Moving average cost formula for accurate inventory valuation
Moving average cost (MAC) is an inventory valuation method that tracks the price of goods purchased. Read on to learn how it works and how to use the moving average cost formula to arrive at an accurate inventory value.
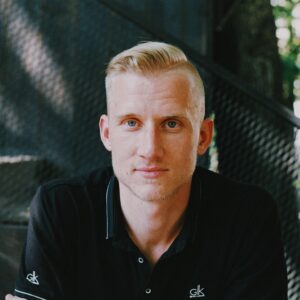
Henry Kivimaa
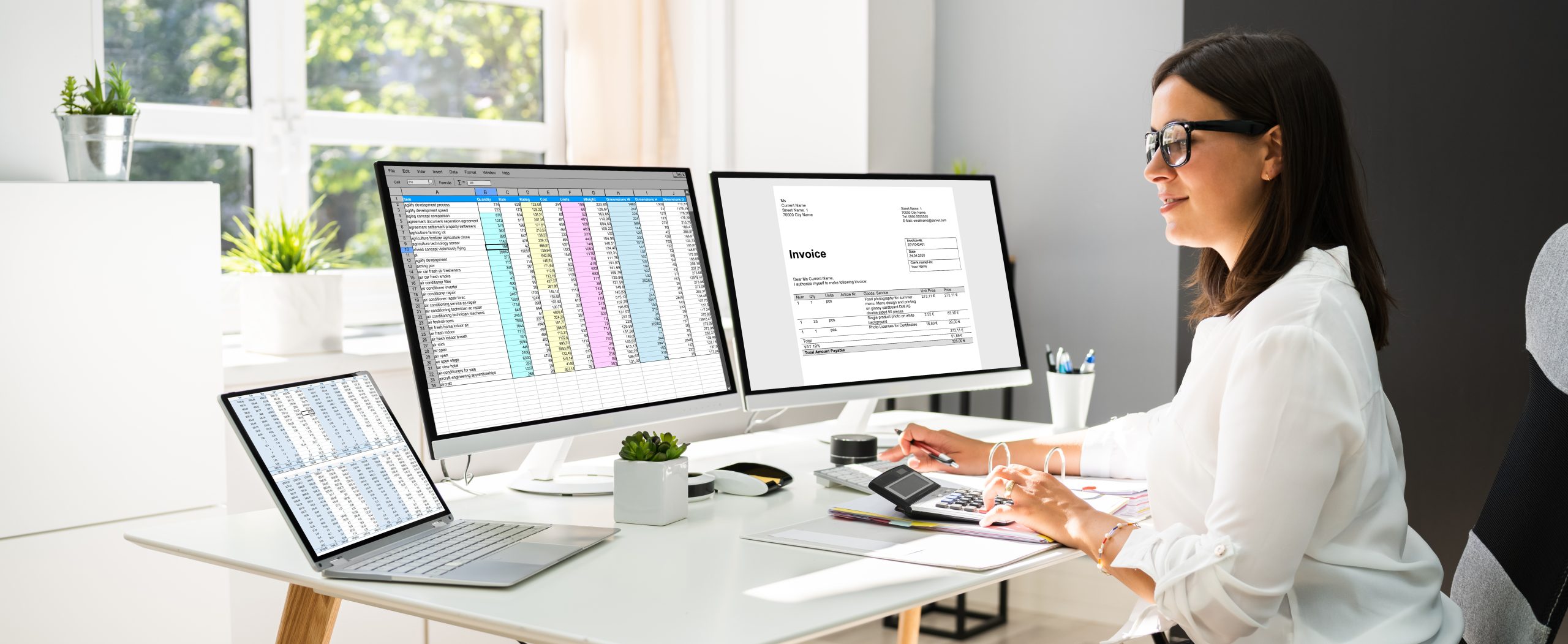
Imagine a bustling manufacturing company that relies heavily on a steady influx of raw materials to produce its goods. Each time they place an order, they find themselves facing an unexpected twist — the price of the materials has changed since their previous purchase.
