OEE in manufacturing: A guide to maximizing efficiency
Think of manufacturing as the backbone of any production business. It’s super important and must be efficient to keep the cash flowing and customers happy. To achieve this, read on to learn how to calculate and improve your OEE in manufacturing.
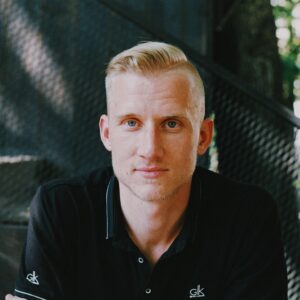
Henry Kivimaa
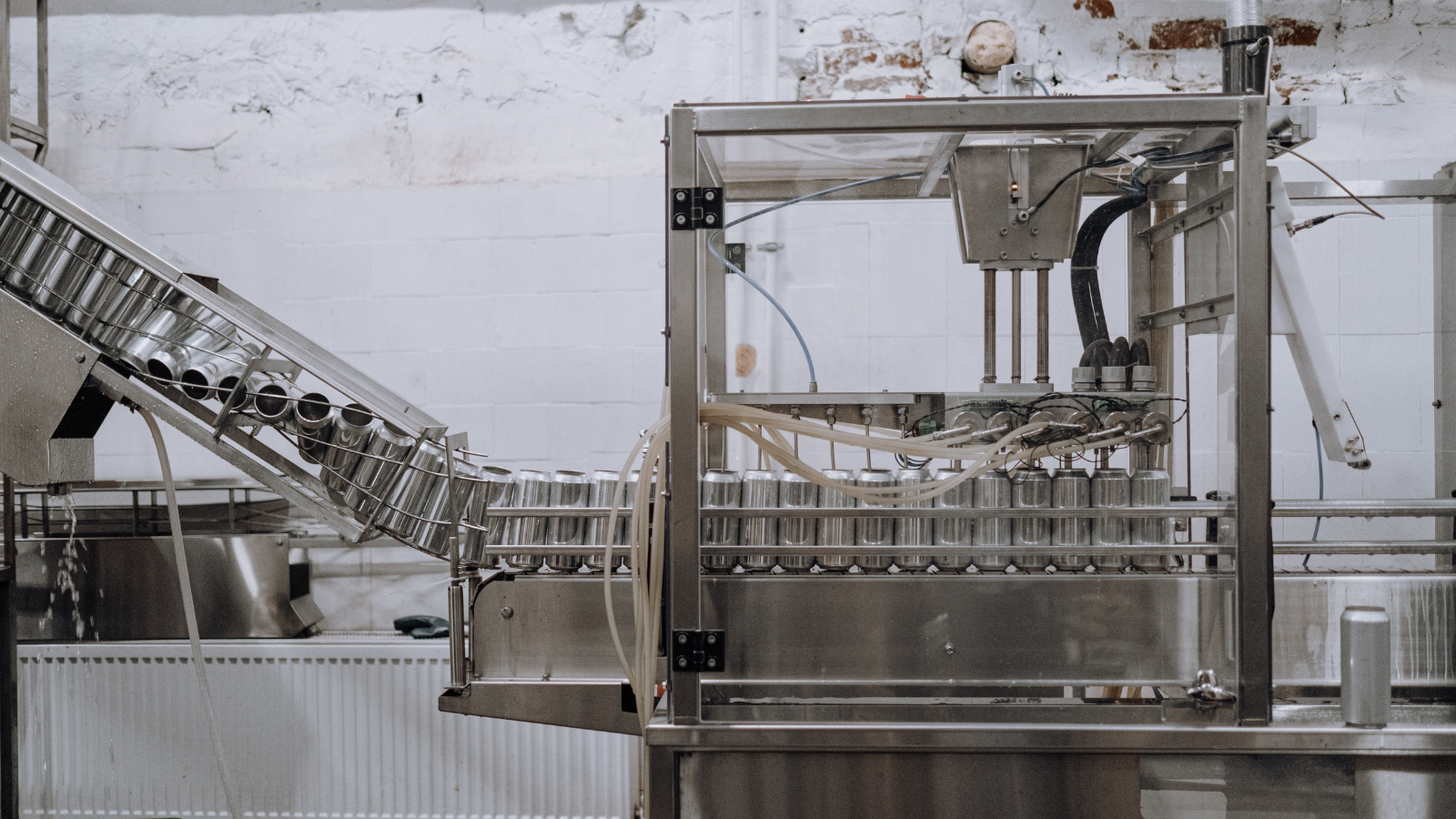
Imagine going to a concert, expecting to have the time of your life, dance your butt off, and sing along until you have no voice. The lights dim, everyone goes quiet, and the band steps out — only to start tuning their instruments because they haven’t done a sound check. The band members are irritated, the manager is on the verge of a nervous breakdown, and the fans want their money back.
