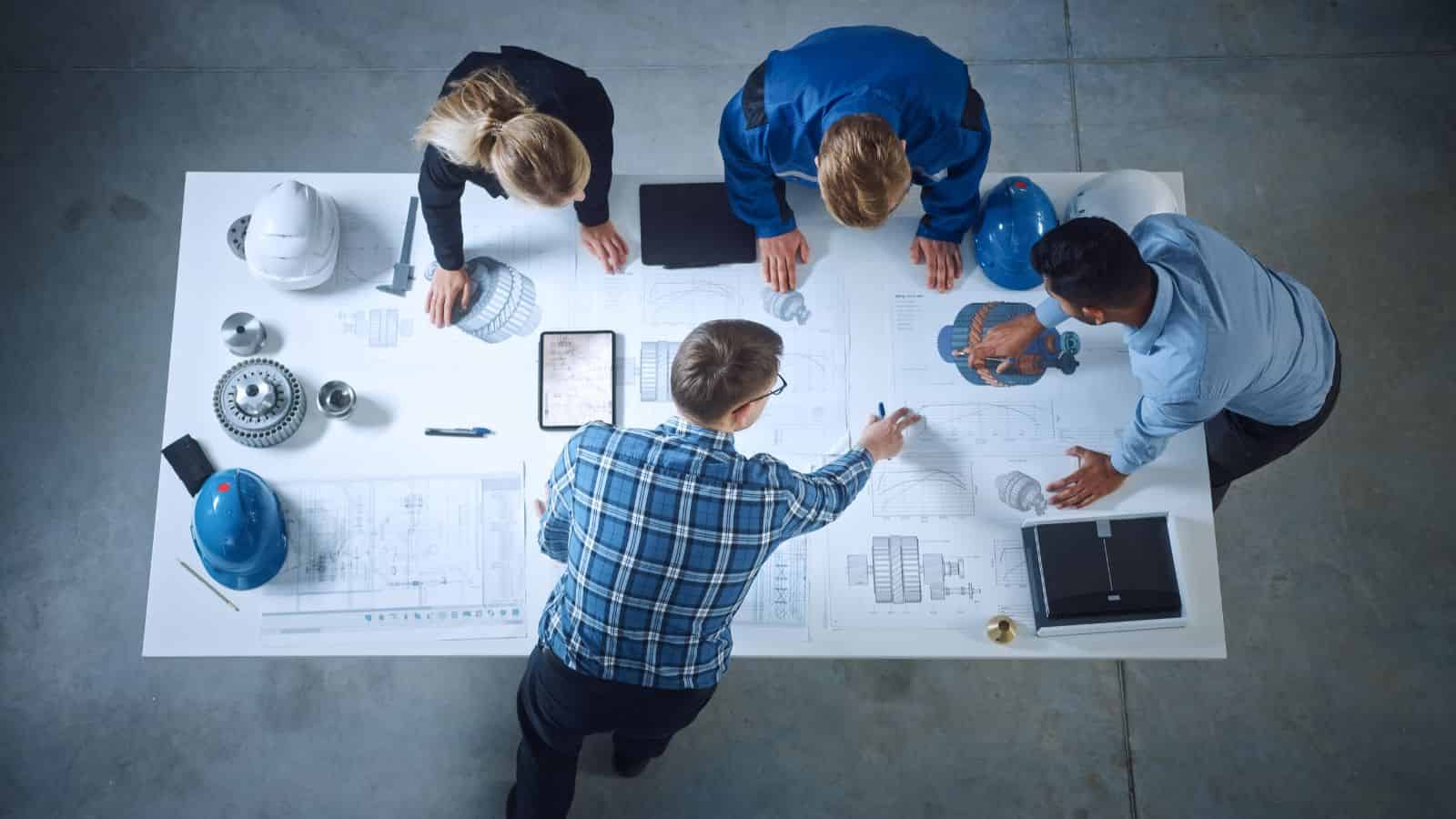
After understanding the flaws in mass production systems, coupled with their own insights on manufacturing practices, Taiichi Ohno and Eiji Toyoda of Toyota created the Toyota Production System (TPS).
