The ins and outs of light manufacturing
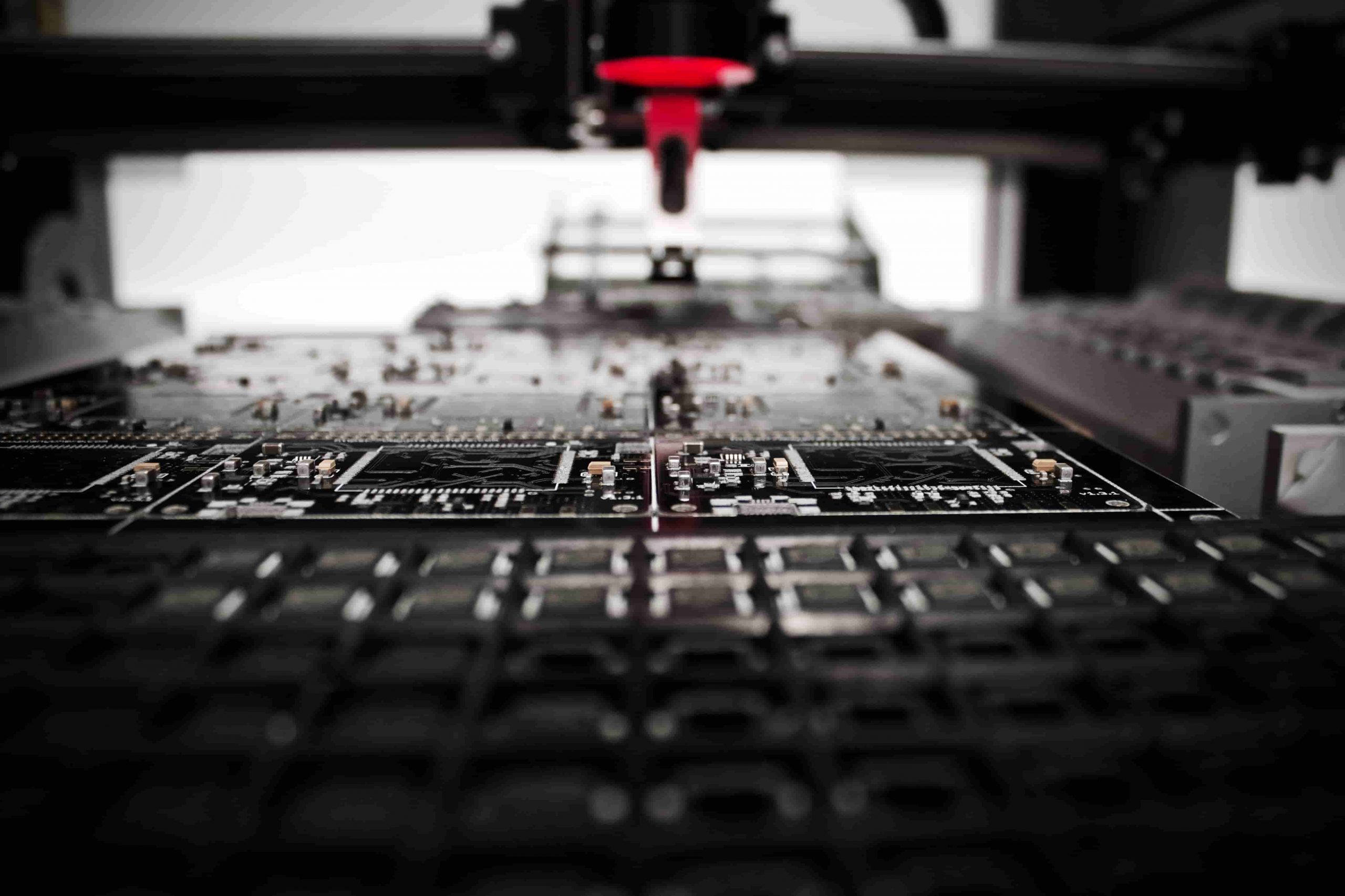
You may have heard the term light manufacturing, but what does it actually mean?
No, it’s not an umbrella term to include all companies that manufacture lamps. That being said, manufacturing lamps and light bulbs does fall under light manufacturing but not because of the end-products’ illuminative characteristics.
