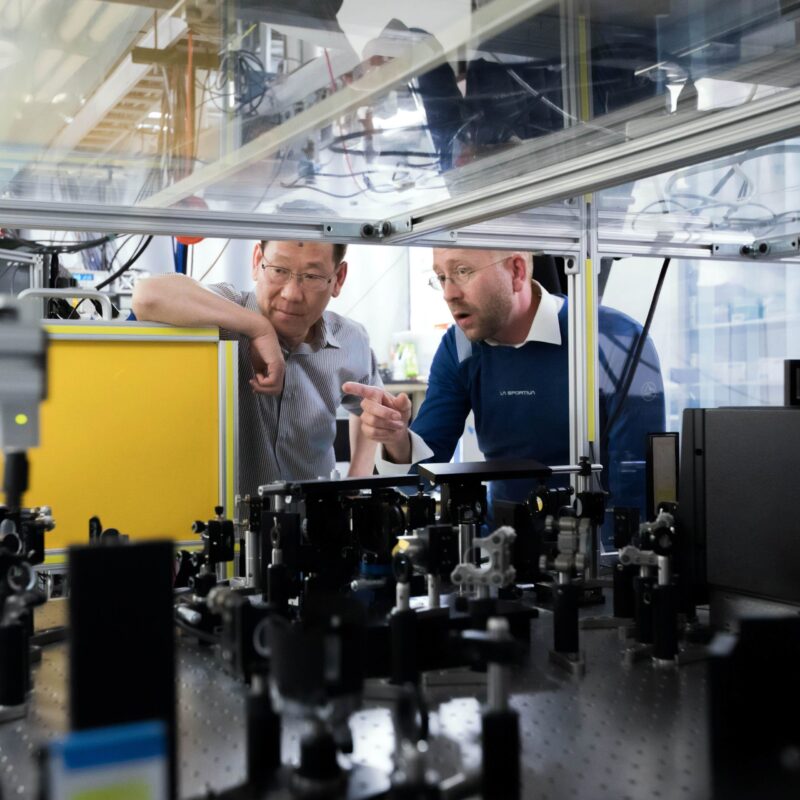
Streamline your electronics inventory and production planning
Katana is a great cloud ERP for electronics manufacturing, offering planning and scheduling to ensure high quality and speedy delivery of products.
Features
Helping electronics companies maintain optimal inventory and always meet market demands
Creating intricate products requires accurate planning and scheduling, and this also applies to electronic manufacturers, whether they create microtechnology or industrial machinery. Katana’s electronics ERP has features that help make daily work easier and automate many everyday activities. Thousands of manufacturers from various industries use Katana to manage manufacturing and distribution in one place.
Bring your innovative spark to the electronic industry with a perfect production process
You might be building tiny microchips for mobile phones or massive industrial machinery for other businesses to use in warehouses. Either way, Katana’s electronics ERP is here to simplify your day-to-day processes, especially in industrial manufacturing. With a greater overview of production, automated stock reordering, and finance, sales, and shipping integrations, you’ll have more time to build and refine your business.
The basis of a well-made product is a structured bill of materials (BOM), and it’s no different for great electronics products. If you need to make an engineering change to your products, you update the BOM, and your team will know what needs to be changed in constructing that item. BOMs are a major part of Katana’s ERP for electronics, essentially a product configurator, helping track the use of all your raw materials and their cost over time, and identify when you need to create automated reorder points so you’re not hit by stockouts.
Automated reordering allows you to maintain the optimum inventory amount to always have the correct raw materials in stock. You can adjust these points in case a particular product sees a drop or sudden spike in sales and you need to change your material reordering. It allows for capacity planning, both in the workload of your team and the space in your warehouse.
Work with your warehouse and get products sold and shipped
Along with your BOM, Katana’s electronics ERP comes with the Shop Floor App, a great warehouse management feature. The app allows you to create tasks for your team and track when products are built, packed, and shipped.
Once tasks in the warehouse are completed and products are made, you need a platform to sell them. For sales management, Katana has native e-commerce integrations with Shopify, WooCommerce, and BigCommerce, as well as third-party integrations with many other fantastic providers. We also have integrations with shipping partners to meet distribution needs and get your products to customers worldwide.
See Katana in action
- Manage production planning, resource allocation, and scheduling in real time
- Issue purchase orders based on precise material requirements and reorder points
- Implement Katana on your own or with a team of experts that will set you up for success
Learn more about our plans and the features they come with
- Plans starting from $179 / month
- Annual and monthly billing options
- Add users and warehouses as you grow
Integrate with the best e-commerce, accounting, reporting, and CRM software out there
Create custom API integrations
Use Katana’s open API to create custom workflows and connect to apps beyond our list of integrations. Automate data transfers between the services you use to level up efficiency. Take a look at our API documentation to learn more.
ERP for Electronics Industry FAQs
ERP for electronics refers to an ERP system specifically tailored to the needs of the electronics industry. It involves various software applications and tools to manage all aspects of electronic manufacturing and distribution processes.
