Multilevel BOMs explained for product-making businesses
Manufacturing businesses with a complex manufacturing process involving subassemblies need a multilevel BOM. Here we look into how to make them work.
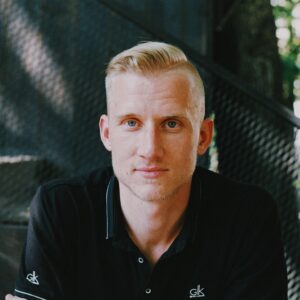
Henry Kivimaa
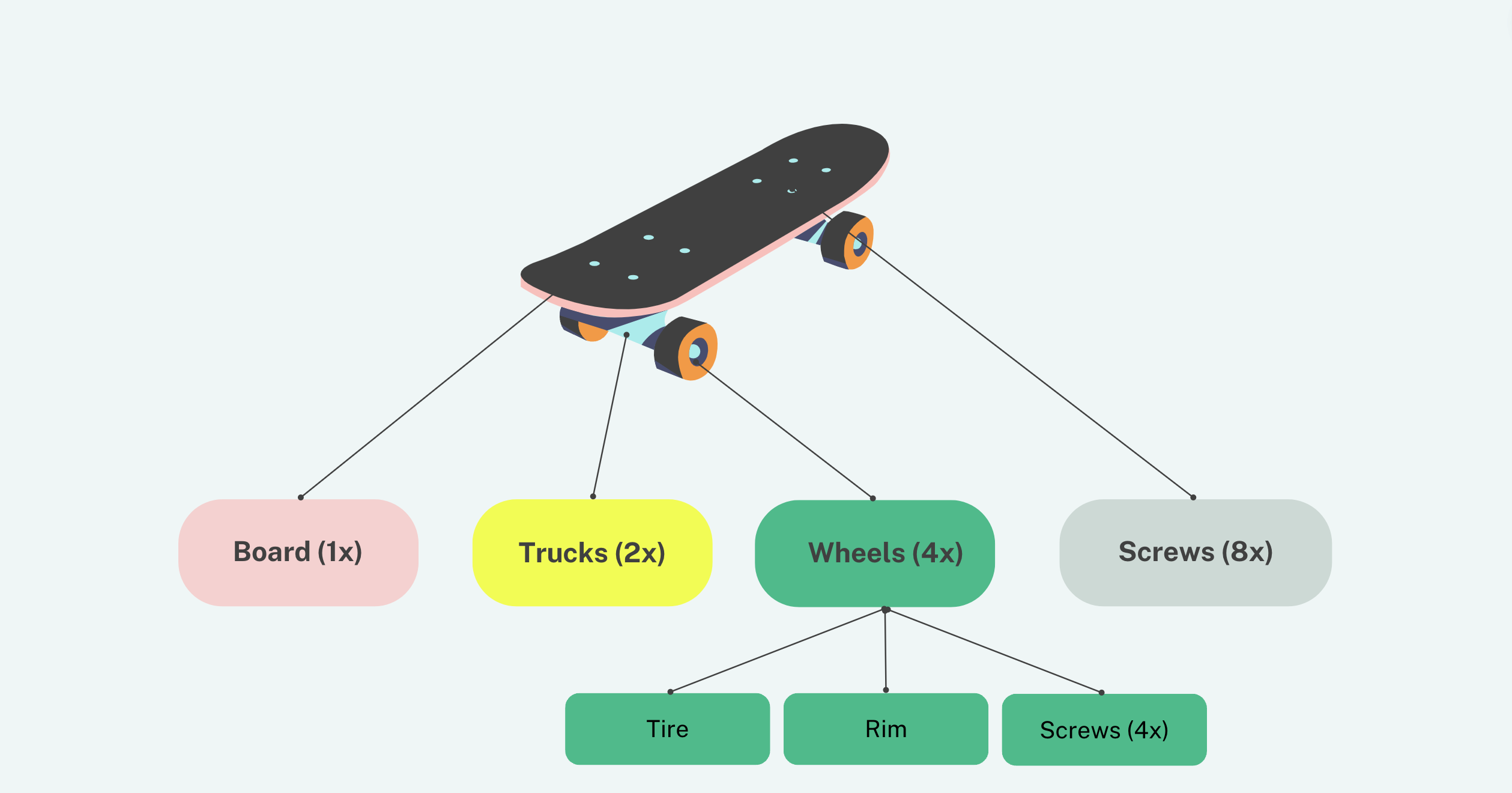
A multilevel bill of materials (BOM), or an indented bill of materials, is a hierarchical structure representing the components, subassemblies, and finished products required to manufacture a particular item. This allows for a comprehensive view of the product’s entire manufacturing process.
The hierarchical BOM structures in your multilevel BOM show your finished product at the top, including your SKUs, part descriptions, quantities, costs, and additional specifications.
Multilevel BOMs are a vital ingredient for manufacturing, especially for manufacturers who use multiple subassemblies to produce their finished goods.
There are different types of BOMs you should be aware of:
- Modular BOM
- Configurable BOM
- Multilevel BOM
This article will explore the world of multilevel BOMs and everything you need to know to get more control over them.
