A comprehensive guide to just-in-time manufacturing
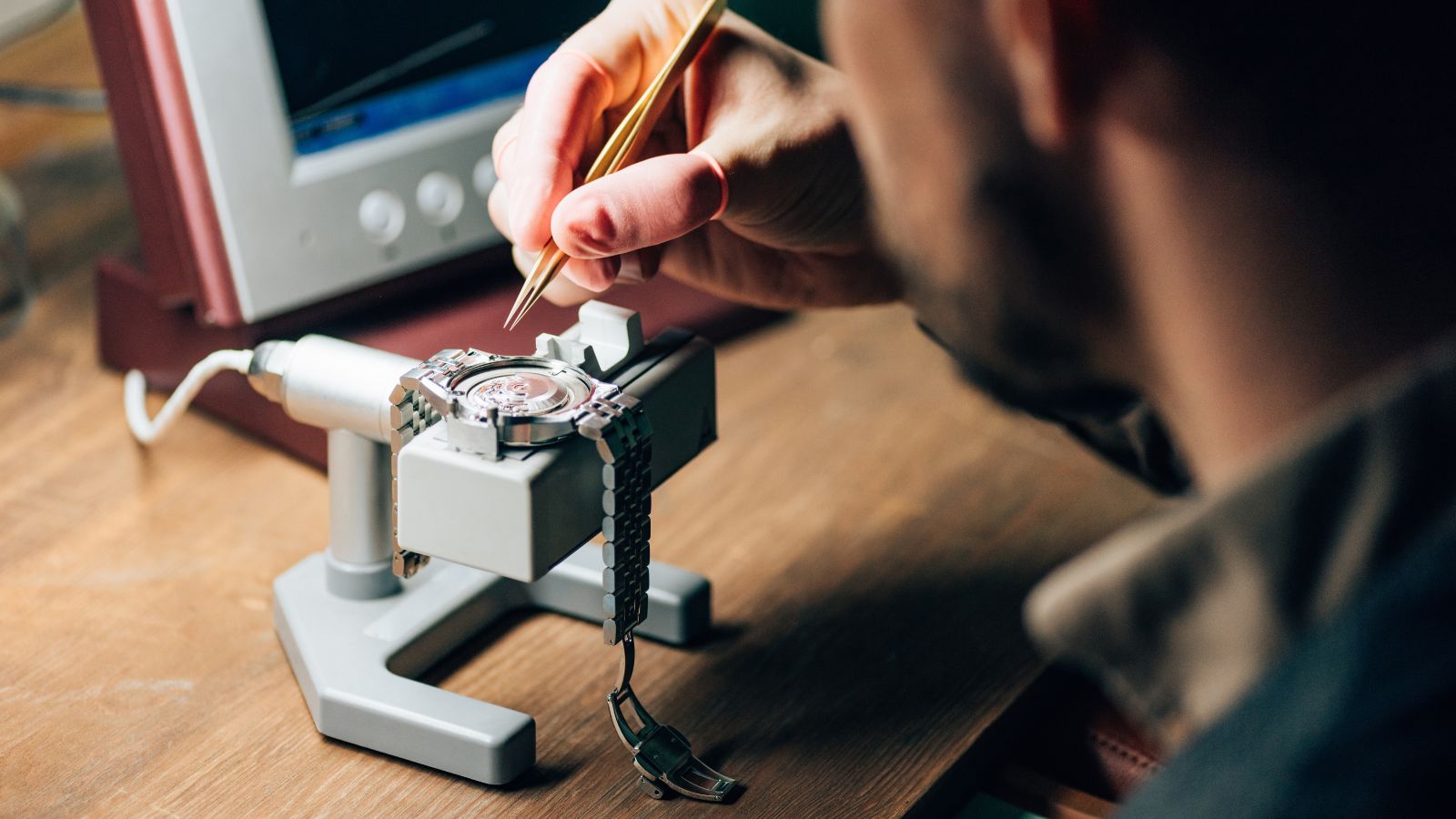
Just-in-time (JIT) manufacturing means using the resources at your disposal to their maximum potential while eliminating all waste in the process. This strategy minimizes carrying costs and the need for storage space and maximizes efficiency in production and inventory management all at once.
What sets JIT manufacturing apart from other inventory and manufacturing techniques is the minimal buffer that is created. Typical manufacturing is seen as the production of goods that are then set aside on a shelf to wait for incoming orders.
JIT production works the other way around — an order comes in, and then manufacturing starts, working with just the right amount of supplies and materials.