Now picture a similar scenario in your factory — the band manager is the production manager, the instruments are the manufacturing equipment, and the fans are your customers. Just like the band needs their instruments to be in order before the show starts, manufacturing equipment and machinery must be ready before production to deliver maximum performance. This is where OEE comes into play.
What is OEE in manufacturing?
Overall equipment effectiveness (OEE) is a performance metric in manufacturing to calculate the productivity and efficiency of a production process. It measures the effectiveness of equipment or manufacturing processes while producing quality products on time.
In traditional manufacturing, the focus is often on maximizing the output of equipment and processes without necessarily considering the quality or efficiency of the final result. In contrast, OEE in lean manufacturing strongly emphasizes quality and efficiency. The goal is to create value for the customer while minimizing manufacturing waste , and OEE is used as a tool to help achieve this goal.
OEE takes into account three factors that contribute to overall productivity:
- Availability — Refers to the amount of time that the equipment or process is available for use.
- Performance — Measures how well the equipment or process is performing compared to its maximum potential output.
- Quality — Refers to the percentage of products that meet the required quality standards.
Breaking down efficiency into these three components allows manufacturers to identify specific areas for improvement.
For example, low availability may indicate frequent breakdowns with the equipment, which ultimately means emotional breakdowns for the team. If performance is low, it may suggest bottlenecks in the production process that need to be addressed. Finally, if the quality is low, this may indicate issues with the raw materials or the production process itself. Manufacturers can take targeted actions to improve efficiency and optimize production by understanding the factors driving low OEE.
How to calculate OEE in manufacturing?
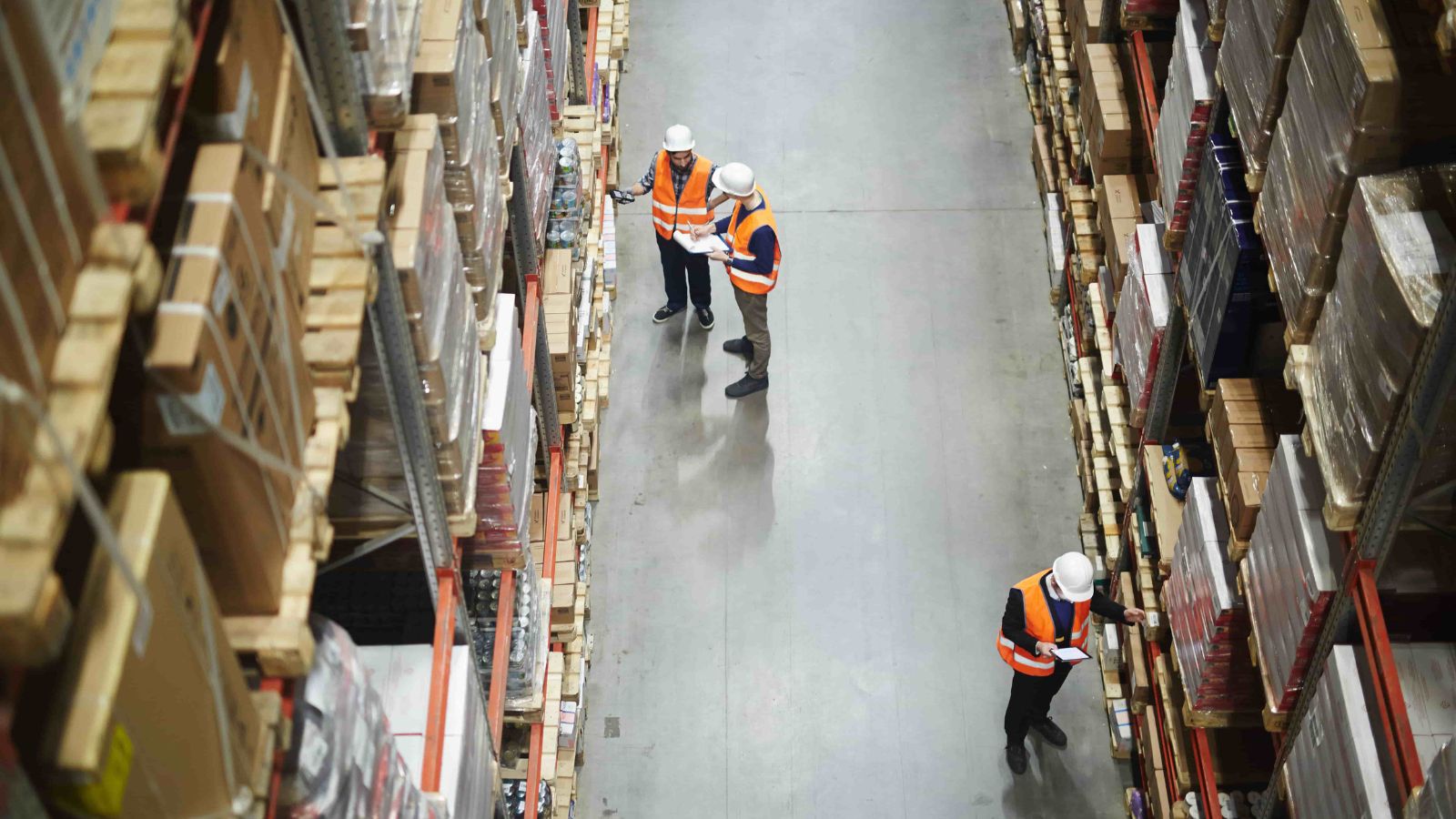
The calculation for OEE is relatively easy if you follow the formula:
OEE = Availability x Performance x Quality
Each factor is represented as a percentage, with 100% representing perfect performance. The goal of measuring OEE is to identify areas where production processes and equipment can be improved to increase productivity and reduce waste.
