Agile manufacturing: What it is and how it works
If you’ve been around the business world for long enough, you’ve heard plenty about something called agile methodology. Here’s how it applies to manufacturing.
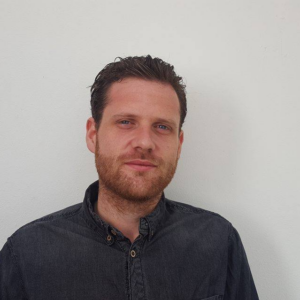
James Humphreys
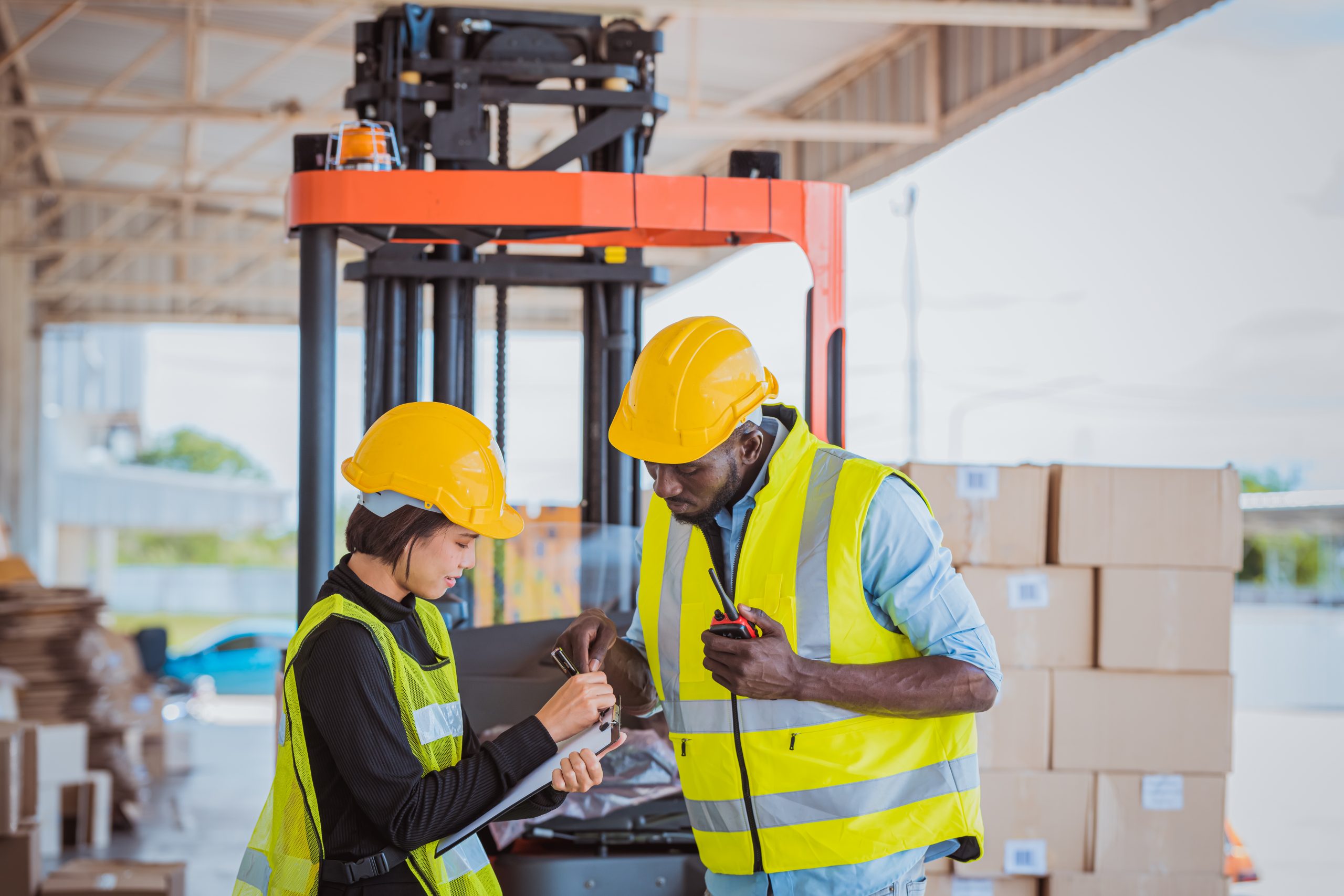
In most cases, the term agile means breaking projects into smaller, more manageable pieces so that work is completed more efficiently. It has taken root in the world of software development because of its versatile practices and easy-to-learn tenets.
