Intermittent production: Making sense of the irregularity
In this article, we look into intermittent production, the difference between continuous production, and the pros and cons of using this production method.
Team Katana
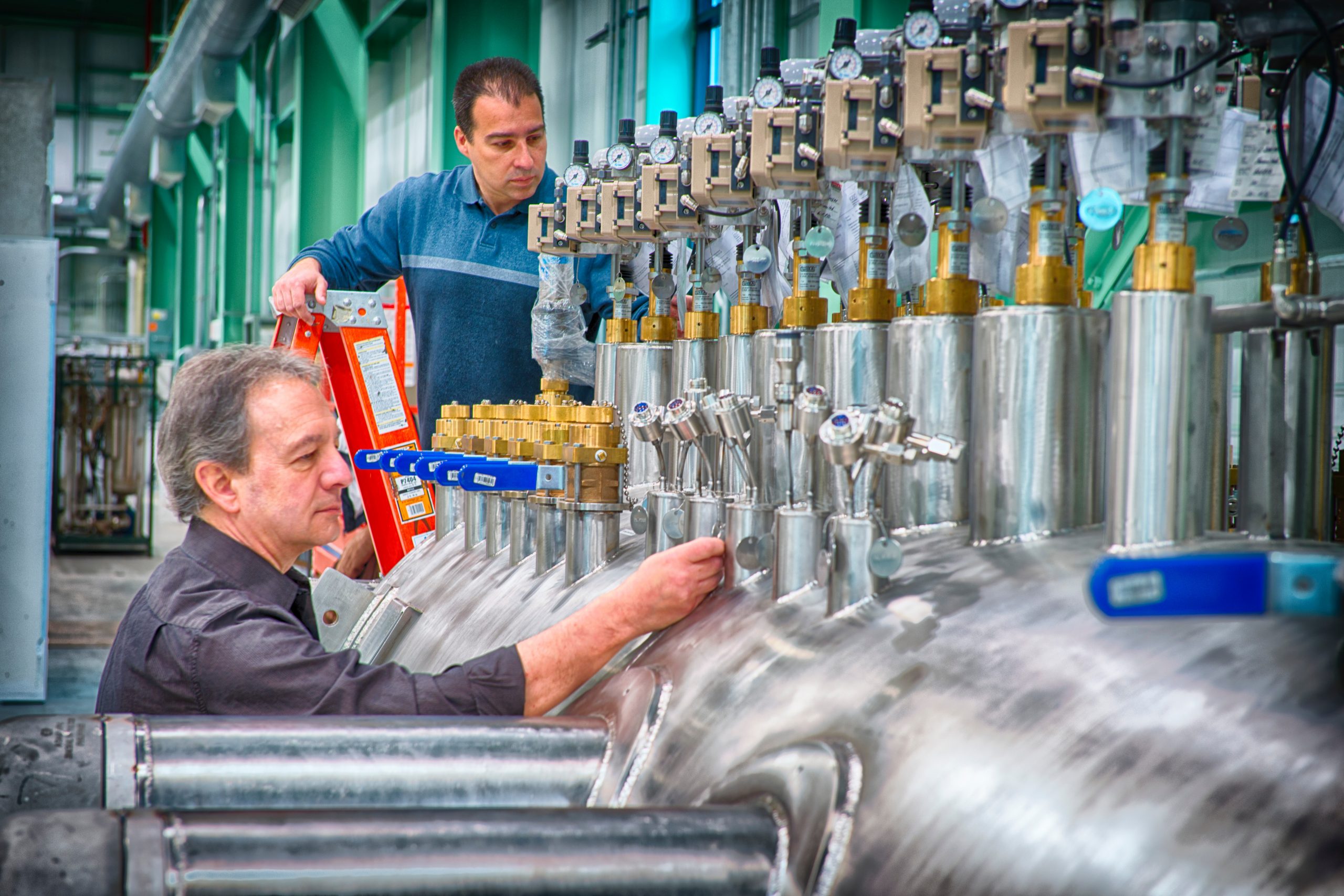
What is intermittent production?
Intermittent production is an umbrella term for manufacturing processes that use irregular production schedules to create several different products using one production line.
It’s used by manufacturers who produce low-volume, high-variety products for either mass customization or bespoke manufacturing.
If a manufacturer produces products, either one-by-one or in a batch, but the next product(s) requires a different manufacturing route or machines to be taken down and set back up in a different configuration, it would be an example of an intermittent production system.
Intermittent manufacturing workflows that use this method are:
- Batch manufacturing
- Job shop manufacturing
- Discrete manufacturing
We’ll look more into these later in the article.
