Going lean with cellular manufacturing
An important component of the lean manufacturing mindset, cellular manufacturing is a great technique for process improvement. Discover its strengths and how to implement it.
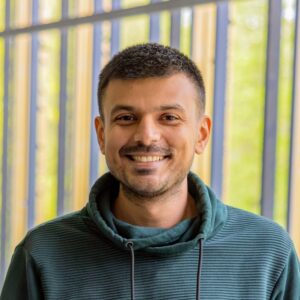
Tejas Shah
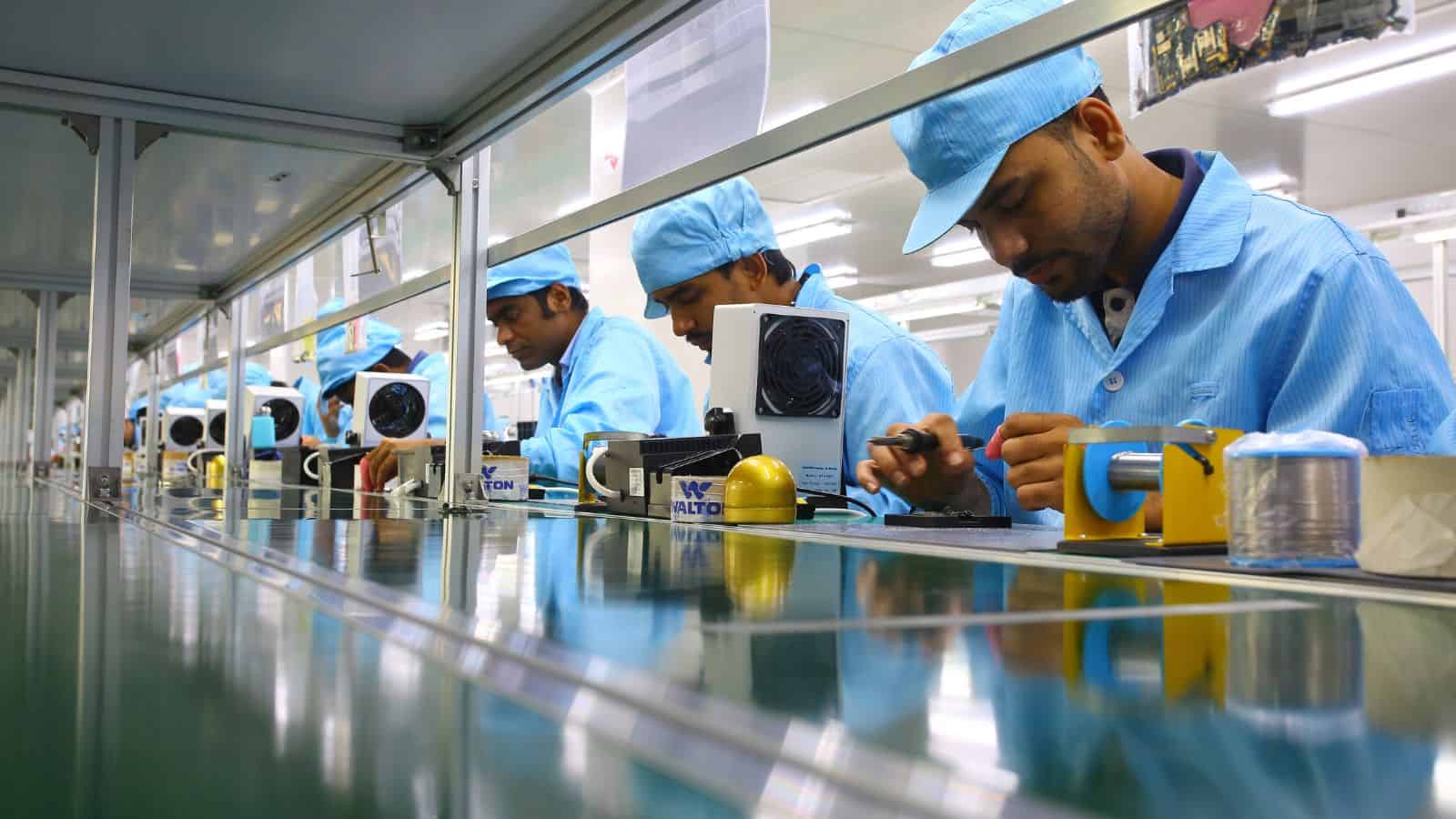
In biology, a cell is the smallest unit of life that can survive on its own.
