Complete guide to cost of good sold (COGS)
In accounting and finance, few concepts hold as much significance for businesses as cost of goods sold (COGS). Whether you’re an aspiring entrepreneur, a seasoned business owner, or simply someone curious about the financial intricacies behind the products you purchase, understanding COGS is essential.
This metric lies at the heart of every company’s financial operations, shedding light on the direct costs of production, the efficiency of operations, and the foundation of profit calculations.
COGS, often referred to as the cost of sales, provides a window into how much it truly costs a company to manufacture or acquire the goods it sells to its customers. From the raw materials used to create a product to the final packaging that reaches consumers, every step along the production chain contributes to the COGS equation.
This blog delves deep into the world of COGS — exploring its definition, significance, calculation methods, and the pivotal role it plays in influencing pricing strategies, inventory management, and overall business decision-making.
What is cost of goods sold?
Cost of goods sold (COGS) is an essential accounting term that represents the direct costs incurred by a company to produce or purchase the goods it sells during a specific period. COGS is a significant component of a company’s income statement, which helps determine the gross profit.
COGS is a method of giving a real-world valuation to your inventory. It’s a must-know for proper inventory management. Your material and labor expenses could fluctuate from month to month. It pays to keep up with the price of getting your goods to market.
COGS tells you how much you spend to turn your raw materials into sold products.
It is useful in two main ways:
- It gives you important information about your business’ expenditure
- It is necessary to produce accurate tax statements
In the US, scaling manufacturers are routinely subject to tax audits. The IRS makes sure they are reporting their income accurately. This means that COGS is serious business.
Calculating cost of goods sold is vital to know your taxable income. Other metrics, like leftover stock, can also be taxable, so you need to be on top of everything. Additionally, the accurate calculation and reporting of COGS is necessary under generally accepted accounting principles (GAAP).
We’ll get to how to calculate cost of goods sold, but first, let’s go over the importance of COGS.
Importance of COGS

Cost of goods sold is one of the vital cogs in your business. It may be tempting to ignore or overlook it — this is not only bad practice but bad for your margins. We mentioned tax implications, but there are many more reasons why you need to know your COGS:
- Profit calculation — COGS is a critical component in calculating a company’s gross profit. Gross profit is the difference between total revenue (sales) and COGS. It provides insight into how efficiently a company is producing goods and generating revenue from its core operations.
- Inventory management — By comparing COGS with inventory levels, a company can assess how effectively it’s managing its inventory. If COGS is significantly higher than the change in inventory, it might indicate inefficiencies in managing stock or potential issues with overproduction.
- Pricing strategy — Understanding COGS is crucial for determining the appropriate pricing strategy for products. Pricing too low could lead to insufficient profits, while pricing too high might result in decreased sales. An accurate understanding of COGS helps strike a balance between profitability and competitiveness.
- Cost control — Analyzing COGS helps identify cost drivers and areas where costs can be controlled. This information can be used to optimize production processes, negotiate better deals with suppliers, and streamline operations.
- Financial analysis — COGS is a key metric for financial analysis. It’s used in various financial ratios and calculations, such as the gross profit margin and inventory turnover ratio. These ratios provide insights into a company’s efficiency, profitability, and liquidity.
- Tax reporting — COGS is deducted from total revenue to calculate the gross profit, which affects the taxable income of a business. Accurate reporting of COGS is crucial for complying with tax regulations and minimizing tax liabilities.
- Investor and stakeholder communication — Investors, lenders, and stakeholders use COGS as a measure of a company’s operational efficiency and financial performance. It’s an essential piece of information in financial reports and presentations.
- Performance measurement — COGS allows companies to evaluate their performance over time and against industry benchmarks. Comparing COGS with competitors or industry standards can highlight areas for improvement and innovation.
- Budgeting and planning — COGS data is crucial for budgeting and planning purposes. It helps companies forecast expenses, set production targets, and allocate resources effectively.
As you can see, COGS is a fundamental metric that impacts many aspects of a company’s operations and strategic decisions. Next, let’s see what’s different about cost of goods sold in manufacturing.
