Manufacturing control: Creating a plan to optimize output
Manufacturing control to ensure all your products follow the same plan and the processes are executed accordingly for consistent, high-quality results.
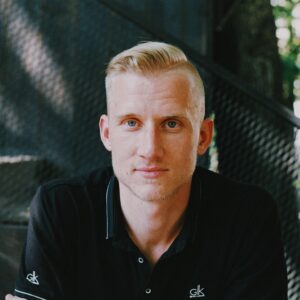
Henry Kivimaa
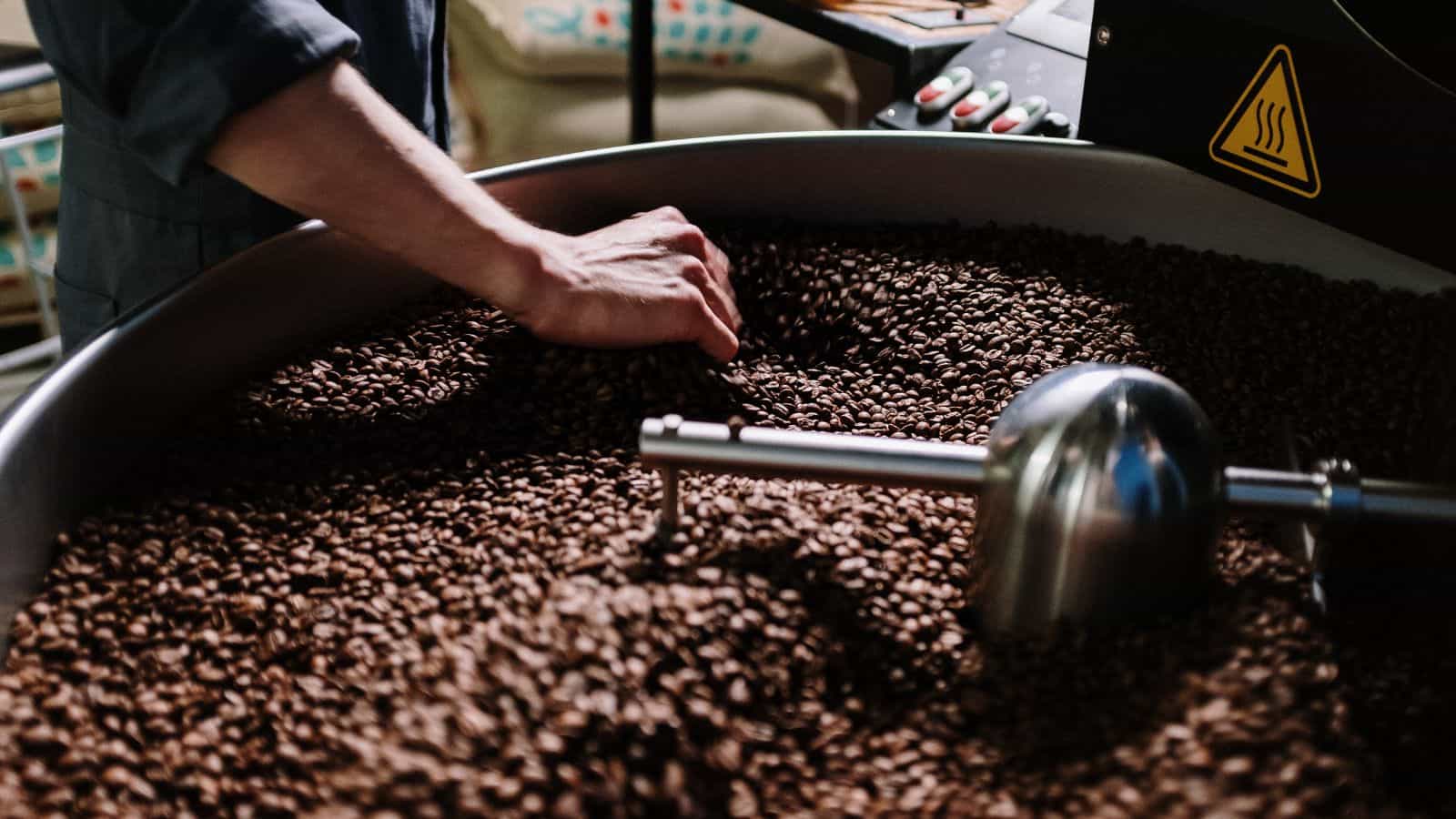
If you’ve ever tried to run a manufacturing business, even one out of your own home, you will know how challenging it can be to calibrate output properly.
