Digital transformation in manufacturing: entering a new era
Wise managers and business owners are digitalizing their businesses to maintain a competitive edge. In this article, learn all about digital transformation in manufacturing to take your business to the next level.
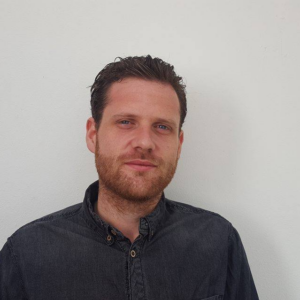
James Humphreys
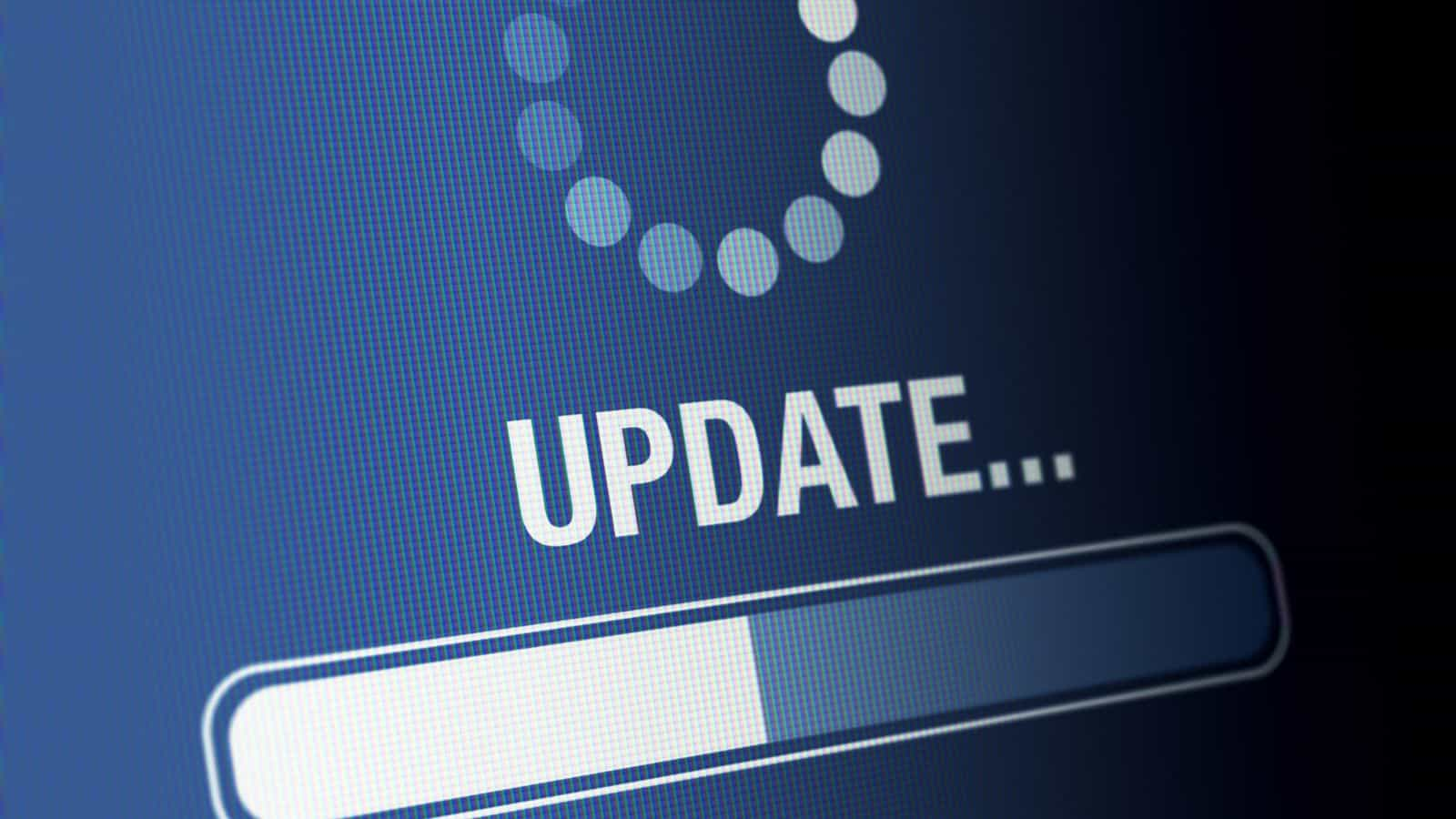
Software, robots, AI, gadgets, and gizmos.
The latest insights into manufacturing trends show that businesses are quickly transitioning from ye olden ways of doing things to using sleek, state-of-the-art technologies that can help them manage their business. And it’s the direction the entire world is going — inside and outside of business. Most people can go into their kitchens right now and play chess with their refrigerator.
Regardless of whether this rush to use advanced technologies will lead us to a situation like the movie “The Terminator.” if your business doesn’t jump on the bandwagon, it will soon be left behind by others taking advantage of the tools available to them.
That’s why we’ve put together this article on digital transformation in manufacturing to help you understand what it is and how you can implement it into your business processes.
What is digital transformation in manufacturing industry?
