Total productive maintenance: Tips to boost efficiency
Ready to amp up your productivity? This article will guide you in implementing total productive maintenance (TPM), helping you to minimize downtime, maximize output, and exceed your performance goals.
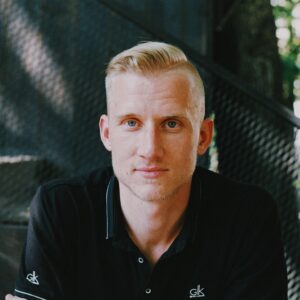
Henry Kivimaa
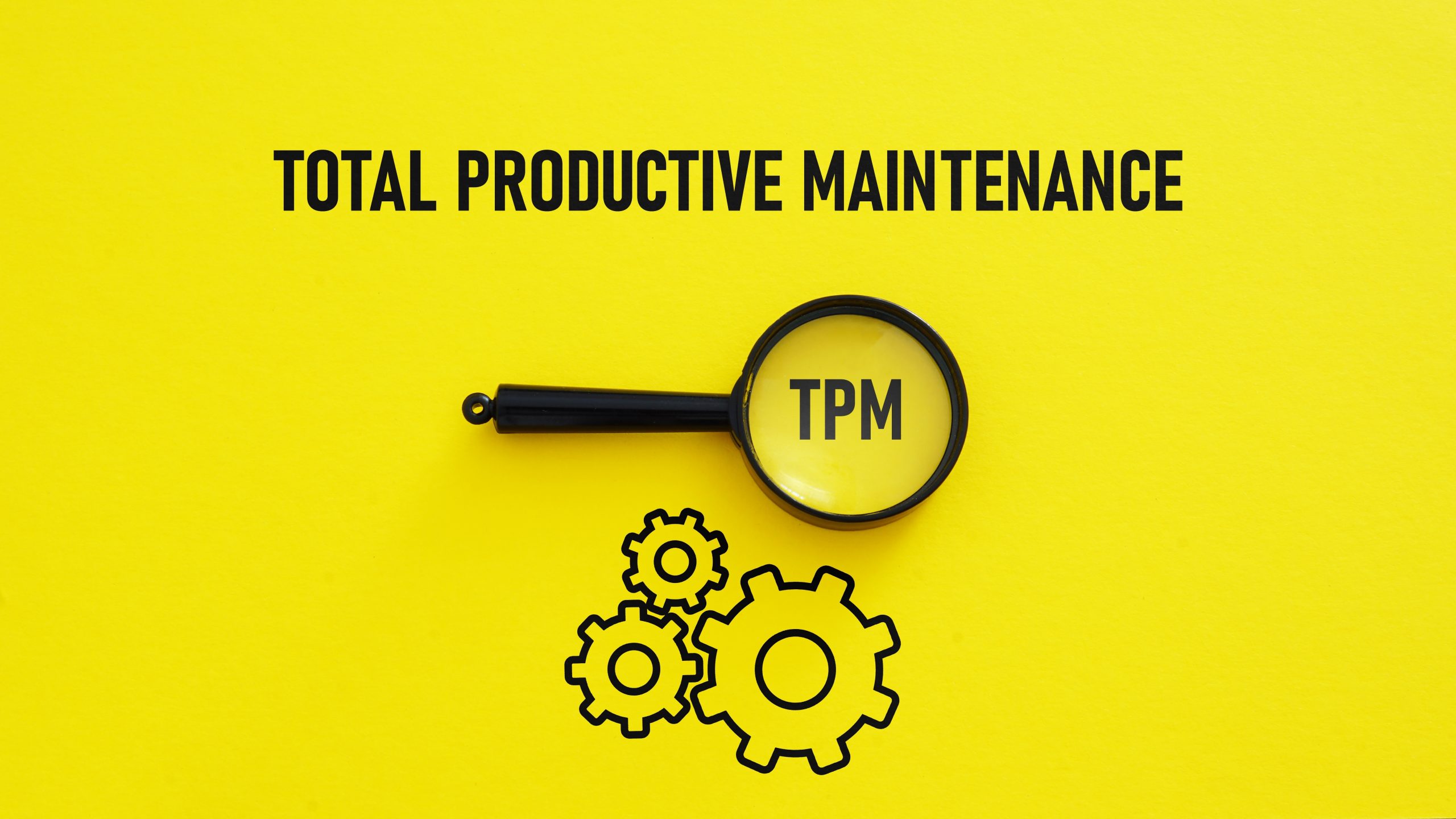
Whenever we write about a system that was developed to improve manufacturing efficiency, we have to start with Japan and often with Toyota. This was the case when we talked about:
And this time is no different. Somewhere between 1950 and 1970, a man named Seiichi Nakajima developed a method we now know as total productive maintenance or TPM.
It’s probably no surprise that the first company to ever benefit from this method was none other than — drumroll — Nippondenso. Well, this name may not actually tell you much — it didn’t tell me much before I started researching the history surrounding TPM. However, as it turns out, Nippondenso builds automotive parts for Toyota.
Now that we have once again established Japan, and more precisely, Toyota as the manufacturer constantly on the cutting edge of innovation, let’s get to the topic at hand and see what this total productive maintenance really is about.