We’re going to look into what is the difference between intermittent and continuous production processes, the intermittent workflows, and how you can get started with intermittent production with smart manufacturing.
So, without further ado, let’s begin.
Master your production scheduling. Thousands of manufacturers use Katana for its real-time overview of their entire production process. Request a demo to see it in action.
What is the difference between intermittent and continuous production processes?
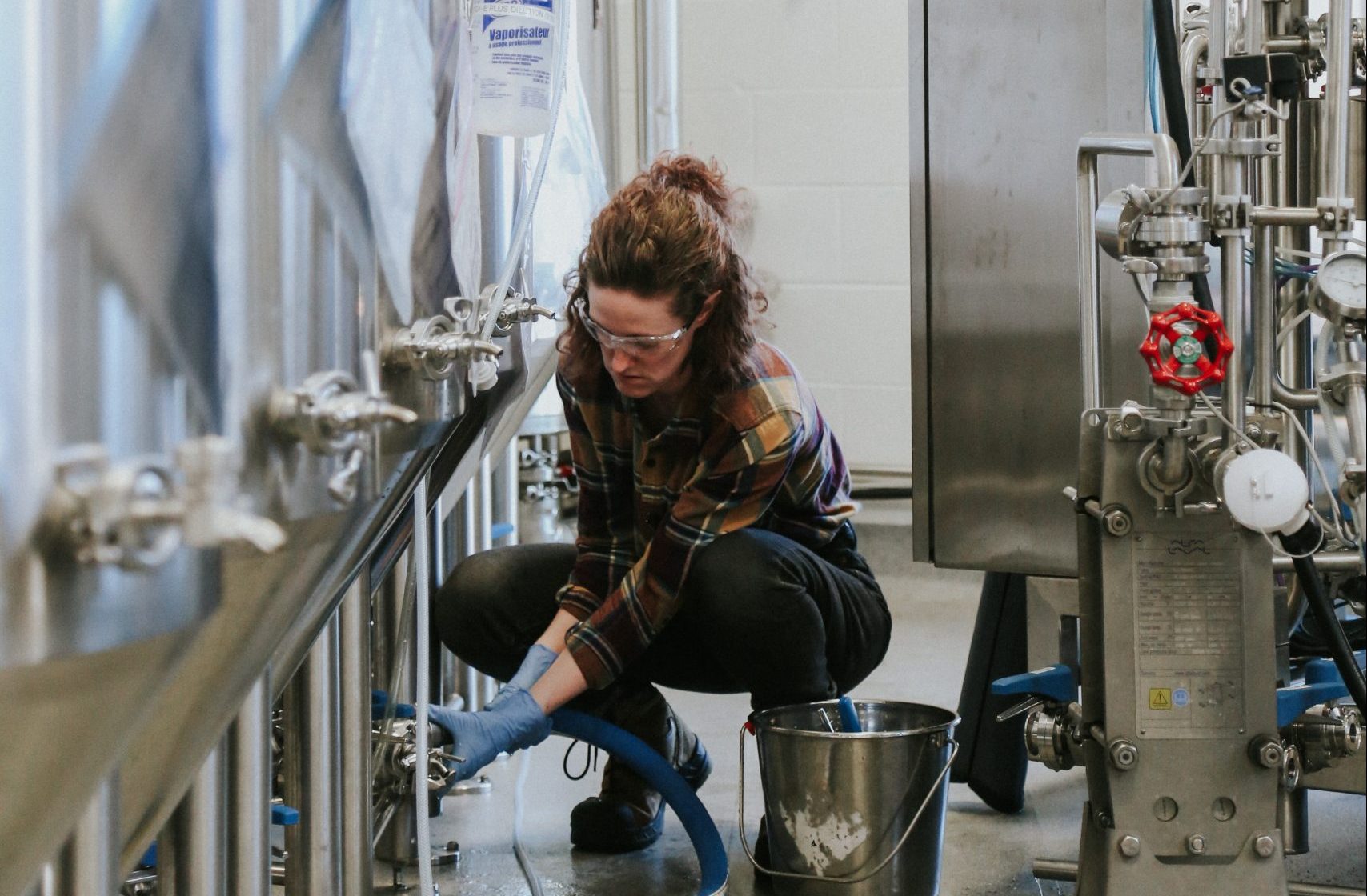
Firstly, intermittent production isn’t the only way of running your manufacturing business. There is a counter-part, called continuous production.
But, exactly what is the difference between intermittent and continuous production processes?
If intermittent production covers make to order (MTO), irregular production. Continuous production is the opposite.