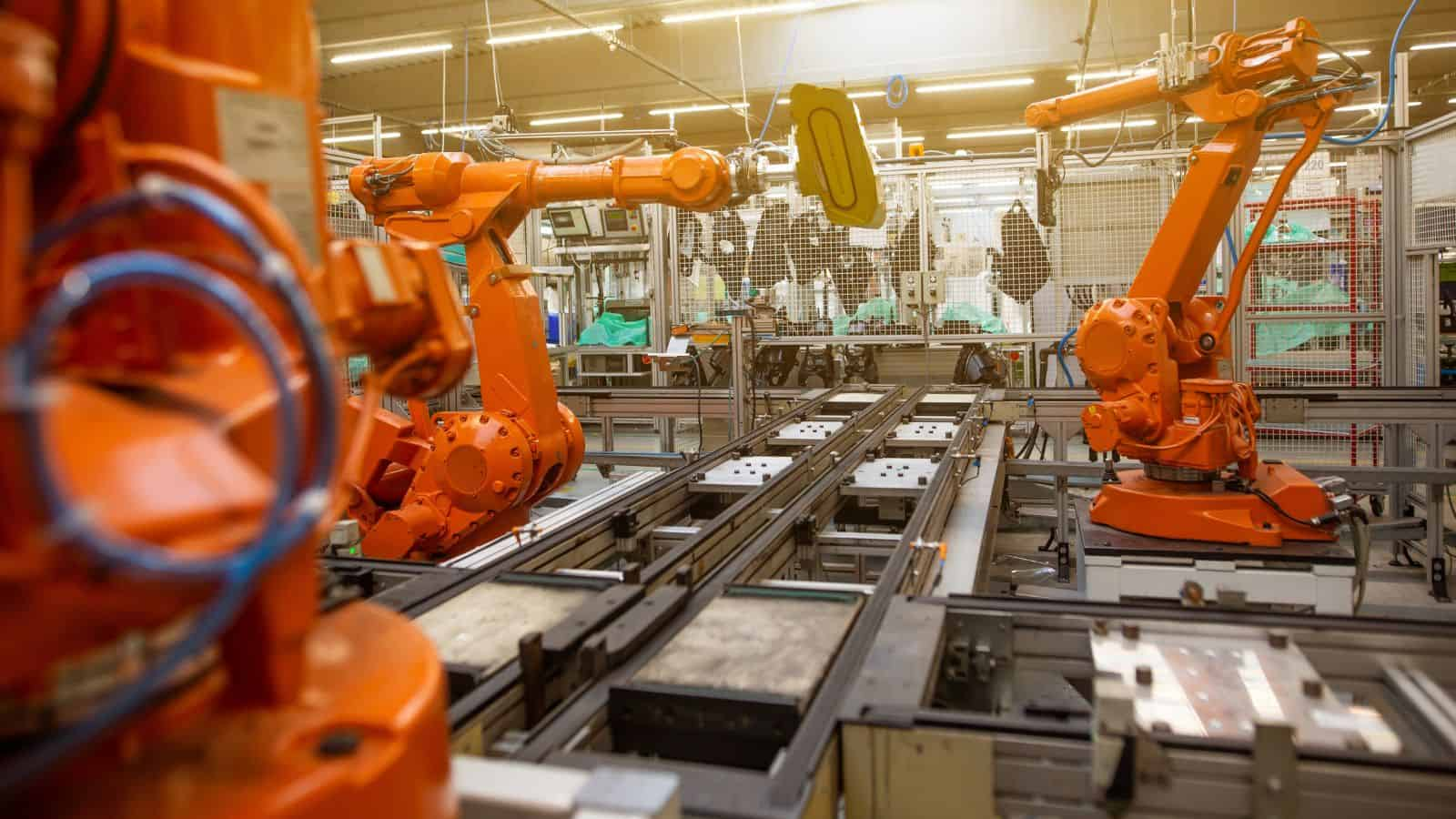
Digital transformation in manufacturing refers to integrating digital technologies, processes, and data throughout the entire manufacturing value chain to:
- Optimize business operations
- Increase efficiency
- Improve customer satisfaction
They accomplish this through automating production processes, gathering and analyzing data, and facilitating speedy decision-making — utilizing tools like the Internet of Things (IoT), artificial intelligence (AI), robotics, and cloud computing. This helps manufacturers improve their production processes, reduce costs, and increase their competitiveness in the market.
Digital transformation in the manufacturing industry is about leveraging technology to create a more efficient and customer-centric manufacturing environment, enabling companies to stay competitive and adapt to the changing business landscape.
Download the manufacturing e-book for manufacturers
Learn how to organize and scale your manufacturing.
