Shop floor planning and scheduling
Shop floor planning and scheduling are crucial to maintaining a healthy and successful production line. Discover how you can improve your processes.
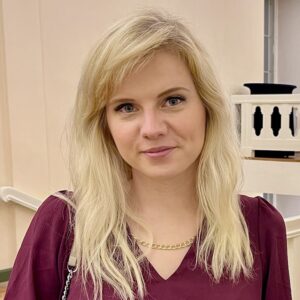
Laura Timberg
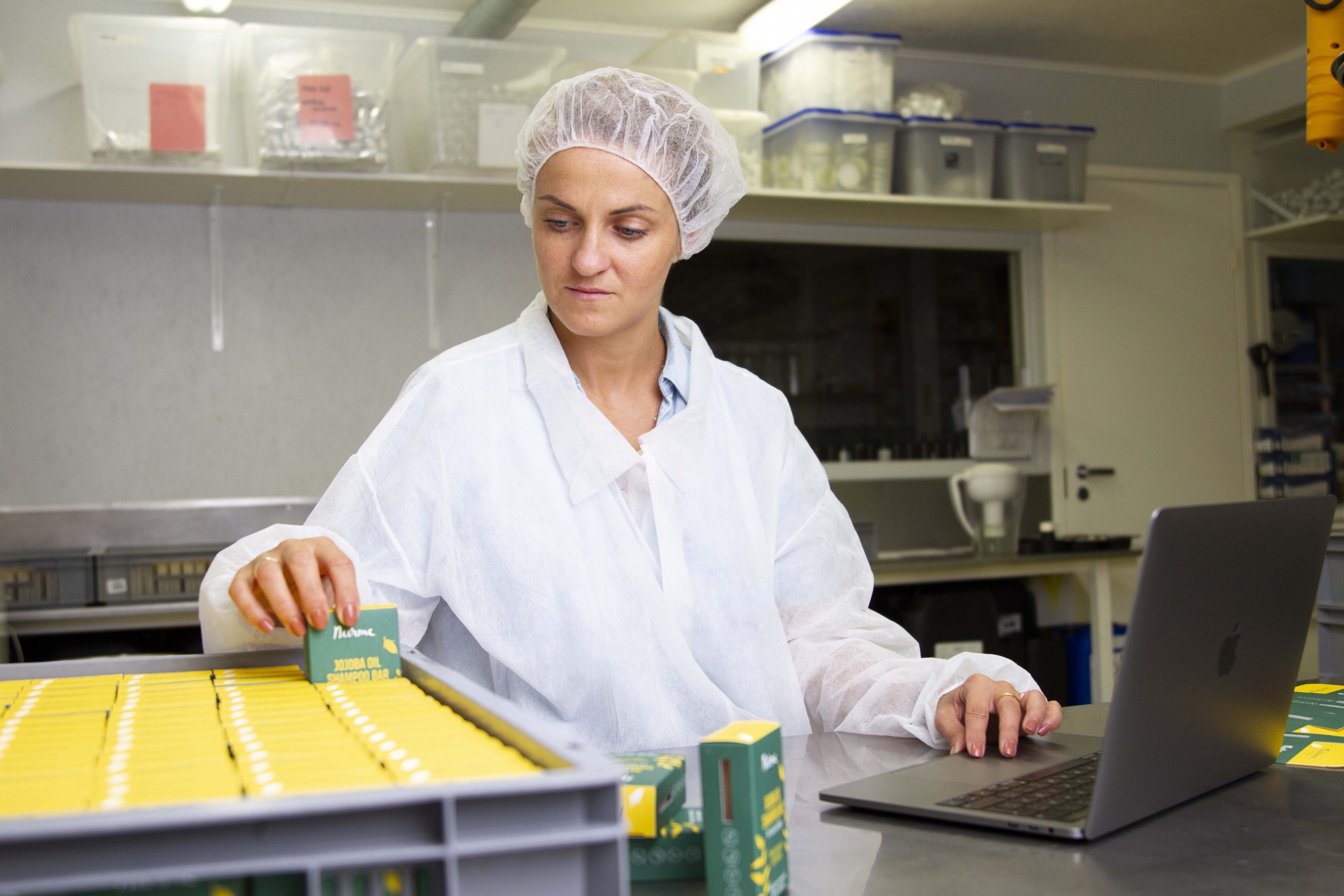
Taking a step into the unknown is often considered bravery.
And maybe that’s true. But, when it comes to manufacturing, sending your employees out without a plan is a recipe for disaster. That’s why having a system in place is essential to help you carry out production tasks.
