Root cause analysis: The ultimate investigation guide
While mistakes and errors can be annoying and disruptive, they can also be a valuable asset. In this article, we investigate root cause analysis so you can dig up dirt on those little mishaps in your business.
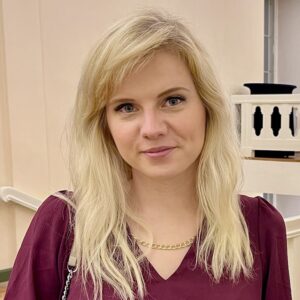
Laura Timberg
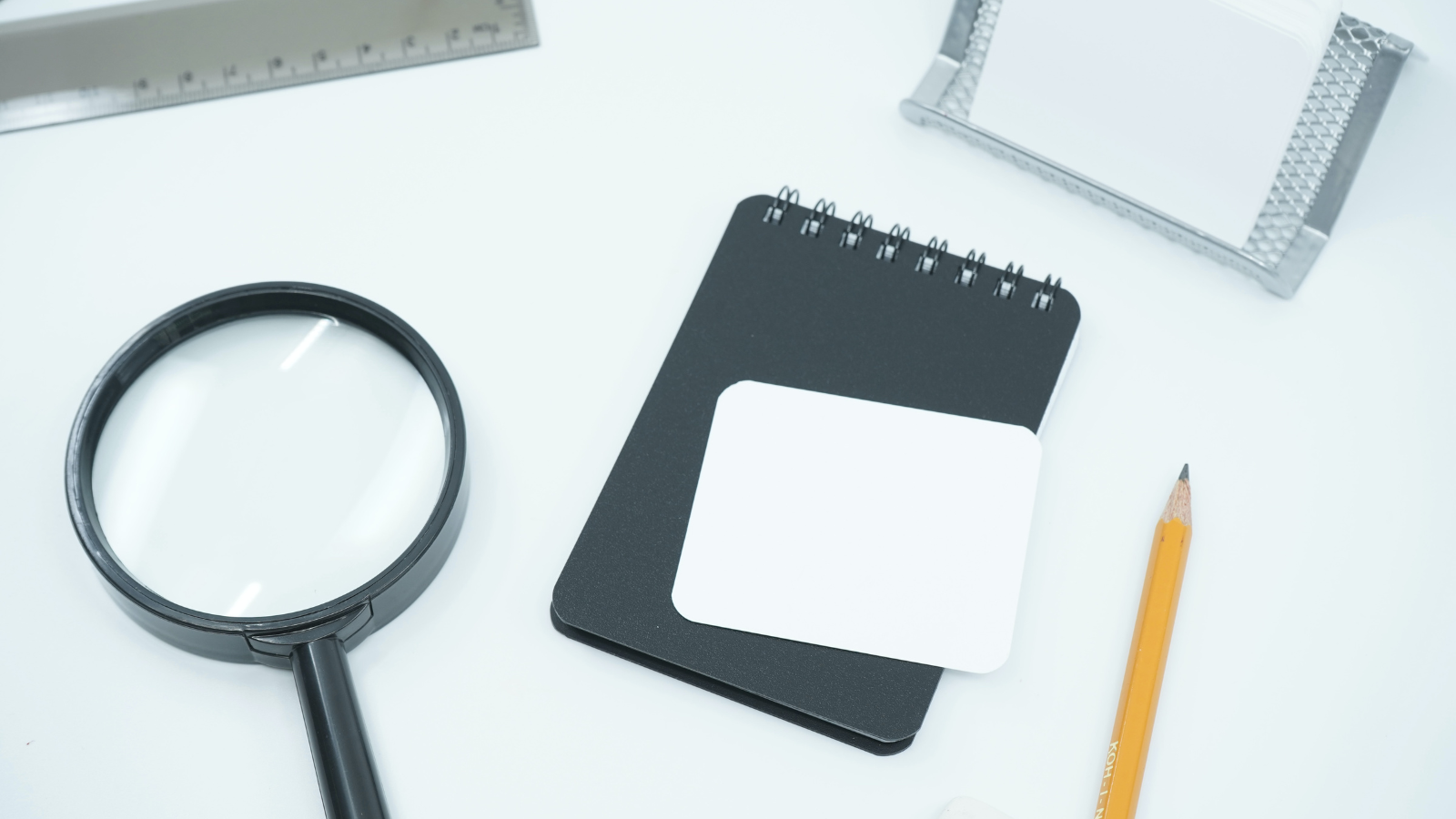
Imagine stepping into the shoes of a detective, ready to solve a thrilling mystery.
Now, picture yourself not at a crime scene but in a buzzing manufacturing facility. Like uncovering clues and solving puzzles, there’s a fascinating process called root cause analysis that helps investigators uncover the secrets behind manufacturing glitches and errors. In a factory, when something goes wrong, like a machine malfunction or a defective product, pinpointing the exact reason behind it isn’t always easy.
That’s where root cause analysis comes into play.
It’s like a magnifying glass that helps us dig deep and find the real culprit hiding beneath the surface. By examining clues and investigating step by step, we can identify the root cause of why the problem occurred in the first place. Once that is clear, it’s easier to eliminate the source of mishaps and make sure that issues like this don’t happen again.
What is root cause analysis in manufacturing?
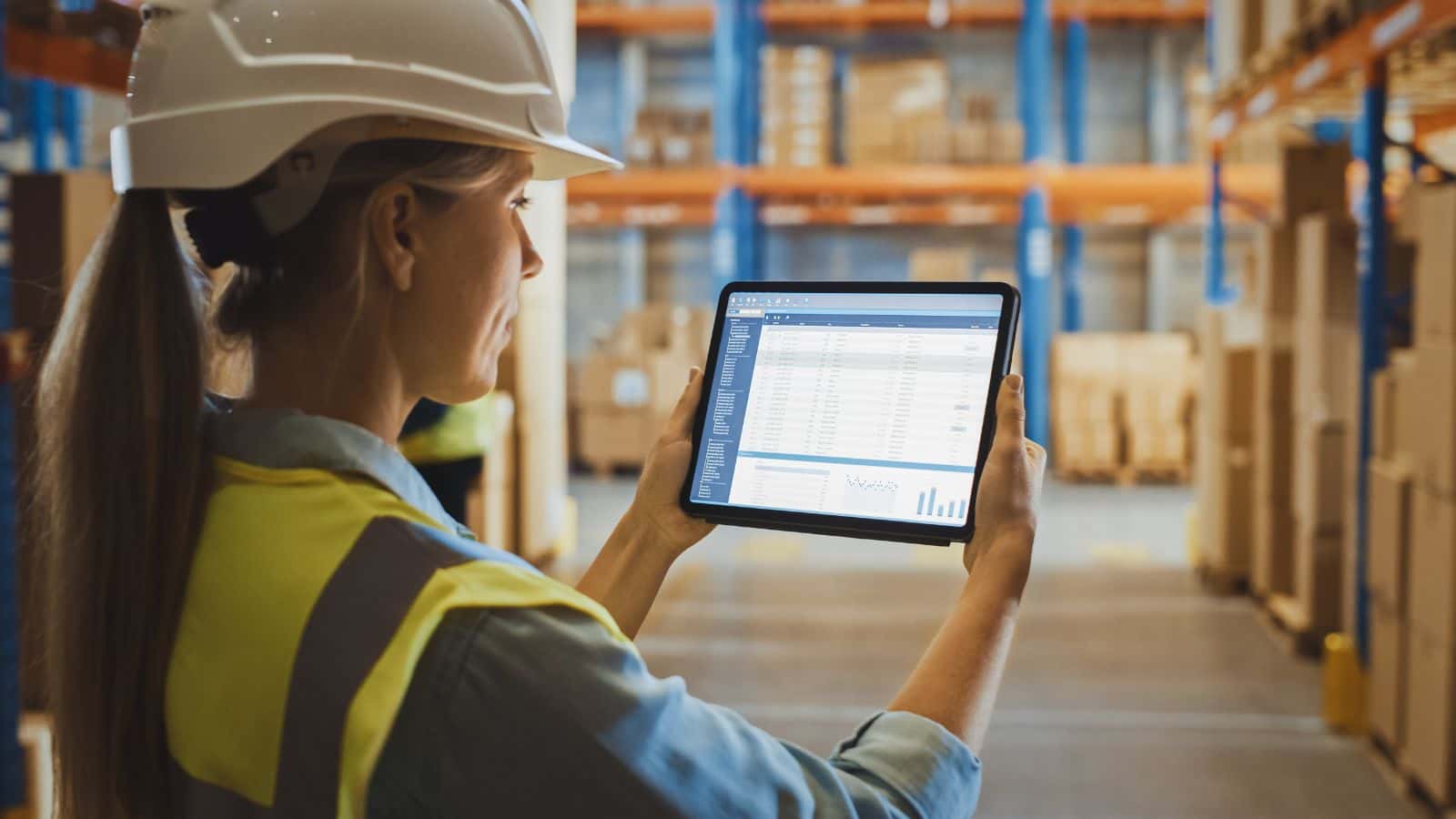
Root cause analysis is an efficient way for manufacturing businesses to figure out why things go wrong and find long-lasting solutions.