How digital transformation in manufacturing gives businesses an advantage
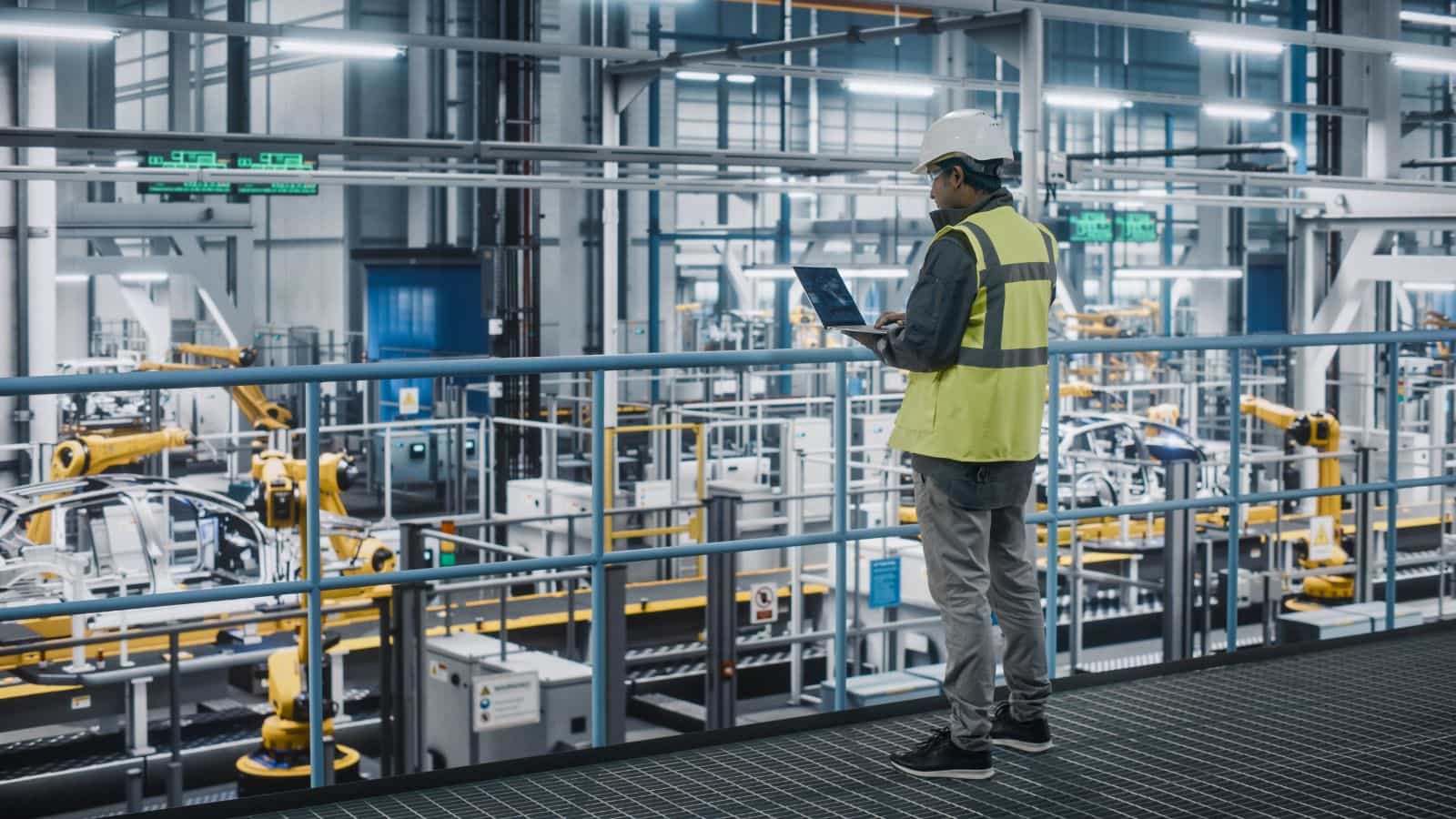
Digital transformation in manufacturing helps companies optimize their operations, improve quality, increase efficiency, and create new business models by leveraging digital technologies and data.
Here are a few reasons why digital transformation is essential for manufacturing companies looking for an advantage.
Improved efficiency
Manufacturers can automate repetitive tasks, reduce errors, and increase productivity by digitizing processes and operations.
Digital technologies like IoT sensors and automation can help reduce the time required for product development, testing, and delivery.
Manufacturers can effortlessly optimize workflows and improve communication between departments by leveraging digital technologies. Here are some reasons why improving efficiency digitally is important in manufacturing:
- Faster time-to-market
- Improved quality
- Increased productivity
Better customer experience
Digital transformation can help manufacturers gain insights into customer behavior and preferences, enabling them to create personalized products and services. This can result in improved customer satisfaction and loyalty.
Manufacturers must focus on meeting the needs of their customers and delivering exceptional customer experiences to stand out from their competitors. A better customer experience is vital in manufacturing for the following reasons:
- Increased customer satisfaction
- Increased revenue
- Improved brand reputation
Increased innovation
By using digital technologies such as AI, machine learning, and big data analytics, manufacturers can gain new insights into their operations, identify areas for improvement, and develop new products and services.
By leveraging digital technologies and data, manufacturers can gain new insights into their operations, identify areas for improvement, and develop new products and services. Increased innovation in manufacturing is critical for the following reasons:
- New revenue streams
- Competitive advantage
- Sustainability
Competitive advantage
Firms that adopt digital transformation are better equipped to maintain their competitiveness in a market that is changing quickly. Businesses risk slipping behind their rivals if they don’t adopt new technologies and procedures.