Post World War II, Japan was cash and resource-strapped. Toyota was forced to move away from prioritizing higher output and working with excess inventories, which was the norm in mass manufacturing. Instead, they built their manufacturing system to focus on just-in-time (JIT) production, continuous improvement, and waste elimination.
For instance, their system allowed technicians to halt the entire assembly line in order to fix a defect as soon as they spotted one — this was unimaginable in earlier production systems. Empowering the technicians to fix mistakes early in the process led them to make fewer mistakes and reduce waste over time.
The production systems that we now call lean inventory are a direct result of the Toyota Production System. These ideas were first described in the book “The Machine That Changed the World” by James P. Womack, Daniel Roos, and Daniel T. Jones. Later these were distilled into the five principles of lean manufacturing by Womack and Jones:
- Value
- Value streams
- Flow
- Pull
- Perfection
These are the fundamentals of lean manufacturing. We’ll take a look at the five principles in more detail soon but first, let’s go over the lean manufacturing definition.
Putting the lean manufacturing principles into action
Implement your lean manufacturing principles with ease by using a live inventory management system for real-time overviews of inventory and operations.
What is lean manufacturing?
Lean manufacturing is a production methodology that focuses on eliminating waste and maximizing efficiency. In lean manufacturing, all activities and processes are scrutinized to identify any areas where waste is generated. Once these areas are identified, they are streamlined or eliminated to improve overall efficiency.
One of the key principles of lean manufacturing is the continuous flow of information and materials. This means there is no stopping or starting in the production process — everything flows smoothly and continuously from one step to the next. This helps eliminate waste and maximize efficiency by ensuring no bottlenecks or delays in the production process.
What are the 5 principles of lean manufacturing?
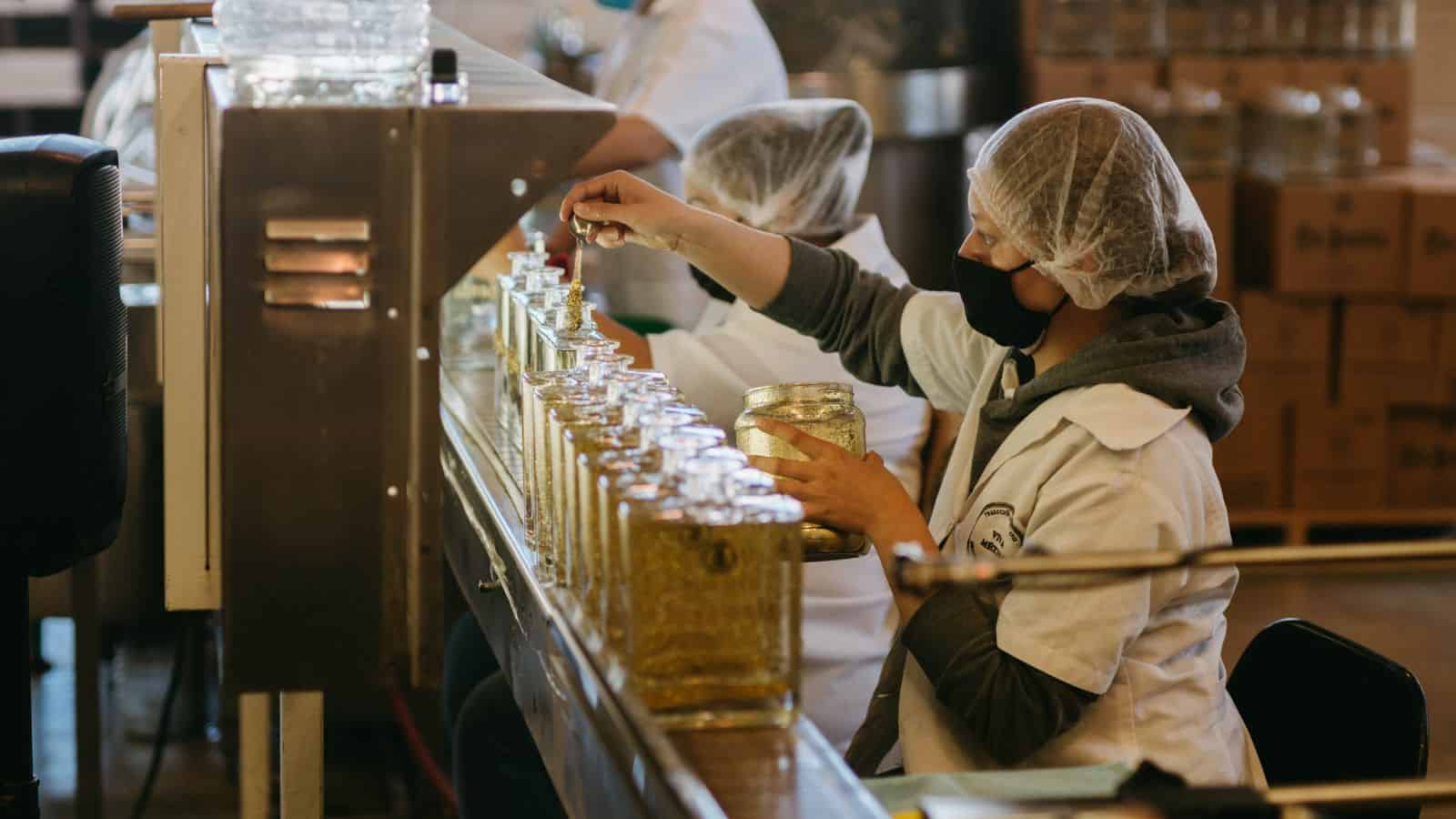
Now that we understand what is lean manufacturing let’s see what are the five principles of lean manufacturing developed by Womack and Jones.
1. Value
In order to optimize your manufacturing processes, you first need to understand how you deliver value to your customers.
The durability of your products or quick turnaround times may be the value your business delivers to customers and clients. This is why understanding and defining your business’ value is the first lean principle. Determining your value and, in doing so, knowing your competitive advantage, allows you to invest time and resources in the right activities.
