Continuous vs. batch process: what are the differences?
Choosing the right production process can make all the difference. In this article, we’ll dive into continuous vs. batch processes to help you make an informed decision for your business.
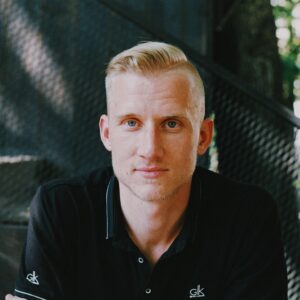
Henry Kivimaa
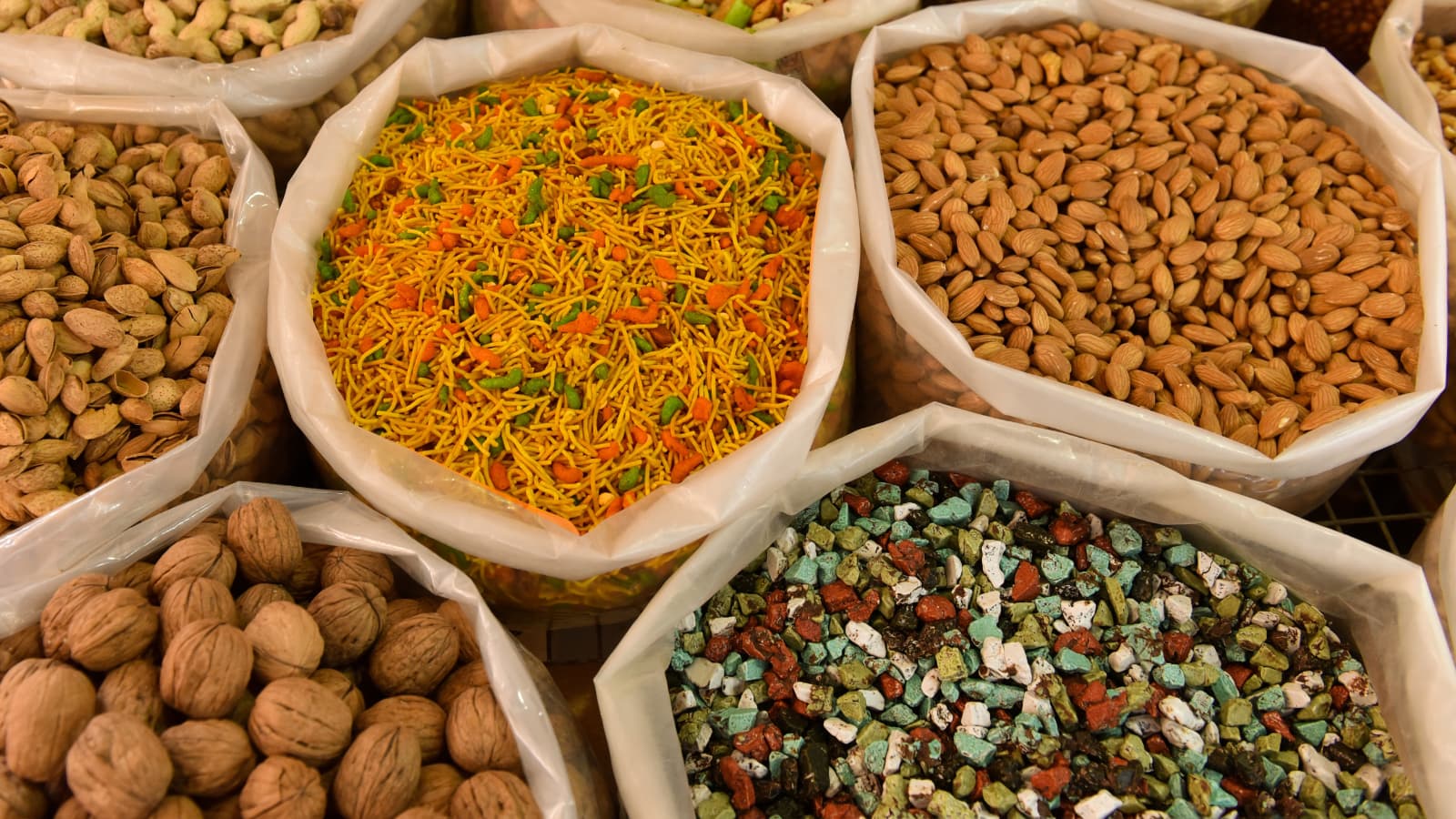
Running a manufacturing business can sometimes feel as though the whole universe is against you, and choosing the right production process is just as crucial as building a reliable team. Like picking a sidekick to help you tackle challenges, deciding between batch and continuous processing can make or break your success.