In a highly competitive market, manufacturers must continually seek ways to stay ahead of their competitors by improving their products, services, and processes. In manufacturing, competitive advantage is significant for the following reasons:
- Increased market share
- Improved profitability
- Ability to weather market changes
The 4 main areas of digital transformation
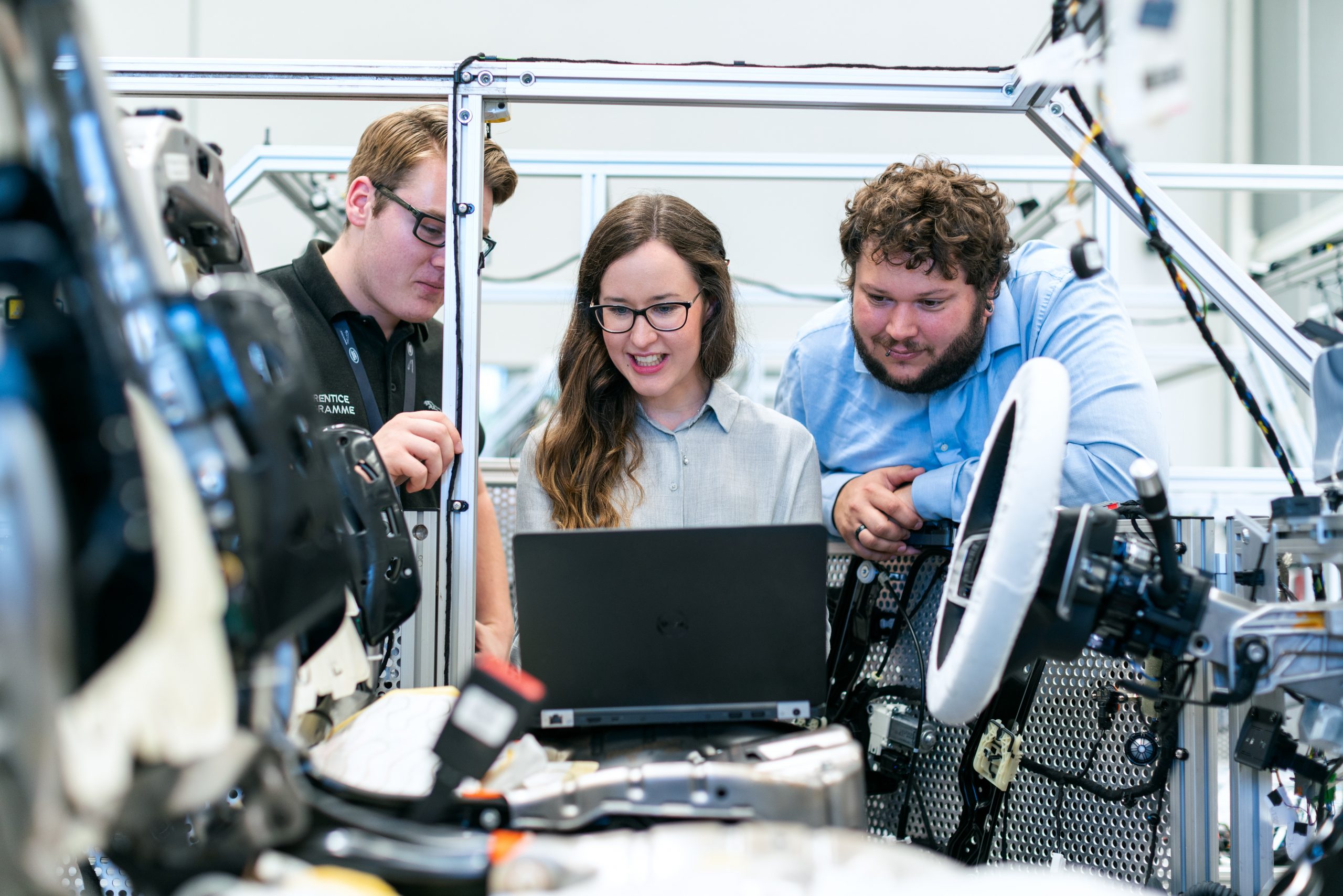
Now you know what digitization in manufacturing is and about the huge advantages of adopting it into your business — the next step is deciding what to transform.
There are many ways you can go about digitally transforming your business. However, there are some areas that other manufacturers tend to favor when making this transition. Here are the four main areas you can focus on to get you started.
1. Process transformation
This involves digitizing and automating existing processes, making them more efficient and streamlined. This includes using digital tools and technologies to optimize processes and reduce costs, such as implementing robotic process automation (RPA), workflow automation, and data analytics.
Here’s a plan you can follow in the process transformation journey:
- Identify areas for improvement — The first step in process transformation is to identify business areas that can be improved through digitization and automation. This can include production, supply chain management, and customer service.
- Define digital goals — Once areas for improvement have been identified, it’s important to define specific digital goals for each area. For example, a goal for production might be to reduce downtime by implementing predictive maintenance using IoT sensors.
- Evaluate current processes — To identify opportunities for improvement, it’s important to evaluate current processes and workflows. This can include mapping out existing processes and identifying areas of inefficiency and waste.
- Select digital tools and technologies — Based on the digital goals and process evaluation, select the digital tools and technologies that will most effectively achieve the desired improvements. This includes tools like RPA, workflow automation software, and data analytics platforms.
- Implement digital solutions — With the digital tools and technologies selected, it’s time to implement them into your manufacturing processes. This may involve integrating the new digital solutions with existing systems and processes.
- Monitor and analyze performance — To ensure that the digital solutions are meeting the desired goals and achieving the expected results, it’s important to monitor and analyze their performance. This can include setting up key performance indicators (KPIs) and analyzing data to identify areas for further improvement.
- Continuous improvement — To ensure ongoing success in process transformation, it’s important to adopt a continuous or lean improvement approach. This involves regularly reviewing and refining digital solutions to optimize their performance and ensure they continue to meet the evolving needs of the business.
2. Business model transformation
This involves leveraging digital technologies to create new business models and revenue streams.
This includes using digital platforms to connect with customers, creating new digital products and services, and exploring new markets through digital channels.
One example of a successful business model transformation is Amazon’s move from an online bookstore to a global e-commerce giant and cloud computing provider. When Amazon was first founded in 1994, it was an online bookstore with a limited selection of books. However, the company quickly realized the potential of the internet to disrupt traditional retail and began to expand its offerings to include other products, such as electronics and toys.
Over time, Amazon continued innovating its business model by launching new services and offerings such as:
- Amazon Prime
- Amazon Web Services (AWS)
As a result of these business model transformations, Amazon has become one of the world’s most successful and valuable companies, with a market capitalization of over $1 trillion as of April 2023.
The company’s success has been driven by its ability to innovate its business model and adapt to changing market conditions, allowing it to maintain a competitive advantage and grow.
Now, wouldn’t that be nice for your business to experience? Think outside the box — you could be the next big disruptor like Amazon.
3. Domain transformation
This involves using digital technologies to transform entire industries or domains.
This includes using technologies such as AI, blockchain, and the IoT to create new products and services, optimize supply chains, and create new business models.