For instance, if your edge comes from fast deliveries, knowing that narrows your focus to improving that aspect of your business — increasing the value for your customers.
You can identify the value you deliver in different ways, from one-on-one interviews with your customers to using cloud inventory software to help you analyze your sales data.
2. Value stream
Once you have understood what your customers value, you are in a good place to identify and map the value stream.
A value stream consists of all the actions in your business that go into taking raw materials to a finished product. You would start tracing your processes from creating the orders for raw materials all the way to delivering and maintaining the product. The idea here is to understand the factors and processes that contribute to making your product valuable to the customers.
Let’s use the earlier example of fast deliveries. You can break down how orders move through your system, from the customer placing the order to successful delivery. At every step, ask yourself how a specific process can be improved to achieve the goal of faster delivery times.
Mapping the value streams first provides a greater understanding of the manufacturing process. Often this leads you to discover processes that do not add value and are unnecessary. Needless to say, these are wasteful. In lean thinking, the elimination of waste plays an integral role.
Mapping value streams allows you to identify and minimize waste.
3. Flow
With value identified, value streams mapped, and waste minimized, you are in a great position to think about the processes that add value to your products.
In this step, lean thinking calls for streamlining your processes — this can involve breaking down each process into smaller steps, reconfiguring your shop floor, eliminating bottlenecks, or increasing the efficiency of your manufacturing operations.
With total shop floor control and end-to-end traceability built in, Katana can make value stream mapping and establishing flow in your journey of applying lean principles a breeze.
4. Pull
Building up and maintaining excess inventory leads to manufacturing overheads, such as:
- Storage costs
- Lost inventory
- Excessive spending on marketing of unsold products
- And more
These are rightly considered wasteful in lean. Your business production should focus on creating just-in-time delivery of products and raw materials across processes. This allows you to create a pull-based system for your products. Instead of spending time and resources on moving inventory, your business can become nimble enough to cater to orders as they arrive from your customers.
Establishing a pull-based system and moving away from a push-based one was one of the major shifts in thinking that came from the Toyota Production System and lean manufacturing principles.
5. Perfection
Although applying the first four principles can provide a great boost to your business, the pursuit of perfection is what will set you apart.
