GMP vs GLP: Understanding the differences
In pharmaceuticals or chemicals, manufacturers need to understand the different regulations. Here is GMP vs GLP to help you understand these.
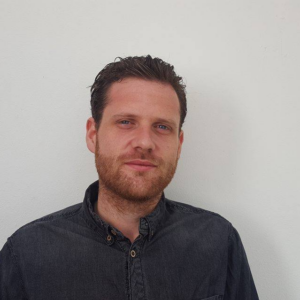
James Humphreys
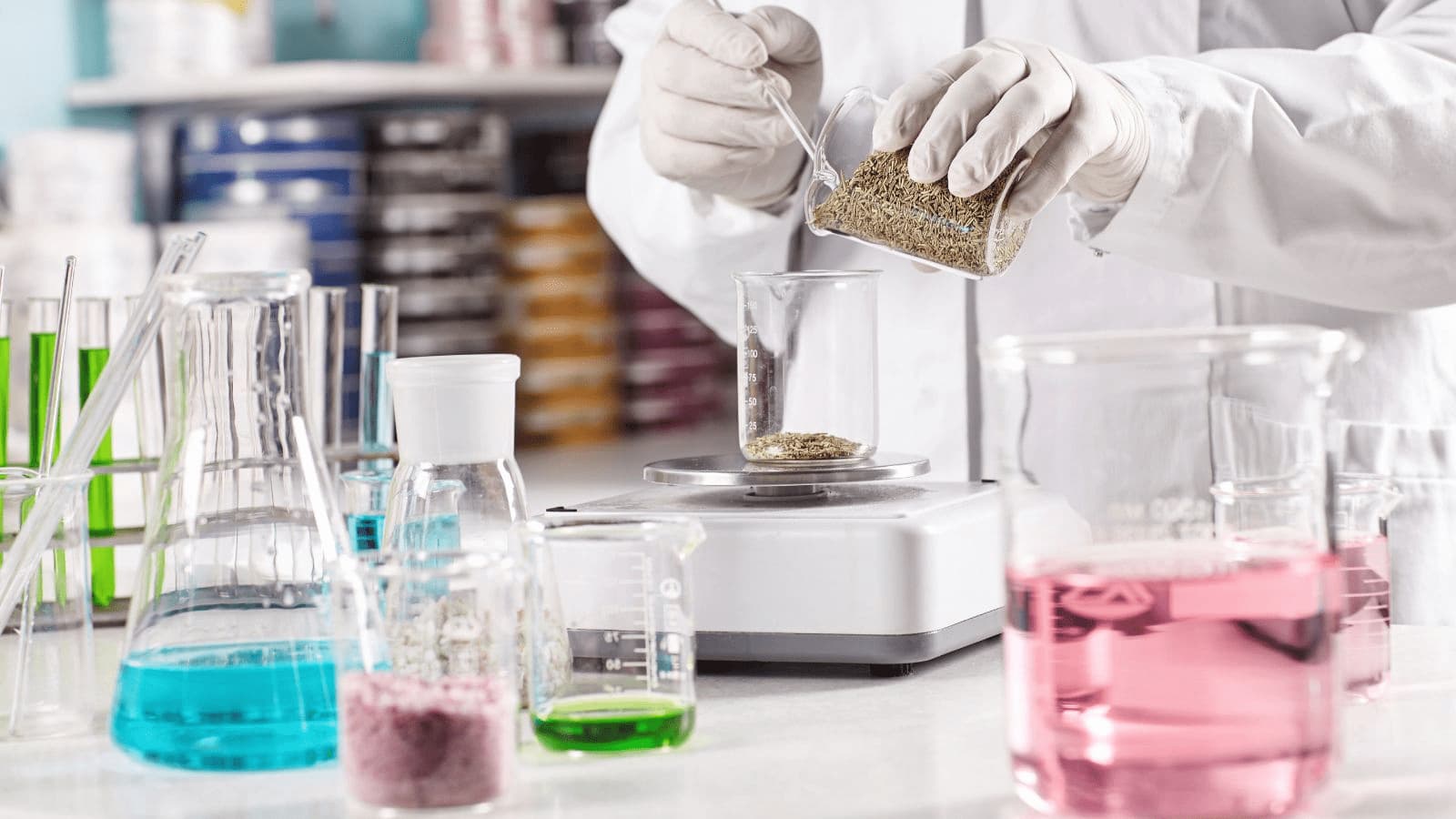
The manufacturing industry is filled with initialisms. Most of them have to do with regulations and standards that manufacturers must follow. GMP (Good Manufacturing Practice) and GLP (Good Laboratory Practice) are two of the most important, but they’re often confused with one another.