There are several ways to categorize domain transformation, but here are four types of domain transformation:
- Industry-specific transformation — Transform specific industries, such as healthcare, finance, or manufacturing. For example, in healthcare, digital technologies can be used to improve patient outcomes through personalized medicine and telemedicine.
- Market-focused transformation — Expand into new markets or serve existing markets more effectively. For example, a retail company might use digital technologies to create an online store and reach customers in new geographic areas.
- Product or service transformation — Transform the products or services a business offers. For example, an automotive manufacturer might use digital technologies to create connected cars that can communicate with other vehicles and infrastructure.
- Functional transformation — Transform specific functional areas within a business, such as finance, HR, or supply chain management. For example, a business might use digital technologies to automate routine finance tasks such as accounts payable processing or to optimize its supply chain using predictive analytics.
4. Cultural/organizational digital transformation
This involves creating a culture of digital innovation within the organization.
This includes developing a digital strategy, investing in digital talent, and creating a flexible and agile organizational structure that can adapt to new technologies and changing market conditions.
Putting together a digital transformation strategy can be a complex and challenging process, but here are some general steps that can be followed:
- Define the scope and objectives — The first step is to define the scope of the digital transformation initiative and its objectives. This involves identifying the business areas that will be impacted, such as processes, systems, people, and culture, and determining the desired outcomes, such as increased efficiency, improved customer experiences, or new revenue streams.
- Conduct a gap analysis — Once the objectives have been established, it is important to conduct a gap analysis to identify the current state of the business and the gaps that need to be addressed to achieve the desired outcomes. This involves assessing the existing systems, processes, and infrastructure and identifying areas that need improvement.
- Develop a roadmap — Based on the objectives and the gap analysis, a roadmap should be developed that outlines the steps that will be taken to achieve the desired outcomes. This roadmap should include a timeline, milestones, and metrics to track progress.
- Identify the necessary resources — Digital transformation initiatives often require significant financial investment, technology expertise, and organizational support. It is important to identify the necessary resources and secure the support of key stakeholders, including senior leadership and employees.
- Implement the plan — Once the roadmap and necessary resources have been identified, it is time to implement it. This involves changing processes, systems, and infrastructure and providing training and support to employees. Monitoring progress and adjusting the plan to ensure the desired outcomes are achieved is important.
- Continuously improve — Digital transformation is an ongoing process, and it is important to continuously monitor and improve the systems and processes that have been implemented. This involves collecting and analyzing data, soliciting stakeholder feedback, and making necessary adjustments to ensure the business achieves its desired outcomes.
Challenges faced by businesses turning to digital manufacturing
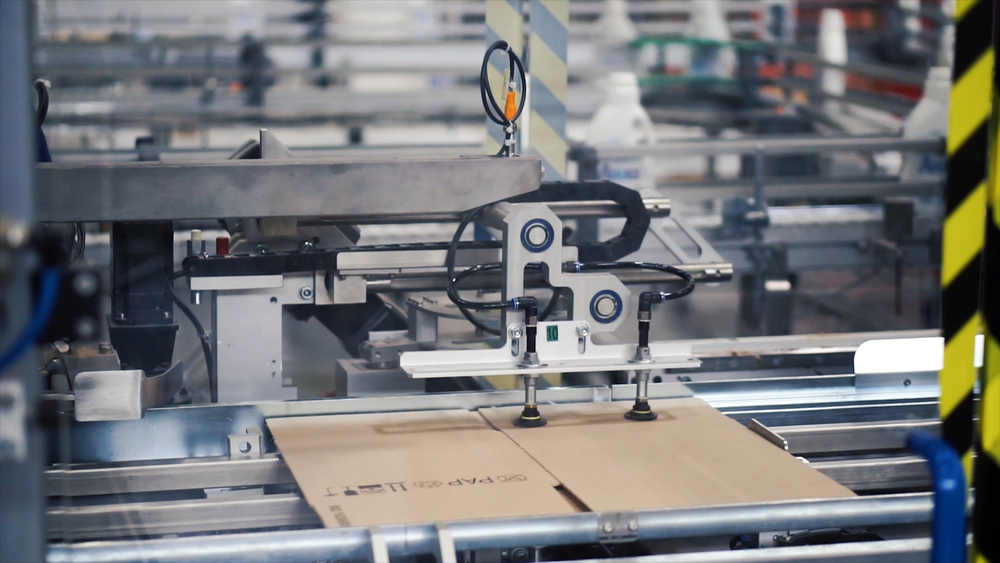
Digital transformation can be a challenge for manufacturing firms for several reasons.
Legacy systems
Many manufacturing firms have outdated legacy systems that are difficult to integrate with newer digital technologies. These systems may be difficult to replace or upgrade due to cost, time, and complexity.
Solution
Moving from a legacy system can be a complex and challenging process, but there are several solutions that manufacturing businesses can consider when digitally transforming their operations:
- Incremental modernization
- Cloud computing
- Integration platforms
- Application programming interfaces (APIs)
- Robotic process automation
- Migration tools
Pro tip: There’s an abundance of free resources online that can help you look for and choose the best software for your business. For example, be sure to check out these guides if you’re looking for software:
Skill gap
Digital transformation requires new skills and expertise like data analytics, cybersecurity, and artificial intelligence. Many manufacturing firms may not have the necessary skills in-house and may struggle to attract and retain talent with these skills.
Solution
Addressing the skill gap is crucial for a successful digital transformation in manufacturing. Here are some solutions that manufacturing businesses can consider:
- Upskilling and reskilling programs
- Partnerships with educational institutions
- Hiring new talent
- Collaboration with technology partners
- Creating a culture of innovation
Data complexity
Manufacturing generates vast amounts of data from various sources, including machines, sensors, and production processes. Managing and analyzing this data can be challenging, particularly for firms with limited resources or expertise.
