Supply chain for manufacturing: From raw materials to finished products
The manufacturing supply chain is like a well-choreographed dance, with each step contributing to the success of the final performance. It is the cornerstone of many industries, ensuring products are efficiently produced, transported, and delivered to consumers worldwide.
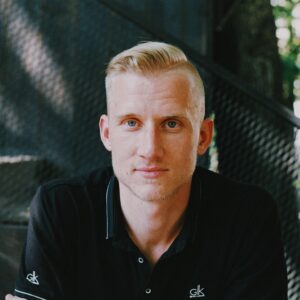
Henry Kivimaa
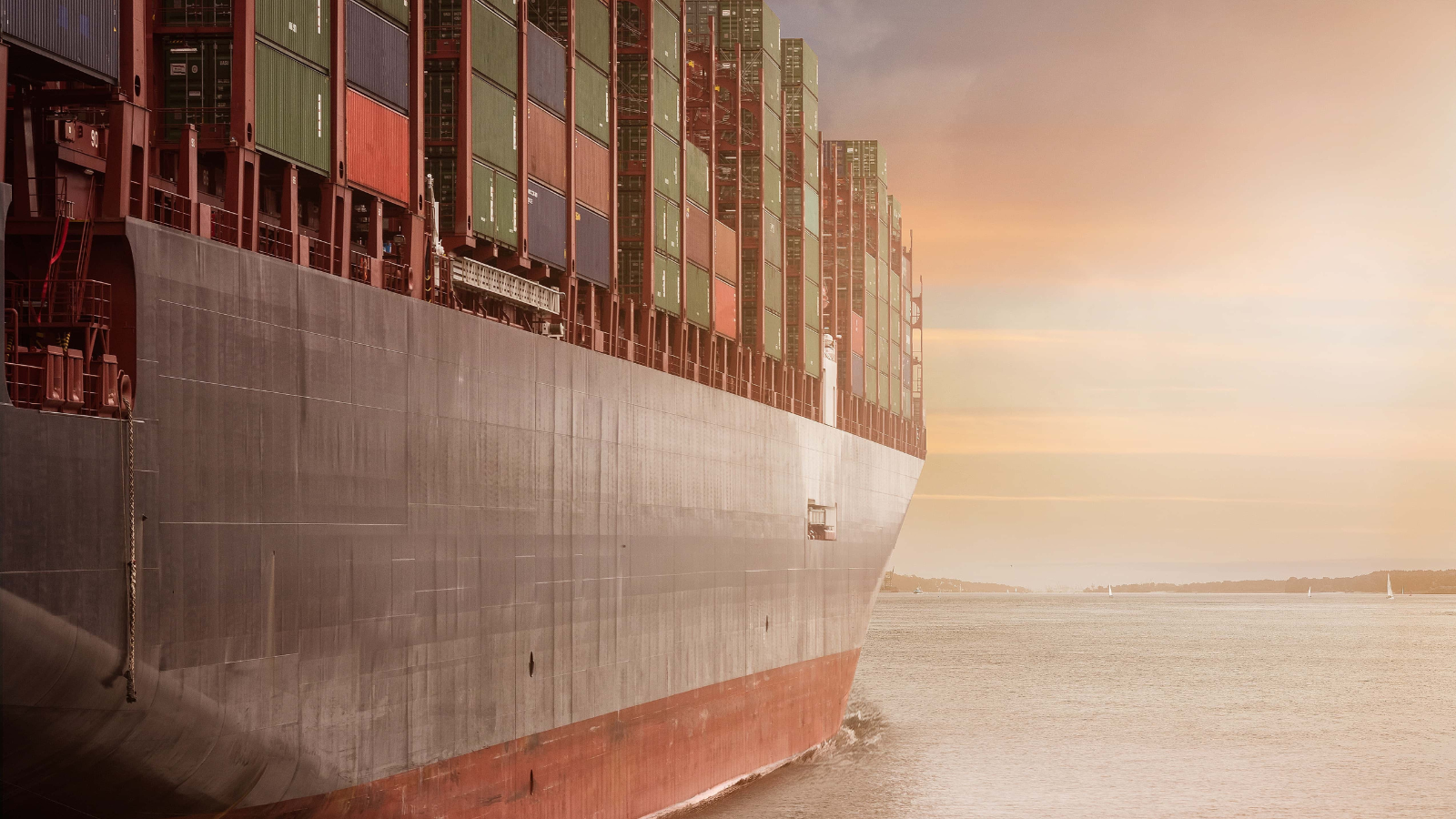
The supply chain is the backbone of the manufacturing world.