Katana is an ERP solution designed for small and mid-sized manufacturers. It offers a range of features tailored to the electronics industry, including:
- Supply chain management — Efficiently manage purchasing, logistics, and supplier tracking for electronic components
- Product lifecycle management — Track and manage the entire lifecycle of your electronic products
- Process manufacturing management — Streamline electronics manufacturing, optimize efficiency, and track orders
- Quality control and compliance — Ensure product quality, regulatory compliance, and traceability
- Sales order management — Manage customer orders, quotations, pricing, contracts, and order fulfillment
- Financial management — Integrate accounting systems to track costs, revenue, and profitability
By implementing Katana’s ERP for electronics industry, manufacturers can centralize their operations, improve efficiency, and make data-driven decisions.
Katana’s tailored features help manufacturers streamline their processes and drive growth and profitability in the dynamic electronics industry.
Yes, this is possible using our e-commerce partner Shopify. This integration allows you to have sales management across all potential sales points and link the data back to Katana. Read more about the Katana+Shopify integration from our Knowledge Base.
Katana’s electronics ERP system is also designed to integrate with a range of e-commerce and B2B sales platforms, allowing you to scale industrial manufacturing sales whether you’re selling B2B or D2C — or both.
Yes, Katana supports a range of barcode scanning features, so you can track individual products, orders, or batches using barcodes. Improve quality control and streamline your production processes by easily tracking items and products across multiple warehouses using a range of barcodes supported by Katana’s electronics ERP.
Get visibility over your sales and stock
Wave goodbye to uncertainty by using Katana Cloud Inventory for total inventory control
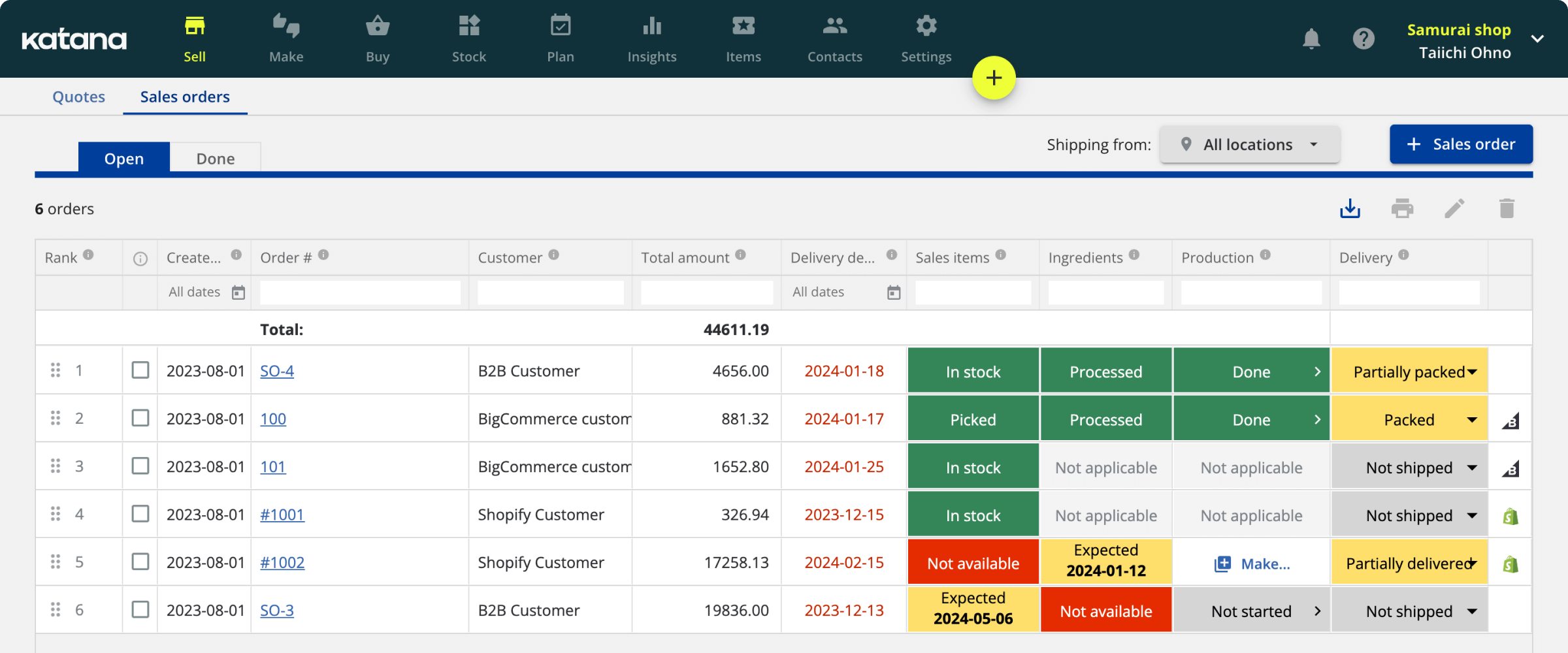