Cost of goods sold in manufacturing
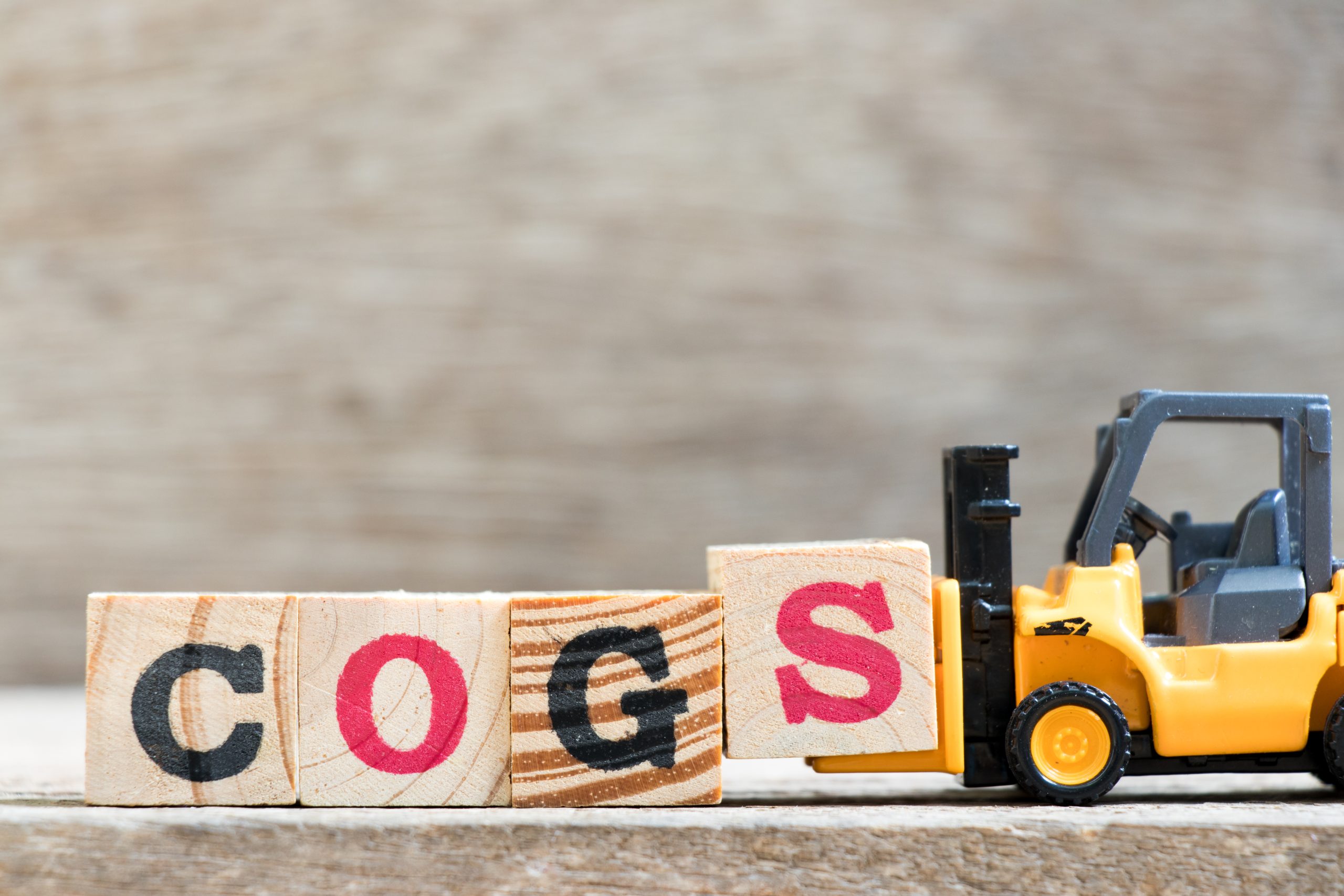
Cost of goods sold in manufacturing holds specific considerations that differentiate it from other types of businesses. In the manufacturing sector, COGS encompasses not only the direct costs associated with acquiring or producing goods but also factors that are unique to the manufacturing process. Here are some specific aspects of COGS in manufacturing:
- Bill of materials (BOM) — Manufacturing involves assembling products from various components. The COGS calculation in manufacturing incorporates the costs of raw materials, components, and subassemblies specified in the BOM required to create the finished goods.
- Work-in-progress — COGS in manufacturing considers work-in-progress inventory, which represents partially completed products at various stages of the production process. The costs incurred for these partially completed units are included in COGS when the finished goods are completed and sold.
- FIFO, LIFO, or MAC — Manufacturing companies often use either FIFO, LIFO, or MAC to value their inventory and calculate COGS. These methods are especially relevant when dealing with different batches of raw materials and components.
