Resource leveling vs resource smoothing
If you’re experiencing scheduling issues, you’re going to need to use resource leveling or smoothing to fix the problem. But, how do you use them?
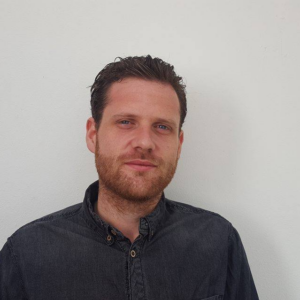
James Humphreys

You’re a project manager, and you stand before your production schedule. You realize, with the operations you have scheduled, you can’t finish production within your current chosen timeframe. When problems like this arise, there are two solutions you can adopt to fix the scheduling issues: resource leveling vs smoothing.
Project management techniques that’ll help you compress your schedule, so you can finish your orders without over-burdening your resources.
Before we get started, what are these project management techniques?
What is resource leveling?
Resource leveling overlooks allocating resources and resolving any issues from over or under-allocation of resources for new projects.
What is resource smoothing?
Resource smoothing is a project management tool for optimizing your resources, and adjusting your schedule activities, so resources don’t exceed the pre-defined limits during planning.
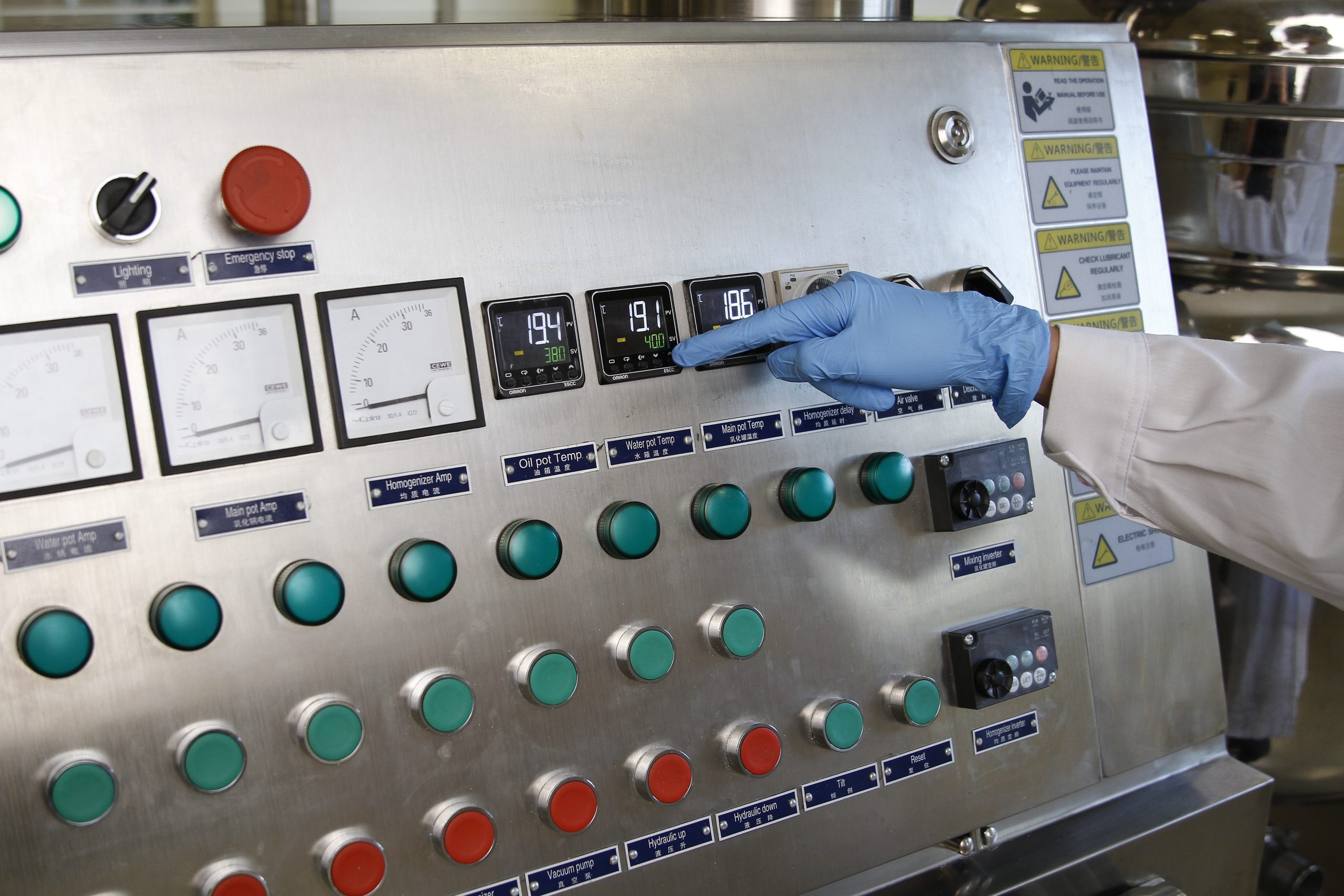
The difference between resource leveling vs smoothing
The difference between resource leveling vs smoothing can be broken down to this:
Resource leveling – This is used when scheduling the production of available resources is limited and needs to be used optimally.