Even on something as simple as baking cookies, variables out of your control may lead to spoiled batches or items that don’t live up to your standards.
Manufacturing control, the steps taken to ensure that each successive output is the same as the last, can be a daunting task. But with the right processes in place, it doesn’t have to be.
To create an effective manufacturing control plan, you will first need to understand your process and its capabilities. Once you have this baseline understanding, you can begin to implement the necessary controls to ensure that every batch meets your expectations.
What is manufacturing control?
Manufacturing control is the combination of technologies and methods used to manage manufacturing processes. It includes both the hardware and software components necessary to monitor, control, and optimize production.
Manufacturing process control aims to produce products that meet or exceed quality standards while minimizing waste and maximizing efficiency.
To do this, manufacturers rely on various sensors, controllers, actuators, and other devices that collect data about the production process. This data is then analyzed to identify trends and issues that can be addressed to improve quality and efficiency.
The four parts of the manufacturing process
The four elements of any manufacturing process are:
- Inputs
- Controlled variables
- Uncontrolled variables
- Outputs
Let’s take a closer look at each.
Inputs
The first step in any manufacturing process is to gather the raw materials and other inputs that will be used in production. This includes everything from the individual components that will be assembled into a final product to the packaging materials and labels used for finished goods.
These inputs exist as the basis of all process control in manufacturing, as without them, the entire system will not function. No matter how strong your controls are down the line, without carefully inspected and managed inputs, the entire process is at risk of being thrown off course.
In the cookie example, the inputs might be:
- Flour
- Sugar
- Eggs
- Baking powder
- Butter
- Energy (for the oven)
If the butter is rancid or the eggs are spoiled, the cookies will not come out right, no matter what else you do.
Want to see Katana in action?
Katana’s batch tracking software has everything you need to ensure all your products have consistently high quality.
Controlled variables
Next, we have controlled variables. These are the elements of the manufacturing process that can be manipulated in order to achieve the desired results.
In our cookie example, the controlled variables might be the:
- Recipe
- Baking time
- Oven temperature
By changing these factors, you can affect the outcome of your product.
However, it is important to note that there is a limit to how much you can change a controlled variable without affecting other aspects of the process. For example, if you were to double the amount of baking powder called for in a recipe, the cookies would likely come out too dry.
This is where process knowledge and experience come into play. To be successful, manufacturers must understand how controlled variables interact with one another and what effect each has on the final product.
Uncontrolled variables
In contrast to controlled variables, uncontrolled variables are those elements of the manufacturing process that cannot be changed.
In our cookie example, these might include the attention of the baker or the ambient temperature and humidity in the kitchen. While there may be nothing you can do to change these immediately, understanding how to either counteract them or account for them in your final product is critical.
Outputs
Finally, there are outputs. These are the manufacturing process results that can be measured and quantified.
In our cookie example, outputs might include the number of cookies baked, their average weight, or their average diameter. It is important to note that not all outputs are physical products. In many cases, outputs may also include data or information that is generated by the process itself.
For example, a machine tool might generate a log of the speeds and feed rates used during a manufacturing run. This information can be used to improve future runs or diagnose issues with the process.
While the most common might be yield and quality, other important outputs might include manufacturing cycle time, energy usage, or material waste.