Continuous production is the non-stop approach to manufacturing products for make to stock, which applies to workflows such as:
- Repetitive manufacturing
- Continuous manufacturing
The quickest way of explaining what is the difference between intermittent and continuous production processes would be:
- Intermittent production – Products are made based on a customer’s order
- Continuous production – Products are constantly made, based on demand planning
While the finished goods made from intermittent manufacturing might be varied from product to product, with a continuous production method, products, and the manufacturing route, is standardized, easily allowing for large-scale manufacturing.
Now that you know how these two processes are different, let’s look more into the various types of intermittent manufacturing processes.
Pro tip:
If you’d like to look more into the different manufacturing processes, we have the free and ultimate guide to understanding what is manufacturing, which you can use to optimize your business.
Different intermittent production methods
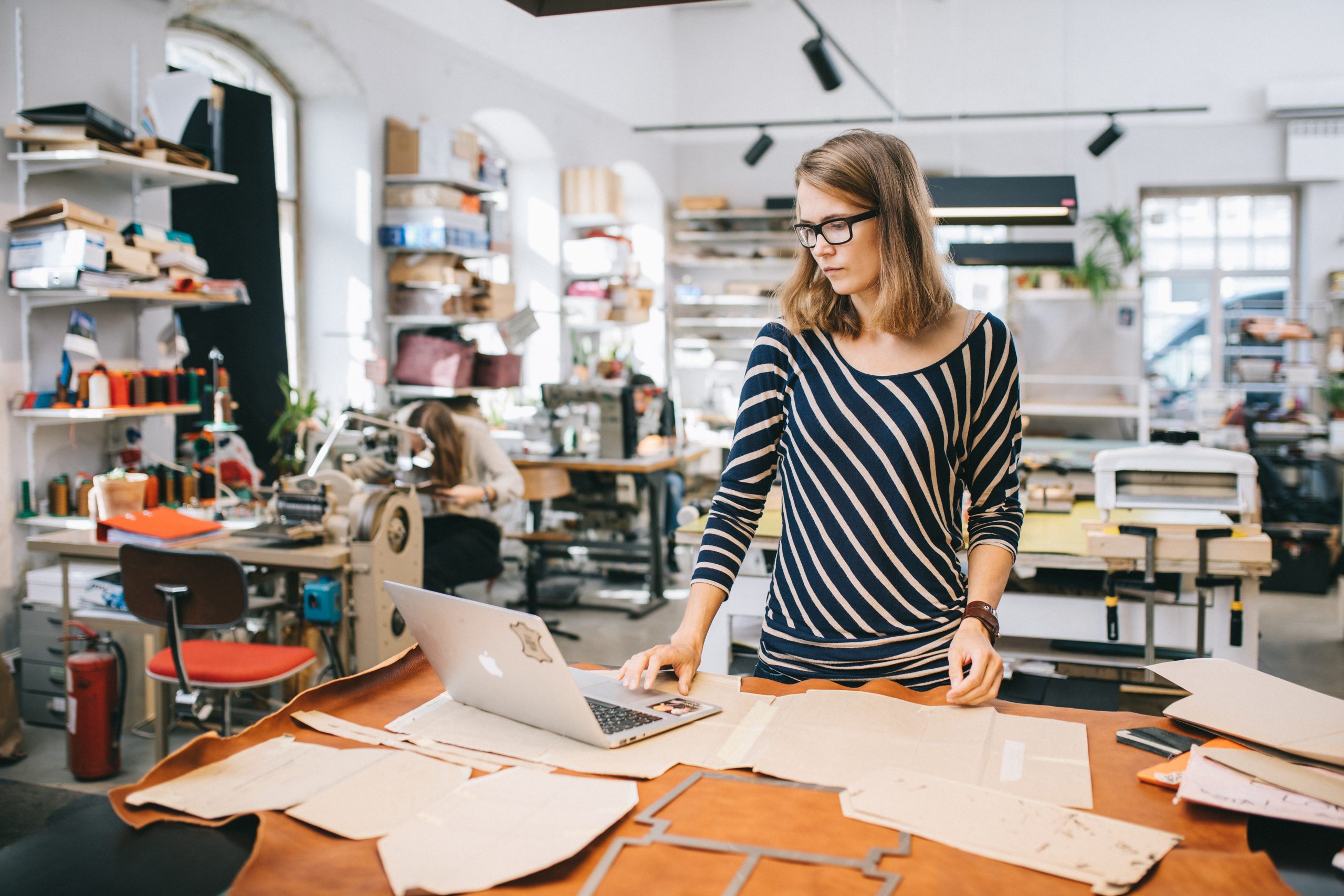
Here are the different intermittent manufacturing processes and how they function:
Batch manufacturing
Batch manufacturing is a method of producing your finished goods or sub-assemblies by compiling the different components of a product, through a step-by-step process.