In this article, we’ll take a closer look at light manufacturing, what it is, how it’s different from heavy manufacturing, and how you can improve your light industry processes.
What is light manufacturing?
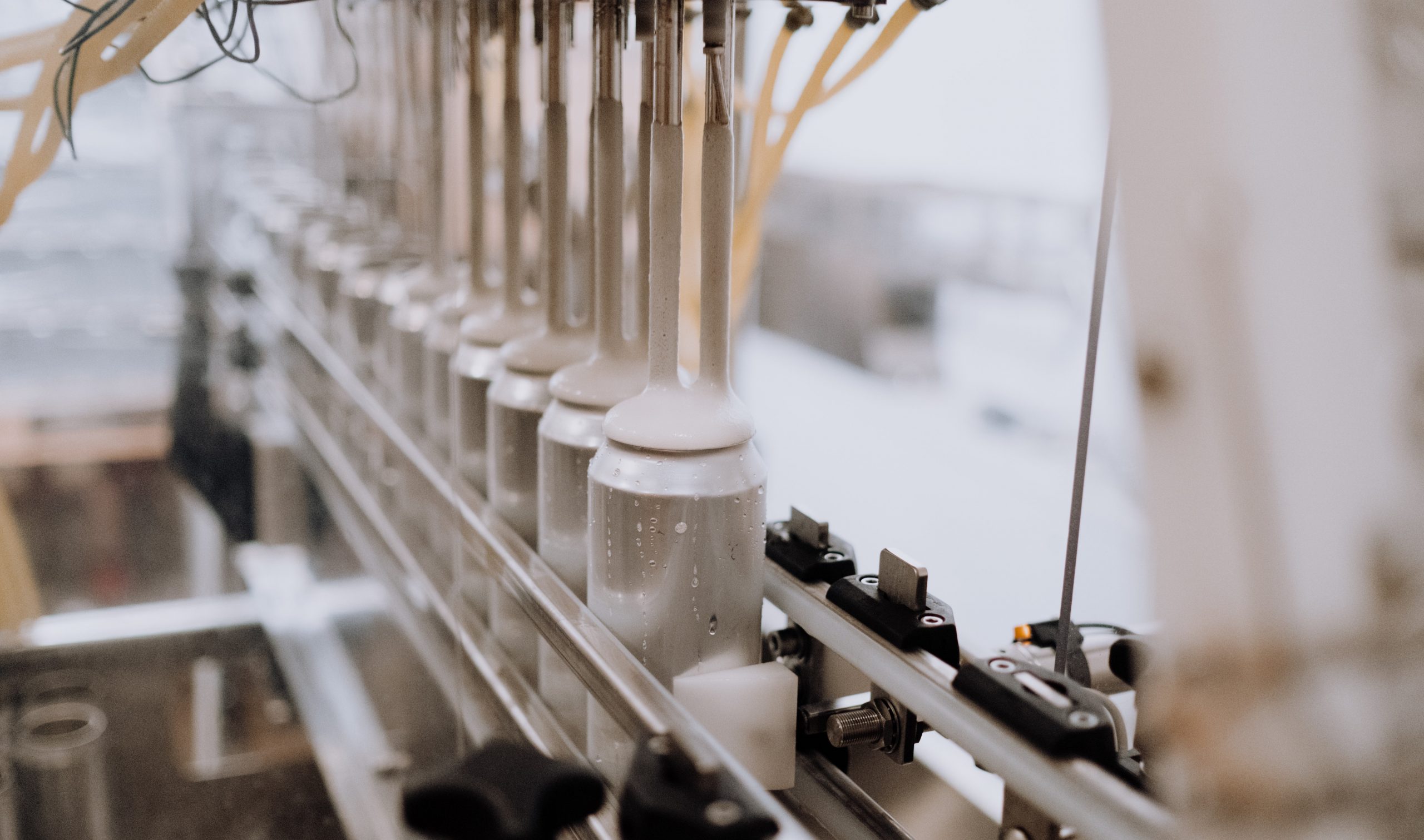
Light manufacturing, often referred to as light industries, is a process of manufacturing goods using light machinery and equipment where the whole manufacturing takes place inside an enclosed building — rather than outdoors, using heavy equipment and plants, covering a large industrial area.