This seemingly small difference poses a critical question to the company’s accountant — which price should be used to calculate the cost?
Enter the world of moving average cost (MAC), a financial technique that aims to find a balance between accurate bookkeeping and practical decision-making.
This article will look into the moving average cost method and the moving average cost formula and show you how to calculate the moving average cost.
What is moving average cost?
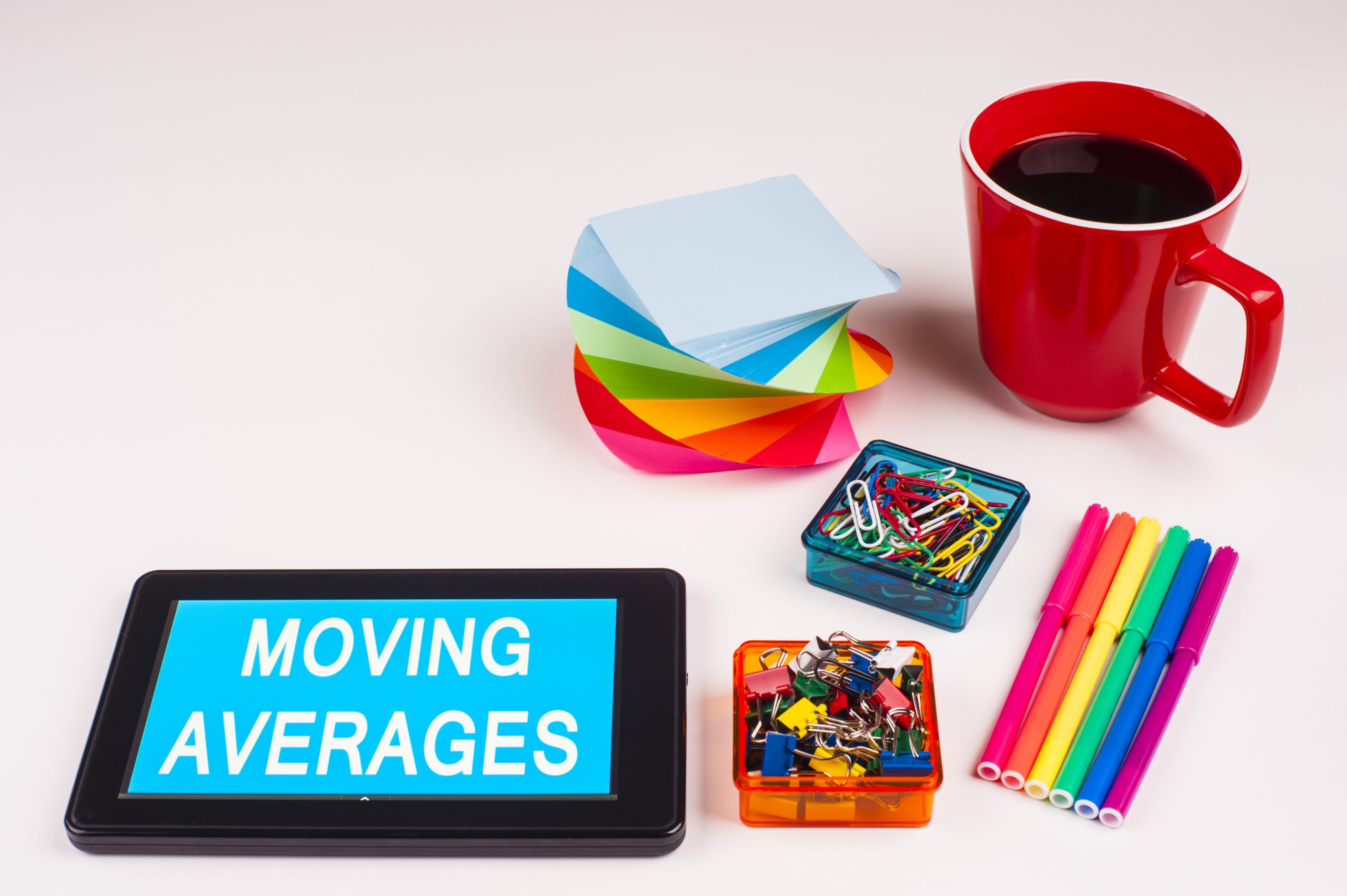
Moving average cost is a financial accounting method used to determine the cost of inventory items in situations where the price of those items fluctuates over time. It is particularly relevant for businesses regularly purchasing materials or goods at different prices.