It’s like a giant game of “telephone,” but instead of whispering, it’s passing along goods and services to get our beloved products into the hands of the customer as quickly and efficiently as possible. With some planning and a lot of coffee, we can conquer any supply chain challenge that comes our way.
How does the supply chain affect manufacturing?
The manufacturer supply chain plays a crucial role in the production process, encompassing all the steps in getting raw materials to the final product. The efficiency and effectiveness of the supply chain can significantly impact the quality, cost, and timeliness of the manufacturing process.
But although manufacturing supply chain management sounds dull, it doesn’t have to be. There are many interesting and relatable examples. Imagine a burger delivery business — they have to manage their supply chain carefully to ensure having enough buns, sauce, cheese, and other toppings to make burgers and deliver them quickly and reliably. They can’t make the burgers if they run out of any of these ingredients, which will almost definitely result in customers being upset and, even worse — hangry.
Or, imagine a toy manufacturer who needs plastic to make their toys. What sounds like a simple process of molding a doll or a model car is actually a whole series of fortunate events.
- The manufacturer orders plastic from a supplier
- The supplier orders plastic from a chemical plant
- Chemical plants get their raw materials from oil refineries
- Plastic is shipped to the toy factory
- Machines and tools mold plastic into toys
- Finished products are shipped to distributors
- Distributors sell the products to retailers
- Kids and parents can finally go and purchase the goods
If any part of this chain is slow, inefficient, or disrupted, it can cause delays, stockouts, and lost sales. Supply chain management involves coordinating and optimizing all these processes to establish a smooth and efficient flow of products.
What are the steps of a supply chain?
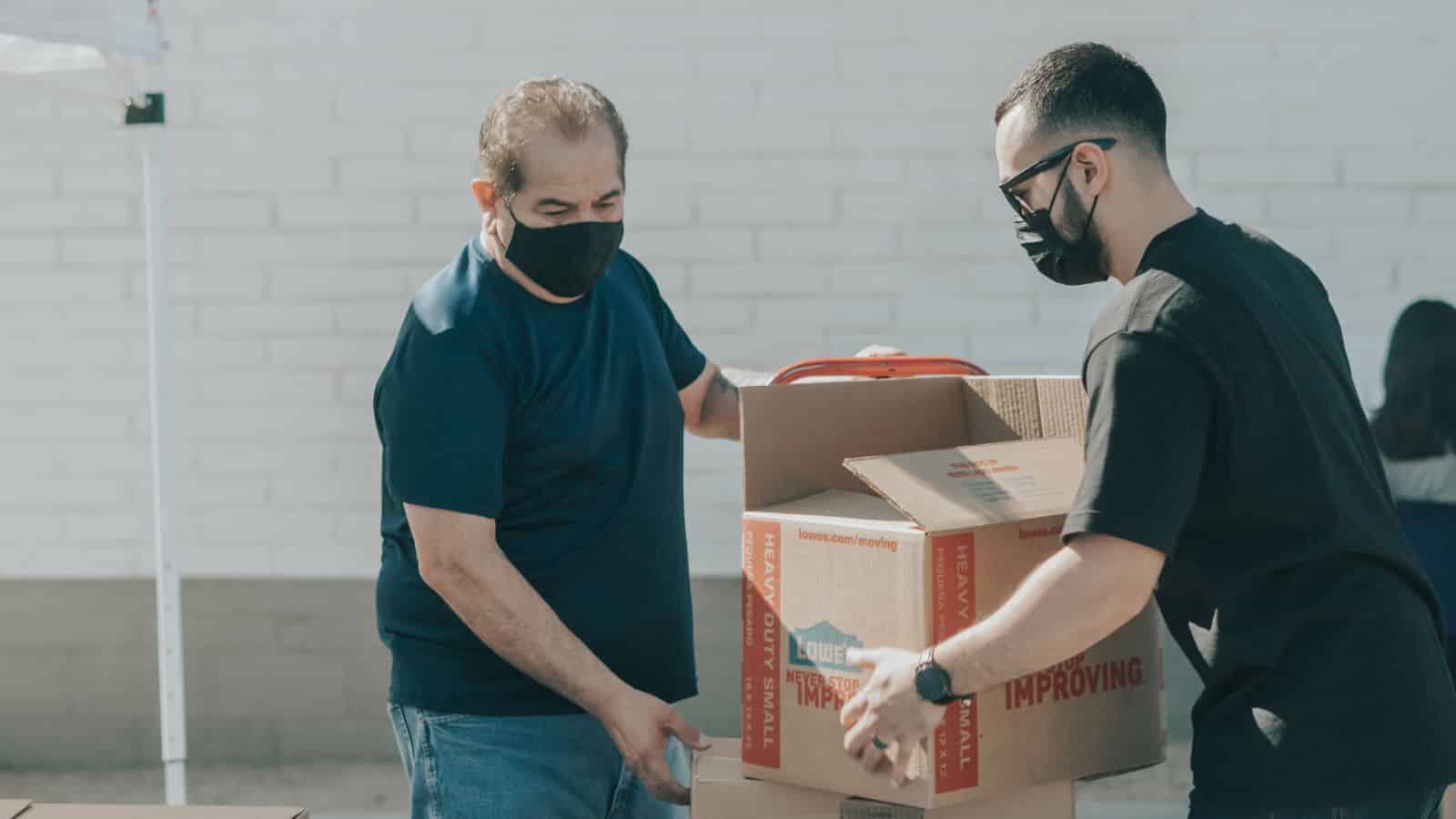
