Toll manufacturing vs contract manufacturing
Should you let a third-party company source raw materials for your products with contract manufacturing? Or should you supply them yourself and pay a toll for the manufacturing services? Read on to find out.
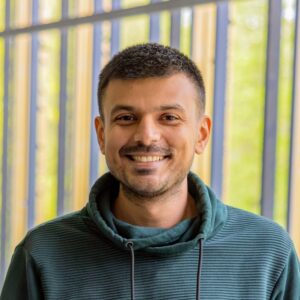
Tejas Shah
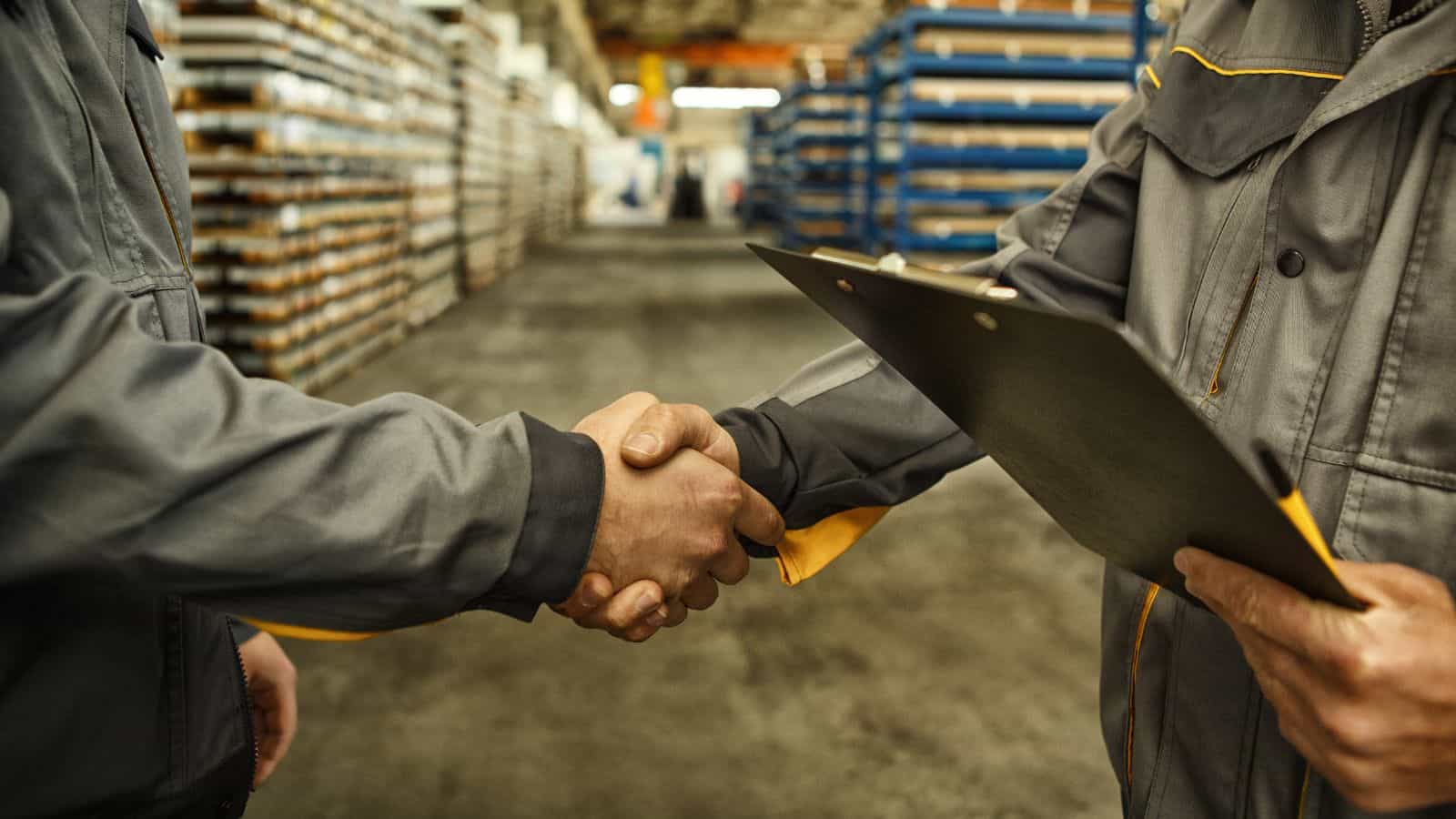
You are in an enviable position.