Historical background of JIT manufacturing
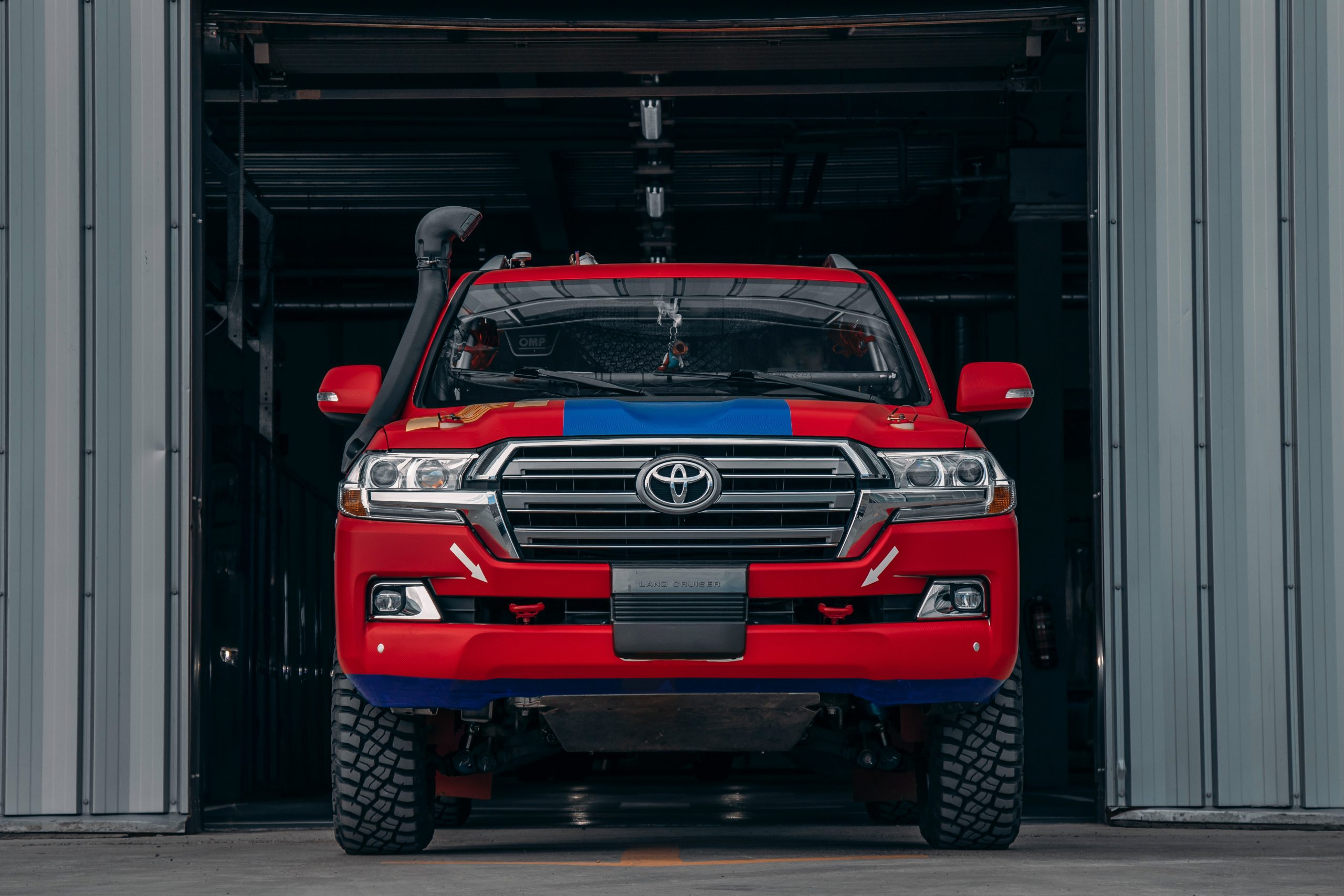
Since the early 1970s, just-in-time manufacturing has been applied in production across the globe, but it originated from Japanese businesses. JIT is said to have been developed and perfected within Toyota’s car-making plants by Taiichi Ohno, as Toyota was on the hunt for new methods to help them meet customer demands without delays.
As Taiichi Ohno and Japanese manufacturers proved that the JIT philosophy could work, it was adopted in other countries. Especially after the 1973 oil embargo, which led to shortened fossil resources across the globe.
Toyota’s case study was backed by examples from Japanese shipyards, which used JIT to reduce inventory levels. Other companies saw how Toyota and Japanese shipyards, partially due to JIT manufacturing, survived the oil crisis. Both Toyota and the shipyards managed to figure out a way to engage with every employee during the crisis and streamline their manufacturing processes for maximum output. Toyota’s production evolved from a curious test into an exemplary success case in only a few years.
Three ways to describe JIT manufacturing
Commonly known as a philosophy originating from Toyota production, just-in-time production is sometimes also described as an environment and control technique.
Now, you might be asking yourself: “How can a manufacturing practice be an environment, philosophy, and technique?”
Let’s dissect the question into three puzzle pieces.
