Forward scheduling vs. backward scheduling for manufacturers
Here we explain the differences between forward scheduling and backward scheduling. Which is the best method for manufacturers looking to organize their workflow?
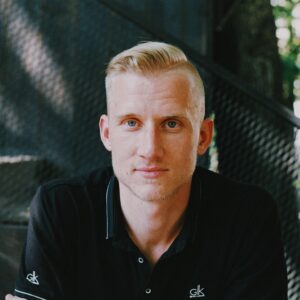
Henry Kivimaa
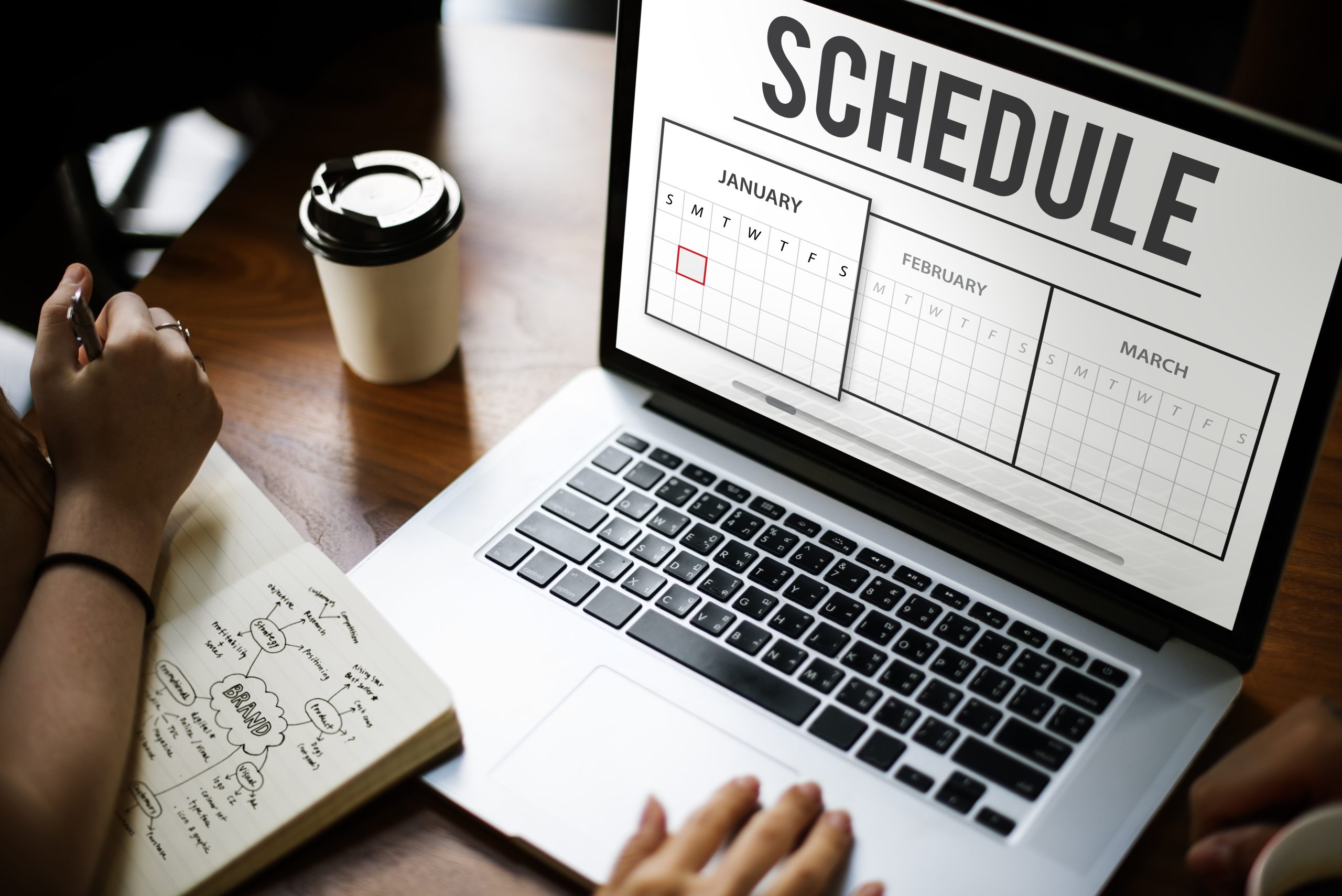
You’re back in school, and Mrs. Smith has dropped an assignment on your desk.