But is agile methodology used in manufacturing industries? Simply put, yes!
For the manufacturing world, it’s a process that helps factories respond quickly to customer demand.
In other words, manufacturers using the agile approach create products based on what customers want to buy rather than making products and then trying to sell them. If you’ve always been interested in what agile manufacturing is and whether it could work in your own business, you’ve come to the right place.
Below, we will examine the definition, benefits, and key principles of agile manufacturing, while also comparing it to lean practices and discovering some software solutions that can help along the way.
?What is agile manufacturing
Agile manufacturing is a way to create and produce things in a manner that is more flexible and adaptable than traditional methods.
This means changing or altering the production process quickly and easily to meet customer needs and demands better. Agile manufacturing systems are designed to be very responsive. They allow manufacturers to rapidly respond to changes, whether those changes are in customer demand, technology, or even the marketplace itself.
They can also provide several key benefits to drive overall growth, including:
- Improved customer satisfaction — Agile manufacturing is all about providing what the customer wants when they want it. This helps to build a loyal customer base that keeps coming back for more
- Increased efficiency — When done correctly, agile manufacturing can help to reduce waste and improve overall efficiency throughout the production process. This leads to lower costs and higher profits
- Enhanced competitiveness — In today’s highly competitive marketplace, responding rapidly to changes can be the difference between success and failure. Agile manufacturing helps businesses stay ahead of the curve
- Higher levels of sustainability — Sustainability is becoming increasingly important to consumers and businesses. By being more efficient and waste-conscious, agile manufacturing helps businesses operate sustainably
Despite these clear advantages, agile manufacturing is not without its challenges. Perhaps the biggest challenge is that it requires a complete change in mindset for many organizations.
Traditional manufacturing approaches are based on long-term planning and predictability, while agile manufacturing requires short-term planning and adaptability. Fortunately, new technologies facilitate flexible manufacturing now more than ever before — let’s take a look at some before diving into the principles of agile manufacturing and how it compares to lean manufacturing.
How manufacturers use new technologies for facilitating agile production
As manufacturing processes have become more complex and globalized, manufacturers have become more agile to stay competitive.
New technologies are helping them do just that.
For example, additive manufacturing (AM), also known as 3D printing, is one of many technological advancements that have revolutionized manufacturers’ production of parts and products. AM offers several advantages over traditional manufacturing methods, including:
- Shorter lead times
- Reduced material waste
- Increased design freedom
These benefits have made AM particularly well-suited for agile manufacturing processes.
Many manufacturers are using AM to create a “digital inventory” of spare parts and components that can be quickly produced on-demand. This flexibility is crucial in today’s rapidly changing marketplace. Manufacturers must quickly adapt to new customer demands without incurring the high costs associated with traditional manufacturing methods.
In addition to 3D printing, planning and scheduling software is another important tool manufacturers use to stay agile.
This software helps manufacturers plan and optimize production schedules based on changing conditions in real-time. This is essential for reducing downtime and maximizing efficiency. By quickly adjusting production schedules, manufacturers can avoid costly delays and disruptions.
Overall, new technologies are helping manufacturers become more agile and responsive to the ever-changing needs of the marketplace.
3D printing and scheduling software are just two examples of manufacturers using new tech to stay competitive.