Resource smoothing – This is used when time constraints are the biggest factor blocking production. The idea is to finish a project on time while avoiding peaks and dips in resource demand.
You can identify the differences by their traits and decide where you should hedge your bets when it comes to resource leveling vs resource smoothing:
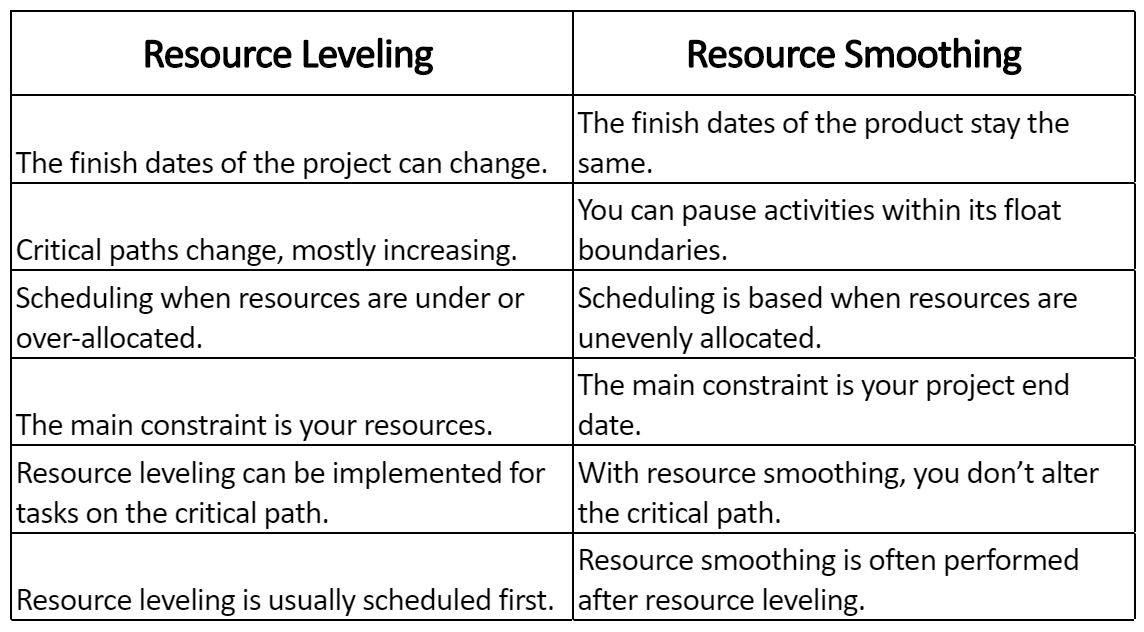
Resource leveling is usually performed before resource smoothing when trying to compress your schedule. That’s why we’re going to look more into resource leveling, starting with the two key elements of this planning tactic.
The two key elements of resource leveling
The main objective of leveling is to allocate resources efficiently, so you’re able to finish production within a given period.
When you start your resource leveling, there are two main elements you’ll need to be focusing on.
These two elements of resource leveling are figuring out which projects:
- Can be completed by using up all available resources
- Can be completed with limited resources
Manufacturing orders that use a limited amount of resources can be extended over a period until the resources become available.
However, if the number of orders you need to undertake exceeds the number of resources you have available, then postponing manufacturing orders for a later date may be the wiser decision.
The structure of resource leveling
Manufacturers structure their resource leveling following these steps when doing their project management:
- Stage
- Phase
- Task/Deliverable
The above steps will help you determine the scope of the project for your manufacturing orders, and find ways to organize your team members, which will make it easier for you when planning your production.
However, when you’re managing your projects, the level of resources needed for each of these three parameters may be different (depending on seniority, experience, and skill level of your staff). This means the resource requirements between projects vary when planning production in these three areas.