It allows you to acknowledge that efficiency and providing higher value to customers is a continuous process and requires building a company culture open to learning. Often great results come from persistence and constant refinement of the production process. You might have to go through the cycle of mapping value streams multiple times, and additionally, what customers value in your products could change over time.
For instance, during high economic growth, customer preference could shift towards buying premium products with better finishing and packaging.
At times like these, you need to go through the process of optimizing again. The essence of this principle is the willingness to go back to the drawing board and improve what is already working well. It is almost as if lean principles throw out, “If it ain’t broke, don’t fix it,” and propose, “If it ain’t perfect, make it” instead.
What are some of the lean manufacturing tools and techniques?
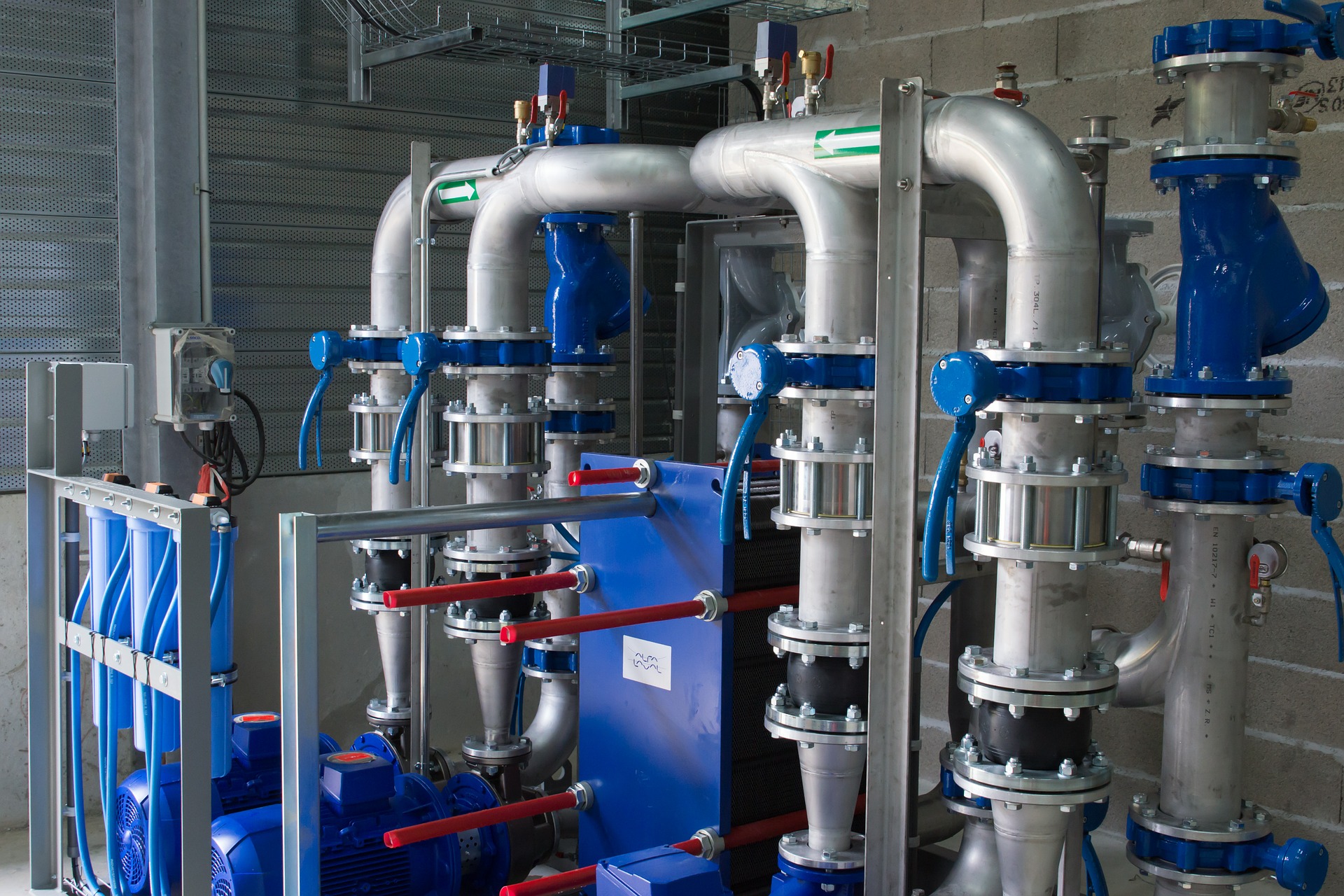
Lean techniques are those practices that contribute to the elimination of waste of any kind. There are a lot of different techniques, but the common goal is always to reduce waste and make the process as efficient as possible.