It’s like investigating a problem to discover the main reason behind it. Instead of fixing the superficial issue, this analysis helps us dive deep and address the main factor that led to the problem.
The great thing about it is being able to prevent similar problems in the future.
Once we identify the root cause, we can come up with strategies to fix it and put measures in place to prevent the problem from happening again. It’s like learning from our mistakes and making sure we don’t repeat them.
Root cause analysis is important because it helps us learn and improve.
By addressing the underlying issue, we can make manufacturing processes more efficient, prevent errors from happening, and find ways to improve continuously. Analyzing the root cause doesn’t just help fix issues but also works toward optimizing the existing processes and eliminating inefficiencies.
Download a free production quality control checklist
One aspect of root cause analysis is maintaining high quality. Grab a free production quality control checklist to keep your customers happy and standards high.
How to conduct root cause analysis?
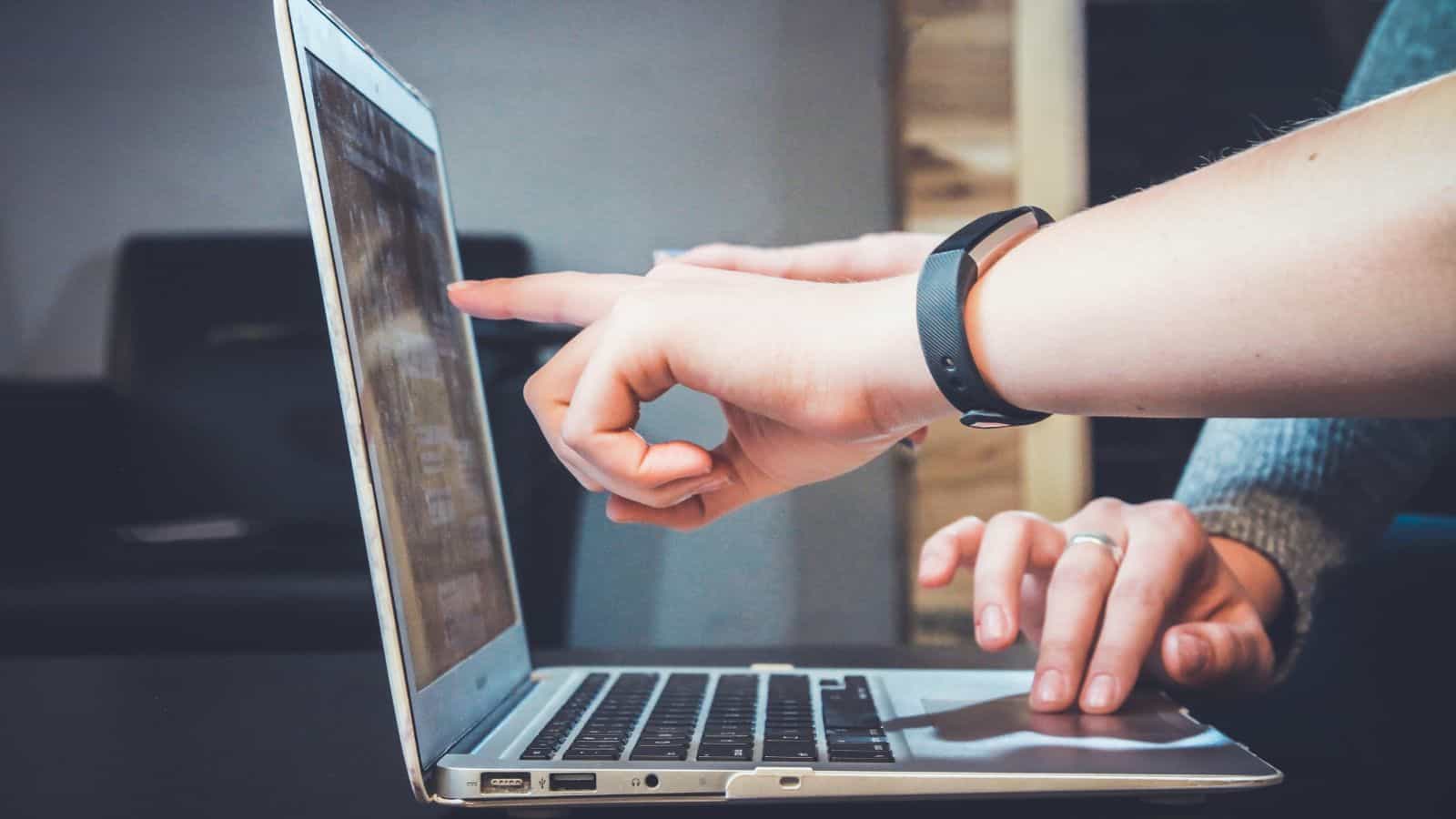
Root cause analysis focuses on finding out the main reasons behind malfunctions, defects, and inefficiencies. The best way to run these analyses is to break down potential causes into different types.
Physical causes
Physical causes refer to issues caused by tangible factors within a process or system related to physical components, equipment, materials, or environmental conditions.
Examples of physical causes include:
- Equipment malfunctions
- Material defects
- Design flaws
- External factors like temperature or humidity
Human causes
Human causes are related to the actions, behaviors, or decisions of individuals involved in a process.