Under the moving average cost method, the cost of inventory is calculated by taking into account the average cost of all units purchased up to a specific point in time. Instead of relying on the actual purchase price of each unit, the method assigns an average cost to each inventory unit. This average cost is recalculated each time new purchases are made, considering both the quantity and the price of the new items. As a result, the cost per unit can change with each new purchase of material, reflecting the most recent prices paid.
The moving average cost method provides a way to smooth out the impact of price fluctuations on inventory valuation. It offers a compromise between the first-in, first-out (FIFO) method, which values inventory based on the earliest purchased items, and the last-in, first-out (LIFO) method, which values inventory based on the most recent purchases.
By using MAC, businesses can mitigate the effects of price volatility and achieve a more balanced representation of their inventory value.
Why is moving average cost important?
The moving average cost method holds significant importance in financial accounting for several reasons:
- Accurate inventory valuation — MAC helps businesses maintain a more accurate representation of the value of their inventory. Considering the average cost of all units, including recent purchases, provides a more realistic cost basis for inventory valuation. This accuracy is crucial for financial reporting, decision-making, and evaluating profitability.
- Smoothing over price fluctuations — In industries where raw material prices are subject to frequent oscillations, using MAC can help smooth out the impact of these price changes. Rather than valuing inventory solely based on the most recent prices (as in LIFO) or the oldest prices (as in FIFO), MAC offers a compromise that accounts for the average cost over time. This approach reduces the volatility of inventory values, making financial statements more consistent and reliable.
- Mitigating the effects of inflation and deflation — MAC can be particularly useful in managing inventory costs during periods of inflation or deflation. Incorporating the average cost of all units helps mitigate the impact of rising or falling prices on inventory valuation. This allows businesses to track changes in the cost of goods sold and maintain a more accurate understanding of their profitability.
- Practical decision-making — The moving average cost method provides a pragmatic approach to cost calculations for businesses that face price changes. It reflects the current market conditions by considering recent purchases, enabling managers to make informed decisions regarding pricing, production, and inventory management.
Now that the benefits are clear let’s see how to calculate the moving average cost.
Download the ultimate guide to inventory management ebook
A comprehensive ebook with everything you need to know about inventory management.
MAC formula: how to calculate moving average cost
To calculate moving average cost, you’ll need to:
- Determine the previous average cost — Calculate the average cost per unit before the new purchase.
- Calculate the cost of the new purchase — Multiply the quantity of the new purchase by its corresponding unit price to determine the total cost of the new items.
- Update the quantity in inventory — Add the quantity of the new purchase to the previous quantity of units in inventory to obtain the total quantity after the purchase.
- Recalculate MAC — Use the formula to determine the new MAC per unit.
Here is the moving average cost formula:
MAC = (Previous MAC × previous quantity + new purchase cost) / total quantity
The previous MAC refers to the average cost per unit before the new purchase, previous quantity is the number of units in inventory before the new purchase, new purchase cost represents the total cost of the new purchase, and total quantity represents the sum of the previous quantity and the quantity of the new purchase.
