Inventory management methods that improve efficiency
Are you struggling to keep inventory stocked at an adequate level?
It could be that increasing demand has you on the back foot, and your lead time is slowly increasing with each fulfillment. Or maybe you have some finished goods stocked that aren’t selling so well and are taking up space. If these issues sound familiar to you, it’s time to audit your inventory management practices.
In this article, you’ll learn all the essentials to adopting inventory management methods, with a choice of eight to get you started on this path.
What is inventory?
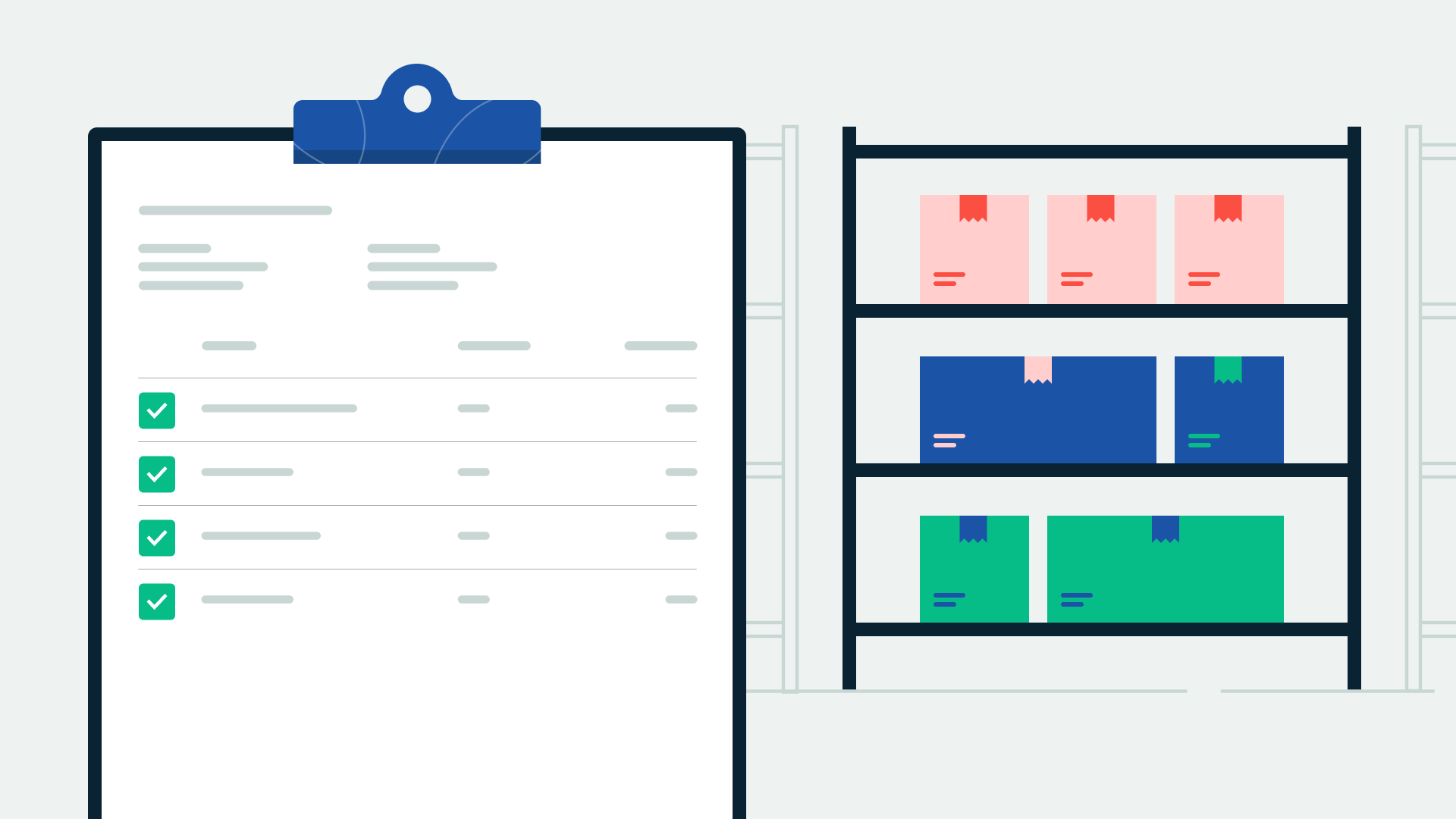
Inventory refers to all the materials and products that a company owns and intends to sell as part of its business operations.