Applying this idea to manufacturing gives us cellular manufacturing and the concept of creating units called manufacturing cells. These manufacturing cells can be thought of as miniature versions of a plant layout capable of producing a complete product or a product family.
Cellular manufacturing is a part of lean manufacturing ideology and can help grow your business by optimizing your production process. Let’s examine cellular manufacturing under a microscope and learn more about it.
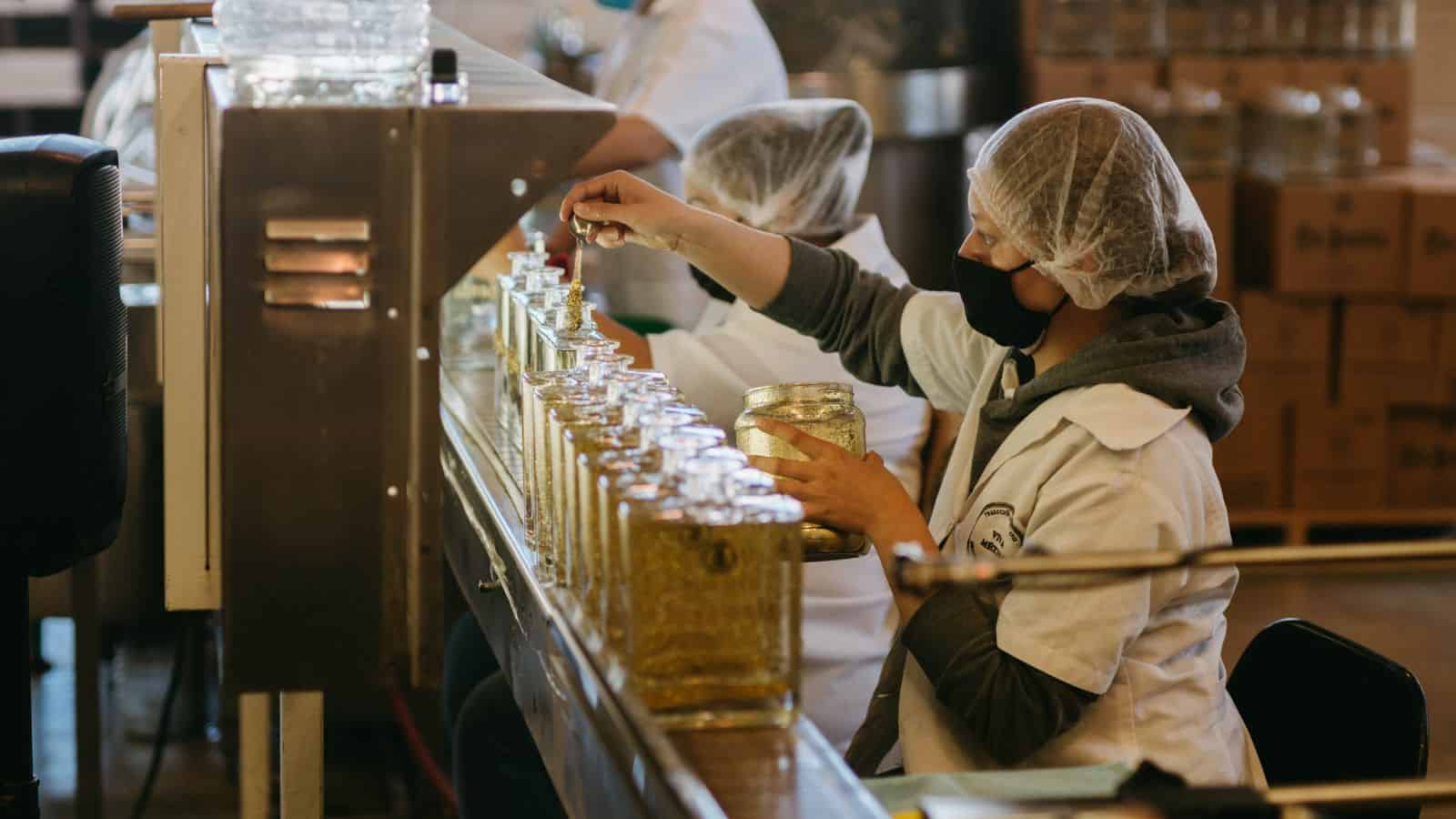
What is cellular manufacturing?