Here’s an example:
Let’s say a company has 200 units of a product in inventory with an average cost of $8 per unit. They then purchase an additional 100 units at $10 per unit. To calculate the new MAC, we apply the formula:
MAC = ($8 × 200 units) + ($10 × 100 units) / (200 units + 100 units)
= $1,600 + $1,000 / 300 units = $8.67 per unit
Therefore, the new MAC per unit would be approximately $8.67.
By following these steps and using the formula, businesses can accurately calculate MAC, taking into account the impact of new purchases on the overall cost per unit. This enables them to maintain up-to-date and reliable inventory valuations for financial reporting and decision-making purposes.
What is the difference between weighted and moving average cost?
When it comes to inventory costing, weighted average doesn’t mean the same as it does in mathematics, so you don’t have to start assigning weight to every order.
In inventory management, weighted and moving average work the same way. The only difference is that in a perpetual inventory system, it’s referred to as MAC, and in a periodic inventory system, as weighted average costing (WAC).
Let’s look at an example to illustrate this difference. The table below shows a company’s inventory movements over a 3-month period. Let’s check the inventory valuation using both methods.
Weighted average cost example (periodic inventory)
The company bought 100 units in January, 50 in February, and 75 in March. We can also see the cost per unit and the total value of the purchase.
With weighted average, the cost is calculated at the end of the period. It divides the total inventory cost by the total number of units.
2550 / 225 = $11.33 per unit
Once we have the average cost, we can calculate the total sales.
(48 + 95 + 54) = 197 units
2550 – 197 x 11.33 = $317.99
This means that at the end of March, the company’s inventory value is $317.99.
Hopefully, that’s all clear. Now, let’s run through the same example with MAC calculation and see how the same company would value its inventory with MAC.
Moving average cost example (perpetual inventory)
In January, the company purchased 100 units for $10 each. They also sold 48 units, so we need to subtract that to work out the inventory value:
(100 – 48) x 10 = $520
Since all units were purchased at the same price, in this case, the MAC does not change.
In February, the company purchased another 50 units for $13 per unit. So, to get the new MAC, we would need to do the following calculation:
(52 x 10 + 50 x 13) / 102 = $11.47 per unit
The business also sold 95 units:
102 – 95 = 7 units
(102 -95) x 11.47 = $80.29
We can see that at the end of February, the business had 7 units in inventory with a total value of $80.29.
In March, the company purchased 75 units for $12 per unit, meaning the MAC would change again.
(11.47 x 7 + 75 x 12) / 82 = $11.95 per unit
The business sold 54 units in March, so let’s subtract that to find the final inventory value:
(82 – 54) x 11.95 = $334.6
If we now compare the WAC vs. MAC, we can see that with MAC, the remaining inventory value is $16.61 more. This is because the cheapest units were mostly sold, and now the business has the higher-cost units left. Clearly, the MAC would be lower if the last batch had been cheaper, as it reacts quicker than WAC.