Let’s take a look at some of the most popular lean manufacturing techniques.
Kanban
Kanban is a scheduling system that helps you organize and optimize your manufacturing process. It uses visual cues (such as cards or boards) to signal when a particular task needs to be completed. This helps you to manage your production line better and avoid bottlenecks.
5S
5S is a technique for organizing your workspace to be more efficient and effective. It involves the following steps:
- Sorting — removing unnecessary items
- Setting in order — Organizing necessary items
- Shining — Cleaning the area
- Standardizing — Developing rules and procedures
- Sustaining — Maintaining the system over time
Poka-yoke
Poka-yoke is a Japanese term that means “mistake-proofing” or “fail-safing”. It is a preventative measure that is put in place to avoid errors from happening in the first place. For example, a poka-yoke could be a simple device that is used to ensure that a part is installed correctly before the next step in the production process can begin.
Jidoka
Jidoka, or autonomation, or intelligent automation, is a quality control technique where machines automatically stop the production line as soon as an error is detected. This allows you to fix the problem quickly and avoid making defective products.
Andon
Andon is a Japanese term that refers to a visual signal (usually a light or flag) that alerts workers to a problem on the production line. It is usually used in conjunction with Jidoka to help workers quickly identify and fix errors.
Kaizen
Kaizen means “improvement” or “change for the better”. It is a philosophy that focuses on continuous improvement of processes, products, and services. It involves everyone in the organization, from the top down, and encourages employees to suggest improvements.
Heijunka
Heijunka is a Japanese term that means “leveling” or “smoothing”. It is a technique used to even out production so that there are no peaks or valleys in demand. This helps to avoid overproduction and inventory buildup.
Kitting
Kitting is a manufacturing process where parts and components are gathered together to make a final product. This can help to improve efficiency by reducing the time and effort required to assemble products.
Single-piece flow
Single-piece flow is a process where each product is made one at a time and moved quickly through the production line. This helps avoid errors and waste and ensures that each product is of high quality.
Benefits of lean principles
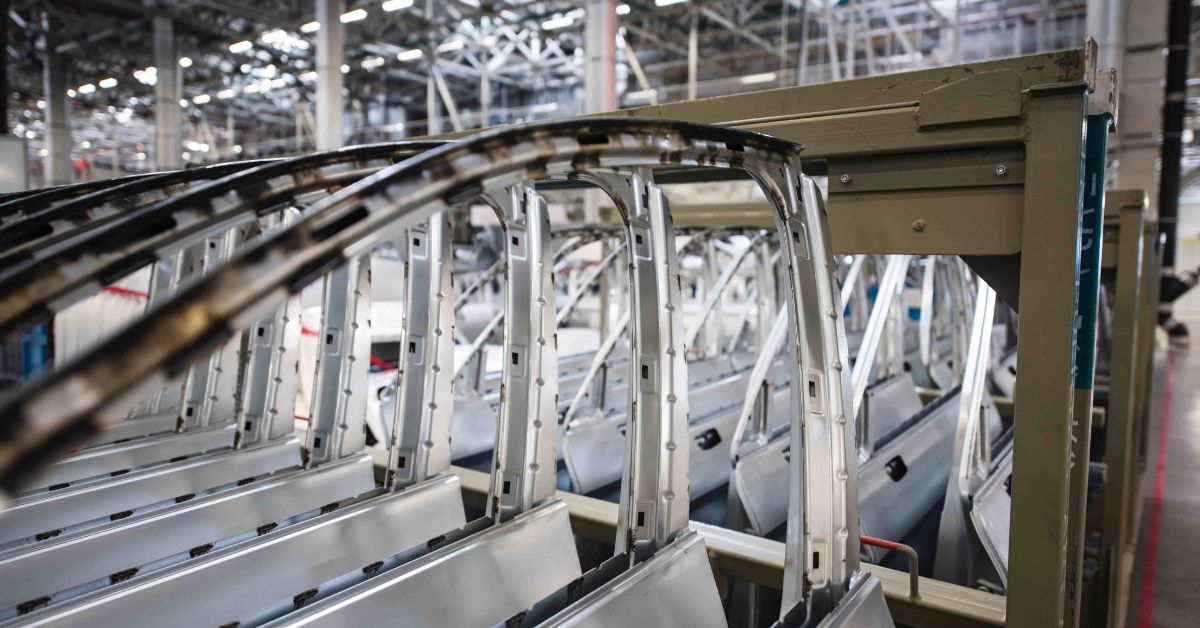
From large corporations like Toyota to smaller family-owned businesses like Buck Knives, plenty of companies have implemented lean principles to grow and stay competitive. The Lean Enterprise Institute also publishes detailed case studies and results from various companies using lean principles.
