Process costing and process costing accounting
Running a successful manufacturing business can sometimes feel like a juggling act at the circus. Making sure not to drop any balls can eventually become overwhelming and exhausting. Luckily, there are methods and tricks that can make the balancing seem effortless, allowing you to bask in the applause.
Enter process costing — a method that helps manage manufacturing expenses, optimize costs, and gain a competitive edge. In this article, we will explore the world of process costing, what it is, and how it can benefit your business. So, grab your calculator, and let’s get processing.
What is process costing?
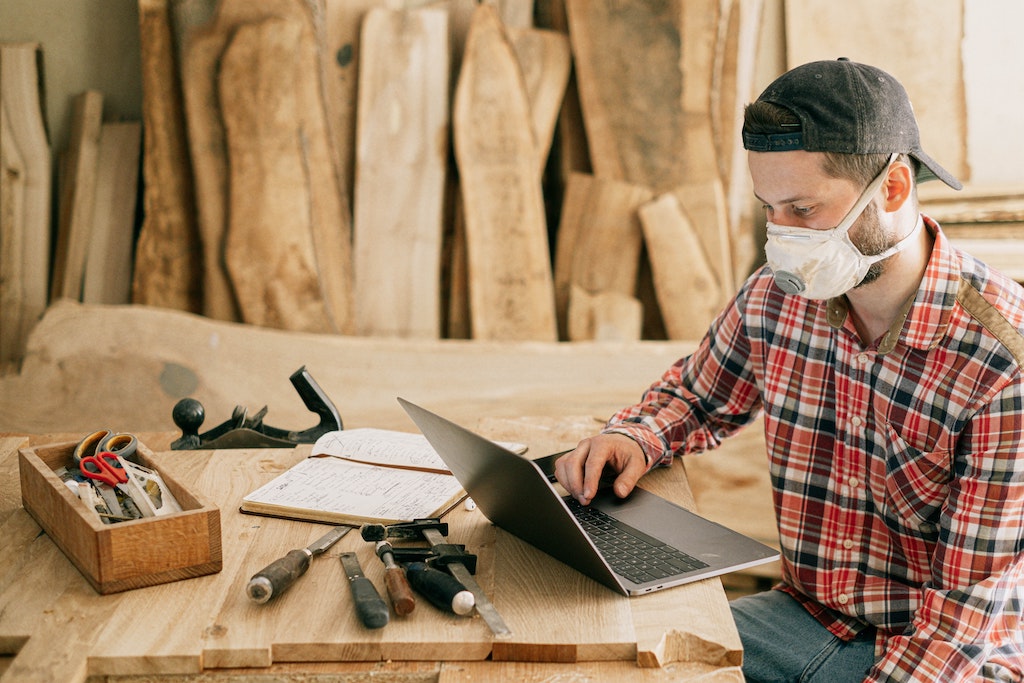
Process costing is a way for businesses to figure out the overall cost of manufacturing in large quantities. It involves looking at how much money is spent on things like materials, workers, and machines during the production process. By using process costing, companies can calculate the average cost per unit, make smart pricing choices, and improve their operations to make more money.
Imagine an electronics company that manufactures televisions.
They produce thousands of TVs that are almost identical. In such cases, process costing is crucial for determining the cost per unit or at least putting them in the same price class. Since the products are so alike, the cost to make each item tends to be very close.
Process costing helps these companies calculate the average cost of putting together one TV by analyzing the expenses incurred throughout the production process.
They consider costs associated with each step of production, such as:
- Materials
- Labor
- Machinery and equipment
- Overhead expenses
Process costing helps ensure that the price per unit remains consistent or falls within the same price range for products of similar nature.
With this information, companies can make informed decisions about pricing their products, setting competitive rates, and determining profit margins. Process costing provides valuable insights into the costs of producing similar products on a large scale. It helps companies optimize their operations, improve efficiency, and maintain a competitive edge in the market.
What is process costing in cost accounting?