Precise cost calculations with Katana
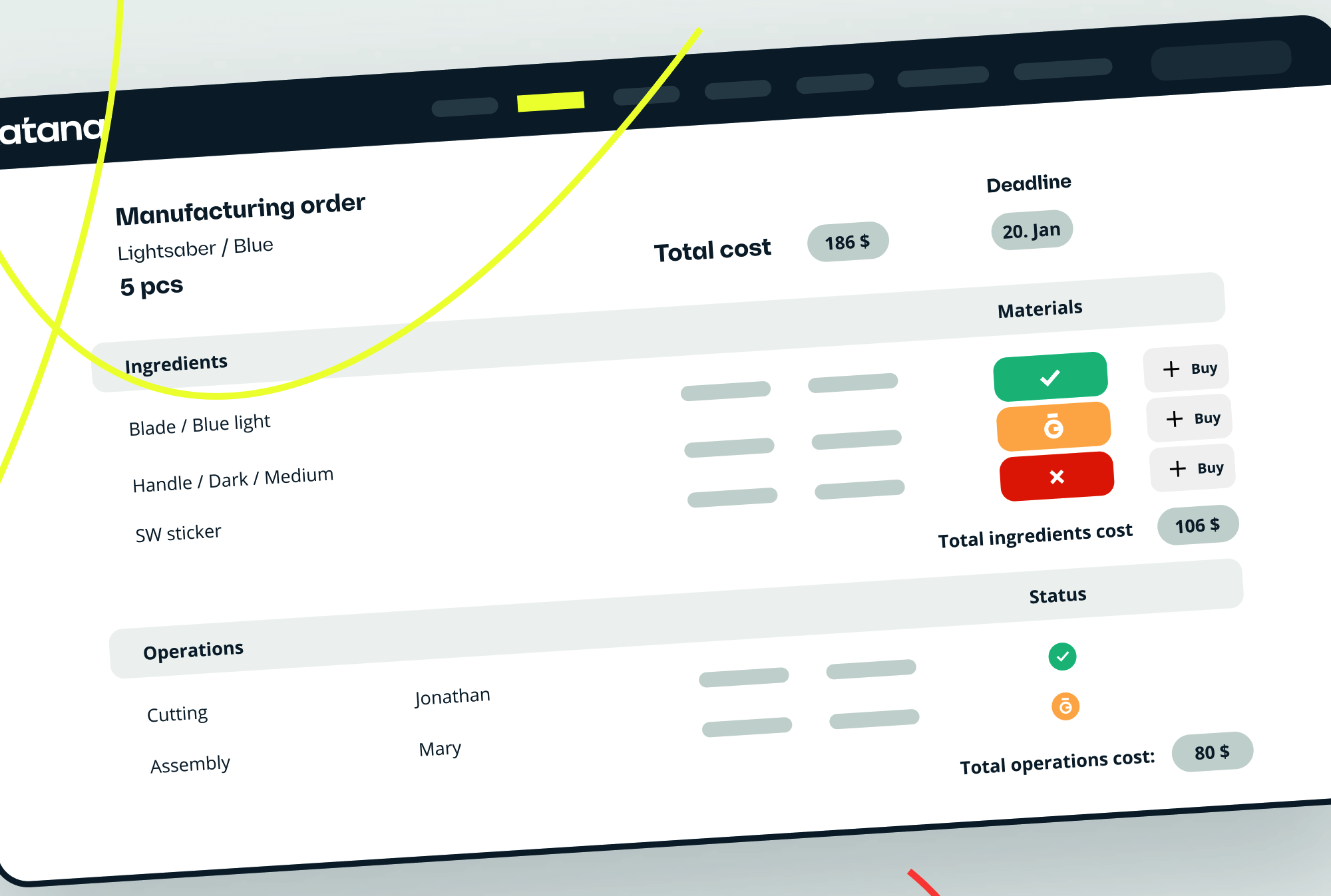
While these calculations are quite straightforward, running the numbers can get tedious, and doing it all manually can easily introduce errors. If you still wish to get the benefits of the MAC without worrying about costly mistakes, there is a better solution.
With its production management and live inventory management capabilities, Katana’s cloud inventory platform automatically recalculates your MAC whenever you procure new materials. This way, you can be sure that you have the most up-to-date price for accurate costing.
Katana also helps you manage production and inventory and unify your other business tools like QuickBooks Online and Shopify through seamless integrations.
Get started by booking a demo with Katana and get accurate inventory valuation without the headache.
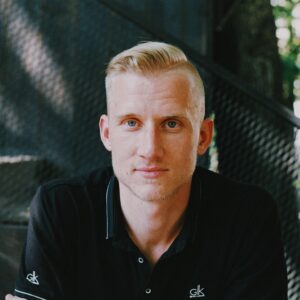
Henry Kivimaa
Table of contents
Get inventory trends, news, and tips every month
Get visibility over your sales and stock
Wave goodbye to uncertainty with Katana Cloud Inventory — AI-powered for total inventory control