Understanding manufacturing batch records
Manufacturing batch records are crucial documents for verifying quality in chemical and process manufacturing. Here’s everything you need to know about them.
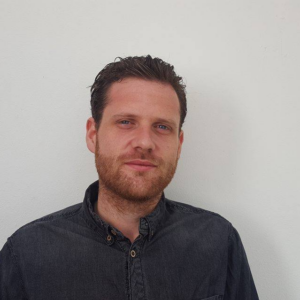
James Humphreys
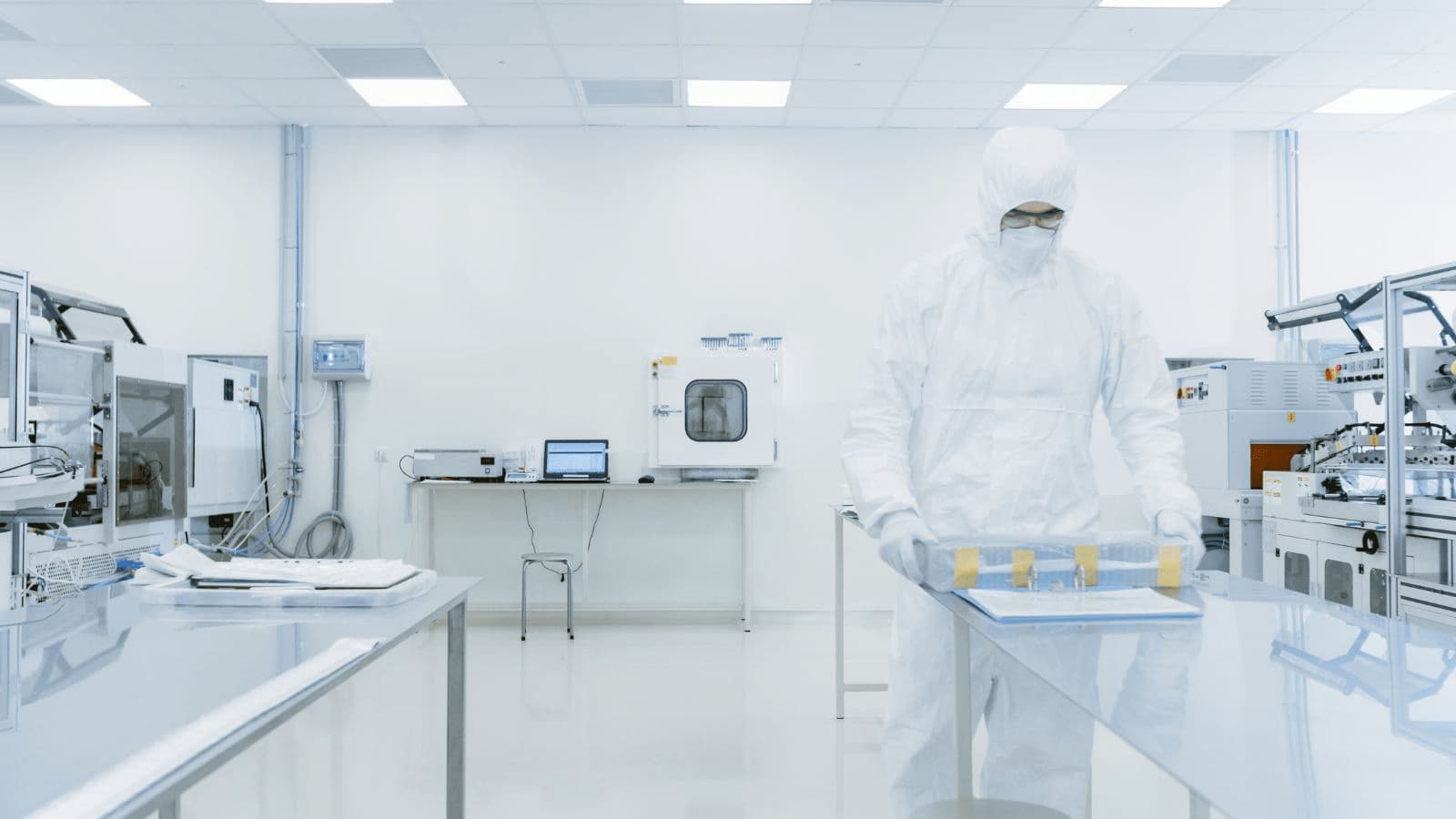
There is an old saying used in the Food and Drug Administration and other compliance organizations:
If it isn’t written down, it didn’t happen.”