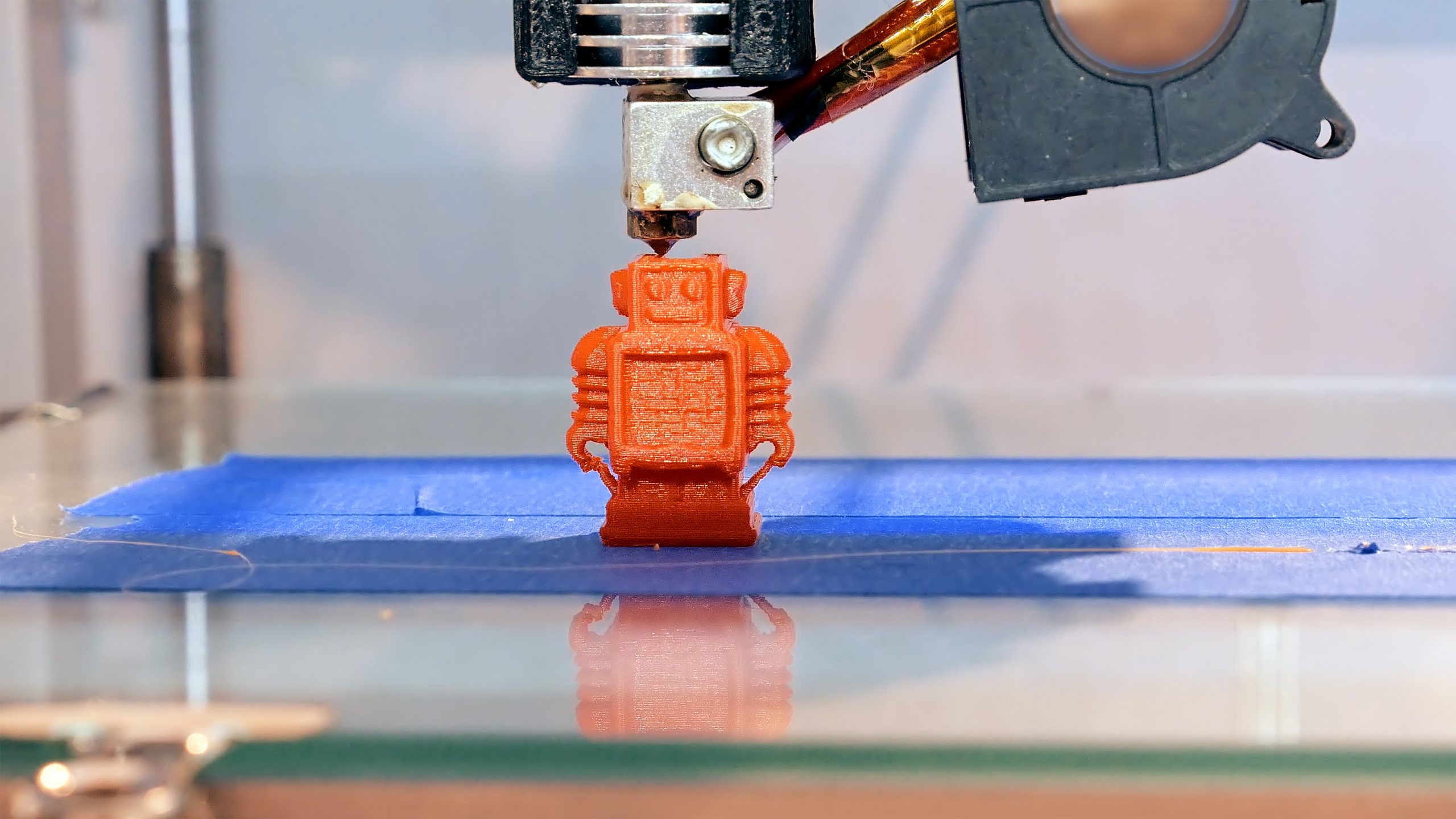
Lean vs agile manufacturing
It is important here to stop and discuss the differences between agile and lean methodologies because they can sometimes get intertwined.