This is simply a testament to the fact that lean manufacturing principles have stood the test of time, but let’s look at some of the direct benefits:
- Improved customer satisfaction — Providing high-quality products that meet the buyer’s requirements translates to happy customers
- Reduced costs — Eliminating waste and reducing the time and resources required to manufacture products
- Increased efficiency and productivity — Optimizing resources and processes, resulting in less downtime and less rework
- Improved employee morale and engagement — Creating a work environment that promotes employee involvement and empowerment and is safe, clean, and organized leads to increased satisfaction and motivation
Types of waste to eliminate in the lean manufacturing process
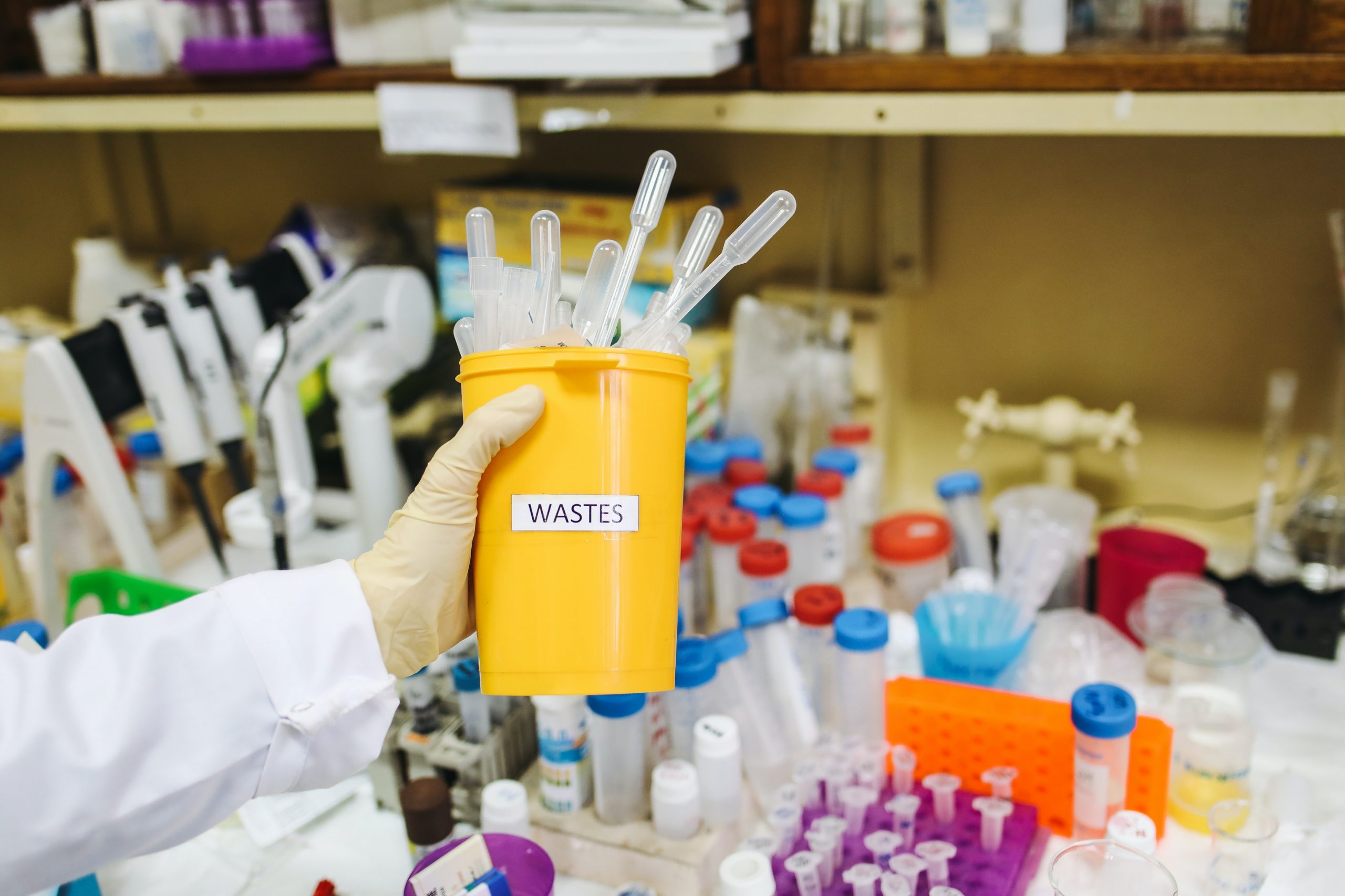
As we have established many times over, lean manufacturing is all about eliminating waste. Let’s see the seven types of waste that lean manufacturing aims to eliminate:
- Overproduction — When more product is produced than is actually needed by the customers. This can lead to inventory buildup and excess costs