Do you:
- Do your homework as soon as possible
- Do your homework closer to the deadline
If you complete your tasks as soon as possible, you have the security of knowing your work is done long before the due date. This is the basic principle of forward scheduling.
But what happens if you’re a day into your assignment and Mrs. Smith gives you another assignment that needs to be ready by tomorrow? Well, this is when the student who chose to work closer to the deadline shines.
Leaving the first assignment until the last minute allows you to make sure you’re organized, meaning you can be more flexible when prioritizing your workload.
This is the basic principle of backward scheduling.
Let’s go through these scheduling tactics so you can get a better understanding and see which is the best for you.
Why is it important to schedule?
When scheduling, you should efficiently utilize your resources to complete operations within the specified time frame. Scheduling aims to make your manufacturing process flow at maximum efficiency.
According to some studies, poor scheduling leads to employees multitasking, which drops productivity by 40%.
If done correctly, it will allow you to fulfill your orders most effectively, helping you avoid interruptions, delays, and stress. As businesses adopt the principles of lean manufacturing and just-in-time inventory, they also put more emphasis on scheduling. The two main concepts are forward scheduling and backward scheduling.
But what are these two scheduling practices?
What is forward scheduling?
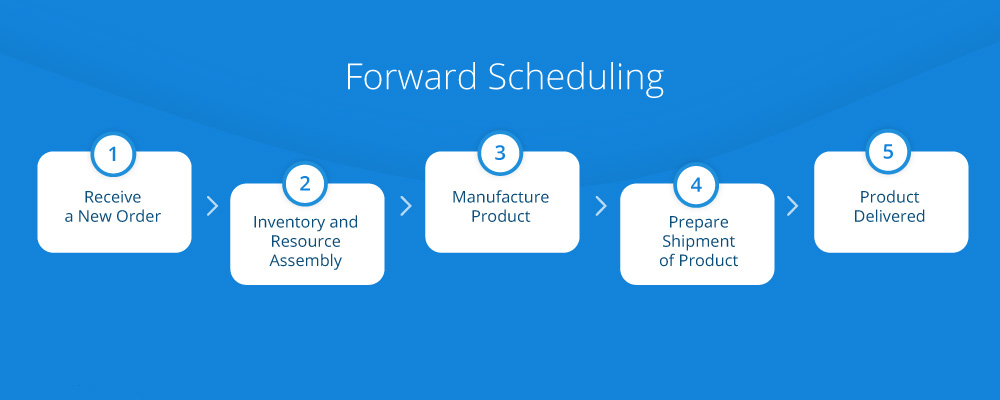
Forward scheduling is when businesses manufacture their items as soon as possible before the due date. This is achieved by scheduling the relevant resources and materials as soon as they’re available.
Let’s illustrate this with an example.
Suppose a customer orders an item with a delivery date that is six days away, and the lead time for the item is three days. Production begins as soon as the manufacturing order is created, and the item should be ready three days before it is due (assuming there are no snags along the way).
As you can see, some orders can be fulfilled long before they must be dispatched, meaning you have to hold the products in inventory until you can send them.
What are the advantages of forward scheduling?
There are two notable advantages to using forward production:
- High labor utilization rate
- Minimized slack time
Let’s explore these in more detail.
1. High labor utilization rate
Because you’re working on completing tasks immediately, you can maximize the use of your human resources and design a workflow that gives you the highest output without straining your workforce.