Lean manufacturing puts a much greater emphasis on eliminating waste in the production process so that every step creates value for the customer. This includes things like overproduction, defects, and waiting time.
In contrast, agile for manufacturing focuses on creating a more adaptable, responsive process. That can sometimes result in lower waste as a byproduct of manufacturing agility but it is not its core focus.
Still, many companies will try to combine the best practices of both agile and lean manufacturing to create an even more efficient system.
The key principles of agile manufacturing
While responsiveness may be the goal, four key principles drive that adaptability in agile manufacturing.
1. Iteration
Perhaps the most important principle of agile in manufacturing is the iteration or the continuous improvement of products and processes.
This means that businesses are constantly looking for ways to improve their offerings based on customer needs and market data. Iteration helps businesses to avoid the common pitfall of investing too much time and resources into a product or process that may not be successful. By making small changes and then testing those changes, businesses can reduce the risk of failure while still moving forward toward their goals.
2. Bottom-up planning
In traditional manufacturing approaches, businesses typically start with a high-level plan and then work their way down to the details. In agile manufacturing, the process is reversed. Businesses start with the details and then work their way up to the big picture.
This bottom-up approach has several advantages:
- It allows businesses to be more responsive to changes since they can easily adjust plans based on new information
- It helps businesses make better use of resources since they can focus on what’s most important at any given moment
- It empowers employees that are on the ground floor to take risks and express their ideas since they have a better understanding of the situation
3. Flexibility
To be truly agile, a manufacturing organization must be flexible in all aspects of its operation.
This includes everything from the manufacturing process itself to the organizational structure and even the company culture. This is especially relevant in an era of mass customization and high competition — meaning more product variants and a high emphasis on quality management to maintain market share.
Flexibility is about more than just being able to quickly change direction or create customized products. It’s also about being able to adjust on the fly and accommodate unexpected changes. To do this, manufacturers need to have systems and processes in place that allow for easy adaptation in order to maintain competitive advantage.
4. Augmentation
Finally, manufacturers need to be able to quickly and easily add new capabilities to their existing processes. This could include adding new machines, software, or even people.
An agile manufacturing example might be a company that makes bicycles and needs to add a new assembly line to accommodate a new model of bike.
To do this quickly and efficiently, the company would need to have a system in place that allows them to easily add the new assembly line without disrupting their existing process. This could involve modular machines that can be connected or software that can be quickly installed and integrated.
softwareAgile techniques and tools like manufacturing
Enterprise resource planning (ERP) software or MRP software has come a long way in recent years to help manufacturers become more agile.
ERP systems like Katana now offer features that allow manufacturers to quickly and easily add new products, processes, and even locations. Production planning features combine with inventory and sales order management to align all business operations in one intuitive software solution.
In addition, ERP software can provide real-time visibility into every aspect of the manufacturing process. This allows manufacturers to quickly identify and solve problems as they arise. Most importantly, perhaps, is the ability for different pieces of software to integrate seamlessly with each other to create an end-to-end agile manufacturing solution.
For example:
A company might use one software package for product design, another for inventory management, one for material requirements planning, and yet another for shipping and logistics. In the past, these different software packages would have been difficult or even impossible to integrate.
But today, thanks to advances in technology, they can all communicate with each other and share data in real-time. This allows production managers and business owners to have a complete picture of their process from start to finish and makes it easier to make changes as needed.
While there are many different software packages and tools available to help manufacturers become more agile, ERP software is often considered the foundation upon which an agile manufacturing strategy is built.
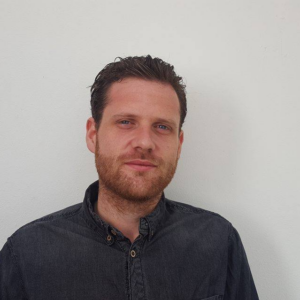
James Humphreys
Table of contents
Get inventory trends, news, and tips every month
Get visibility over your sales and stock
Wave goodbye to uncertainty with Katana Cloud Inventory — AI-powered for total inventory control