Solution
Here you’ll want to create easy-to-follow systems for managing data. To get you started, here are some things you can consider to help you with that task:
- Data governance
- Data integration
- Data analytics
- Data visualization
- Cloud computing
- Data science expertise
Resistance to change
Digital transformation often requires significant changes to a firm’s culture, processes, and operations. Employees may resist these changes, leading to resistance and slow adoption.
Solution
Resistance to change is a common challenge when digitally transforming a manufacturing business. Here is what you can consider to overcome this challenge:
- Communicate the benefits
- Involve employees in the process
- Provide training and support
- Celebrate small wins
- Address concerns and challenges
- Lead by example
Security risks
Digital transformation can also increase a firm’s cybersecurity risks. As more data and systems connect, the risk of cyberattacks and data breaches increases.
Solution
Keeping your business’s important information secure is highly important. To make sure your business doesn’t become exposed while you perform the digital transformation in manufacturing, you can:
- Conduct a risk assessment
- Develop a security plan
- Train employees
- Implement a security monitoring system
- Implement data backups
- Implement incident response plans
Cost
Digital transformation can be expensive, requiring significant investments in new technologies, systems, and talent. For many manufacturing firms, the cost of digital transformation may be a significant barrier to adoption.
Solution
Digital transformation can be a costly endeavor for manufacturing businesses, but there are several solutions that can help address the cost:
- Develop a clear strategy
- Use agile methodologies
- Use cloud services
- Use open-source software
- Partner with vendors
- Reinvest savings
8 examples of manufacturing digitalization
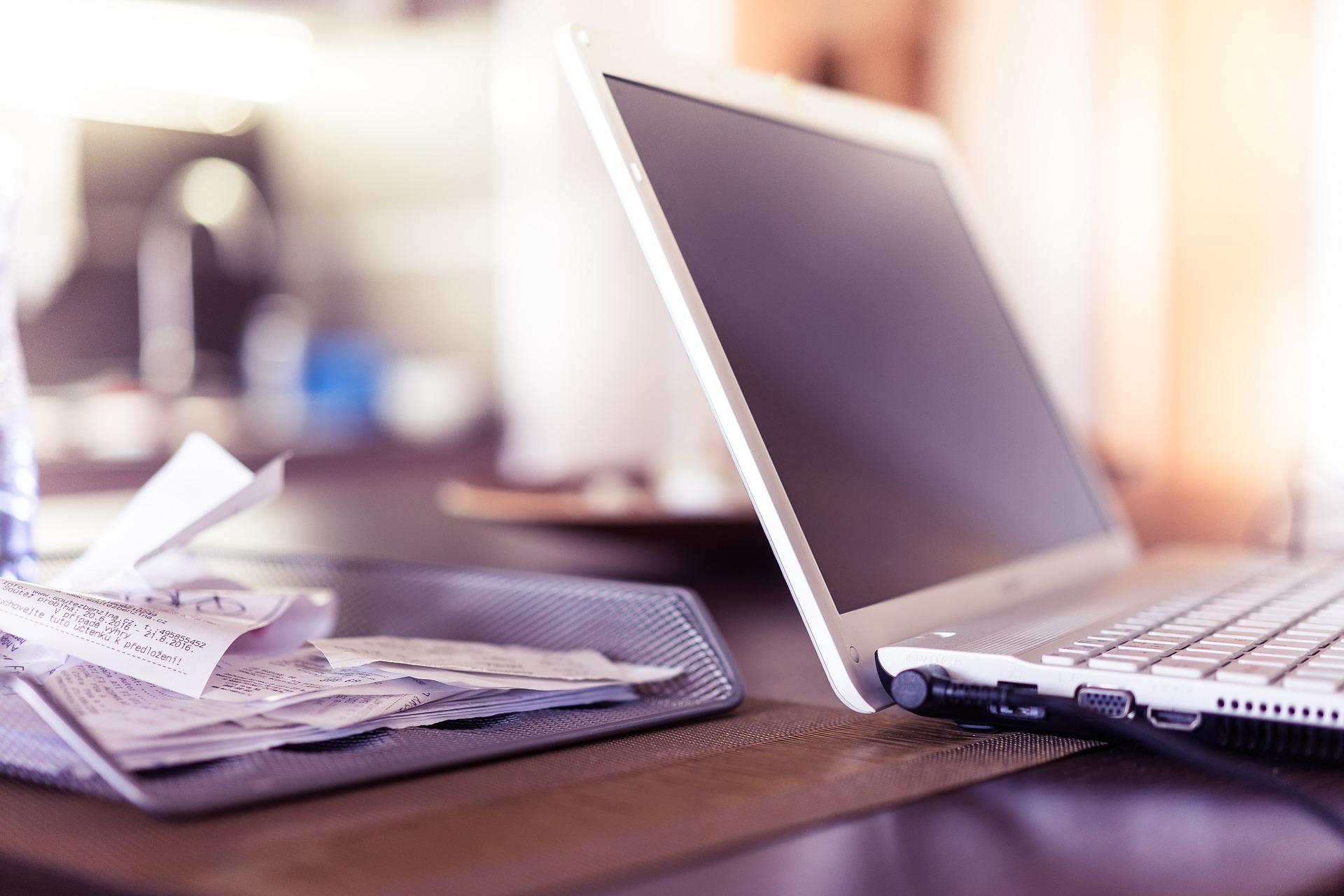
Here are some examples of manufacturing digitalization that you can implement into your business to get more control and optimize your operations:
- Predictive maintenance — Using sensors and machine learning algorithms to predict when machines will require maintenance reduces downtime and increases efficiency.