- Waiting — When equipment or materials are unavailable when needed, which leads to delays in the production process
- Transportation — This is when products or materials have to be moved unnecessarily, which can lead to damage and wasted energy
- Motion — When workers or machines have to move unnecessarily, resulting in wasted time and energy
- Inventory — When there are more raw materials or finished products than what is needed for the current demand leading to waste and extra costs
- Defects — When products are not up to the standards required by the customer, resulting in double work
- Overprocessing — This is when more processing is done than what is actually needed, which can lead to waste and extra costs.
Lean manufacturing aims to eliminate all seven of these types of waste in order to create a more efficient and effective production process.
Become a mean lean manufacturing machine
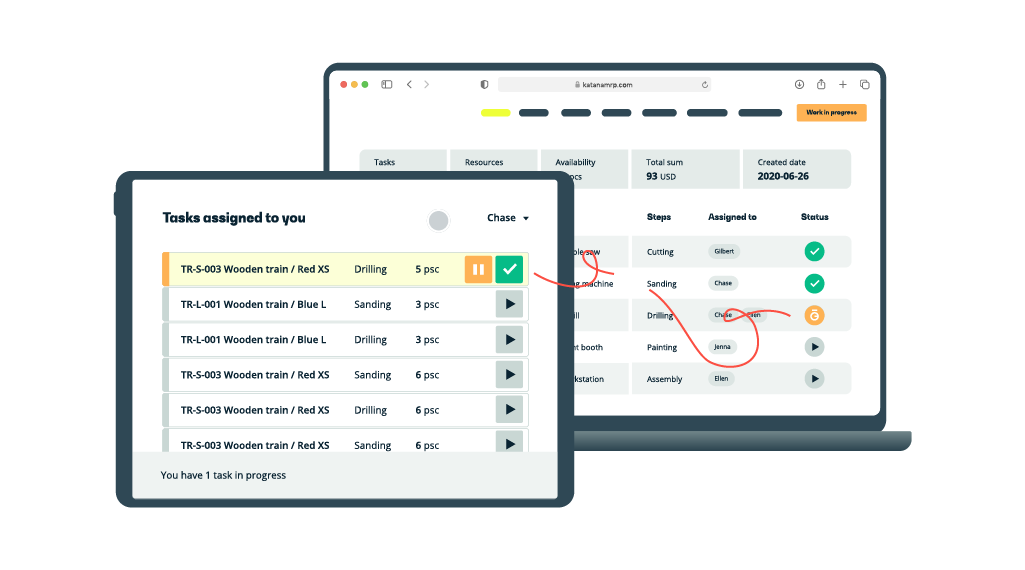
There you have it — with everything you’ve learned about lean principles, you are in a great place to start implementing them. As the saying goes, a journey of a thousand miles begins with a single step. The good news is that you’ve already taken that first step.