2. Minimize slack time
Similar to having more flexibility with your workforce, you can also redistribute your resources during downtime to ensure time is fully utilized on the work floor. This also allows you to respond to a high influx of orders by shifting your resources to meet these new orders.
Download the manufacturing ebook for small manufacturers
Learn how to organize and scale your manufacturing.
What are the disadvantages of forward scheduling?
Disadvantages of forward scheduling are:
- Materials being consumed in advance
- Increased lead times
- Difficult to rush production
- Meeting deadlines on time decreases
- Difficult to schedule customized goods
1. The material is consumed in advance
Since you’re working ahead of the deadline, your material will be used up sooner. So, if demand does increase, you will be playing catch up as you restock the material shortages.
2. Lead times increase
The same applies to your manufacturing lead time. As you have scheduled productions to your capacity, you won’t have much room to increase your workflow speed when new/more orders come in.
3. Difficult to rush production
You can already see a snowballing effect of issues with this workflow. All your resources will have been committed to jobs, meaning no extra resources will be available to focus on a particular job.
4. Meeting deadlines on time decreases
This might not make sense, but because you started early doesn’t necessarily result in an early finish. New orders can create a bottleneck as you wait for materials or resources to free up.
5. Difficult to schedule customized goods
Forward scheduling doesn’t account for some items having a longer lead time than others, meaning you might begin work on a job with a short lead time, delaying production on a bigger job that should be prioritized.
Now, let’s look at the alternative scheduling strategy.
Production scheduling software
Katana’s production scheduling software gives both forward and backward scheduling manufacturers full control of their processes. Katana offers a live look at their operations and automatically schedules production.
What is backward scheduling?
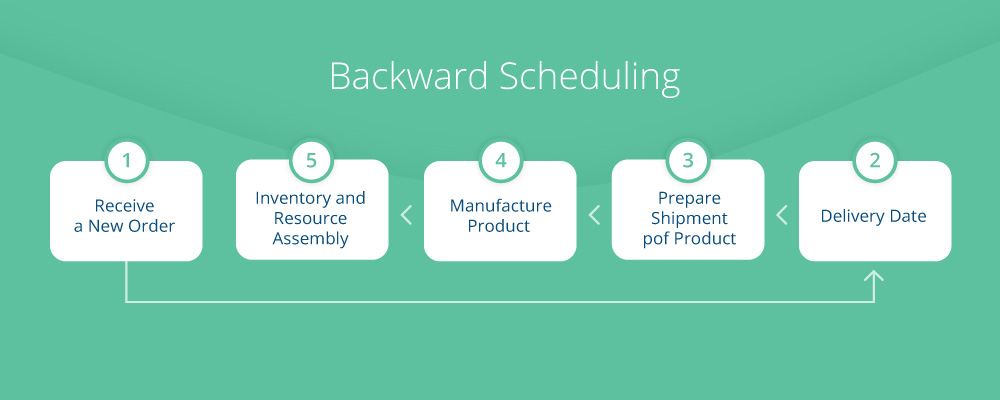
Backward scheduling is when businesses make their items at the last available period before the due date.
The order starts with a planned receipt date or due date, usually defined upon the customer’s order. Then you work backward, allocating resources and materials to the order, and determine the latest start time.
To keep it simple, let’s use the same example as before.
A customer orders an item with a delivery date that is six days away, and the lead time is three days. From the due date, a manufacturer will figure out when they can start manufacturing. So, if the 6th day is the due date and the lead time is three days, the production will begin on the 3rd day.
Using back scheduling can help you identify bottlenecks, monitor resource availability, and have an easier time completing tasks in priority.
What are the advantages of backward scheduling?
The advantages for manufacturers who want to utilize backward scheduling are:
- Lower cost
- Less risk
1. Lower costs
Material and resources will be utilized when needed. Also, they should have no products in inventory (though having some safety stock doesn’t hurt), as production will finish on the due date. This means there will be a lower carrying cost.
