Mastering batch production: Enhance efficiency and quality control
Learn what is batch processing in manufacturing and explore its benefits and drawbacks. Uncover the secrets to mastering this production method, along with how to streamline your batch manufacturing process.
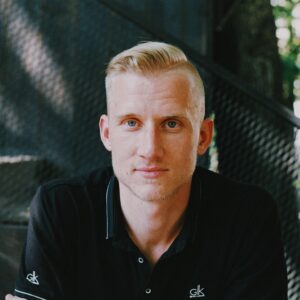
Henry Kivimaa
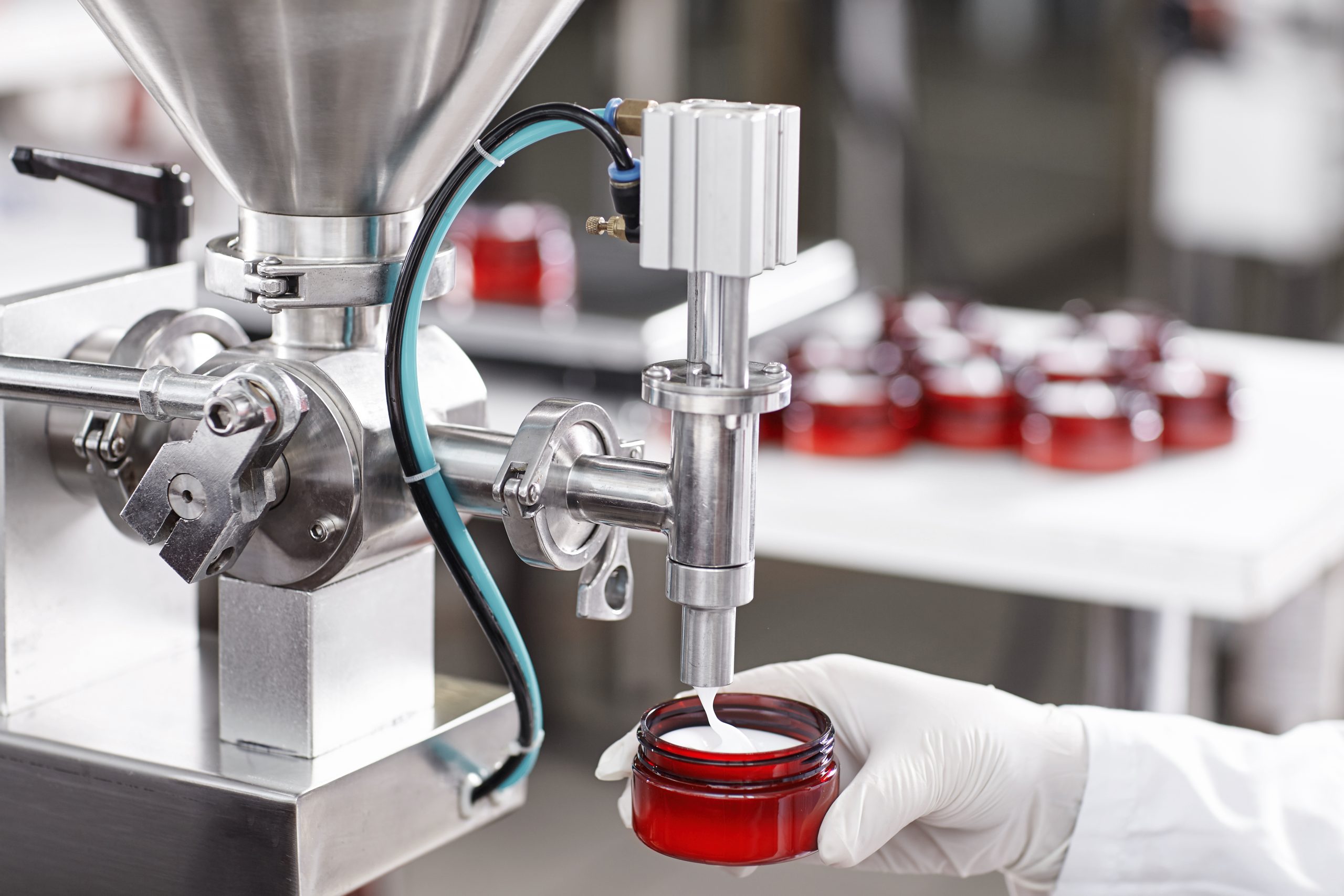
In the vast landscape of manufacturing processes, each with its own merits and drawbacks, batch production stands out as a popular and time-tested method. With its step-by-step approach, batch production allows for the creation of distinct product configurations with relative ease.