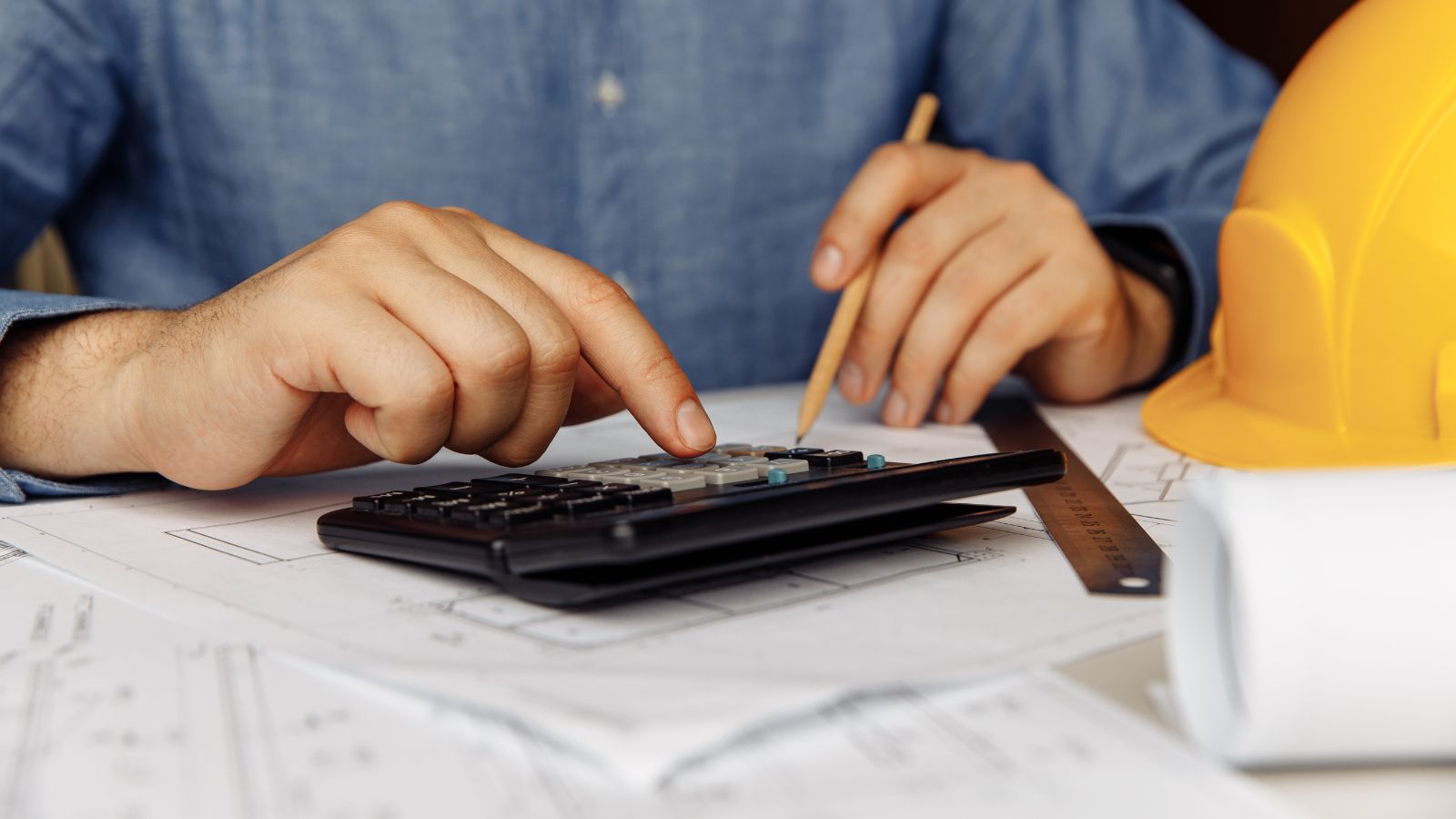
In cost accounting, process costing is a method used to determine the cost of producing goods or services in a continuous manufacturing environment. The total expenses incurred during a particular production process or within a department are allocated to the units produced within that process. Instead of assigning costs to individual units, process costing focuses on spreading the costs evenly across all units manufactured within a specific time period.
The process starts by dividing the production process into distinct stages or departments.
Each department has its own costs, such as materials, labor, and manufacturing overhead. These costs are summed up for a given period, typically a month, to determine the total cost incurred by each department. The sum for each department is then divided by the total number of units produced within that department during the period.
This calculation yields the average cost per unit (CPU).
It is important to note that process costing assumes that all units within a department are identical or very similar in terms of cost. Process costing is particularly useful in industries where mass production is common, such as chemical manufacturing, oil refining, food processing, and electronics assembly. It provides valuable information about the CPU and helps businesses assess the efficiency and profitability of their production processes.
By using process costing in accounting, companies can monitor and control costs, make informed pricing decisions, and evaluate the performance of different departments or stages within their production processes. It plays a vital role in cost accounting by providing accurate cost information that directs decision-making and financial analysis.
Optimize your manufacturing with a production schedule template
Our free downloadable production scheduling template is designed to help you streamline your production processes and allocate costs effectively.