In the pharmaceutical manufacturing industry, this is especially true. Documentation is critical if a company is to follow current good manufacturing practice (cGMP) regulations. Batch manufacturing records (BMRs) are an important part of that documentation process.
However, maintaining complete and accurate BMRs can be challenging without the proper systems in place. Below, we’ll walk you through the different types of documents that you should be creating, why they are important, and what is included in each.
Download the definitive guide to batch production
Download our free ebook guide on batch production to learn more about the benefits, workflows, and software you need to get started.
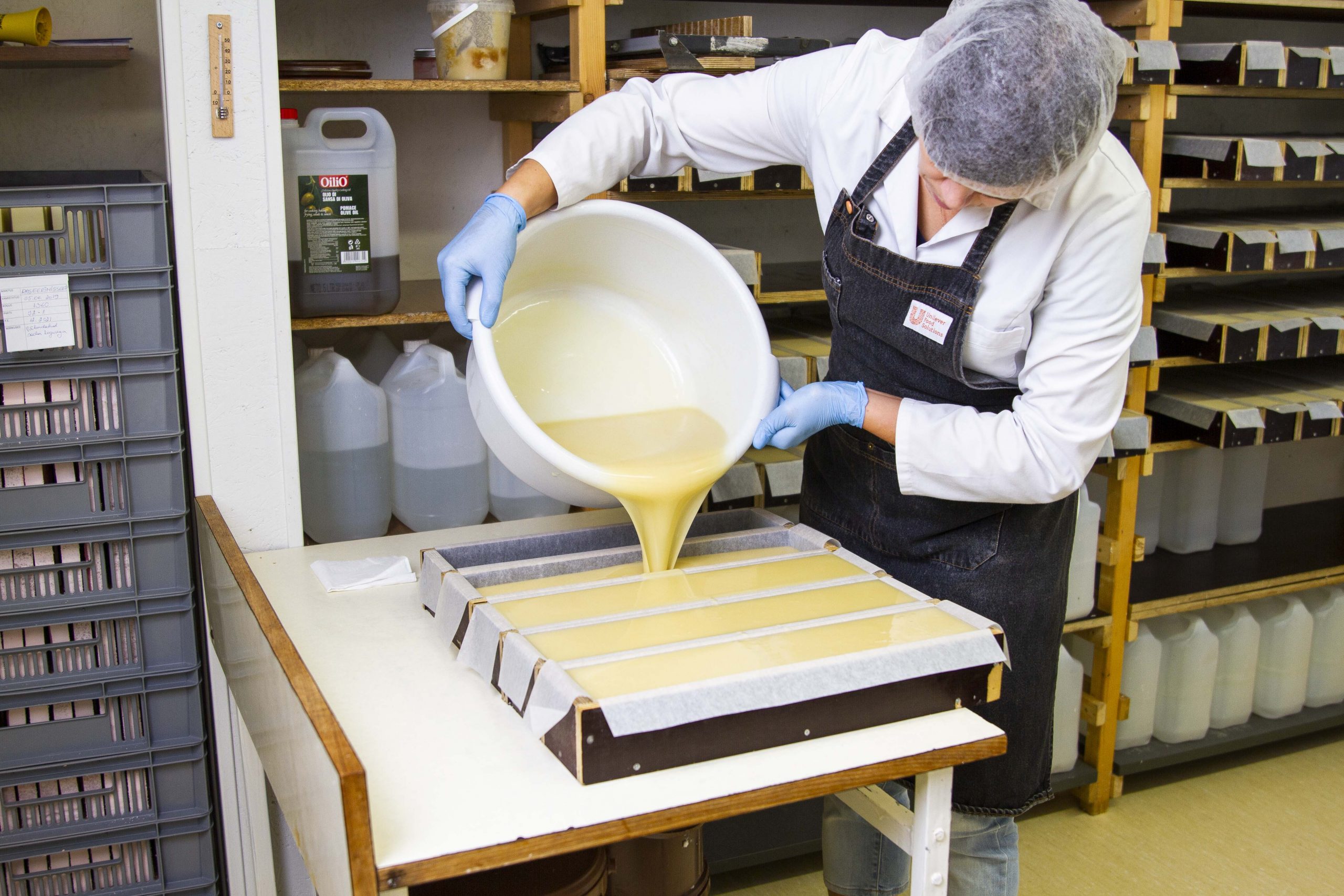
What is a batch?