These causes can be:
- Human error
- Lack of training or competence
- Negligence
- Fatigue
- Distractions
- Deviations from established procedures
- Communication breakdowns
- Poor teamwork
- Insufficient supervision
Organizational causes
Organizational causes originate from the structure, culture, or management practices within an organization. These issues are systemic and can impact multiple processes or individuals.
Examples of root organizational causes include:
- Inadequate policies or procedures
- Poor leadership
- Insufficient resources or training programs
- Inefficient communication channels
- Conflicting goals or priorities
- A culture that discourages reporting or learning from mistakes
What are the 5 steps of root cause analysis?
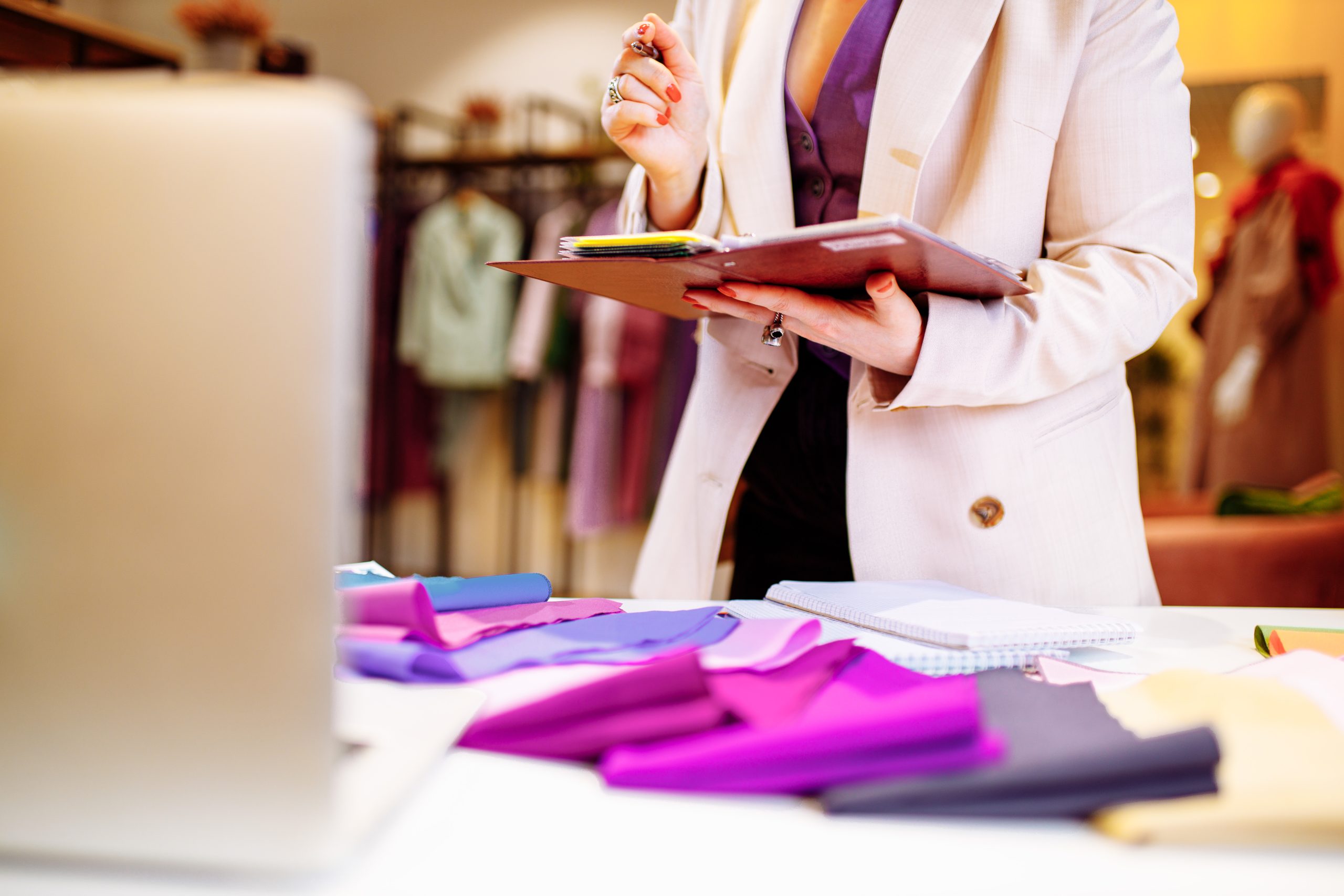
Conducting root cause analysis in manufacturing involves a systematic approach to uncovering the underlying causes of problems. While every company eventually develops its own processes, there are five common steps in root cause analysis.
1. Defining the problem
Clearly define and describe the issue that needs to be addressed.
This step involves understanding the scope of the problem, its impact, and the desired outcome of the analysis. It’s important to phrase the issue as precisely and in detail as possible, as this allows for the examination and solution to be more straightforward too.
2. Data gathering
Collect relevant data related to the problem.
This includes gathering documentation, conducting interviews, reviewing records, and observing the process or system in question. The goal is to collect accurate information that provides insights into the problem.
3. Possible cause identification
Brainstorm and identify potential causes or factors that could have contributed to the problem.
This step involves analyzing the collected data, considering different perspectives, and involving subject matter experts or stakeholders who have knowledge about the process or system under investigation. The main goal of this step is to list as many potential reasons as possible to provide maximum input for the following analysis step.
4. Data analysis
Analyze each potential cause to determine its relevance and contribution to the problem.
Evaluate the available evidence, use analytical tools or techniques, and consider any emerging patterns or correlations. This step helps narrow down the list of causes and focuses on those most likely to be the primary cause.
5. Root cause identification
Identify the root cause by determining the underlying reason behind the problem.
The goal is to go beyond the immediate causes and uncover the fundamental cause that, when addressed, will prevent the problem from recurring. This step involves analyzing the root cause and breaking down its reasons, effects, and solutions.