Examples of process costing
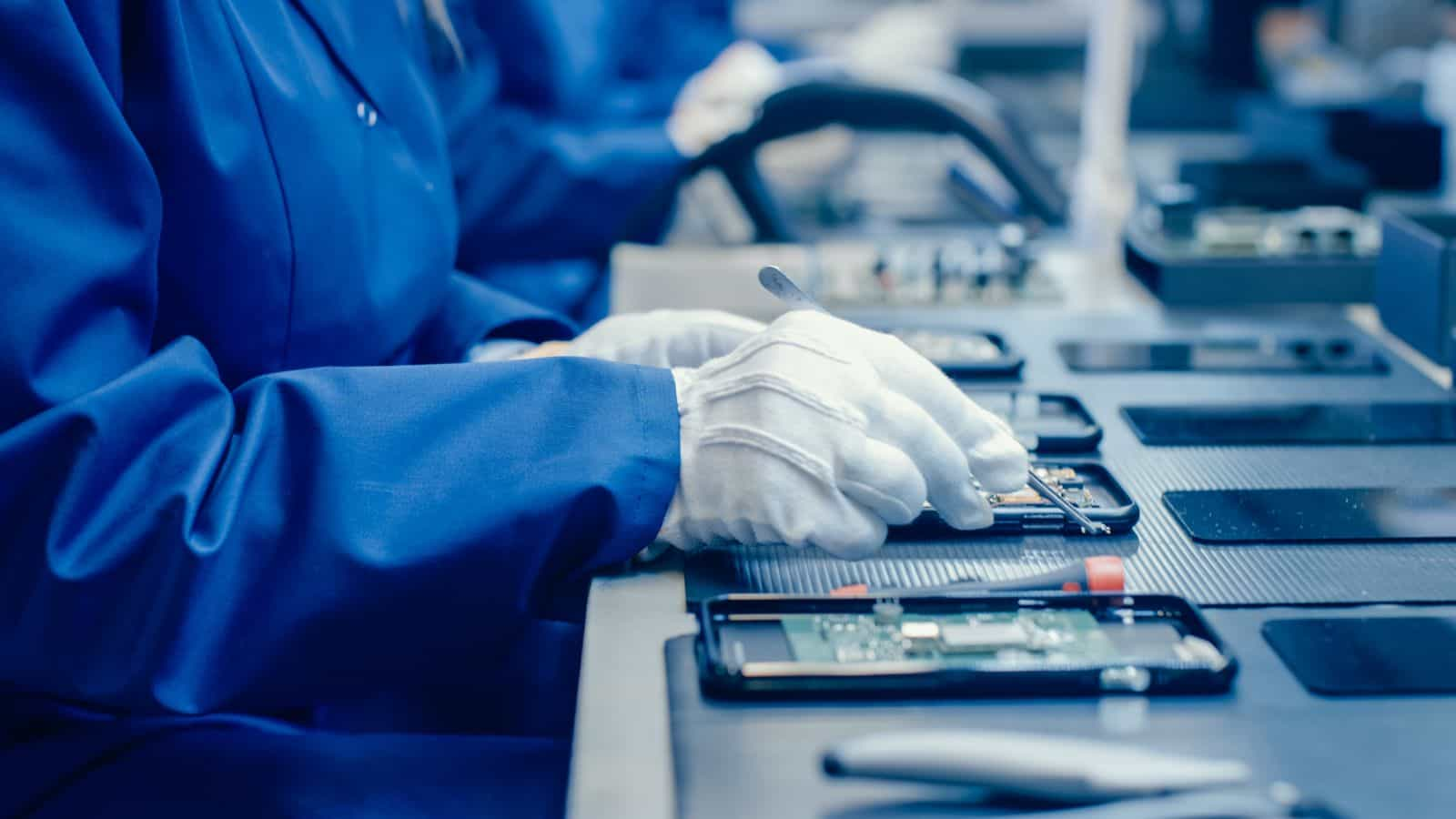
Here are a few examples of industries or scenarios where process costing is commonly used:
- Chemical manufacturing — In the chemical industry, process costing is essential for determining the cost of producing various chemical products. Whether it’s making fertilizers, plastics, or pharmaceuticals, process costing helps allocate expenses incurred at each stage of the production process, such as mixing, reaction, and purification.
- Food processing — Process costing is used in the food industry, producing large quantities of similar products. For example, a company that makes canned goods or beverages would utilize process costing to determine the CPU by allocating costs incurred during processing, packaging, and labeling.
- Textile manufacturing — Textile manufacturers rely on process costing to calculate the CPU of fabrics or garments. From spinning yarn to dyeing, weaving, and stitching, process costing helps track and allocate expenses at each stage of the textile production process.