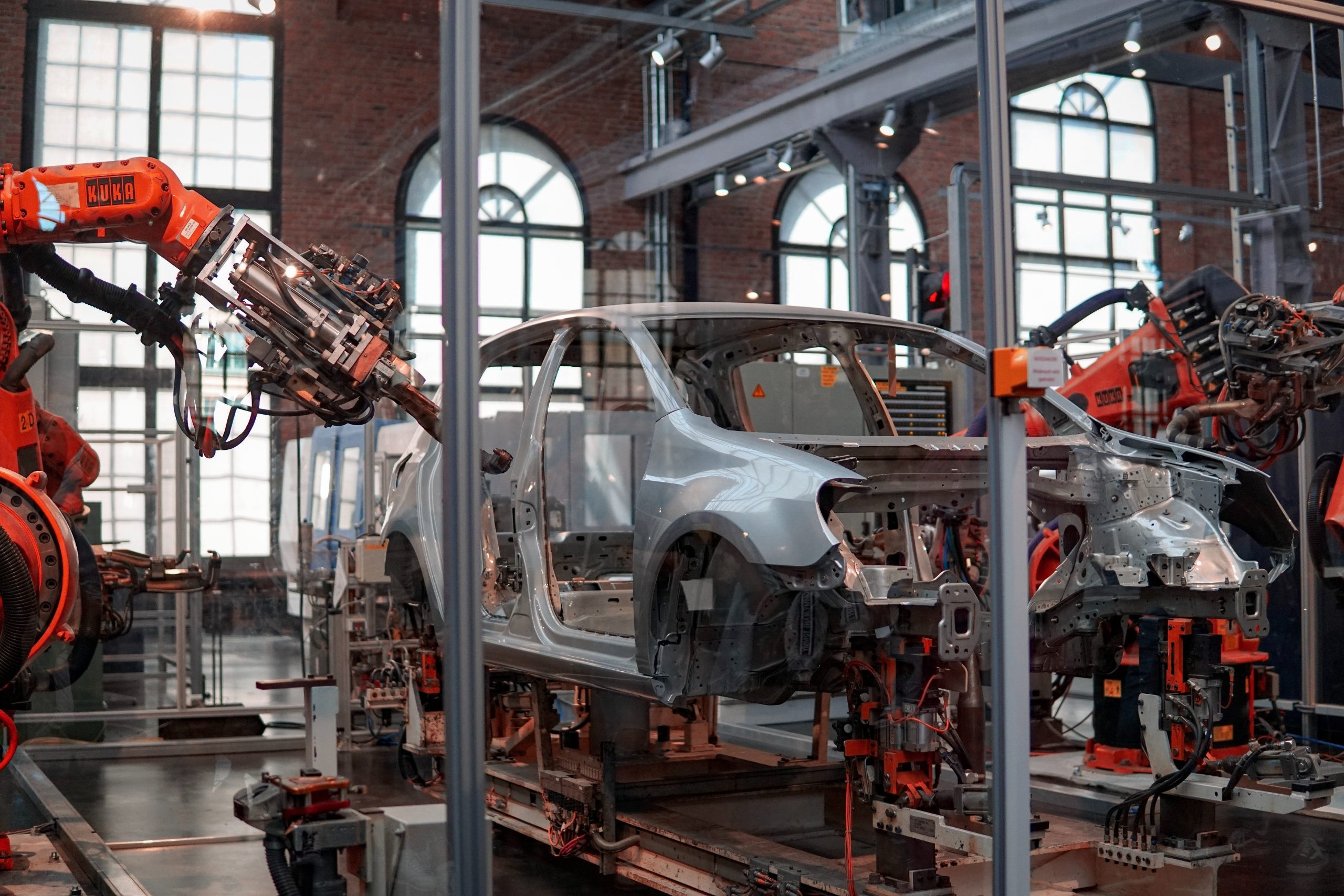
What is TPM?
Total productive maintenance is a systematic way of managing machines and equipment to improve their performance and lifespan. It focuses on preventing breakdowns and maximizing the efficiency of the equipment we use.
Think of TPM as taking care of a car. Regular oil changes, tire rotations, and inspections keep the vehicle running and help prevent any major problems. TPM does something similar for machines and equipment in factories.
In TPM, everyone who works with the machines gets involved in their upkeep.
It’s not just the maintenance crew’s responsibility but a team effort. Operators and managers learn how to perform routine maintenance tasks and keep an eye out for potential issues. By catching small problems early on and fixing them, you can avoid costly repairs and keep the machines running at their best.
TPM is all about being proactive.
Instead of waiting for something to break down, it’s best to take steps to prevent it from happening. This saves time and money while helping businesses run more smoothly. Giving the machines regular check-ups helps keep them in top shape and ensures you can keep up with the production demand.