For example, let’s imagine a soap manufacturer and take a closer look at the three primary stages of soap production:
- Saponification
- Drying
- Mixing
In this method, soap is produced in batches, with each batch comprising 10 pieces. Until all 10 pieces have undergone saponification, the drying process is put on hold. Once saponification is complete, the batch proceeds to the drying stage, and so on.
The logical flow of batch production raises the question of whether it could be the right fit for your growing business. Let’s delve into the realm of batch production to understand its benefits and determine if it aligns with your unique requirements.
Now that it’s clear what is batch production, let’s take a look at the advantages this manufacturing method brings.
Advantages of batch production
Batch production, like any production style, boasts distinctive attributes that can be both advantageous and challenging.
This section delves into the advantages of batch production, which contribute to its widespread popularity in the manufacturing world. Let’s uncover 12 reasons behind its acclaim and the benefits it offers to businesses.
1. Reduced setup time
In batch manufacturing, the setup time is significantly reduced as the preparation and adjustment of equipment occur before commencing the production of each batch.
Unlike continuous production systems that demand frequent changes in product specifications, batch production allows manufacturers to streamline their processes, fine-tune equipment settings, and optimize workflow efficiency for a specific batch. This minimizes downtime between batches, ensuring a smoother transition from one production run to the next, ultimately leading to higher overall productivity.
2. Efficient use of equipment
One of the key advantages of batch production lies in its ability to make efficient use of heavy-duty equipment and machinery.
By grouping similar or identical products together in batches, manufacturers can maximize the utilization of specialized machinery. This approach ensures that equipment is not underutilized or left idle during production runs, leading to improved output efficiency and reduced production costs per unit.
Furthermore, it enables businesses to capitalize on economies of scale, as the larger quantities produced in batches can help spread fixed costs over more units, resulting in cost savings.
3. Consistent operations
Batch manufacturing promotes consistency in operations, offering a stable and predictable production environment. Once the initial setup and configuration adjustments are made for a specific batch, there is little need for constant readjustment during the production process. As a result, operators can focus on maintaining steady and reliable production rates, reducing the risk of disruptions or variations in product quality.
This advantage is particularly valuable when producing goods with precise specifications, like products for your cosmetics inventory, as batch manufacturing ensures that each unit within a batch adheres to the same set of parameters.
4. Workflow optimization
The repetitive nature of batch production enables workers to establish a comfortable and efficient workflow.
With each batch comprising identical or similar products, employees can gain proficiency and expertise in producing specific items, leading to increased speed and accuracy in their tasks. This operational rhythm, often referred to as getting in the flow, not only enhances productivity but also reduces the likelihood of errors or delays caused by frequent changeovers, which may be common in other manufacturing methods.
5. Minimize transportation time
Batch production offers time-saving advantages in transportation logistics. Rather than moving individual products at different intervals, batched units are transported together to the next stage of the production process.
This consolidation of products optimizes transportation efficiency, reduces handling time, and lowers transportation costs. It is particularly beneficial when dealing with intermediate products that need to undergo multiple processing steps, as batch transportation ensures smooth and organized movement through the various stages of production.
6. Flexibility for customization
Batch manufacturing grants businesses the flexibility to accommodate unique configurations and variations in products. Since each batch can be tailored to specific customer demands or market preferences, manufacturers can respond more effectively to changing market trends and individual customer requirements.
This adaptability fosters customer satisfaction and enables businesses to differentiate their offerings, making it an advantageous approach in markets where customization is highly valued. Furthermore, this versatility allows manufacturers to test new product variations within manageable batch sizes before committing to large-scale production, reducing the risks associated with introducing novel products.
Download the Definitive Guide to Batch Production
Download our free ebook guide on batch production to learn more about the benefits, workflows, and software you need to get started.