- Oil refining — In the petroleum industry, process costing is employed during the refining process. From the initial distillation of natural oil to the various refining steps, process costing helps determine the cost per barrel of refined petroleum products like gasoline, diesel, and jet fuel.
- Assembly line manufacturing — Industries that rely on assembly line production, such as automotive manufacturing, often utilize process costing. Each stage of the assembly process incurs costs, including labor, equipment, and overhead. Process costing helps calculate the CPU by allocating these costs to the final product.
These are just a few examples, but process costing is applied in other industries where large quantities of similar products are produced through repetitive processes.
3 elements of process costing
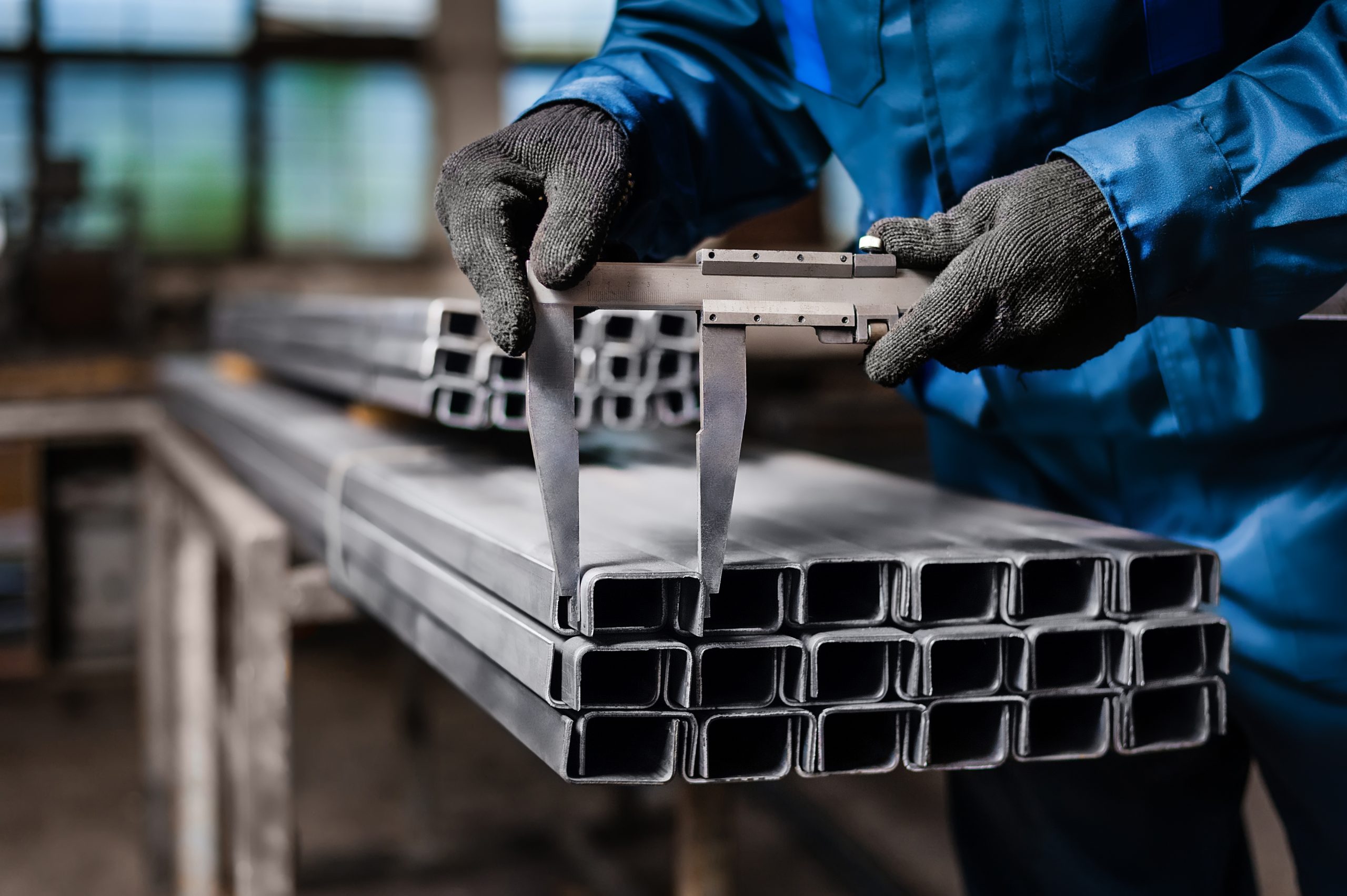
To accurately calculate the total cost incurred in each process, three fundamental elements of process costing come into play:
- Direct materials
- Direct labor
- Manufacturing overhead
1. Direct materials
These are the materials that can be specifically identified and directly traced to a particular production process. Direct materials include raw ingredients used in manufacturing a product, such as wood, steel, or plastic.