Root cause analysis example in manufacturing
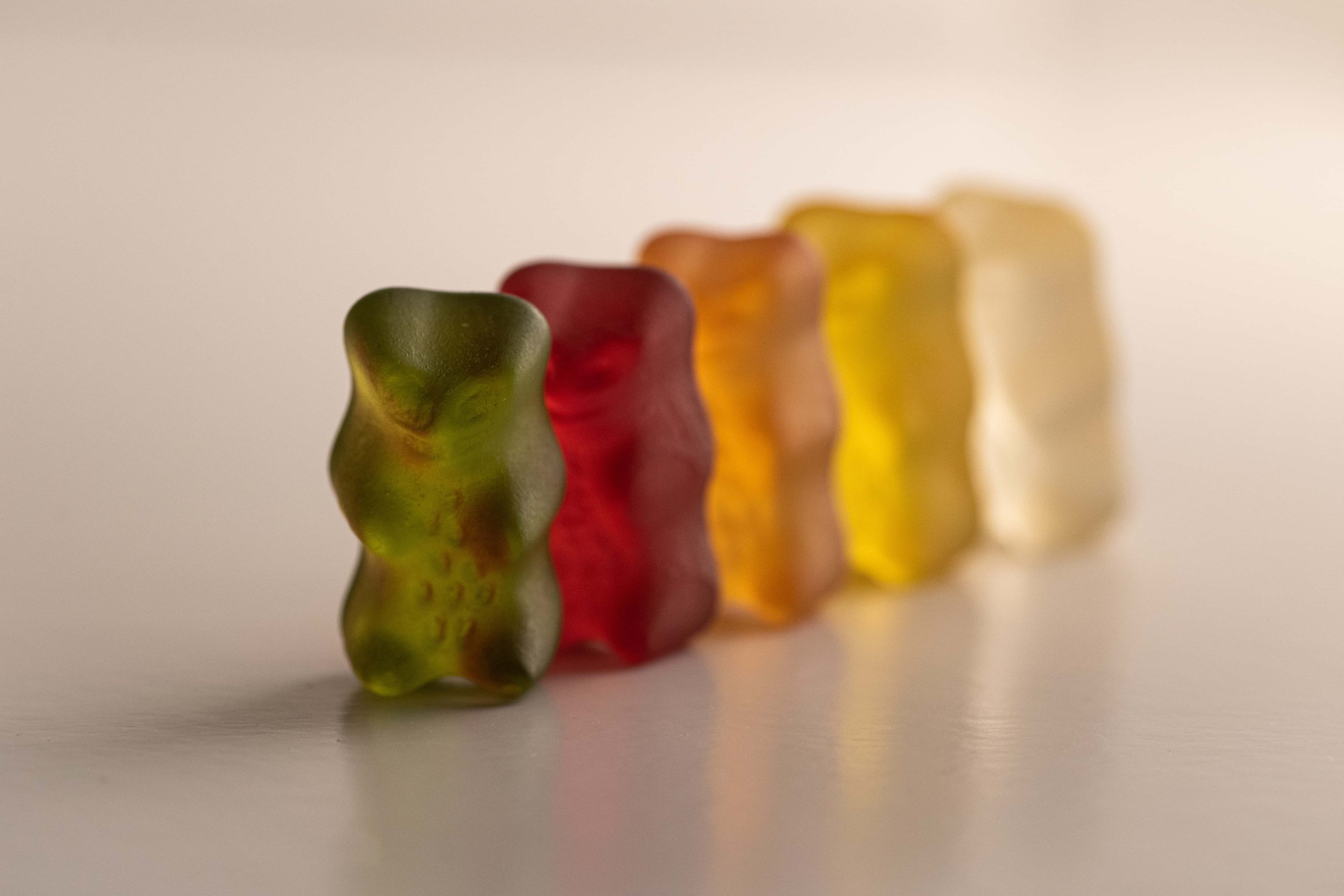
Problem: In a candy factory, the production of gummy bears is experiencing uneven coloring, resulting in some bears being a mix of two colors instead of a single color.
Step 1: Defining the problem
The problem is the irregular dye distribution among gummy bears, where some bears exhibit a blend of two colors instead of a consistent, singular color.
Step 2: Data gathering
Collect data to support your analysis.
This can be done through various investigative methods, such as:
- Observing the production process
- Reviewing manufacturing quality control records
- Interviewing operators
- Examining samples of the affected gummy bears
- Gathering information about the used colors, the mixing process, and any recent changes in the production line
Step 3: Possible cause identification
Brainstorm possible causes for the inconsistent color distribution.
Potential causes could include:
- Insufficient mixing time or uneven mixing during the manufacturing process
- Inaccurate measurement or improper ratio of color dyes during the formulation stage
- Malfunctioning equipment or machinery affecting the mixing process
- Variation in the quality or consistency of color dyes used
Step 4: Data analysis
Analyze each potential cause and gather evidence to support or eliminate them.
Conduct tests and experiments by:
- Adjusting mixing times
- Measuring color dye ratios
- Inspecting equipment
- Evaluating the quality of color dyes
- Reviewing production records
- Looking for correlations between batches with inconsistent color distribution
Step 5: Root cause identification
Based on the analysis, it is determined that the root cause of the uneven color distribution is insufficient mixing time during the manufacturing process. The gummy bear mixture is not mixed thoroughly enough, resulting in uneven dispersion of color dyes and the formation of two-colored bears.
Summary
The 5 steps of root cause analysis have led to the conclusion that the main reason for inconsistent color distribution in the gummy bears is insufficient mixing time during the manufacturing process.
There are several steps the factory should take to address and solve the issue:
- Increase the mixing duration
- Implement stricter quality control measures
- Ensure consistent application of color dyes
This helps the manufacturer achieve a more uniform and appealing appearance for their gummy bears.
Benefits of root cause analysis
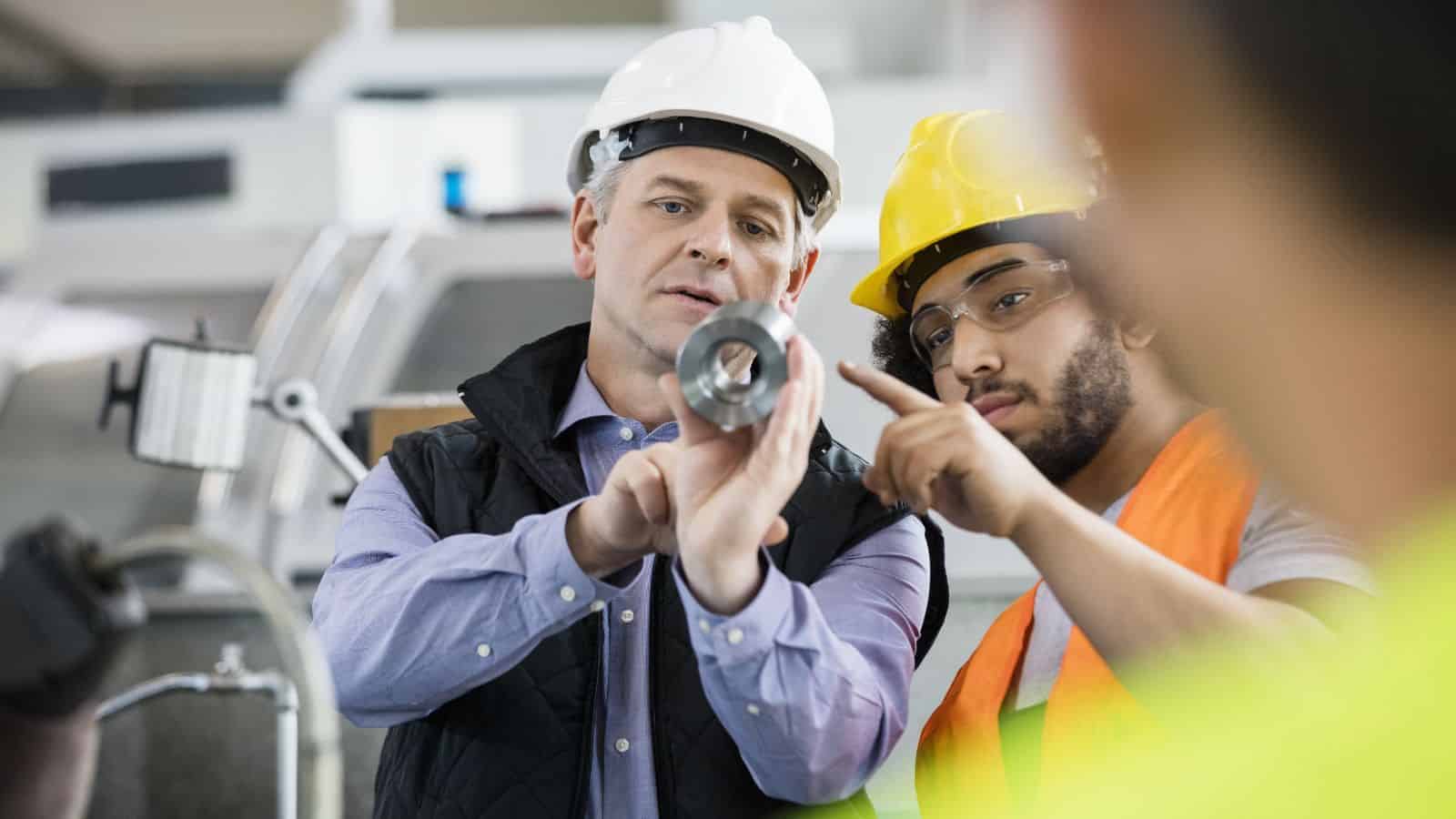
Root cause analysis offers several advantages in various aspects of problem-solving and process improvement. Here are some of the key benefits.