- Quality control and scrap — COGS considers quality control efforts and potential waste or scrap generated during the manufacturing process. These factors impact the cost of producing each unit and subsequently influence COGS.
- Inventory valuation — Manufacturing often involves more complex inventory scenarios, such as work-in-progress and finished goods. Properly valuing these different types of inventory is crucial for accurate COGS calculations.
Accurate COGS calculations are vital for understanding the true cost of producing goods and making informed decisions related to pricing, inventory management, and overall profitability in the manufacturing sector.
How to calculate cost of goods sold
First, it’s important to understand what is included in COGS and what isn’t.
Income included in COGS:
- Sale income from manufactured goods
- Sale income from any resold goods
Income not Included in COGS:
- Income from any other services besides selling goods
Expenses included in COGS:
- Raw materials
- Direct labor costs
Expenses Not Included in COGS
- Overheads and other indirect costs
- Taxes
To calculate COGS, you first need to decide on the time period you want to measure. Then find out the value of your inventory at the beginning and end of the chosen period. Don’t forget to include any additional inventory purhcased. Include the direct labor cost as part of the inventory valuation.
The COGS formula is relatively straightforward.
Cost of goods sold formula:
COGS = Opening inventory + purchases during the period – closing inventory
Here’s what each of these terms means:
- Opening inventory — The value of the inventory (raw materials, work-in-progress, or finished goods) at the beginning of the accounting period.
- Purchases during the period — The total cost of additional inventory purchased or manufactured during the accounting period.
- Closing inventory — The value of the inventory at the end of the accounting period.
As mentioned above, COGS excludes other costs like operating expenses (e.g., salaries, rent, utilities, marketing, etc.), which are recorded separately on the income statement. The result of the COGS calculation represents the actual costs directly associated with producing or acquiring the goods that have been sold during the given period.
The gross profit is then calculated by subtracting COGS from the total revenue (sales) generated during the same period:
Gross profit = Total revenue – COGS
Of course, this doesn’t take into account all your losses (and maybe not all your income). You need to work out other forms of revenue and expenses for your net profit.
So how to value your inventory? This depends on the inventory costing method you use. Each has advantages and disadvantages. The three main options are:
- First in, first out (FIFO)
- Last in, first out (LIFO)
- Moving average cost (MAC)
FIFO, LIFO, or MAC
Let’s take a closer look at the three costing methods and which one to use for calculating your cost of goods sold in manufacturing.
First in, first out (FIFO)
Many large manufacturers regard this as the theoretically correct inventory valuation method. It asserts that the first materials and stock to come into inventory will be the first out when sold.
- Advantage — Gives you a more accurate valuation of your current inventory because all present inventory best represents the cost of the inventory most recently purchased.
- Disadvantage — The COGS reflects older historical costs. That means the gross profit calculation may not reflect the actual figure.
Last in, first out (LIFO)
This is selling the most recent additions to your inventory first. If the cost of raw materials increases, the company will sell the higher-cost goods first. This means a business can report higher deductions for tax purposes.
- Advantage — Can be good for a company’s cash flow as it records less taxable income.
- Disadvantage — The last items added to inventory are usually the most expensive. This can inflate your COGS.
Is LIFO allowed?
- Allowed by generally accepted accounting principles (GAAP)
- Banned by international financial reporting standards (IFRS)
GAAP , but most other countries comply with IFRS.
Moving average cost (MAC)
As the name suggests, this method takes your average unit cost and applies it to all goods sold in that period. To calculate it, simply multiply the average purchase price by the number of units sold.
- Advantage — Gives a more realistic reflection of your COGS. Using averages smooths out changes in market prices.
- Disadvantage — The IRS and other tax authorities may still require you to report your inventory costs using another method.
All of the above accounting methods are accepted under GAAP, so can be used in the US.
Calculating COGS example
Say you have a handmade jewelry business. You start with $1,000 of jewelry inventory. This includes $800 in raw materials and $200 in direct labor (manufacturing) costs.
You sell $600 worth of jewelry, leaving $400 remaining in stock. To keep up with this demand, you manufacture $500 more jewelry, including $100 in labor costs. You then sell $350 worth of jewelry.
Over this period, the cost of goods sold formula will look like this:
COGS = 1,000 + 500 – 550 = $950
Now you know the cost of goods sold, you can decide if you have a reasonable markup for your products. For handmade jewelry, this could be at least two times the material and labor cost. So, if the cost-price of $1,500 was sold with a 100% markup, then the revenue would be $3,000.