7. Streamlined planning and scheduling
The structured nature of batch production facilitates streamlined planning and scheduling processes. Manufacturers can efficiently allocate resources, including materials, labor, and equipment, by grouping production runs into batches.
This approach aids in optimizing production schedules, reducing idle time, and minimizing production bottlenecks.
By pre-planning batch schedules, businesses can optimize inventory levels, ensure timely material availability, and foster efficient communication and execution of production plans across departments.
8. Enhanced error detection
Batch manufacturing improves the identification and rectification of errors throughout the production process.
Since products are manufactured in discrete batches, any issues that arise can be isolated to specific batches, making it easier to pinpoint the source of errors and defects. This targeted approach enables manufacturers to implement corrective measures promptly, preventing the recurrence of problems in subsequent batches.
By closely monitoring quality and performance within each batch, businesses can maintain consistent product standards and uphold a high level of quality assurance. Furthermore, the ability to detect and address errors in a timely manner contributes to overall cost savings by minimizing wastage and rework.
9. Cost-effective production
Batch production offers cost-saving benefits by leveraging economies of scale. With larger quantities of products being produced in each batch, fixed costs associated with setup, changeovers, and machinery operation are distributed over a greater number of units. As a result, the cost per unit decreases, making batch production financially advantageous.
Additionally, bulk purchasing of raw materials and components for larger batches can lead to volume discounts, further reducing production expenses. This cost-effectiveness makes batch production an attractive option for businesses seeking to optimize their production processes and achieve competitive pricing in the market.
Batch production example
Let’s go over an example using again the soap manufacturer.
- Gathering raw materials — The soap manufacturer gathers all the necessary raw materials for making a batch of Lavender soap, including oils, lye, distilled water, lavender essential oil, and any desired colorants or additives.
- Weighing and measuring — Precise measurements are taken for each ingredient to ensure the correct formulation and consistency within the batch. The quantities are scaled up based on the desired batch size, which in this case is 200 bars of Lavender soap.
- Mixing the soap batch — The measured oils and lye are carefully combined, and the mixture is blended thoroughly until it reaches trace, the point at which the soap mixture thickens and starts to resemble a custard-like consistency.
- Adding fragrance and color — Once the soap mixture reaches trace, lavender essential oil is added to impart the desired fragrance. If any colorants are used, they are added at this stage to achieve the desired color of Lavender soap.
- Molding the soap — The fragranced and colored soap mixture is poured into soap molds, each capable of producing multiple soap bars. In this case, the batch aims to produce 200 bars.
- Curing the soap — The soap-filled molds are left undisturbed to cure for a specific period, typically 24 to 48 hours. During this time, the soap undergoes saponification, a chemical process in which the oils and lye react to form soap.
- Unmolding and cutting — After the curing period, the soap is removed from the molds and cut into individual bars. The bars are then placed on drying racks or trays to further harden and dry out over several weeks.
- Packaging and storage — Once fully dried and hardened, the Lavender soap bars are packaged for sale or distribution. The remaining soap is stored in inventory until needed for orders or future sales.
Following the batch production process, the soap manufacturer can repeat these steps to create another batch of Rosemary soap or any other soap variety, ensuring consistency within each batch while allowing for diverse soap offerings to meet customer preferences.
10. Ideal for new product introduction
Batch production provides an ideal environment for introducing new products to the market. Instead of committing to full-scale continuous production immediately, businesses can produce manageable quantities in batch runs.
This approach allows manufacturers to gauge the market response, obtain valuable feedback, and identify any necessary product improvements before scaling up production.
By piloting new products in batches, businesses can mitigate potential risks and losses associated with large-scale production of unproven items. This staged approach to new product introduction ensures greater control and adaptability during the early stages of market testing.
11. Smooth inventory management
The organized nature of batch manufacturing simplifies inventory management for manufacturers. Each batch represents a distinct set of units, making it easier to track inventory levels accurately.
Manufacturers can maintain better control over stock quantities, ensuring that appropriate levels of finished goods, work-in-progress, and raw materials are available for each batch.
