Your complete guide to raw materials inventory management
As companies are increasingly driven by technology and innovation, the importance of raw materials often remains overlooked.
However, these fundamental elements form the backbone of various industries, from construction and manufacturing to technology and renewable energy. Raw materials, whether mined from the earth or harvested from nature, are the starting point for almost everything we use in our daily lives.
Maintaining an efficient and effective inventory of raw materials is vital for the smooth operation of any business.
This article explores the strategies and best practices for managing raw materials, from procurement to storage. It discusses how to balance cost with demand, minimize waste, and optimize the supply chain.
Whether you’re a small business owner or a manager in a large corporation, you’ll find actionable insights to help you streamline your inventory process, reduce costs, and boost overall productivity.
So, let’s get started on how to master the art of raw material inventory management.
What is raw materials inventory?
Raw materials inventory is the total cost of a manufacturer’s components, subassemblies, and supplies in stock that are not currently in production. There are two types of raw materials that go into making a final product:
- Direct materials (DM)
- Indirect materials (IM)
Direct materials
Direct materials are the components that are part of your final product. For example, direct materials are:
- Leather used to manufacture leather bags
- Wood used to manufacture furniture
- Copper used to manufacture electronics
Indirect materials
Indirect materials are the components that are not part of your final product but are used during the manufacturing process. Examples of indirect materials are:
- Glue
- Oil
- Cleaning supplies
- Disposable tools
- Light bulbs
Get the ultimate guide to inventory management
A comprehensive ebook that covers everything you need to know about inventory management.
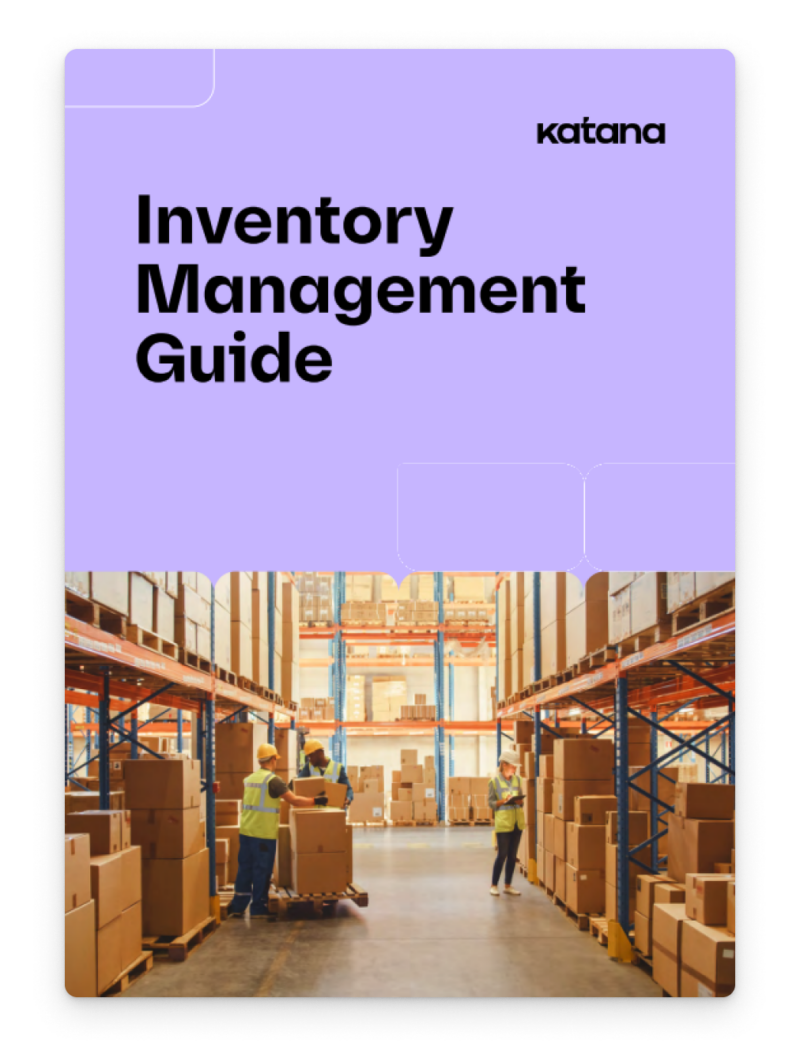
Why is raw material inventory management important?
Raw material inventory management is the process you or your managers will follow to ensure enough stock on hand, from direct materials to indirect materials, to keep production moving.