This is why many manufacturers turn to manufacturing execution systems to help them structure their production.
The purpose of resource leveling
Resource leveling is a response to a production schedule that has been put together poorly, to redistribute resources, focus, and time to achieve production within a given timeframe.
And, you’ll do this by identifying your:
Dependencies
Dependencies are the relationships between your tasks, which one comes first, and which one comes after.
Resource conflicts
Resources that are needed for multiple projects that have started at the same time. For example, maybe you have a worker who does engraving but has two orders arrive at his workstation.
Another thing you’ll need to establish is constraints that affect production, and these constraints can be:
Mandatory
Constraints are caused by physical limitations such as experiments.
Discretionary
Constraints based on your team member’s preferences and actions.
External
Constraints are often imposed by the needs or desires of a third party.
Knowing your dependencies, resource conflicts, and constraints are going to be essential for helping you put together later production schedules.
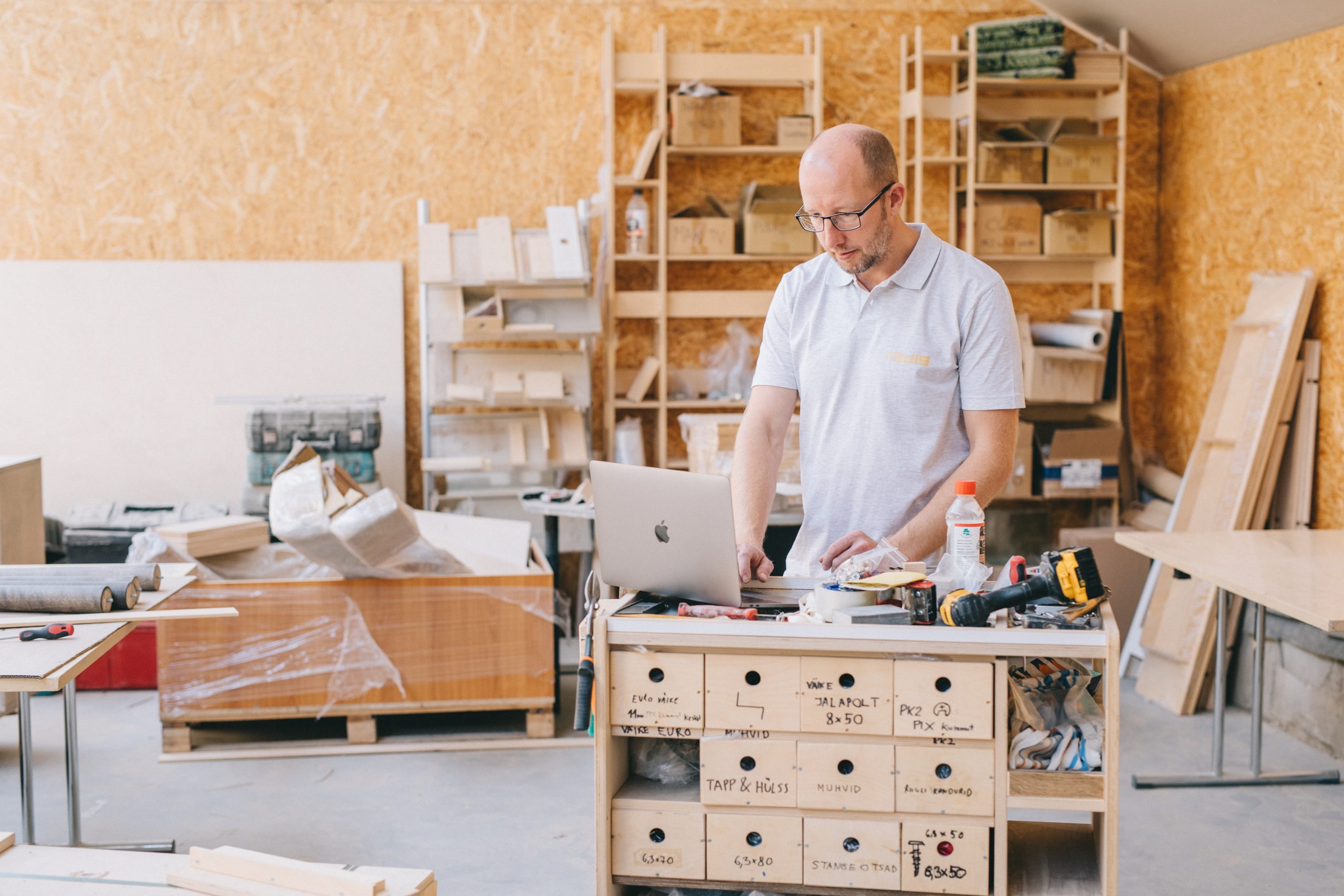
The resource leveling techniques
So, that’s the basics of resource leveling, but what are the techniques that you can adopt into your business to get you started with project management.