Cellular manufacturing refers to a manufacturing strategy used to arrange different machines functionally in specific geometric layouts and larger functional units known as manufacturing cells to optimize the production process.
The manufacturing cells are designed in such a way that each cell consists of all the machinery and workforce required to produce a product or a product family that is similar to each other. Since there are various machines in a unit, cellular manufacturing systems focus on training a cross-functional workforce that can easily operate all the machinery within a cell. This encourages the technicians to be creative and suggests process improvements, adding fewer defects and higher product throughput.
Cellular manufacturing evolved from ideas that were first proposed by Ralph Sanders. They then went on to mature into important concepts of lean manufacturing and lean six sigma principles due to their common focus on reducing waste and continually improving production processes.
Cellular manufacturing vs traditional layouts
Cellular manufacturing is in sharp contrast to the traditional manufacturing approach to factory route manufacturing layouts, in which functionally similar machines are grouped and placed close to each other.
Unfinished products have a larger travel distance between different groups of machines than the traditional approach. Also, defects pass through faster due to the slower communication about process improvements. These contribute towards multiple wastes of manufacturing, such as transport, motion, and correction.
In cellular manufacturing, a single cell can produce a finished product, and this drastically reduces materials handling and the travel distances of resources.
However, the traditional approach has a saving grace in the form of its robustness against machinery breakdown. In the cellular approach, a broken down machine could take the entire cell offline until the machine is repaired. That being said, at larger workloads, cellular manufacturing systems outperform traditional approaches by miles simply because of their flexibility and efficiency improvements.
