Advanced planning and scheduling: A crash course
Optimize your manufacturing operations and take your production planning and process scheduling to the next level with an advanced planning and scheduling (APS) system.
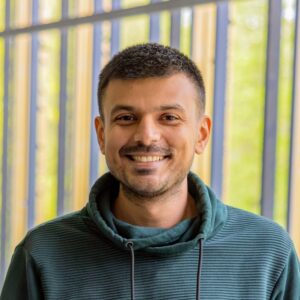
Tejas Shah
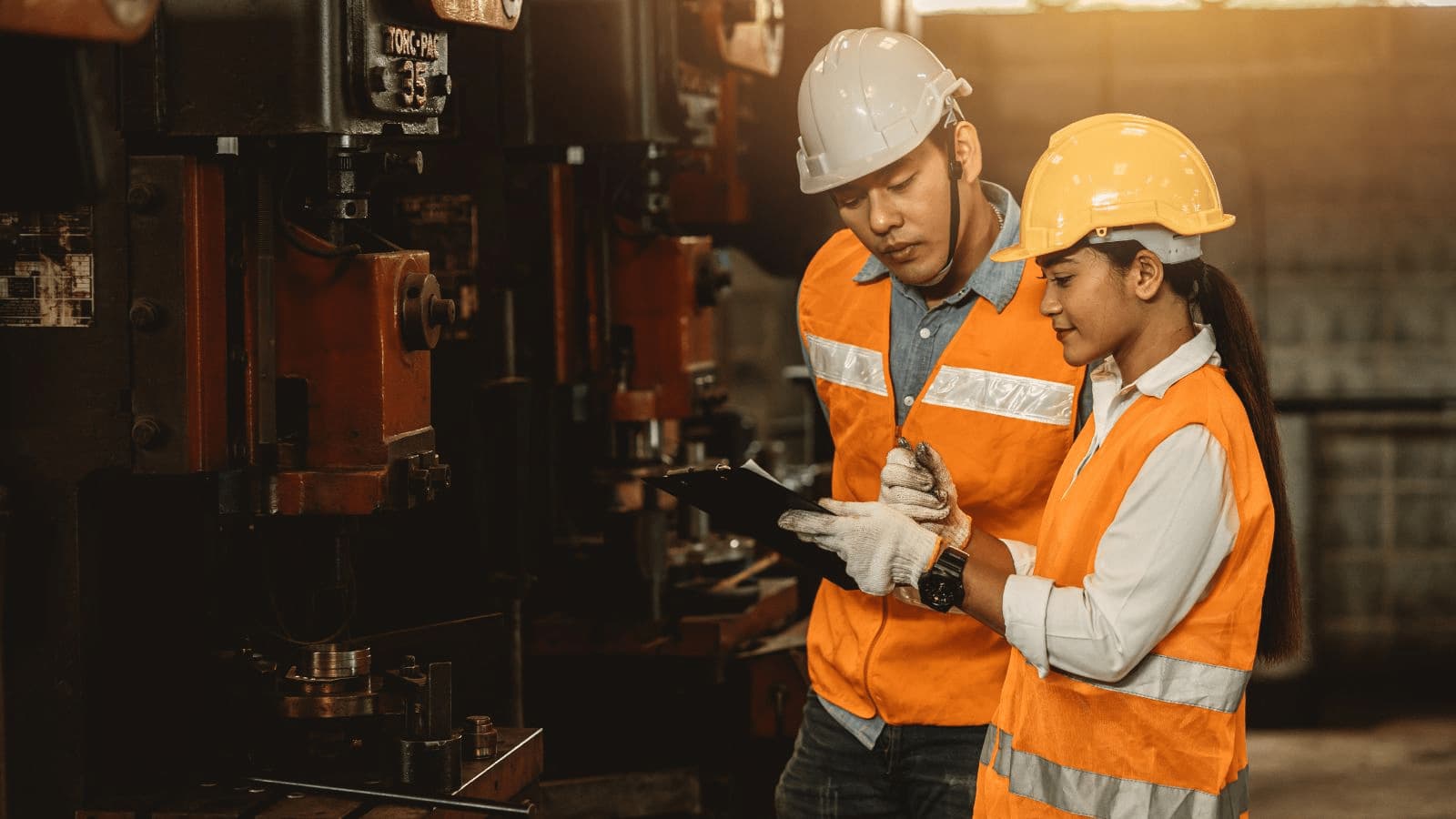
Your manufacturing business is flourishing, and you are considering expanding your product line and production capacity. Now, although you have all the resources to set up another manufacturing plant, building more production capacity haphazardly simply leads to chaos and is a sure-shot way to production hell.