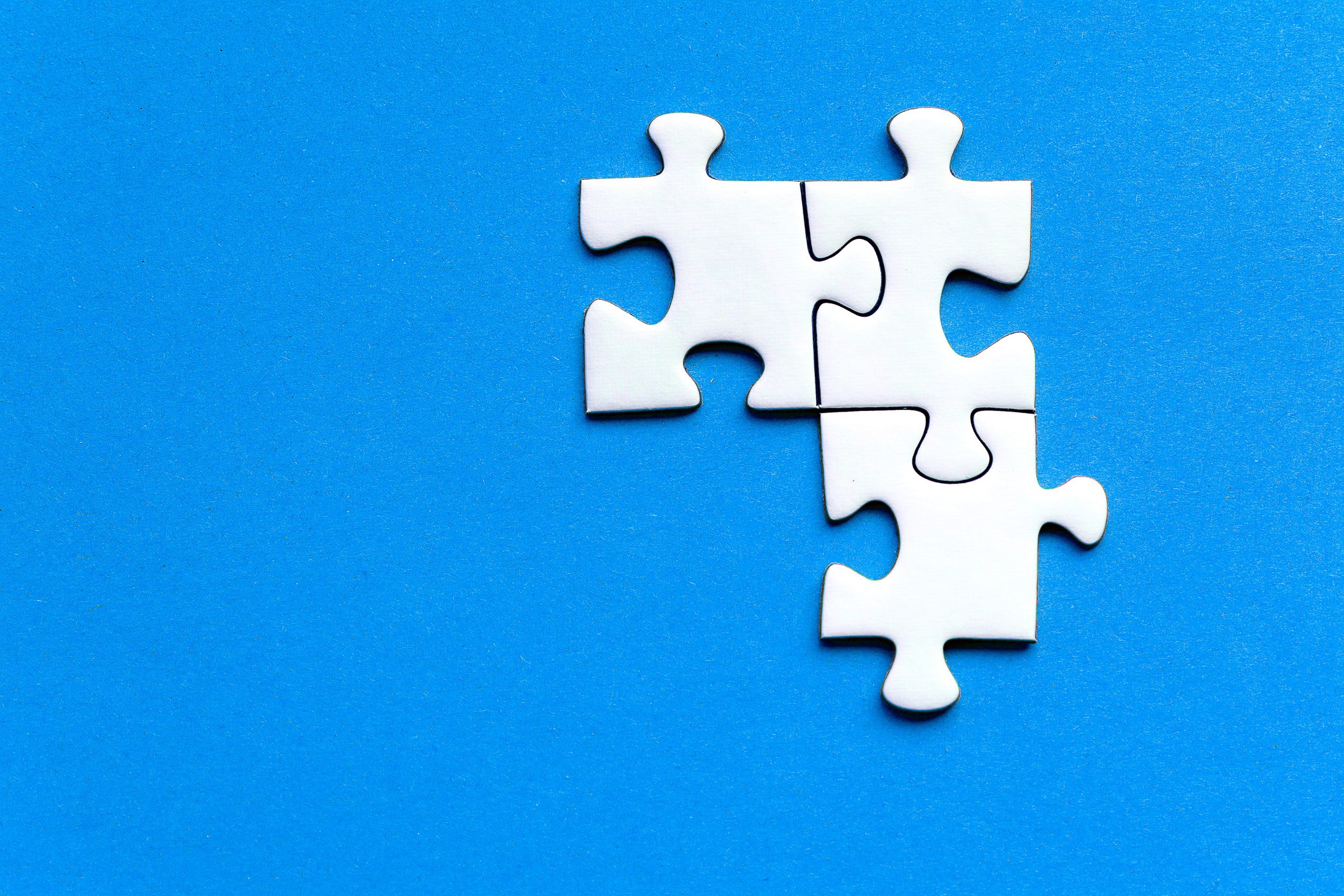
Just-in-time manufacturing — a philosophy
JIT philosophy initially focused on the production of goods to meet exact customer demands rather than making and storing them in advance. In this scenario, the customer could mean the final buyer of the product or the next manufacturing process along the production line. Currently, JIT manufacturing is commonly interpreted as production or manufacturing with minimal waste — including time, resources, and materials.
Just-in-time manufacturing — an environment
A JIT environment is established by the previously mentioned philosophy since JIT mandates that you manufacture products efficiently and keep an eye on every production process. Some key elements in this environment are repetitive manufacturing, total quality management, employee engagement, and healthy supplier partnerships.
Just-in-time manufacturing — a control technique
Employees are equipped with just-in-time control methods in their daily operations if JIT manufacturing is implemented at their company. The characteristics of JIT control techniques include:
- A pull system
- Repetitive processes
- Uniform loading
- Production card usage
- A synchronized production center
Get total inventory control
Thousands of manufacturers use Katana to get a live look at their material and product stock levels, set up reorder points, and automate production planning.