Critical path analysis
The critical path analysis/method is an algorithm for scheduling production. It’s the most common type of technique that involves looking into the longest and shortest time duration paths in the network diagram for completing a project.
This is done by looking into your resource dependencies to understand the realistic timeframe in which a manufacturing order can be completed.
With this resource leveling technique, the tasks of the critical path are the ones considered to be highly important, and analyzing these paths will bring out activity interdependencies, which will highlight the resources needed to collaborate on them.
Critical path analysis is a resource leveling technique that is widely used in industries that have complex production processes. But today, most businesses use production scheduling software that automatically calculates the completion time of their operations.
Fast tracking
Fast tracking is the resource leveling planning technique of buying more time, by completing tasks in parallel, which you would not otherwise normally do.
This approach to resource leveling can only be completed if activities can overlap, allowing you to finish production on time and without additional costs.
An example of this could be building prototypes of a new product before the design has been approved.
The purpose of this approach is to compress your schedule if following the usual steps one-by-one will put you over the deadline.
However, fast tracking might have a high reward of completing tasks sooner or getting a product out to the market quicker, it also comes with higher risks, and can be prone to issues such as having to rework what you’ve already done due to mistakes.
Crashing
If you gamble with fast tracking and fall short, another resource leveling technique you can implement when you’re schedule compressing is crashing.
The purpose of crashing is to shorten your duration by adding more resources to a manufacturing order, with the least possible cost.
When adopting crashing, you’ll be prioritizing based on the lowest crash cost per unit team, and this focus will allow your team members to identify activities that deliver the most value for your business.
By understanding which projects fall on and outside the critical path allows you to see which tasks benefit from additional resources, meaning you can prioritize and rearrange schedules in advance for future projects.
So, there we have it, the different resource leveling techniques you can adopt when addressing your production planning and scheduling issues.
However, when you look online, there’s some confusion between resource leveling vs fast tracking, so very quickly let’s look into this.
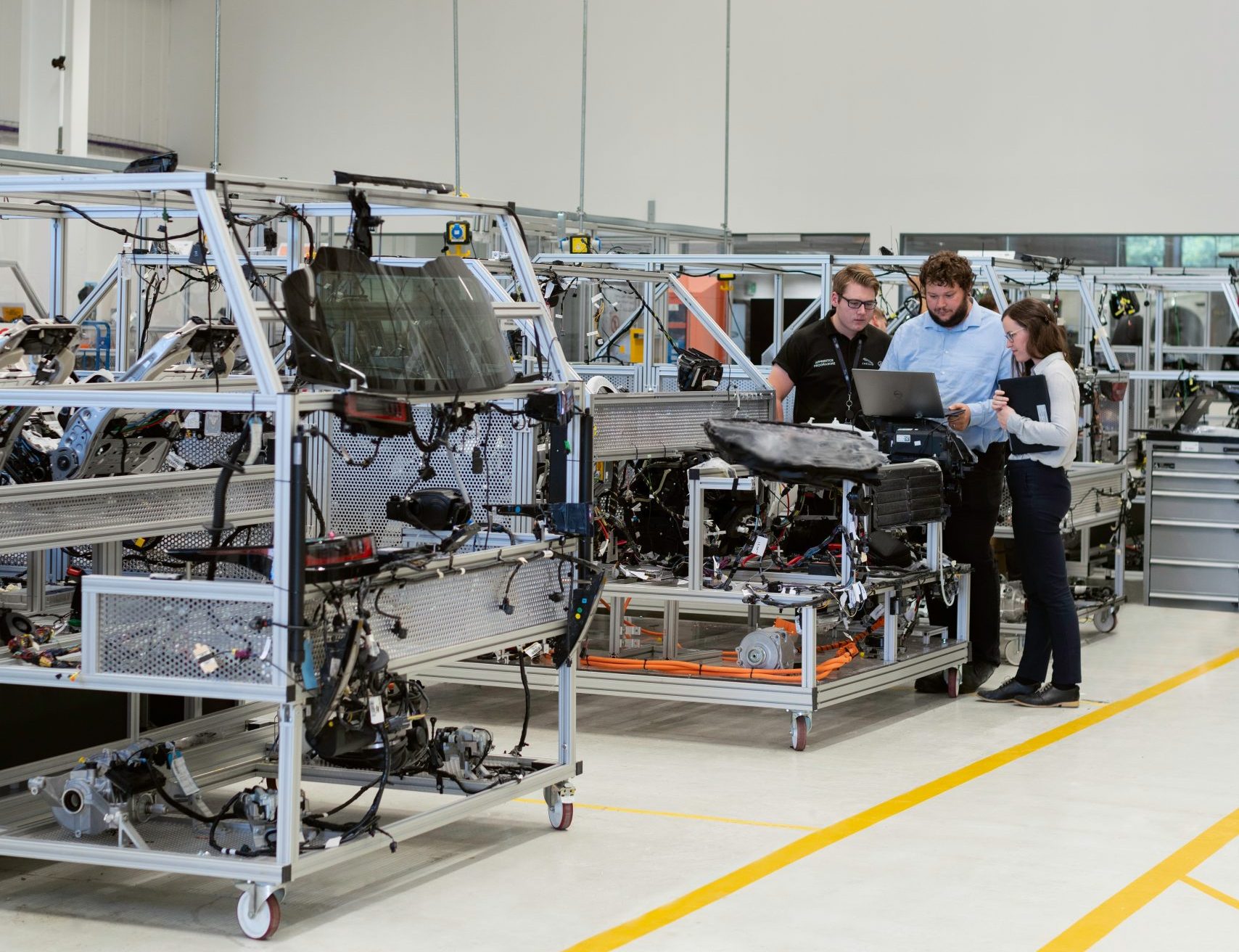
Resource leveling vs fast tracking
As we’ve already mentioned, when it comes to resource leveling vs fast tracking, you shouldn’t really be distinguishing a difference between the two, as fast tracking is a technique that exists within the world of resource leveling.
Realistically, when you’re scheduling production, and your biggest constraints to manufacturing is time or resource availability, you’re probably going to be more concerned with choosing between fast track vs crashing.
Using the table below is going to help you determine which is the best for your business:
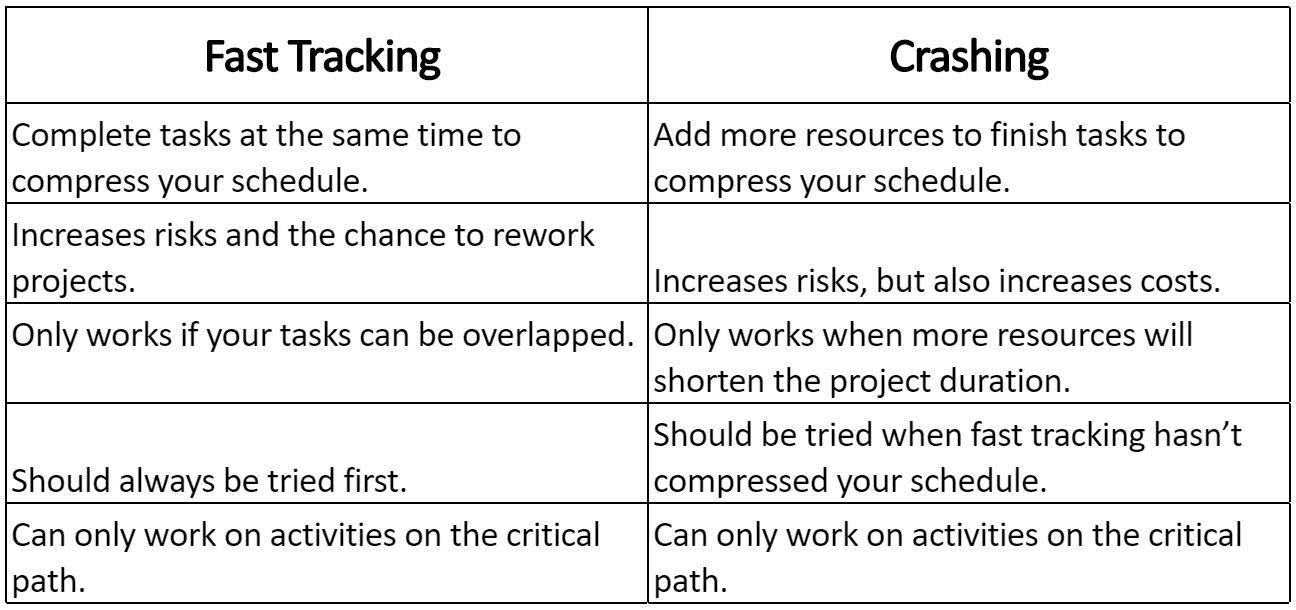
So, that’s everything you need to know about resource leveling, resource smoothing, and the different techniques.