In pharmaceutical manufacturing, a batch is defined by the FDA as “a specific quantity of a drug or other material that is intended to have uniform character and quality, within specified limits, and is produced according to a single manufacturing order during the same cycle of manufacture.”
For example, a company that is producing 100,000 pills of a certain medication would consider the entire 100,000-pill run to be one batch. Each pill is expected to be identical to the others in terms of the active ingredient, strength, and other specifications.
What is a batch record?
A batch record is a comprehensive set of documents that outlines all aspects of the manufacturing process for a particular batch. It includes details about ingredients and supplies used, equipment settings, personnel involved, test results, and more.
Types of batch records
There are a few titles for these records that often are used interchangeably:
- Batch manufacturing records (BMRs)
- Batch production records (BPRs)
- Master production records (MPRs)
However, each differs slightly in scope and function, so it is critical to understand the differences.
Batch manufacturing records
This is the most comprehensive type of batch record. It includes all the data associated with the manufacturing process, from raw materials to finished products. This is used to track and document each step in production, including any deviations that occur along the way.
Essentially, it is a roadmap and a ledger for the product’s journey from raw ingredients to finished goods. It is instructional, serving as a guide for manufacturing the product.
Batch production records
A BPR is a subset of the BMR. It includes only information about the production, such as equipment settings and personnel involved. This record is used for tracking and documenting results rather than providing instructions for how it should be done.
A BPR checklist will contain:
- Overall information — The name of the product produced, batch size, license number, and location of manufacturing
- Ingredients — The quantity and source of raw materials used, along with any identification numbers
- Equipment — Classification and identification numbers of the machines used, along with maintenance documentation
- Production — The dates each step took place, a signature of who completed it
- Yield — Including both expected and actual
- Packaging — The type and size of the container used, along with any additional labeling
- Quality control — Documentation of all tests performed, such as for potency and sterility
- Finished product — New batch number, analysis, and expiration date
Unlike a BMR, this is not a roadmap but a log of the product’s actual manufacturing journey. It documents what happened, not what is planned.
Master production record
An MPR is the highest-level batch record. It is a master set of instructions that outlines how the product should be manufactured, including all steps and processes. This document serves as a template for creating BMRs and BPRs for each batch produced.
It will include things like:
- Estimated cost and yield
- Raw materials and supplies needed
- Processing steps and times
- Testing criteria and results
- Storage requirements for the finished product
An MPR is an important document to have on file, as it serves as a starting point for all future batches. It ensures that each batch is manufactured consistently according to cGMP regulations.