You can then use this to calculate gross profit:
Gross profit = 3,000 – 950 = $2,050
Of course, it’s possible to calculate cost of goods sold without including direct labor costs. As per GAAP, direct labor costs should be included.
By doing this, you can work out the ratio of labor to manufactured goods on a larger scale. This is useful to consider when analyzing your workshop’s overall efficiency.
Calculating direct materials
Let’s break this down further by showing the calculation of raw materials expenses per unit as part of COGS.
Say you’ve started a hobby business selling handmade scented candles. You purchase the necessary equipment, raw materials, and supplies. In order to calculate COGS, you need to know the value of raw materials that goes into one unit.
Let’s go over the raw materials cost and how it relates to COGS.
The raw materials are:
- Wax
- Fragrance oil
- A wick
- A glass jar
- A warning label
- A brand label
You buy the primary material, wax, at $0.07/oz. You decide that for a good size, each candle will use 6oz. of wax.
$0.07 x 6 = $0.42
That’s $0.42 worth of wax for each candle.
Each candle needs fragrance oil at an amount of 6% of the wax weight. So, multiply six percent by the total wax weight to find the amount of fragrance oil.
0.06 x 6oz = 0.36oz
Multiply this by the total price of fragrance oil per ounce ($1.25), and you get $0.45.
Then you add in the cost of the wick at $0.10. The other materials are a glass jar at $0.50, a warning label at $0.03, and your brand label at $0.50.
Your total raw materials cost per unit is $2.00. This is useful for calculating the total manufacturing cost. You sell each candle for the price of $8. So, you have a $6 gross margin per unit sold.
You create a first batch of 30 candles which is worth $60 plus direct labor costs.
In the first two weeks, you sell 25 candles at the standard selling price of $8.
As the first batch is running low, you manufacture a further 30. But your supplier costs have gone up, and it now costs $3 to make one candle. You then sell a further 15 candles. Using moving average cost, it doesn’t matter which batch is sold for the calculation to work.
So, the cost of goods sold breakdown for this month would look like this.
In practice, you would also add in direct labor costs, depending on wage per hour and the time it took to produce those two batches.
Don’t forget that this is gross profit, and you still need to take into account taxes and other expenses. This makes the calculations even more complicated. But don’t fret — there is a way to do this automatically.
Want to simplify your COGS calculations?
Katana’s cloud inventory platform tracks the cost of all resources needed to manufacture a product, saving you hours when calculating your COGS.
How Katana helps with product costing
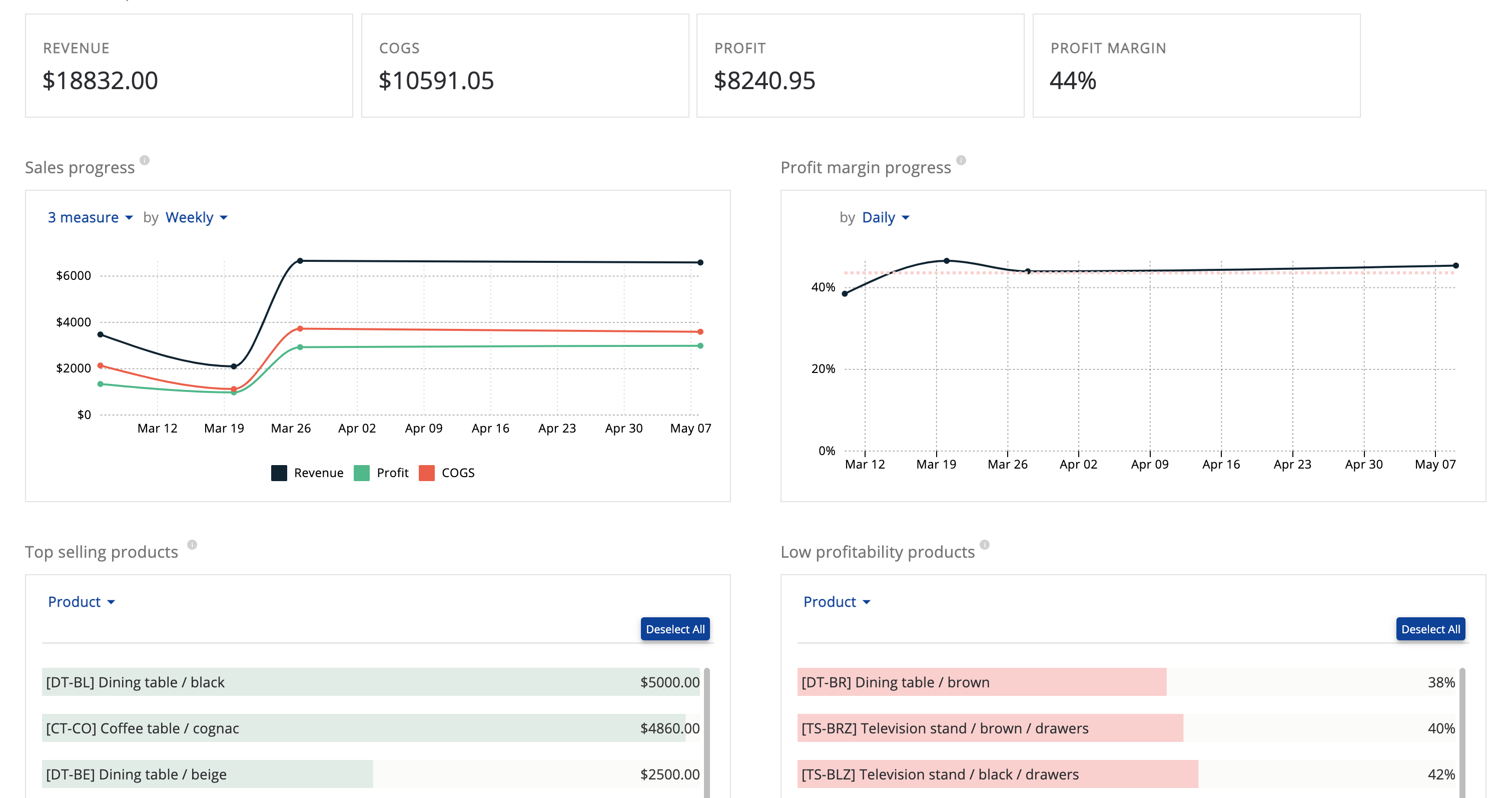
In the ever-evolving landscape of modern business, efficiently managing inventory is a make-or-break factor for success.