And the quantity of these finished goods or sub-assemblies produced in a batch will also depend on different factors, such as raw material levels and demand planning.
This means in Batch A you could produce 100 finished goods, while in Batch B, you might only produce 50.
In this intermittent manufacturing process, raw materials move along your production line, leading to pauses between each step as the batch moves through each workstation.
Measuring the efficiency of the batch method in intermittent production all comes down to how long it takes to finish, as there could be delays that increase your manufacturing lead time, such as setting up a machine.
Job shop manufacturing
Job shop manufacturing is the intermittent production system for manufacturers who have a shop floor populated with workstations that have different tools and machines for performing different tasks.
The outcome of a production run with this intermittent process could be one product or a small batch of varying quantities.
But, regardless of quantity, due to the workstation separations and the nature of job shop manufacturing, customers have the opportunity to customize their orders.
This, in turn, means that products aren’t standardized and are produced in a low volume.
However, a smaller quantity of finished goods means that job shop manufacturers can offer a level of personalization that cannot be matched by factory owners producing items en masse.
Products pass different routes on the shop floor, since one customer’s order may travel an entirely different route to another customer’s order, depending on the amount of customization they requested on their product.
Discrete manufacturing
The final intermittent production method, discrete manufacturing, is essentially your IKEA styled-approach to manufacturing.
Meaning that discrete manufacturing concerns anything that uses components and sub-assemblies, such as bikes or skateboards, that can be easily taken apart.
What separates discrete manufacturing and the other methods is that the final product can have parts replaced, unlike an artisan lotion, for example, and is used by assemble to order (ATO) businesses.