That’s why we’ve summoned the two titans to battle it out and find the best manufacturing process out there. In the right corner, we have batch processing, and in the left, continuous processing. Both have their strengths and weaknesses and choosing the right one depends solely on your business needs.
So, without further ado — let’s get ready to rumble!
Download the Guide to Batch Production
Download our free ebook guide on batch production to learn more about the benefits, workflows, and software you need to get started.
What is the difference between batch vs. continuous manufacturing?
Batch and continuous processes both have their own advantages and disadvantages. Understanding the differences between these two methods can help businesses choose the most suitable manufacturing process for their specific needs and optimize their production efficiency.
Definition
Batch process refers to a manufacturing method where a specific quantity of goods are made in a single production run.
It has a defined start and endpoint, meaning the process is completed once the batch has been produced. For example, making cookies in a bakery is a batch process, where the exact amount of ingredients is measured, mixed, and baked, resulting in a specific number of cookies. Once the batch is complete, the process ends, and a new batch can begin.
Continuous process is a manufacturing method where the production of a product is ongoing without a defined start or endpoint.
Continuous processes are designed to produce products constantly without interruption.For example, manufacturing chemicals in a refinery is a continuous process that takes place 24/7. Raw materials are constantly fed into the process, producing the final product without stopping.
Production rate and volume
Batch processes are typically slower since they involve stopping and starting the process after completing each batch.
The production rate is limited to the capacity of the materials and ingredients used. This also means that the production output of a batch process is smaller than that of a continuous process. The equipment used in continuous processes is designed to run for extended periods without stopping, allowing for higher production output.
Continuous processes can produce huge volumes of product at a consistent rate, enabling manufacturers to meet demand with a low risk of facing production bottlenecks.
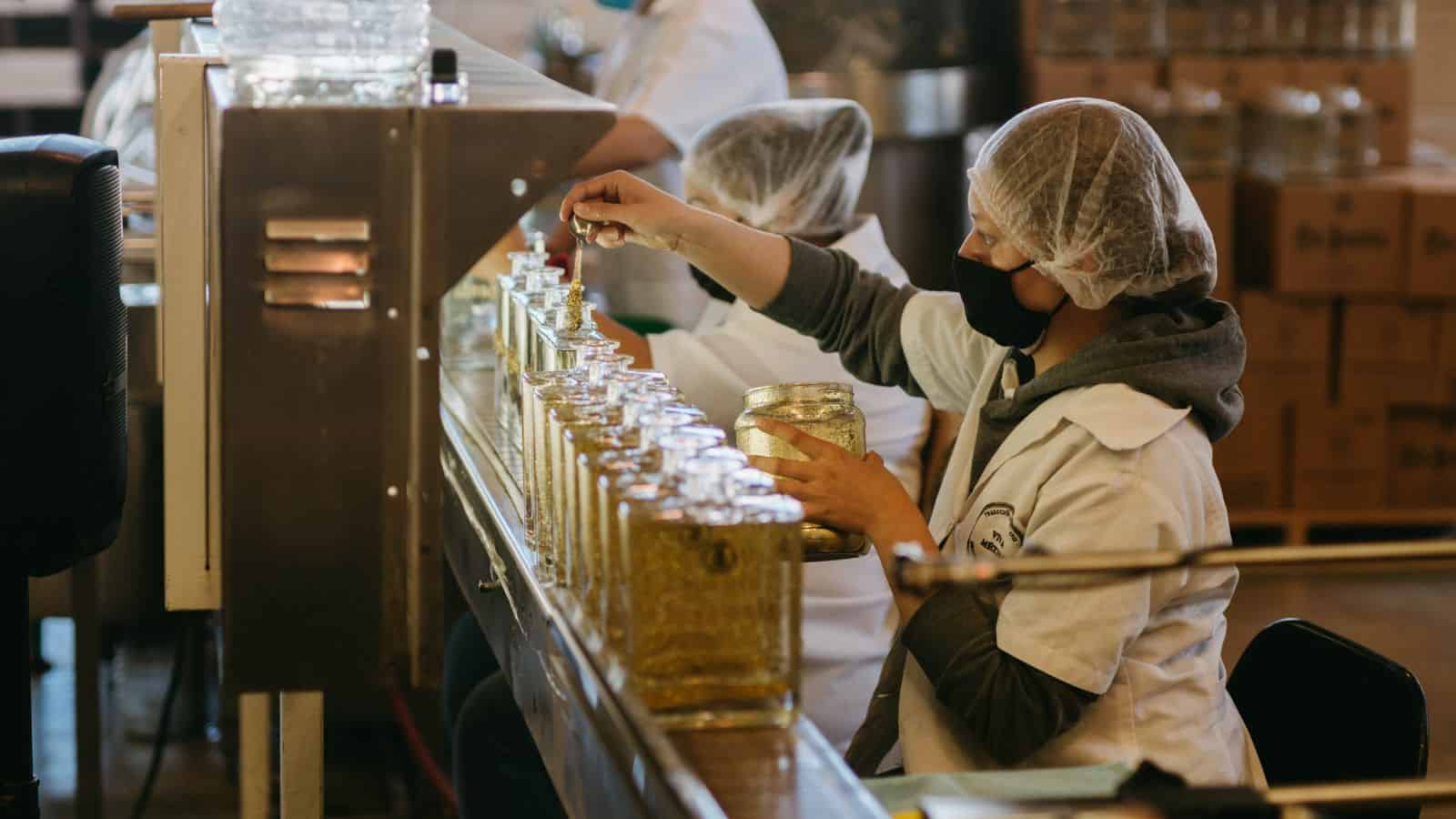
Flexibility
Batch processes are more flexible compared to continuous processes.
In a batch process, the production equipment can be modified to produce different products with relatively low effort. The tools and machinery can be reconfigured to accommodate other materials, formulas, and packaging requirements. This makes batch processing more suitable for smaller productions.