Accurate tracking of inventory is essential for businesses to manage their resources effectively and efficiently. Inventory management involves recording and tracking information such as quantity, value, and stock location. This information helps businesses make decisions about operations, purchasing, and sales.
Techniques of inventory management are the different ways of overseeing and controlling inventory levels.
This includes activities such as order planning, warehousing, and transportation. Effective inventory management ensures businesses have the right stock level to meet customer demand. This can also help to minimize waste and optimize workflows.
The most appropriate method will depend on the type of inventory and the business’s accounting needs.
Inventory is a key asset for businesses and can significantly impact financial statements. For this reason, it is important to have accurate and up-to-date records of inventory levels. Regular stocktaking can help to ensure that inventory levels are correct in accounting records.
Get the ultimate guide to inventory management
A comprehensive ebook that covers everything you need to know about inventory management.
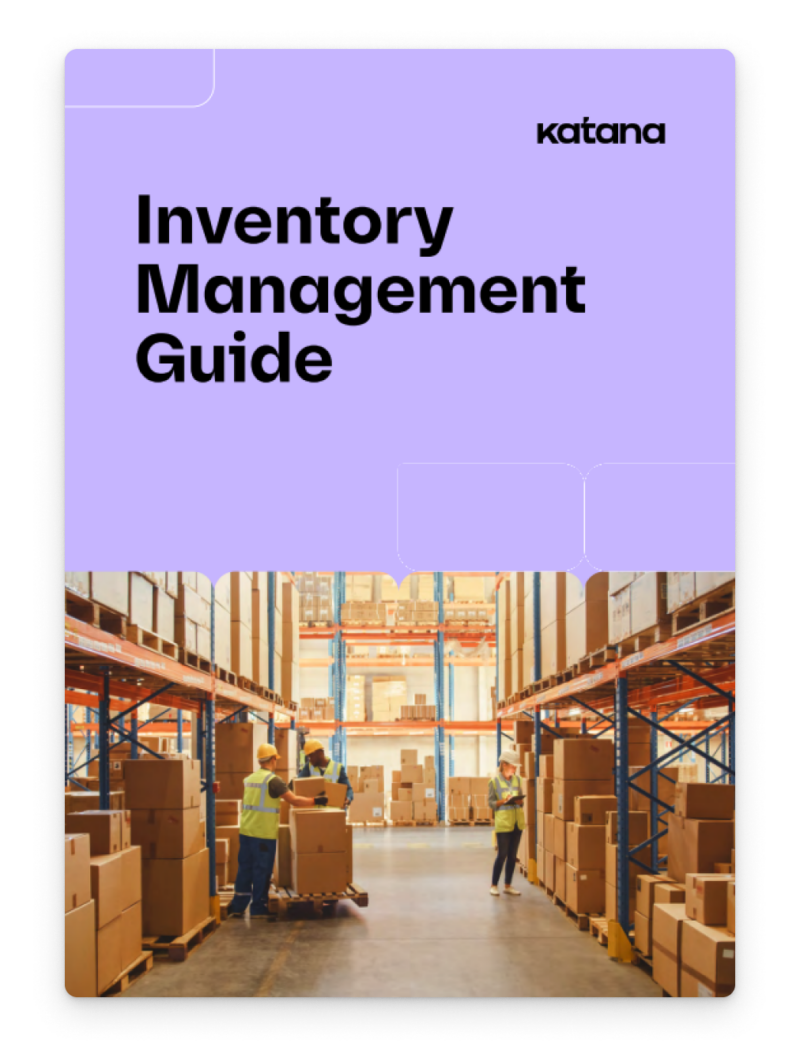
What are the methods of inventory management?