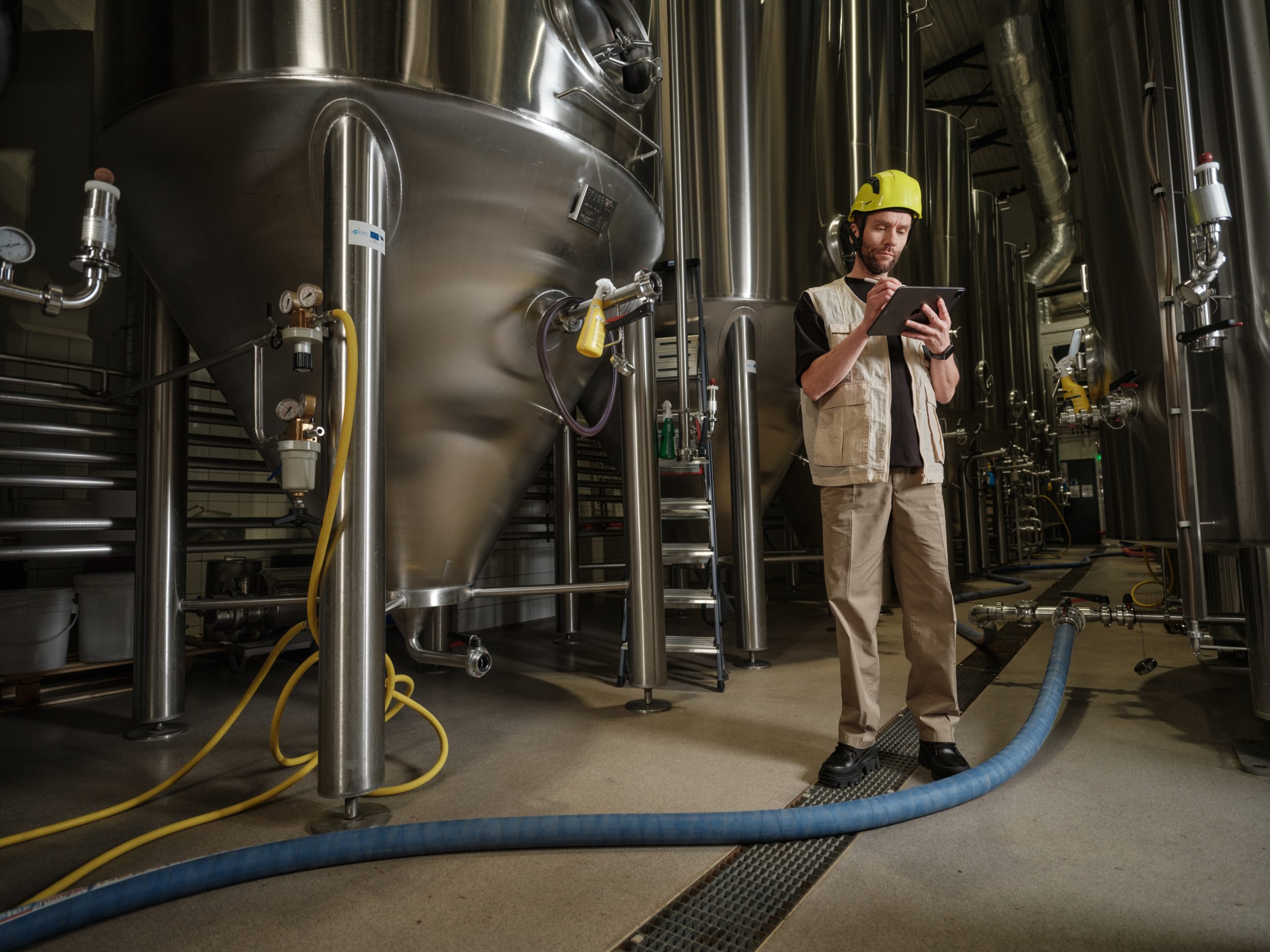
What are the benefits of TPM?
TPM provides a holistic approach to maintenance and operations management, offering many benefits to organizations that implement and embrace its principles. Below, you’ll find some of the key benefits of TPM.
Increased equipment reliability
TPM focuses on proactive maintenance and equipment care which improves equipment reliability. Addressing potential issues and performing regular maintenance activities helps organizations reduce breakdowns, unplanned downtime, and disruptions in production.
Better equipment availability
TPM makes sure your equipment is available for production by minimizing breakdowns and reducing setup times. This leads to increased effectiveness and allows companies to consistently meet production targets.
Higher product quality
Since TPM focuses on quality maintenance, it ensures your equipment is in optimal condition to produce high-quality products. Preventing defects and errors helps to improve product quality and, in turn, customer satisfaction.
Improved overall equipment effectiveness (OEE)
OEE is a metric that measures the utilization and performance of equipment. Through different TPM methods, organizations can enhance OEE by reducing downtime, improving cycle times, and optimizing equipment efficiency.