However, the even bigger question is how you plan, implement, and monitor the progress of tasks.
In this article, we explore the world of shop floor planning — the advantages, the different aspects you need to consider, and how you can implement it into your business.
Live overview of your shop floor
Stop. Drop. Open up Shop (Floor App). Get a real-time overview of your business and gain the visibility you need to make decisions in real time. Request a demo today.
What is shop floor control?
Shop floor planning and control is the process of using methods and tools to track, schedule, and report the status of work-in-progress (WIP) manufacturing from your floor-level, giving you a clear channel of communication between your operators and managers on the production line. Shop floor activity control is an essential tool for:
- Creating a master production schedule
- Setting production priorities
- Minimizing WIP and finished goods inventories
But what is the workflow of shop floor manufacturing planning?
What are the three phases of shop floor control?
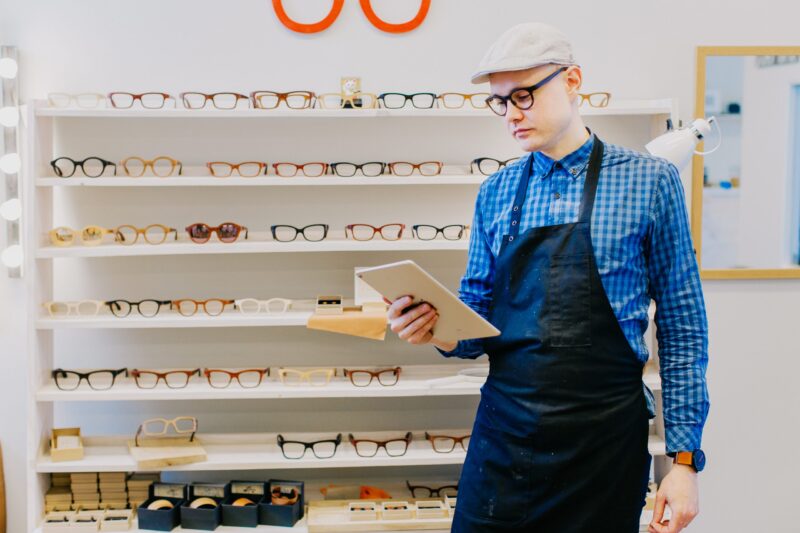
Moody teenagers aren’t the only ones going through phases.
Shop floor planning concerns the management of your operations planning, inventory, equipment, and workers. Your shop floor planning and control will go through these three phases:
- Order release
- Order scheduling
- Order progress
1. Order release
Your master production schedule will help you determine which manufacturing order (MO) needs to be generated first. From there, the order release document will inform the shop floor management of the resources and manufacturing processes needed to complete the order.
2. Order scheduling
Once the order release has been generated, shop floor applications will schedule the production of the order while providing you with a detailed workflow of the manufacturing route the order will pass through.
The order scheduling phase will explain:
- The workstations the order passes through
- The materials and quantity needed for the order
This allows managers and employees to understand what needs to be done, who needs to do it, and how it needs to be done.
3. Order progress
Manufacturing managers create a shop floor schedule and monitor the progress of orders and other manufacturing operations within your business.
Order progress gives you breakdowns of:
- Raw materials, work in progress, and finished manufacturing orders
- Individual orders along the production line
- The employees who are working, about to work, or have worked on an order
So, that’s the workflow in short. But why should you even bother with all this?
What is the importance of shop floor control?

Using shop floor management boards gives you access to automated manufacturing and provides more control and visibility over your production lines and operators.
Let’s look at the advantages of shop floor control.
1. Real-time information
Shop floor planning and control software gives you real-time updates immediately, allowing managers and operators to keep up with the progress of manufacturing orders passing through the factory.
This live data from your shop floor planning software allows you to quickly identify problems and make changes to your production schedule on the fly.
2. Reduced setup cost
Lean shop floor management practices will help you locate areas along your production line that need improvement, such as bottlenecks in manufacturing.
Improving the efficiency of your manufacturing will allow you to:
- Reduce your manufacturing lead time
- Reduce your manufacturing overheads
- Increase your profit margin by avoiding delays and minimizing unexpected issues
3. Resource planning
Another advantage of shop floor control is how easy it is to allocate resources to other tasks, as the software can handle the production process efficiently.
Shop floor planning software helps you automate your resource management and workflows. And, because it allows you to perform these tasks quicker, it removes the need for inefficient spreadsheets.