How does JIT manufacturing work?
Just-in-time manufacturing embodies a demand-pull system instead of the traditional “push” system. Every manufacturing operation produces only what is required to satisfy the demand of the following processes. Components and raw materials arrive in the manufacturing plant on time and are effectively used in production.
Here’s a neat graph to explain JIT manufacturing visually.
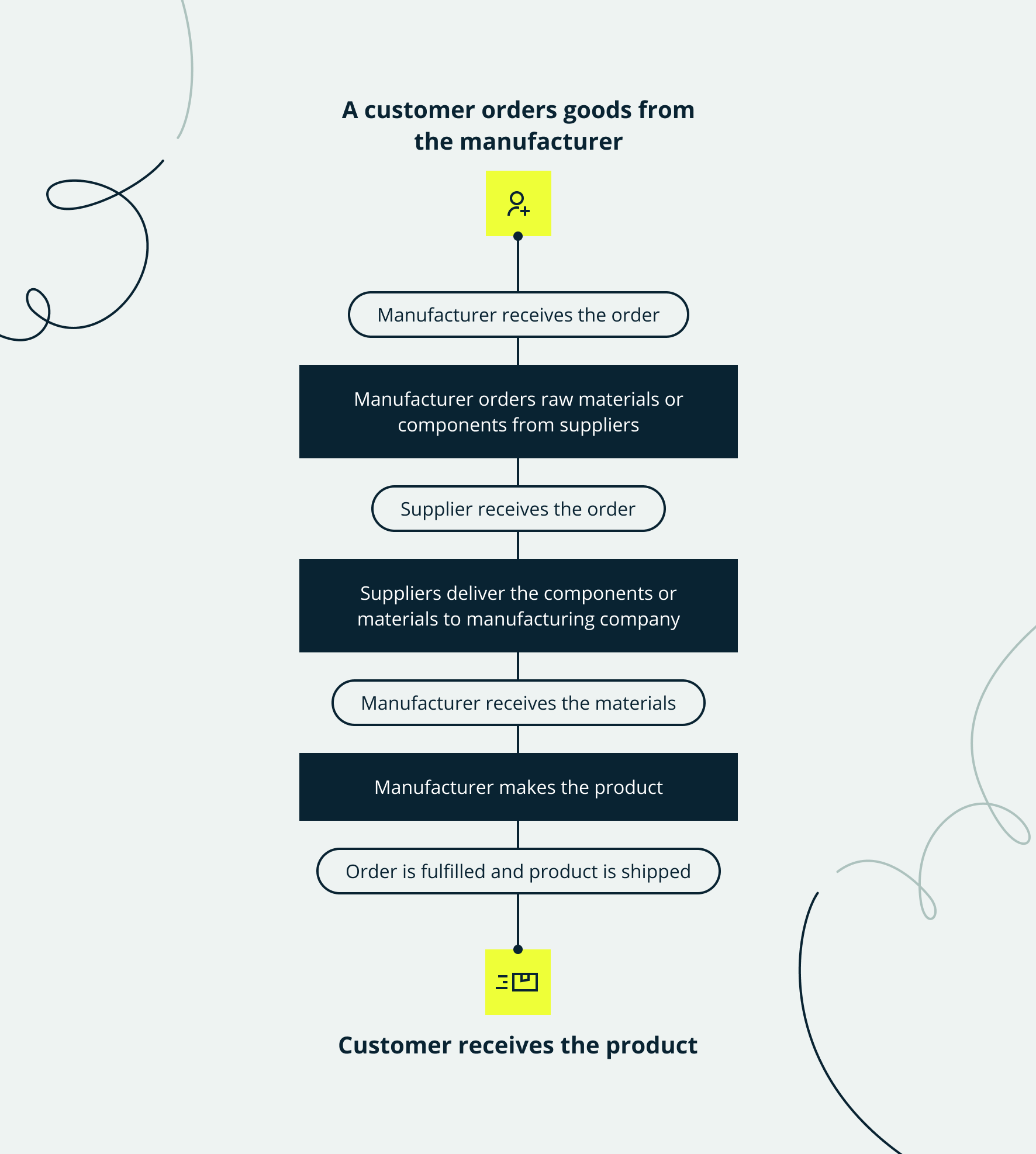
Example of just-in-time production
Subway (the sandwich maker, not the NY Metro) is a great real-life example of how a pull-based system works in a different type of industry.
What happens at a Subway when a client orders a cheese sandwich?
The sandwich maker fetches the bread and starts to make you a cheese sandwich. The shift manager keeps an eye on the ingredients for making sandwiches and orders more cheese or tomatoes when they see the inventory levels dropping too low. The customer’s purchase is a trigger for pulling new materials through Subway’s system.