As the complexity of supply chains grows and customer demands become more intricate, businesses seek innovative solutions to simplify their operations. Many turn to cloud inventory software like Katana.
Katana is a live inventory and production management software designed to revolutionize how businesses handle their day-to-day operations, including COGS calculations. It does that by offering the following features:
- Real-time inventory tracking — At the heart of accurate COGS calculations lies real-time visibility into your inventory. Katana’s intuitive interface provides instant insights into your stock levels, making it easier to track changes in inventory and manage the flow of goods effectively. With real-time data, you can ensure that your COGS calculations are based on the most up-to-date information.
- Automatic COGS calculation — Katana takes the guesswork out of COGS calculations by automatically updating costs as inventory transactions occur. It provides accurate cost estimates and adjusts the average cost per unit based on your bill of materials. This ensures precise COGS even in fluctuating price environments, empowering confident decisions in pricing, inventory, and profits.
- Accurate profit margins — Katana’s precise COGS calculations contribute to accurate profit margin assessments. By incorporating all direct costs associated with producing or purchasing goods, you can make informed decisions about pricing strategies, sales targets, and operational improvements. This level of accuracy empowers you to optimize your business’ financial performance.
- Effortless integration — Integrating new software into existing workflows can be a concern for businesses. Katana addresses this by seamlessly integrating with popular e-commerce platforms, accounting software, and other tools you might already be using. This integration ensures that your COGS calculations are synchronized across all relevant platforms, reducing the risk of errors and discrepancies.
In a business environment where accuracy, efficiency, and adaptability are paramount, Katana stands out as a catalyst for simplifying COGS calculations.
By harnessing the power of automation, real-time data, and user-friendly interfaces, Katana empowers businesses to make more informed decisions while focusing on what truly matters — delivering exceptional products and services to their customers.
Book a demo and learn firsthand how it can transform your approach to calculating COGS, leading to better profitability and streamlined operations.
Cost of goods sold FAQs
How to calculate the cost of goods sold?
Calculating the cost of goods sold involves summing up the direct expenses incurred to produce or acquire the goods that a company sells during a specific period. This is done by adding the cost of opening inventory to the purchases made during the period and then subtracting the cost of the closing inventory. The resulting figure represents the COGS for that period, which is a vital component for determining a company’s gross profit.