Pro tip: For more information on resource planning, feel free to browse our ERP guide, describing the different types of ERPs, how they work, and why you should seriously consider using one in your business.
4. Problems and variations become transparent
Shop floor management gives managers and operators a comprehensive overview of relevant data and manufacturing orders in production. This practice creates a transparent work environment where all teams have access to the same information while working towards a mutual goal.
It means, everyone can start their workday with a complete understanding of what is happening along the production line. Cost transparency can increase profitability to around 21%, increasing profitability from about 2.3% to 2.8% per customer.
5. Direct support of management
Everyone within the team can communicate with each other quickly and efficiently, allowing you to solve issues faster and keep production going without delays.
Having your shop floor data centralized and easily accessible means wasting less time trying to explain issues or giving feedback to other departments when addressing a topic.
6. Key performance indicators (KPI)
A skilled and experienced team is crucial for a successful production run. Shop-floor applications allow you to communicate with your team about performance levels and help improve in underperforming areas.
7. Quality control
Shop floor control software gives your managers the ability to:
- Track batch failures
- Trace material waste
- Sperate failed goods from the rest of the inventory
Your operators will easily handle different units of measure and report material waste while identifying whether batch failures are recoverable or not.
8. Price products fairly
As already mentioned under KPIs, improved analytics and reporting means you can gather data collection on manufacturing aspects such as:
- Operators (working hours, break times, downtime)
- Manufacturing costs
- Production lead time estimations
- The workload a workstation can take and its capacity
This information will help you better understand how many products you can produce at any given time and the value of those consumer products.
9. Project-based purchasing
Shop floor planning is perfect for businesses that practice bespoke manufacturing. Although shop floor software does support both make-to-order (MTO) and make-to-stock (MTS), the software will help you with material procurement for:
- Custom projects
- MTO
- Assemble-to-order (ATO) jobs
However, it doesn’t have to be one or the other. Shop floor planning software can help you switch between workflows for individual projects.
10. Paperless manufacturing
The latest trends and predictions show that customers are more informed than ever before and want to purchase goods from businesses that practice green manufacturing.
Adopting shop floor planning on your production lines allows you to achieve a paperless manufacturing workflow by giving you the tools to:
- Schedule production
- Track progress
- Manage your entire business from a smartphone, tablet, or computer
So, that’s the 10 advantages of shop floor control. But, what are the other aspects you need to be aware of with shop floor planning?
Production activity control
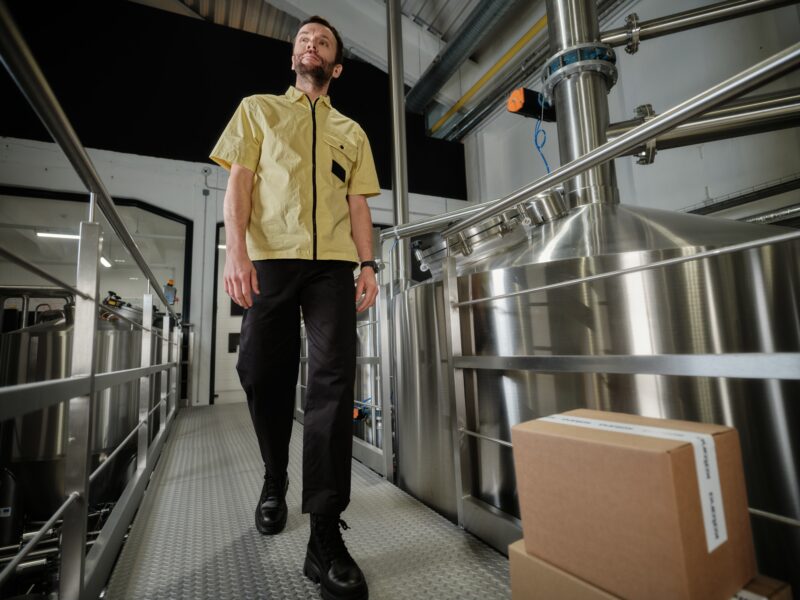
Production activity control in shop floor planning is the process of coordinating your:
- Manufacturing resources
- Productions orders
- Schedules
- Material consumption
Production activity control is responsible for executing your plans and providing proper guidance on how to complete production.
Shop floor management allows you to analyze which workloads you should prioritize for a workstation and the ideal capacity that a workstation can take before it becomes under or overworked.