The steps of a typical supply chain for manufacturing may vary depending on the specific industry and product. Effective supply chain management involves coordinating and optimizing these various production phases to reduce costs, increase efficiency, and improve customer satisfaction.
No one-size-fits-all solution exists, but a supply chain in manufacturing commonly includes the following production stages.
Planning
The first stage in the supply chain includes creating a detailed roadmap. It’s where businesses determine what, how much, where, and when to produce. This stage involves forecasting demand, setting manufacturing targets, and developing a production plan.
The planning stage involves the following activities:
- Demand planning — Forecasting customer demand by taking into account historical data, market trends, and other factors. Accurate demand planning is crucial for ensuring the right products are available in the right quantities and at the right time to avoid the bullwhip effect.
- Supply planning — Establishing an inventory plan to meet the forecasted demand. When making supply plans, businesses must consider factors such as lead times, safety stock levels, and manufacturing capacities.
- Production planning — Creating a detailed production plan based on the demand and supply plans. This includes determining the optimal manufacturing levels, scheduling production, and managing inventory levels.
- Distribution planning — Determining the best distribution strategy for getting products to customers efficiently. This also involves selecting suitable transportation modes, creating delivery schedules, and managing inventory levels.
- Capacity planning — Ensuring that the necessary resources, including equipment, labor, and space, are available to meet the forecasted demand and manufacturing plans. Manufacturing capacity planning helps businesses optimize their resources and minimize costs and waste.
Sourcing
Once the production plan is established, the next step is determining and finding the resources needed to manufacture the products. These include necessary raw materials, components, and services. This stage also involves finding suppliers, negotiating contracts, and managing partner relationships.