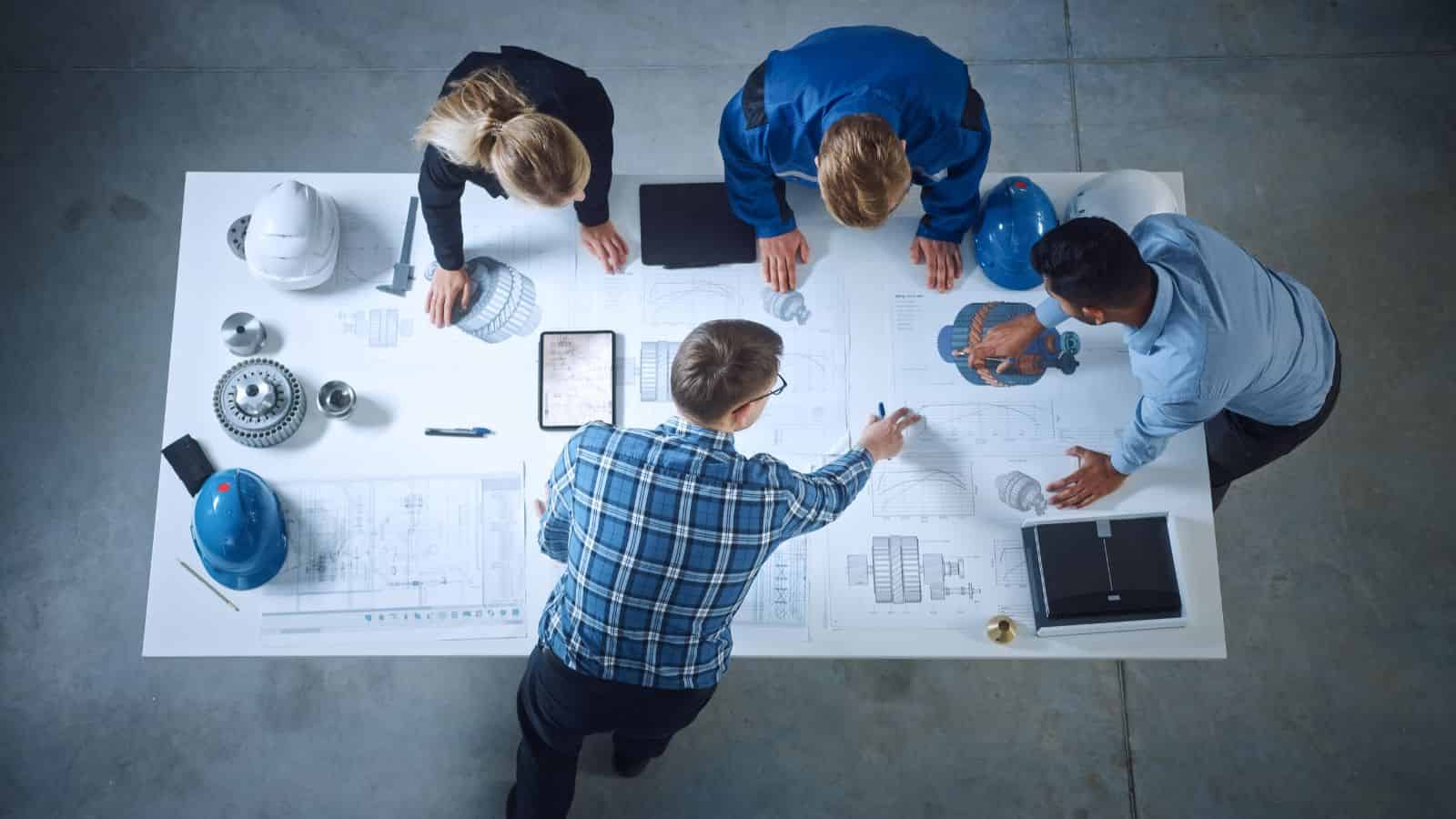
5 advantages of cellular manufacturing
Here are some advantages of implementing cellular manufacturing in your lean manufacturing workflow:
- Enhanced production environment and quality control
- Improved capacity to produce high-volume, high-variety products at a fast pace
- Substantial reduction in manufacturing lead time and waste
- Smaller work-in-progress (WIP) inventory
- Develop a highly versatile and efficient workforce
3 disadvantages of cellular manufacturing
As with everything, there are disadvantages to cellular manufacturing as well. Here are three:
- Prone to production bottlenecks in case of machinery breakdown
- Errors in the setup can lead to a loss of efficiency instead of the promised improvements
- The setup time can be long since moving machinery and training take time
Cellular manufacturing layouts
As described earlier, the core idea of cellular manufacturing is to arrange equipment and workstations in specific geometric patterns in order to optimize the production process. So let us now look at some of the most common cellular manufacturing layouts or cell layouts to understand which ones suit your needs.
I-shaped cell
The I-cell, also known as the linear cell, is an arrangement of machines in a linear order. Being one of the simplest of the cellular layouts, this arrangement is the closest to having multiple assembly lines. It is great for products where the sequence of operations is straightforward, and materials don’t need to move back and forth between machines.
Additionally, the I-shaped cell can be configured so that technicians can work on both sides of the cell.
U-shaped cell
The U-cell, as the name suggests, is when the machinery is arranged in the shape of the letter U. Although this is similar to the linear cell, the U-shaped cell is more compact and has a smaller footprint on the shop floor. In addition to the space savings, this type of cell layout allows for better communication between technicians since they are much closer to each other than in the I-shaped cell.