Material requirement planning system
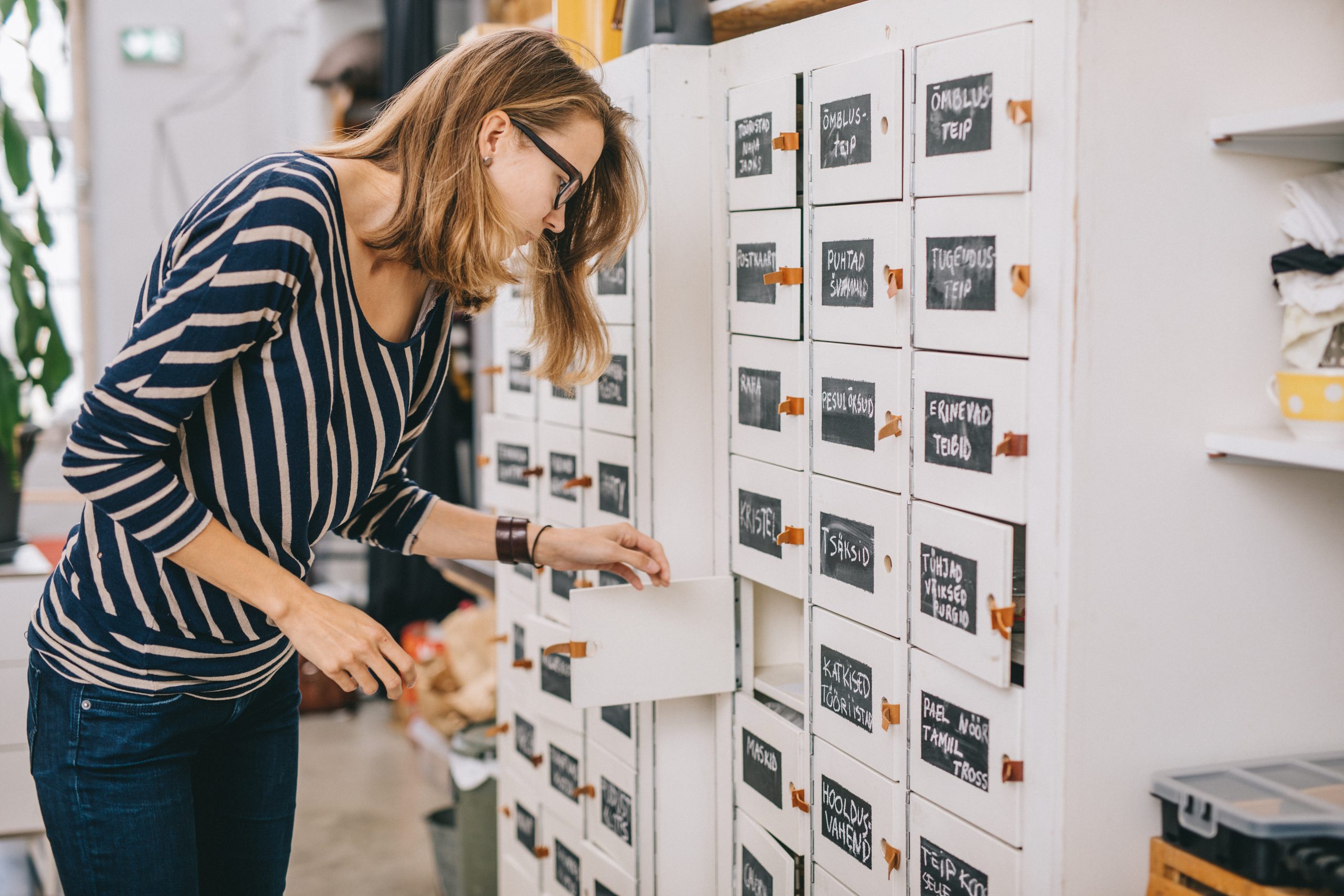
Material requirement planning (MRP) software is essentially an inventory management tool for improving productivity for manufacturing businesses.
Essentially, the purpose of MRP systems is to tell you the number of materials and finished goods you need in order to meet demand and at what point you’ll need those quantities. Your MRP will be able to figure out these quantities by using the following data.
Bill of materials
Your bill of materials will detail the materials, components, sub-assemblies, and manufacturing costs associated with making a product.
Production plan
Once you’ve set up your resources and operations, the material requirements planning and execution system will formulate a plan for a manufacturing order so you know the:
- Routing
- Labor needed
- Machines and tools needed
Production planning and scheduling software
Maximize productivity and get a floor-level overview of your business with software designed to give you total shop floor control. Katana tracks time and materials spent on production and provides you with the insights you need to grow.