A high OEE value indicates that the equipment is being used effectively, and there is little waste or downtime in manufacturing , leading to a higher output of quality products. On the other hand, a low OEE value indicates problems with the equipment, processes, or workflow that must be addressed to improve efficiency and productivity.
An ideal OEE value in a manufacturing plant is 100%, and achieving that would be ace. But, 85% is considered the goal to work towards. The all-around average OEE in manufacturing seems to be 60%, with many companies starting their OEE tracking at around 40% and working their way up from there.
How to improve OEE in manufacturing?
Knowing the percentages is one thing. But, how do you start actually optimizing your manufacturing? Here’s how to improve OEE in your business:
- Improving availability — Ensure that equipment is well-maintained and breakdowns are minimized. Have spare parts and maintenance personnel available, and schedule maintenance during periods of low demand.
- Increasing performance — Optimize production processes to reduce cycle times and eliminate bottlenecks. Train your operators on best practices and implement regular maintenance to ensure that machines operate at maximum efficiency.
- Improving quality — Implement quality control measures to reduce defects. Monitor product quality and identify areas for improvement.
- Enhancing equipment and processes — Analyze production data, find ways to optimize manufacturing processes, and enhance tools to reduce reasons for downtime.
Benefits of OEE
As with any data, there are always many benefits to having a specific analysis of your business. The most essential advantages of calculating your OEE include the following:
- Increased productivity — OEE helps identify the root cause of production inefficiencies and allows to target improvements, resulting in increased productivity.
- Improved quality — By measuring and tracking OEE, it is easier to identify and address quality issues in the production process, resulting in improved product quality.
- Reduced downtime — OEE provides insights into downtime and can help reduce it by identifying areas for improvement in processes and equipment.
- Better planning — With a better understanding of manufacturing performance, OEE allows better production planning and scheduling , resulting in improved capacity utilization .
- Improved employee engagement — OEE provides visibility into the performance of the manufacturing process and can help engage employees in continuous improvement efforts.
- Reduced costs — OEE can help reduce manufacturing costs and improve profitability by identifying and addressing inefficiencies and downtime.
How can OEE improve maintenance?