- Smart factories — Implementing Industry 4.0 technologies such as the IoT, robotics, and artificial intelligence to automate processes and optimize production.
- Augmented reality (AR) — Using AR technology to enhance worker productivity and improve training processes by providing real-time instructions and visualizations of complex processes.
- Digital twin — Creating a virtual replica of a physical asset or process allows for simulation and optimization of processes and predicting future performance.
- Additive manufacturing — Using 3D printing to manufacture parts reduces lead times and inventory costs and enables customization.
- Cloud computing — Storing and accessing data and applications on remote servers, allowing for greater collaboration and scalability.
- Supply chain optimization — Using data analytics and predictive algorithms to optimize supply chain processes, reducing costs and improving delivery times.
- Quality control — Implementing digital technologies such as machine vision and AI algorithms to automate quality control processes and detect defects in real time.
The key components of a successful digital transformation in manufacturing
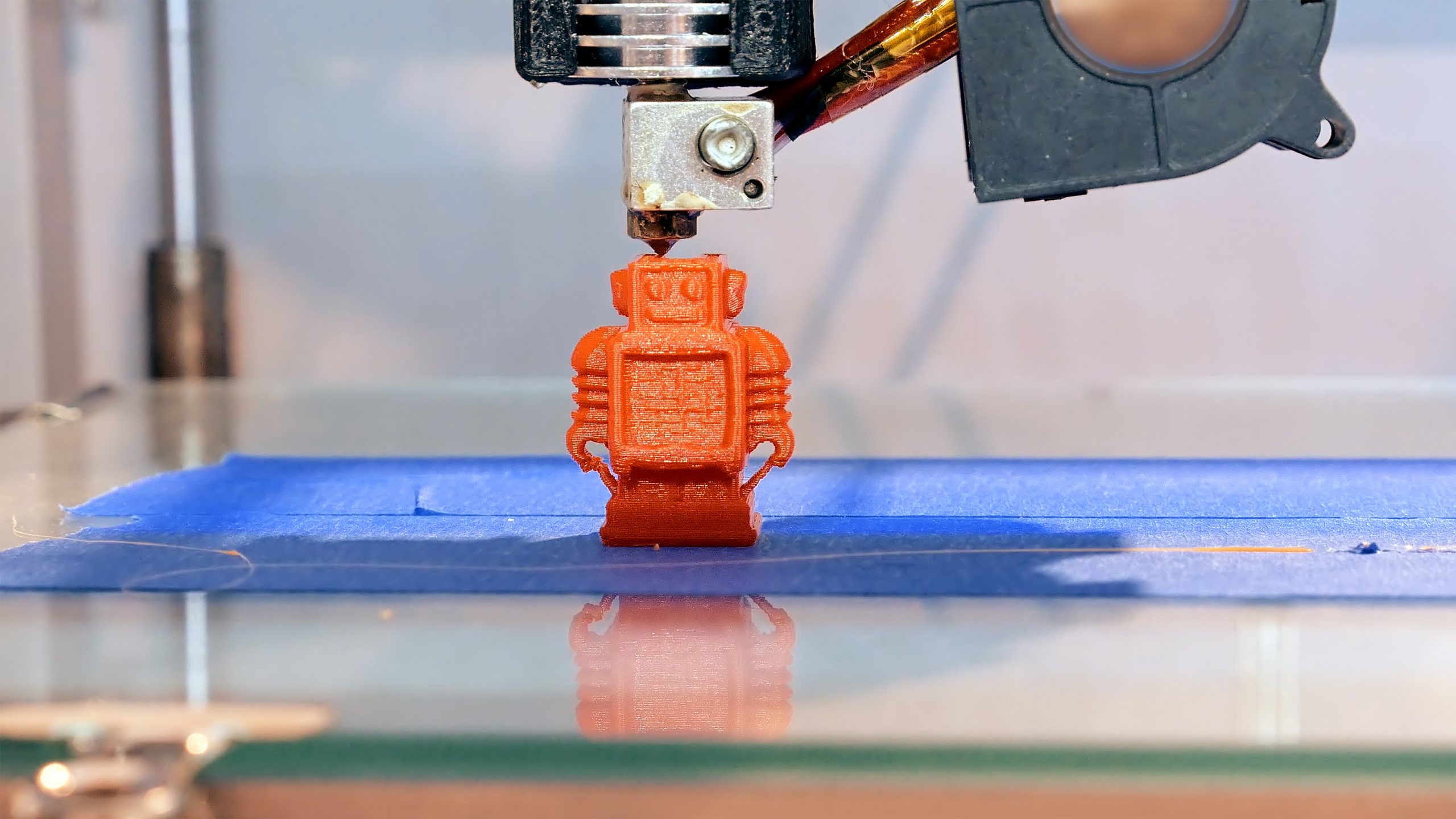
Here are some key components of a successful manufacturing digital transformation:
- Clear vision and strategy — A clear vision of the desired outcome and a well-defined strategy are essential for a successful digital transformation. This includes setting clear goals and identifying the key business areas that need to be transformed.
- Leadership and cultural change — Digital transformation requires a cultural shift within the organization, with leaders driving the change and fostering a culture of innovation and collaboration.
- Data management — An effective data management strategy is essential for successful digital transformation. This includes collecting and analyzing data to gain insights and improve decision-making.
- Technology infrastructure — Implementing the right technology infrastructure is key to achieving digital transformation. This includes adopting modern technologies such as cloud computing, IoT, and AI.
- Integration and interoperability — Ensuring that all systems and processes are integrated, and interoperable is essential for a successful digital transformation. This includes integrating new technologies with legacy systems and ensuring that all systems can communicate with each other.