Structure of a multilevel BOM
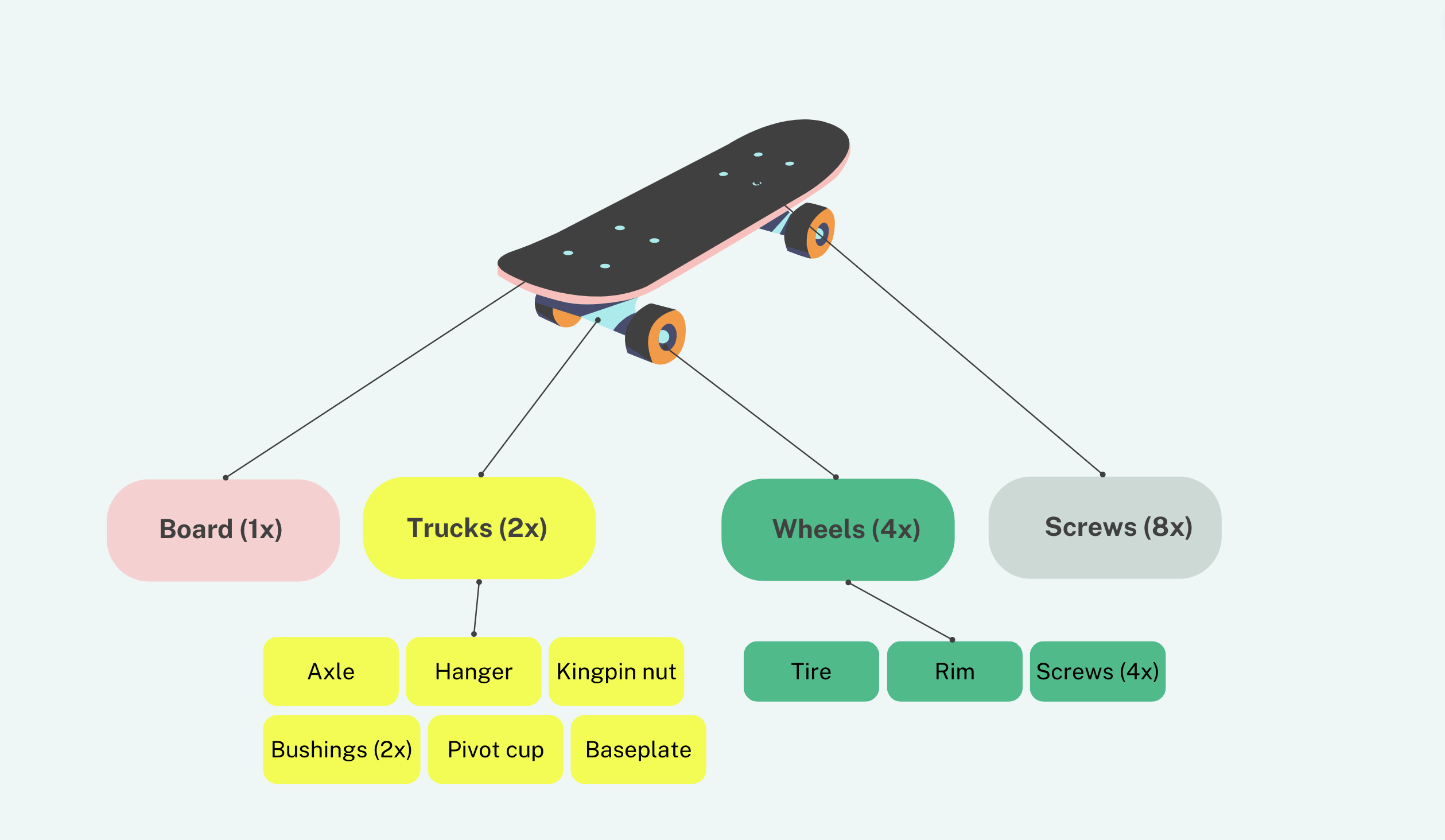
The structure of a multilevel BOM resembles a family tree and maps out all components and subassemblies of a product. Each BOM level will detail all the components that are directly or indirectly used in the production of a parent item.
The purchased parts and raw materials can also be found within a BOM level, which will look like a BOM tree.
Importance and purpose of multilevel BOM
If you want to set up your operation with the smoothest production flow possible, there’s a lot you need to do not to bog down your production later.
This includes finding the best manufacturing routes and optimizing your inventory management. However, one document you need to have ready long before you even begin production is a bill of materials (BOM).
The purpose of having your multilevel BOM is:
- Overview of assemblies — To have greater details and specificity on the parent and subassemblies in the product and their exact relationship between the subassemblies and the finished product.
- Prevent errors when dealing with subassemblies — If your manufacturing business is scaling, it becomes necessary to break down your products into subassemblies and them into smaller subassemblies, components, and so on. This is essential for preventing errors and helping accurately track parts.
We’ll be talking a lot about subassemblies, so let’s go over the definition and look at an example.
What is a subassembly?
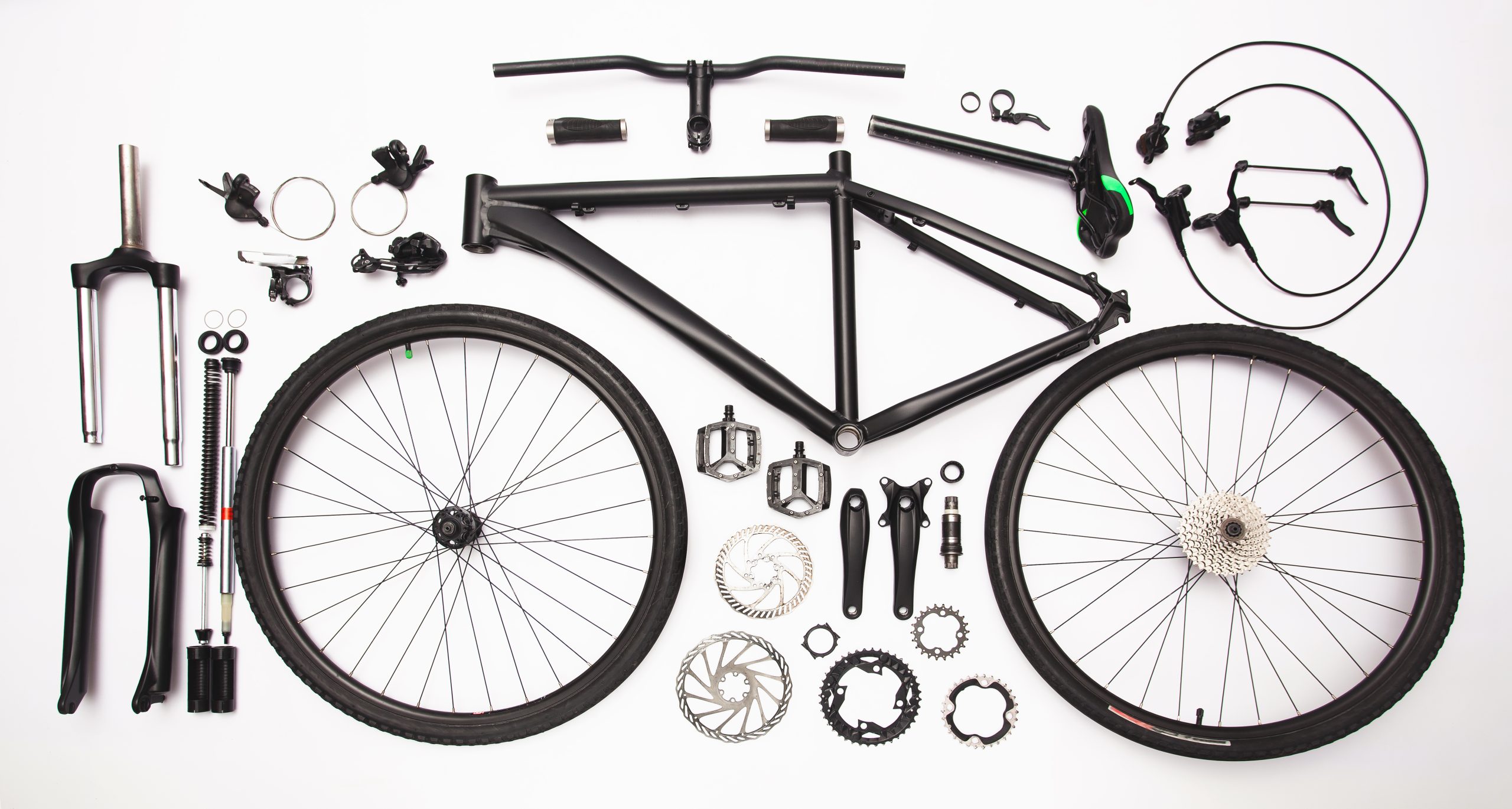
Subassembly can be described as several components put together to make a unit, which can then be used as a part for a larger assembly or a finished product. A subassembly can also function as a finished item sold separately to customers or used to finish constructing another product.
Understanding subassemblies is essential as this is a key part of developing your multilevel BOM.