O-shaped cell
Also known as the Cage, this is similar to the U-shaped cell but with machines arranged in a rough circle. Usually, these cells are managed by only one technician who is highly skilled at using all the machines in the cage. It is suited for products that require multiple passes through the machines.
T-shaped cell
When products need raw materials from different sources, or when products need to be slightly specialized it is normal to have a T-shaped cell. Cells designed in this pattern can be configured to either have a converging or diverging flow of materials.
S-shaped cell
This layout is used when you want to work around obstructions or irregularities on the shop floor and you still want to implement cellular manufacturing. Although the exact shape of the cell itself doesn’t matter so much in this arrangement, the idea is to have a small logical unit of production.
Putting the lean manufacturing principles into action
Implement your lean manufacturing principles easily by using a live inventory management system for real-time overviews of inventory and operations.
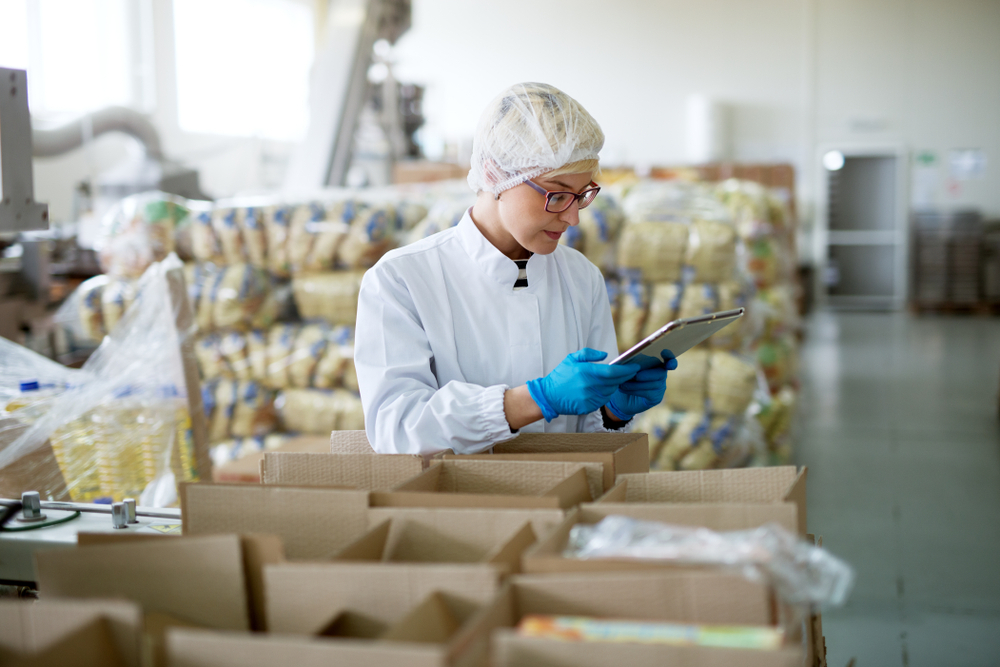
Implementing cellular manufacturing
Since cellular manufacturing is part of the lean inventory ideology, the implementation process should start with understanding lean manufacturing principles.
With that covered, in order to implement cellular manufacturing, your focus should be on mapping value streams and understanding how materials and resources move across your shop floor. This is where cloud inventory software like Katana can come in handy with its shop floor control features that help you understand and track the patterns.
However, Nancy Hyer and Urban Wemmerlöv, who are distinguished production process researchers, note that implementing cellular manufacturing has a “hard” side and a “soft” side. The hard side of things is the technology, the machinery, and the processes themselves. While the soft side is composed of people and the soft skills required to work with the hard side. Changing the soft side is often far more difficult than moving heavy machinery and modifying processes.
However, given the advantages of cellular manufacturing, it could prove well worth the effort to undergo this large change. Thankfully, tools like Katana can make optimizing the hard side of cellular manufacturing easier, allowing you to focus your energy on the soft side. Request a demo and see how Katana can help you optimize workflows and grow your business.