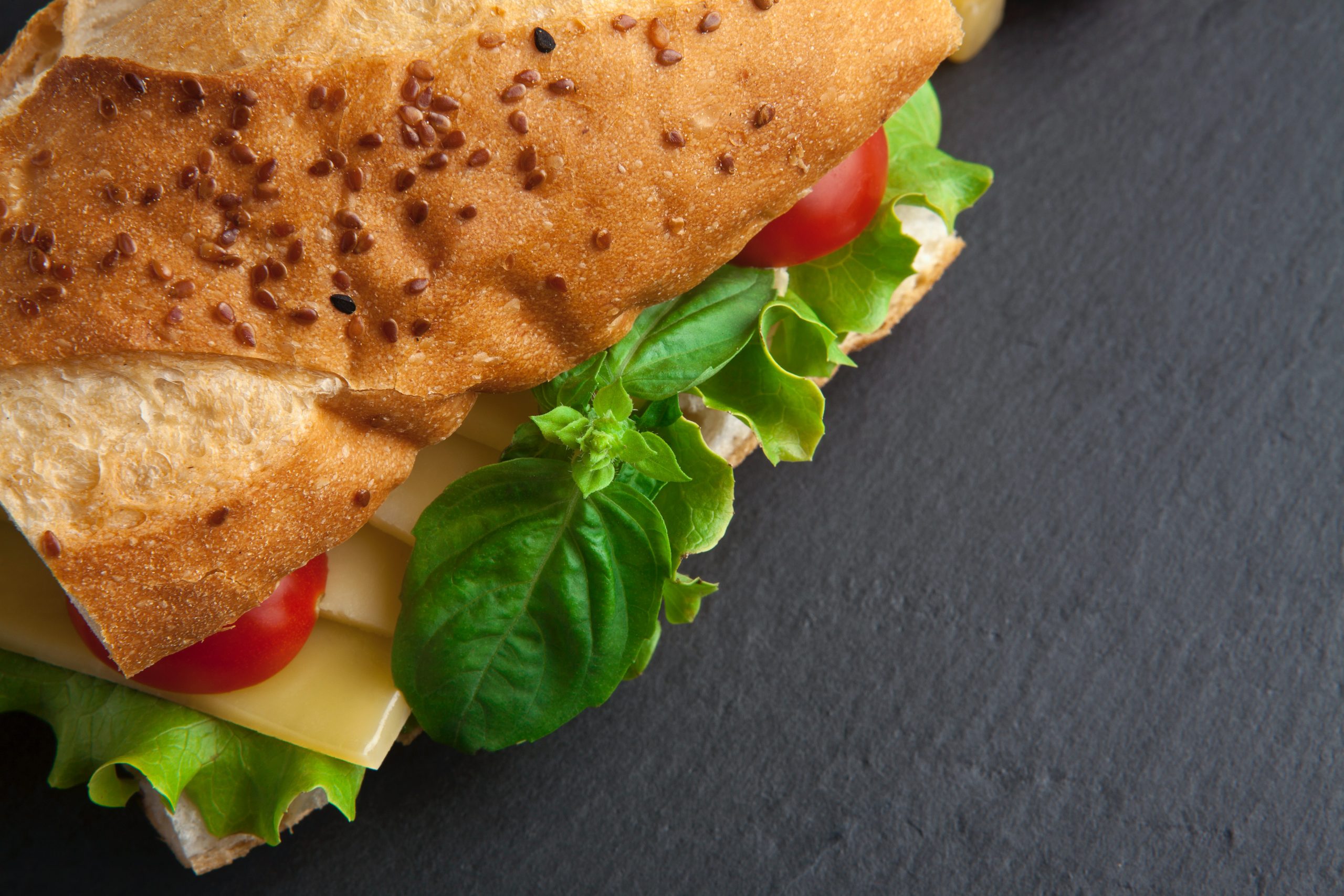
In a push-based system, the shift manager would estimate how many sandwiches they need for any given week or month, using data from past sales and seasonal performance. Then they calculate roughly what type of inventory needs to be ordered in advance.
What is the difference between JIT manufacturing and lean manufacturing?
Just-in-time manufacturing often reminds managers of lean manufacturing, and the terms are sometimes synonymous. However, you should be wary of the nuances that differentiate them.
Lean manufacturing is a production strategy that focuses on reducing waste. Like JIT, lean manufacturing seeks to produce what is needed, when, and in the amount needed.
JIT manufacturing is almost like a subset of lean manufacturing. While both strategies seek to reduce waste, JIT focuses specifically on production timing, while lean manufacturing focuses more on addressing all inefficiencies causing waste of resources across your operations.
