Project management for manufacturing: The five stages of planning
Using project management for manufacturing is a great way to manage your time and resources efficiently while making sure you reach your goals in an efficient manner.
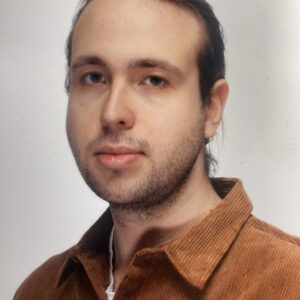
Erik Väli
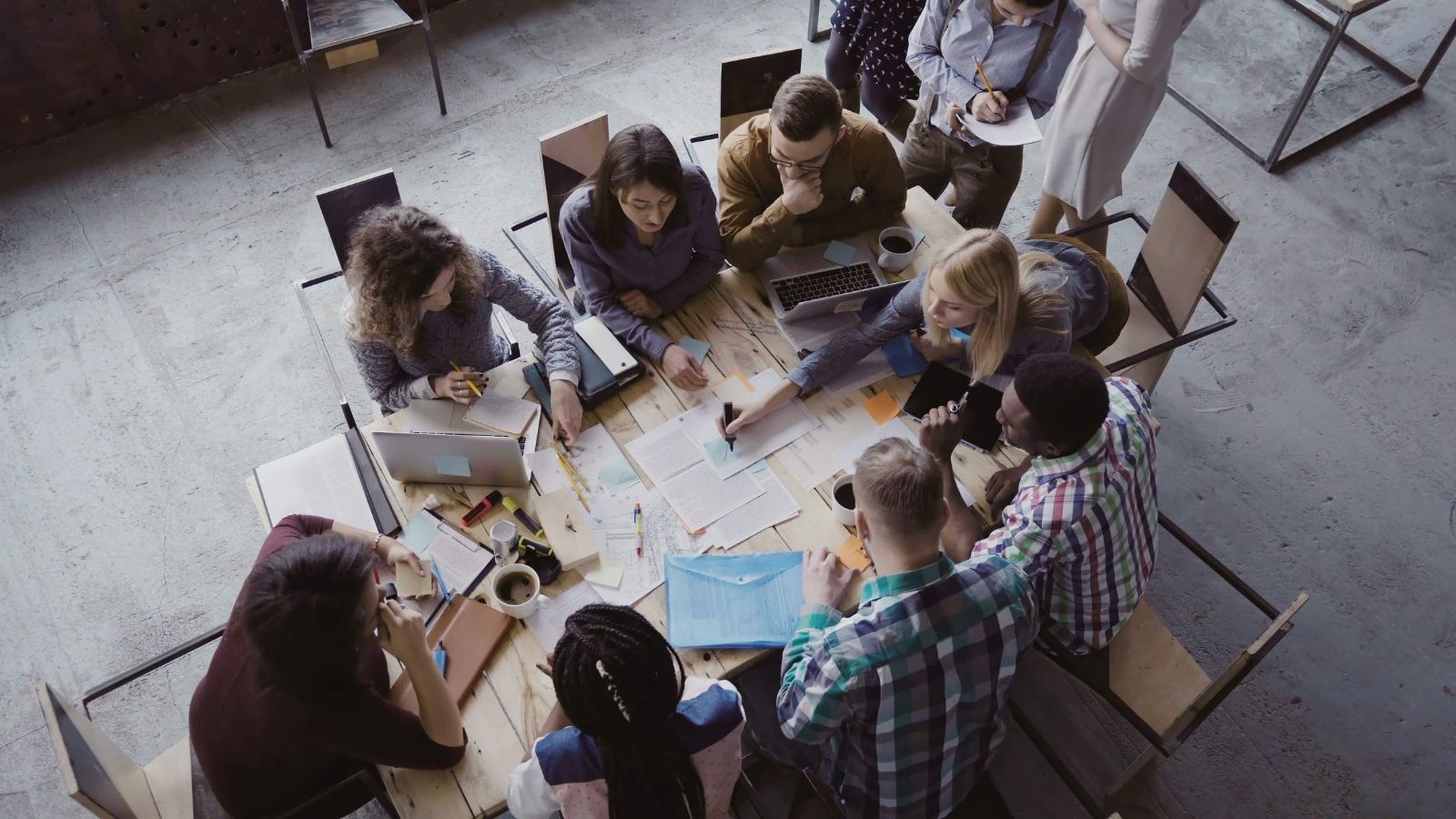
You have manufacturing and production goals you want to reach. Maybe they are:
- Introducing a new product to your catalog
- Making your workplace more efficient
- Reducing waste in your manufacturing process
To make sure that goal is reached, you need to plan and schedule your projects, outline the processes, and track each project from start to finish.