Your business is growing, and you are looking to add production capacity. After considering your options and reading about outsourcing manufacturing, you have decided to go this route. However, you find yourself at the crossroads of contract manufacturing and toll manufacturing since these are the two main paths when it comes to getting third-party manufacturing involved.
Let’s take a closer look at toll manufacturing vs contract manufacturing. We will look at each modality’s advantages and disadvantages and help you understand which one better suits your needs.
Get your outsource manufacturing off the ground with Katana
Organize purchase orders for outsource manufacturers and track stock levels for those materials to keep production moving.
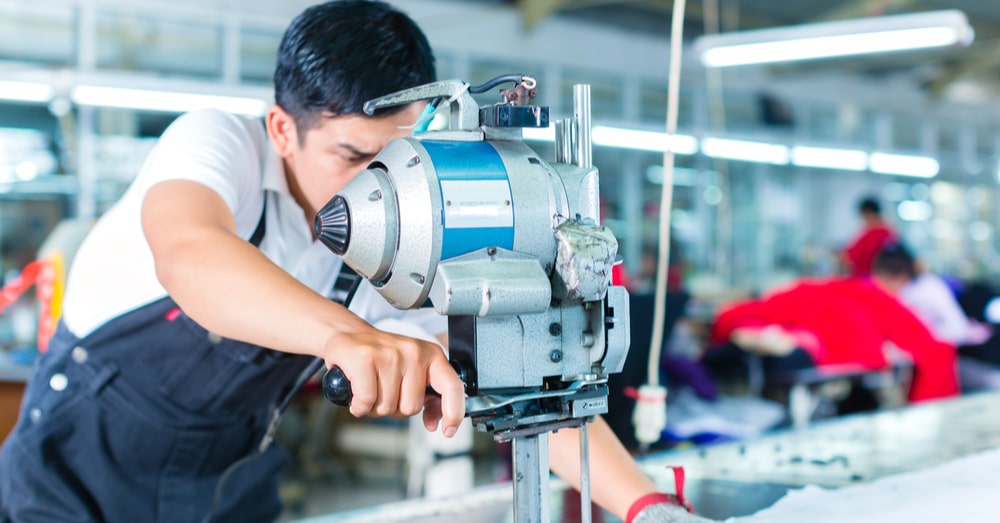
What is contract manufacturing?
Contract manufacturing is a form of supply chain management where you outsource either a part or all of your production to a third-party manufacturer as a means to increase your output. The company that takes up your contract is referred to as either a subcontractor or contracting company.
In this article, we will focus on a key point of contract manufacturing, which is that the subcontractor manages the entire product cycle. This means that the contracting company is also responsible for the procurement of raw materials. So, as the parent company, you simply need to place an order, and they do the rest.
Putting the contractor in charge of the raw materials allows you to leverage your contractor’s already established vendor networks. Additionally, contracting often produces equal or higher quality goods at the same price points because the workforce is highly specialized, and you can also derive the benefits of economies of scale. The catch here is that you have to invest more into quality control processes on your end to make sure that the final products meet your quality standards.
What is toll manufacturing?
Toll manufacturing is an outsourcing arrangement in which you supply the raw materials and pay a fee (or toll) to access the subcontractor’s manufacturing capabilities. In this case, the subcontracting company is also called the tolling company or toll manufacturer.
A toll manufacturing situation could arise if you have better access to raw materials in terms of price and/or quality. Or you simply want to have more of a say in what is used to produce products that will carry your brand name. In either case, toll manufacturing can help you scale your business without having to build more manufacturing infrastructure.