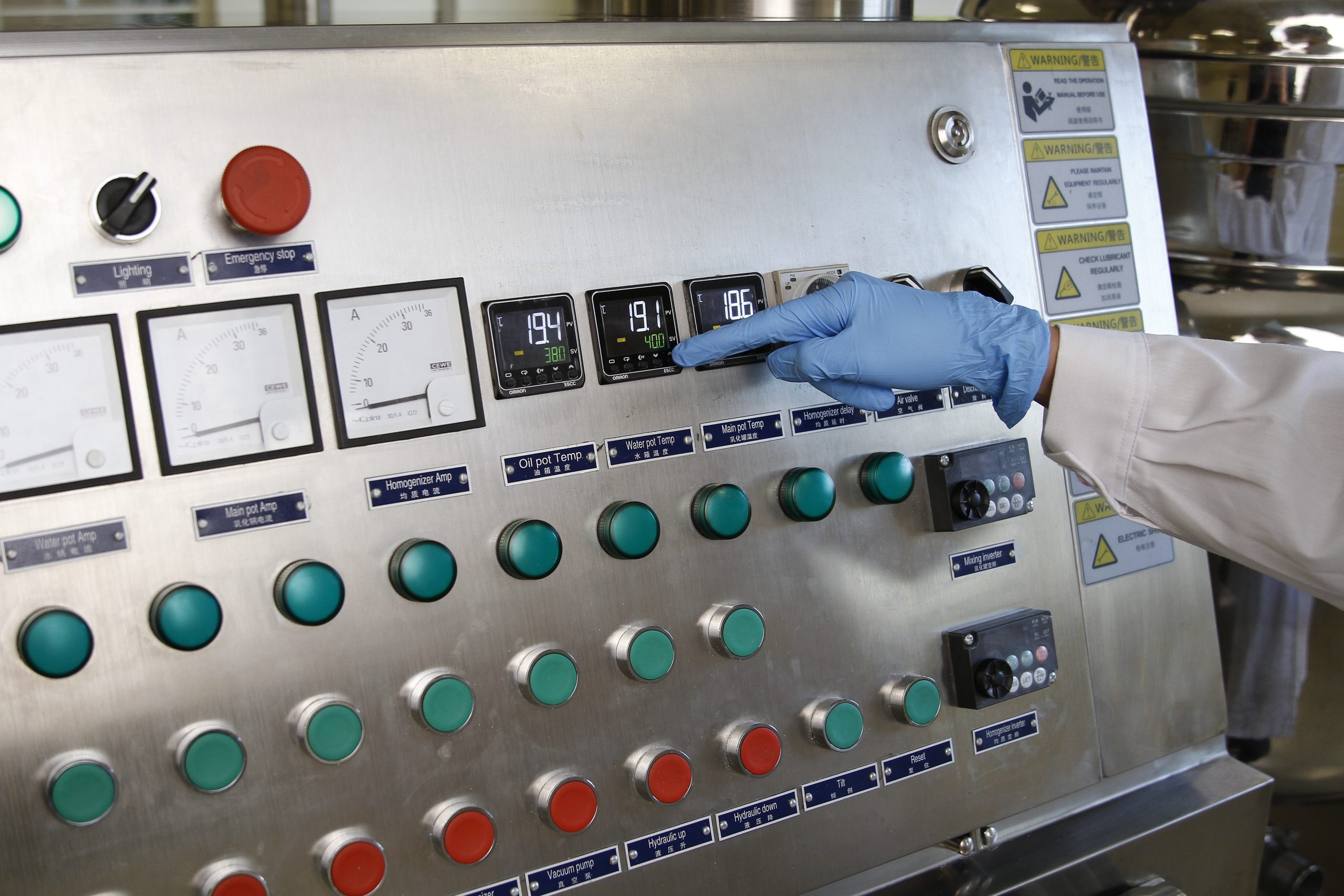
By tracking OEE, manufacturers can identify areas for improvement in their production processes, including maintenance.
Here are a few ways that OEE can help improve maintenance:
- Identify equipment problems — By measuring OEE, manufacturers can quickly identify equipment that’s not performing optimally. This can help maintenance teams prioritize their work and focus on fixing the most critical issues first.
- Reduce downtime — OEE can help maintenance teams understand the root causes of downtime, such as equipment breakdowns and deterioration or insufficient servicing, and develop strategies to reduce them. This can help improve equipment availability and reduce the costs associated with unplanned downtime.
- Optimize preventive maintenance — OEE data can help teams optimize preventive maintenance schedules and better plan their MRO inventory . By tracking equipment performance over time, maintenance teams can determine the best time to perform technical services, such as lubrication or calibration, to minimize the impact on production.
- Improve equipment reliability — By monitoring OEE, manufacturers can identify patterns in equipment performance and use this data to improve equipment reliability. For example, if a particular machine consistently has a low OEE score, maintenance teams can investigate the root cause and implement changes to improve efficiency.
OEE and cloud software
Many businesses use software to monitor, analyze and find ways to increase their OEE. Katana is a cloud platform that can do that for you and much more.
Katana’s goal is to make manufacturing simpler and more efficient, and it offers many features to make monitoring and improving your OEE much easier, including the following.
Inventory management
In Katana, manufacturers can ensure they always have the necessary raw materials, optimize their work-in-progress inventory, and track finished goods. This helps improve availability for production and leads to higher OEE.
Shop Floor App
Katana’s Shop Floor App helps manufacturers improve OEE by providing real-time visibility into their production operations. The app allows operators to track production progress, identify bottlenecks, and monitor performance — all from a smart device.
Production scheduling
Katana’s production scheduling feature allows businesses to optimize manufacturing and improve OEE. It helps users create a visual production schedule, track progress, and adjust real-time actions based on demand planning and resources.