This level of visibility helps prevent stockouts, overstocking, and material shortages, leading to improved supply chain efficiency and reduced carrying costs. Efficient inventory management allows businesses to respond swiftly to fluctuations in demand and optimize their inventory turnover ratios.
12. Maintenance convenience
Batch production facilitates efficient maintenance scheduling and cleaning routines for equipment and machinery. Since production occurs in discrete batches, manufacturers can plan maintenance activities during downtime between batch runs.
This proactive approach minimizes production interruptions and ensures that equipment is well-maintained, operating at peak performance, and adhering to safety standards.
Regular cleaning and maintenance help prevent cross-contamination between batches and ensure consistent product quality. By incorporating routine maintenance into the batch production schedule, businesses can extend the lifespan of their equipment, reducing the frequency of breakdowns and associated production delays.
Disadvantages of batch production
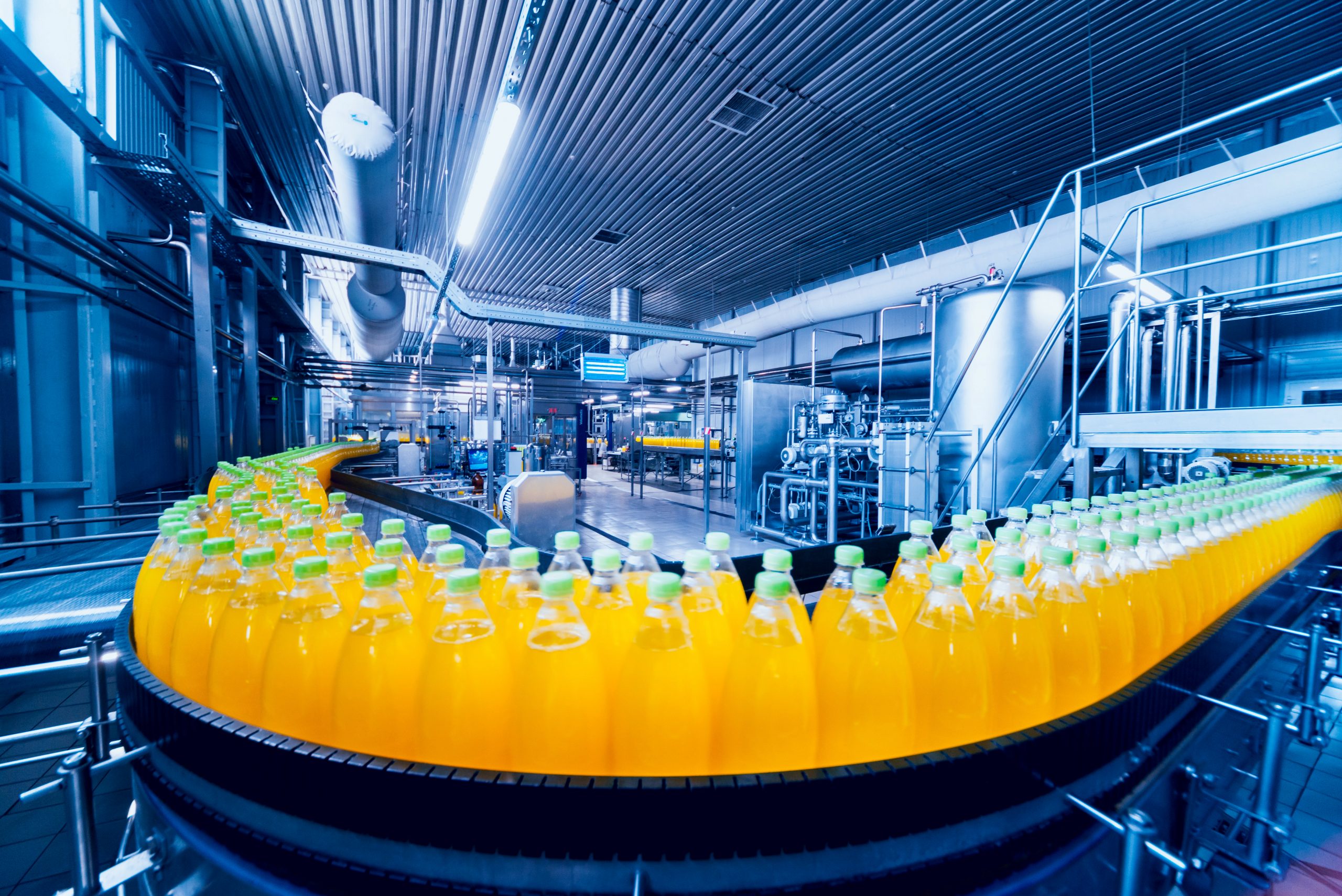
So far, we’ve explored the remarkable advantages of batch processing, from enhanced scheduling to reduced mistakes, bringing a sense of reassurance to manufacturing operations.