Light manufacturing is used to produce various goods, including food items, shoes, and toys. It is a type of manufacturing process that is done on a smaller scale than heavy manufacturing and often uses less energy and resources. Whenever the manufactured product is targeted to be sold to the end consumer — it is classified as light manufacturing.
Examples of light manufacturing
The definition of light manufacturing isn’t as clear-cut, so let’s look at some examples to better understand what it encompasses.
Light manufacturing includes things like clothes, electronics, and furniture inventory. The steps to manufacture these products are often quite similar.
As a first step, manufacturers need to gather the raw materials. These can include fabric for clothes, wood for furniture, or metals and plastics for electronics. These raw materials go through a series of processes to create the final product. For example:
- Fabric will be cut to the correct size and shape for clothes, then sewn together
- Wood will be cut, sanded, and joined together with fasteners to make furniture
- Metals and plastics will be molded, shaped, and assembled to make consumer electronics
The main differences between light and heavy manufacturing
Both light and heavy manufacturing deal with the production of goods — here are the key differences between the two manufacturing methods.
Scale of production
One major difference between light and heavy manufacturing is the scale of production. Light manufacturing often takes place on a smaller scale than heavy manufacturing, meaning that products are typically manufactured in smaller quantities. This is because light manufacturing generally uses less energy and resources than heavy manufacturing, making it more suitable for small-scale production.
Types of products
The types of products that are manufactured also differ between light and heavy manufacturing. Light manufacturing typically produces goods targeted at the end consumer, such as clothes, shoes, toys, and electronics. Heavy manufacturing, on the other hand, focuses on producing goods that are used in producing other products, such as raw materials, machinery, and equipment.
Energy and resource usage
Light manufacturing generally uses less energy and resources than heavy manufacturing. This is because light manufacturing often takes place on a smaller scale with less machinery and equipment. While light industry consumes less raw materials and resources, it’s very labor-intense, so it may need a lot more human resources.
Environmental impacts
The environmental impacts of light and heavy manufacturing also differ. Light manufacturing typically has lower emissions than heavy manufacturing since it uses less energy and resources. In addition, light manufacturing often takes place indoors, which can help to reduce the release of pollutants into the environment.
There are some exceptions to this rule, however. If light manufacturing processes use harmful chemicals or generate a lot of waste, they can still have a significant environmental impact.