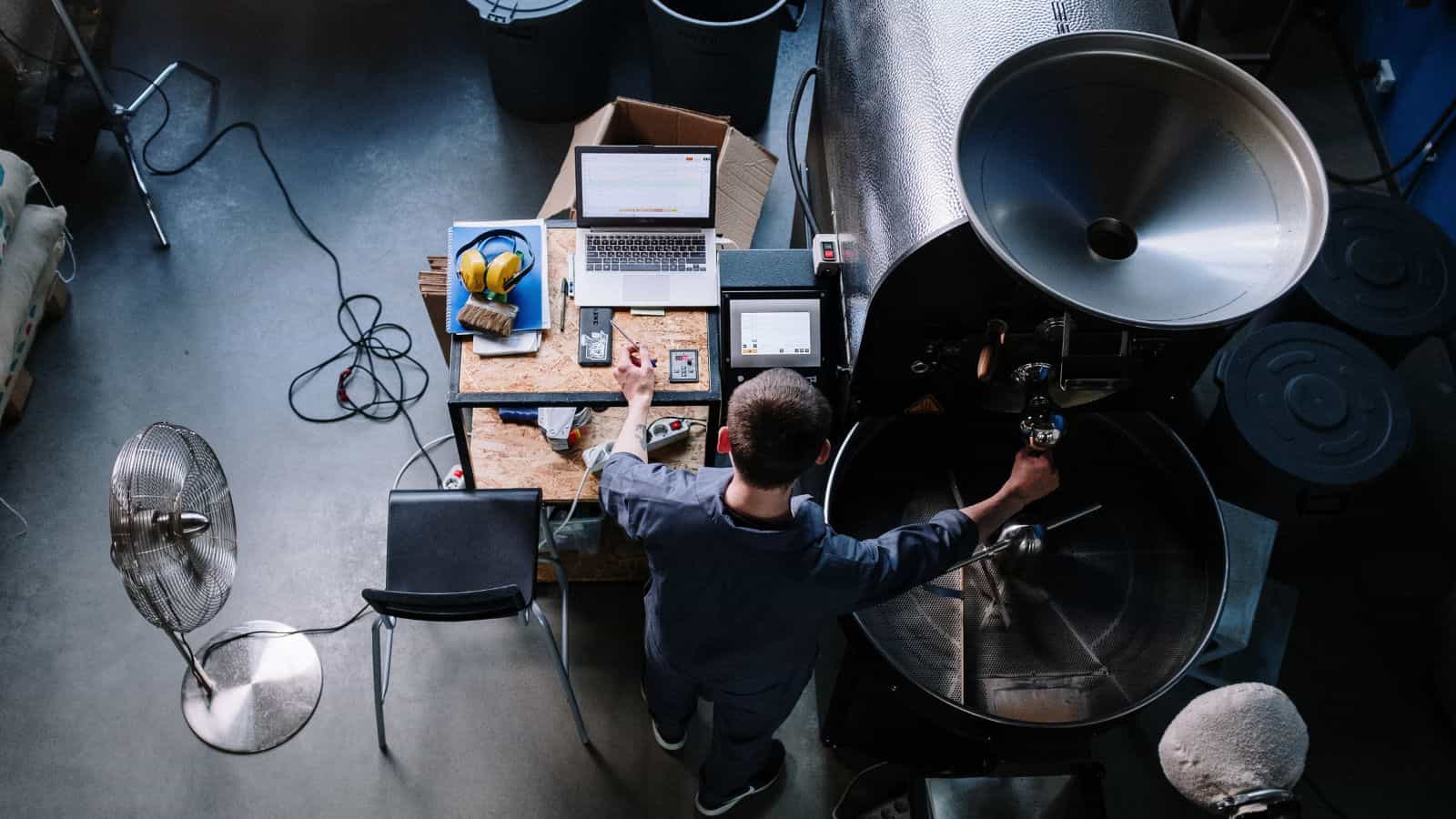
What is a manufacturing control plan?
A manufacturing control plan is a document that outlines the specific steps that will be taken to ensure that a manufacturing process meets all of the required outputs.
This plan must take into account all of the different variables that can affect the process, both controlled and uncontrolled, and must be tailored to the specific process being used.
A good control plan will address all of the following questions:
- What are the inputs to the process?