Problem resolution
Root cause analysis helps identify the underlying causes of problems rather than merely addressing the symptoms. By addressing the root cause, organizations can implement targeted solutions that effectively deal with the issue, leading to long-term problem resolution.
Preventive action
By identifying and addressing root causes, organizations can implement preventive measures to avoid similar problems in the future. This proactive approach helps minimize future disruptions, reduce problem-solving costs, and enhance overall efficiency and reliability.
Process improvement
Root cause analysis enables organizations to identify inefficiencies, bottlenecks, or gaps in processes. By addressing these causes, process improvements can be made to optimize workflows, enhance productivity, reduce manufacturing waste, and streamline operations.
Quality enhancement
Businesses can improve the overall quality of products or services by identifying and addressing the root causes of quality issues. This leads to higher customer satisfaction, reduced customer complaints, improved brand reputation, and increased customer loyalty.
Decision making
Root cause analysis provides valuable insights and data-driven evidence that can support informed decision-making. By understanding the underlying causes of problems, organizations can make better decisions regarding resource allocation, process changes, risk mitigation, and strategic planning.
Learning and knowledge sharing
Root cause analysis encourages a learning culture within organizations. It promotes knowledge sharing, collaboration, and cross-functional communication as team members work together to analyze problems, share insights, and implement solutions. Lessons learned can be documented and clearly communicated to improve organizational knowledge and continuous improvement.
Challenges of root cause analysis
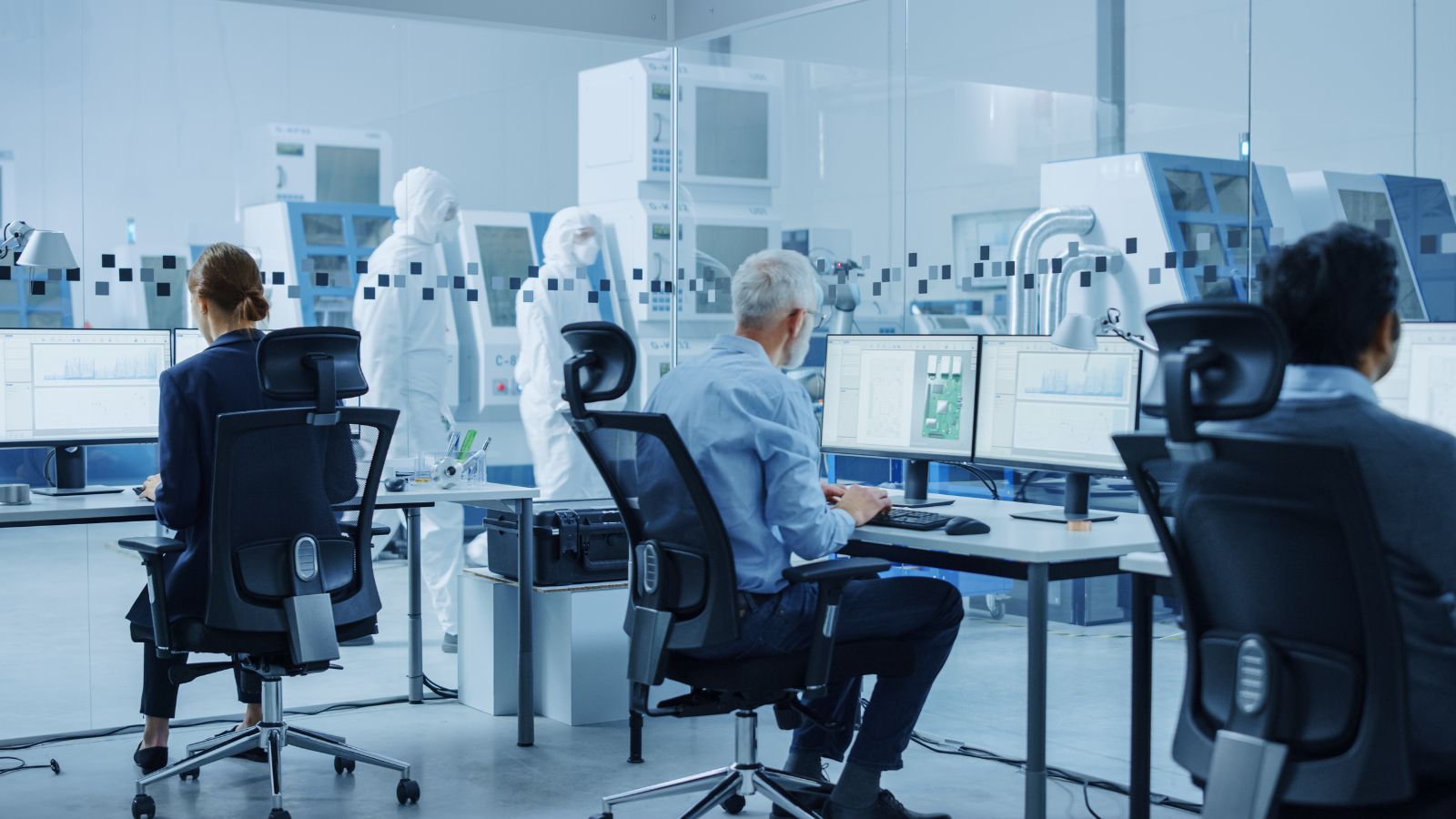
While root cause analysis is a valuable problem-solving technique, it is not without its challenges. Here are just some of the difficulties associated with it.
Complexity of systems
Many problems arise from complex systems with mutually dependent components and variables. Identifying the root cause can be challenging when multiple factors contribute to the problem. Understanding the delicate relationships and interactions within a system requires careful analysis and expertise.
Data quality
Root cause analysis heavily relies on accurate and comprehensive data. However, obtaining relevant information can be challenging, especially if proper data collection and documentation practices are not in place. Inadequate input can lead to incorrect analysis and flawed conclusions.
Subjectivity and bias
Root cause analysis often involves subjective interpretation and judgment. Different people may have varying opinions on the causes and may be influenced by biases or personal views. Encouraging a collaborative and open environment is essential to minimize the impact of bias and ensure a thorough and objective analysis.
Resources
Conducting a thorough root cause analysis requires time, resources, and effort. Organizations may face challenges regarding available resources, such as personnel, expertise, or tools, which can limit the effectiveness and precision of the analysis. Balancing the need for a comprehensive analysis with time and resource limitations can be challenging.