In situations like these, you need a system to plan and set goals for your company. Once plans are charted, you need to translate them into detailed steps for your teams across your production floors. This is exactly what advanced planning and scheduling systems help you achieve by first helping you plan the big picture and then generating detailed schedules in line with the plans.
In this article, we cover everything you need to know about advanced planning and scheduling systems so that you can make an informed decision when it comes to implementing one for your workflows.
Automatic production plans and scheduling with Katana manufacturing ERP software
Thousands of manufacturers trust Katana to manage their day-to-day operations, allowing them to focus on growing their business.
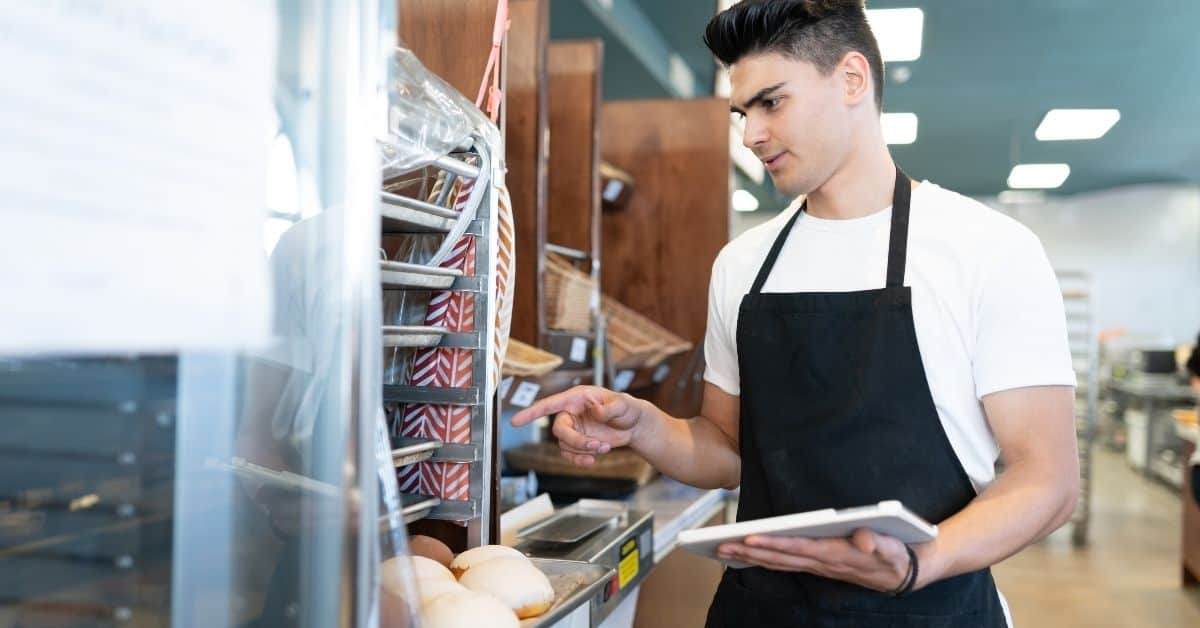
What is an APS system?
Advanced planning and scheduling (APS) is a manufacturing management process that helps you to deal with production planning and shop floor scheduling. APS systems employ advanced algorithms to balance various variables in the production process, such as demand and capacity, to create achievable production schedules.
It is well known that the number of variables that influence the efficiency of your production processes goes up exponentially with higher production capacity and an expanding product range. It becomes humanly impossible to optimize your manufacturing processes — this is when you can employ advanced planning and scheduling to solve this complex problem of optimization.