Difference between COGS and price?
The distinction between COGS and price lies in their fundamental meanings within a business context. COGS refers to the direct costs associated with producing or purchasing the goods that a company sells. It encompasses costs such as raw materials, labor, and manufacturing expenses.
On the other hand, price is the amount that customers pay for the products. While COGS impacts a company’s profitability and gross profit margin, the price reflects what the market is willing to pay, and it includes the desired profit margin.
Is COGS considered an expense?
Yes, COGS is indeed considered an expense. It is an essential component in the determination of a company’s gross profit, which is the difference between total revenue and COGS.
COGS represents the costs directly incurred in the production or acquisition of goods that were sold during a specific period. It is subtracted from revenue to calculate the gross profit, highlighting the operational efficiency and profitability of a company’s core business activities.
Table of contents
Accounting Guide
Readers also liked
Get visibility over your sales and stock
Wave goodbye to uncertainty by using Katana Cloud Inventory for total inventory control
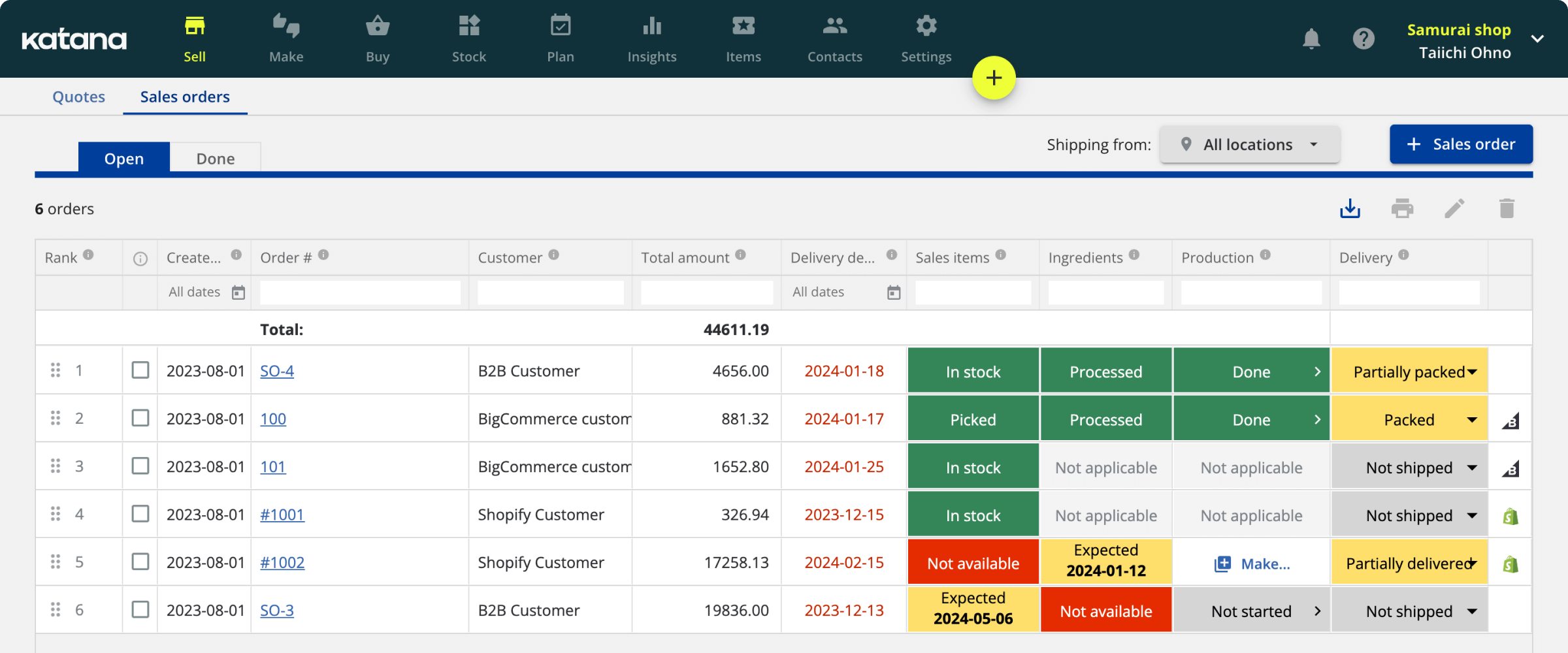