However, discrete manufacturing might also only produce sub-assemblies as the final item, which will then be used elsewhere to build the finished product.
So, there you have it, the different types of intermittent manufacturing processes. But, let’s move onto intermittent production examples.
Intermittent production examples
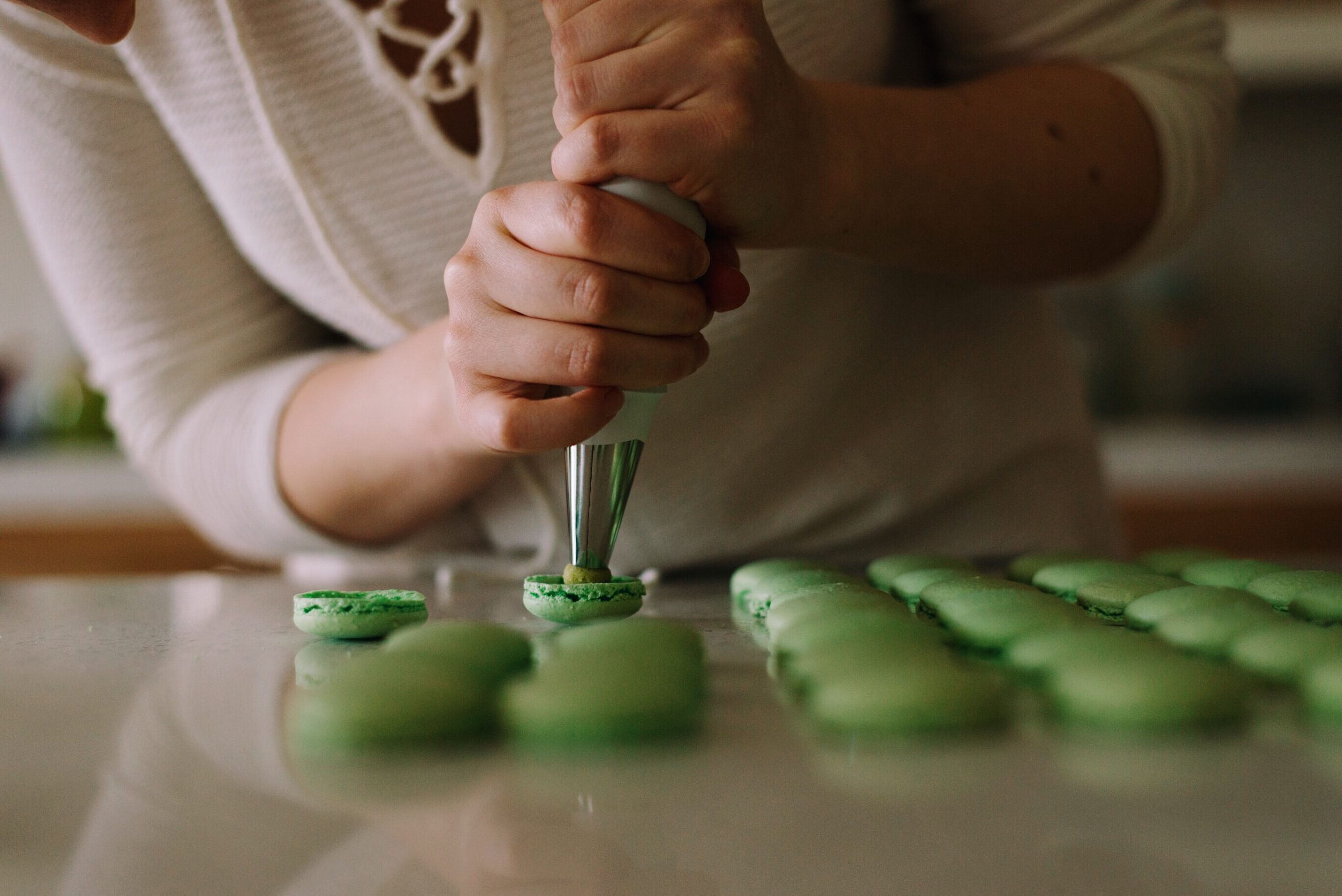
We have an idea about what is intermittent production, but let’s look at intermittent production examples to get a better understanding of what a business’s workflow might look like.
Let’s say you’re a baker making yummy cakes.
The processes for making cakes and treats are largely the same, but some cakes will be made differently from others.
So, maybe you make the sponge in batches, which will be used for all your cakes. You finish a batch, and most of the sponge will be used for cakes to be sold at your physical store.
However, you receive an order online, and someone has asked for a bespoke birthday cake.
You or a teammate might continue with the batch for your store, while someone else handles the custom order that might use some of the sponge, but this cake will require icing and different techniques.
As you can see, production would stop and start, and materials go through different workstations, as the cakes move through different points.
Maybe the batch and birthday cake pass through a jamming station, but that being the only process that they share.
So, that’s the intermittent production examples, what exactly are the advantages and disadvantages of using intermittent production?
Pro tip:
Regardless of your business type, intermittent manufacturing requires careful management of your inventory. So, be sure to get yourself up-to-date with raw material inventory management practices to not let your stocks get out of control.
Advantages and disadvantages of using intermittent production
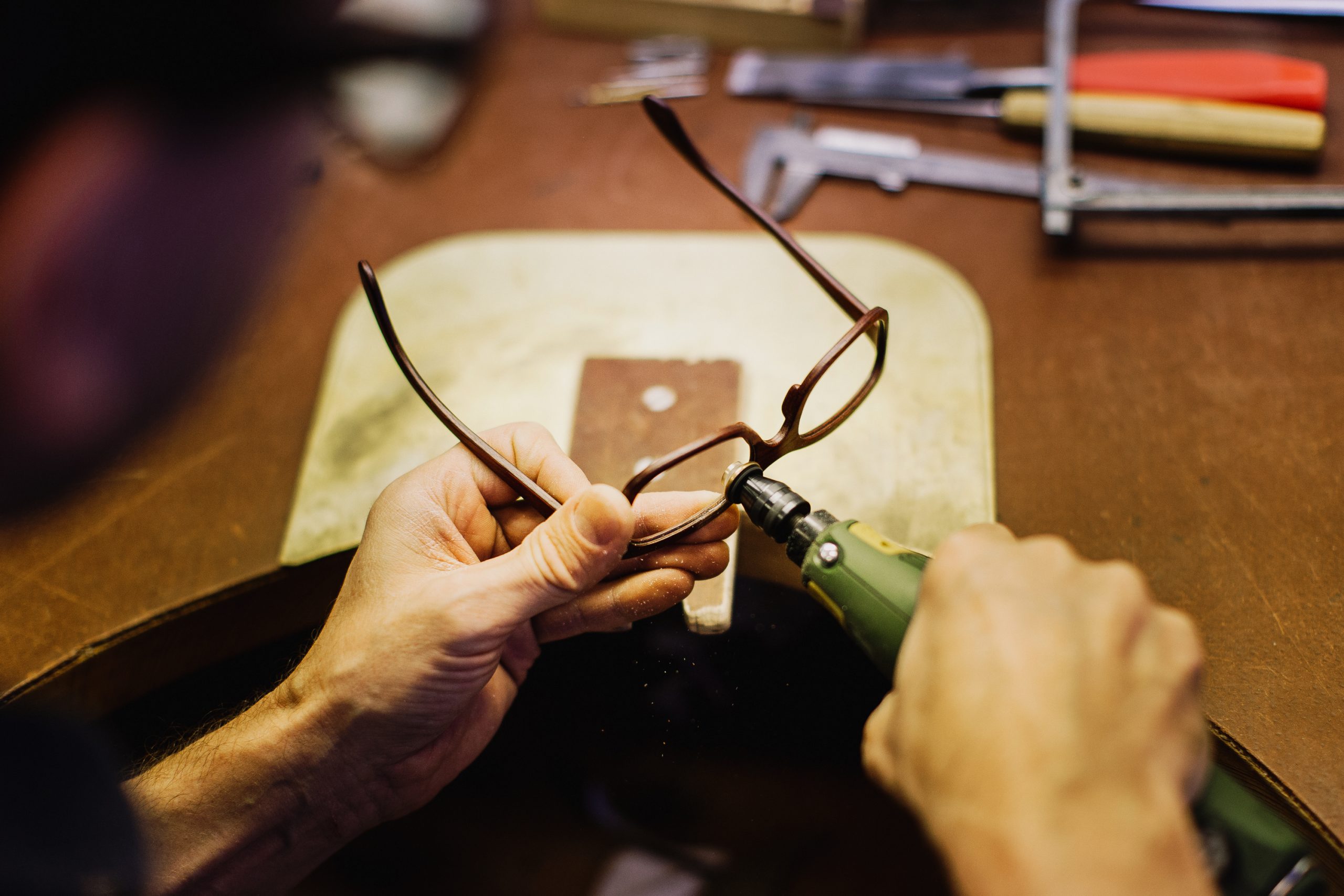
Using intermittent production in your business comes with a load of pros and cons.
And not only that, as we’ve explored throughout the article, intermittent manufacturing is only going to be beneficial for direct-to-consumer (D2C) manufacturers who follow an MTO workflow and offer, at least, some customization on their products.