Human factors
Many problems have human factors as root causes, such as communication breakdowns, lack of training, or human error. Analyzing and addressing these complex human factors requires a deep understanding of individual and group behaviors, organizational culture, and human psychology.
Sustainable solutions
Implementing corrective actions to address root causes is essential for sustainable problem resolution. However, ensuring the effectiveness and sustainability of the implemented solutions can be challenging. Regular monitoring, evaluation, and implementation of the solution are necessary to prevent the recurrence of the problem.
What are 5 root cause analysis techniques?
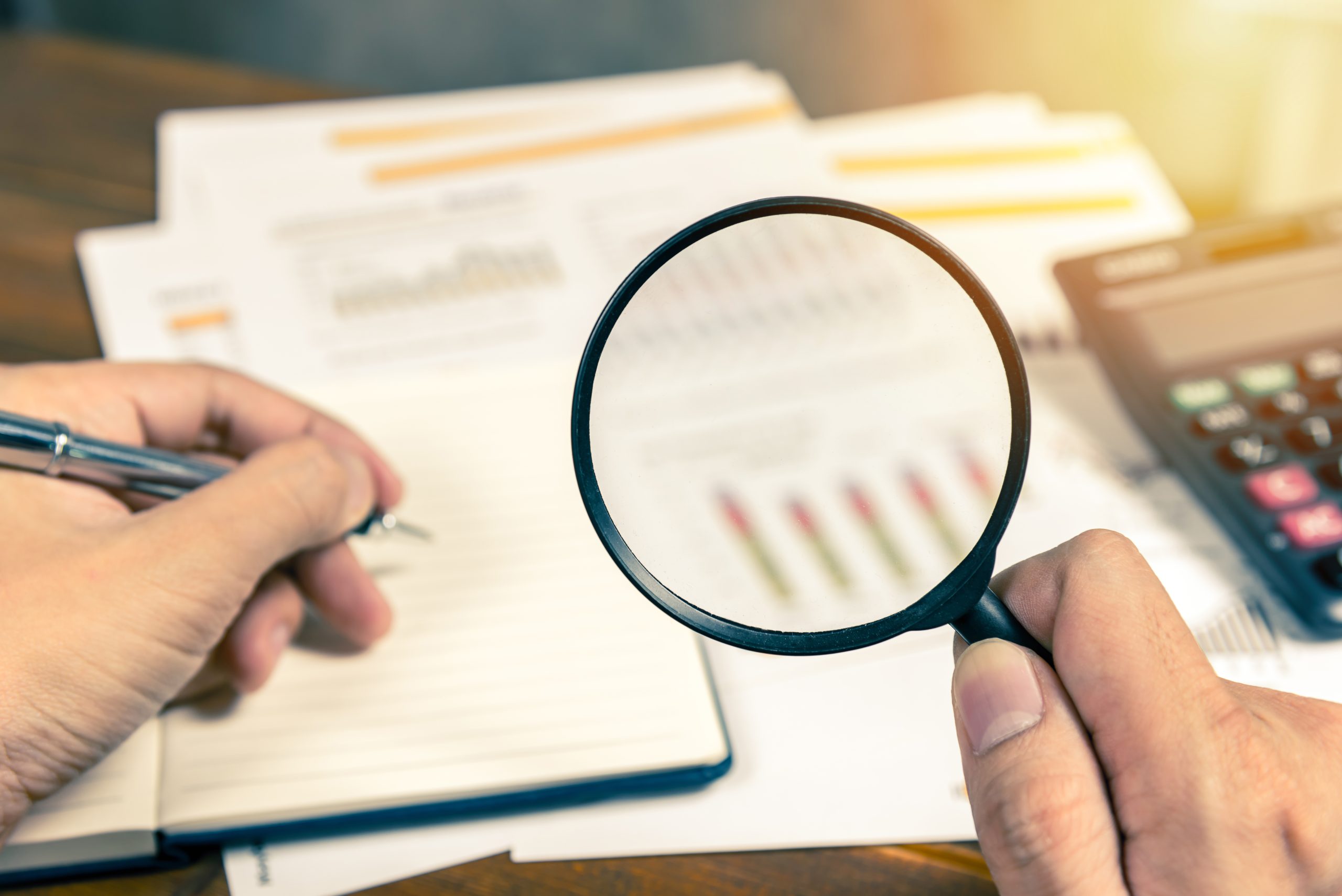
There are several root cause analysis techniques available, and here are five commonly used ones.
1. Fishbone diagram
This technique, also known as the Ishikawa diagram or cause-and-effect diagram, is used to identify and analyze the potential causes of a specific problem. It helps teams systemize the various factors that could be influencing an outcome.
Here’s how the Fishbone diagram works.
- State the problem or effect you want to analyze clearly. This becomes the main issue and the head of the fish.
- Represent the major categories of potential causes related to the problem as branches extending from the main horizontal line, resembling the spine of a fish. Common categories include people, processes, equipment, materials, environment, and management.
- Brainstorm with your team to generate potential causes within all categories. Write each cause as a sub-branch extending from major categories.
- Delve deeper into the underlying factors of each cause. Add more sub-branches to explore the root causes and contributing factors. This process helps uncover all the layers of causes and connections.
- Analyze the fishbone diagram to identify the most likely or significant causes. Look for patterns, common points, or areas with the most contributing factors. This analysis helps prioritize tasks for further investigation or corrective action.
The Fishbone diagram promotes a comprehensive and visual approach to problem-solving.
It encourages team collaboration, knowledge sharing, and a deeper understanding of the complex relationships between causes and effects. By visually mapping out the potential causes, teams can identify focal points, find areas for improvement, and make more data-driven decisions.
The Fishbone diagram is widely used in various industries, such as:
- Manufacturing
- Health and beauty products
- Quality management
- Process improvement
It provides a structured framework for problem analysis, allowing teams to address the root causes and make informed decisions for long-term solutions.
2. The 5 whys analysis
The 5 whys analysis is a common and simple technique where teams repeatedly ask “why?” to uncover the root causes of a problem. The goal is to identify the underlying causes behind each answer, gradually diving into the fundamental cause. Here’s how the 5 whys analysis works.
- Identify the problem or effect you want to analyze. Ask, “Why did this problem occur?” and write down the answer.
- Investigate the cause by taking the first answer and asking, “Why did that happen?” and writing down the answer.
- Ask “why?” for each response, repeatedly probing deeper into the causes. Each “why?” should be based on the previous answer until you reach a point where the answer is no longer meaningful or further questioning is not possible.
- Continue until you reach the root cause. This may take less or more than five iterations, depending on the complexity of the problem.
The 5 whys analysis helps avoid assumptions and uncovers the primary cause of a problem. It encourages critical thinking and prevents surface-level solutions that only address symptoms. By asking “why?” multiple times, you peel away the layers of causes and get closer to the root issue.
It’s important to note that the 5 whys analysis is not a rigid rule, and the number of times you ask can vary depending on the situation.
Sometimes the root cause is reached faster, while other times it may require diving deeper. The key is to keep the questions focused on the cause of the problem rather than steering off into unrelated topics. Involving a diverse team with different perspectives will ensure a broader brainstorming of possible causes.
