Lean warehousing — Trimming down costs by getting rid of waste
Lean warehousing, following other lean principles, is the attempt to remove any waste from within your warehouse. Read all about how here.
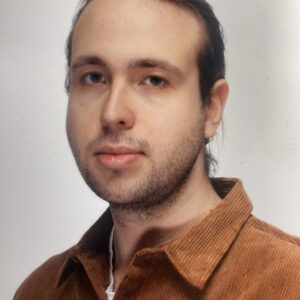
Erik Väli
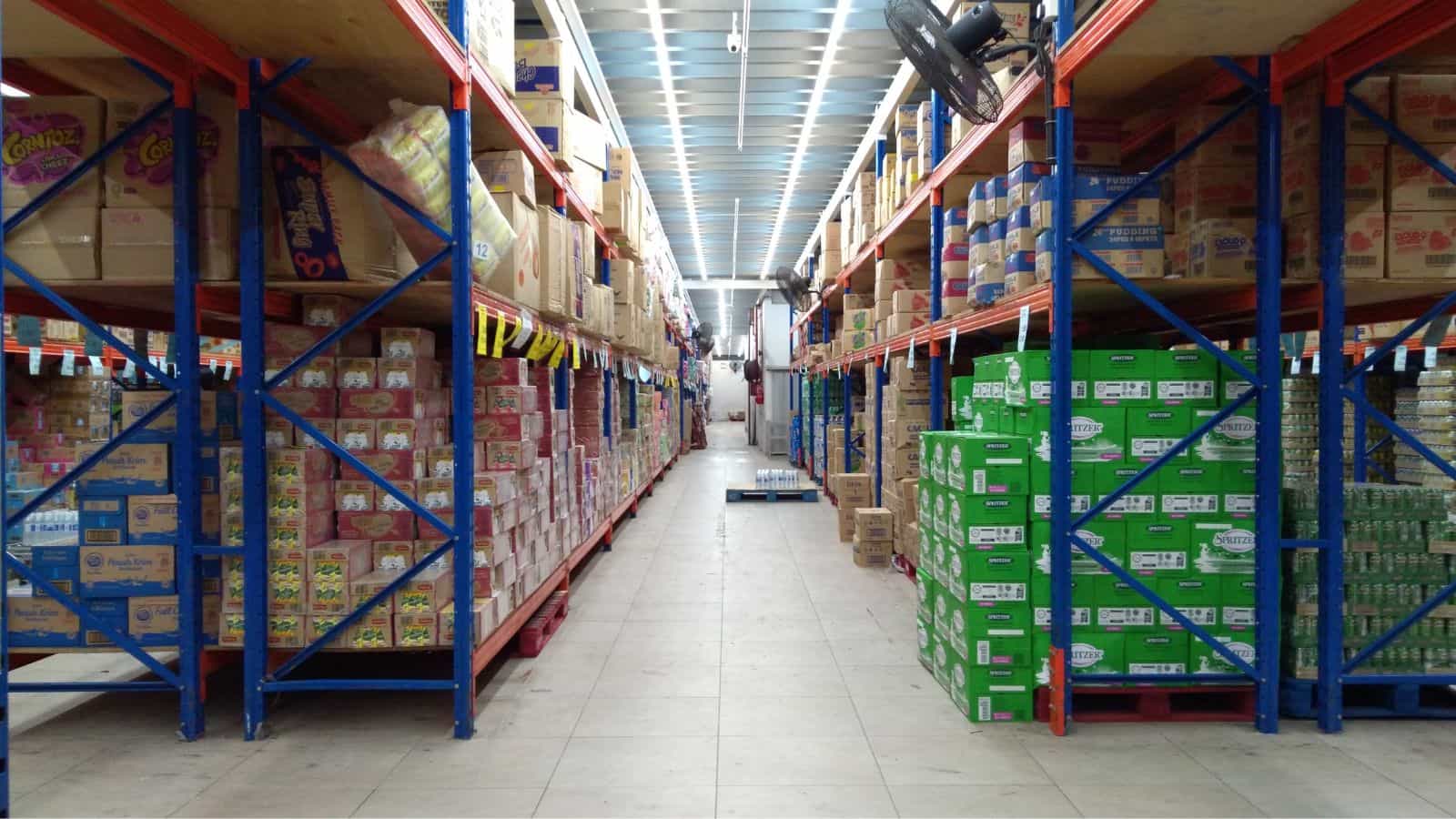
Since the dawn of time, when one caveman sold a particularly fine spearhead to another caveman, manufacturers have faced all types of warehousing and manufacturing challenges.