For companies producing food, pharmaceutical, or medical products, understanding the difference between GLP and GMP is essential for meeting regulatory requirements.
Below, we will take a high-level look at each and then examine some of the specific requirements that have been put in place.
Manage quality control and compliance tasks
Read how pharmaceutical manufacturing software helps you stay focused.
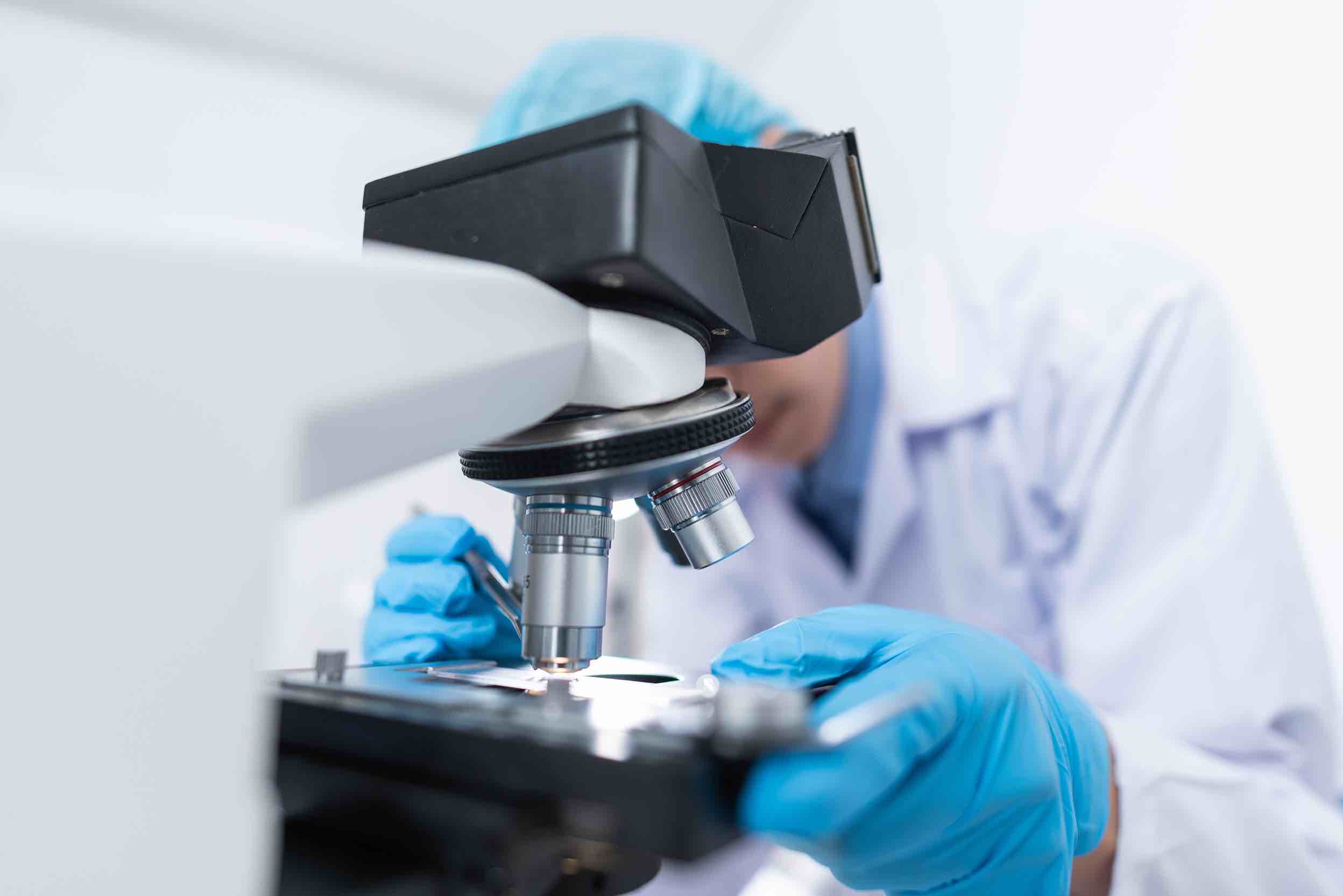
GMP vs GLP: An overview
Good Manufacturing Practice (GMP) is a set of guidelines that ensures that products are manufactured consistently, with quality in mind. This includes:
- Documenting processes and procedures
- Developing personnel training and qualifications standards
- Establishing clear communication between departments
- And more
You will sometimes see it referred to as Current Good Manufacturing Practice (cGMP), which focuses on the ever-changing landscape of technology. While GMP is a set of fundamental requirements, cGMP is constantly updating to reflect the most recent standards.
Good Laboratory Practice (GLP) is the counterpart to GMP. It focuses on ensuring the reliability of laboratory tests by laying out specific requirements for:
- Documentation
- Record-keeping
- Personnel qualifications and training
- Equipment maintenance
- Calibration records
GLP also requires laboratories to apply their protocols uniformly across all experiments conducted in any given lab. This helps ensure uniformity among different labs worldwide.
An easy way to remember the difference between cGMP/GLP/GMP:
- GLP is meant to protect against data contamination
- GMP is meant to protect against product contamination
- cGMP is meant to keep that protection up-to-date as technology changes
Let’s take a closer look at the specific requirements of GMP vs GLP.
GLP in the pharmaceutical industry
One of the places where Good Laboratory Practice is most important is in the pharmaceutical industry. Under GLP, laboratories must maintain detailed records of all experiments conducted, and these records must be available for inspection by regulatory authorities such as the U.S. Food and Drug Administration (FDA).