So, before we look into the advantages and disadvantages of using intermittent manufacturing, it might be a good idea for you to start implementing this method into your business if:
- Your workstations are designed and located on your shop floor (or in other factories) to easily handle a wide variety of products
- You can achieve lean manufacturing, that is that your transportation (be that on the shop floor or between factories) is designed to be easily flexible to handle products going different routes
- You have the systems in place for multi-location inventory management necessary for storing raw materials and finished goods at different places
However, if you don’t meet these requirements, it doesn’t mean that intermittent production isn’t for you.
Advantages of intermittent manufacturing:
- You can adapt to changes in a product’s design or if a machine or tool breaks, you can avoid bottlenecks since another workstation will be able to perform the same tasks
- You can focus on a smaller group of products, which will help you to improve quality control by following your production quality control checklist and make the process of manufacturing products easier each time
- You can reduce your manufacturing costs as workers will be able to focus on specific tasks and your machines and tools can be repurposed for different product configurations
- Repeat orders lead to a smoother and more consistent production flow
- A workstation will have downtime, saving you on energy costs
Disadvantages of intermittent manufacturing:
- It’s a complex method, yes you can offer customization, but without a standardized approach, products will have a long manufacturing lead time
- Production planning and scheduling is complicated since manufacturing orders (MOs) come in at different times
- The raw materials and work-in-progress (WIP) inventories are high because of the irregular flow of work
However, by adopting software, such as an MES system, you can have an easier time mitigating these disadvantages.
Production planning and scheduling software
Katana connects your inventory, purchasing, and production in one platform for accessible, streamlined manufacturing. Read how it does it here.