This is where project management for manufacturing comes in. In this article, we’ll take a look at the steps involved in project management and how they can be applied to manufacturing.
Complete control at your fingertips
The Katana Shop Floor App gives manufacturers a real-time master planner and a clear communication channel to their operators from anywhere with an internet connection.
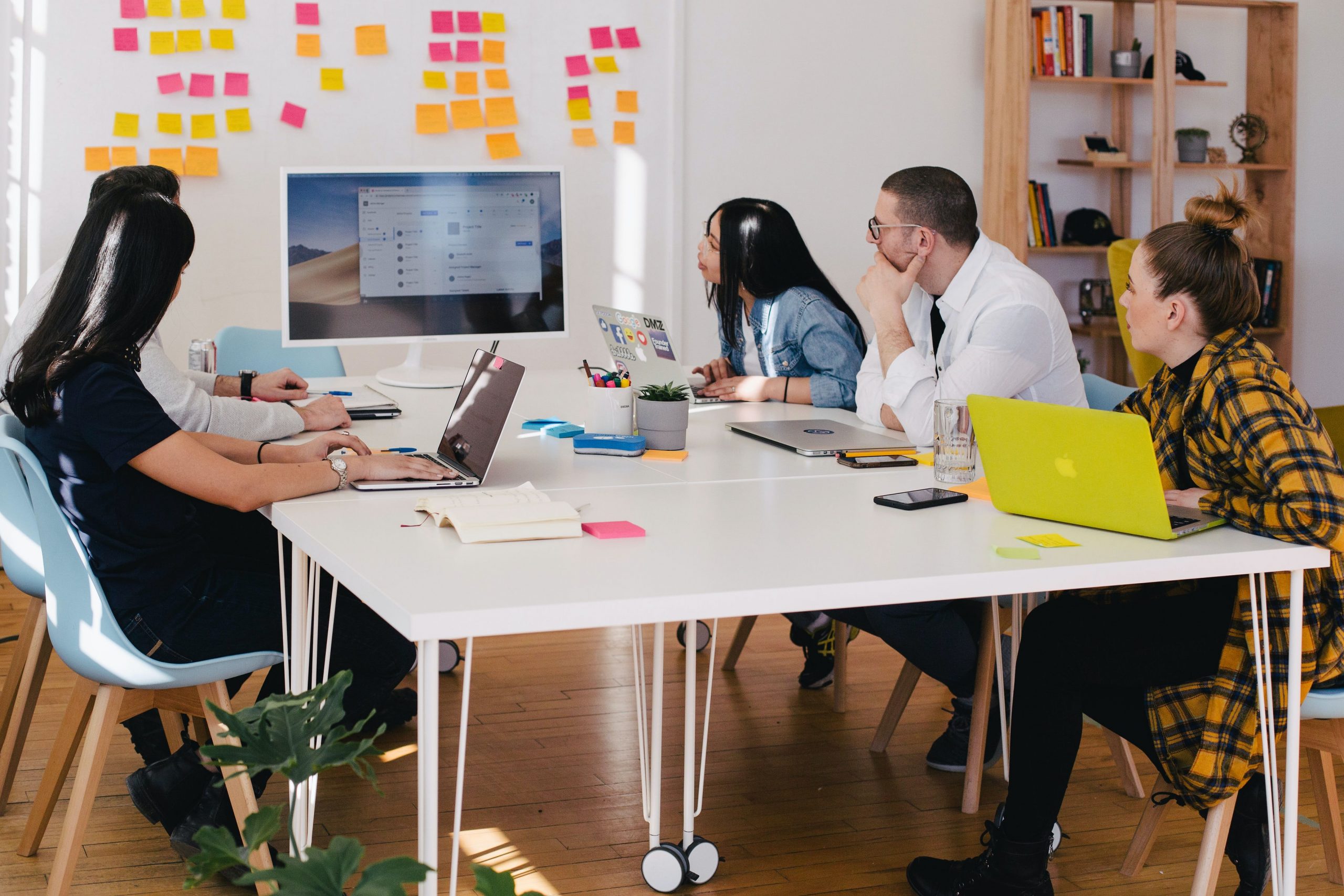
What is a project?