3. Fault tree analysis
The fault tree analysis (FTA) technique is used to identify all the potential routes of a specific event or problem. It helps analyze how unfortunate events and failures can lead to mistakes or overall inefficiency.
Here’s how FTA works.
- Start with the undesired event or problem you want to analyze. It is called the top event. For example, this could be a product failure or a safety incident
- Identify the contributing factors or events that could lead to the top event. These are called basic events. For example, in the case of a product failure, the basic events could be a component malfunction, a design flaw, or an inefficient process
- Create a graphical representation of the fault tree by connecting the basic events to the top event using symbols called logical gates. The logical gates represent the relationships between events. Standard gates used in FTA include “AND” gates, “OR” gates, and “NOT” gates
- The “AND” gate — All the events connected to it must occur for the top event to happen. It represents a combination of factors leading to the undesired outcome
- The “OR” gate — Any one of the events connected to it can cause the top event. It represents alternative factors that separately can lead to the undesired outcome
- The “NOT” gate — Marks the absence of an event or condition. It expresses negation or failure to meet a specific requirement
- Continue adding more events and gates to the fault tree, breaking the contributing factors down into smaller, more specific events. Keep asking, “What could cause this event?” until you reach the most basic causes
- Analyze the fault tree to understand the combinations of events that could result in the top event. Identify critical paths or events most likely to lead to the undesired outcome
Similarly to the 5 whys analysis, the FTA includes very elaborate deep diving and asking the same question multiple times until you find the bottom line of the issue.
This technique helps to understand relationships between events and factors, providing a structured approach to identify and prioritize potential causes. It helps teams focus on the combinations of events that can lead to the undesired outcome, allowing you to move forward with risk assessment and preventive actions.
FTA gives businesses insights into the key contributing factors and helps them develop ways to prevent these issues from rising in the future.
4. Failure mode and effects analysis
Failure Mode and Effects Analysis (FMEA) helps identify issues and assess their impact. It helps to pinpoint and prioritize potential failures and their consequences to prevent or minimize their occurrence.
Here’s how the FMEA process usually goes.
- List all the potential ways in which a product or process can fail. This is called a failure mode
- Consider the severity of each failure mode and its effects, such as safety risks, customer dissatisfaction, or production delays
- Evaluate the potential causes of each failure mode and determine how easily it can be detected before it affects the customer or the overall process. This helps identify the underlying reasons for failures and catch them in a timely manner
- Determine the Risk Priority Number (RPN) for every failure mode. It provides a numerical value that helps prioritize actions based on the level of risk associated with each failure mode
Risk Priority Number = Severity x Occurrence x Detectability
- Severity — The severity of the failure mode is rated on a scale from 1 to 10, where a high severity rating indicates severe risk.
- Occurrence — The potential of failure occurrence is rated on a scale from 1 to 10. The higher the number, the higher the failure occurrence potential.
- Detection — The failure detection capability is rated on a scale from 1 to 10. A high detection rating reflects low detection capability.
A high RPN means an increased risk of failure and requires attention before issues arise.
- Prioritize the failure modes that require immediate attention, based on the calculated RPN. Develop action plans to mitigate or eliminate the high-risk failure modes. These actions may include process improvements, design changes, additional inspections, or enhanced training.
Systematic FMEA allows companies to anticipate and address potential failures before they occur. It helps improve product quality, reduce risks, enhance customer satisfaction, and optimize processes. FMEA is commonly used to enhance product and process design and ensure better outcomes in industries such as:
- Manufacturing
- Automotive
- Aerospace
- Healthcare
5. Pareto analysis
Also known as the 80/20 rule, Pareto analysis finds the most significant causes or factors contributing to a problem or outcome. It is based on the theory that a small number of causes often account for most of the effects.
Here’s how Pareto analysis works:
- Gather data on various causes or factors related to the problem you are analyzing. For example, this could include customer complaints, product defects, or process errors
- Group the data into categories or types of causes. For example, if you’re analyzing customer complaints, you might categorize them by the kind of issue, such as product quality, customer service, or delivery time
- Determine the frequency or impact of every cause within each category. This could be done by counting the number of occurrences, measuring the time or cost associated with each cause, or using other relevant metrics
- Outline the causes on a Pareto chart, with categories marked on the X-axis and the frequency or impact on the Y-axis. Arrange the causes in descending order, from the most frequent or impactful to the least
- Identify the point on the chart where the cumulative frequency or impact reaches 80%. This is often referred to as the vital few causes. These are considered the most significant contributors to the problem
- Allocate resources and take targeted actions to address the most significant factors and achieve the greatest impact, by prioritizing the vital few causes.
Pareto analysis helps direct attention and resources to the factors that will show the most substantial improvements.
It enables organizations to identify and address the few key causes that have the most influence on the problem rather than attempting to address every possible cause equally. Pareto analysis helps make more informed decisions, allocate resources effectively, and improve overall equipment efficiency. It is a valuable tool in many business areas, including:
- Quality management
- Process improvement
- Problem-solving
How to conduct root cause analysis with software?
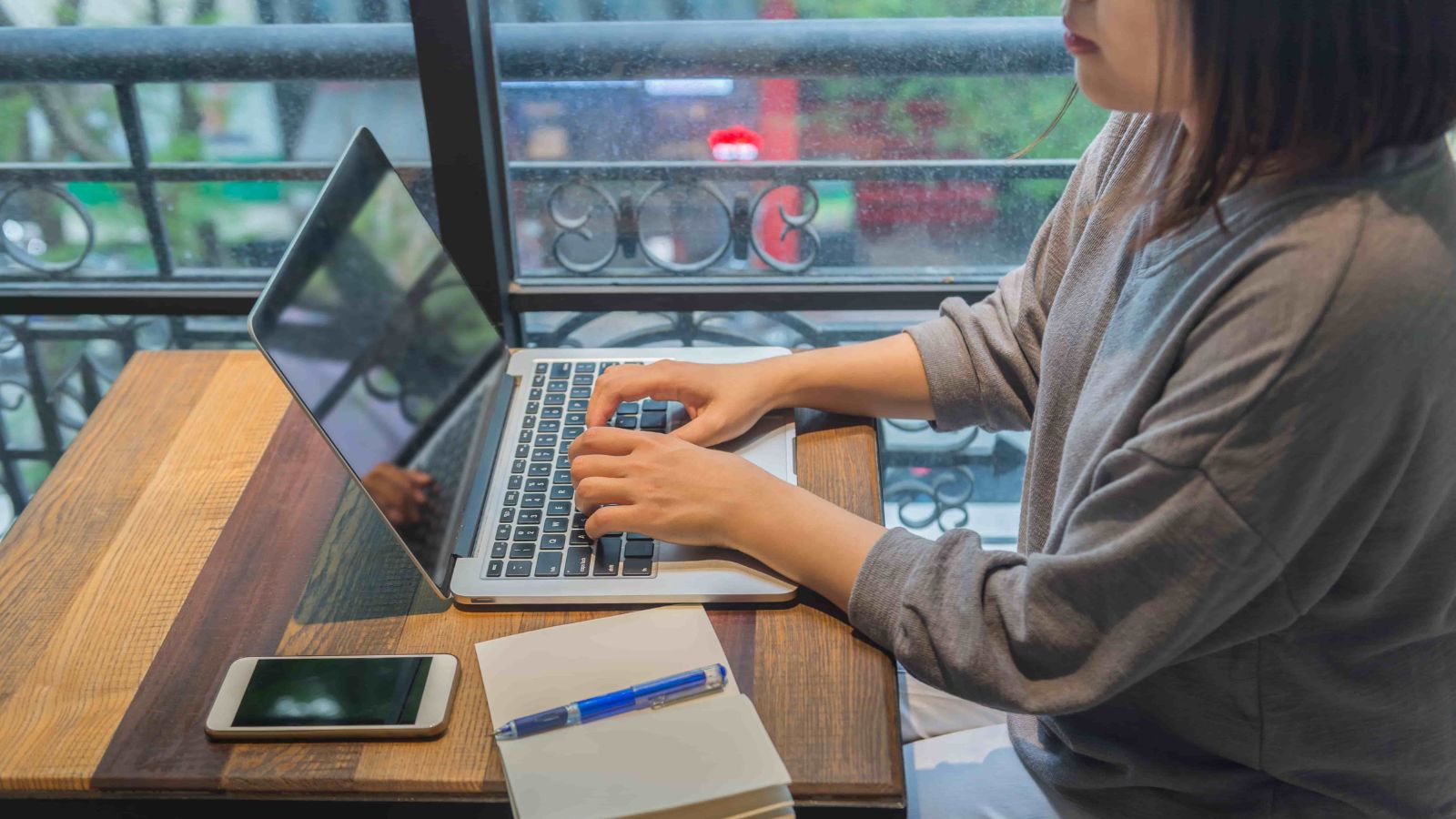
There’s plenty of software out there to optimize and streamline root cause analysis for you. One option is Katana Cloud Inventory Platform, explicitly designed as an all-in-one solution to meet all your manufacturing needs.