Now let’s look into the advantages of using these scheduling compression plans.
Katana production scheduling software
Prioritize manufacturing tasks, track availability for required materials for efficient sales order fulfillment, and have a live floor-level production status overview.
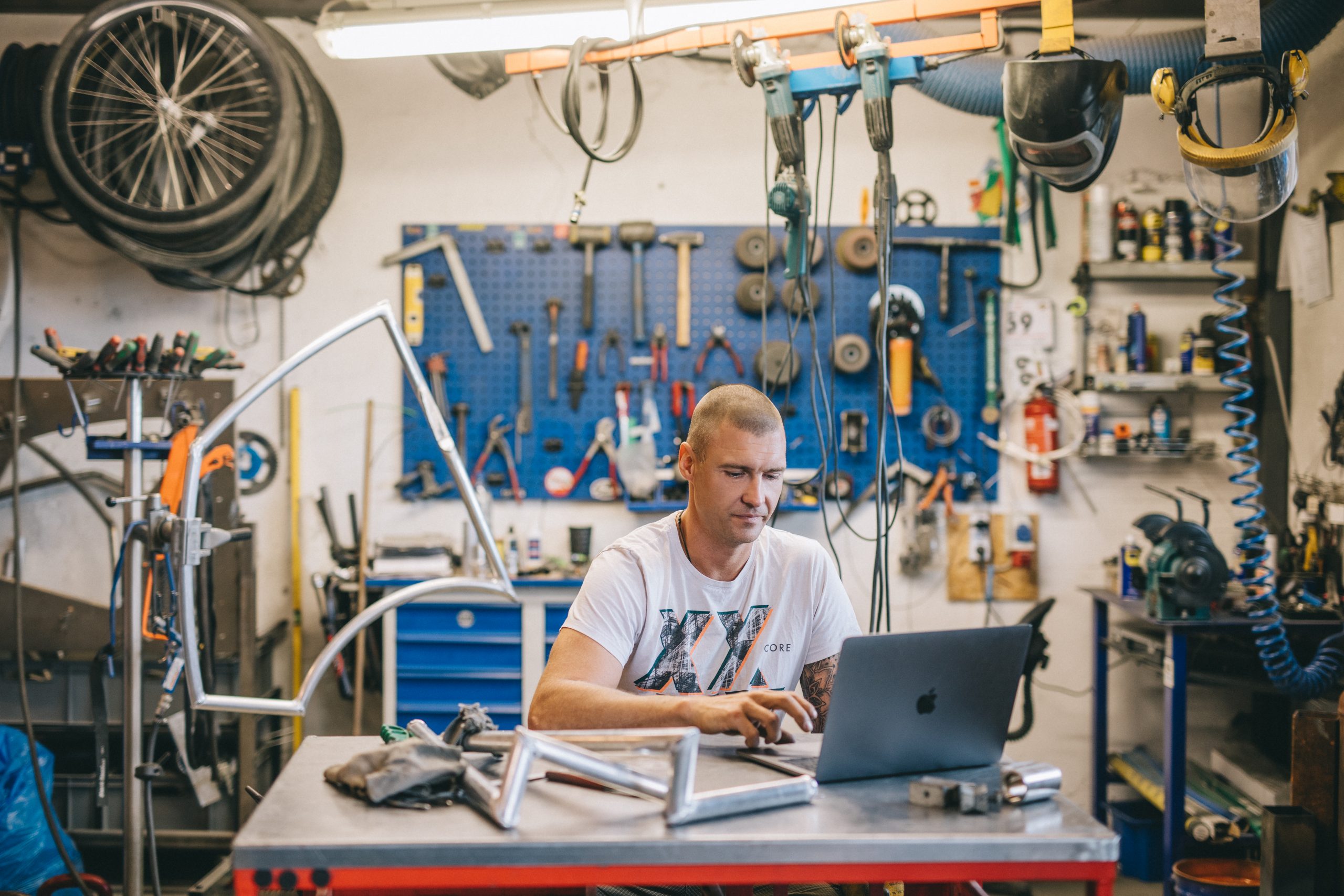
Advantages of using resource leveling
Resource leveling is going to help you understand imbalances with your resource allocation, and avoid those resources becoming over-burdened.