APS systems can be used as a standalone solution to create strategic long-mid-term plans and detailed sequencing and scheduling for the short term. Sometimes they come bundled with a manufacturing enterprise resource planning (ERP), as is the case with Katana. The bundling can equip your business with a comprehensive set of digital tools to tackle the complexities of production.
Before we venture into the deeper waters of “advanced” planning and scheduling, let’s take a step back and understand the basics of planning and scheduling.
Manufacturing planning
Manufacturing planning involves thinking strategically about the goals for your business and essentially coming up with a “plan” to achieve the goal. This translates to first understanding the value that you bring to your customers. Interestingly, knowing the value your business brings is the first principle of lean manufacturing.
As a simple example, let’s assume that you are in the automobile manufacturing space, and your cars are known to have the best mileage in their class. So your planning process should start by first cementing your ideas about the business and what your customers buy your products for, which in your case happens to be mileage.
The next step in planning involves answering questions about the quantities of products, the raw materials, resources, sourcing, etc. This step takes into account the current state of your business and helps you set goals.
Continuing with our example, at the end of your planning phase, you could aim to increase the output of your best-selling car by 10% and increase the total revenue generated by 5%.
You would turn to the production schedule with planning out of the way.
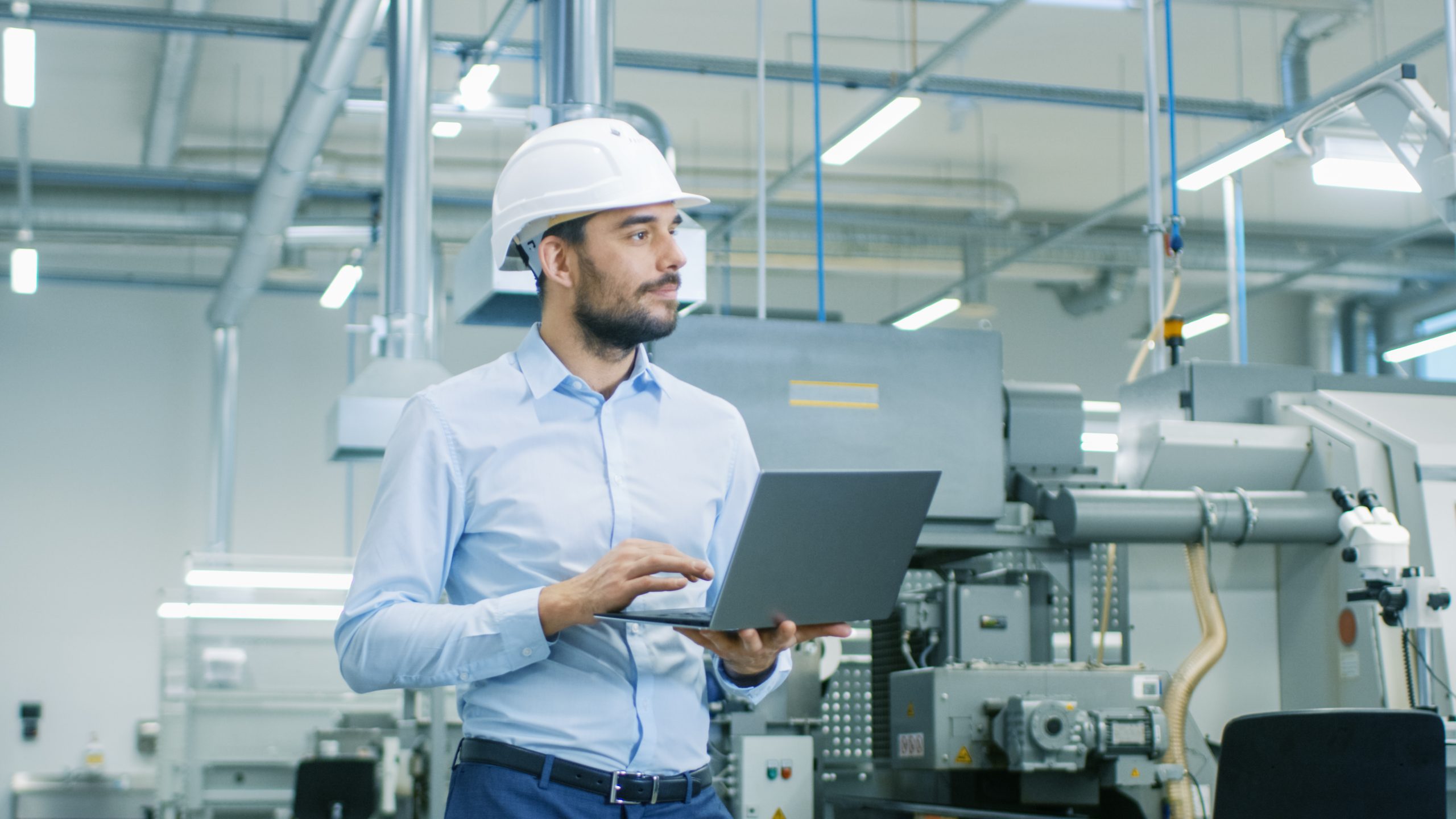
Production scheduling
A production schedule lists every product manufactured, including when and where it’ll be made. Production scheduling identifies which materials a manufacturing project requires and improves the process of allocating the correct resources.