- What are the controlled variables?
- What are the uncontrolled variables?
- What are the outputs of the process?
- How will the process be monitored?
- Who is responsible for each step of the process?
- What should be done if an issue is identified?
A well-designed control plan will provide a clear and concise roadmap for ensuring that the manufacturing process runs smoothly and meets all quality requirements. Outlining the steps that need to be taken allows manufacturers to avoid potential problems and react quickly if an issue does arise.
Incoming quality control
There are three stages at which quality control can be managed. The first is incoming, as raw materials and supplies are brought into the facility.
To ensure that only quality materials are used in the manufacturing process, it is important to put into place a system for incoming inspection. This inspection should be conducted by a trained individual who knows what to look for and how to document any issues that are found properly.
If an issue is identified, the material should be either returned or quarantined until it can be determined whether or not it meets the required specifications.
Assembly quality control
Next is during the assembly process. This is where most products are put together and will have several quality checks throughout.
A clear understanding of how the product should be assembled and what tolerances are acceptable is critical. This will help to ensure that each component is put in its proper place and that no steps are missed.
If any issues are identified during this stage, it is important to take corrective action immediately to avoid further problems.
Outgoing quality control
Finally, there is outgoing quality control. This is the last chance to catch any issues before the product ships out to the customer.
A thorough inspection should be conducted at this stage, and any product that does not meet the required specifications should be fixed or scrapped.
It is also important to document any issues that are found so that they can be addressed in future batches.
By implementing a manufacturing control plan, you can help to ensure that your process runs smoothly and that all products meet the required quality standards. This will help to improve your reputation and build customer trust.
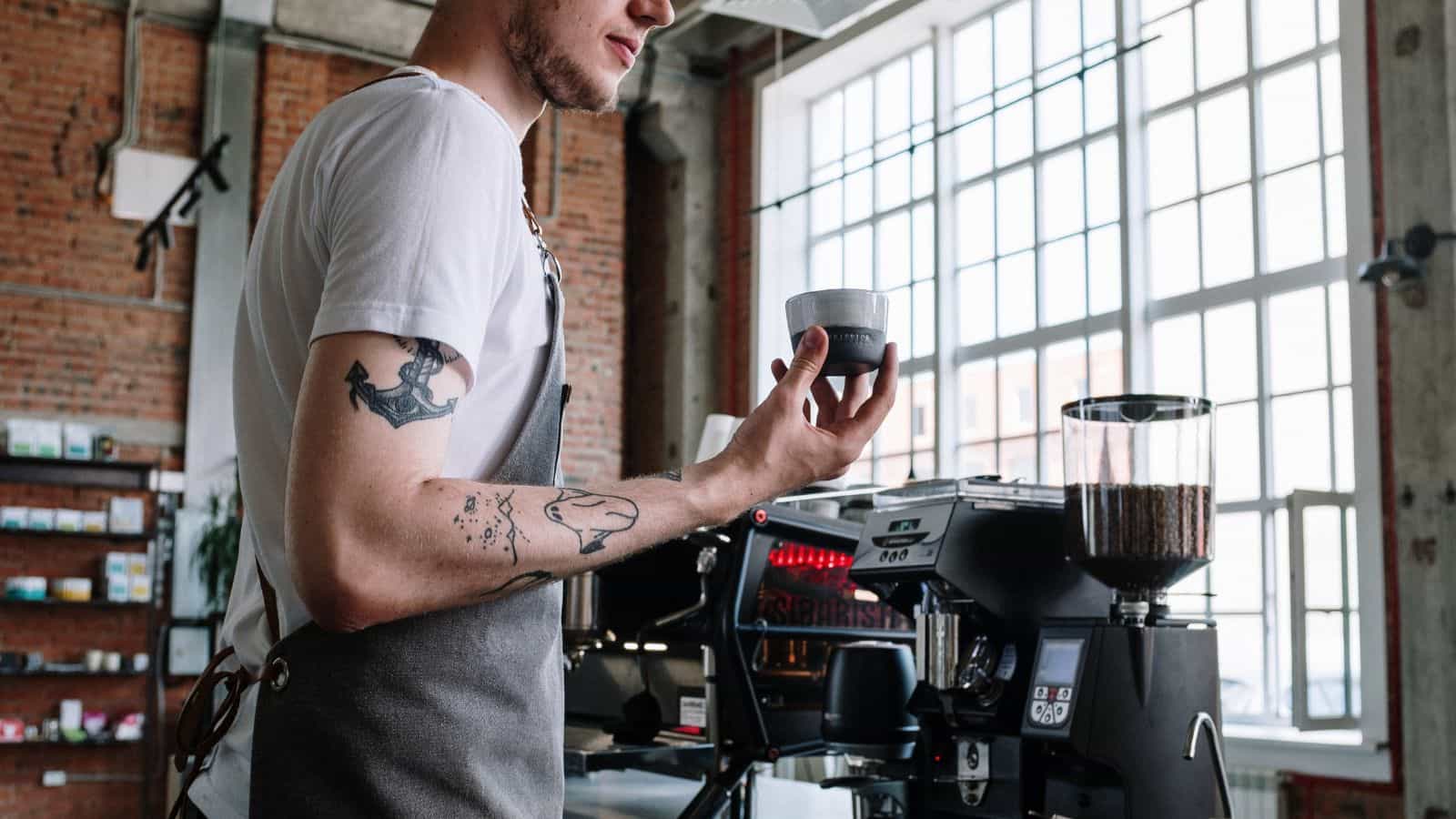
Example of a manufacturing control plan
Each company will have its specific guidelines and requirements, but a handful of things need to be included in every manufacturing control plan. If you are new to process control management, create a spreadsheet with the following.
Process name
In the lefthand column, list the process or item name. This can be something as simple as “butter” or “mix dry ingredients” for a baking recipe.
Tool