One of the main advantages of toll manufacturing is that you have complete control over the inputs, and as a result, you have more due control over the quality of the final product. Often toll manufacturing also turns out to be cheaper than contract manufacturing since you simply pay for the manufacturing capabilities of the tolling company. The obvious drawback here is that the transportation hassles are on your plate instead of the tollers’.
Toll manufacturing is highly prevalent in the consumer electronics industry. A textbook example of such an arrangement is Apple and Foxconn. Apple has very limited manufacturing capabilities, and almost all of its products are, in fact, manufactured by Foxconn, a Taiwanese electronics manufacturing giant.
A fun fact is that Foxconn is the largest private employer in the People’s Republic of China and one of the largest employers worldwide. Ethical concerns aside, economies of scale are clearly on the side of contract and toll manufacturing.
Returning to toll manufacturing, Apple supplies Foxconn with all the raw materials, such as the screens, chips, and components required for its products, and pays Foxconn only for the manufacturing services. Clearly, toll manufacturing worked wonders for both Apple and Foxconn.
Easily manage your contract manufacturers with ERP
Contract manufacturing has never been easy to manage with Katana. Have raw materials delivered directly to your CM or send sub-assemblies for production and monitor the entire process from the Katana platform.
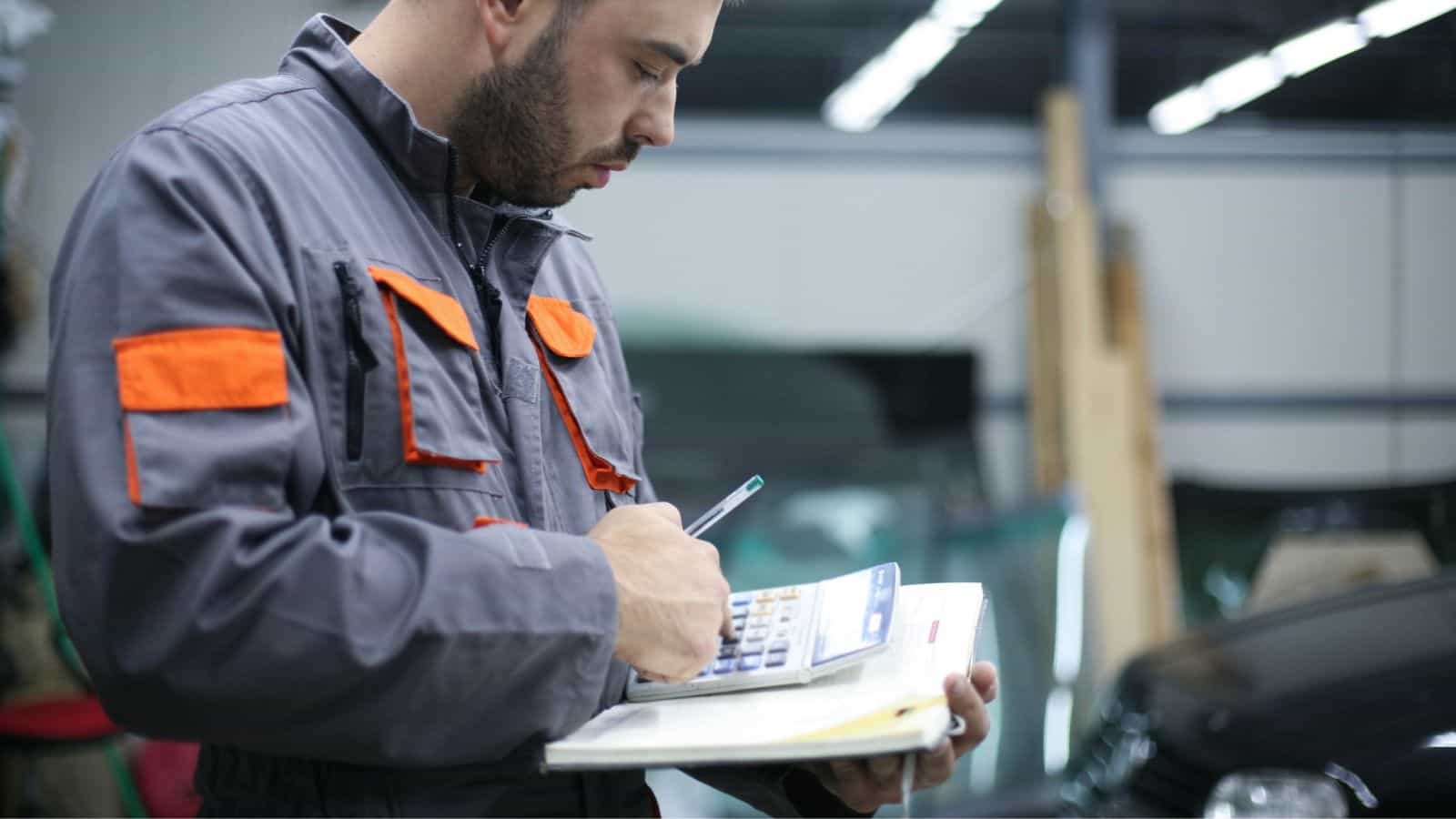
The difference between toll manufacturing and contract manufacturing
As you can see, the key difference boils down to who is responsible for procuring raw materials. However, this key difference has plenty of implications.
Toll manufacturing can shine when you want to protect your intellectual property or have some form of proprietary technology involved. For example, let us say that you are in the food manufacturing space and have a proprietary blend of spices that is the secret to your best-selling sauce. You wouldn’t want to give it away to a third party, so you could simply package the blend yourself and ship it to the tolling company.
The other advantage of toll manufacturing is that you don’t have to worry about price fluctuations of the raw materials from the contractor. You only need to pay for the manufacturing service, and that price is generally quite stable. As discussed earlier, toll manufacturing might better suit your needs if you have better access to the raw materials.