2. Direct labor
This refers to the cost of labor directly involved in the production process. It includes the wages or salaries of the workers directly converting the raw materials into finished goods. Direct labor costs are usually tracked based on the number of hours worked or through other relevant measures.
3. Manufacturing overhead
Also known as indirect expenses or factory costs, manufacturing overhead includes all the production costs that cannot be directly assigned to a specific product or process. It consists of various expenses necessary for the production process, such as rent, utilities, equipment, indirect labor, maintenance, and other overhead costs. Factory costs are allocated to products using predetermined overhead rates based on factors like machine hours, direct labor hours, or material costs.
Benefits of process costing
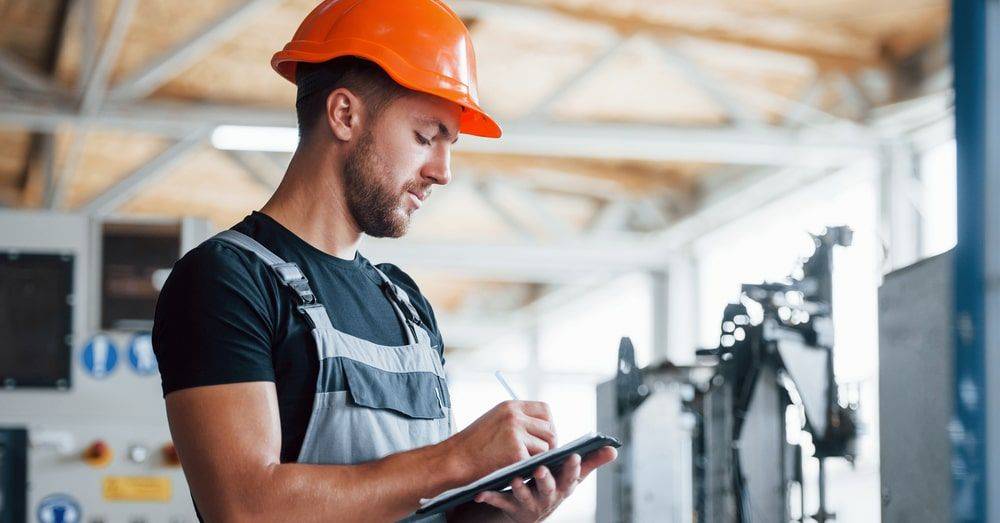
Process costing holds significant importance for businesses in several ways:
- Cost analysis — Process costing provides a detailed breakdown of costs incurred at each stage of the production process. It helps businesses identify areas of spending, enabling them to analyze and manage expenses effectively. Companies can make informed decisions regarding resource allocation, process improvement, and cost reduction strategies by understanding the cost composition.
- Pricing decisions — Process costing plays a crucial role in setting product prices. By accurately calculating CPU, businesses can determine the appropriate selling price that covers all expenses and allows for a reasonable profit margin. It ensures that pricing decisions are based on actual costs that incur during manufacturing, avoiding product underpricing or overpricing.
- Profitability assessment — Process costing allows businesses to assess the profitability of their products or services. By comparing the CPU with the selling price, they can determine whether the production process generates profits or incurs losses. This information helps evaluate the viability of different product lines and identify areas where cost improvements are needed.
- Performance evaluation — Process costing allows performance assessment at various stages of the production process. It enables businesses to compare actual costs with expected budgets, helping identify inefficiencies or excess spending. By monitoring performance, manufacturers can take corrective actions to optimize processes, reduce costs, and improve overall efficiency.
- Financial reporting — Process costing provides accurate cost information essential for financial reporting purposes. It ensures that the costs associated with inventory and goods sold are correctly accounted for in financial statements. This information assists with accurate financial analysis, profitability assessment, and informed financial decisions.
- Decision-making — Process costing is a valuable method for decision-making within a business. Process costing provides the necessary cost data to evaluate the financial implications of different decisions, whether it means expanding production, introducing new products, or outsourcing certain processes. It enables businesses to make informed choices that align with their financial goals and objectives.
Altogether, process costing helps manufacturers find the best ways to improve processes, eliminate inefficiencies, and stay competitive.