This is the machine or tool used for completing this process. In a more complicated business, it might be listed as an “assembly line” or “injection molding machine.” If it is a component that is created elsewhere and procured, it might be listed as “vendor” or “outsourced“.
Control process
Next is the process that will be used to measure and maintain the quality of this output. Does it require a visual inspection or a measurement with a ruler or caliper? Is it weighed on a scale or tested for functionality?
Tolerance
For many control inspections, there will be a binary decision. It works, or it doesn’t. But for many others, there will be a level of acceptable quality. This is known as tolerance, and it should be clearly defined in your manufacturing control plan. For instance, if a cookie is a little flatter than usual, it might still be within the bounds of acceptable quality. But if it is burned, it has failed the inspection.
Measurement technique
Here, list exactly how the item data will be measured. Will a visual inspection also require photographic documentation? Does the testing machine automatically log the stress data, or will it need to be manually entered into a computer?
Sampling
In this column, list what percentage of the total output will be subject to this control process. In some cases, it might make sense to test every single item. But in others, a random sampling might be more practical.
A visual inspection of each one is costly for a company that produces 1,000 cookies an hour. But a sample of 10% or 100 cookies every hour might be more manageable.
Reaction plan
The final thing that every manufacturing control system must have is a concrete reaction plan. If the butter arrives rancid, is it wasted or sent back to the supplier? What happens if a batch is burned because of an operator error?
Keep in mind that this is just a basic outline of what should be included in your manufacturing process control plan. You will also need to consider other factors, such as how often these checks should be done and who will be responsible for doing them.
But with a little bit of planning and forethought, you can ensure that every batch of cookies — or any other product — meets your high standards.
Improving a manufacturing control system
Of course, there are also ways to automate much of this and free up your time to focus on other aspects of the business. Enterprise resource planning (ERP) software solutions like Katana can help you track all the moving parts in your manufacturing process, from raw materials to finished products.
With Katana, you can create a digital version of your manufacturing process control plan and put it into action with just a few clicks. The software will guide you through the steps of creating control specifications, assigning tasks, and scheduling production runs.
And because it’s all done digitally, you can easily make changes and adjustments as needed — no more wasted paper or lost data.