GLP principles
In addition to documentation requirements, GLP includes several other core principles.
Test facility organization
Each facility that will be involved in the testing or evaluation of pharmaceutical products must be organized in such a way that it can produce accurate, reliable data.
This includes:
- Having a clear chain of command
- Assigning responsibilities and authority to personnel
- Ensuring that the facility has adequate resources for conducting tests
Standard operating procedures (SOPs)
Clear SOPs must be in place for all laboratory tests. These should include instructions on how to set up, run, and analyze experiments, as well as detailed information on the apparatus used.
Quality assurance
A comprehensive quality assurance program (QAP) is critical for ensuring data accuracy and reliability. This includes having written SOPs for test protocols, as well as conducting reviews of the laboratory’s operations to ensure that it complies with GLP requirements.
Facilities
The facility should be at a suitable location to avoid any interference from external sources such as noise, vibration, dust, or temperature. It also needs to be large and well-equipped to ensure that separate tests do not interfere with one another.
Apparatus
Cleaning, maintenance, and calibration of all apparatus used in laboratory tests must be documented and kept up-to-date. This helps ensure that the data produced is accurate and reliable.
Test systems
Biological test systems — animal and plant — must be maintained and monitored to ensure that they are suitable for use in laboratory tests. Any with unexpected morbidity or mortality must be reported to the appropriate regulatory authorities and not used in further testing.
Performance
Before any test or evaluation is started, a comprehensive plan should be put in place outlining the objectives, methods, and resources required to experiment and any safety measures that need to be taken. Regular review of the test results is also recommended to ensure that the desired outcomes are being achieved.