Projects are a series of tasks that have to be completed in order to reach a specific goal. A project can be basically anything, from building a house to writing a book to implementing new safety procedures in your production line.
But the one thing that all projects have in common is that they involve some sort of plan in order to bring all of these tasks together. A plan that will hopefully one day come together to reach the goal outlined in the project.
But seeing that plan through requires a bit of effort and organization. This is where you can benefit from project management.
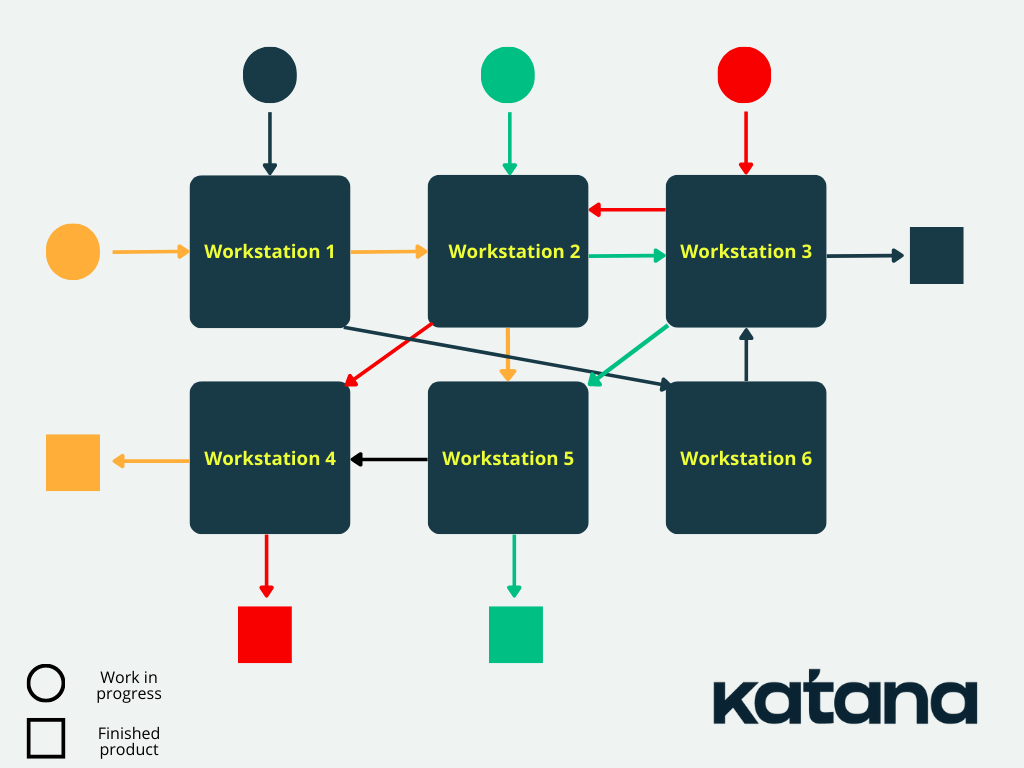
What is project management?
Project management is essentially a way to keep your project on track and make sure all the smaller tasks and processes that are part of that project stay on schedule. It is meant to help you follow through with the project, so you actually make it to the finish line.
Project management uses a mix of different methods, techniques, systems, software, and tools to make sure a project is completed. A specialized project management team or project manager will usually handle this.
Almost every goal an individual or business wants to achieve needs project management. And your manufacturing projects are no different.