This means you’ll need intimate knowledge of your materials, components, and subassemblies to develop your indented bill of materials.
Subassembly example
As mentioned earlier, subassemblies look like a BOM tree comprised of your raw materials, components, and subassemblies. At the top of the tree, you have your finished good (or parent product/level 0), and branching off from there, all your subassemblies.
A subassembly example for a bicycle will look something like this:
-
1. BICYCLE WHEEL SUBASSEMBLY:
-
1.1 Rim subassembly:
- Rim
- Rim Tape
-
1.2 Spokes subassembly:
- Spokes
-
1.3 Hub subassembly:
- Front hub
- Axle
- Hub end caps
-
1.4 Tire and tube subassembly:
- Tire
- Inner tube
-
1.1 Rim subassembly:
Workflow:
- Gather the required components and tools.
- Assemble the rim subassembly by applying rim tape to the rim.
- Assemble the spokes s by attaching the spokes to the rim.
- Assemble the hub subassembly by combining the front hub, axle, and hub end caps.
- Assemble the tire and tube subassembly by mounting the tire onto the rim and inserting the inner tube.
- Combine the rim subassembly, spokes subassembly, hub subassembly, and tire and tube subassembly to form the bicycle wheel subassembly.
- Conduct checks as per your quality control checklist.
- Complete subassembly documentation.
- Place the finished bicycle wheel subassembly in inventory.
This example demonstrates a multilevel BOM structure with three levels of indentation. It clearly organizes the bicycle wheel subassembly and its respective subassemblies, allowing for a clear understanding of the component hierarchy and assembly process.
Is Excel the best option to manage multilevel BOMs?
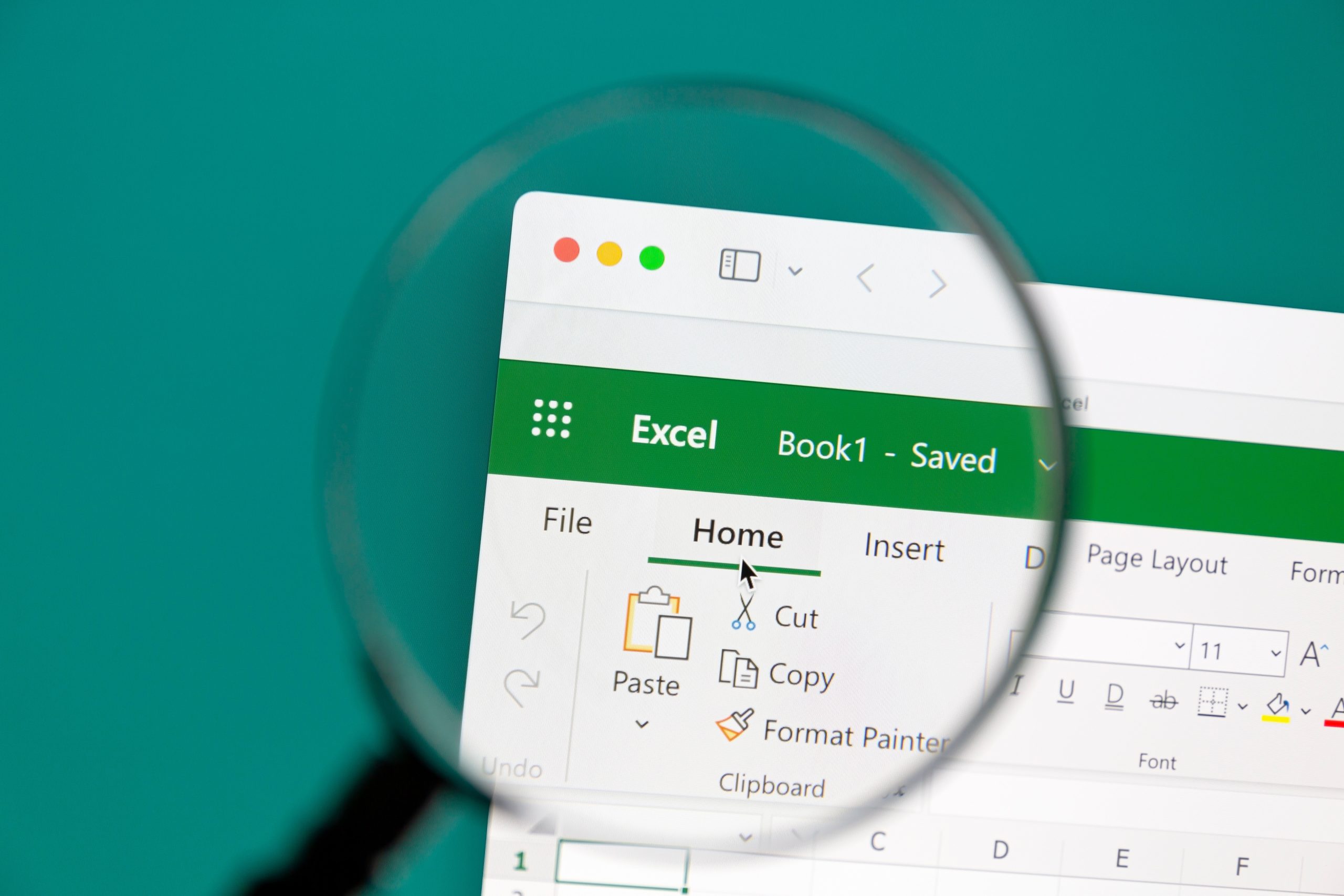
Let’s say you decide to keep your multilevel bill of materials in a spreadsheet. Is that feasible, or should you consider some other options? Let’s go over some of the challenges you may face.
Prone to errors
Maintaining multilevel BOMs in inefficient Excel spreadsheets can lead to problems ranging from simple copy/paste errors to complex issues with macros and scripts, necessitating frequent manual updates that consume significant resources. This not only wastes time but also compromises the accuracy of data used for crucial business decisions.
Creating a multilevel BOM is complicated
Creating a multilevel BOM in Excel is possible but can be complicated. You need to find a way to indicate a hierarchy level across parts and subassemblies. This is difficult for the following reasons:
- It’s easy to make errors when adding or removing parts from your existing multilevel BOM, for example, accidentally deleting all the associated parts when inserting the new values or removing subassemblies. Small mistakes can lead to huge errors if you make a business decision based on incorrect data.
- The sorting function in Excel is incredibly useful but can also cause significant problems like messing up your key columns and delaying your production process.
- Various products can often use the same parts. Managing multiple instances of a part across products across different levels of the BOM hierarchy can cause severe issues in Excel. For example, if you update the part number for one product, will all instances of the part in the BOM be updated?
Difficult to add variants
It is difficult to add in your potential product variants. When a product has multiple variants, it can be complicated to manage in Excel as the number of resolved BOMs will grow exponentially with the number of variants, very quickly becoming impossible to manage.
Calculating costs and quantities
Calculating totals in Excel may seem simple, and it is for flat or single-level BOMs. However, multilevel BOMs require extensive setup and complex formulas. This takes valuable time away from other important tasks and can be quite error-prone.
So, if Excel or any other type of spreadsheet documentation isn’t reliable, what options are there for manufacturing businesses looking to get more control over their BOMs?