As your orders increase, you may order a ton of extra materials, assuming that the more safety stock you have, the better.
Well, imagine your raw material inventory was raw produce in a supermarket. Stocking up to last until next Christmas could be a bad move since perishable goods could expire. Even if your inventory never expires, holding too much of it will ultimately increase your carrying costs. This won’t be a small error — something like this could spell the end for your business.
Without a proper raw materials inventory plan in place, you will drive up your manufacturing costs for no good reason.
Your raw materials may not spoil like supermarket produce, but the result of keeping large amounts of raw material stock around is the same. That’s why it’s important to understand your raw materials’ value and customer demand.
How bad is it really to let inventory manage itself?
According to Celect and Coresight Research, retailers lost $300 billion in revenues due to markdowns in 2018.
That’s a lot of cheddar.
Accounting for raw materials inventory
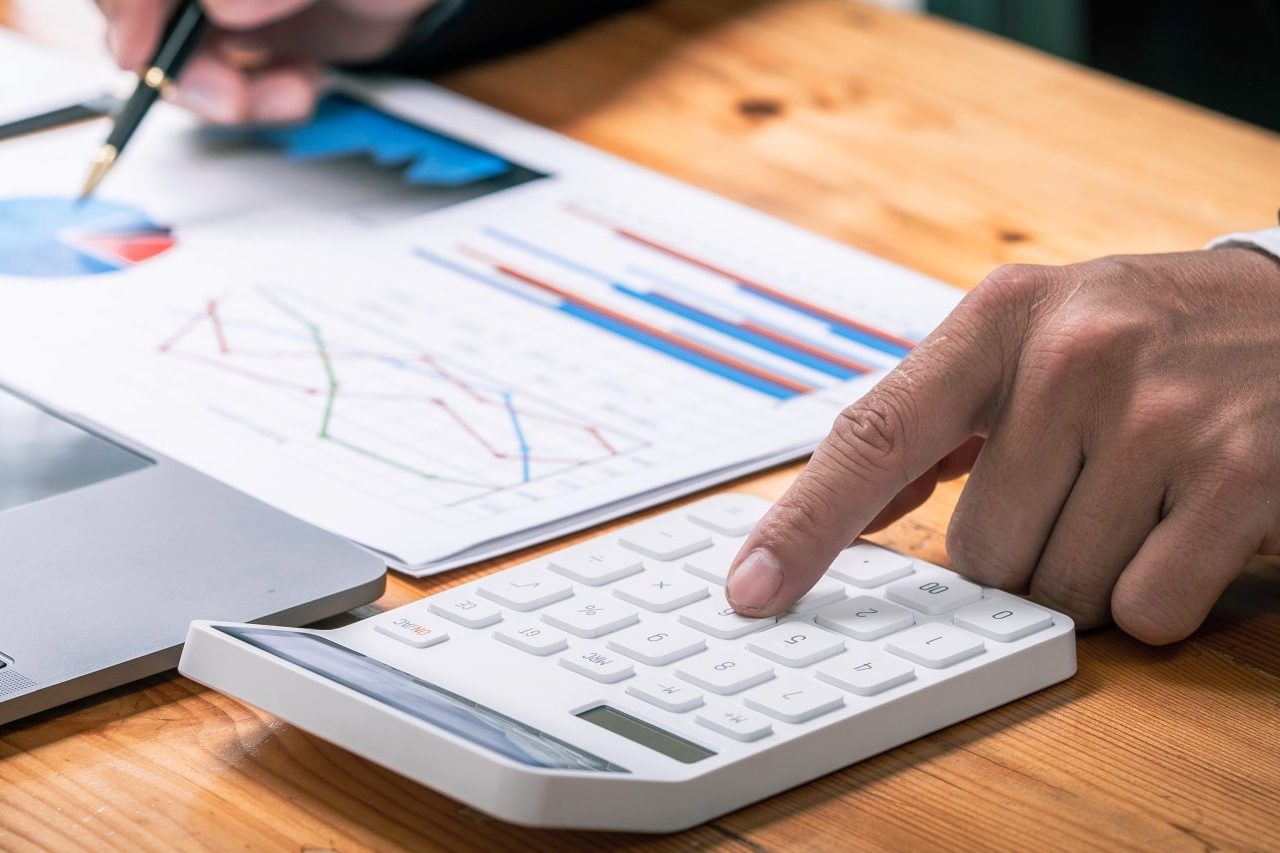
Managing raw materials inventory is crucial to effective supply chain and financial management. In manufacturing accounting, raw materials are considered a key asset for businesses. Accounting for raw materials inventory involves tracking and valuing the materials used in production.