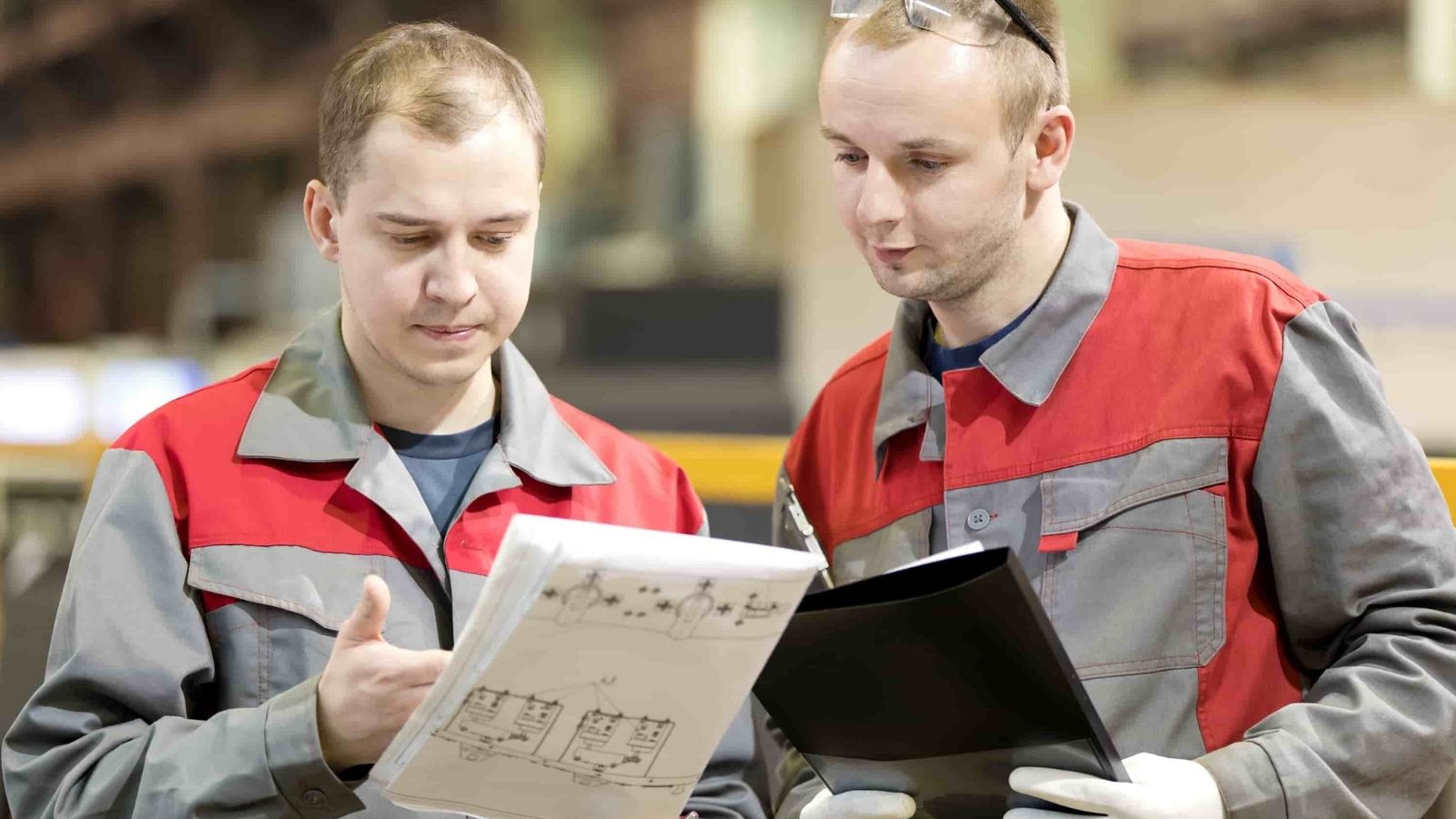
What does project management look like in manufacturing?
Now that we have a basic understanding of project management as a whole, let’s get more specific here and take a look at project management in manufacturing.
The exact details of project management for manufacturing are going to vary depending on your particular needs, such as what type of manufacturing process you use, the kind of goods you produce, and, most importantly, what kind of project you are actually hoping to complete. But there are still many commonalities here that we can bring out.