If you’re ready to take your manufacturing business to the next level, Katana can help. Get started by booking a demo and see how Katana can streamline your operations and improve your output.
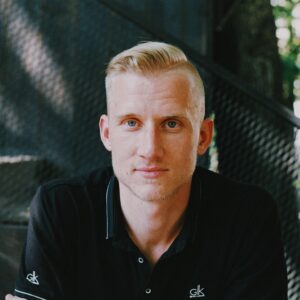
Henry Kivimaa
Table of contents
Get inventory trends, news, and tips every month
Get visibility over your sales and stock
Wave goodbye to uncertainty by using Katana Cloud Inventory for total inventory control
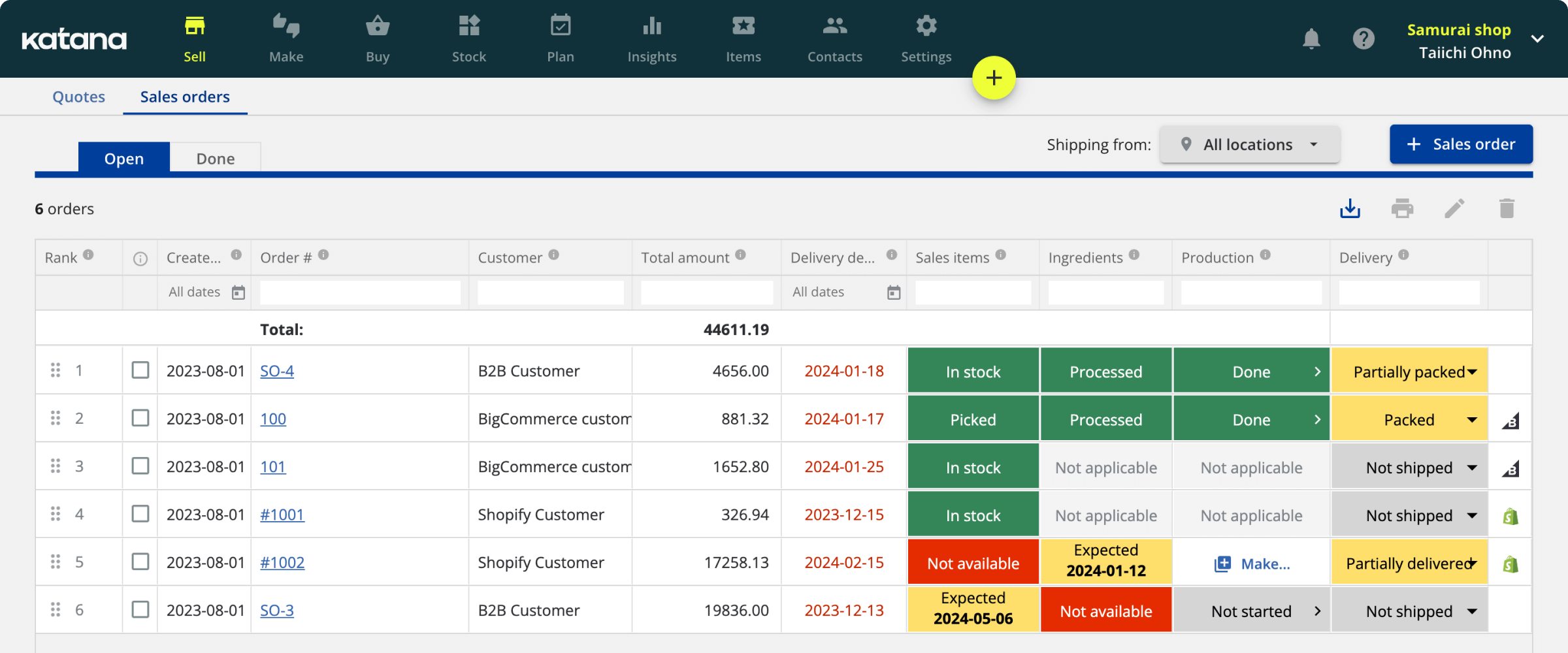