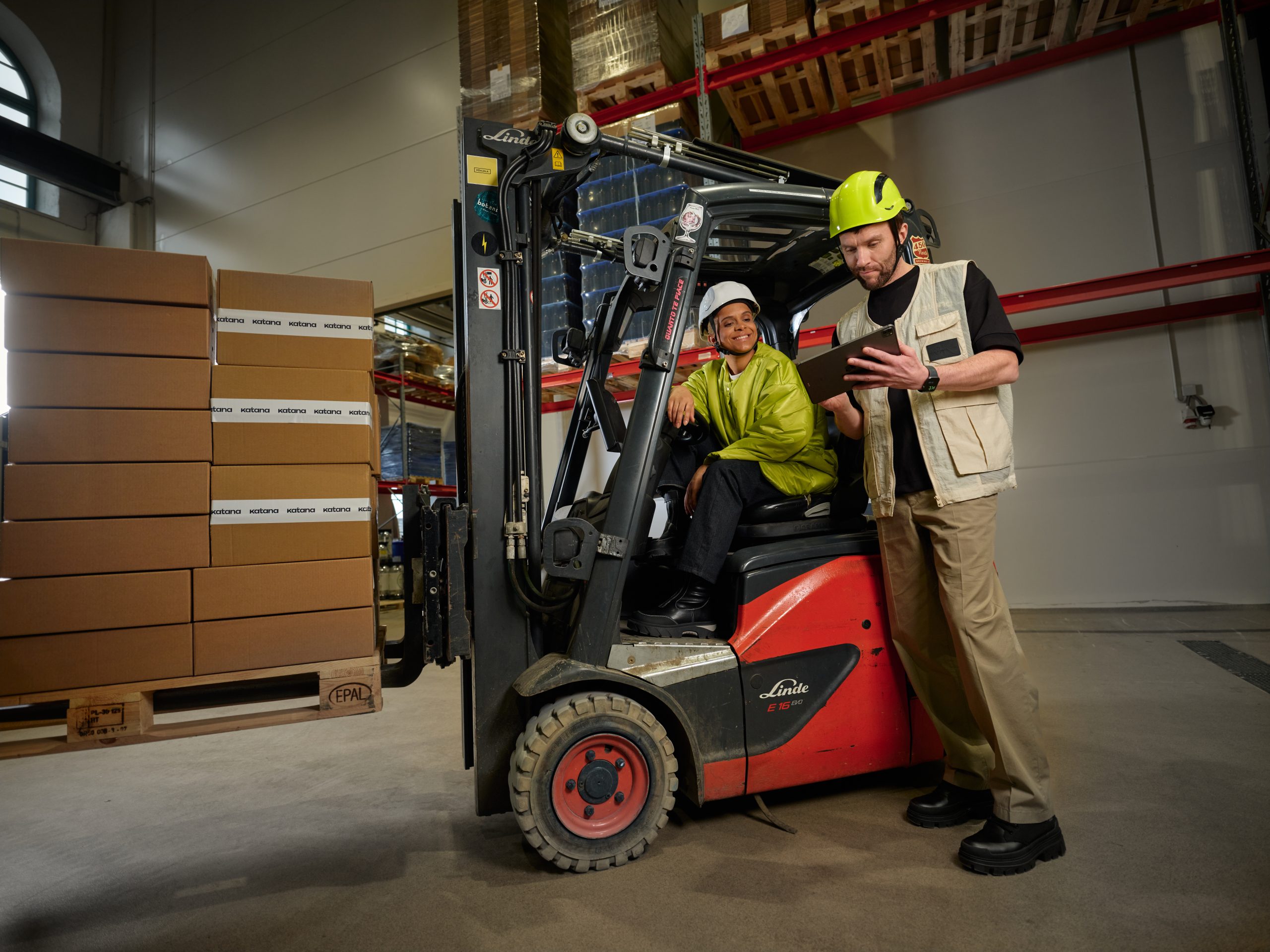
Motivated workers
TPM promotes active participation and empowerment of workers by involving them in maintenance and offering training. This builds a sense of ownership and responsibility, enhancing a team-oriented and learning-focused work environment.
Cost savings
TPM helps reduce maintenance costs by focusing on preventive and predictive practices. It minimizes the need for costly repairs, emergency maintenance, and equipment replacement due to premature failures. Additionally, improved equipment efficiency reduces downtime, contributing to cost savings and increased profitability.
Safer workplace environment
Safety is an inherent part of TPM in manufacturing. Promoting regular equipment inspections, maintenance, and employee training helps identify and address potential safety hazards. It also creates a safer and healthier workplace environment for employees.
Continuous improvement culture
TPM fosters a culture of continuous improvement by engaging employees in problem-solving activities, encouraging innovative ideas, and promoting an ongoing learning and development mindset.
Download your free production quality control checklist
Why go through the stress of creating your own when you can grab a production quality control checklist from Katana? Use it to keep standards high and ensure your customers love your products.
What are the 8 pillars of TPM?
The TPM philosophy consists of eight pillars aiming to maximize the efficiency and effectiveness of equipment and processes:
- Autonomous maintenance
- Focused improvement
- Planned maintenance
- Quality maintenance
- Early equipment management
- Education and training
- Administrative and office TPM
- Safety, health, and environment (SHE)
Let’s take a look at these in more detail.
1. Autonomous maintenance
Empower operators to take responsibility for routine maintenance tasks, including cleaning, inspection, and minor repairs. It promotes a proactive approach to equipment maintenance and encourages a sense of ownership among operators.
2. Focused improvement
Identifying and eliminating losses, inefficiencies, and waste in production processes encourages continuous improvement. This pillar emphasizes problem-solving, root cause analysis, and implementing innovative ideas.
3. Planned maintenance
Planned and scheduled maintenance activities focus on preventing equipment failures and unplanned downtime. It involves creating inspection plans, conducting preventive maintenance, and regularly monitoring equipment conditions.