For companies that deal with production or manufacturing, in the case of contract manufacturers, good project management can improve risk management, reduce waste, improve overall efficiency on the production line, and overall, just help make sure you can see your manufacturing projects through to completion.
The five stages of project management for manufacturing
Manufacturing project management is usually broken down into five stages, which outline how the project will be managed. These stages are usually easily applicable to any manufacturing project.
Let’s go over each of the stages of project management in more detail, and apply them to manufacturing.
Stage 1 — Initiating the project
Initiating the project, despite what the name might imply, is less about charging headfirst into things and starting your project. It’s actually more about making some preliminary preparations to make sure you have everything you need before you really get the ball rolling.
Here’s where you’ll be setting up your goals and figuring out which resources you’re going to need to actually follow through with your project. You’ll go over:
- What are your actual goals
- What is the timeline of the project
- Which deliverables will you need
- What are your expectations
- What are your limitations
Essentially, you’re going to be figuring out the requirements, limits, and goals for your project during this stage. It’s generally a good idea to be as detailed as possible during this stage, as that will help your project management team know exactly what they’re getting into and what they need to get there. This will, in turn, ensure the next steps go as smoothly as possible.
Stage 2 — Creating a plan for the project
Once you’ve figured out what you want to achieve and what you need to achieve it, it’s time to put together a roadmap on how you’re actually going to be getting there.
A good idea here is to choose a manufacturing methodology that suits your project and your specific needs. For example, if the goal of your project is to eliminate waste in your manufacturing process, you might want to look into implementing some lean manufacturing principles in your project.
How strictly you stick to the methodology you choose is up to you, of course. Ultimately, the most important thing here is to put together a clear step-by-step plan on how you’re going to tackle the project.
Stage 3 — Executing the project
You’ve figured out what you want to do, what you need to do, and how you’re going to get it done. Now it’s time to start making the project a reality.
Executing the project is all about communication. You or your project management team will have to make sure everyone knows what they’re supposed to be doing and when they’re supposed to be doing it. Essentially, you have to make sure everyone sticks to the plan.
You’ll need to pick the right people and tools to complete this. Since it can be difficult to make sure all of the planning you did during the earlier stages goes to plan, you want to use a tool like manufacturing ERP system to help you out.
And if you’re a project manager yourself, you’ll want to keep your client updated during this stage of the project. So, once again, communication is key here — the manufacturer, the project management team, and the workers should hopefully be keeping each other in the loop.
Stage 4 — Monitoring the project
Now that everyone is hard at work, it’s time to make sure you don’t lose that momentum. There’s a bit of accountability involved here — this step is about ensuring things get done in the right way.
In manufacturing, this is important not only for the sake of efficiency but to make sure everything in your project gets done safely and without causing any hiccups along the way. If there are any mistakes, you’ll want to know about them as soon as possible to avoid having all your hard work fall apart.
If you’re using software to help you out with project management and some form of manufacturing methodology, this is where they can really help you out. Production tracking software will help you keep a close eye on the process and manage things with less of a headache, and your manufacturing methodology will give you a clear framework to follow.
Stage 5 — Closing the project once it’s all done
Congratulations! You’ve followed through with your plan without any major hiccups. But it’s not quite time to celebrate yet, as we still need to get through the last stage.
Closing the project involves a bit more than wrapping up and popping the champagne. Now that everything is done, you’ll want to make sure that:
- It was done correctly
- There are no unresolved issues
- It’s delivering the results that you were hoping for
And since we’re talking about project management in manufacturing and production specifically, it doesn’t hurt to double-check once again that everything we’ve implemented through the project is working safely.
After you’ve finished reviewing everything, there’s still one last chance to go back and iron out any unresolved issues. Once you’re sure everything checks out, it’s time to officially conclude the project, write everything up, and why not pop open the champagne?
Want to see Katana in action?
Book a demo to get all your questions answered regarding Katana’s features, integrations, pricing, and more.