And this is, of course, the biggest advantage because if you can avoid over-allocating resources, you’re going to increase productivity.
But other advantages you’ll experience are:
- Minimizing production delays
- Identifying and utilizing downtime
- Team members can better prepare for tasks with more time to adjust between activities
- Team members aren’t working on projects they aren’t trained for
- Better resource allocation
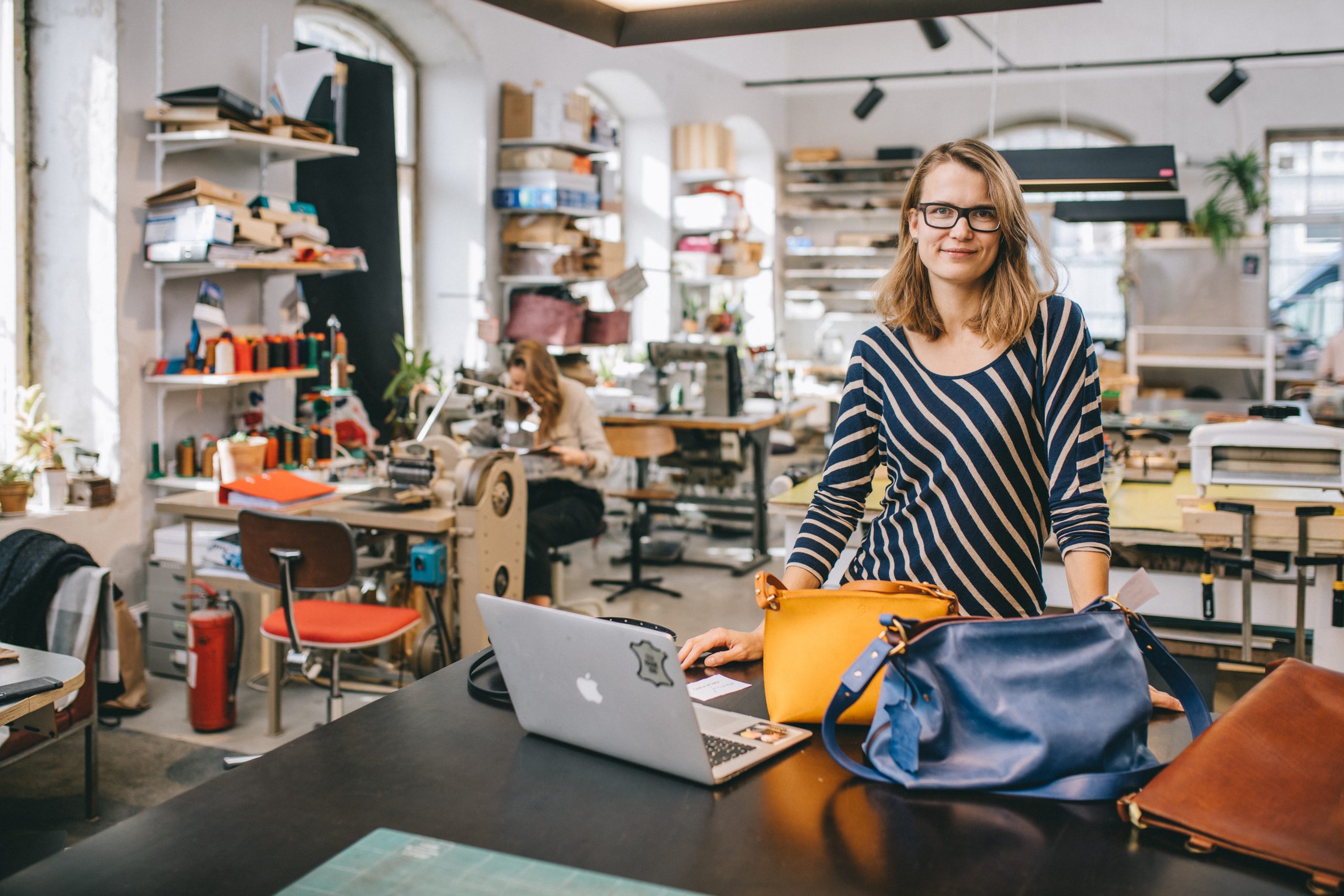
Conclusion
So, there you have it, everything you need to know about resource leveling, resource smoothing, and the different leveling techniques you can adopt to fix any scheduling issues that might occur.