Steps of process costing
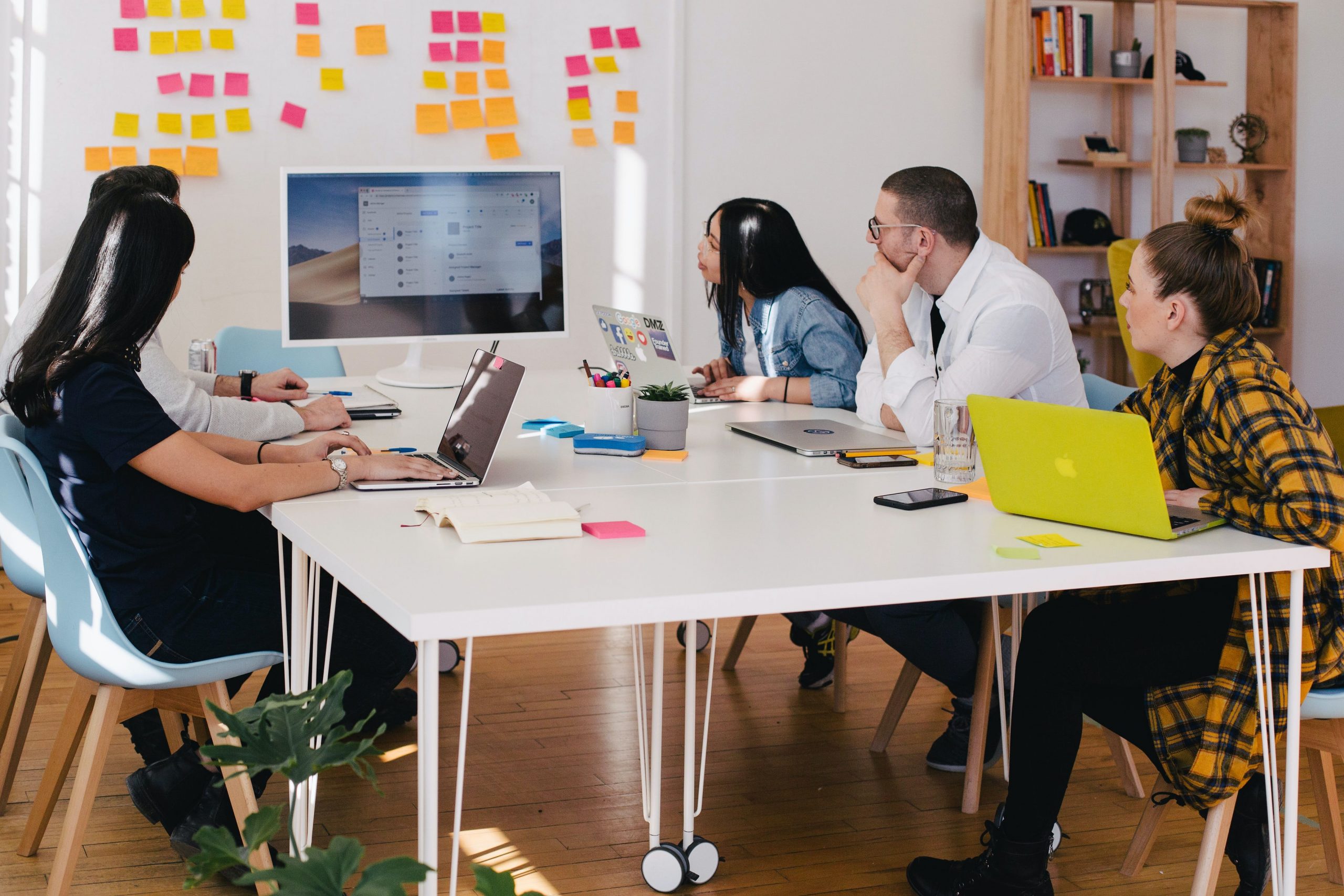
The process costing method involves several steps to allocate costs and accurately determine CPU in production. Simply put, the formula for process costing calculation is:
Cost per unit of output = total expenses / total number of units produced
Here are the typical actions involved in process costing in cost accounting.
- Identify the production process — Determine the specific production process or department within the organization for which you want to calculate the CPU. It could be a specific manufacturing step, assembly, or department involved in a particular task.
- Determine cost elements — Identify the cost elements or categories relevant to the production process. This may include direct materials, direct labor, and manufacturing overhead costs.
- Accumulate costs — Accumulate all the costs associated with the production process for a specific time. This involves collecting data on the direct materials used, direct labor hours expended, and the manufacturing overhead costs incurred during that period. This information can be obtained from accounting, invoices, payroll, and other appropriate sources.