However, it’s essential to acknowledge that batch production is not without its shortcomings. In fact, the pharmaceutical manufacturing industry alone has reported an annual loss of approximately $50 billion due to the inefficiencies associated with batch processing.
This revelation might seem deflating, but it prompts us to delve deeper into the reasons behind such challenges.
To gain a comprehensive understanding, we’ll compare batch production with mass production, also known as continuous manufacturing, and highlight the differences that can lead to inefficiencies in batch processes. So, let’s take a look at the 10 disadvantages of batch production.
1. Increased setup time and changeovers
Unlike continuous manufacturing, batch production requires setup and adjustments for each batch. The time spent configuring equipment, cleaning, and preparing for the next batch can lead to significant downtime, impacting overall productivity.
2. Lower production efficiency
Batch production may result in lower production efficiency compared to continuous manufacturing. While each batch is processed as a distinct unit, there can be inefficiencies in terms of equipment utilization and handling between batches, affecting overall output.
3. Higher inventory costs
The batch production approach often necessitates the storage of intermediate products between different stages of processing. This can lead to higher inventory costs, as storage and handling expenses increase when products are not in continuous flow.
4. Potential for overproduction and underproduction
The fixed production quantities of batch production can lead to overproduction or underproduction. If the demand for a specific batch’s products fluctuates, businesses may face challenges in adjusting production accordingly, leading to excess inventory or unmet customer needs.
5. Quality variability
Since each batch is produced separately, there may be variations in product quality and consistency between batches. Maintaining uniform quality across all batches requires stringently following the production quality control checklist and frequent testing.
6. Increased wastage risk
In batch production, any errors or defects in a single batch can lead to the entire batch being discarded or reworked. This higher risk of wastage can result in increased production costs and material losses.
7. Complex production planning
Batch production necessitates meticulous planning to optimize scheduling and resource allocation. Coordinating multiple batches with varying production requirements can lead to complex production planning, making it challenging to respond quickly to changing demand.
8. Potential for product obsolescence
In industries with rapidly changing technology or consumer preferences, batch production may increase the risk of product obsolescence. Large batch sizes can lead to stockpiling of outdated products, making it difficult for businesses to adapt to market shifts.
9. Delayed customer feedback
Due to the discrete nature of batch production, customer feedback and market response might be delayed until the entire batch is produced and released. This delay can hinder rapid product improvements and responsiveness to customer needs.
10. Higher labor costs
And as the final disadvantage, batch production can require more frequent changeovers and manual handling between batches, potentially leading to higher labor costs. Skilled labor is often required to set up, operate, and clean equipment between each batch, adding to production expenses.
Understanding these disadvantages of batch production allows businesses to make informed decisions about their manufacturing processes, considering factors such as product complexity, market demand, and production efficiency. Balancing the benefits and drawbacks can help organizations optimize their production methods and achieve better outcomes in their respective industries.