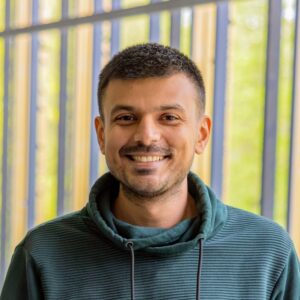
Tejas Shah
Table of contents
Get inventory trends, news, and tips every month
Get visibility over your sales and stock
Wave goodbye to uncertainty by using Katana Cloud Inventory for total inventory control
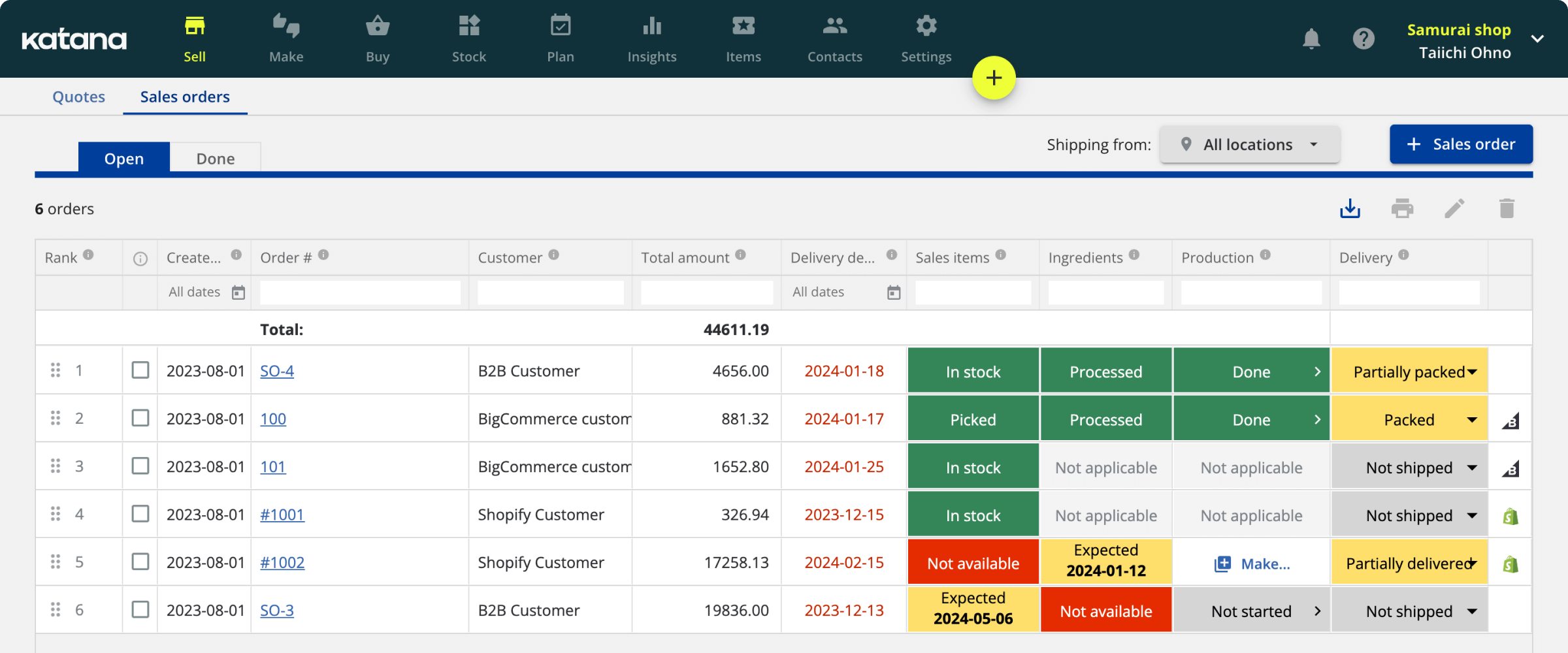