How to improve shop floor planning and control in your business?
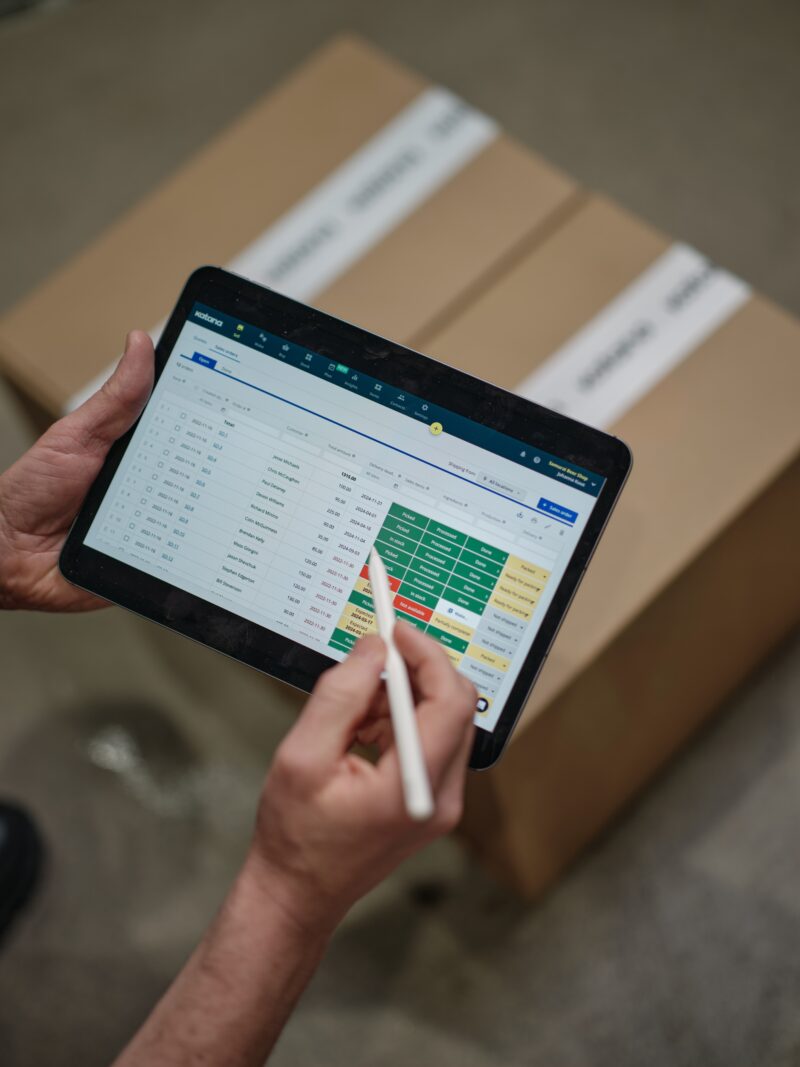
Although manufacturing shop floor planning and control can be performed via spreadsheets or a Kanban board, it takes up time and resources that could be better spent elsewhere in your business. By using cloud manufacturing software, you can make shop floor management lean.
Automation
Automated manufacturing processes will help save you time and money by improving the accuracy of your shop floor control.
Collecting data
Using automated tools will allow you to collect in-depth data, providing you with an overview of the shop floor production processes.
Scheduling
Streamline how you develop your schedules with automated production scheduling and have materials and resources assigned to manufacturing orders automatically.
Tracking
Have a centralized overview of your entire shop floor in manufacturing to view:
- Inventory management — from shop floor to distribution center
- Production planning
- The progress of your floor workers and tasks
So, here is how you can easily and quickly improve your shop floor planning and control, but what about scheduling?