For example, a cosmetics manufacturer can use batch processing to produce various skincare products, such as creams, lotions, and serums, by changing the raw materials and adjusting the production equipment between production runs.
Continuous processes, on the other hand, are more specialized and less flexible.
The equipment is designed to produce a specific product continuously without interruption, making it difficult to modify the process to accommodate a different outcome. Changing the raw materials, formulas, or packaging requirements can require significant investment and reconfiguring the entire process.
For example, metal fabrications use a continuous process to produce steel rods.
The materials are continuously fed into the process, and the final product is made at a high rate. Continuous processing is ideal for large production of a single product in businesses that can afford multiple production lines running simultaneously or where downtime in manufacturing or equipment reconfiguration doesn’t disrupt operations too much.
Quality control
In a batch process, quality control is typically performed at the end of each production run, where the final product is inspected to ensure it meets the quality specifications.
Since each batch is produced separately, any quality issues can be identified and corrected before this batch is sent to retailers and the next lot is started. For example, a bakery may inspect each batch of bread, ensuring that the texture, color, and taste meet their quality requirements before being sold to customers. In case of deviations from the standard, the material and equipment can be adjusted to ensure the next batch has a higher quality.
In continuous processes, quality control is performed throughout the production process.
The equipment used in continuous processes is often designed to monitor the work in real time, allowing for immediate detection and correction of quality issues. This is done using sensors and automated systems that monitor different aspects of the production process, such as temperature, pressure, and flow rate, to ensure the final product meets the desired quality standards. For example, a beverage bottling plant may use automated systems to ensure that each bottle of drink has the correct amount of carbonation, flavor, and color.
Seeing that the quantities in continuous processing are much larger, it’s essential to quickly catch any deviations from the standard to reduce waste.
Pro tip: Quality control is even easier when you’ve established proper standards and guidelines to follow for inspecting products. A production quality control checklist makes tracking quality easy, flexible, and reliable.
Equipment and maintenance
The equipment is typically simpler and smaller in batch processing since it is designed to handle a specific amount of raw materials for each production run.