The devil is, as they say, in the details. Scheduling can be especially tricky because the day-to-day operations depend on the scheduling. The scheduling system you employ should help you deal with competing priorities and be robust and dynamic in the face of changing circumstances.
So continuing with our example, in the scheduling phase, you’d deal with ironing out the details. For instance, it could mean figuring out which factories would get upgrades or which plants would start producing more. Additionally, your schedule would list where each car you manufacture will be produced down to which machines will do what.
Schedules like these are manageable with simple systems at a small scale. However, as your business grows, you need more powerful tools.
Planning vs scheduling
Before we proceed further, it is important to understand the difference between planning and scheduling.
On a high level, planning deals with the big picture, while scheduling deals with the specifics.
Planning sets the direction and defines what needs to be done.
Scheduling is about the tactics that need to be used to reach the goal defined in the plan.
Another way to differentiate between planning and scheduling is to understand the timescales they work on. Planning generally involves long-term strategies covering months and even years or medium-term tactical planning with a time horizon of a few weeks. Scheduling, however, reacts to real-time production and supports immediate and short-term decisions.
With the basics out of the way, let’s look at the current approaches to planning and scheduling.
Current planning and scheduling systems
Planning and scheduling systems naturally emerge when you start a business. This could mean an ad hoc schedule made by the shop floor manager every day. Or, more often than not, it is an excel spreadsheet.
Just to state the obvious, these solutions don’t work well when you want to expand your business.
With human-based solutions, the inevitable human errors could hold you back from achieving the goals that you set for yourself. Besides, when it comes to human-based solutions, there is no good way to track performance except by looking out for the big indicators. Whereas spreadsheet solutions become extremely messy at the drop of a hat. Eventually, they become too cumbersome and unwieldy because they contain too many things.
Another common system that is used when it comes to planning is material requirements planning (MRP). Let’s pit MRP against an APS and see why APS systems are better.
The difference between APS and MRP
Material requirements planning (MRP) systems are among the earliest software-based inventory management systems and, as such, are predecessors of APS systems. MRP systems help develop a production plan for finished goods by defining inventory requirements for components and raw materials.
MRP systems work under the assumption of the infinite capacity of production. When it comes to planning, this assumption is the Achilles heel of MRP systems — they can’t handle constraints and changing priorities.
Advanced planning and scheduling systems were built to handle situations exactly like this. APS systems employ advanced mathematical concepts such as Linear Programming, Constraint-based Programming and also take heuristics into account to accommodate constraints and competing priorities. Additionally, manufacturing ERP systems, like Katana, come with great features like real-time master planning, which allow you to reprioritize your orders while automatically rescheduling the workflow.