5 ways to improve your shop floor scheduling
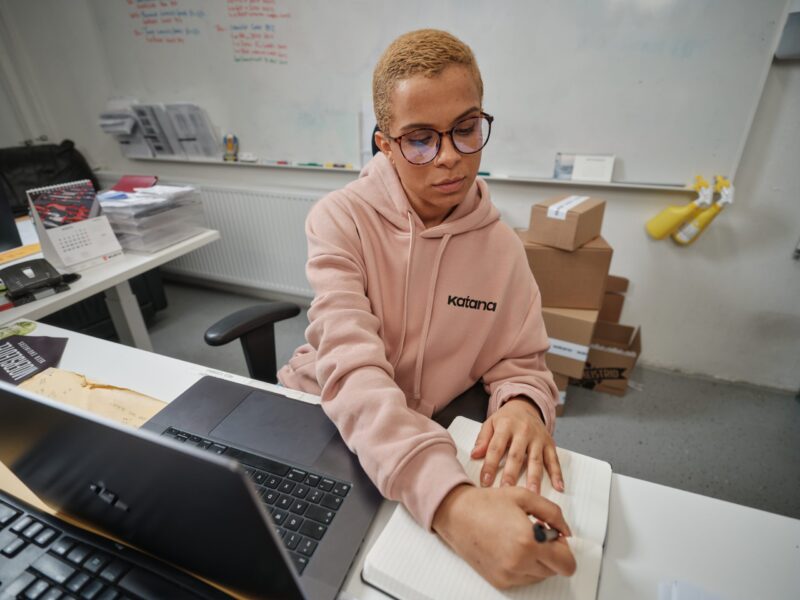
Different manufacturing processes also need different approaches on the shop floor.
Shop floor scheduling is taking all your manufacturing resources and coordinating them into a master production schedule (MPS), letting your managers and operators know:
- What needs to be done?
- Who needs to do it?
- When does it need to be done?
Perfecting your shop floor scheduling is essential. Otherwise, you end up with inefficient processes, costly mistakes, and disgruntled customers. So, to minimize stress and maximize success, let’s look at some guaranteed ways to improve your shop floor schedule and overall efficiency.
1. Raw material inventory management
To follow your shop floor scheduling, you’re going to need raw materials and components ready to complete manufacturing orders.
But that doesn’t mean stocking up on inventory just in case orders come in because that takes up valuable storage space and drives up your carrying costs.
This is where raw material inventory management comes into play.
By understanding how much inventory you need, you can plan your shop floor scheduling to include:
- A realistic output of finished goods
- The manufacturing lead times
2. Demand planning
Another way to improve your shop floor scheduling and even your inventory management is to do some demand planning.
Demand planning allows you to make an educated prediction on future demand by looking into:
- Seasonality
- Your historical sales
- Trends
- Customer behavior across the industry
Basing your shop floor schedule on accurate and personalized data helps you better plan your production, anticipate future orders, and be prepared for potential spikes in demand.
3. Real-time tracking
The only true way to understand what’s happening on your shop floor is to get a system that can provide you with a live overview of production.
With shop floor scheduling software and real-time tracking, you can monitor and make business decisions regarding:
- Inventory
- Production progress
- Employees status
Getting this information quickly and updated constantly means you can easily:
- Reduce waste
- Minimize downtime
- Maximize output
- Read your manufacturing overheads
Pro tip: If you’re interested in learning more about inventory management, we recommend checking out our inventory management guide and downloading the ebook for a more comprehensive overview.
4. Flexibility
In manufacturing, you can have your shop floor planned to the last detail. But life is unexpected, and so is manufacturing. At any moment, issues can arise which can affect production, for example:
- Late deliveries of raw material
- Employees unable to come in and finish a job
- An important order comes through and puts all other projects on hold
Problems will inevitably arise. Your shop floor scheduling needs to anticipate these problems and adjust production accordingly so you can continue making your products and manufacturing doesn’t stop because of a little hiccup.
5. Using a reliable system
You can implement the majority of the points listed above manually. But to effortlessly implement these points, manage your business, and optimize production, you’ll need to set up a reliable and automated software system.
A shop floor scheduling software is going to give you:
- Total visibility
- Improved reporting and planning
- Improved efficiency
Software can help you increase your shop floor scheduling by allowing you to break down complex processes, avoid data re-entry, and give you the tools to improve everything else from production to delivery.
Katana + shop floor planning and scheduling
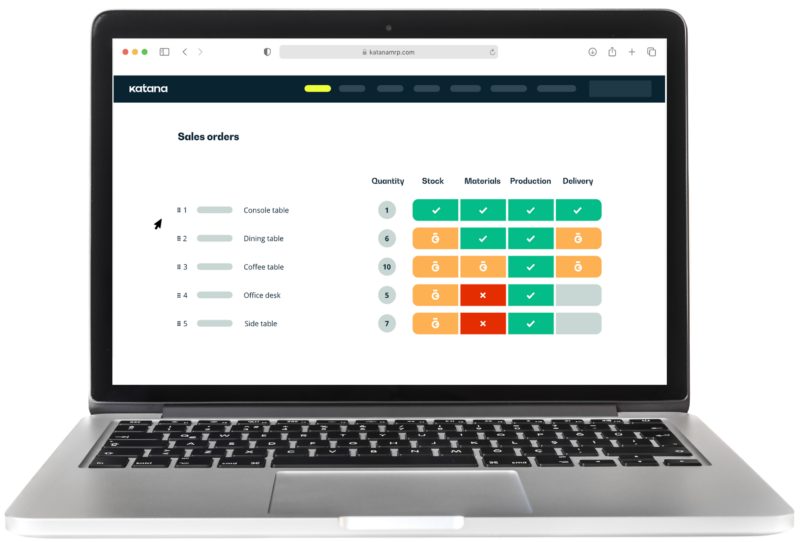
Katana is an all-in-one solution for modern businesses looking to get more control over:
Cloud software is built to support your business by giving you the tools you need. Let’s go over a few of them, specially designed to help with your shop floor planning and scheduling.