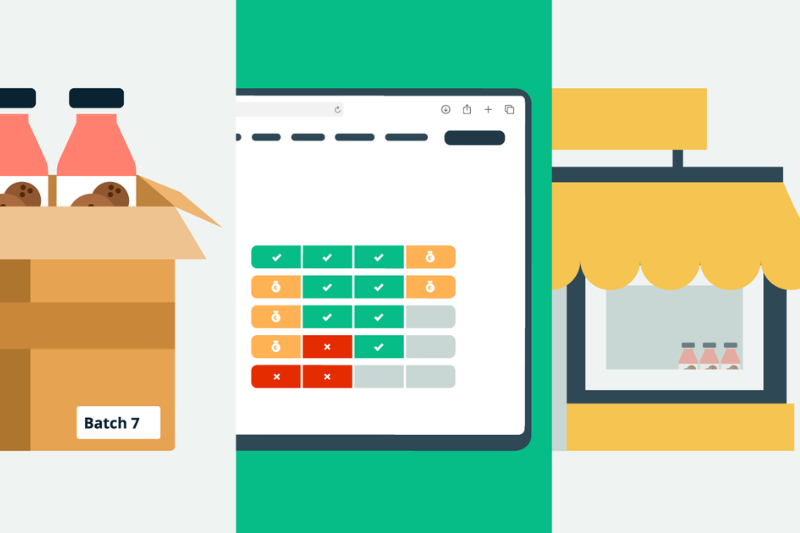
Modern methods of inventory management include tracking and managing stock levels to ensure businesses can meet customer demand. Businesses can use various methods to manage their inventory, such as:
- FIFO — first in, first out
- LIFO — last-in, first-out
- JIT — just-in-time
- Economic order quantity
- Average costing
- Cycle counting
- ABC analysis
- Perpetual inventory system
Each method has its own pros and cons, so it’s important to choose the right one for your business based on your specific needs.
Choosing the right method for your business will depend on various factors, including the type of products you sell, your customer demand, and your budget.
Inventory management is an important part of running a successful business. Using the right tools and techniques of inventory management can minimize carrying costs, reduce waste, and increase efficiency.
8 inventory management techniques
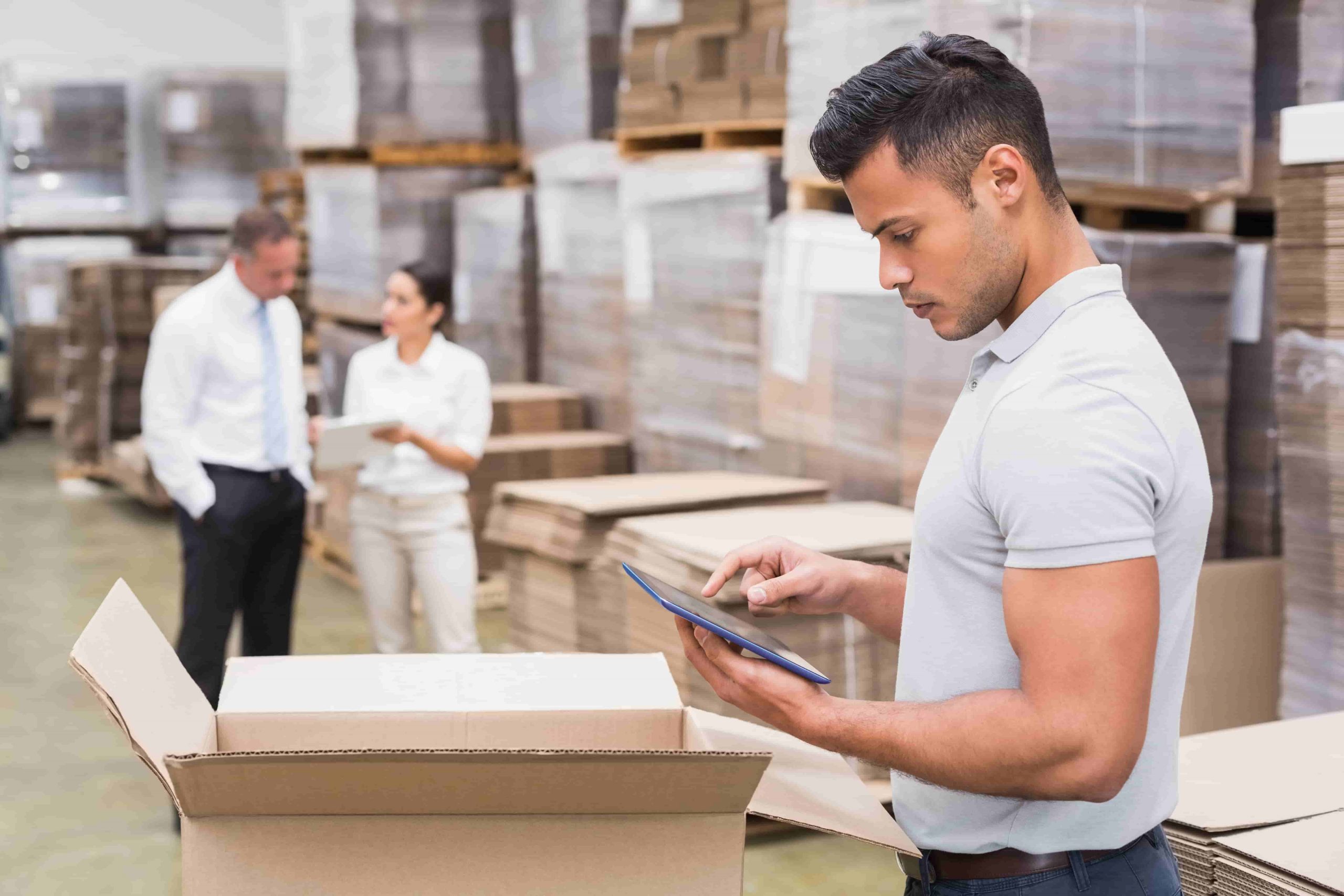
Now that you know everything there is to know about handling stock in general, here are eight inventory management methods to get you started.