For example, many businesses that would have once relied solely on traditional storefronts have had to adapt to the growing demand for delivery services.
But this is just one change among many that manufacturers have had to implement in a relatively short amount of time over the last couple of years. And all of these rapid changes can easily lead to the day-to-day management of your warehouse getting out of hand as your business struggles to keep up.
Thankfully, there is a solution in the form of lean warehousing.
Katana’s cloud inventory software
Katana is trusted by 1000’s of businesses to automate their inventory management, sales, and manufacturing processes. Get a demo and take your business to the next level.
What is lean warehousing?
Lean warehousing uses the principles of lean manufacturing to reduce wasteful processes in the warehouse, saving time and money, as well as preventing mistakes and defects occurring within a business’s workflow.
Modern warehouses must navigate a complex world of global supply chains — and one mistake here will increase lead times and create waste in inventory management. This is where lean warehousing comes in — a system with the goal of trimming down as many wasteful steps along the way, ensuring things keep running as smoothly as possible. The original lean principles were developed in Japan by Toyota as a more efficient approach to manufacturing, but over time, these principles have expanded and have been applied to new areas — such as warehousing.
At its core, the basic idea of lean warehousing could be summarized as:
Getting rid of as many “wasteful” processes, steps, and practices as possible
At first glance, this might seem like a simple case of streamlining warehouse management. However, lean warehousing also aims to increase productivity and reduce mistakes.
When implementing your lean warehouse ideas, just remember that it’s not about cutting corners. The “wasteful” elements removed by lean warehousing are just that — wasteful. That waste can take many forms, whether it’s keeping fast-moving goods at the far end of the warehouse or overproducing goods that aren’t needed.
What does lean warehousing improve?
Managing a warehouse is complicated. You have to make sure:
- Everything gets done on time
- To keep track of stock and make sure everyone is on the same page
- Try to avoid mistakes and defects, and deal with them once they inevitably occur
This is why lean warehousing aims to eliminate overstocking and reduce stockouts.
Lean warehousing also aims for zero defects. Since these issues can quickly spiral out of control, the goal is to catch them as early as possible. The focus here is solving the root cause of the problem.
Finally, lean warehouse management aims to increase overall efficiency in the warehouse — which equals faster delivery times and fewer delays.
All these things are primarily accomplished by eliminating wasteful practices and promoting more efficient ones. Quite simply, it encourages what works and eliminates what doesn’t.