Bill of materials software
There’s no place for spreadsheets in a scaling manufacturing business. Level up your production, purchasing, and costing with a bill of materials (BOM) software that gives the visibility you need to make decisions in real-time.
Cloud manufacturing platform to manage your BOMs
Adopting cloud inventory software, like the one offered by Katana, into your manufacturing business will mean more control over your BOMs.
Katana centralizes your entire business, from your sales channels to manufacturing operations, to one intuitive, visual platform.
Let’s see how to create a bill of materials in Katana using a bicycle subassembly example.
How to create a bill of materials in Katana?
Within Katana, when creating your BOMs, you’ll need to simply input your subassemblies as a product, which will later be used in the BOM for your finished product.
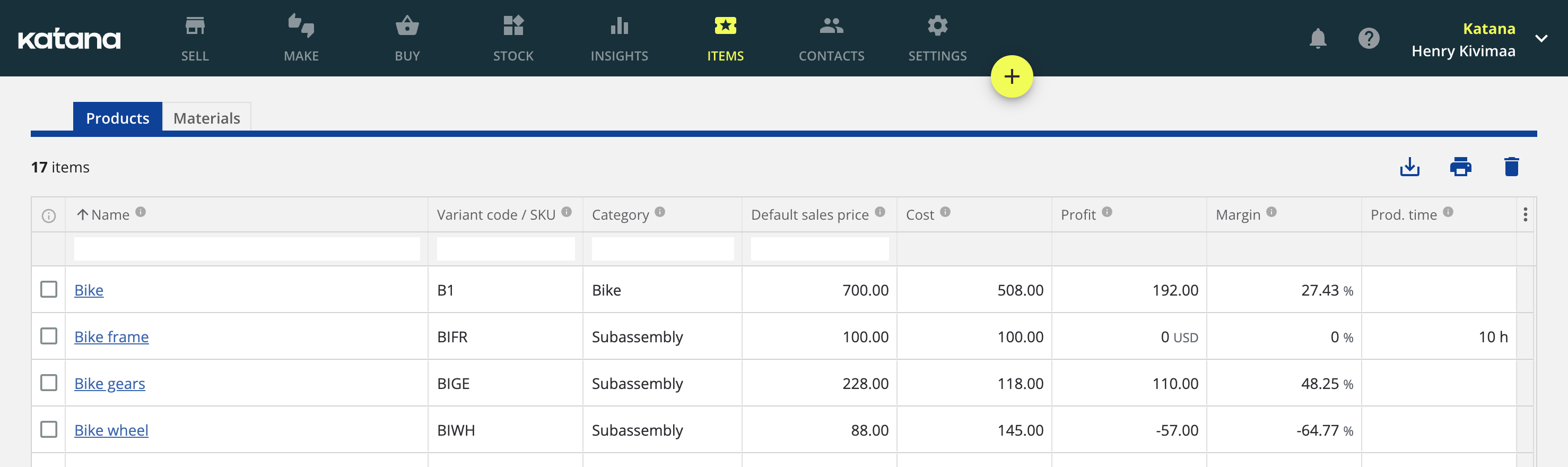
As you can see above, the frame, gears, and wheels appear as individual products but will be used as the ingredients for making the bicycle.
However, if you select the materials tab, you can see all the components which have been used to make those subassemblies.
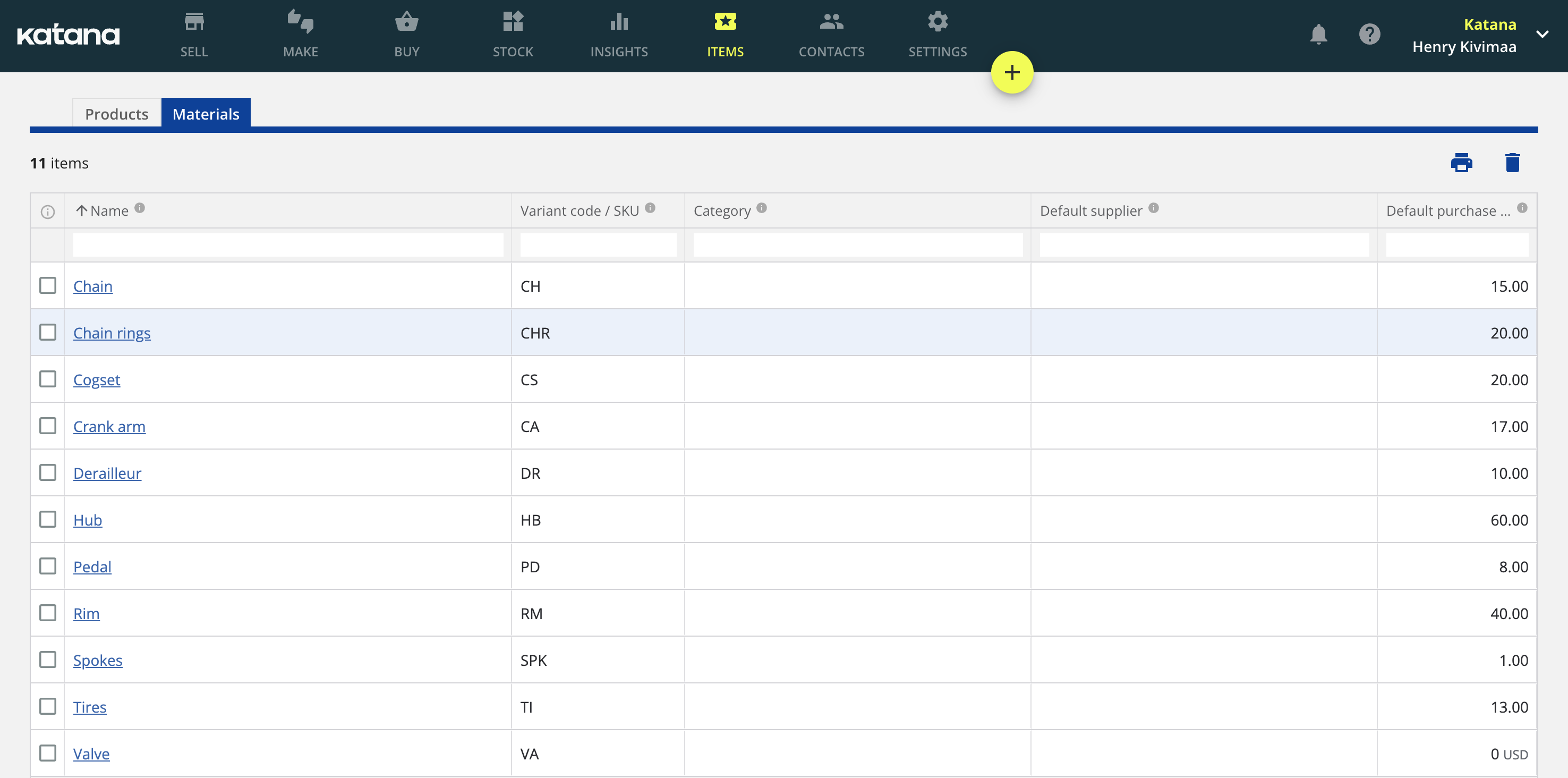
So, to begin adding in your subassemblies, simply follow these steps:
1. Click on the + symbol at the top of the platform, and at the drop-down menu, select New product card
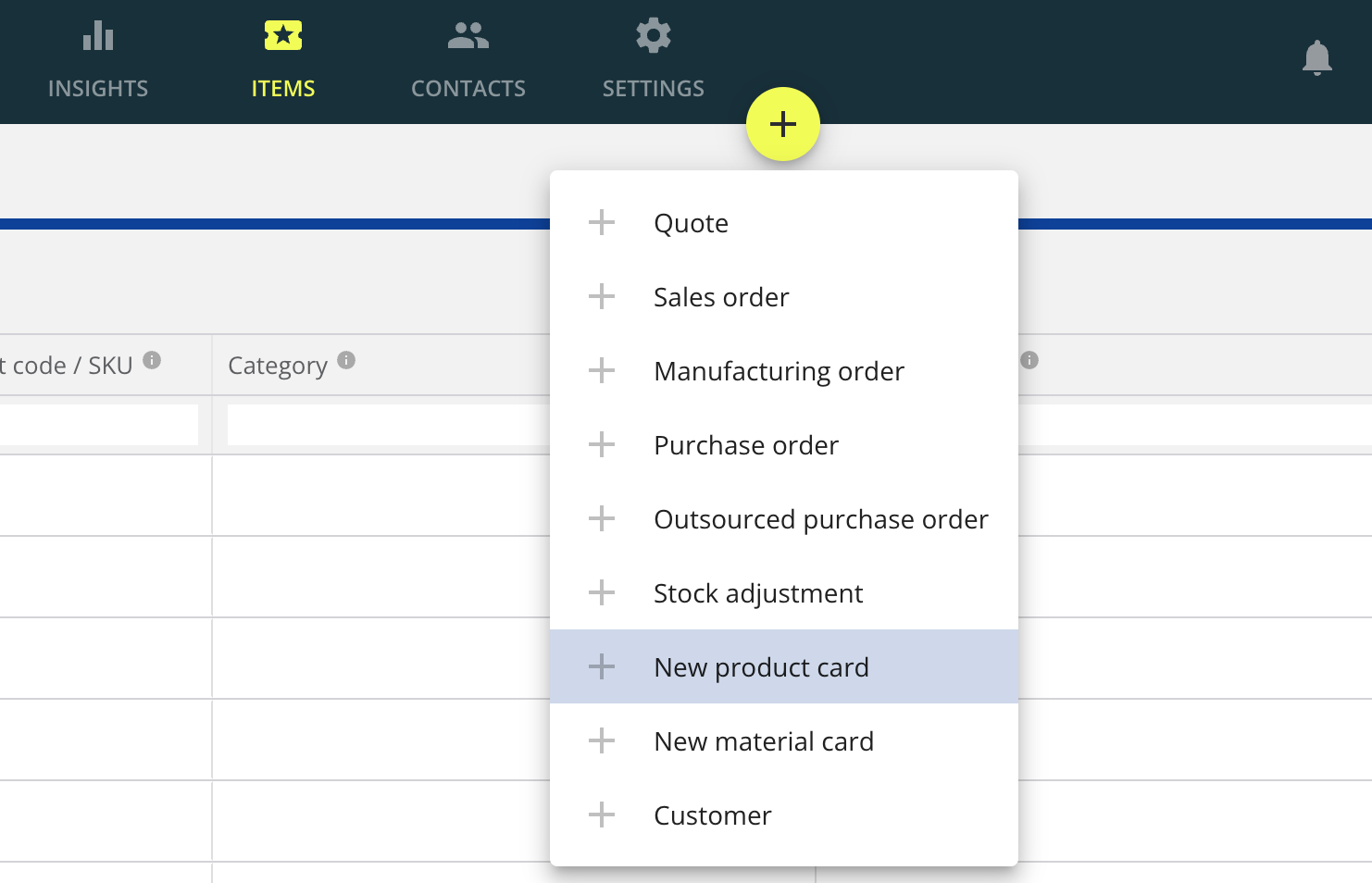
2. Here, you can input the subassemblies’ information, including the sale costs, ingredient costs, operation costs, quantities, the required materials/components, and the production process to make the subassembly.