1. FIFO — first in, first out
FIFO is one of the most common inventory management methods used in stock operations.
This technique helps ensure that the oldest products are used first, reducing the chance of spoilage or obsolescence. FIFO is an inventory valuation method in which assets are sold, used, or disposed of in the order in which they are acquired.
This method is often used for accounting purposes, providing a more accurate picture of an organization’s inventory levels and costs.
2. LIFO — last-in, first-out
LIFO (last-in, first-out) is one method used to calculate the cost of inventory for the cost of goods sold.
As the name suggests, the LIFO inventory valuation method sees that the last items placed into inventory are sold first. This results in higher costs being assigned to goods sold in periods of inflation because the most recent purchases have been made at the highest prices. LIFO can lead to lower taxes because the IRS allows businesses to deduct the higher costs of inventory from their taxable income.
Pro tip: Undecided about which is best for you? This article on FIFO vs. LIFO will help clear up any confusion.
3. JIT — just-in-time
Just-in-time (JIT) inventory is a system where businesses only order enough stock to meet current customer demand.
This system minimizes holding costs and ensures that businesses always have the products they need on hand.
JIT is a system where businesses align their supply orders with sales planning. By ordering stock only as needed to meet demand, sellers can minimize the costs associated with holding excess inventory. This approach allows them to enhance efficiency and profitability by ensuring that the right products are always available at the right time without overstocking.
However, this technique can be difficult to implement and maintain.
Pro tip: JIT can be unreliable as it’s susceptible to supply chain disruptions. Be sure to equip your business with purchase order management software to help you mitigate any unforeseen emergencies.
4. Economic order quantity (EOQ)
Economic Order Quantity (EOQ) models help businesses determine the optimal order quantity for their inventory.
This method considers various expense factors, such as holding and ordering, to help businesses find the most cost-effective way to manage their stock levels. The EOQ is the optimal order quantity for a company to minimize its total costs related to ordering, receiving, and holding inventory. The EOQ model considers the trade-off between the cost of ordering inventory and the cost of carrying inventory.
There are a few different ways to calculate EOQ, but the most common is the EOQ formula developed by economist Harold A. Hotelling in 1931. This formula is:
Q = √[2(DK/H)]
Where:
Q = The optimal order quantity
D = Annual demand
K = Ordering costs
H = Carrying costs
Get live inventory management tools
Katana seamlessly integrates with your favorite business tools to give you the features necessary to manage your inventory, sales, and production all from one screen. Get started now.
5. Average costing
To use the average cost or weighted-average method, a business assigns a cost to items in inventory based on the total cost of goods acquired in a period, divided by the total number of items:
Average cost formula = Total cost of purchases / Number of units purchased
Under this method, each unit in stock is assigned a cost equal to the average of all costs incurred to acquire the units available for sale.
The average cost per unit is computed periodically, usually at the end of each accounting period — and all units in inventory are then valued at this average cost.
Pro tip: Some cloud solutions on the market automatically calculate the average inventory in your business. Such as Katana, which uses the moving average cost.
6. Cycle counting
With cycle counting, inventory checks and balances are confirmed with physical inventory counts to match records.
To do this, businesses need to perform regular stocktakes and record adjustments of specific products. Cycle counting has many benefits, including reducing the need for annual or quarterly inventory counts, catching errors and discrepancies early, and providing accurate data for decision-making purposes. In addition, cycle counting can help identify areas where processes need to be improved to prevent future mistakes.
When done correctly, cycle counting can be an extremely helpful tool for managing inventory.
7. ABC analysis
ABC analysis, or ABC inventory management, determines the value of your inventory based on the item’s importance.
ABC ranks items based on demand, cost, and risks and groups items into classes.
ABC analysis can be used to decide which inventory items to stock, how much to stock, and when to order more.