The sourcing process involves the following steps:
- Supplier identification — Identifying potential suppliers based on the requirements of the business. This can include factors such as price, quality, delivery time, and location.
- Supplier evaluation — Evaluating potential suppliers based on various criteria, such as financial stability, quality certifications, and performance history. Supplier evaluation helps businesses identify the most suitable suppliers for their needs.
- Supplier selection — Choosing the most appropriate suppliers based on the results of the supplier evaluation process. The selection process typically involves negotiations and contract agreements.
- Supplier management — Managing supplier relationships to ensure a reliable and consistent supply of goods and services. This includes monitoring supplier performance, addressing any issues that arise, and maintaining effective communication channels.
Manufacturing
Manufacturing is also a stage of the supply chain. It involves the actual production of goods, including assembly, testing, and packaging. This stage can occur at a single location or across multiple factories, depending on the size and complexity of the production process.
Manufacturing aims to produce high-quality products efficiently and cost-effectively to meet customer demand. Effective manufacturing in the supply chain requires careful planning, efficient execution, and regular improvement.
By adopting best practices, businesses can optimize manufacturing processes and achieve quality, efficiency, and profitability goals. This can lead to higher customer satisfaction, increased profits, and a competitive advantage in the market.
The manufacturing process involves the following steps:
- Design — Creating a design for the product, including specifications for materials, dimensions, and manufacturing processes.
- Production planning — Planning the production process, including selecting the appropriate equipment, scheduling production, and determining the required resources and labor.
- Execution — The actual production of the product, including the use of materials and equipment to transform raw materials into finished products.
- Quality control — This involves following a strict production quality control checklist at various stages of the manufacturing process to ensure that it meets the required standards.
Logistics
Once the products are finished, they need to be transported to the next stage of the supply chain. Logistics involves managing the movement of goods and services from the point of origin to the point of consumption.
The goal of logistics in the supply chain is to ensure that products are delivered to customers efficiently and cost-effectively while meeting their expectations.
The logistics process involves the following activities:
- Transportation — Selecting the appropriate mode of transportation, such as air, sea, rail, or road, for bulk shipping products from one location to another. This also includes planning the best routes and maintaining relationships with delivery partners.
- Warehousing — Storing products in a warehouse or distribution center until they are ready to be shipped to customers. Warehouses have to be well-organized, and the local teams need proper training to manage the stock effectively and safely.
- Inventory management — Managing inventory levels to ensure that products are available when customers need them without holding excess inventory that can tie up capital. Inventory management also means optimizing stock levels, as excess inventory will waste time, money, and space in the warehouse, while understocking means potentially losing buyers and business.
- Order fulfillment — Processing customer orders and delivering products to customers on time and in the proper conditions. It involves several activities, including picking and packing products, preparing them for shipment, and delivering them to customers on time.
- Reverse logistics — Managing the return of products from customers, including handling product recalls, repairs, and recycling. Effective reverse logistics management can improve customer satisfaction and minimize environmental impact.
Distribution
This stage involves managing the storage and delivery of finished products to the end customer. Distribution can include managing inventory levels, coordinating transportation, and delivering products directly to retail stores or customers.
Distribution channels can be direct or indirect. A direct distribution channel involves the manufacturer selling products directly to the end-user or consumer, while an indirect distribution channel involves intermediary parties such as wholesalers and retailers.
To achieve efficient distribution, companies need to carefully plan and manage their supply chain, including inventory levels, transportation routes, and logistics operations. This can help minimize costs, reduce lead times, improve customer satisfaction, and increase profitability.
Retail
In the final stage of the manufacturing supply chain, the products are sold to the customer through various retail channels. These can include traditional shops, online stores, and other sales channels.
Retailers play a crucial role in the supply chain by providing a platform for manufacturers and distributors to reach their target customers. They must balance inventory levels carefully to ensure having enough stock to meet customer demand while minimizing costs and reducing the risk of overstocking. Effective retail management involves various activities such as pricing, promotions, store layout, and customer service.