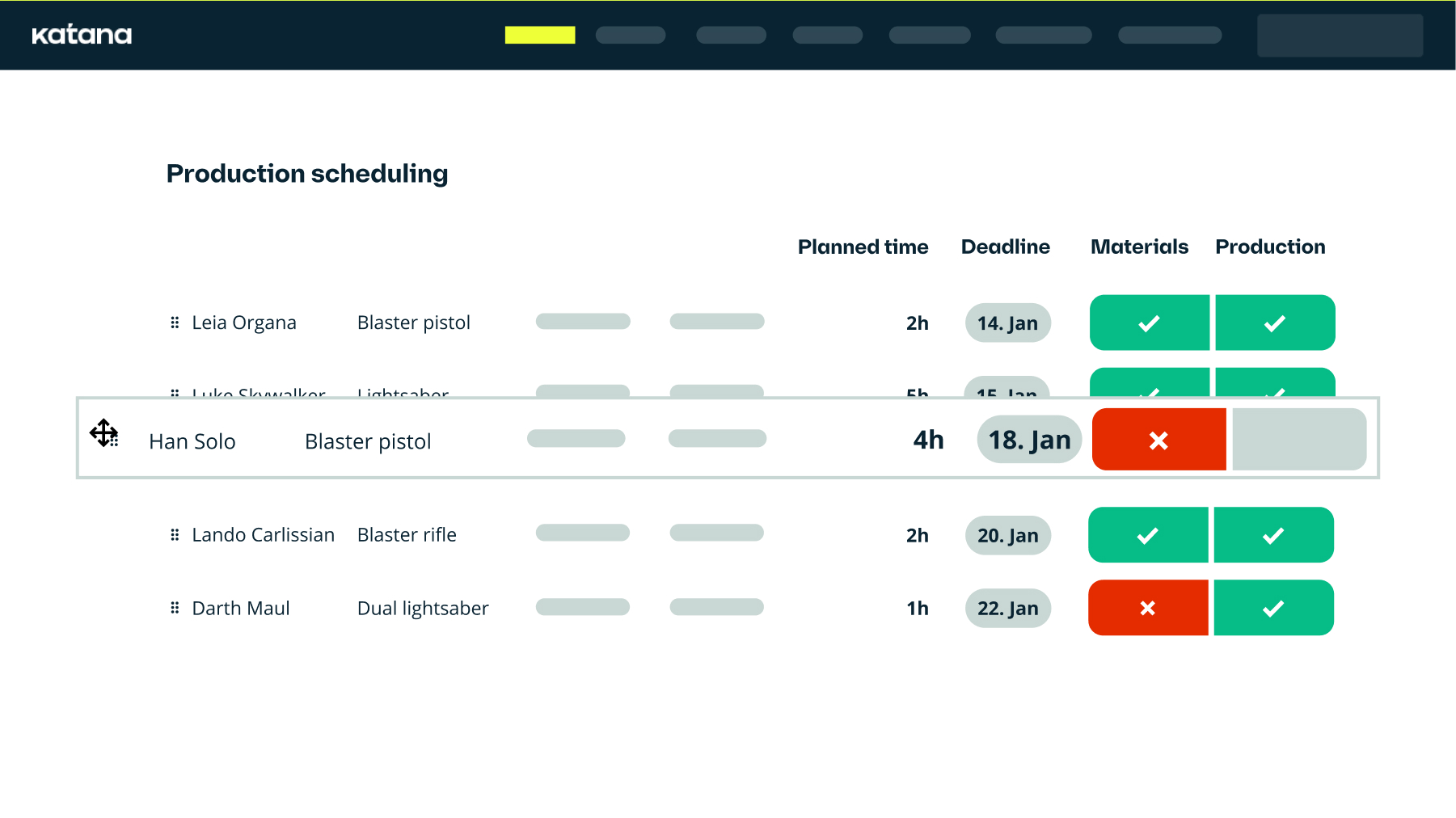
The need for APS systems
To demonstrate the need for better solutions, let’s look at automobile manufacturing and car manufacturing in particular.
An average car has about 1800 large parts. However, if you count all the parts down to the nuts and bolts, there could be as many as 30,000 parts. Now to put things into perspective, Toyota produced about 8.1 million cars in 2022, which is close to 1000 cars every hour. The only way Toyota could have pulled off a feat like that is to have all of those 30,000 parts at the right place and at the right time for each of the 8.1 million cars that were produced.
As you can imagine, simple planning methods fall short by a mile when it comes to balancing the variables and trade-offs that go into complex manufacturing. To begin with, Toyota would need an advanced planning system to plan capacities and output since it operates globally. It also needs an extremely sophisticated and advanced scheduling program to have detailed work plans and schedules. An APS system takes care of both these requirements.
