Manufacturing capacity planning software to make what you can, when you can
Reap the many benefits of capacity planning, with clear lead times, automated reorder points and improved overall resource management. Using Katana as capacity planning software for manufacturing will save you time and make daily operations easier.
Manufacturers and distributors always need to plan ahead to avoid stock-outs, delays, and unhappy customers
Using manufacturing capacity planning software gives you an overview of your entire production process, greater control over resource management, and an understanding of how your entire supply chain can support your daily operations. It’s planning and management in a single platform.

Use manufacturing operations data to do predictive analytics and always know what you need
Manufacturing practically any product is complex and has a number of steps involved to make sure the finished product is up to scratch. This is why a well-plotted planning process is crucial, and this includes understanding your manufacturing capacity on a daily, weekly, and monthly basis.
With the holistic overview and thorough business data provided by Katana, you can use analytical modeling to help plan ahead and not over or under-order on raw materials for your business. Here are some features of capacity planning Katana helps with:
- You’ll have complete control over your inventory within Katana, including the units of measurement it comes in
- With our detailed bills of materials, you can create recipes for each individual product to precise specifications
- Watch both your stock and safety stock, and get automatic calculations and updates as new orders come in
- Set automatic reorder points, just in case an item is suddenly in huge demand, so you won’t need to manually reorder
- Manage all of this in a single platform with clear information across your business
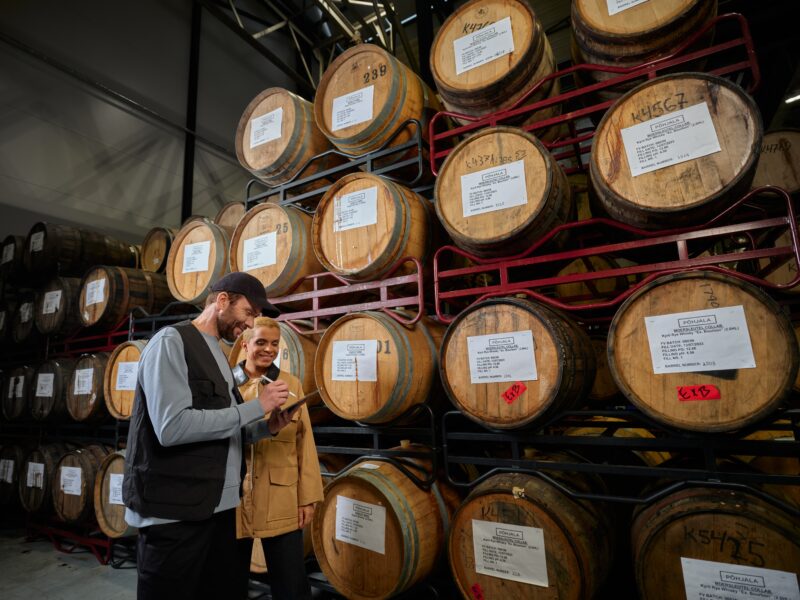
With forecast accuracy, you make daily operations easier for your team and yourself
Along with understanding your requirements for raw materials, knowing your accurate capacity will allow for greater supply chain optimization across your entire production process. This makes life simpler for your production team, whether it’s one individual, or a whole crew working in your warehouse. Using historical data to inform your production management means production and capacity are working in sync.
Here are a few of the capacity planning tools Katana offers that can feed into your overall production data and make operations easier:
- Our mobile shop floor app lets you set tasks for your team remotely, so they know what needs to be done on a daily basis
- Using the app you can then track completed products and shipped orders
- This helps with better overall warehouse management making your operations streamlined and adding clarity
- Track your raw material inventory and completed stock with barcode tracking in one, or multiple, warehouses
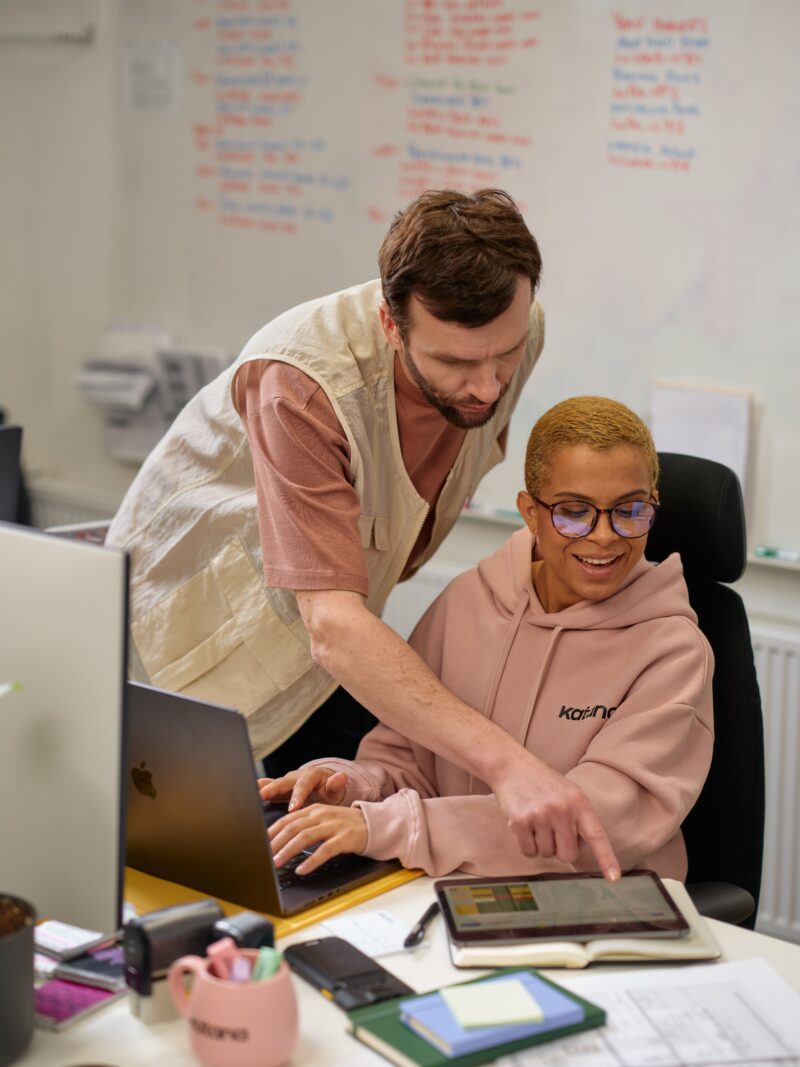
How capacity planning helps lead to more finished products and happier customers
With optimized production, your finished products will be stacking up, ready to be shipped out to eager customers. As you make sales, you’ll be able to start utilizing sales data from your e-commerce store and Katana to forecast demand in the future and feed this into your production planning.