One fundamental practice is the use of a perpetual inventory system. This system enables real-time tracking of raw material quantities and costs, accurately reflecting the current asset value. Regular reconciliations between physical inventory and accounting records help identify discrepancies and prevent errors in financial reporting.
The first-in, first-out (FIFO) and moving average cost methods are commonly employed for raw materials inventory accounting. Under the FIFO method, the assumption is that the initial materials procured are the first to be utilized in the production process. This approach aligns seamlessly with the flow of goods in manufacturing, ensuring that the value attributed to the inventory on the balance sheet accurately reflects the current cost of the materials in stock.
The moving average cost method calculates the average cost of the materials on hand, incorporating the costs of all units, whether newly acquired or previously in stock. The moving average cost provides a dynamic and continuously updated valuation of the raw materials, offering a more fluid reflection of their current value in the inventory.
Both FIFO and moving average cost methods contribute to effective inventory management and precise financial reporting.
Implementing these best practices in raw materials inventory accounting enhances financial accuracy and enables businesses to make informed decisions about production, procurement, and overall resource management.
Next, let’s take a look at some specific formulas for calculating your raw materials inventory.
How to calculate raw materials inventory value
Regardless of their factory floor size, businesses will need to account for their raw materials, business supplies, and finished products.
To do this, you’ll need to determine the ending inventory value at the end of each period. You need to add the number of units you manufactured and the raw materials you purchased during the period to the number of units at the beginning of a period. With that said, here is the raw materials inventory formula to help you calculate this:
Let’s imagine you’re a shoe manufacturer and want to account for the number of laces you have:
50 laces + 100 laces = 150 laces
Now, subtract that number from the amount of inventory you used during this period to calculate your ending inventory. You used 60 laces during production:
150 laces – 60 laces = 90 laces
Time to uncover the value of your remaining inventory. Simply multiply your remaining inventory by the cost of one unit of raw material:
90 laces x $1.50 = $135
And there you have it. The remaining raw materials inventory formula value comes in at $135.
A relatively easy raw materials inventory formula to follow when calculating the value of your raw materials. However, what about those of you who have different materials or even make products at different prices? It can be complicated to calculate the value for each different item.
In this instance, it’s best to use the weighted inventory method to evaluate your raw material value.
Try calculating your raw materials inventory value yourself following this formula:
Beginning raw materials inventory = (COGS + ending raw materials inventory) – raw materials inventory purchased
How to calculate the raw material value with weighted average costing
To calculate your raw material inventory value using weighted average costing, you just need to follow a simple formula. So, let’s imagine you sell two products, A and B:
- Product A costs $4 and sells at a rate of 80%
- Product B costs $2 and sells at a rate of 20%
The formula for this scenario will look like this:
($4 x 0.8) + ($2 x 0.2) = $3.60
If calculating the value yourself becomes too tedious, there are automated inventory management solutions available on the market. They will help you manage raw material inventory and automatically calculate your inventory costs.
How to calculate raw materials inventory turnover
The raw materials inventory turnover ratio is a measure of how efficiently a company uses its raw materials in the production process. To calculate it, you need two pieces of information:
- Cost of goods sold (COGS) — The total cost of all the raw materials used in production during a specific period. It includes the cost of materials that were actually transformed into finished goods.
- Average raw materials inventory — Calculated by adding the beginning inventory of raw materials to the ending inventory of raw materials and then dividing by two. This gives you an average inventory value over the period.
Once you know both of these values, you need the formula for calculating the raw materials inventory turnover:
Raw materials inventory turnover = COGS / average raw materials inventory
The result tells you how many times the company’s raw materials inventory is used and replaced over a given period. A higher turnover rate indicates efficient use of materials, while a lower rate might suggest overstocking or inefficiencies in the production process.
Best techniques for raw material inventory management
When you start to optimize your raw material inventory management, here are some tips and tricks to get you started on your journey.
Don’t obsess over work-in-progress inventory
Typically, companies start with finished product inventory tracking, implement basic raw material stock management, and more complex work-in-progress (WIP) management.
We strongly recommend not trying to jump to the latter immediately.
Although proper inventory management has great benefits, it also comes at a cost — it takes a lot of time and resources to track your WIP inventory. Thus, if possible, start with basic raw materials management and do not try to track different stages of production immediately.