It’s easier to maintain, clean, and inspect between production runs to ensure that it operates correctly. Maintenance is typically performed periodically, depending on the production schedule. However, since each production run involves starting and stopping the process, the equipment may experience more wear and tear, requiring frequent maintenance to ensure it operates correctly.
This also means that batch processing equipment tends to be easier to maintain and less expensive than continuous processing equipment.
Continuous processes, on the other hand, require specialized equipment designed to run for extended periods without stopping.
It is larger, more complex, and more expensive than batch processing equipment. Maintenance for continuous processing is critical since any equipment failure can cause significant production downtime, resulting in substantial losses. The machines are designed to monitor operations continuously using sensors and automated systems to detect any potential issues, allowing maintenance to be performed proactively.
Maintenance for continuous processing equipment is typically more frequent and more involved than in batch processing, but because of the higher production rate and efficiency, the investment in maintenance is necessary to ensure consistent output.
Cost
Batch processing typically has higher unit costs compared to continuous processing.
This is due to lower production rates, smaller equipment, and more frequent equipment cleaning and maintenance. Batch processes are often used for smaller productions or niche markets where the cost of production is less critical. It can be a more cost-effective choice for producing high-value or specialty products where quality and flexibility are essential, such as pharmaceuticals or cosmetics.
Continuous processes have lower unit costs than batch processes due to higher production rates, larger equipment, and lower cleaning and maintenance fees.
Continuous processing is commonly used for large-scale manufacturing. The process allows for higher production rates, resulting in lower unit costs. Continuous processing is suitable for products with stable demand, where large quantities are produced over an extended period.
Power up your business
Beat inefficiencies and dominate your competitors with Katana.
What are semi-continuous processes?
Some manufacturing processes aren’t as black and white or easily distinguishable.
That’s why the term “semi-continuous processes” was coined to describe activities that combine both batch and continuous processes. Materials are processed in batches but then linked together in a continuous sequence. This means no breaks in the production process, and materials are constantly fed into the system.
Semi-continuous processing can be seen as a compromise between the flexibility of batch processing and the efficiency of continuous processing.
While continuous processes are typically set up to run at a constant rate, with minimal adjustments made during production, semi-continuous processing allows for adjustments between batches to optimize the workflow and ensure consistent quality. An example of semi-continuous processing is certain food manufacturing, such as bread or pasta. It involves a combination of continuous and batch processing steps. For instance, the mixing and kneading of dough could be done continuously, while the shaping and baking of individual loaves or batches of pasta are done in batches.