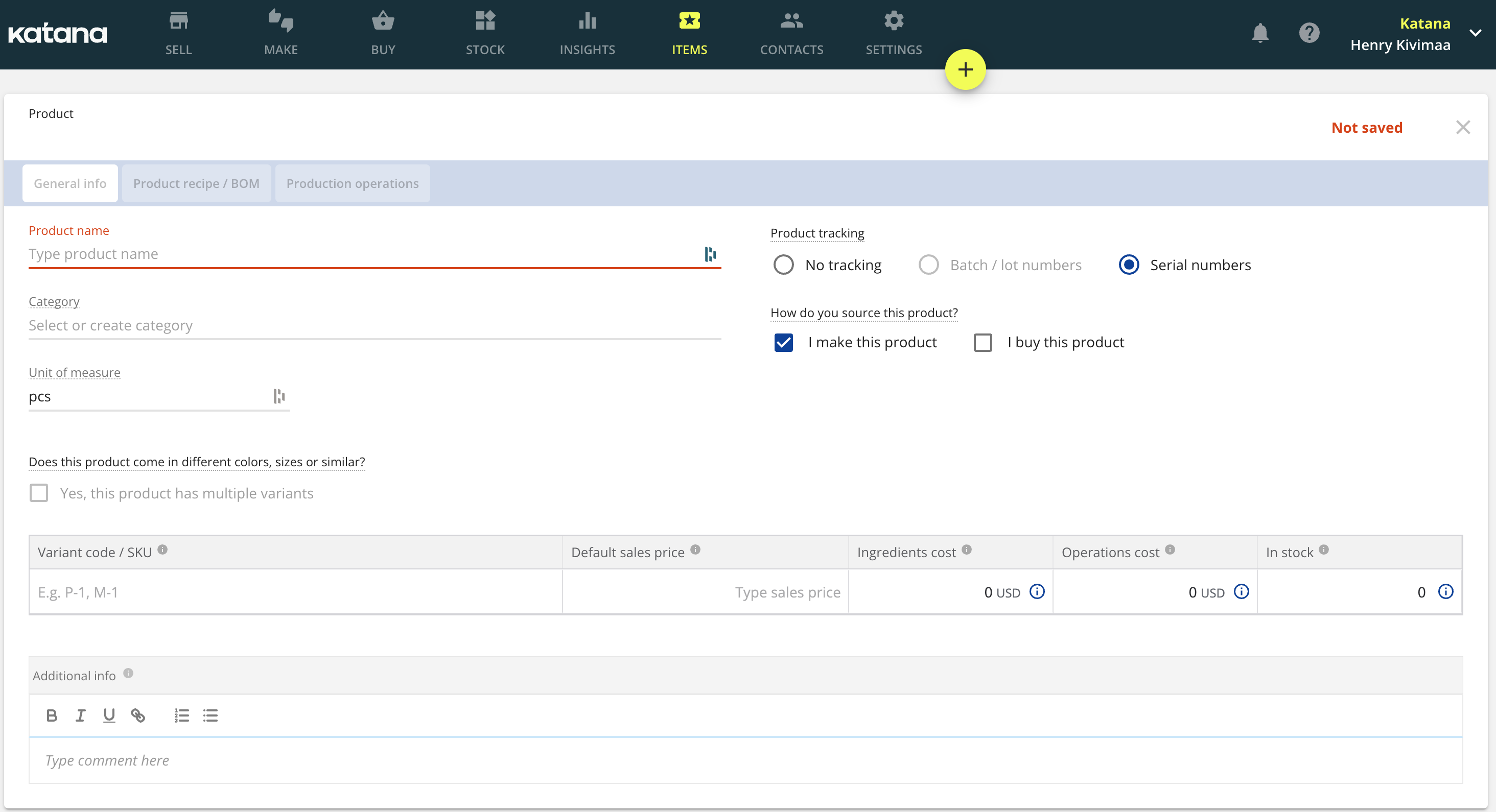
3. Once you have done this for each subassembly, you can now create the BOM for your finished product.
Open a New product card again, and this time when you’re imputing your Product recipe / BOM, instead of adding new material or using saved materials, select your subassemblies (which will appear as a product) and begin designing your multilevel BOM.
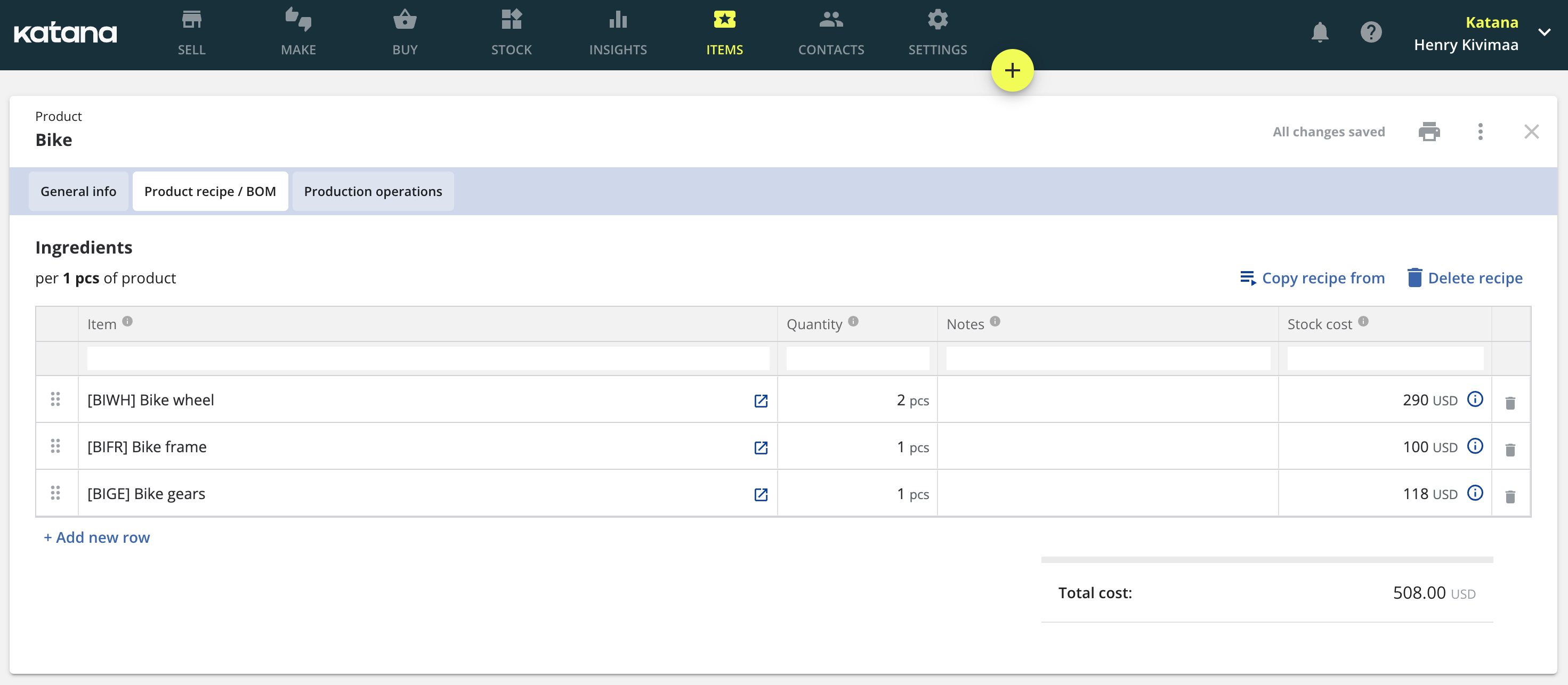
And that’s it, it’s that simple to add multilevel BOMs.
However, we should mention that Katana doesn’t take the traditional approach of an indented bill of materials structure. Instead, what will happen is if a sales order is generated, Katana’s real-time master planner will automatically allocate available finished goods to the order so that you can fulfill it as soon as possible.