Just take stock of your raw materials and finished products.
It’s better to have something simple working well than something complex that does not work at all. Keep everything lean and increase raw inventory management complexity only if there is a clear business need.
Update safety stock and reorder points
Safety stock describes the inventory a business keeps in the warehouse to protect against spikes in demand or shortages in supply.
A good reorder point ensures that your business typically does not dip below your safety stock levels. Most businesses employ some minimum inventory principles for raw materials used in production. Manufacturers often fail to calculate raw materials used regularly. As a result, these raw materials inventory levels become inconsistent.
All the events below should trigger an adjustment:
- A significant change in sales volume
- Major changes in supply lead times
- A change in production volumes
Also, don’t forget to adjust safety stock and reorder points to account for seasonal changes like an upcoming holiday season.
Keeping these levels up to date ensures you always have just the right amount of raw material inventory in your warehouse so that you won’t have too much cash tied up.
Don’t try to put all materials on your BOM
Having proper raw materials management in place does not mean you should track every material consumed in your production.
For example, several indirect materials could be consumed during the production process (nails, screws, buttons, and so on) that do not cost a lot and are typically purchased by the box in high volumes. It often makes sense not to have such materials on your bill of materials (BOM).
Instead, cost them at the time of purchase and do not try to track every piece consumed in production.
Getting the high-cost raw material stock in place on a BOM is important so you know early on if this is a profitable product. Don’t spend hours saving pennies. Focus on what has a greater effect on your margins.
Use industry-standard metrics to find out what works for you
Your business is unique, and what works for one business might not work for another.
The basic guiding principles of this are simplicity, directness, and freedom. There is no dogmatic loyalty to one technique. This is the key to overcoming any challenging situation for your business. Take what works and discard the rest.
The key for you is to use all the tools at your disposal to form your unique style of manufacturing. You can find the secret formula to your optimal raw materials inventory game.
Software for simplified tracking
Material requirements planning software available on the market gives manufacturers all the tools they need to get their raw materials under control.
How much energy needs to go into raw materials inventory management?
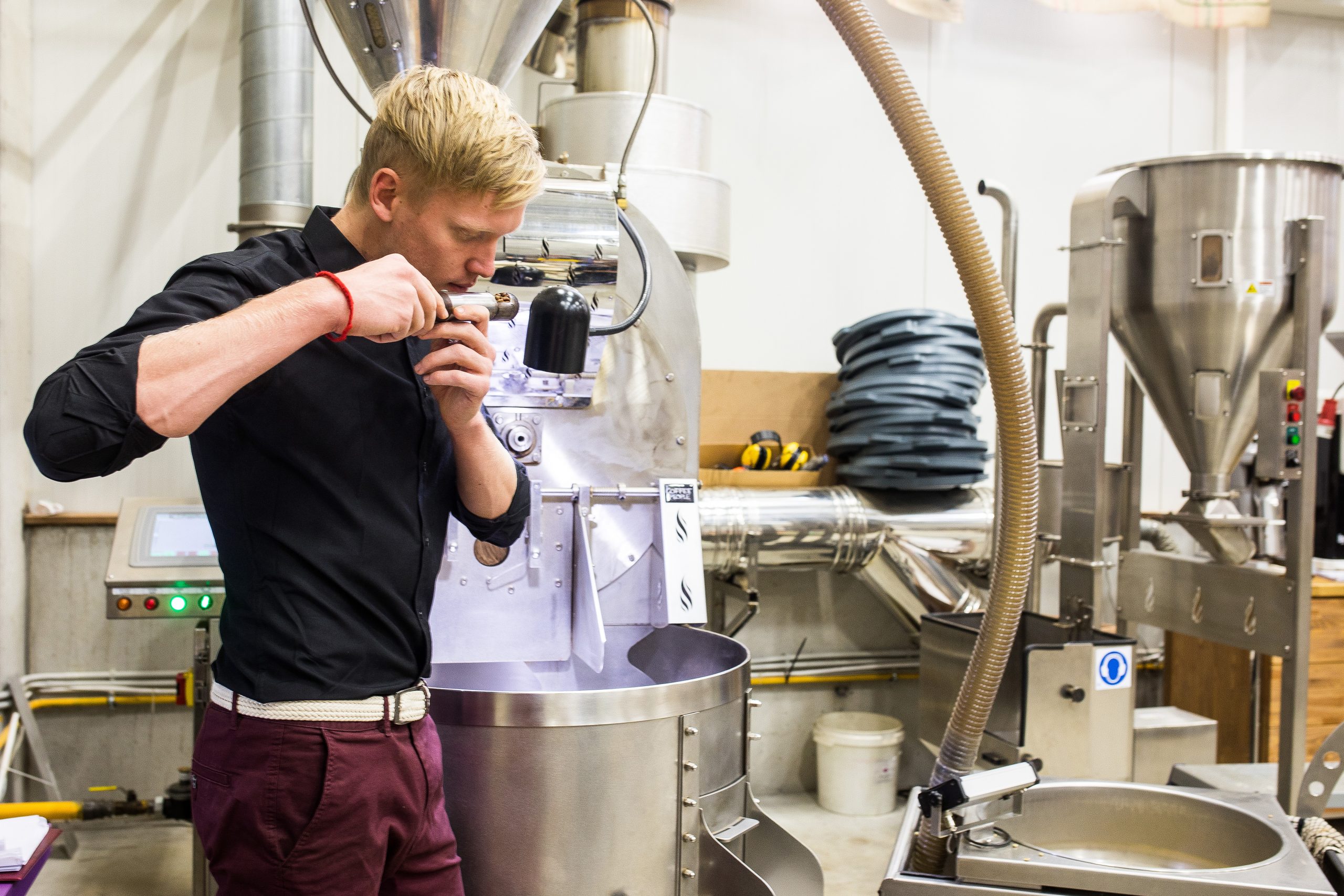
Have you heard of the Pareto Principle? The famous 80/20 rule is that 80% of the results come from 20% of the input. You could be working your socks off for 100 hours a week, but only 20 of those hours get the majority of your results.
What’s more, 20% of the stuff you learn about managing your raw materials inventory is used for 80% of your operations. And guess what? This 20% is the tried-and-tested fundamentals that go to the heart of inventory management. Get your foundation right, and the rest will follow. Most disciplines have a core set of principles to learn that will put you at the top of the game if you take the time to master them.