This allows for more efficient use of equipment and resources while still maintaining quality control.
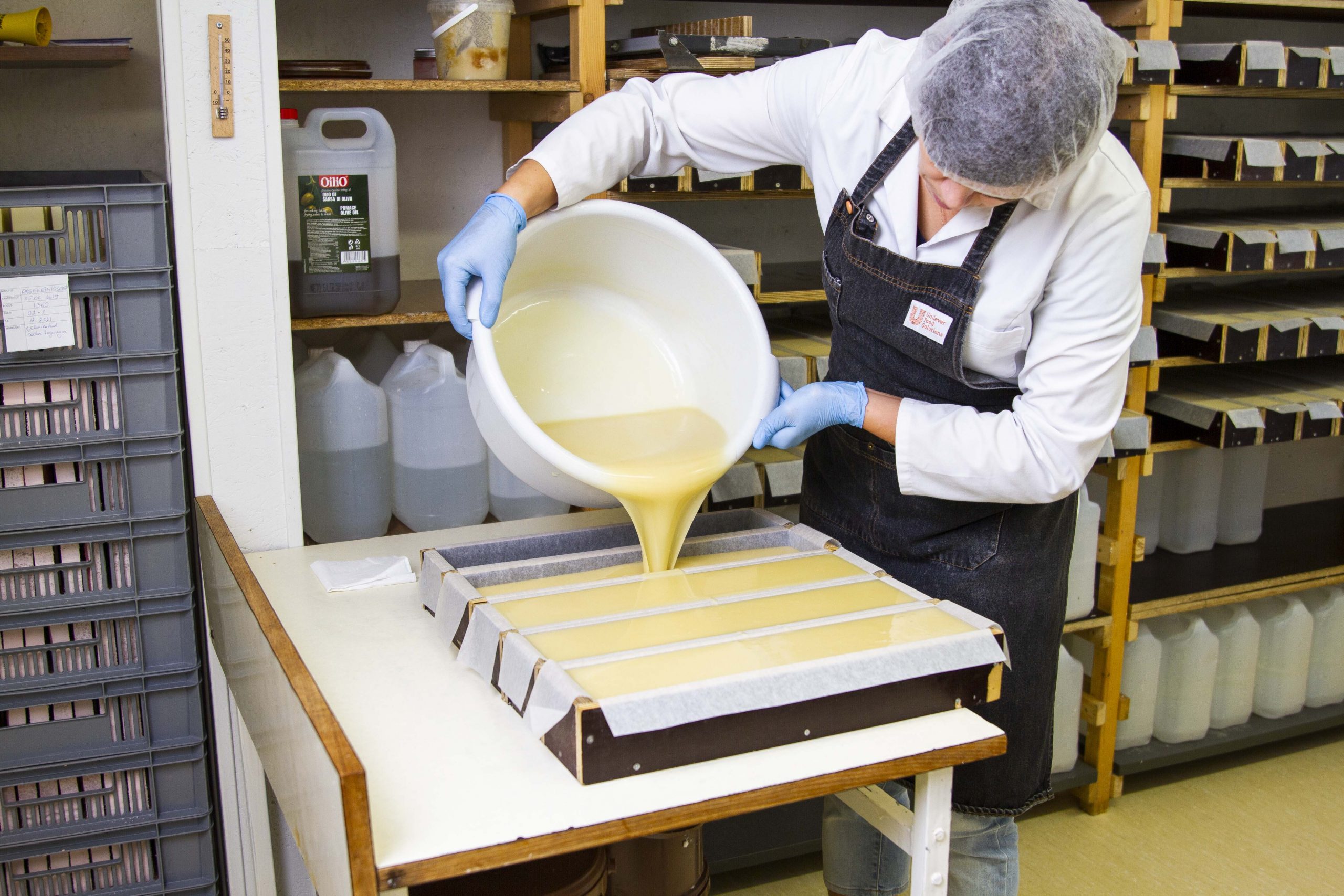
Partner up with Katana
In addition to a sidekick, every hero also needs a superpower.
Laser vision, as fun as it may be, won’t do much for you in manufacturing. That’s where Katana comes to the rescue. It offers many features to enhance and simplify your production experience, including the following.
Inventory Management
Katana offers real-time insights into stock levels to track raw materials, work in progress, or finished goods. Track inventory in all your locations and set reorder points to minimize the risk of a supply shortage.
Inventory levels are automatically adjusted based on incoming sales orders and supplier data, which can be done periodically in a batch process or constantly in a continuous process to keep inventory levels up-to-date.
Production Scheduling
Many businesses use Katana to optimize their production plans. For instance, you can create schedules or reprioritize production based on incoming orders, material availability, and other business decisions.
Both batch and continuous processes need schedules to run efficiently, so whichever model you choose for your business, Katana will have the data to support your decisions.
Shop Floor App
Similarly to production scheduling, Katana’s Shop Floor App helps you plan operations and assign tasks to your shop-level workers.
It is accessible via a smart device and streamlines much of the manufacturing. After completing a task in the Shop Floor App, its status and impacted inventory levels are automatically changed in Katana too.
In a batch process, the Shop Floor App in Katana can be used to track the progress of a batch of products as they move through production stages. In contrast, in a continuous process, the Shop Floor App can monitor material consumption throughout the production run.
Data Analytics
Katana offers various data analytics, which involve different types of insights from customers, sales, orders, and production.
For instance, Katana can analyze sales data to identify how customers purchase products and use that information for upcoming demand planning. Or, businesses can gather detailed manufacturing analytics to find better ways to optimize their operations.
In a batch process, the data can be used to analyze past batches and to identify purchase patterns and trends. However, in a continuous process, Katana’s data insights can be used in real-time to improve business performance.
Integrations
Katana offers integrations with a wide range of software for all requirements and use cases.
Accounting, e-commerce, automation, and much more — check out all Katana’s integrations and choose the best one for your business. Or, if you have a favorite that isn’t on that list yet, just build it into your workspace using Katana’s open API and make it your own.