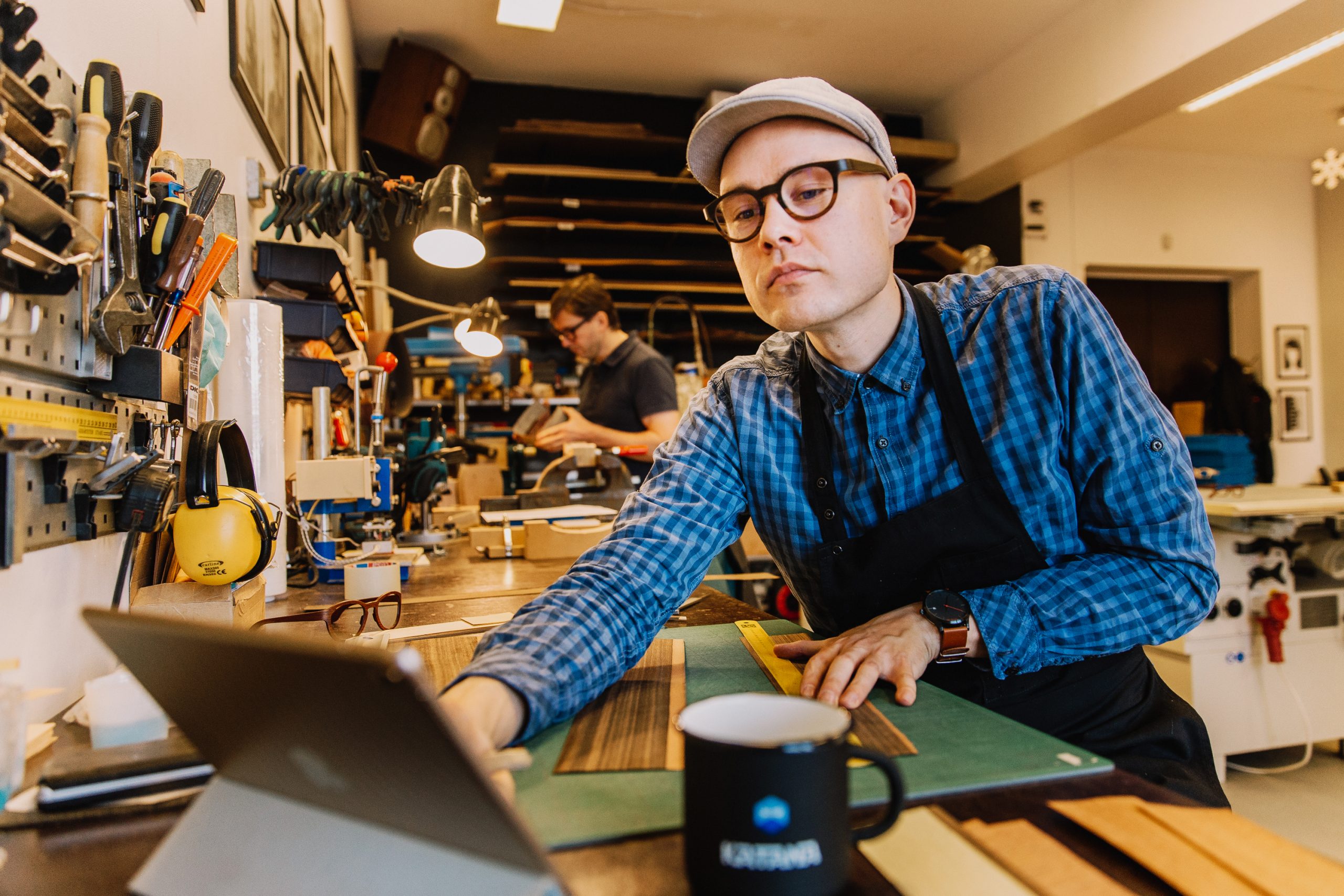
Key areas where you should look out for waste
Let’s look at a few of the areas in the warehouse where you might find waste and what form that waste might take.
Storage
Finding the right balance for stock levels in your storage space is important. Everything should be organized clearly and neatly.
Defects
It goes without saying that defects can lead to waste when products are sent back by the customer (or can’t even be shipped out in the first place). Lean warehousing aims for zero defects by identifying the root cause of any defects that occur.
Inventory management
Waste in inventory management often occurs due to faulty or incomplete information. You might end up in situations where you don’t have the right inventory when you need it. Or you might have what you need, but it’s not kept in the right location.
Movement in the warehouse and internal transportation
Too much unnecessary movement in the warehouse can waste valuable time and energy — whether it’s workers navigating a poorly planned warehouse layout or storing the most popular selling items at the back, where they can’t be quickly loaded onto transport.