2. Less risk
If production speeds need to be increased or decreased, this will be possible as you’ll have resources and material available since it hasn’t been committed to a job yet.
What are the disadvantages of backward scheduling?
Using backward scheduling has the following disadvantages:
- No buffer time
- Hard to fulfill unexpected orders
- Delaying work orders
1. No buffer time
A last-minute rush means last-minute problems. Delaying everything means if a problem occurs during production or even when the production is finished, you have no time to address this issue.
2. Fulfilling orders
The nature of reverse scheduling means it can be difficult to fulfill orders if an unusual or unexpected influx of orders occurs.
3. Delaying work orders
The biggest and most noticeable issue with backward scheduling is that it delays starting work orders. Orders which need to be rushed to meet a deadline get priority, even if it means pushing back the production of other items.
Switching between reverse scheduling and forward production is commonplace, depending on certain situations.
For example, if you’re receiving a huge and unexpected workload. You may need to switch to backward scheduling to sort orders by the longest lead time to meet due dates.
Or, maybe you get different demand levels at different times, and slack means money is being lost. Forward scheduling means you can utilize free resources.
There are other variables you need to consider that will affect whichever scheduling process you decide to use. These factors include:
- The type of job performed
- The nature and availability of resources
- Processing time
- Changeover time
- Your routing manufacturing
- Planned maintenance
So, how are you supposed to conclude which is the best for you?
Which method should I choose?
So, you want to get down to brass tacks, is forward scheduling or backward scheduling the best for your business?
Well, it mostly boils down to what it is you manufacture.
Let’s imagine you make bespoke products. You might receive an order for an item that needs minimal customization and has a relatively short turnaround.
However, you commit resources to make the product, and then you receive an order for a different item that needs much more work.
You’ve now backed yourself into a corner.
You’ve already started work on one project, and now you don’t have the resources to start this other project, which might require you to order more material and delay production.