- Calculate equivalent units — Determine the equivalent units of production for the analyzed process. Equivalent units represent the number of units that could have been completed given the inputs used. This step is necessary when there are units in progress (partially completed) at the end of the accounting period. Equivalent units account for the work done on these units and help in the accurate allocation of costs.
- Allocate costs — Allocate the accumulated costs to the finished and in-progress production units. This involves dividing the total expenses incurred during the period by the equivalent units. The aim is to distribute the costs evenly across all units, considering both completed and partially completed units.
- Calculate cost per equivalent unit — Calculate the price per equivalent unit by dividing the total costs allocated to the units by the number of equivalent units. This provides the average cost per production unit for the process under consideration.
- Determine the total cost of completed units — Multiply the number of completed units by the cost per equivalent unit to determine the total cost of the units completed during the period.
- Account for work in process — Account for any partially completed units remaining at the end of the accounting period. Allocate the costs associated with these units based on their stage of completion.
- Analyze the results — Analyze the results of the process costing calculations to gain insights into the overall cost structure of the production. Assess the CPU, identify any cost variations or inefficiencies, and use the information to make informed decisions about cost management, pricing, and process improvements.
It’s important to note that the exact steps may vary slightly depending on the specific industry or company’s practices.
Software and process costing
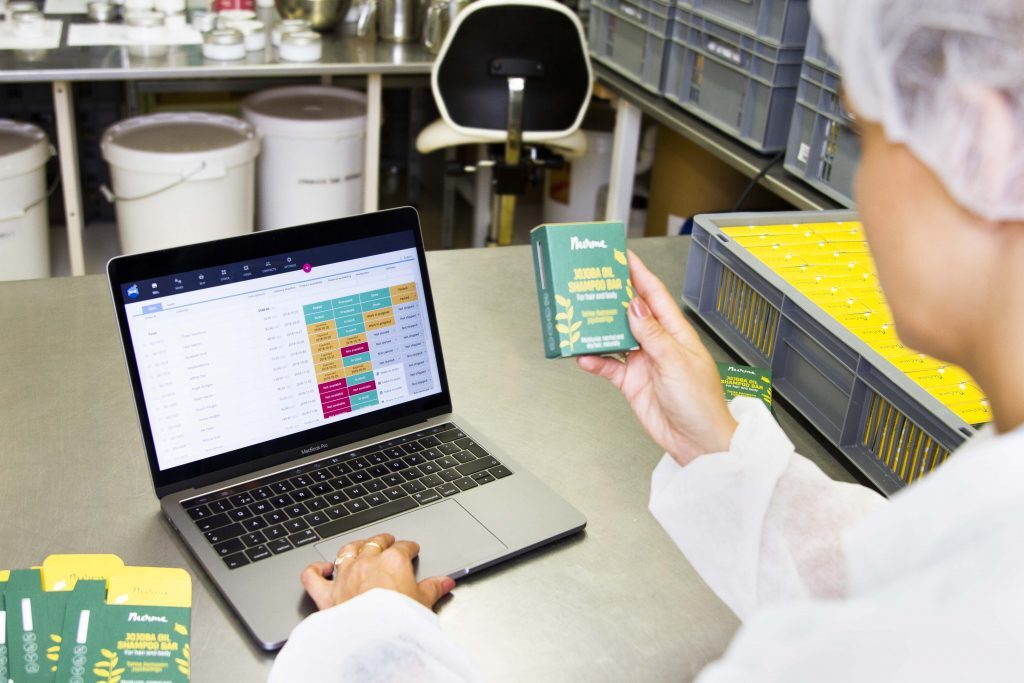
Using software for process costing can revolutionize how businesses manage their manufacturing operations and streamline their cost accounting processes.
Here’s how software like Katana can help businesses with their process costing.
- Simplified cost allocation — Katana automates the distribution of costs to different stages or departments of the production process. With its intuitive interface, businesses can easily assign costs to each step, ensuring accurate and consistent cost allocation.
- Live cost tracking — Katana provides visibility into production costs, allowing businesses to monitor expenses in real time, enabling better cost control and empowering proactive decision-making. Manufacturers can track materials, labor, and overhead expenses, giving them a comprehensive view of their process costing.
- Accurate cost per unit calculation — With Katana, businesses can precisely calculate the price per unit. By automatically adding up costs and dividing them by the number of units produced, Katana eliminates manual calculations and reduces the risk of human errors in determining the CPU.
- Efficient inventory management — Katana integrates process costing with inventory management, providing businesses with a holistic view of their manufacturing operations. It tracks inventory levels, material usage, and production progress, ensuring accurate cost calculations and helping optimize inventory levels.