How to manage light manufacturing?
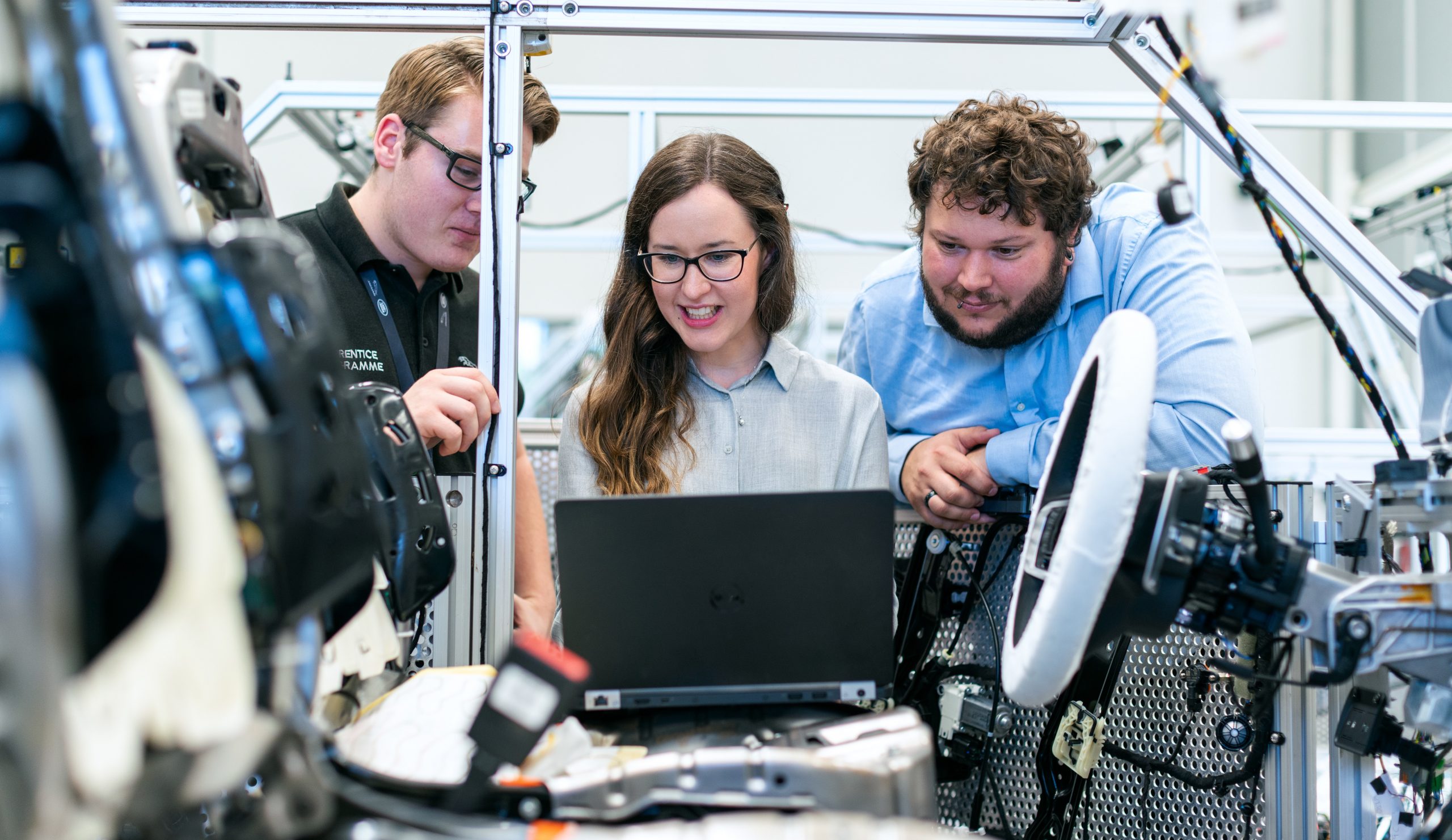
There is a lot of emphasis put on maximizing resources in light manufacturing. As such, it is essential to have a well-managed operation to succeed. Let’s look at some manufacturing processes that can help you maximize your available resources.
Lean manufacturing
Lean manufacturing is a method of production that focuses on minimizing waste and maximizing productivity. In lean manufacturing, the target is maximizing customer value while minimizing waste. This is achieved by streamlining the manufacturing process and eliminating anything that does not add value for the customer.
Operations in a lean manufacturing environment are typically very well organized and managed. This helps to ensure that resources are used efficiently and that products are produced in a timely manner.
In order to implement lean manufacturing, it is important to have a clear understanding of the manufacturing process. Once the manufacturing process is understood, it is then possible to identify areas where waste can be eliminated.
There are many different tools and techniques that can be used in order to eliminate waste in the manufacturing process. Some of these include value stream mapping, 5S, and Kanban.
Cellular manufacturing
Since space is often limited in light manufacturing, it’s important to use the shop floor as efficiently as possible. One way to do this is by using a manufacturing cell.
A manufacturing cell is a group of machines that are arranged in such a way that they can work together to produce a product. Manufacturing cells are typically used in order to produce small batches of products.
The benefits of using manufacturing cells include reduced setup times, increased flexibility, and improved quality control. In addition, manufacturing cells can help to improve the utilization of resources and reduce waste.
Routing
It is important to have an efficient routing plan to determine the order in which operations will be performed. This helps to minimize waste and maximize productivity.
One way to develop an efficient routing plan is by using a flowchart. A flowchart is a graphical representation of the manufacturing process. It can be used to identify the various operations that need to be performed in order to produce a product. In addition, a flowchart can be used to determine the most efficient order for performing these operations.
Another tool that can be used for routing is a Gantt chart. A Gantt chart is a bar chart showing the sequence of operations and the relationships between them. A Gantt chart can help develop a manufacturing schedule. This schedule can then be used to determine the most efficient way to utilize resources and minimize waste.
Adopt Katana and streamline your manufacturing processes
Book a demo to get all your questions answered regarding Katana’s features, integrations, pricing, and more.
Leverage software to manage it all
One way to streamline your processes and boost productivity in light manufacturing is to use software to automate tasks.