To understand if you should use forward scheduling or backward scheduling, you need to ask and answer these two questions for yourself:
- What type of manufacturing process does your business follow?
- How do you prefer to organize your schedules?
Ultimately, if this already sounds like too much introspective thinking for you, there is a shortcut to putting together schedules.
Katana — the easiest way to plan and schedule production
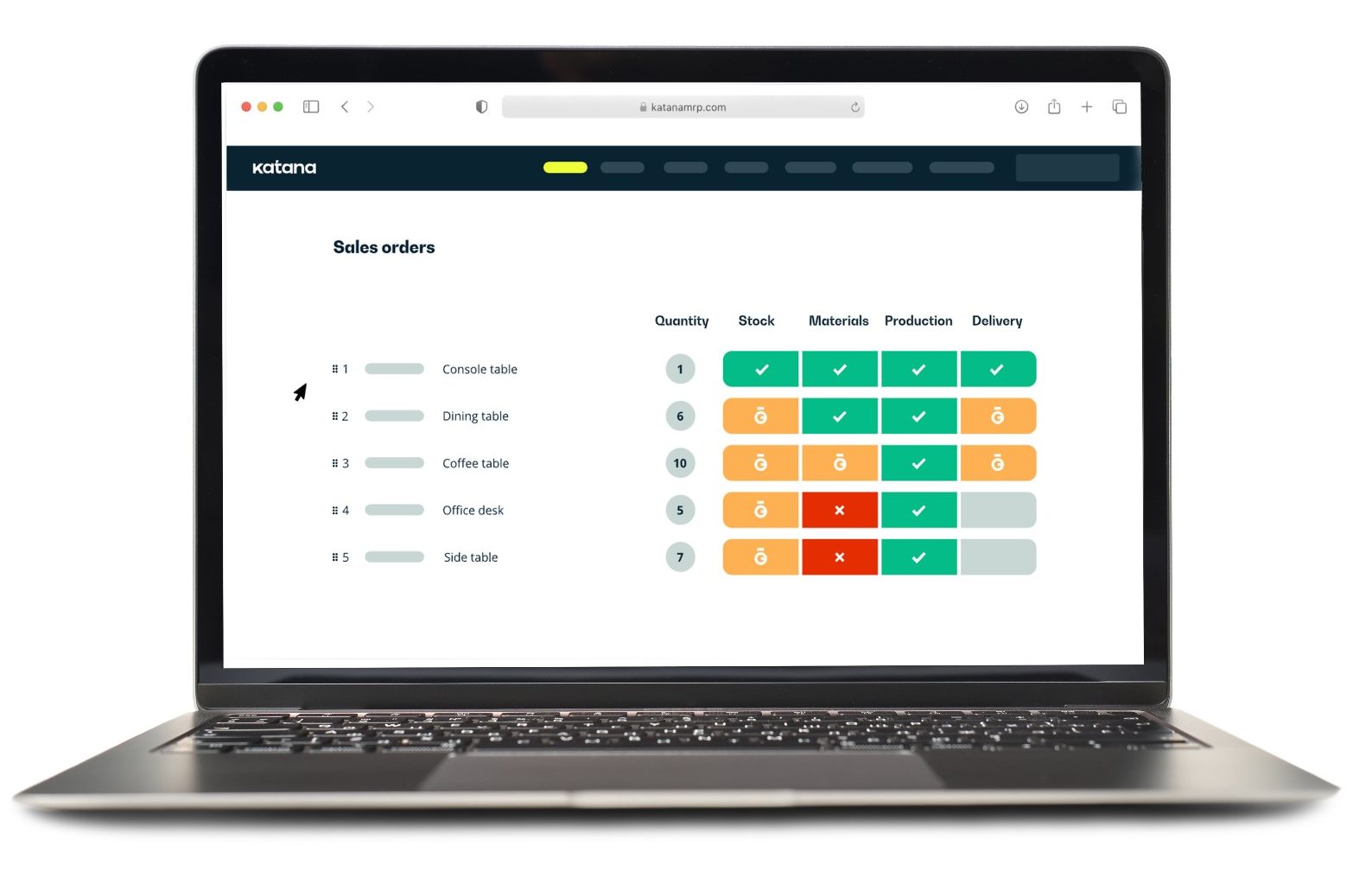
If you cannot decide between forward scheduling and backward scheduling, you’ll be happy to know that you can also opt for flexible scheduling. Flexible scheduling allows you to switch it up depending on the exact order you’re working on.
You can find this flexibility in Katana, a cloud inventory software aimed at scaling manufacturers looking to stabilize the unpredictable nature of an expanding business.
You won’t need to decide the best time to start production, as Katana automatically calculates production deadlines and allocated material to projects for you. Katana helps you maintain a smooth workflow and take production scheduling to the next level.
By integrating Katana into your business, you get to benefit from features such as:
Live inventory management
Real-time inventory management with autonomous updates to monitor stock levels.
Streamlined floor-level management
An intuitive drag-and-drop system lets you reprioritize important orders and track operations progress.
Seamless integrations with other tools
With Katana’s integrations, you can access your other tools, like Shopify and QuickBooks Online, from one platform.
Improved scheduling
Katana considers the available human resources and automatically calculates the job’s production deadlines based on your weekly throughput times. It also takes into account material availability.
The materials are allocated to the oldest order first, but if you have a new order that needs to be finished as soon as possible, simply drag the order to the top of the list. Katana will reallocate all the required resources automatically.
If you wish to manually set different deadline dates, you can switch off the automatic estimation calculations under Configure deadlines. Once you’ve done that, you can go into the manufacturing order and change the dates of each order manually.
Want to see Katana in action? Reach out to our sales team and request a demo to discover how to implement your perfect schedule.