The hierarchy of ABC inventory:
- A — High-value items are in high demand and have a high cost
- B — Medium-value items are in moderate demand and have a moderate cost
- C — Low-value items are in low demand and have a low cost
8. Perpetual inventory system
Perpetual inventory systems, or live inventory management software, automatically record sales, purchasing, and inventory usage through computerized POS systems or ERP software.
This system provides businesses with up-to-date information on their inventory levels, allowing them to make more informed decisions about ordering and selling products.
Perpetual inventory systems can be implemented in several ways, depending on the needs of the business. For example, some businesses may choose to install point-of-sale systems in all of their retail locations, while others may only implement them in certain locations or for certain types of products. Enterprise asset management software can also be used to track and manage inventory levels across multiple locations.
Perpetual inventory systems offer many benefits over traditional tools and techniques of inventory management. Perhaps the most important benefit is that they provide real-time information on inventory levels, which can help businesses avoid stockouts and lost sales. Additionally, perpetual inventory systems can help businesses reduce overall inventory costs by improving visibility into stock levels and turnover rates.
If you are considering implementing a perpetual inventory system in your business, there are a few things to keep in mind:
- You will need to determine what type of system will best meet your needs
- You will need to choose the right software and hardware for your implementation
- You will need to train your employees on how to use the new system
A perpetual inventory system can be a valuable tool for any business with careful planning and execution.
Inventory management is a critical part of business operations. These eight methods can help you optimize your inventory control and reduce waste. Choose the method that best fits your specific needs and start improving your efficiency.
Katana cloud inventory software
Katana is a perpetual system that performs these cost calculations automatically, so you can focus on growing your business. Sign up for a free demo call with our team and see what else is possible.
Inventory management methods for manufacturers
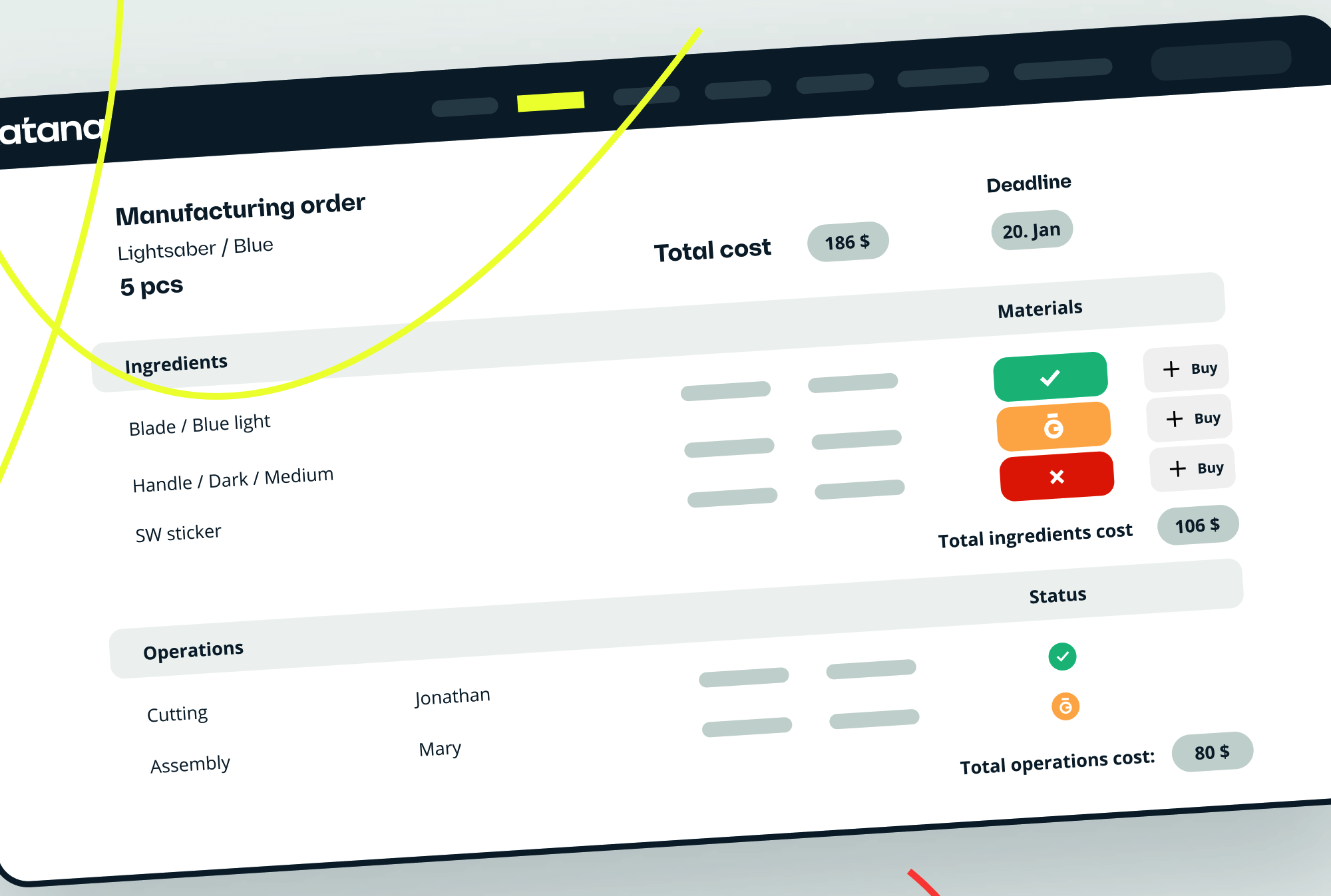
Inventory management is a cornerstone of production efficiency, directly impacting manufacturing flow, cost management, and customer satisfaction.