Are you spending too long on stocktaking, only to find mistakes still happen?
The perpetual inventory workflow could be a better solution for your inventory management. Calculate how much you pay to keep each square foot of stock monthly. You could adopt the principles of just-in-time (JIT) inventory.
We recommend you don’t go for 100% JIT at this stage.
Find out what raw material stock you have lying around the longest and ask yourself, “Why does this need to be here?” Your inventory turnover ratio (IRT) should be increased by keeping less stock. There’s no need to keep raw materials hanging around for months on end.
If your IRT is low, you could lose a good deal of money each month on carrying costs.
Are your costs overtaking your income?
Figure out your cost of goods sold (COGS) and calculate how raw materials used in production affect your bottom line. Spreadsheets are fine for calculating turnover. But this doesn’t take into account every cost you have.
Dedicated inventory management software helps you calculate your actual profitability, covering every aspect of your business.
Why raw materials inventory management is vital for manufacturers?
Imagine you were going on a round-the-world trip.
You could take two large suitcases filled with clothes for every weather condition. You might think you’re smart because you’re prepared for anything, but in reality, it’ll weigh you down and cost more to transport.
Contrast this to a single backpack:
- You save money on baggage fees
- You can run for a bus at short notice
- It makes it easier to hitchhike
Bringing two suitcases seems less risky, but the movement is slower and is less effective overall.
The second option is the road to success:
- You haven’t put all your eggs in one basket
- You can change direction at a moment’s notice
- Take a route that makes the most sense without disrupting plans
This type of thinking goes for keeping extra raw material inventory lying around.
Broadly speaking, as a manufacturer, you handle four different types of inventories:
- Raw materials inventory
- Work-in-progress
- Finished products
- MRO inventory
The average time a business focuses on each type of inventory changes at different stages in the business’ life.
During the startup stage, companies tend to focus more on finished products. This makes a lot of sense, as getting products to customers is the top priority. You have to make a name for yourself, and your product is everything.
As the business grows, the focus might be on manufacturing and inventory management efficiency. What was once barely a concern for the business owner becomes the number one thing on their mind.
It seems like inventory management is taking over their life.
The business owner might spend more time managing their raw material stock with little to show. More raw materials pile up, seemingly enough to last for unforeseen occurrences. This increases your inventory expenditure on your balance sheet.
Not to mention the number of hours lost tracking it all.
Before you know it, you are spending more than ever to sell a single unit of product. Your business is bigger. It may even be more profitable. But what are you doing it all for if your overheads are destroying a higher percentage of your income?