Delays
Delays can cause you to lose business and can seriously hit the warehouse’s morale, which can snowball into more stress as you try to catch back up to the workload. Basically, delays tend to cause even more delays.
Download the ultimate guide to inventory management
A comprehensive ebook with everything you need to know about inventory management.
How does lean warehousing actually work?
The five principles of lean manufacturing are:
- Value — Understanding where the value of your business lies and knowing where you have the edge over the competition
- Value streams — Understanding the step-by-step process you use to manufacture goods from raw materials to the final product
- Flow — Evaluating ways you can streamline your process, remove waste and increase efficiency
- Pull — Using a pull-based system for your products through just-in-time delivery of both raw materials and products
- Perfection — Aiming for perfection and constant improvement once the first four principles have already been applied
All of these can also be applied to warehousing in one form or another.
Pull can be used to lower inventory levels in the warehouse and help identify bottlenecks, which in turn allows for further improvements in the warehouse.
Value streams can be used to get an overview of your manufacturing process, which allows you to better plan inventory management as the goods are produced.
Flow is an important step in analyzing where the actual wasteful steps are in your warehouse management.
Katana Cloud Inventory Platform
Thousands of businesses use Katana daily to implement lean inventory strategies and maximize efficiency.
Lean warehousing tools that you can use
To get you started on your road to perfection, here is a list of lean warehousing tools you can use to optimize your business.
5s
The 5s system is a tool used to eliminate waste and, in doing so, increase efficiency in the workspace (in this case, the warehouse). This is, perhaps, the lean tool that can be most clearly applied to lean warehousing.
The five S’s stand for:
- Sorting — Removing unnecessary items so they do not take up space in the warehouse
- Setting in order — Efficiently organizing the warehouse
- Shining — Keeping the warehouse area tidy and neat
- Standardizing — Creating and maintaining standard procedures in warehouse management
- Sustaining — Making sure the systems you set up stay up over time
Kaizen
Kaizen (improvement) is a technique focusing on the continuous improvement of the business. One of its features is encouraging teamwork within the company on all levels (for example, encouraging employees to suggest improvements).
This approach focuses on fixing the problem, rather than placing blame, and encourages an air of cooperation in the warehouse. Employee feedback can be vital in finding the most effective way to manage inventory in the warehouse.
Kanban
Kanban (visual signal) is a scheduling technique that uses visual cues to signal when a particular task needs to be finished. This can be used in the warehouse’s day-to-day management to ensure the workers always know what tasks need to be done and avoid wasted time.
Heijunka
Heijunka (smoothing) is a technique used to avoid dramatic peaks or valleys in production demand. This should help simplify inventory management on the warehouse level.