After a thrilling and closely-fought match of batch vs. continuous processes, the judges have announced a tie.
There are usually no universal solutions in manufacturing, and this case is no exception. Ultimately, each business is unique and requires a personalized strategy. The ideal manufacturing process is the one that works best for your specific needs.
Unleash your superpowers with Katana
Book a demo to get all your questions answered regarding Katana’s features, integrations, pricing, and more.
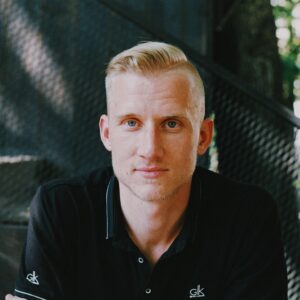
Henry Kivimaa
Table of contents
Get inventory trends, news, and tips every month
Get visibility over your sales and stock
Wave goodbye to uncertainty by using Katana Cloud Inventory for total inventory control
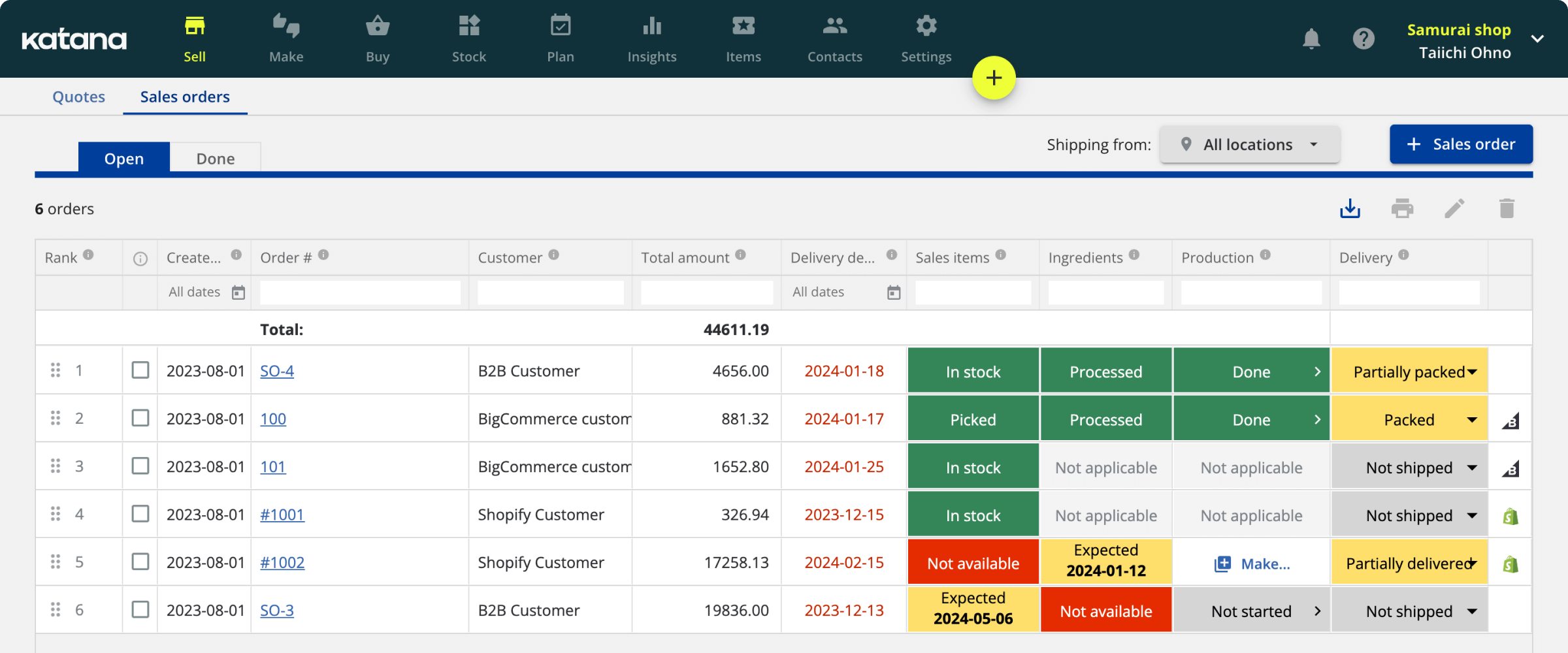