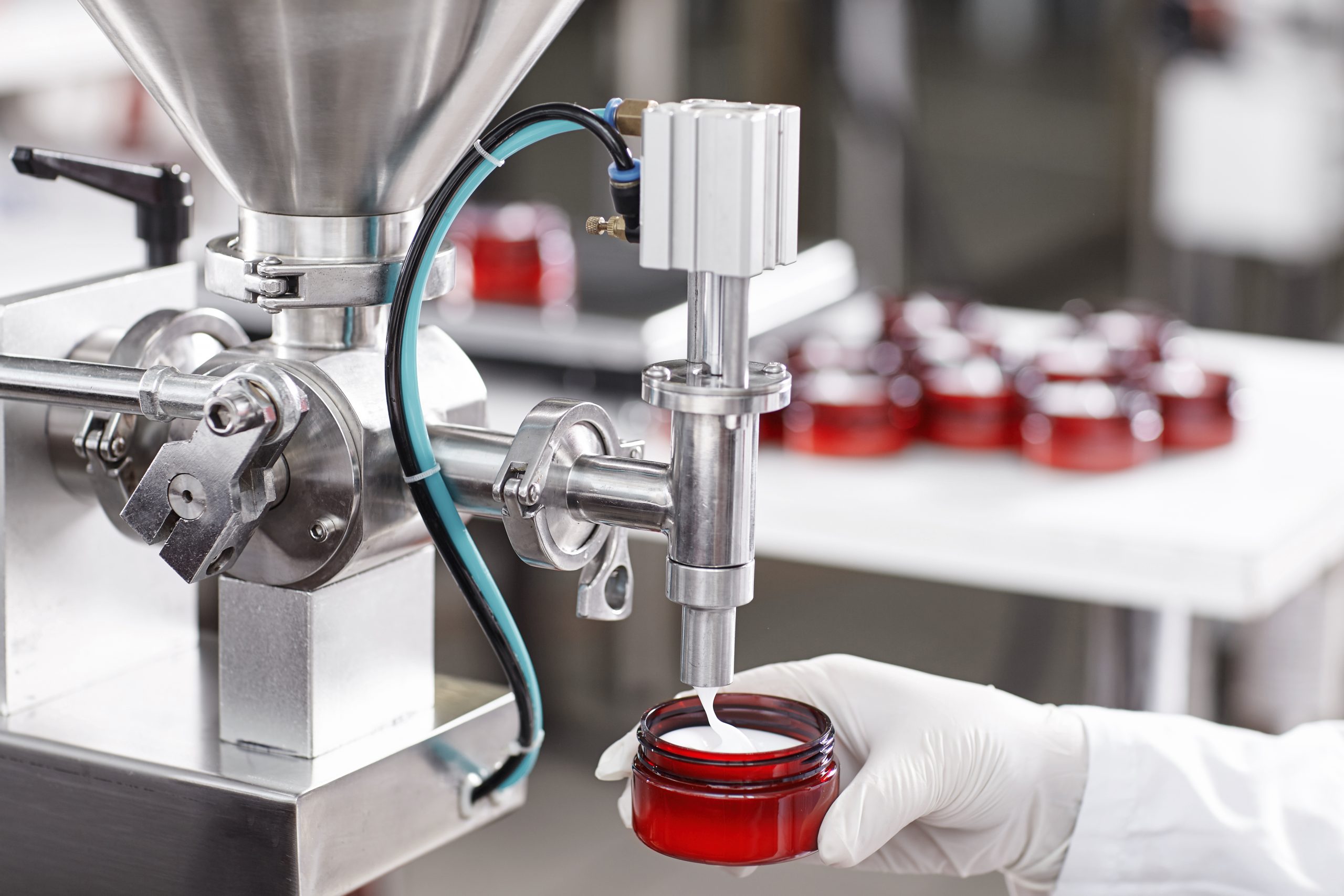
Why are batch records important?
Batch records are important for a few reasons:
- Evidence that the production process is compliant with cGMP regulations. This is critical in demonstrating to regulators that a company is operating within the law and producing safe, effective products
- Traceability and transparency in the manufacturing process. This means any problems can be quickly identified and corrected before more batches are produced with the same issues
- Used to optimize operations by providing data on how long each step takes or which ingredients yield better results. This information can then be used to make improvements where necessary
They also serve as a reference for future production, guiding how to replicate the same outcome.