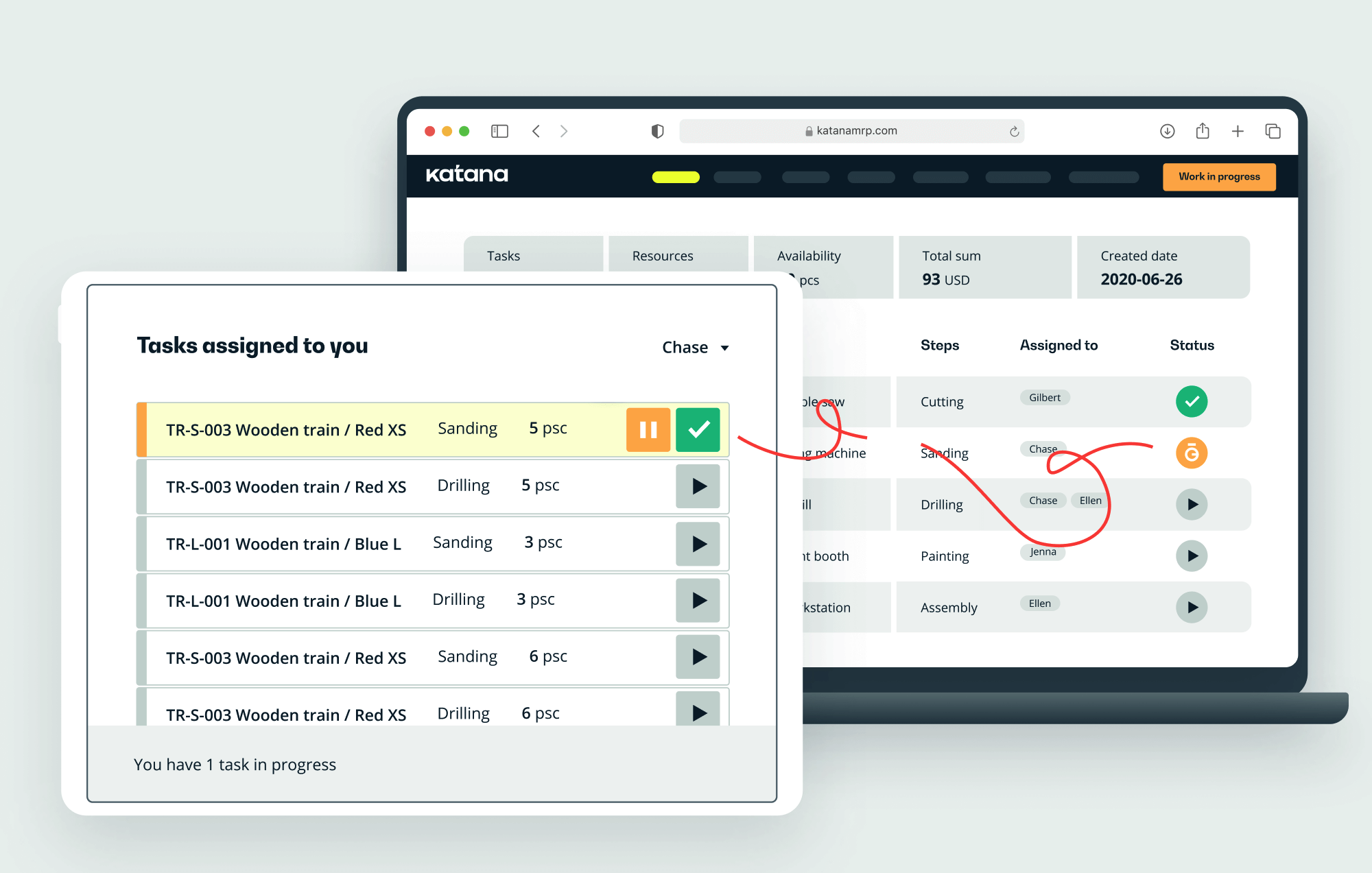
Using manufacturing ERP software to help with project management
Even though we’ve broken down project management for manufacturing, the reality of course, is that this is just a very general overview of how things work.
Once you start to actually follow through with your projects, things are going to get a lot more complicated. You need to make sure all your workers know their specific roles in your project and keep an eye on things on the ground level.
This is where using Katana’s Shop Floor App can help you and your team execute and monitor your project and make sure everything goes according to plan.
With features such as live production status updates, you can get a clear overview of your shop floor, making sure everything is going to plan.