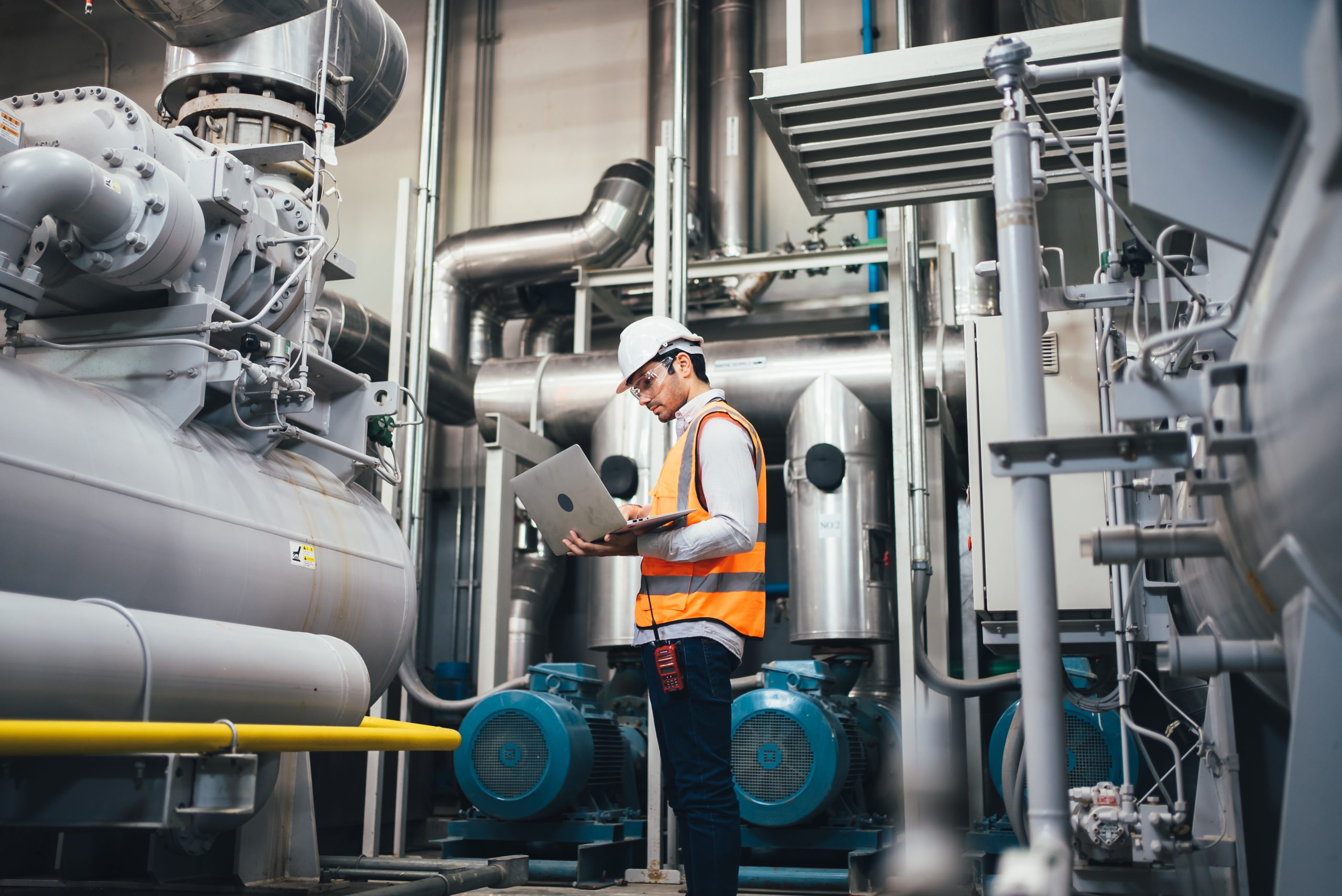
4. Quality maintenance
Prevent defects, errors, and quality issues in the production process with a thorough inspection, quality control, and proactive measures to maintain and improve product quality.
5. Early equipment management
Consider equipment reliability and maintainability during the design and acquisition phase. Early equipment management focuses on improving equipment effectiveness, reducing life cycle costs, and ensuring ease of maintenance.
6. Education and training
Recognize the importance of providing ongoing education and training to employees at all levels. This includes technical training, skill development, and knowledge sharing to enhance competence and promote a culture of continuous learning.
7. Administrative and office TPM
The seventh pillar extends the TPM principles beyond the production floor and into administrative and support functions. It focuses on optimizing administrative processes, reducing waste, improving workflow, and enhancing overall office efficiency.
8. Safety, Health, and Environment (SHE)
The final pillar focuses on a safe and healthy work environment, adhering to safety protocols, and minimizing the environmental impact of operations.