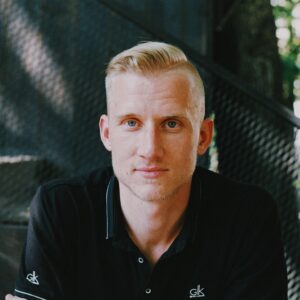
Henry Kivimaa
Table of contents
Get inventory trends, news, and tips every month
Get visibility over your sales and stock
Wave goodbye to uncertainty by using Katana Cloud Inventory for total inventory control
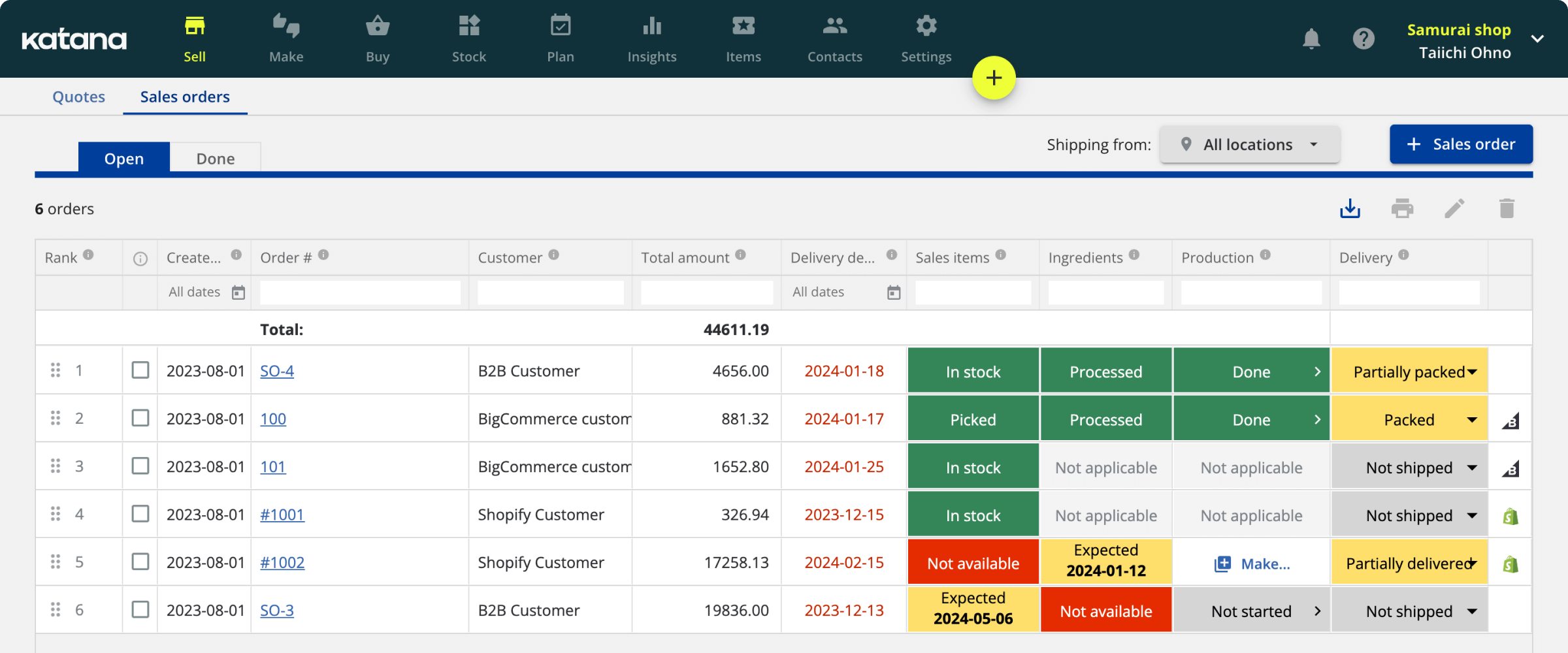