You can also add your employees to the Shop Floor App as Operators and give each Operator their own task list. This ensures everyone involved in your project knows their tasks and responsibilities.
Give your business the best chance of success. Book a demo with Katana, and take your manufacturing business to the next level.
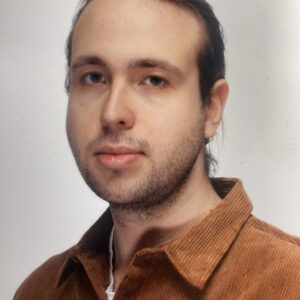
Erik Väli
Table of contents
Get inventory trends, news, and tips every month
Get visibility over your sales and stock
Wave goodbye to uncertainty by using Katana Cloud Inventory for total inventory control
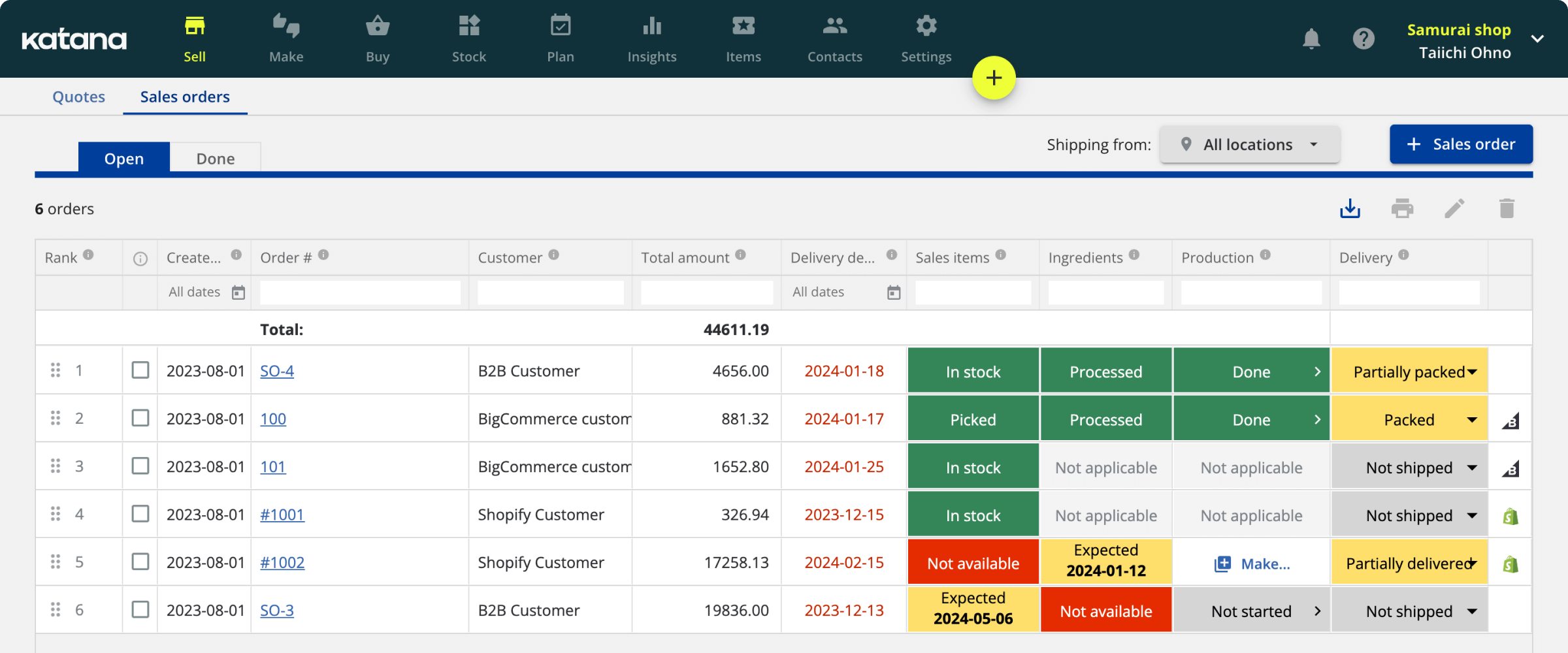