What is included in a batch manufacturing record?
Every BMR, when properly formatted, should include the following sections:
Critical dates
This section should include the start and completion dates of the batch, as well as any other milestone dates. These are important for tracking the progress of the batch and ensuring that it is completed on time.
Bill of materials
All raw materials used in the batch should be listed in the bill of materials (BOM), including ingredients and packaging components. This is to ensure that each component meets cGMP batch record requirements and is suitable for use.
Manufacturing process
This is an overview of the steps taken to complete the batch, from mixing and blending ingredients to packaging and labeling. Any deviations from the standard procedure should be noted here.
Signatures
At the end of each step in the process, a qualified person should sign off on it. This is to confirm that they have inspected and approved the work done at that stage.
Potential hazards
Any potential hazards associated with the product should be noted here. This could include allergens, contaminants, or anything else that may cause harm to those consuming the product.
If personal protective equipment (PPE) is needed, that should also be listed in this section and worn as appropriate.
Equipment
A list of all the equipment used in the process should be included. This is to ensure that all machinery and tools are up-to-date and properly calibrated for optimal results.
Quality control
This section details all tests that are to be performed on the product. It should have instructions on
- How the test should be conducted
- What equipment is needed
- What results are expected
After they are complete, the results will also be noted here, with any significant outliers highlighted.
Maintenance
Any maintenance and cleaning tasks that are carried out during the batch process should be noted here, as well as any unexpected maintenance issues. Dates, personnel, and other details should be included.
Yield
Expected and actual yield from each step in the production process should be listed here. This is important for tracking the efficiency of the process and ensuring that there are no unexpected losses.
Packaging
This section should include the type of packaging used, along with any labels and instructions. Documentation for any special packing requirements should also be included.
Definitions
This section defines the terms used throughout the BMR. This is to ensure that everyone involved in production understands the same language and processes.
Change log
This is a timeline of any changes that have been made to the batch during production. This helps to ensure that all variations are tracked and accounted for.
Batch details
The name, identification number, and quantity of the batch should be included in this section. This helps to ensure that each batch is traceable and that any issues can quickly be identified and resolved.
Compliance documentation
Finally, this section should include any documentation related to compliance with batch records GMP regulations. Approval signatures and materials from third-party testing should be included.
How is a batch manufacturing record presented?
Most batch records examples are presented in a tabular format. This makes it easy to compare data from different batches and quickly identify any potential problems or areas for improvement.
Some software programs can generate BMRs automatically, saving time and reducing the risk of errors.
Who prepares batch manufacturing records?
The person responsible for preparing the BMR will depend on the size and structure of the company. In smaller companies, it is usually a designated individual or team. In larger companies, there may be separate teams for each department involved in production (e.g., quality control, operations).
Regardless of who prepares them, all personnel involved in producing a batch should review and sign off on their accuracy before they are submitted to regulators. This helps to ensure that all cGMP regulations are being met.