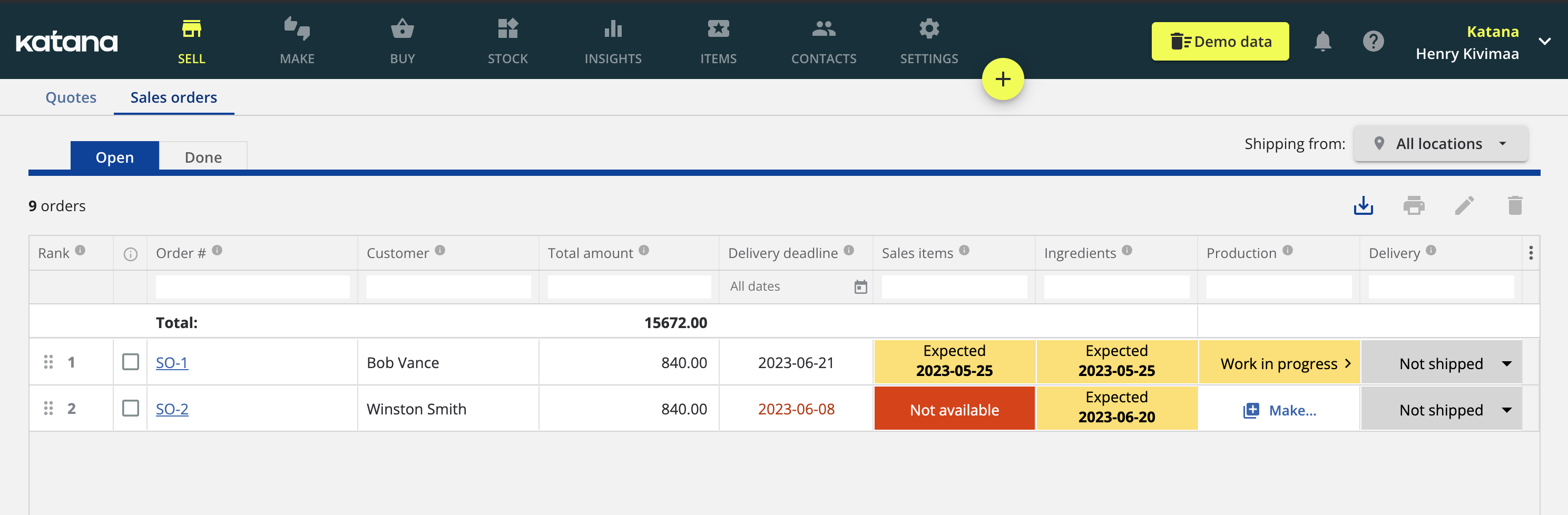
Although, if no bicycles are available, you’ll need to click on the sales order to find more information as to why it’s not available:
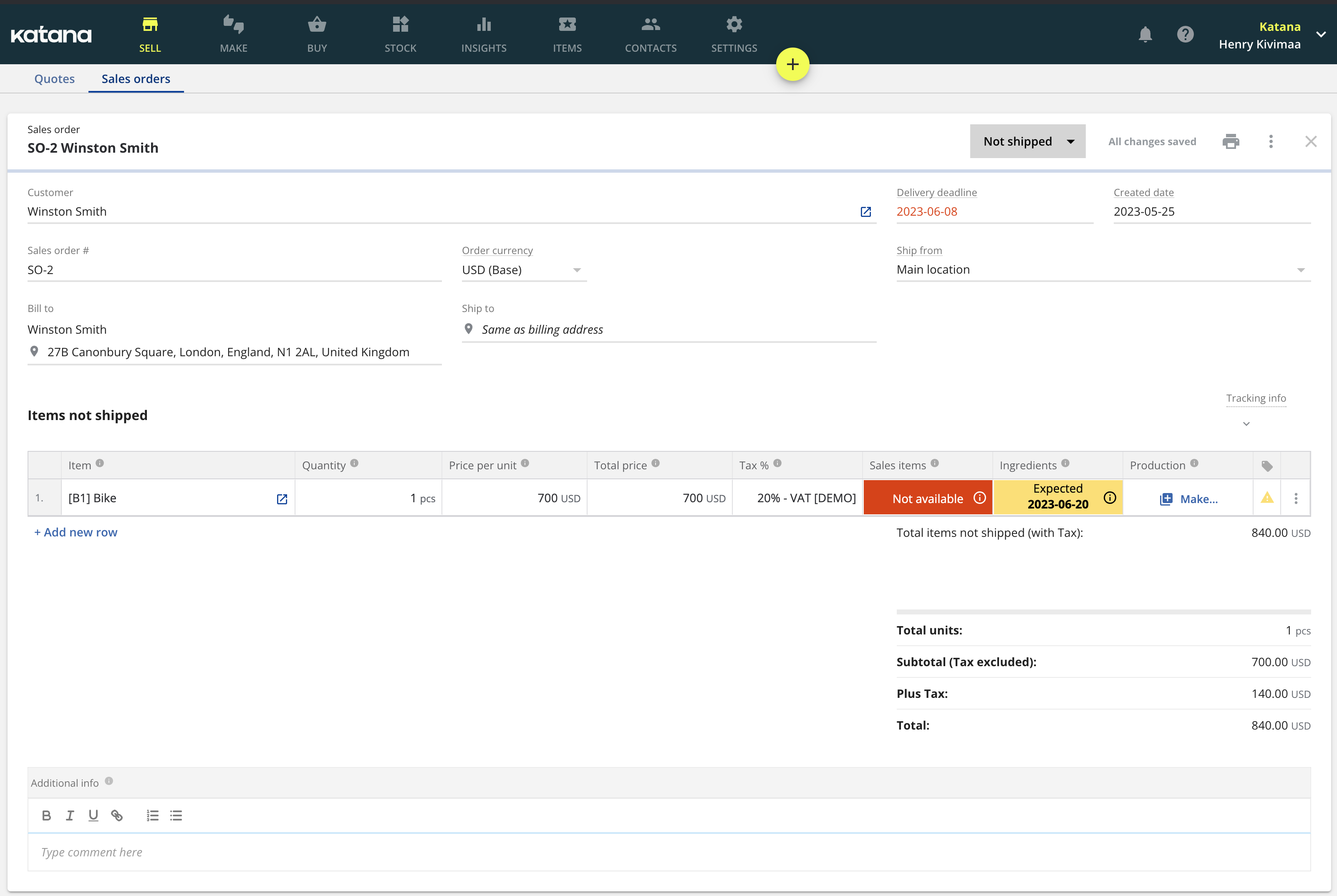
As you can see above, there are no finished bicycles in stock, and the subassemblies aren’t expected to be ready anytime soon. You’ll simply need to generate a manufacturing order (MO) by selecting Make… and select if you wish to Make in batch or Make to order
If you then go over to the MO screen by selecting MAKE at the top of the platform, you can select the MO to get more information on the production status.
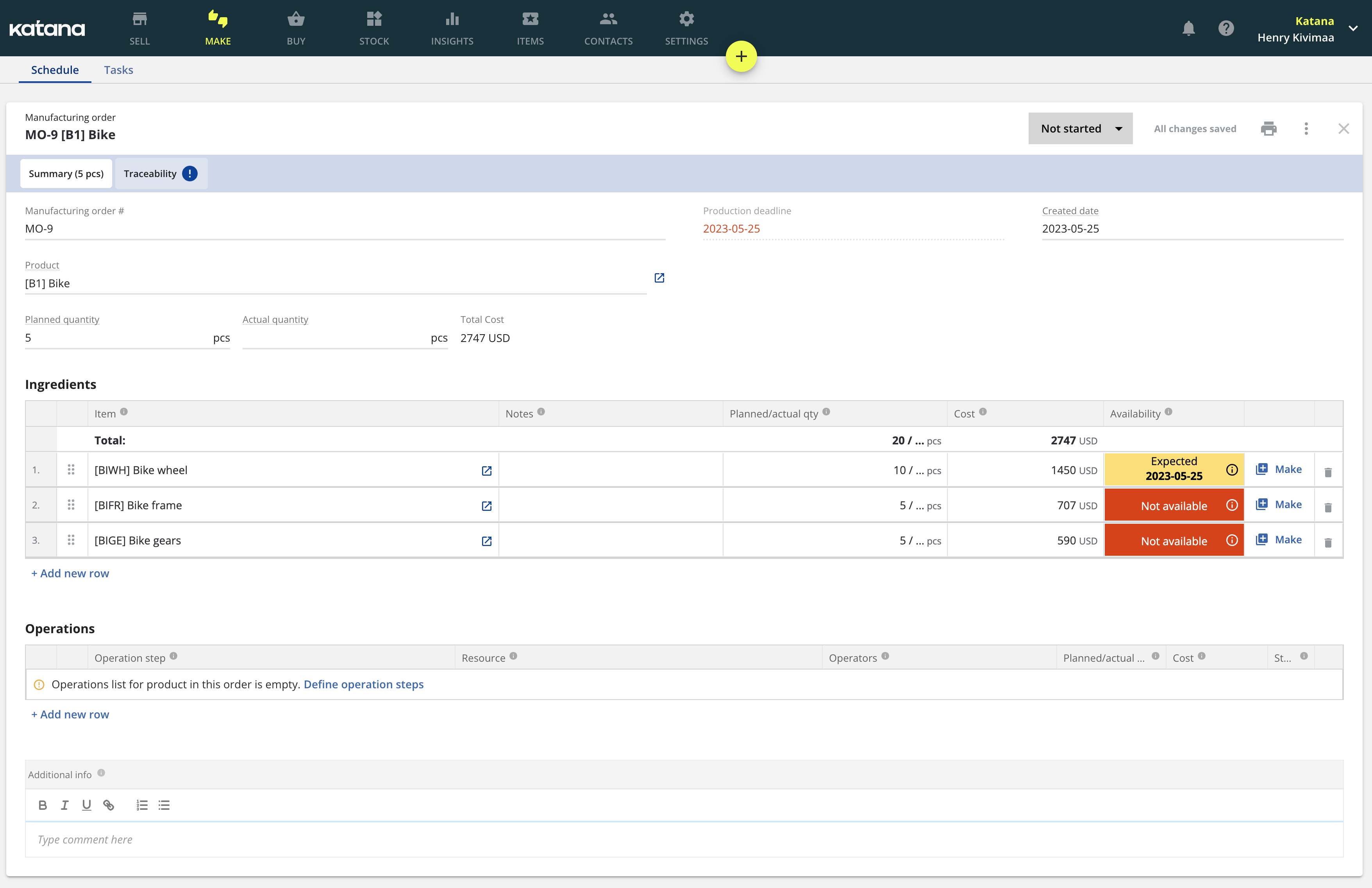
In the above example, the ingredients (subassemblies) are missing, so a purchase/manufacturing order for each subassembly needs to be created.