With your demand plan in place, you’re covered for both sales and operation planning and will comfortably meet customers’ demands every time. Less to sweat about. Here are a few features of Katana that helps with sales, accounting, and shipping:
- Choose from one of our native e-commerce integrations or one of many third-party providers
- Using our partner Shopify will allow you to sync data from an in-store POS system to track both physical and online sales
- Get the best accounting software on the market, with our native integrations with QuickBooks Online and Xero
- For other accounting providers, we offer our API to sync Katana and your software of choice
- And to get orders sent out, we offer two brilliant shipping partners to reach customers across the globe
Want to see Katana in action?
Book a demo to get all your questions answered regarding Katana’s features, integrations, pricing, and more.
Manufacturing capacity planning software that integrates with your favorite tools for a smooth workflow
From native integrations to code-less templates or fully customizable API integrations
Katana cloud ERP software’s batch production features give users access to the API, allowing you to create custom workflows and connect your business apps to manage your sales, manufacturing, and accounting all on one platform. Automate data transfers between the services you use to level up efficiency. Take a look at our API documentation to learn more.
With Katana, we are able to track products, build recipes for materials, and set reorder points for our materials as well. That was one thing that was very difficult to manage was raw material inventory — for example, how many black t-shirts do I need to order? That was the main reason why we selected Katana.”
Lisa Diep
Chief Operating Officer, Peace Collective
With Katana, we can more effectively see and follow inventory levels, and have recipes and bills of materials (BOMs) for our manufactured products that let us follow the manufacturing status throughout the whole production cycle.”
Richie Duncan
Founder, Kodama
We needed something more than just a spreadsheet but we didn’t like to pay a crazy amount for a system we wouldn’t fully use. Tracking inventory and what stage it is in has been incredibly helpful. It’s helped our team have a clearer delineation of the order of operations for each product in our catalog.”
Sarah Zinger
Director of Production Logistics, System76
When working with our previous solution, we noticed that our inventory was completely off. We saw that Katana had in-studio management that would allow us to assign tasks and monitor progress, which is something we really needed.”
Alaina Oehrlein
Production Lead, Essence One
Manufacturing capacity planning software FAQs
Capacity planning in an ERP (Enterprise Resource Planning) system refers to using software tools and techniques to plan and manage the production capacity of a manufacturing plant. The goal of capacity planning in an ERP system is to optimize the use of resources, such as labor, machines, and raw materials, to meet the demand for products while minimizing waste and reducing costs.
An ERP system provides a centralized platform for managing and tracking production processes and can be used to perform the following capacity planning tasks:
1. Forecasting demand — use historical data and market trends to estimate future product demand
2. Identifying capacity constraints — analyze the production process to identify any factors that limit production capacity, such as machine downtime, labor availability, and raw material availability
3. Evaluating current capacity — determine the current production capacity of the manufacturing plant and compare it to the demand forecast
4. Developing capacity options — identify different options to increase or optimize production capacities, such as adding new equipment, increasing shift hours, or outsourcing production
5. Selecting the best option — evaluate the different options and select the one that provides the best balance between cost, feasibility, and production capacity
6. Implementing the plan — once the best option has been selected, implement the plan using the ERP system to manage and monitor the production process
Software capacity planning in manufacturing refers to using software tools and techniques to plan and manage the production capacity of a manufacturing plant. The goal is to optimize the use of resources, such as labor, machines, and raw materials, to meet the demand for products while minimizing waste and reducing costs.
There are three main types of capacity in manufacturing:
1. Design capacity — the maximum possible output a manufacturing plant can produce based on its design specifications, assuming that all resources are being used optimally and without constraints
2. Effective capacity — the actual production capacity that a manufacturing plant can achieve, considering practical limitations such as machine downtime, labor availability, and raw material availability
3. Rated capacity — the production capacity that a manufacturing plant is marketed or rated to produce, usually less than the design capacity and may reflect the expected effective capacity under normal operating conditions
Each of these types of capacity plays a different role in capacity planning and management, and it is important to understand the differences to plan and optimize production effectively. By evaluating and managing these different types of capacity, manufacturers can ensure that they have the resources and capabilities needed to meet the demand for their products.
Get visibility over your sales and stock
Wave goodbye to uncertainty with Katana Cloud Inventory — AI-powered for total inventory control