- Enhanced reporting and analysis — Katana generates comprehensive reports that offer deep insights into process costing. Businesses can analyze cost variances, identify inefficiencies, and make data-driven decisions to improve profitability and operational efficiency. Customizable dashboards and visualizations make it easy to understand and interpret the data.
- Seamless integration with accounting systems — Katana seamlessly integrates with popular accounting systems like QuickBooks Online and Xero, ensuring that process costing data flows smoothly into the overall accounting framework. This integration eliminates manual data entry, reduces errors, and simplifies reconciliation.
- Scalability for growing businesses — Katana is designed to support businesses of all sizes. Whether you’re a small manufacturer or a growing enterprise, Katana scales effortlessly to meet evolving needs. As businesses expand their operations, Katana adapts to accommodate increased production volume and complexity.
Using software like Katana for process costing empowers businesses to optimize their manufacturing processes, gain better cost control, and make informed decisions. By automating and streamlining the process costing workflow, Katana saves time, reduces errors, and provides valuable insights that drive business growth and profitability.
Sounds good? Get a demo and see for yourself what good process costing can do for your business.
Table of contents
Accounting Guide
Get visibility over your sales and stock
Wave goodbye to uncertainty by using Katana Cloud Inventory for total inventory control
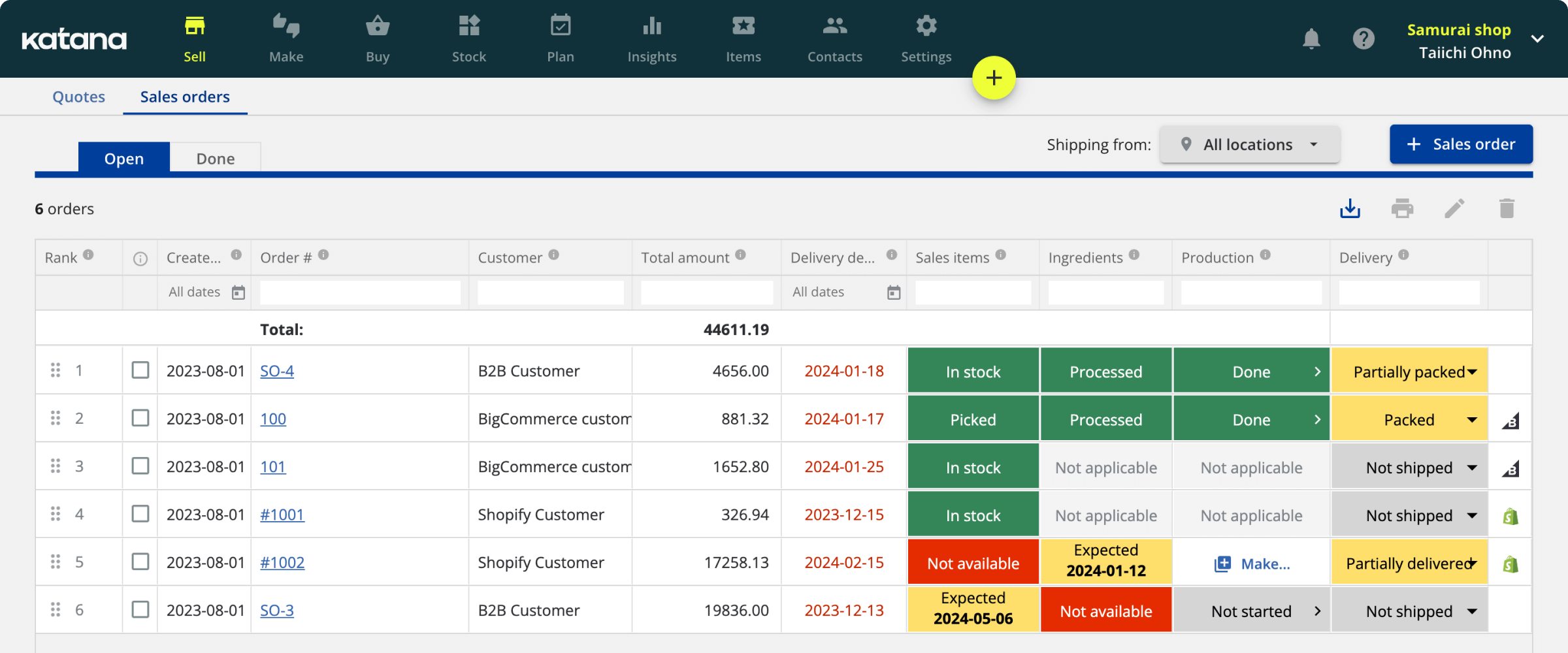