- Talent development — Developing the skills and capabilities of the workforce is crucial for successful digital transformation. This includes providing training and upskilling programs to ensure that employees can adapt to new technologies and processes.
- Continuous improvement — Digital transformation is an ongoing process, and continuous improvement is essential for long-term success. This involves monitoring progress, identifying areas for improvement, and making changes to the strategy as needed.
Want to see Katana in action?
Katana cloud manufacturing software integrates with your favorite business platforms, syncing data across platforms, saving you precious time and eliminating manual copy-pasting of information.
Using cloud manufacturing software to take your business to the stratosphere
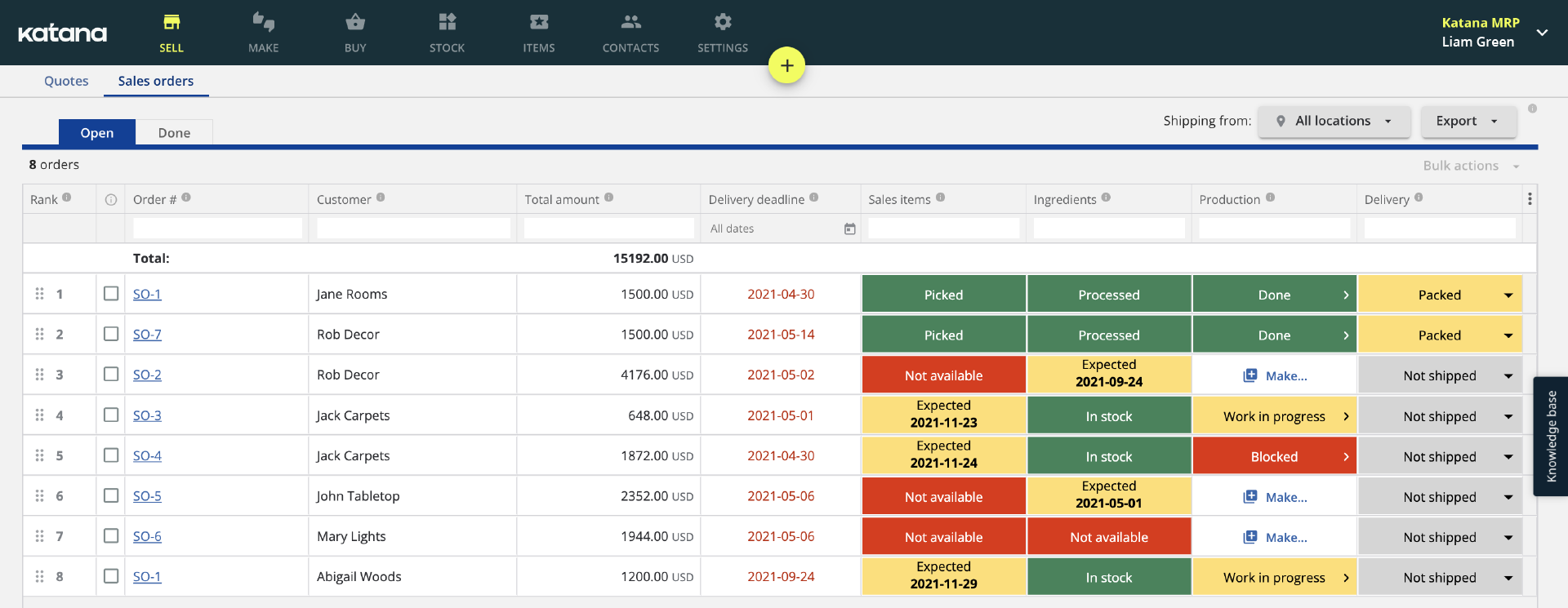
Embracing digital transformation for manufacturing can still be intimidating — especially with all the different routes you can take to achieve this task.
However, the answer to your manufacturing challenges is often the simplest. For many, ditching the pen, paper, and spreadsheets is enough to get their business on the fast track to success. So, what exactly is it that these businesses have found that has launched their business into the digital realm?
Introducing Katana cloud manufacturing software — helping small and mid-sized businesses manage their production and inventory processes.
Katana provides features for automating your and your team’s responsibilities, such as:
- Sales and manufacturing order management
- Production scheduling
- Inventory management
- Purchasing
With Katana, manufacturers can streamline workflows and improve efficiency by providing real-time visibility into production and inventory data. With Katana, users can create and track work orders, manage raw materials and finished goods inventory levels, and automatically calculate manufacturing costs.
As mentioned, integrating tools and processes into your business’s ecosystem is of the highest importance when it comes to digital transformation in manufacturing.
Katana integrates with popular e-commerce platforms like Shopify and WooCommerce and accounting software like QuickBooks Online and Xero. This allows users to synchronize their sales, inventory, and financial data across multiple systems, reducing the risk of errors and improving overall efficiency.
See firsthand why 1000’s of manufacturers trust Katana with managing and automating their processes. Book a demo with Katana, and take your manufacturing business to the next level.
And there you have it! Everything you need to know about transforming your manufacturing into a digital one. If you have any questions, please feel free to reach out, and we hope you found this article useful.
And, until next time, happy transforming.
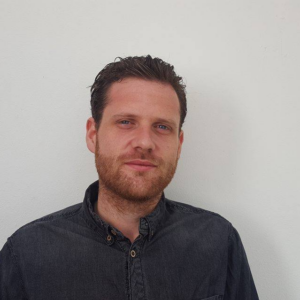
James Humphreys
Table of contents
Get inventory trends, news, and tips every month
Get visibility over your sales and stock
Wave goodbye to uncertainty with Katana Cloud Inventory — AI-powered for total inventory control