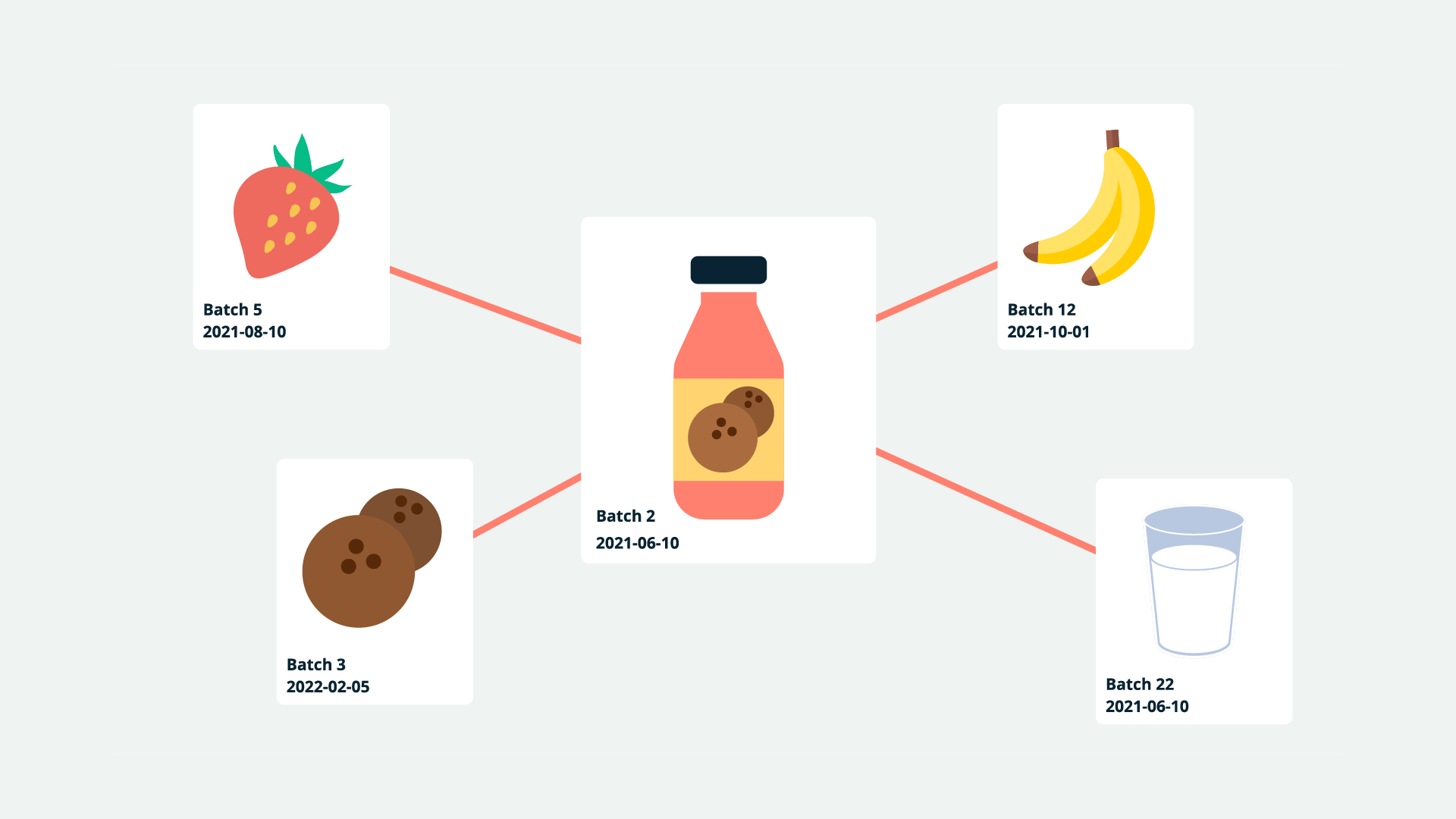
How software can help
Enterprise resource planning (ERP) solutions can help streamline the process of creating, tracking, and managing batch records. This helps companies stay compliant with cGMP regulations by providing comprehensive documentation that is accessible from anywhere.
It also provides real-time visibility into production operations, which allows for more efficient decision-making and better control over quality. Additionally, it can be used to generate reports on performance metrics or data trends to make informed improvements to the production process.
Want to see Katana in action?
Adopt Katana’s batch tracking software to cut back on admin time and streamline your business operations.
Streamlining with software solutions
Without batch manufacturing records, it would be impossible to ensure the quality of a product. When it comes to pharmaceutical manufacturing, quality can be quite literally a life-or-death scenario.
BMRs are the foundation of a successful production process, and software solutions can help to streamline the process and ensure that all records are accurate and up-to-date.
For help gaining visibility and tracking materials, processes, and performance metrics in real time, get a Katana demo!