As businesses strive to streamline operations and reduce waste, adopting effective inventory management techniques becomes essential. Here’s how the mentioned methods can enhance stock efficiency and production precision.
1. First in, first out
FIFO is particularly beneficial in manufacturing environments where product freshness and expiry date tracking are a concern. This method ensures that materials or products acquired first are used or sold first, reducing the risk of spoilage and outdated stock.
It’s essential to maintaining quality and minimizing losses, especially in industries with rapid innovation cycles, like the electronics and automotive industry or perishable goods, such as food or cosmetics.
2. Last in, first out
While LIFO is less common in manufacturing due to its risk of older stock being left unused, it can be advantageous for certain types of products or materials that do not degrade over time. In periods of rising prices, LIFO can reduce taxable income, as the cost of goods sold is calculated based on the most recently acquired inventory, which is typically more expensive.
This method can be used in the petroleum and oil refining sector, where the prices fluctuate all the time.
3. Just-in-time inventory
JIT minimizes inventory holding costs by aligning material orders with production schedules. This method requires precise planning and a reliable supply chain. By reducing the inventory on hand to only what is necessary for immediate production, manufacturers can significantly decrease waste and increase efficiency. However, JIT demands resilience against supply chain disruptions to avoid production halts.
The most common users of the JIT method are in the automotive industry, specifically Toyota, who thereby has reduced manufacturing waste, cut down on manufacturing and inventory costs, increased efficiency, and improved its production quality.
4. Economic order quantity
In manufacturing, the EOQ model is critical for optimizing the procurement of raw materials and the production of goods to meet demand efficiently while minimizing costs. The EOQ formula helps manufacturers determine the most cost-effective quantity of inventory to order and produce, balancing between the costs associated with inventory ordering and holding.
With the high prices of raw ingredients, the need for controlled storage conditions, and production usually happening in larger batches, pharmaceutical companies have found EOQ to minimize their costs.
5. Average costing
Average costing is used by manufacturers to allocate the cost of goods sold and ending inventory. It smooths out price fluctuations of components and raw ingredients over time by averaging the costs of all items in inventory, regardless of purchase date.
This method can be particularly useful in industries where item costs vary due to factors like raw material price changes, currency fluctuations, or supply chain variations, such as chemicals or textiles.
6. Cycle counting
Cycle counting is a flexible and efficient approach to inventory management in manufacturing, allowing companies to maintain accurate records of components and finished goods, and improve production efficiency without the need for disruptive, full-scale physical inventories.
For industries with strict regulatory requirements, such as food and beverage, cycle counting can help ensure regular compliance with inventory tracking and management regulations.
7. ABC analysis
Manufacturers use ABC analysis to prioritize inventory based on the components’ impact on the production process and the final product cost. This method helps in identifying critical components (A items) that require more precise supplier management and might benefit from safety stock, whereas C items can be managed with leaner inventory strategies. For manufacturers, the A items are top priority, meaning that the components and materials required to complete and produce these are also more focused on in inventory management operations.
In the aerospace industry, manufacturers like Boeing or Airbus manage a variety of components ranging from highly expensive engine parts (A items) to moderately priced avionics (B items) and low-cost fasteners (C items).