With the increasing popularity of e-commerce, many retailers now offer online sales channels. E-commerce has made it easier for manufacturers and distributors to reach a wider audience while providing consumers with greater convenience and choice. It has also reduced the costs for sellers at the expense of no longer needing to manage an actual brick-and-mortar store.
A bad chain reaction
Of course, no supply chain is complete without a few surprises along the way. Like that time when a shipment of rubber ducks got lost at sea and ended up washing ashore on beaches all around the world. Or that other time when a truck full of frozen pizzas crashed on the highway, leaving hundreds of pizzas to be cooked in the sun. That’s the beauty of the supply chain — it’s unpredictable and challenging.
How to do supply chain management in manufacturing?
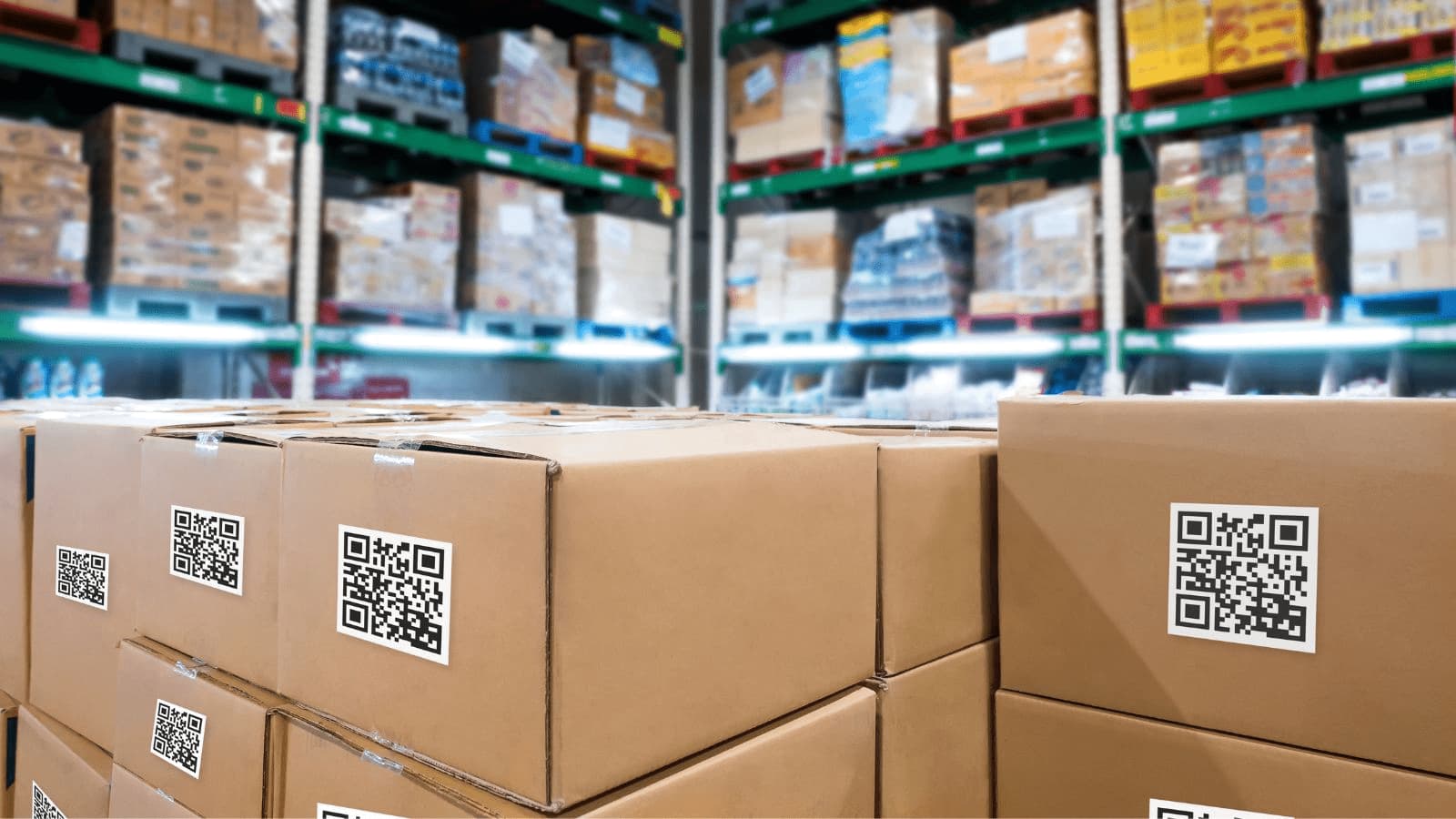
Manufacturing supply chain management (SCM) means handling the entire process of getting raw materials, components, and finished products from suppliers to customers as cost-effectively, efficiently, and fast as possible.