Reporting and analytics
Katana provides real-time visibility of production processes through data, dashboards, and reports. This allows manufacturers to track key performance indicators (KPIs), identify trends, and make data-driven decisions to improve OEE.
Integrations
Katana offers a wide range of integrations to help manufacturers improve OEE. These include accounting software, such as QuickBooks Online and Xero, as well as e-commerce platforms, like Shopify and BigCommerce. Or, if you’re already using a tool you like and need, build it into your custom workflow using Katana’s open API.
So that’s that. Now that you’re an expert in OEE, it’s time to put all this wisdom to good use and start boosting those numbers to win the efficiency game.
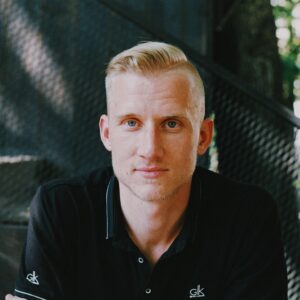
Henry Kivimaa
Table of contents
Get inventory trends, news, and tips every month
Get visibility over your sales and stock
Wave goodbye to uncertainty by using Katana Cloud Inventory for total inventory control
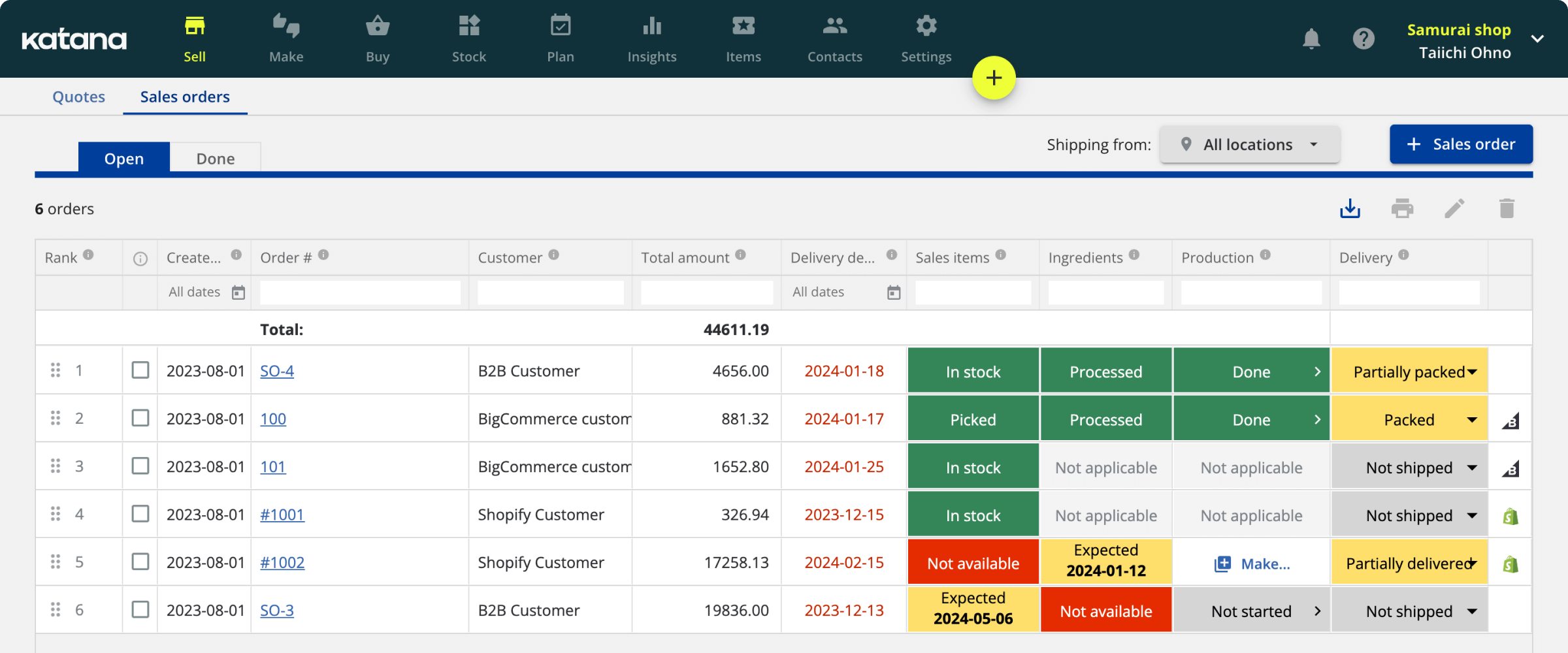