Once you’ve created those orders, you can check the status of your assemblies from the Make screen.
You’ve probably noticed that Katana schedules production by the older MO first, which might appear confusing if your first MO is dependent on the status of another MO. But, have no fear, Katana’s nifty drag-and-drop system allows you to easily reorganize your workflow, and better still if some materials are used in two MOs, Katana will automatically reallocate your material so that the prioritized order can be fulfilled first.
And a long story short, that’s how Katana helps manufacturing businesses get more control over their multilevel BOMs. If you wish to learn more about BOMs in Katana, check out the video below.
Multilevel BOMs can be a tricky element of your business to handle. Looking at the indented bill of materials example, it’s largely due to a manufacturer having to follow not only the production of their finished goods but also their subassemblies.
You will need to keep up stock levels and develop a smooth production flow for a multilevel BOM to ensure that your production floor doesn’t come to a complete halt due to being understocked or a bottleneck occurring when creating a subassembly.
Katana is the all-in-one solution to help you avoid bad multilevel BOM management while allowing you to quickly and easily get an overview of your business for improved management and production scheduling.
Katana also integrates with the best business tools, so if you’ve been using QuickBooks Online to monitor your business or Shopify to manage your e-commerce store, just link them up with Katana and all your platforms will be kept in sync.
Want to see it in action? Reach out to our sales team today and request a demo so you can see firsthand how it can help you become a more disciplined manufacturer.
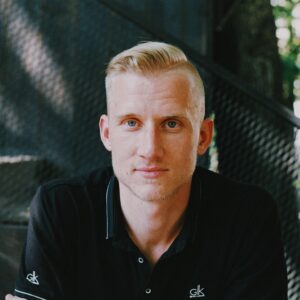
Henry Kivimaa
Table of contents
Get inventory trends, news, and tips every month
Get visibility over your sales and stock
Wave goodbye to uncertainty by using Katana Cloud Inventory for total inventory control
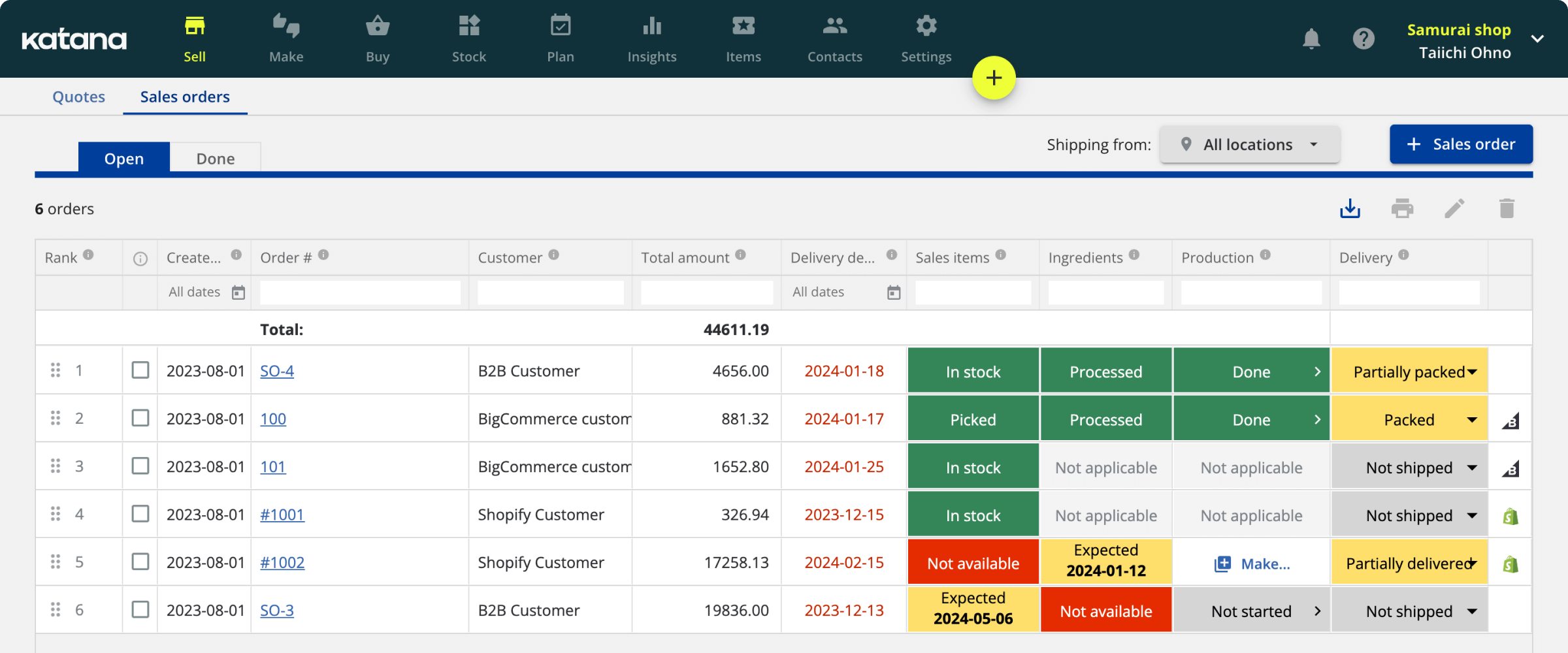