Enterprise resource planning (ERP) software is a business management software that helps streamline manufacturing operations by managing all of the data and information associated with it. This includes customer orders, inventory levels, production schedules, and more.
Katana’s manufacturing ERP software can help to improve communication and collaboration between different departments within the company. In addition, ERP software can provide real-time visibility into the manufacturing process, which can help to identify potential bottlenecks and issues.
Katana’s manufacturing ERP equips you with all the tools you need to take full control of your production lines and inventory. In addition, Katana connects with the most popular business tools to ensure that your data is always up-to-date across all platforms.
Light manufacturing can be a complex process, but using the right tools and techniques can streamline operations and improve productivity. Book a demo with Katana and let there be light (manufacturing).
Table of contents
Manufacturing guide
More on manufacturing
Get visibility over your sales and stock
Wave goodbye to uncertainty by using Katana Cloud Inventory for total inventory control
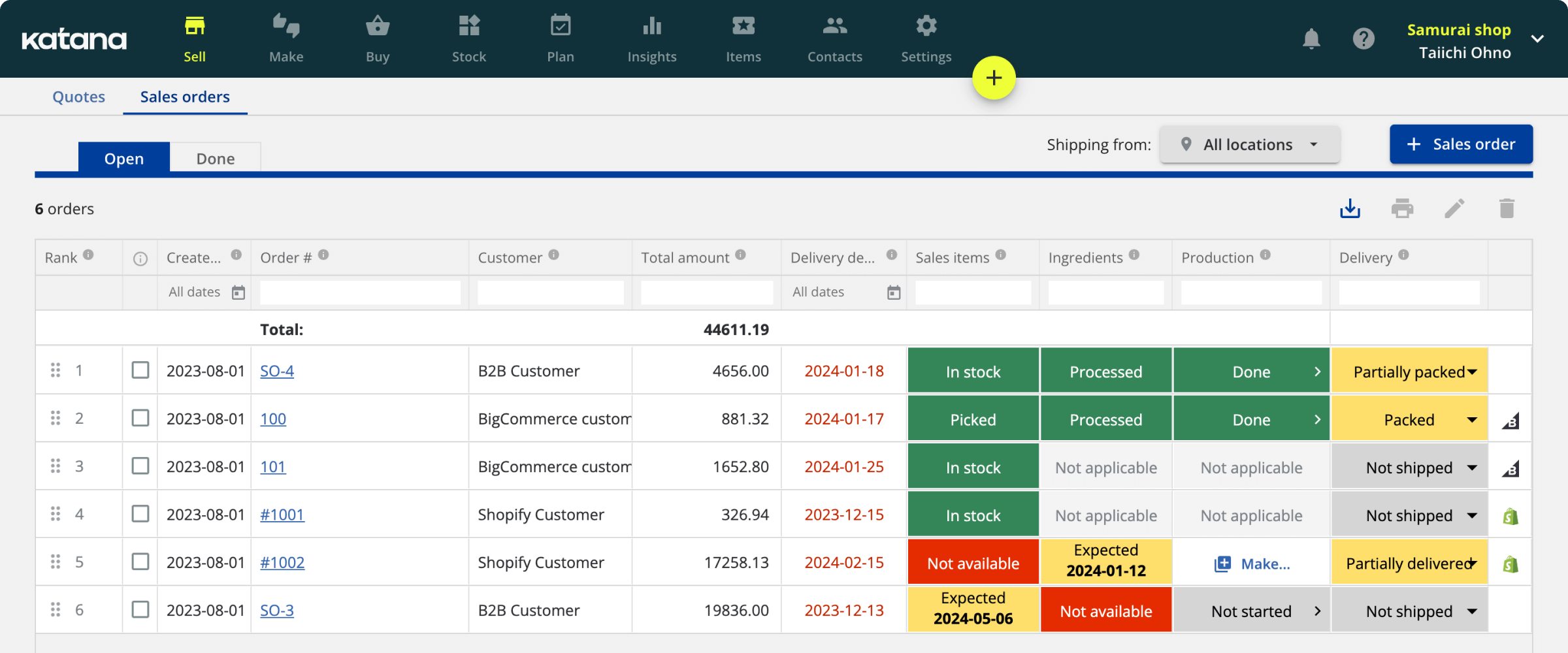