The only drawback to toll manufacturing is that it adds to the overhead of managing logistics. This can be complicated since you have to synchronize the delivery of the raw materials with the production schedule of the tolling company. Of course, these transportation hassles could be well worth it, given the lower costs.
Now let us consider the advantages of contract manufacturing. Speed and simplicity are contract manufacturing’s strong suit. Once you do your due diligence about the subcontractor, you simply have to place an order for your products and focus your energy on other important aspects of your business, such as product development. Of course, quality control needs to be taken care of, but compared to setting up more production capacity, quality control is a lot easier to ramp up.
Apart from these differences, you need to take into account a few other factors before you decide to outsource your production. For instance, assessing the risks involved in outsourced manufacturing setups is difficult with the rapidly changing geopolitical landscape.
Now that you understand the subtleties of toll manufacturing and contract manufacturing, it’s clear that you need the right tools in either case.
With manufacturing ERP software like Katana, you can implement both contract and toll manufacturing workflows. For instance, you can create OPOs (outsourced purchase orders) to have raw materials shipped directly to your toll manufacturer and track those items sent to their location.
You can also create workflows for partially outsourced production. For instance, you can create a sub-component and send it off to your subcontractor to perform specific operations. With Katana, you can also edit service fees to track outsourced operation costs, which helps you accurately track the actual costs of outsourcing.
Come and see for yourself. Get a demo and find out how thousands of manufacturers use Katana to grow their businesses and simplify workflows.
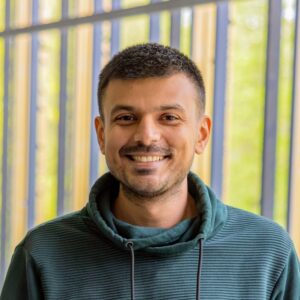
Tejas Shah
Table of contents
Get inventory trends, news, and tips every month
Get visibility over your sales and stock
Wave goodbye to uncertainty with Katana Cloud Inventory — AI-powered for total inventory control