The main takeaway from this is that although adopting project management techniques is inevitable, these particular ones come from poor production planning.
And the best way to avoid poorly designed schedules altogether is to adopt cloud-based inventory software, such as Katana.
Katana Smart Manufacturing Software automatically schedules production and allocates items and resources to your orders, so you can ditch the inefficient spreadsheets for planning production, and stay focused on growing your business.
And that’s it for today, we hope that you found this article useful, and if you have any questions, please feel free to drop us a comment or get in touch with us over on social media.
And until next time, happy manufacturing.
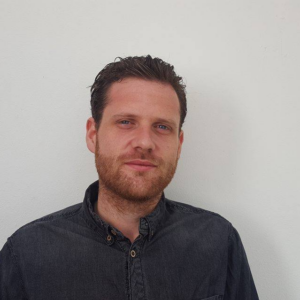
James Humphreys
Table of contents
Get inventory trends, news, and tips every month
Get visibility over your sales and stock
Wave goodbye to uncertainty by using Katana Cloud Inventory for total inventory control
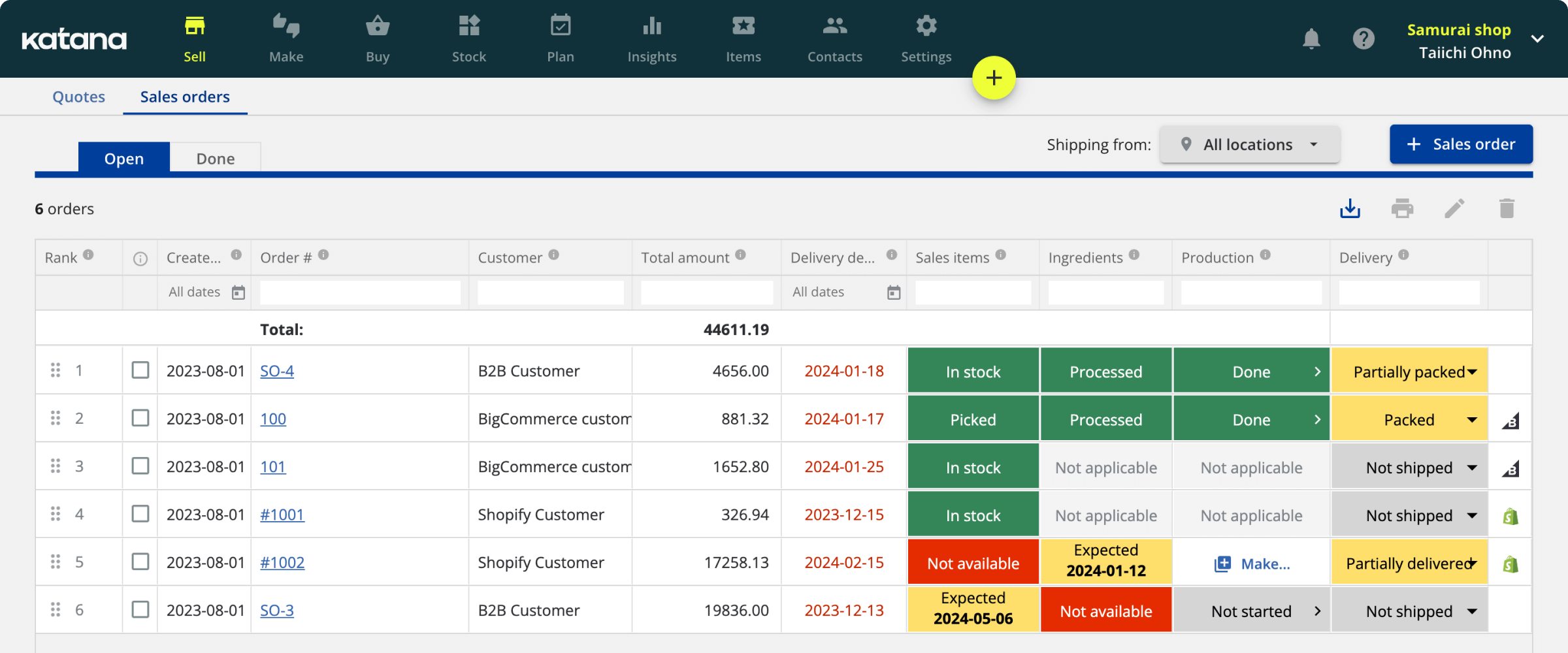