Master batch production process
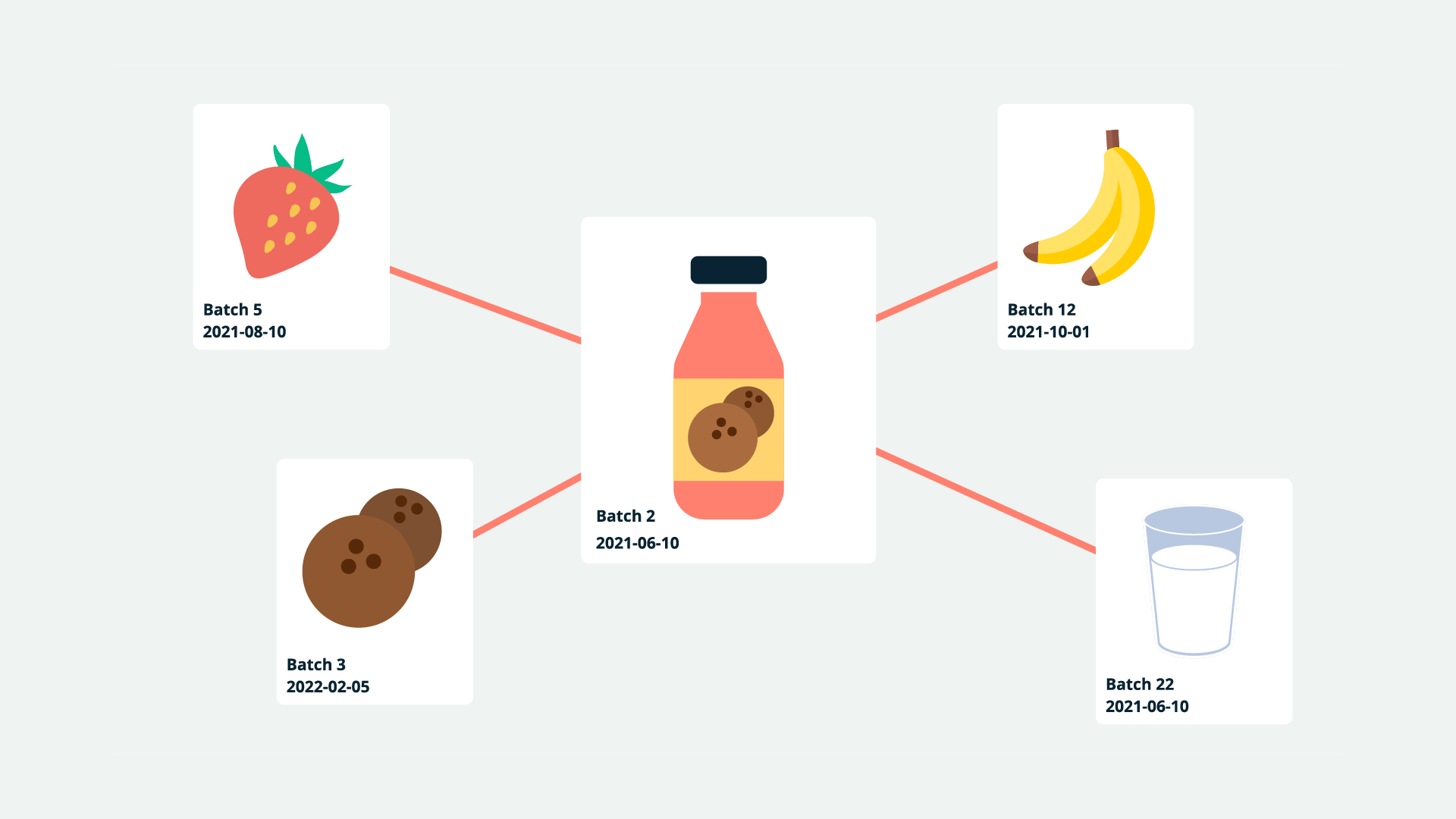
Choosing the proper manufacturing process is crucial for your growing business, and mastering it requires attention to detail. Especially in small-batch manufacturing, the impact of each process can have significant ripple effects on your operations and overall success. That’s where Katana comes in to streamline your production.
Katana’s batch production software is designed to bring all the critical information together, allowing you to make informed decisions and maximize the potential of your batch production model. With Katana, you gain complete visibility and control over your production processes, from raw materials to finished goods.
Efficiently manage inventory levels, reduce setup time, and optimize equipment utilization by leveraging Katana’s intuitive interface and real-time insights. Stay on top of inventory costs, minimize wastage, and ensure consistent product quality with its advanced tracking capabilities, including batch and lot tracking.
As your go-to solution, Katana enables you to tackle the complexities of batch production with ease. With features tailored to your needs, you can respond swiftly to changing customer demands, achieve industry compliance, and enhance your production efficiency.