Now that the need for APS systems is abundantly clear let’s look into the key features of good APS systems.
The 5 M’s of APS
Any advanced planning and scheduling system worth its salt helps you deal with the 5 M-s — Money, Materials, Man, Machine, and Methods.
1. Money
APS systems should help you manage your capital and budgets better. An important feature to look out for here is that the system should integrate well with your accounting software. For instance, Katana has native integrations for Quickbooks Online and Xero, which will help you bridge the gap between manufacturing and accounting.
2. Material
Be it raw materials or finished goods. If you wish to run an efficient operation, you need to know where all the materials are. So, in addition to placing this information at your fingertips, your APS systems should be able to provide you insights about the ebb and flow of the demand for your products — helping you avoid overstocking on the one hand, and stockouts on another.
3. Man
As with materials, you could expand and shrink your production by hiring workers flexibly to optimize your human resources. For instance, if your manufacturing is seasonal, you might need to hire more factory technicians to keep up with the demand during the on-season. Great APS systems also allow you to keep an eye on your HR requirements.
4. Machine
Machines magnify human output, and your APS systems should allow you to be on top of their efficiency and maintenance schedules — allowing you to keep your factory running like a well-oiled machine.
5. Methods
Employing the right production methods can turn the tide on businesses. For instance, implementing cellular manufacturing could improve material throughput and help you develop a versatile workforce. APS systems should allow you to optimize your production methods either directly or indirectly.
APS systems and ERP manufacturing systems like Katana have features that help you take care of these components. Each component is vital, as a sub-optimal pillar will only reduce your production output. For instance, having massive capital, easy access to raw materials, a brilliant workforce, and machinery would be wasted if it produced products through extremely inefficient methods.
With all of that background about APS systems, here is a quick look at the disadvantages and advantages of advanced planning and scheduling systems.
3 disadvantages of APS systems
There are no free lunches, especially in the world of manufacturing. There are a few disadvantages when it comes to advanced planning and scheduling. Some stem from the fact that the knowledge that is required to run a production process resides in someone’s head or is part of tribal knowledge. Often attempts to move from a human-driven process to a semi-automated process fail due to the inaccessibility of this treasure trove of knowledge.
This leads us to the three disadvantages of advanced planning and scheduling systems, namely:
- Difficult and sometimes painful transition process
- Expensive transition and risk of failure
- Complexity of the system can make it difficult to make changes
However, with cloud-based ERP systems like Katana, these disadvantages are mitigated well. You can get a Katana demo and see the features in action and evaluate fit. Additionally, its ease of usage and a simple Getting started guide in the Katana Knowledge Base make sure that the transition is as smooth as possible.
4 advantages of APS systems
The first and foremost advantage is that the advanced math of APS systems takes into account multiple constraints and business priorities and produces achievable production schedules. Plenty of other advantages simply emerge simply as a result of better planning and scheduling.
The advantages of APS systems include:
- Higher margins and profitability
- Efficient use of resources such as human potential, raw materials, and machinery
- On-time delivery of products
- Reduced waste and leaner operations
Katana ERP manufacturing software
The ultimate tool for managing your entire business all from one platform. Katana enables users to implement a real-time dynamic production planner for complete control of their manufacturing.