Katana’s cloud manufacturing software for intermittent production
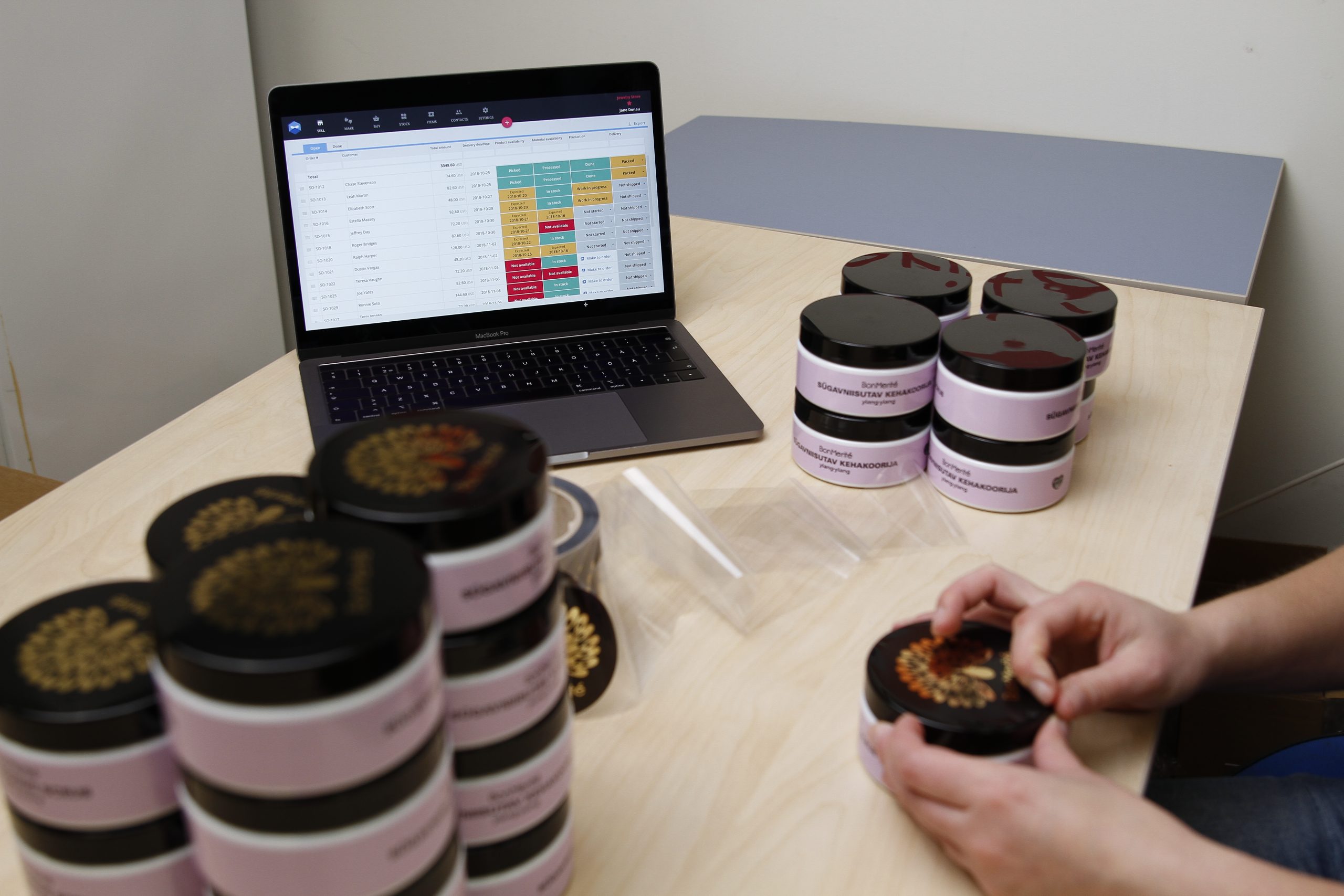
Katana’s cloud manufacturing software is an all-in-one solution for any manufacturer trying to get started with intermittent production in their business.
Katana was made to support MTO and MTS businesses with tons of features and integrations that can help you
Optimize Your Inventory Management
There’s nothing worse than forgetting to update your stock levels after a rush, leaving you making decisions based on incorrect inventory levels, resulting in production stops due to a stockout.
Katana updates inventory movement in real-time, so you know exactly how much stock you have immediately.
Best of all, Katana has a real-time master planner that takes your available raw materials and finished goods, and allocates them to open orders, so you can fulfill your orders as soon as possible.
Keep Your Team Focused
There’s nothing more frustrating and confusing than team members running around trying to find the latest production schedule.
Katana allows you to generate tasks and assign them to team members, so you and your workers know what they need to do, and when to do it.
And as for the schedule, when you generate an MO, Katana automatically schedules production for you.
However, if you need to switch up the workflow, our nifty drag-and-drop system allows you to easily do so, and the auto-booking system will even reallocate your inventory to the new workflow.
Grow Your Business
No more getting lost in your inefficient Excel spreadsheets! Katana gives those using intermittent production the tools to start implementing automated manufacturing into their business.
Doing so will allow you to automate those dull, time-consuming, and repetitive daily tasks, so you can stay focused on your manufacturing and grow your business.