10 benefits of JIT manufacturing
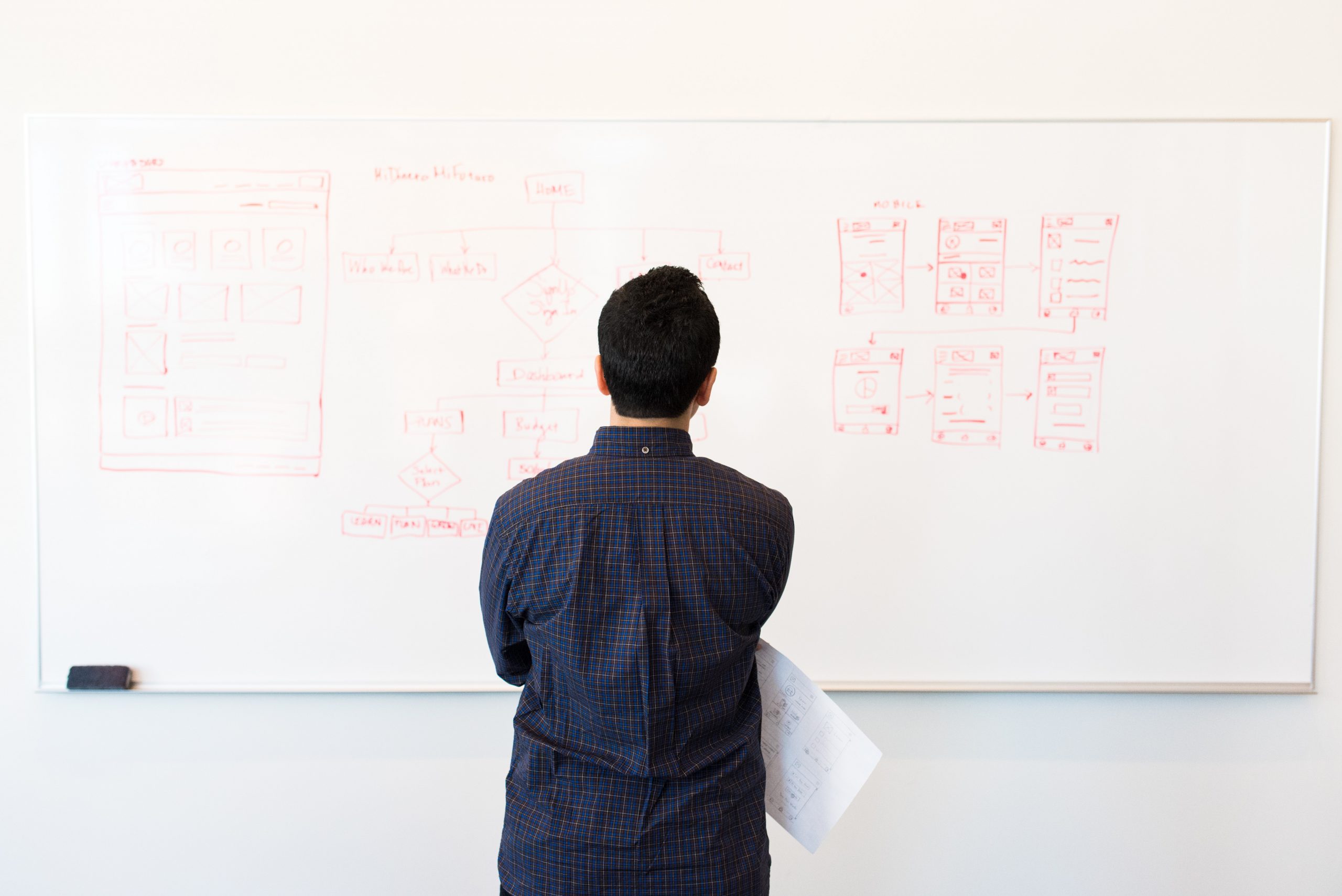
A just-in-time system requires a thorough plan. Managers need to find employees and capable software to analyze the current supply chain and map out the ongoing and future processes from ordering raw materials to product shipment.
This new master production schedule diminishes the chance of starting off on the wrong foot. The plan ensures that you can reliably monitor the new effects of the JIT inventory management system.
Here are ten both common and proven benefits experienced by thousands of JIT manufacturers.
- Fast-forwarded production — JIT manufacturing can reduce throughput time, which is beneficial for satisfying the needs of customers who demand a shorter delivery time
- Increased productivity — JIT manufacturers are always on the hunt to optimize processes, leading to higher productivity
- Diminished rates of defects — Eliminating issues is always a sound strategy to build customer success and avoid bad reviews
- Scaling down WIP processes and products — The fewer “ongoing” processes you have, the clearer your production overview generally becomes
- Cutting labor costs — Which manufacturer doesn’t like saving money?