8. Perpetual inventory system
The perpetual inventory system in manufacturing provides real-time, continuous tracking of all inventory types, including raw materials, work-in-progress (WIP), and finished goods. It integrates closely with production planning and procurement processes to ensure timely replenishment of materials, aiding in efficient production flow.
By carefully selecting and implementing these inventory management methods, manufacturers can achieve greater operational efficiency, cost reduction, and customer satisfaction. The choice of method depends on the specific needs and context of the production operation, including the nature of the goods, work processes, and market dynamics. With the right approach, manufacturers can turn inventory management into a strategic asset, driving competitive advantage and business success.
Katana cloud inventory software for optimizing inventory management
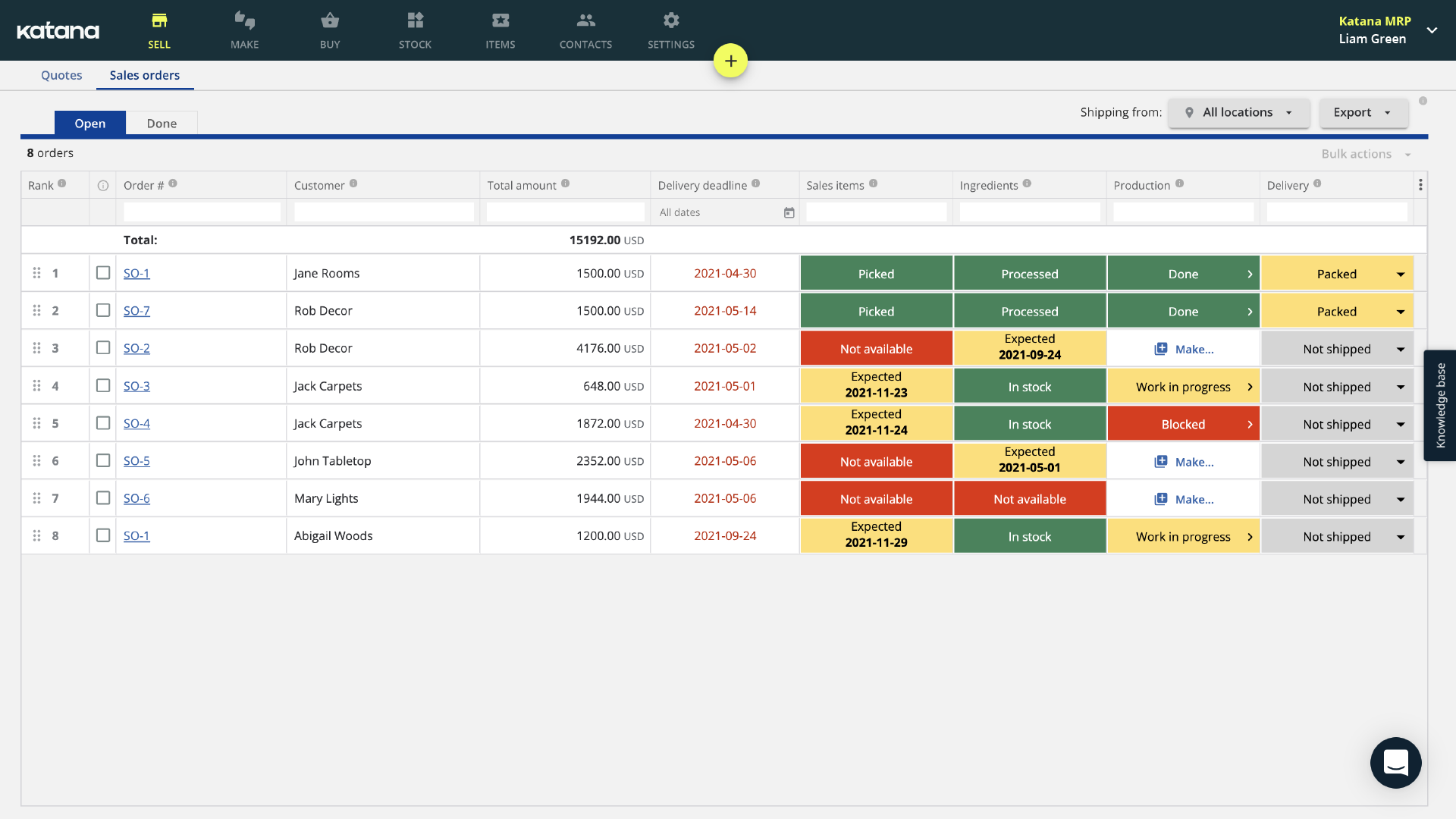
From your shop floor or Timbuktu — if a problem arises, you can easily access your inventory from anywhere with Katana Cloud Inventory, a cloud-based perpetual inventory system.