Production planning
Manufacturing orders are automatically split into tasks, and those tasks are automatically assigned to operators and resources. However, managers can easily transfer and reassign tasks if the workflows need to be changed for some reason.
Task management
Managers can assign tasks to operators and track the progress and time consumption of each assignment.
Operators can:
- Receive tasks
- Start tasks
- Pause tasks
- Complete tasks
Time tracking
Improved time tracking gives you a better idea of your shop level:
- Working hours
- Break times
- Downtimes
- Set-up time
- Clean-up time
Analytics and reporting
Finally, Katana’s shop floor planning features allow you to gather data on your business performance, so you can better understand:
- Price estimation based on actual time
- Product lead-time estimation
- Shop floor employee efficiency
- Labor costs
Katana Shop Floor App
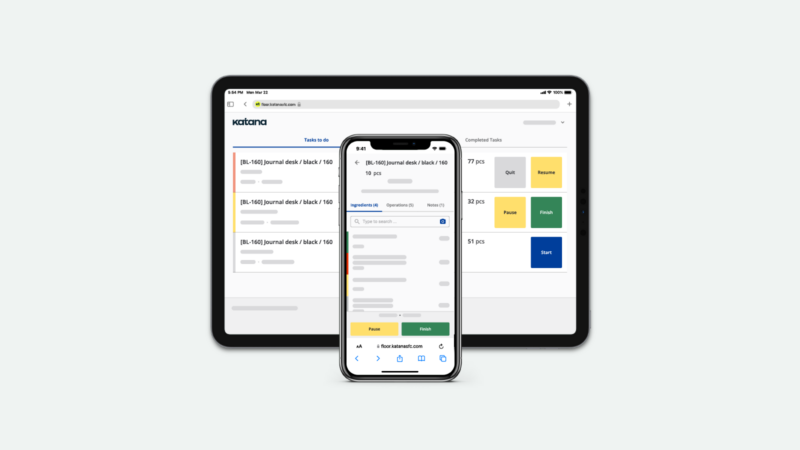
Katana’s Shop Floor App supports you with total shop floor control with tracking, scheduling, and reporting to make the best decisions in real time.
Easy accessibility on mobile and tablet devices allows your team to see, edit, and finish their assignments in the comfort of their workstations. The app tracks their progress as well as the time spent on each task, giving shop-level managers visibility into operational efficiency.
Here are three ways you can use the Katana Shop Floor App to take your business and manufacturing processes to the next level.
1. Round-the-clock control over your shop floor
Anywhere or anytime you need to check into your business is possible with cloud-based access.
Using Katana’s Shop Floor App helps you with the most expensive and time-consuming part of manufacturing — managing the operators making products on the shop floor. Katana’s Shop floor control software allows you to track progress with sales and production orders in real time, giving you a virtual window into your manufacturing floor.
This allows you to spot delays, mistakes, or a decrease in material availability long before they happen — thus avoiding missing deadlines or failing to meet the high demand.
2. Seamless production
A smoothly operating shop floor is essential to success.
With Katana’s Shop Floor App, each production employee or operator has a dedicated account with a clear task list. You can add an operator as a default assignee to a resource, for example, a paint booth or assembly station, so all operations using that resource will automatically be assigned to that operator.
In addition, the Shop Floor App allows you to instruct your operators without needing an avalanche of paper flooding the manufacturing space. Flexibility is the keyword here — adding instructions to manufacturing orders is simple, and your operators can access any new info in real time. You can also add hyperlinks to the manufacturing order’s additional info section so operators can access technical sketches, drawings, specifications, or more detailed work instructions.
3. All-in-one system
The Shop Floor App is essentially an extension of Katana.
Managers, sales reps, and shop floor employees have access to the same data and information to keep their operations in sync.