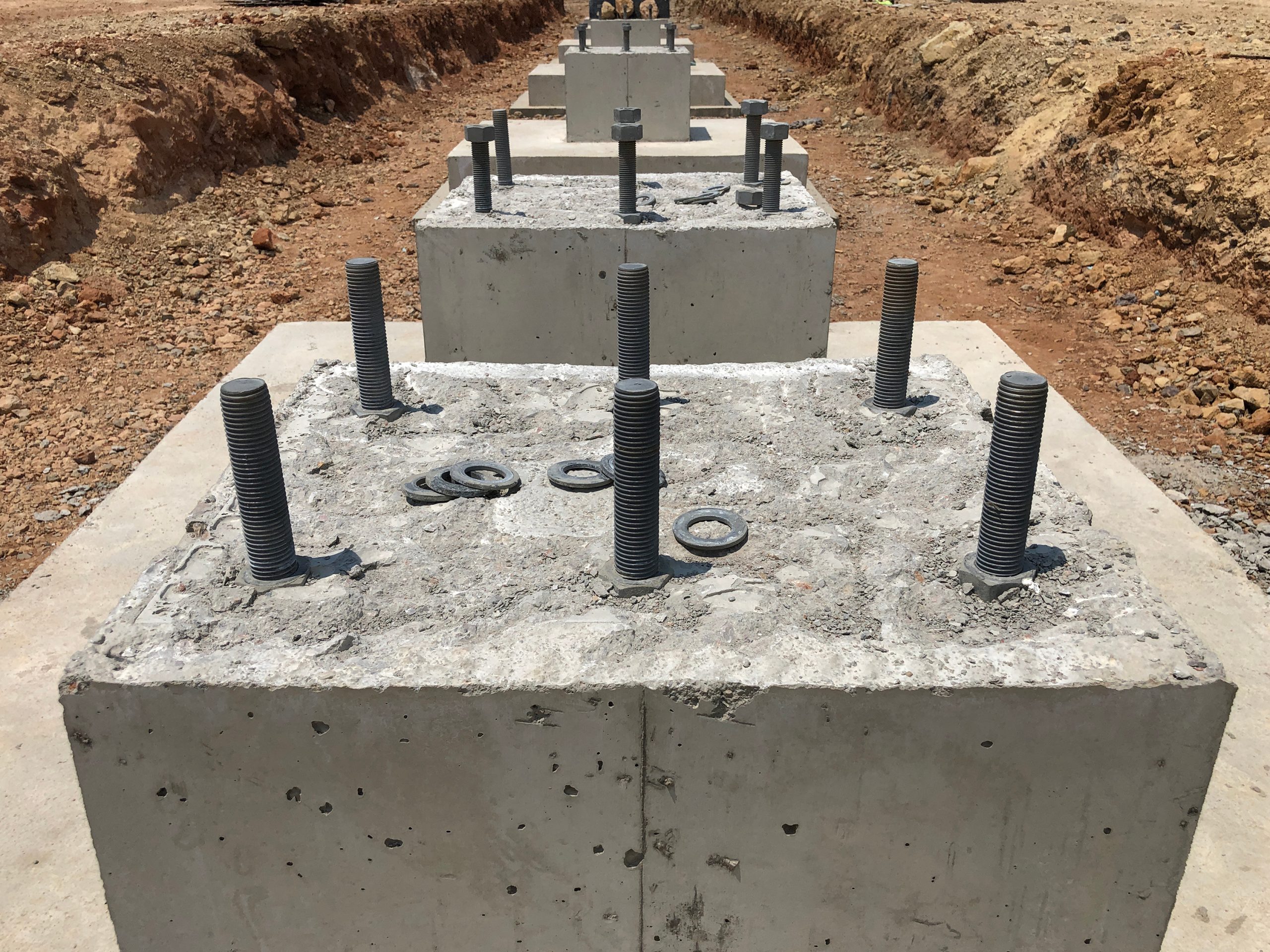
The foundation
Now that we have the eight pillars, we need to ensure a strong foundation. Don’t worry — you don’t have to come up with it. This was also developed by Mr. Nakajima. The foundation for the eight pillars is 5S:
- Sort — Remove everything that’s not needed in the working area
- Straighten — Organize all the items that are left
- Shine — Clean the work area
- Standardize — Standardize the above three activities and schedule them
- Sustain — Make sure the standards are constantly followed
Looks like the top minds in Japan agree with what our parents have been hammering to us for decades. Having only the necessary tools and equipment nicely organized in your clean work area makes it much easier to find what you’re looking for. It also reduces risks and frustration.
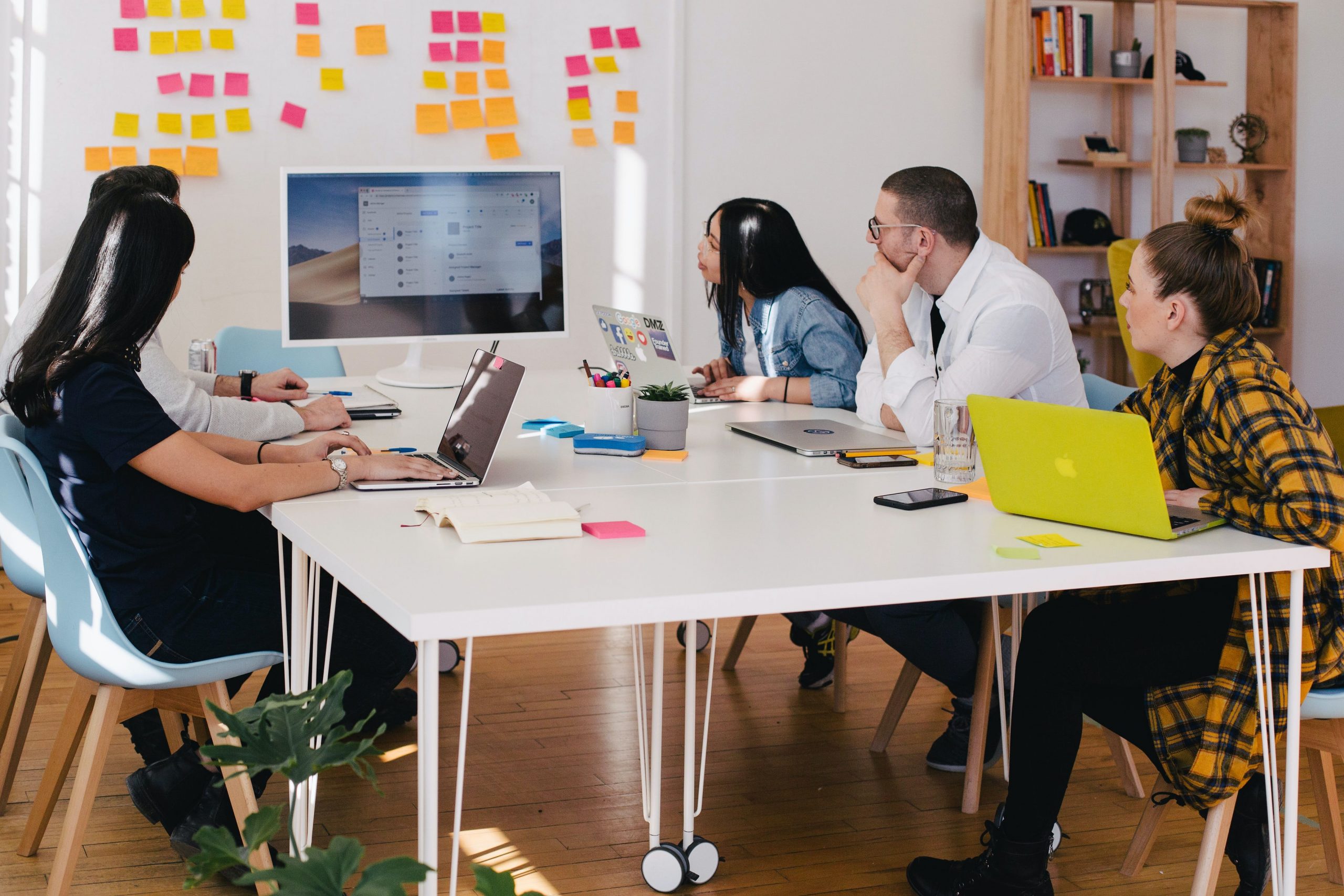
7 steps to implement TPM
Implementing a TPM system involves several steps and requires a systematic approach. Here’s a general outline you can follow to implement TPM.
1. Establish a TPM team
Form a team of representatives from various departments, including production, maintenance, engineering, quality, and management. This team will lead and drive the TPM implementation process.
2. Conduct an initial assessment
Evaluate the current state of maintenance practices and equipment performance. Identify areas that need improvement and prioritize them based on their impact on productivity, reliability, and business goals.
3. Set TPM goals and objectives
Define specific and measurable goals for TPM implementation — TPM KPIs (key performance indicators). Some examples could be:
- Reduce equipment downtime
- Improve OEE
- Increase maintenance efficiency
- Enhance employee skills and involvement
4. Develop a detailed implementation plan
Create a comprehensive plan that outlines the activities, timelines, and responsibilities for TPM implementation. This should include initiatives such as:
- Autonomous maintenance
- Planned maintenance
- Focused improvement
- Education and training programs
5. Implement autonomous maintenance
Empower operators to take responsibility for routine maintenance tasks and conduct autonomous maintenance activities, such as cleaning, inspection, and minor repairs. Provide training and guidance to operators to ensure they can perform these tasks effectively.
6. Implement planned maintenance
Develop a maintenance schedule based on equipment conditions and historical data. Implement predictive maintenance strategies to prevent failures and extend equipment life. Set up a system for tracking maintenance activities and monitoring key performance indicators.
7. Continuous improvement
Nurture a culture of continuous improvement by encouraging employees to identify and address equipment-related issues and inefficiencies. Implement improvement projects and encourage employees to be more involved through suggestion systems, team meetings, and training programs.
The implementation may require additional steps or customization depending on your business, industry, and goals. It’s crucial to configure TPM according to your business needs and to keep adjusting it as you progress.