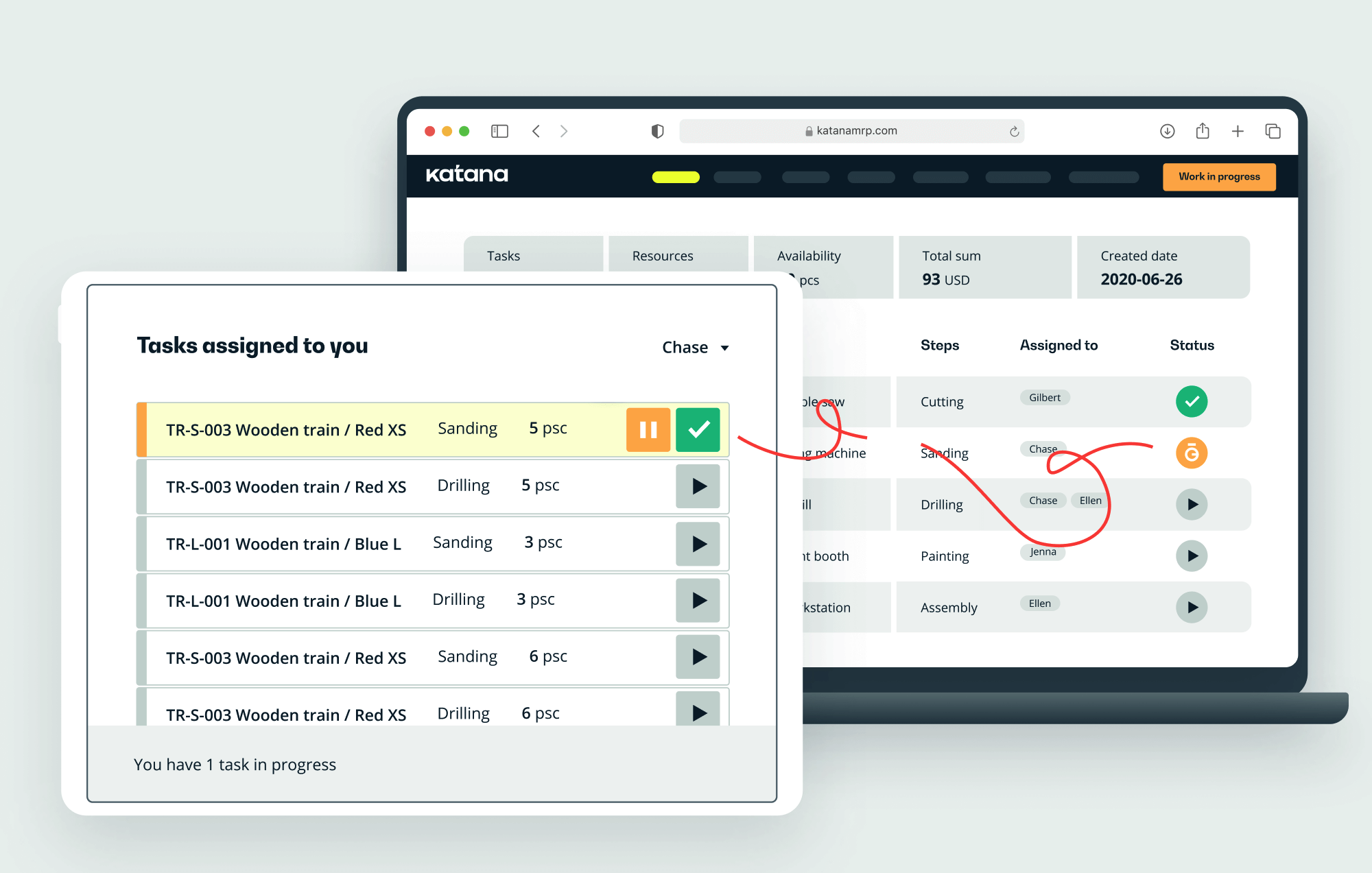
Get your warehouse lean with Katana’s ERP software
Keeping the warehouse lean can help keep up with modern supply chains and catch up to demand without giving up on quality.
Creating a lean warehouse might seem overwhelming. It involves a bit of restructuring and requires a very clear overview of your day-to-day procedures for you to know where to start.
This is where Katana can help you! With features such as inventory management and the ability to integrate with the best lean tools on the market, Katana’s software can be exactly what you need to implement all five lean manufacturing principles in your warehouse.
Get started by booking a demo with Katana to learn more and take your warehouse management to the next level.
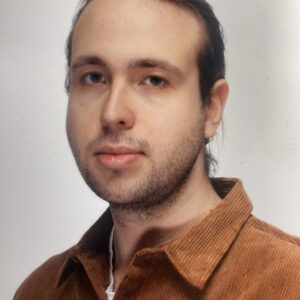
Erik Väli
Table of contents
Get inventory trends, news, and tips every month
Get visibility over your sales and stock
Wave goodbye to uncertainty with Katana Cloud Inventory — AI-powered for total inventory control