Reporting
A full report is to be generated for each experiment conducted, regardless of the outcome. This report should include details about the test plan, methods, resources used, and results.
Storage
All documentation should be stored in a secure, organized manner. This includes samples, test results, and other important data that may be needed for later reference or review. If anything is going to be destroyed or discarded, the laboratory must document it and maintain records of its destruction.
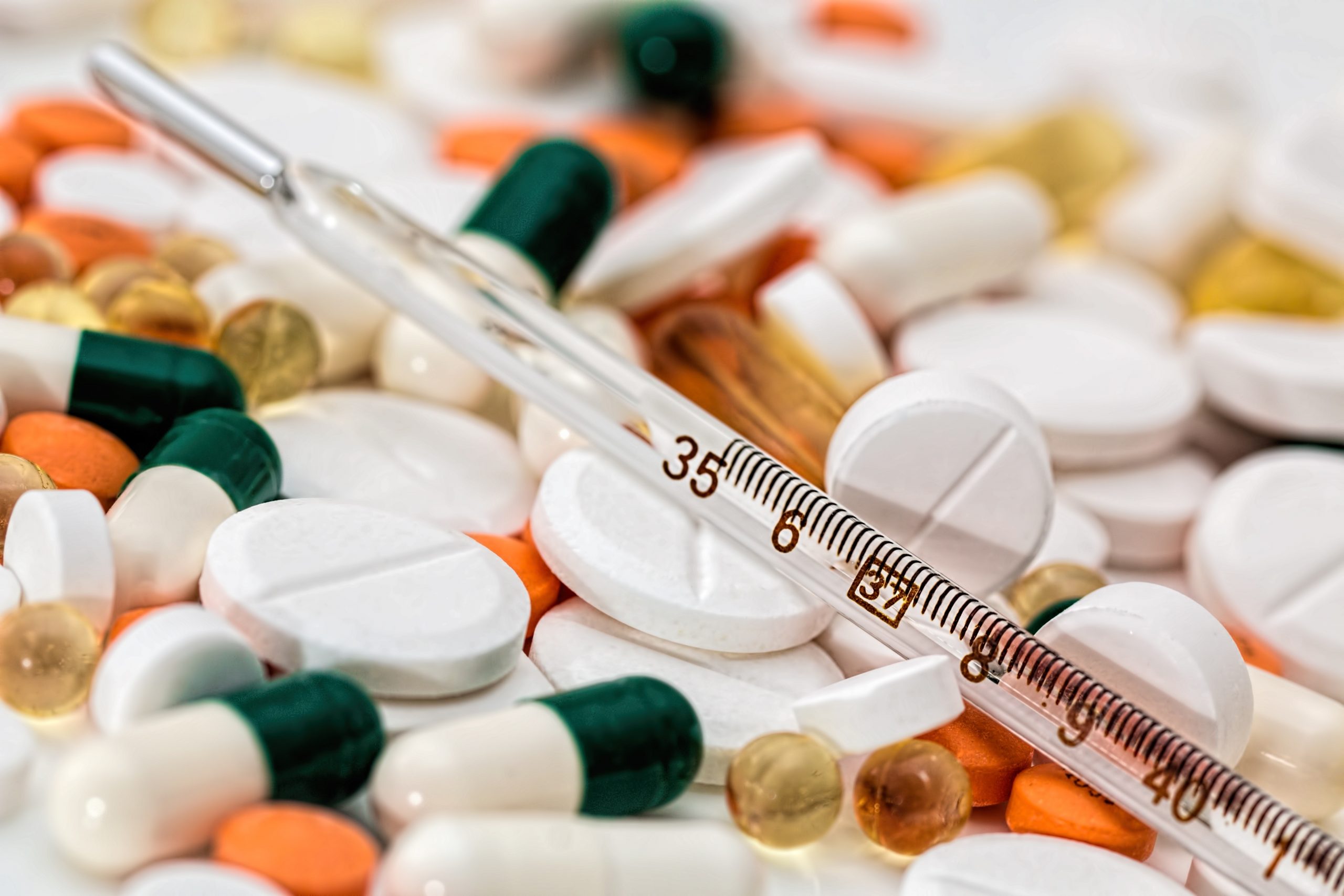
GMP in the pharmaceutical industry
To move from design and testing to production, the pharmaceutical industry must comply with Good Manufacturing Practice (GMP) regulations.