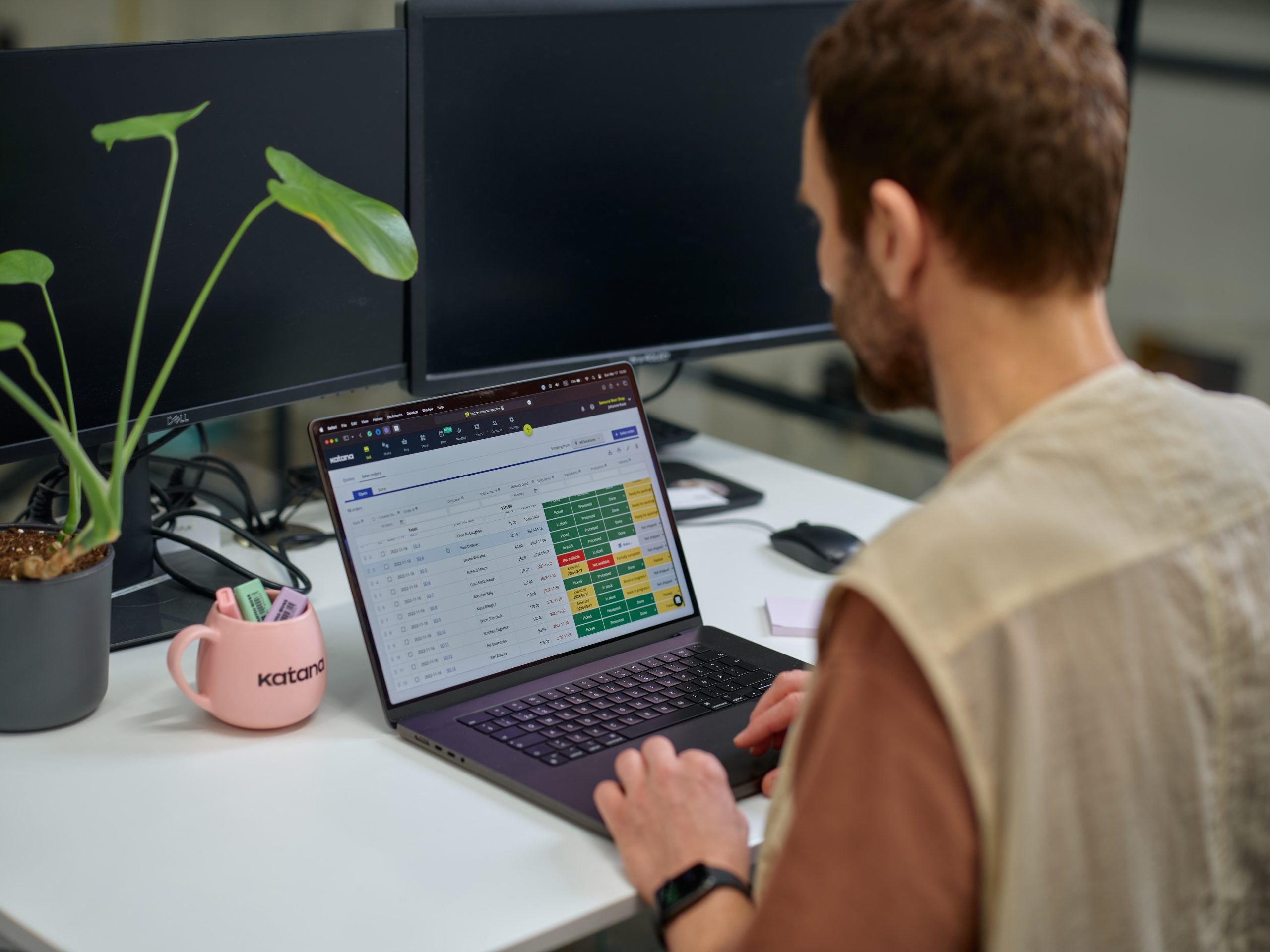
Katana and TPM in manufacturing
As with many aspects of manufacturing, there are systems and online platforms to optimize tasks and operations. Many businesses opt for ERP or cloud solutions to take care of mundane daily tasks for them. In the true spirit of TPM, these tools help streamline workflows and minimize the risk of human errors.
Katana is an all-in-one lean manufacturing platform that can support TPM implementation with its many features.
Production planning and scheduling
Effective manufacturing TPM requires planning and scheduling maintenance activities without disrupting production. Katana’s production planning features enable you to create and manage production orders, allocate resources, and schedule maintenance activities, creating a balance between production output and maintenance efficiency.
Inventory management
Katana’s inventory management capabilities help you maintain optimal stock levels, track spare parts with barcode scanning or serial number tracking, and create reorder points to ensure you have the necessary supplies for maintenance tasks. This will help in reducing downtime and streamlining the maintenance process.
Insights
TPM relies on data analysis to identify patterns, monitor performance, and make informed decisions. Katana provides real-time visibility into production and maintenance data, offering analytics and reports that help you gain insights into aspects of your manufacturing, such as:
- Equipment performance
- Downtime causes
- Maintenance costs
- Other critical metrics
This information empowers you to identify improvement opportunities, prioritize maintenance efforts, and make data-driven decisions for continuous improvement.
Collaboration and communication
A smooth TPM system requires collaboration and communication among different teams and stakeholders. Katana’s Shop Floor App enables seamless communication between departments. It gives you full shop floor control and your operators access to their tasks, fostering a collaborative environment that promotes TPM principles and practices.
Integrations
Katana offers seamless integrations with various software systems, enabling a streamlined TPM implementation. Connecting to tools that optimize accounting, data analytics, and automation, ensures smoother data flow and enhanced visibility while supporting data-driven decision-making for TPM in manufacturing.
Now, having grasped the essence of TPM, it’s time to unleash its full power and explore the boundless opportunities to expand your business. To see how Katana can help you achieve all that, request a demo today.
Unlock the TPM system with Katana’s seamless integration
Learn to streamline your maintenance processes and optimize equipment reliability.
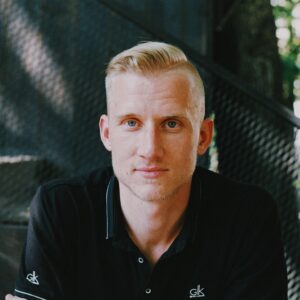
Henry Kivimaa
Table of contents
Get inventory trends, news, and tips every month
Get visibility over your sales and stock
Wave goodbye to uncertainty with Katana Cloud Inventory — AI-powered for total inventory control