Running low on raw materials? Or maybe one of your sales locations needs more inventory to fulfill orders? Simply log into Katana and make purchase orders or perform stock adjustments from anywhere. You just need to be connected to the internet.
Complete inventory overview at your fingertips.
Katana makes stock taking a breeze, saving you time and money with:
- Reorder point management
- Real-time overview of inventory movement and operations progress
- Integrations with your favorite e-commerce and accounting software
- Omnichannel sales and location management
- A smooth, stress-free workflow from purchasing and sales to manufacturing and more
Want to see it for yourself? Reach out to our sales team and request a demo today to see how you can optimize your inventory management techniques with the power of automation.
So, now you know all about the modern methods of inventory management, you can take your business to the next level.
And until next time, happy inventory management.
Table of contents
Inventory management guide
More on inventory methods
Get visibility over your sales and stock
Wave goodbye to uncertainty by using Katana Cloud Inventory for total inventory control
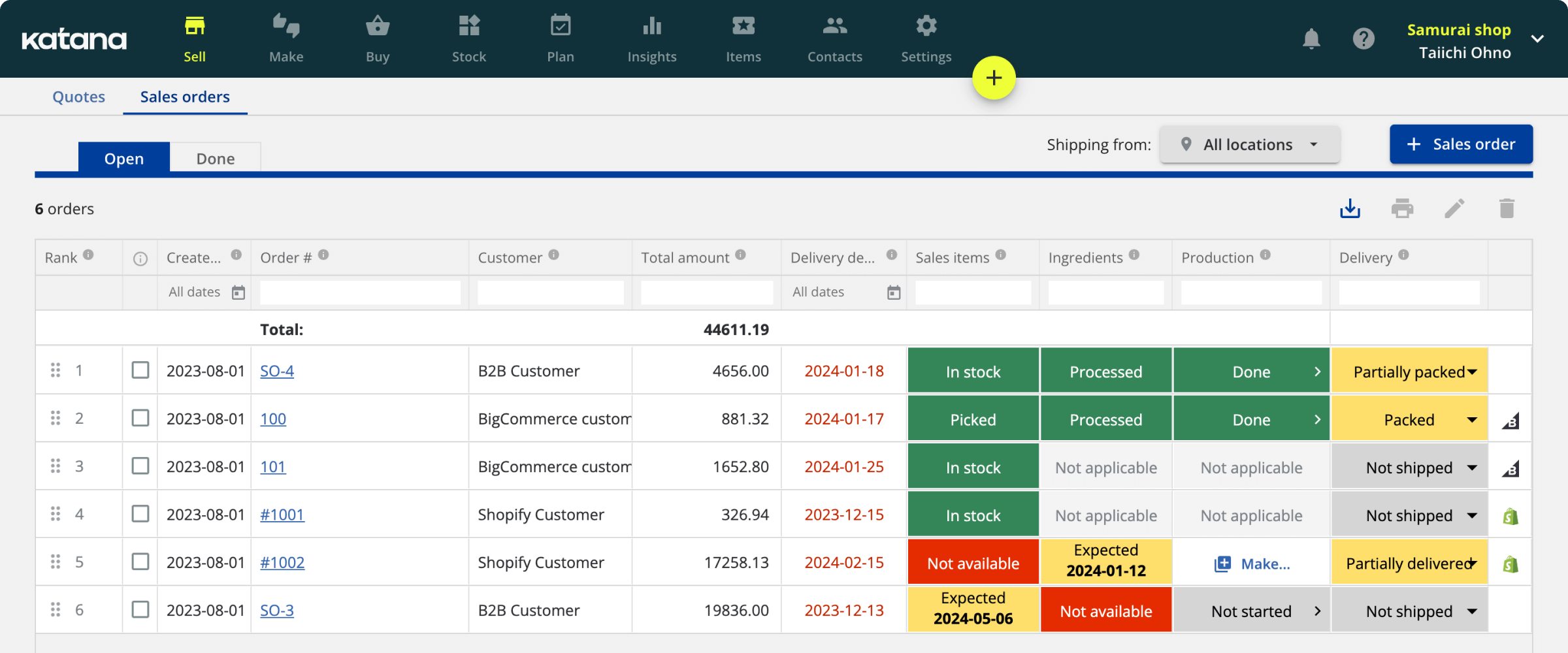