GMP covers a wide range of topics, from the quality control and assurance processes that must be in place to ensure product safety and efficacy to documentation standards for ensuring accurate traceability of products throughout their life cycle.
GMP requirements
While the focus of GMP vs GLP may be slightly different, they also have several overlapping principles. In the following GMP requirements, the same significance is placed on record-keeping and documentation.
Master formula
This document outlines the ingredients, processes, and equipment required to manufacture a product. It also includes specifications for each of these components and instructions for quality control tests that must be conducted throughout production.
Location
The production facility cannot have any contaminants or the threat of contamination. Insects, rodents, and other pests must be controlled. Hygiene standards must be maintained and documented.
Water system
The water used in the production process must meet certain standards for purity to ensure that the product is safe. It must also be tested regularly for contamination or impurities.
Warehousing
Product storage must be secure and labeled correctly. Temperature, humidity, and other environmental conditions must be monitored and documented to ensure the safety of products over time.
Production
A facility must be designed and built to ensure that the production process is efficient and safe. There must be room for product inspection and testing and separate areas for different stages of production.
Ancillary areas
Areas where workers can relax, eat, or rest must meet certain standards for cleanliness. They also must be separate and isolated from the production areas.
Quality control
The quality control area must be designed and built to ensure that products meet the highest standards throughout the production process. This includes testing, inspection, and monitoring of products at each stage of the process.
Personnel
Standardized, effective training must be provided to personnel, and a clear chain of command must be established.
Equipment
Production equipment must be regularly inspected and maintained. It must also meet certain standards for cleanliness, and all maintenance records must be kept in an accessible format.
Labels
For stored products, labels must be accurate and up-to-date. This includes expiration dates, batch numbers, and other relevant information.
Containers
All containers must be tested to ensure they will not contaminate the product or react with it in any way.
Recalls
A procedure for recalling products must be in place, with distribution information available and easily accessible.
Complaints
If a company receives a complaint or report of side effects, adverse reactions, or other issues, it must have a system in place to investigate and respond promptly.
Garments
Personnel must wear clean, appropriate clothing and use PPE garments when necessary. Contamination from clothing must be avoided.
Raw materials
An inventory of the raw materials used in production must be kept and updated regularly. The source of each material must also be documented, and a standard stock rotation must be established.
Want to see Katana in action?
Book a demo to get all your questions answered regarding Katana’s features, integrations, pricing, and more.