All changes made in the Shop Floor App are instantly displayed in Katana’s main platform, thus giving everyone in your organization the knowledge needed to make the right business decisions at any given moment. The same goes for vice versa — all changes made in Katana appear immediately in the Shop Floor App.
And there we have it — everything you need to know about shop floor planning and scheduling. If you want to improve your shop floor planning, Katana can help you.
Request a demo today and see how the shop floor system benefits your business. We hope that you found this article useful, and if you have any questions, please don’t hesitate to get in touch and we’d be more than happy to help.
In the meantime, feel free to browse this interactive tour of Katana.
And until next time, happy manufacturing.
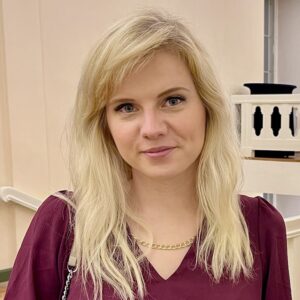
Laura Timberg
Table of contents
Get inventory trends, news, and tips every month
Get visibility over your sales and stock
Wave goodbye to uncertainty by using Katana Cloud Inventory for total inventory control
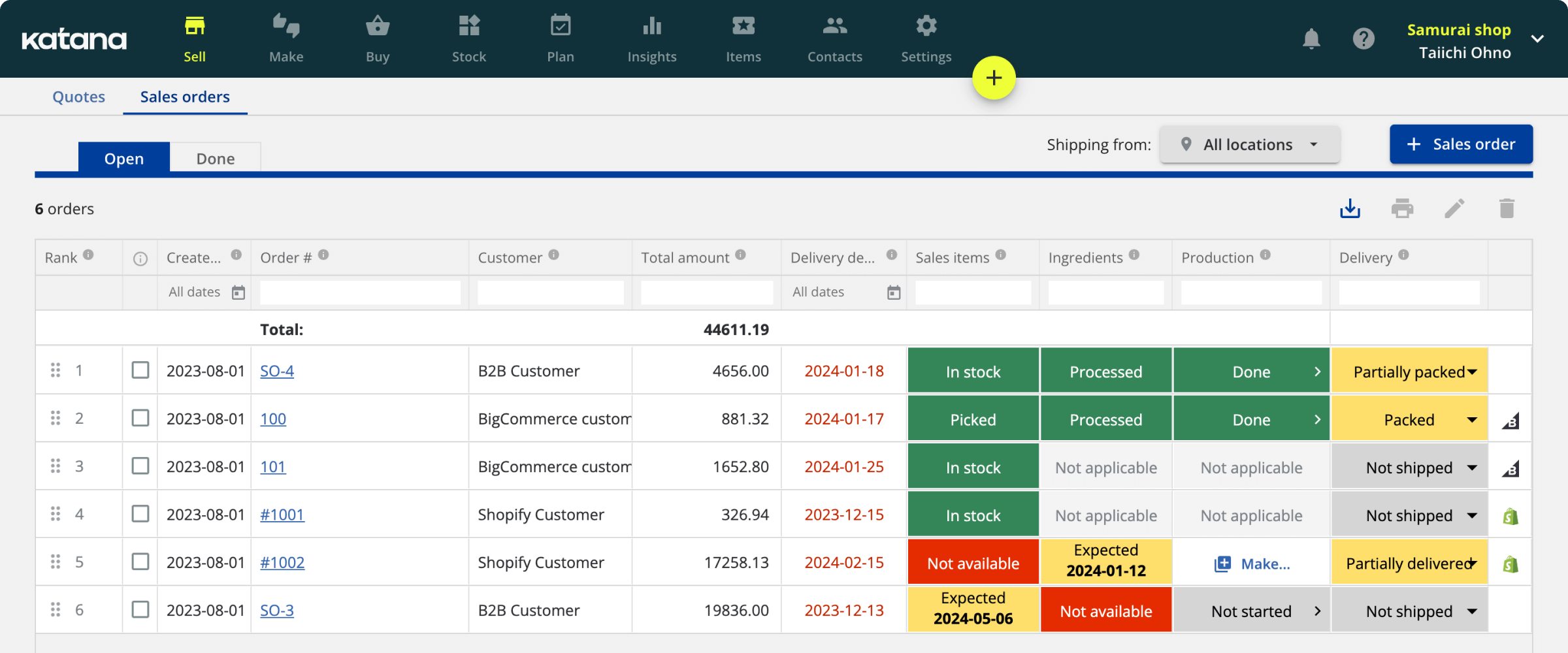