Check out the video below to see exactly how Katana can help your manufacturing business:
Conclusion
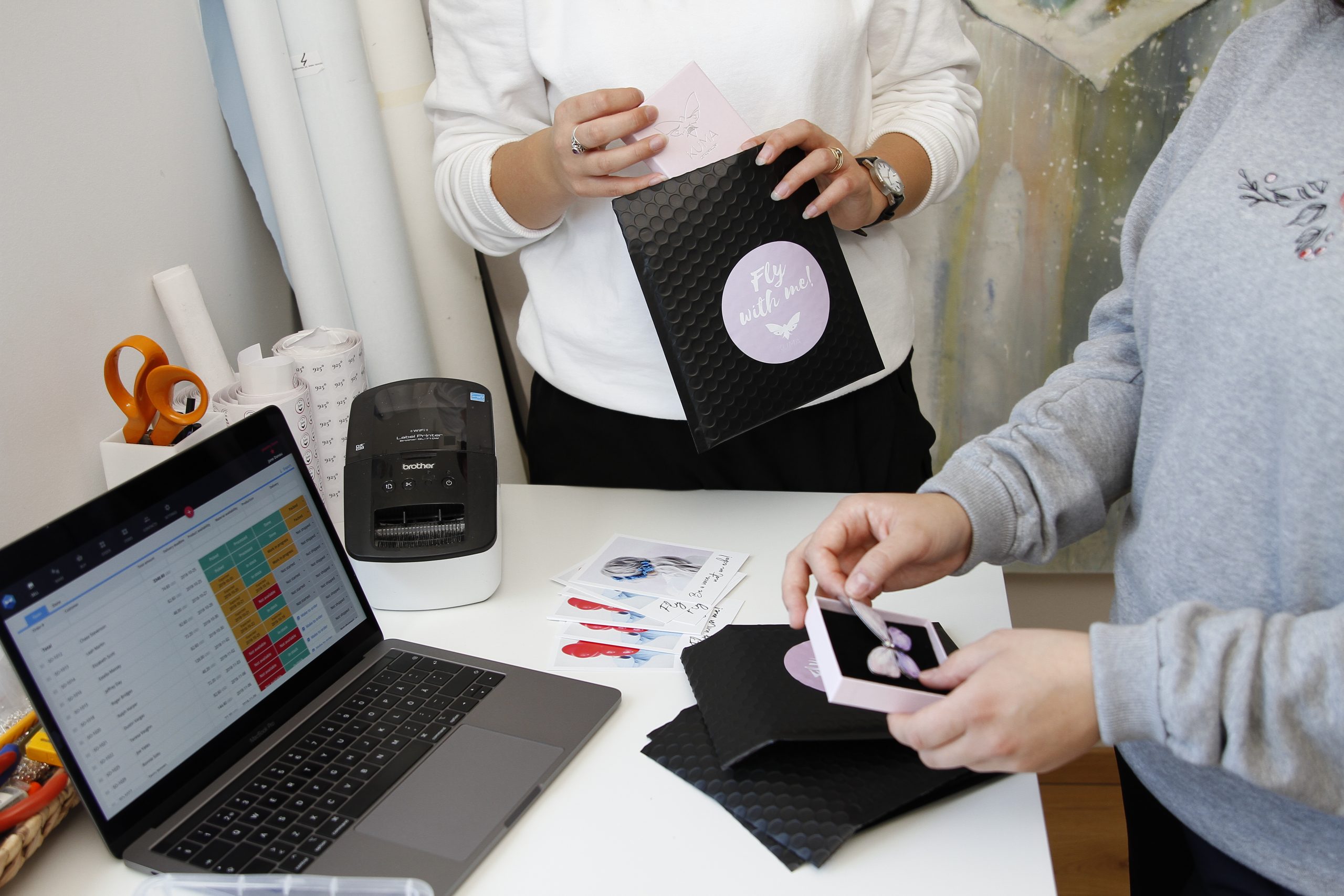
And there we have it, everything you need to know about intermittent production, from what it is, to the workflows it covers, and the software that can help you implement it.
Just be sure to look out for job shop software that allows you to try it out before you commit any resources to it.
Request a demo, so you can see for yourself how it can support your intermittent manufacturing business.
And if you like the look of it and feel like you’d be better off with a demonstration of the software, please don’t hesitate to get in touch, and we’d be happy to go through it with you.
We hope that you found this article useful, and if you have any questions, please don’t hesitate to drop us a message below, or get in touch with us over on our social media channels.
And until next time, happy manufacturing.
Team Katana
Table of contents
Get inventory trends, news, and tips every month
Get visibility over your sales and stock
Wave goodbye to uncertainty with Katana Cloud Inventory — AI-powered for total inventory control