Implementing and following the lean principles does take work, constant monitoring, and tweaking. That’s why it’s important to have lean manufacturing software that enables you to do all that.
With features like real-time master planning, production planning, and purchase order management, Katana can simplify your processes and help you implement lean ideas in your business. Refund a demo and find out why thousands of manufacturers use it to optimize their business operations.
Table of contents
Manufacturing guide
More on manufacturing
Get visibility over your sales and stock
Wave goodbye to uncertainty by using Katana Cloud Inventory for total inventory control
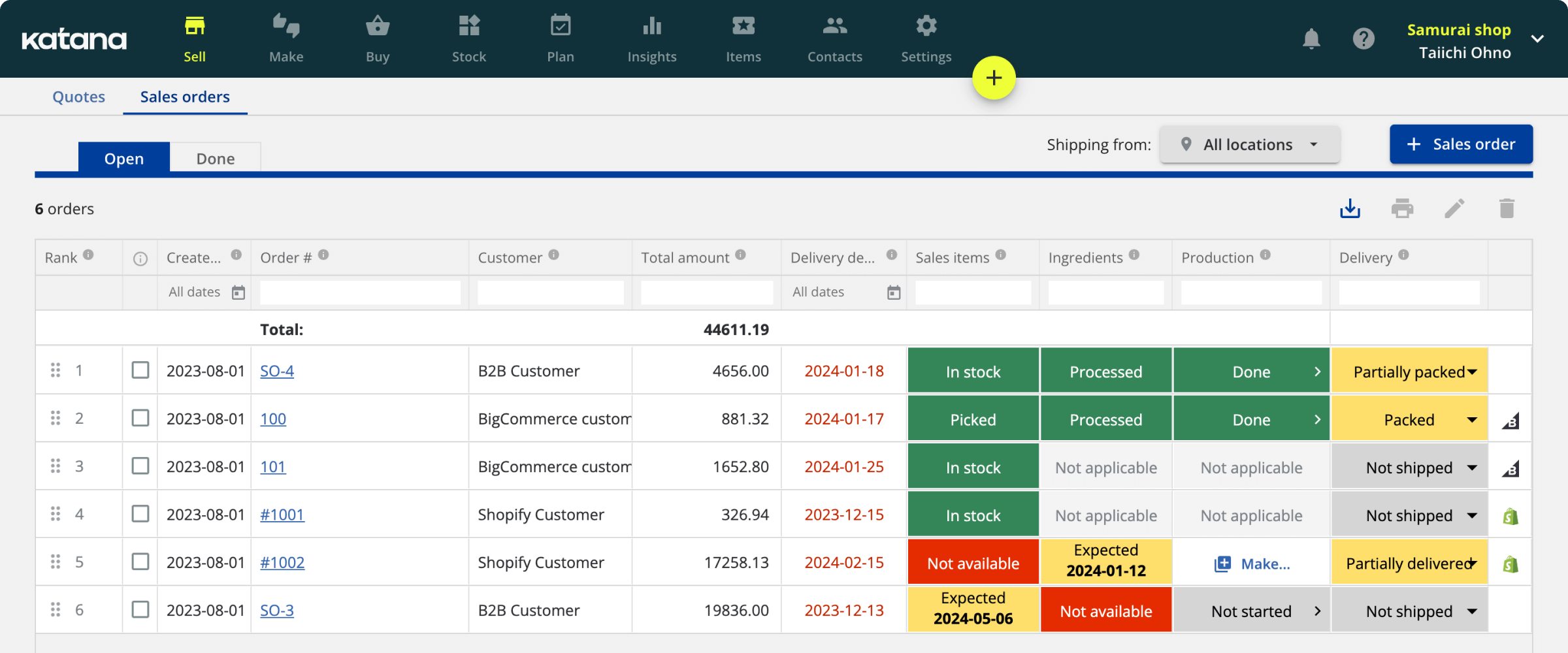