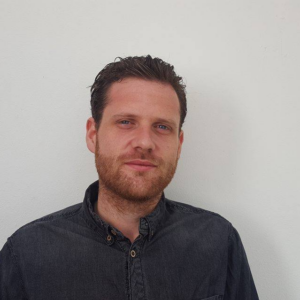
James Humphreys
Table of contents
Get inventory trends, news, and tips every month
Get visibility over your sales and stock
Wave goodbye to uncertainty by using Katana Cloud Inventory for total inventory control
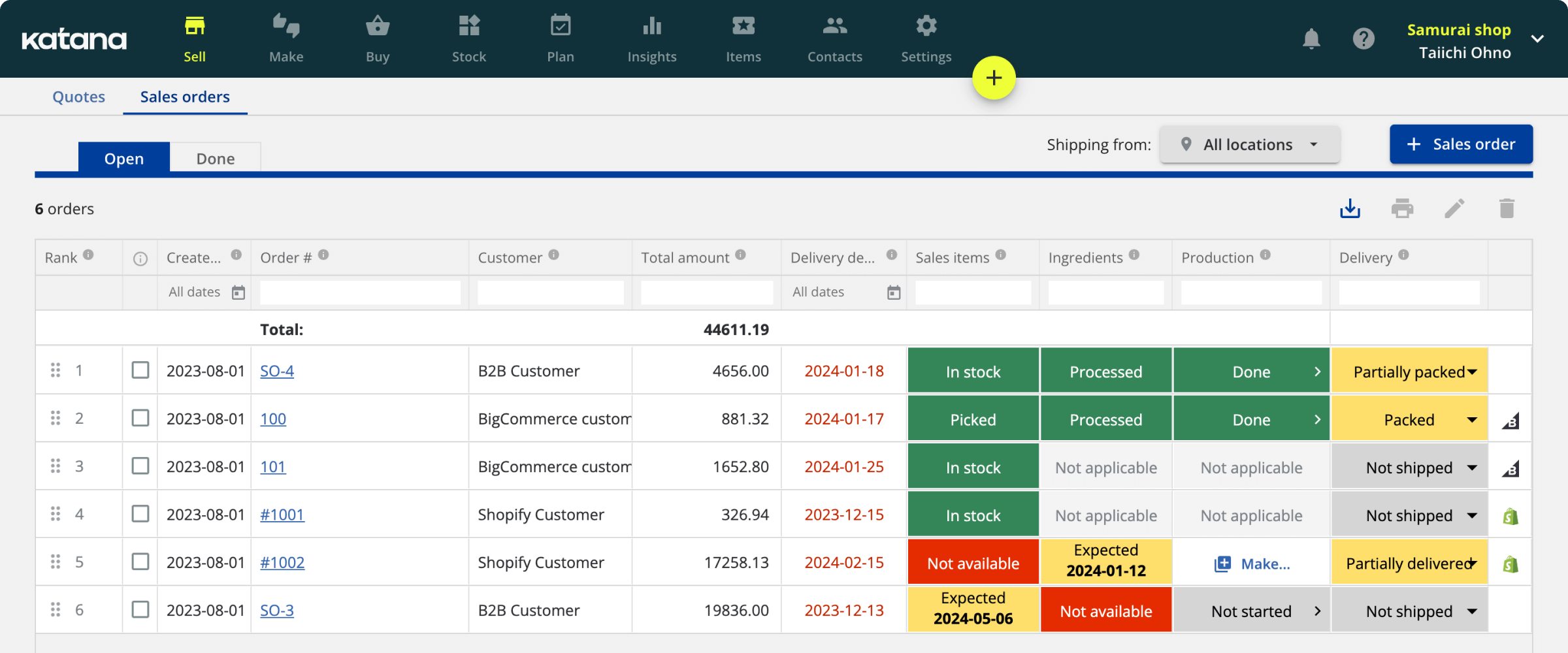