Step into the future of batch manufacturing with Katana and unlock the full potential of your business. Experience the seamless integration, comprehensive insights, and superior production control that Katana offers. Embrace the power of smart manufacturing, and take your batch operations to new heights.
Get a demo and witness the difference Katana can make for your manufacturing success.
Check out the video below to get a better overview of Katana’s batch production features.
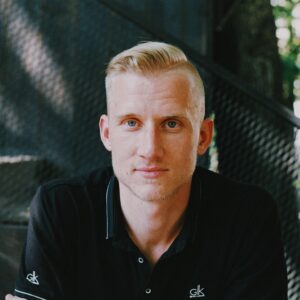
Henry Kivimaa
Table of contents
Get inventory trends, news, and tips every month
Get visibility over your sales and stock
Wave goodbye to uncertainty by using Katana Cloud Inventory for total inventory control
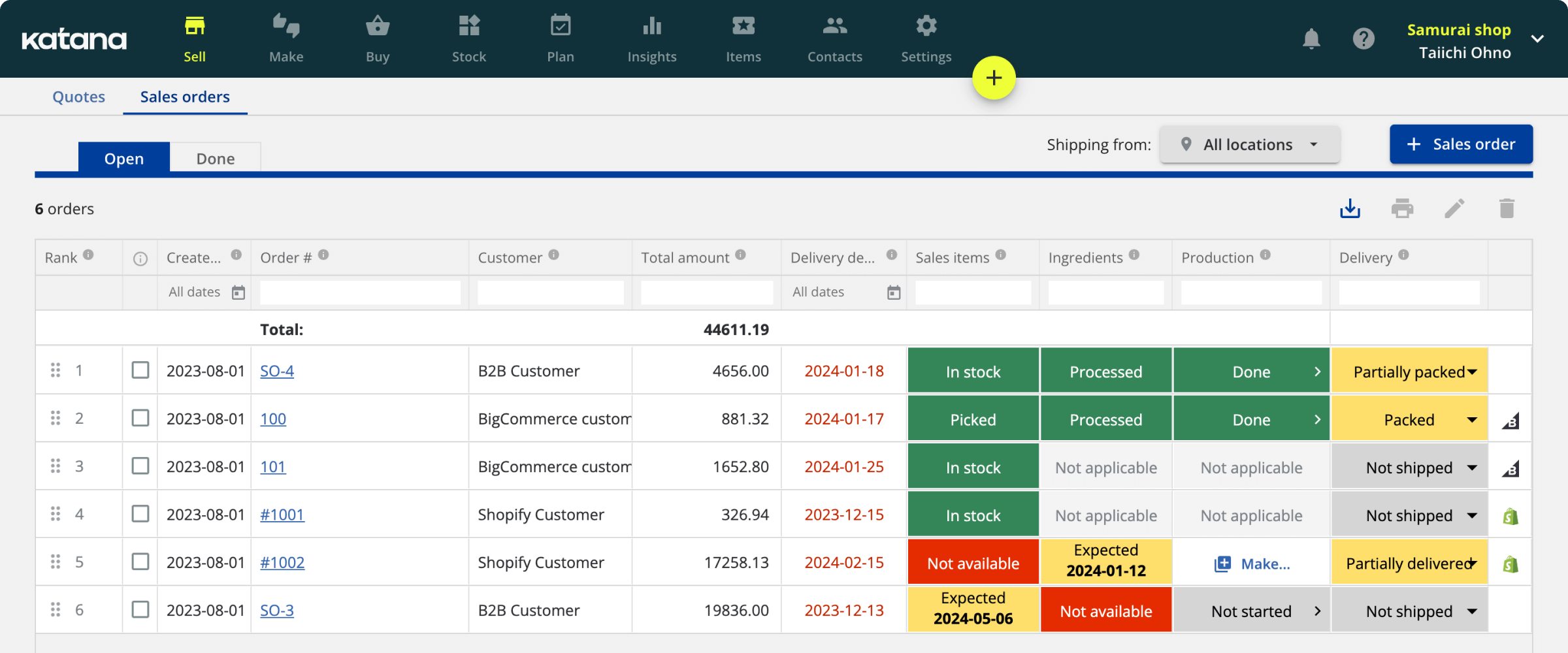