- Less space for operations — Because of ordering materials only once the customer places an order, your product is already sold before it’s finished, and you don’t have to store your JIT inventory
- Better product quality — JIT systems often include extra quality control measures to make sure that the final product is up to par
- Reduced waste — Less time spent on unwanted products means that you can avoid wasting materials, money, and hours
- More control in manufacturing — Having a JIT inventory management system enables manufacturers to keep a closer eye on things and spot potential issues before they become actual problems
- Local material sourcing — JIT philosophy favors sourcing local raw materials that couriers can deliver to your factory sooner. This leads to reduced transportation costs and time, improving local employment rates
Software for JIT manufacturing
Manufacturing software reduces costs and improves the way you manage your business. Here’s how it works.
What are the potential pitfalls of using JIT manufacturing?
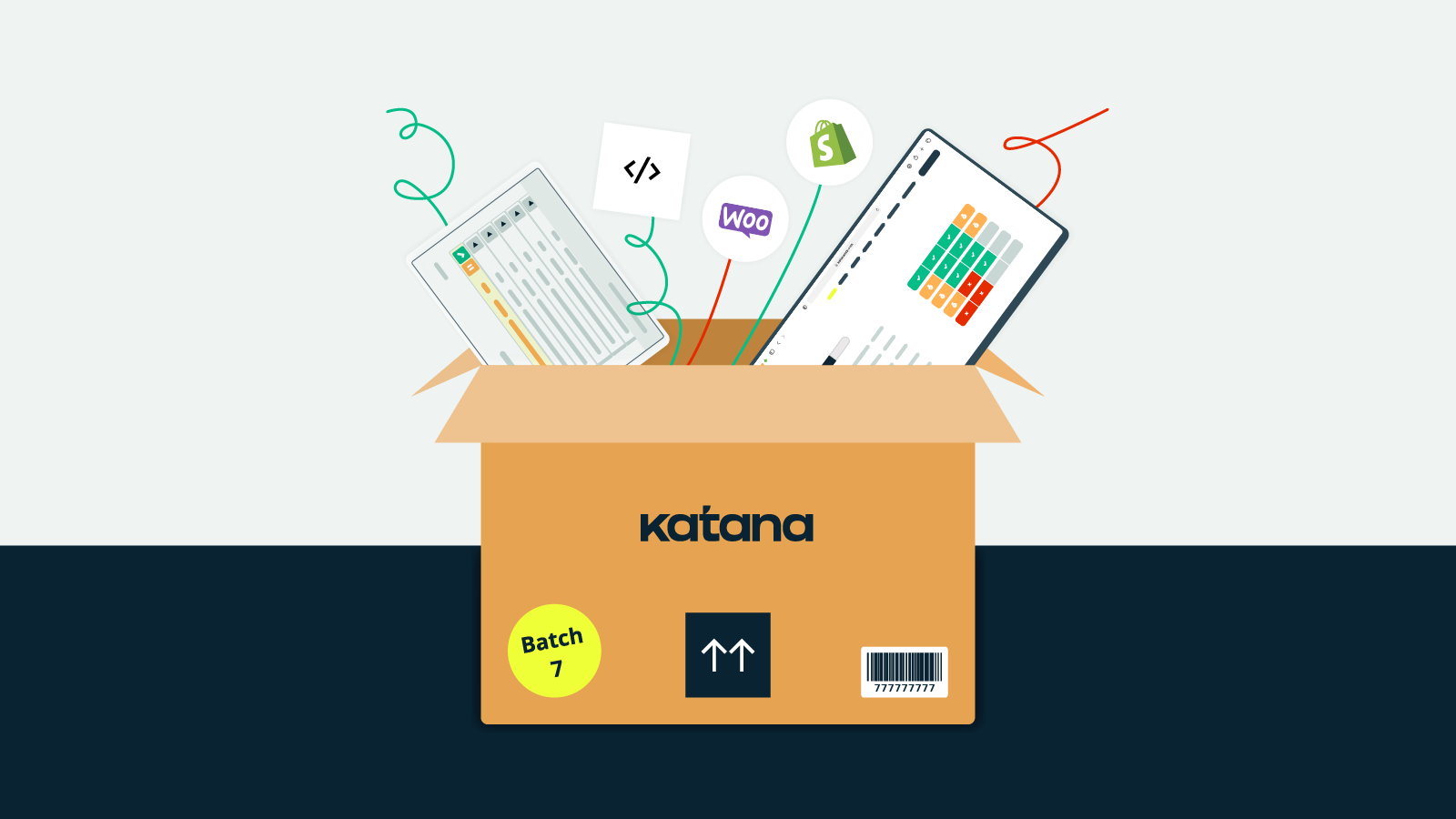
The biggest challenge by far is logistical and economic disruptions that a business has minimal control over. If a disastrous global event occurs, it can impact a just-in-time manufacturing business more since there is no excess inventory to fall back on. When that happens, sales dry up like grass during a drought.