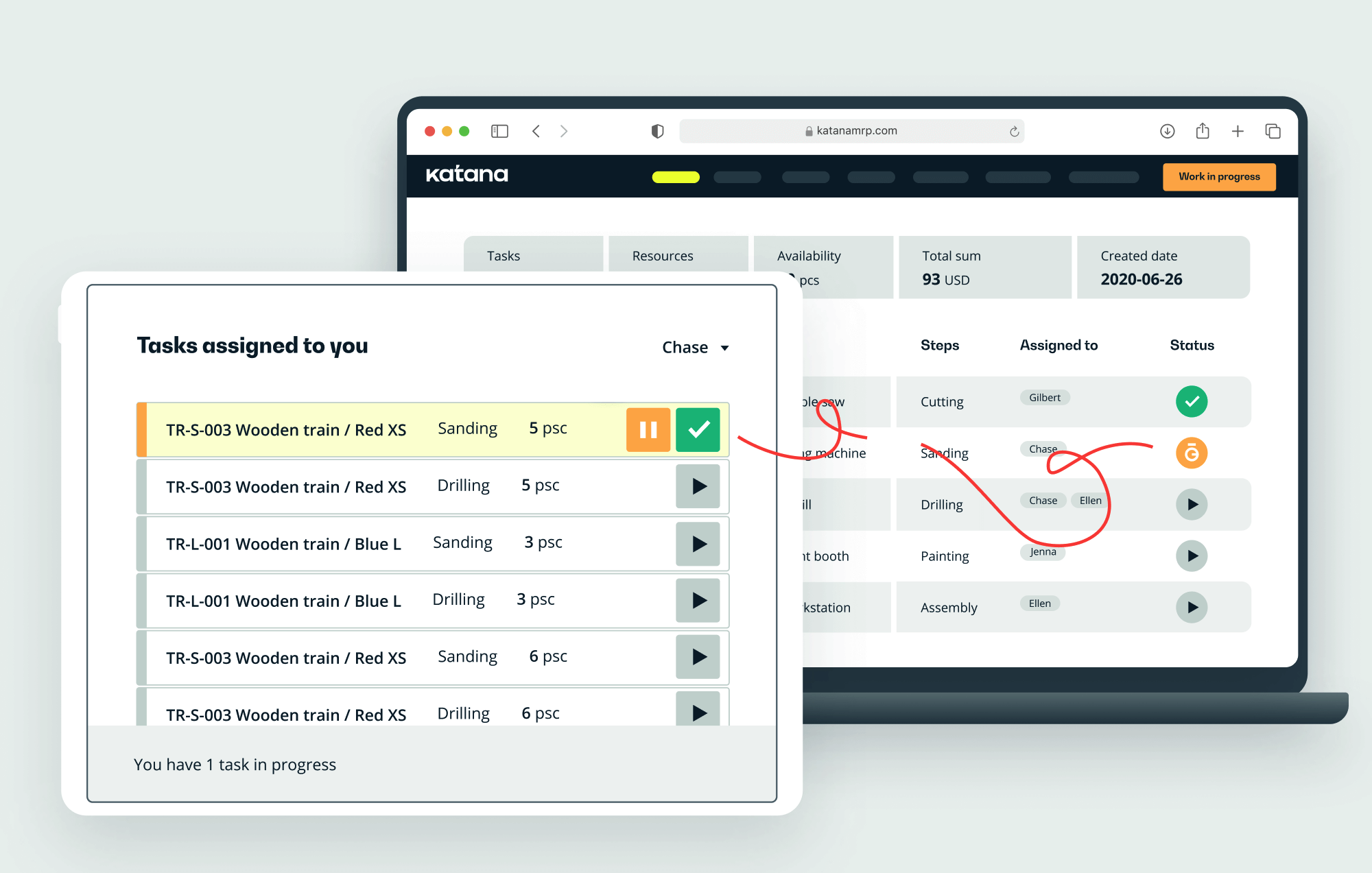
Implementing GMP vs GLP: What’s next?
To maintain these practices, companies must reduce human documentation errors as much as possible.
Manufacturers can increase efficiency and compliance with GMP and GLP regulations with software solutions to help inventory management, resource planning, quality control, and process automation.
With Katana, a cloud-based ERP platform, companies can streamline production processes and stay compliant. With its easy-to-use interface and customizable features, Katana helps manufacturers create an efficient manufacturing workflow that aligns with the highest safety and quality standards.
Get a demo and see how it can help your production process.
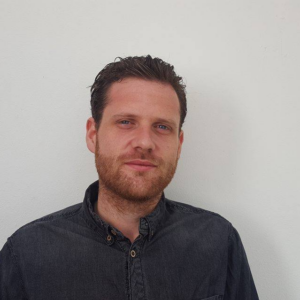
James Humphreys
Table of contents
Get inventory trends, news, and tips every month
Get visibility over your sales and stock
Wave goodbye to uncertainty with Katana Cloud Inventory — AI-powered for total inventory control