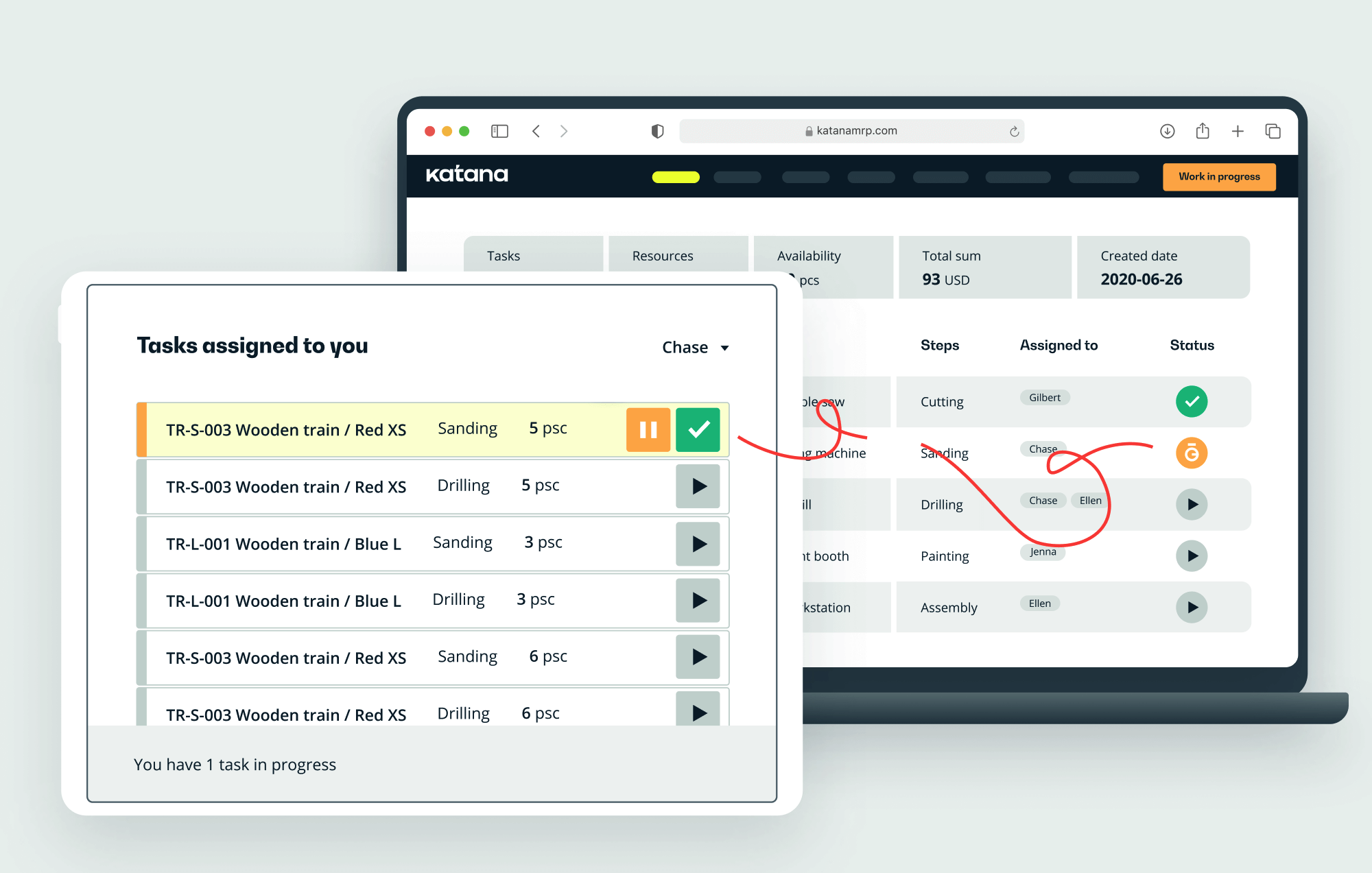
Simplify your planning and scheduling needs with Katana
Your business’ success depends on your adeptness at creating resilient plans and robust schedules. However, as noted in the article, traditional tools begin to falter as the business scales, leading to lost efficiency. Avoid well-known pitfalls with a manufacturing ERP like Katana and see your planning and scheduling needs turn into child’s play.
That’s not all — Katana also comes with great features like live inventory management and powerful integrations, providing you with end-to-end inventory traceability and amplifying the effectiveness of the tools you already use.
Get a demo, and see why 1000s of manufacturers are already using it.
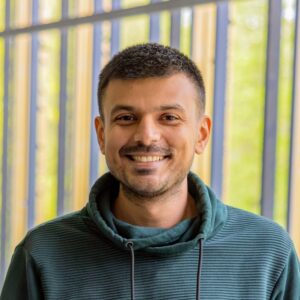
Tejas Shah
Table of contents
Get inventory trends, news, and tips every month
Get visibility over your sales and stock
Wave goodbye to uncertainty with Katana Cloud Inventory — AI-powered for total inventory control