JIT production could make you very dependent on your suppliers’ performance. If a supplier increases their prices suddenly, it affects your expenses and also causes new issues as you scramble to find a better deal while inventory levels dwindle. If the price surges too high, you risk not making a profit.
JIT manufacturers also find it challenging to rework orders due to low inventory and dependency on original orders. Related to reworking orders is the relative complexity of tracking all processes.
This is where material resource planning software or enterprise resource planning (ERP) software comes into play.
Katana Cloud Inventory acts as an ERP software intended to boost efficiency and empower your teams with tracking features to give you total visibility and control over production. It can help you in developing a production system that respects the values of JIT inventory management.
You can use Katana production management software to streamline all your production processes and use live data for real-time planning. Katana is a flexible solution for JIT manufacturers as you can integrate it with multiple accounting, e-commerce, reporting, and CRM tools while also benefiting from essential business tools like order management.
If you’re interested in learning more about Katana, sign up for a free demo with one of our experts to get a guided tour of the platform and find out how it can improve your manufacturing.
Until then, check out this interactive tour about Katana’s manufacturing features and get a taste of what we offer.
Table of contents
Manufacturing guide
More on manufacturing
Get visibility over your sales and stock
Wave goodbye to uncertainty by using Katana Cloud Inventory for total inventory control
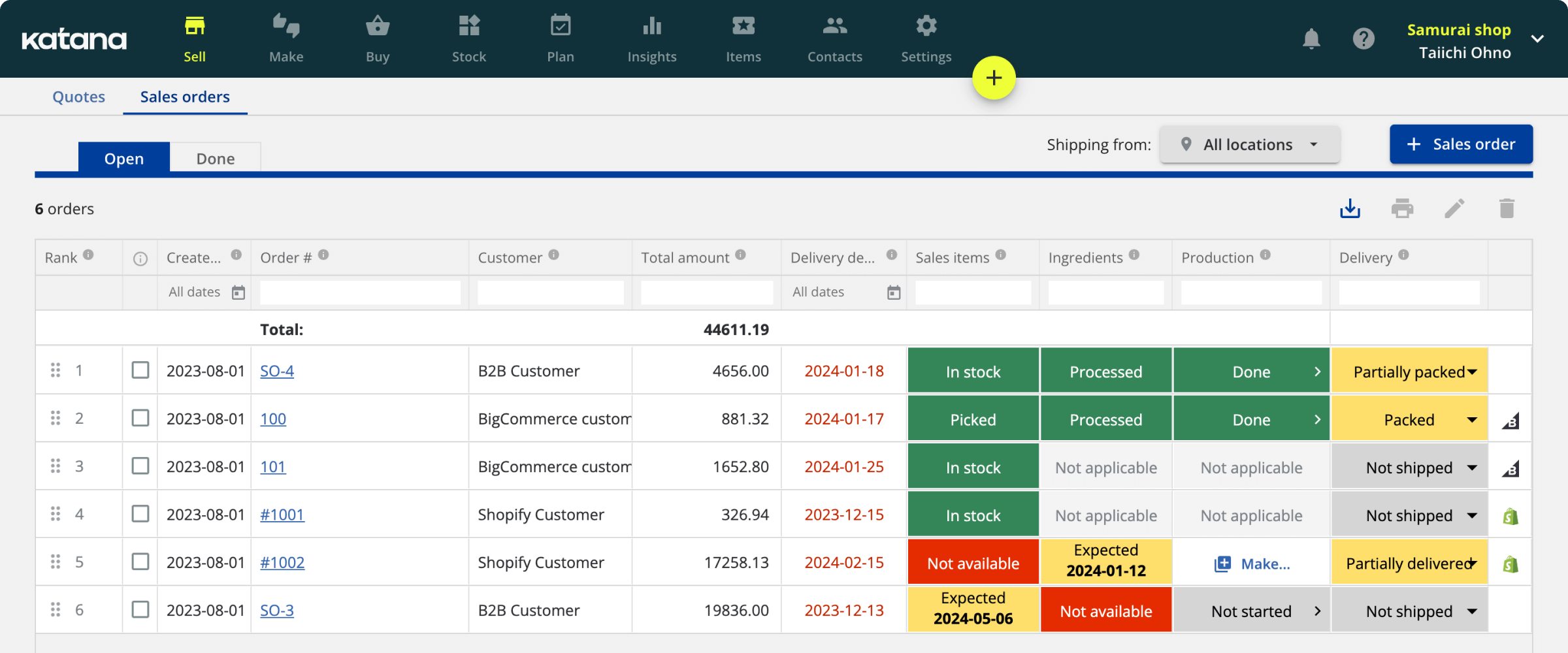