There are several supply chain management techniques that can be used to optimize the flow of goods and services through the supply chain and improve overall efficiency and effectiveness.
Lean manufacturing
Lean manufacturing is an approach that emphasizes minimizing waste, reducing inventory levels, and optimizing production processes. It involves continuous improvements to streamline processes, eliminate activities that add less value, and maximize the use of resources. Some well-known lean manufacturing businesses are Nike and Intel.
Just-in-time
Just-in-time manufacturing is an approach that involves producing goods only when they are needed and in the exact quantities required. This technique aims to minimize inventory levels and reduce the risk of overproduction and waste. The just-in-time method is used by Toyota and McDonald’s.
Agile supply chain management
Agile manufacturing is a flexible, adaptable, and responsive approach. It involves using real-time data and analytics to make quick decisions and respond to changes in customer demand, supply chain disruptions, or other external factors. Apple and Microsoft are known to use the agile approach in their manufacturing.
Vendor-managed inventory
Vendor-managed inventory is a supply management technique that involves the supplier or vendor taking responsibility for managing inventory levels on behalf of the customer. This approach can help to reduce inventory costs, minimize stockouts, and improve supply chain efficiency. Companies that use vendor-managed inventory include Amazon and Walmart.
How can Katana help your supply chain and manufacturing?
Katana is a cloud inventory software for manufacturers to have an overview of all aspects of their business. It offers insights and features to streamline processes and start working more efficiently. Here are some ways Katana will enhance your manufacturing.
Inventory management
Get real-time updates on your stock — from raw materials to finished goods. Get a detailed overview of your inventory across multiple locations and set up reorder points to be reminded to refill the shelves and avoid stock-out.
Production scheduling
Create tasks for your shop-level operators and reprioritize them based on demand, stock levels, and business decisions. Operators can access their assignments in Katana’s Shop Floor App via any smart device and, by completing a task, change the operations and inventory status in Katana as well.
Insights
Katana offers live data on production, order, sales, and customers. Insights are helpful in manufacturing analysis and making more data-driven business decisions. Track performance, monitor sales, and plan future demand — all in one place.
Integrations
Katana’s open API lets you connect to other software to enhance your manufacturing experience. Or choose from existing integrations to optimize your bookkeeping, sales, and other business areas.
So, there you have it.
The supply chain is the unsung hero of the manufacturing world, ensuring that your favorite products are made with quality materials and delivered to your doorstep timely and cost-effectively. So the next time you unwrap that shiny new gadget or curl up in a warm blanket, take a moment to appreciate the suppliers, manufacturers, and logistics providers that made it all possible.
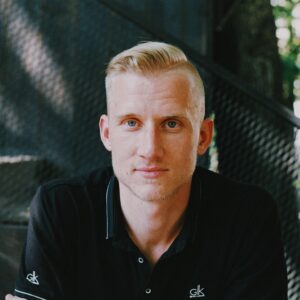
Henry Kivimaa
Table of contents
Get inventory trends, news, and tips every month
Get visibility over your sales and stock
Wave goodbye to uncertainty with Katana Cloud Inventory — AI-powered for total inventory control