Here’s how you can use Katana for effective root cause analysis.
Data collection and analysis
Begin by collecting relevant data using Katana’s insights.
This includes information on production, orders, sales, and customers. Using Katana’s data for manufacturing analytics can help you eliminate inefficiencies and identify patterns or anomalies that could be potential root causes.
Production planning
Use Katana for production scheduling and to reprioritize manufacturing based on demand planning.
This helps identify critical steps, potential bottlenecks, and areas where issues are likely to occur. Understanding the process flow lets you focus your root cause analysis efforts on specific stages or components.
Inventory management
Katana’s inventory management system helps keep track of raw materials and finished goods in real time. Optimize inventory operations with barcode scanning and assign serial numbers to items to minimize the risk of human error.
This is a valuable feature for root cause analysis because it helps identify any inventory-related issues that may impact production or cause delays. By managing inventory in Katana, manufacturers can pinpoint issues, such as shortages or stock discrepancies, set reorder points to avoid stockouts, and take other measures to ensure smoother operations.
Multilocation operations
Katana gives you complete shop floor control, enabling cross-functional teams to work together in conducting root cause analysis.
Team members can view and complete their tasks in the Shop Floor App, a collaborative environment for sharing assignments across functions and warehouses. This promotes open cooperation, encourages discussions, and ensures everyone is aligned with mutual goals.
And there you have it — the all-encompassing guide on how to solve manufacturing mysteries and investigate inventory issues. You, too, can be a detective, but without the peculiar headwear and constant reliance on a magnifying glass. Fight away inefficiencies like Sherlock tracks down perpetrators and elevate your manufacturing to new heights.
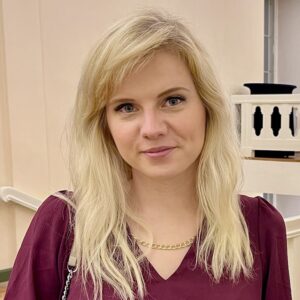
Laura Timberg
Table of contents
Get inventory trends, news, and tips every month
Get visibility over your sales and stock
Wave goodbye to uncertainty by using Katana Cloud Inventory for total inventory control
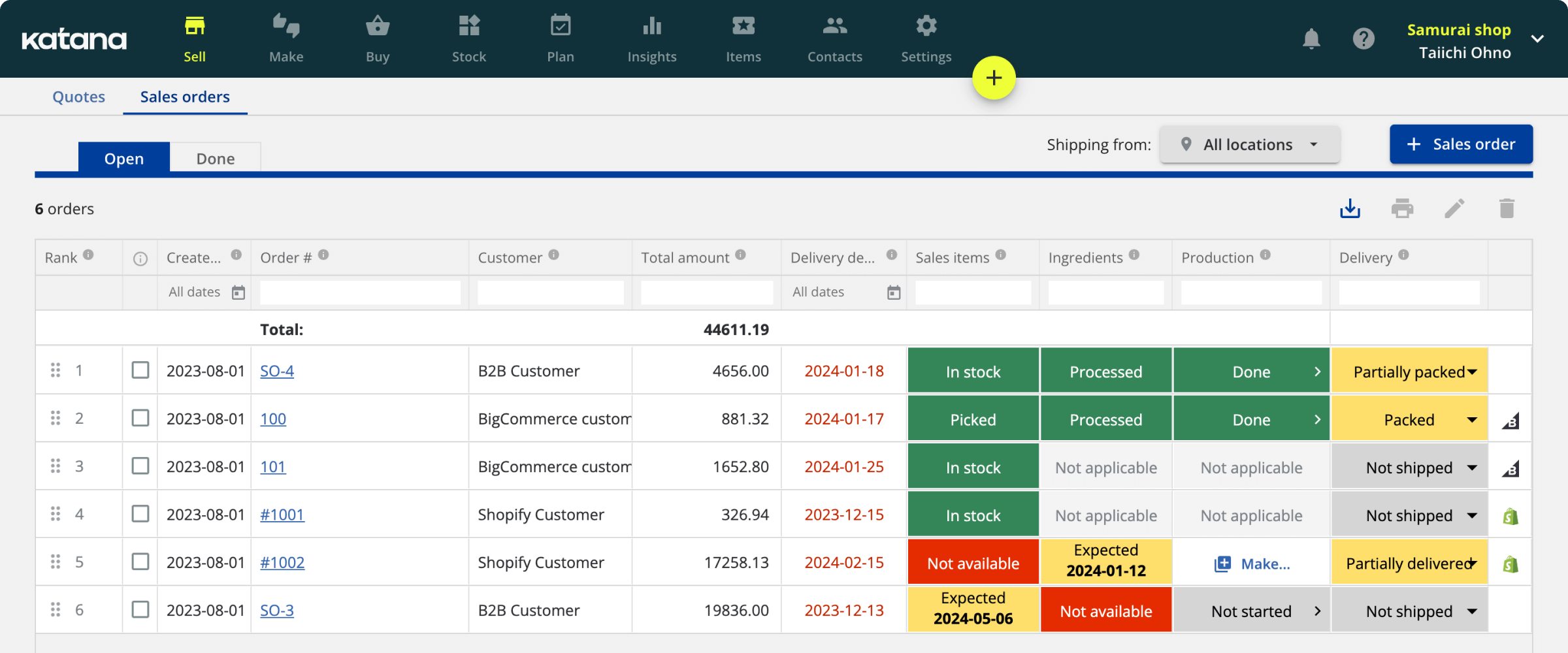