Material prices increased by 80.28% in 2022
Covid-19 led to inflation surging to 8%, resulting in supply increasing raw materials. Download the report and see how rising costs have affected different industries.
Overcoming challenges with raw materials inventory management
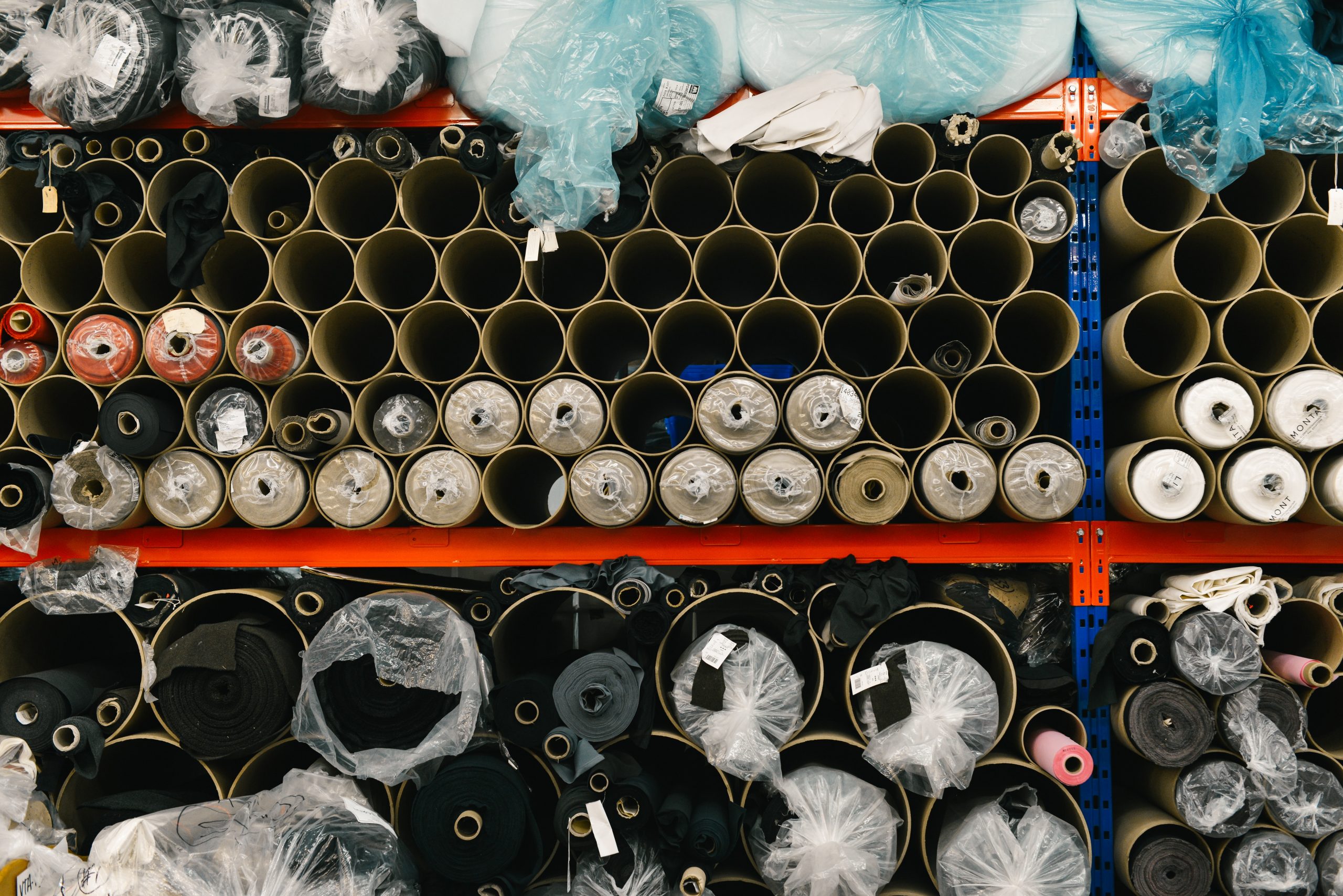
As you probably already gathered from this article, practicing solid raw material inventory management can be difficult.
So, before we move on to the best solution for handling your raw materials, here are some things you’ll need to consider when improving your raw material inventory management.
Planning and forecasting
Improving your raw material inventory management is one thing, but having a dynamic management system that considers your demand planning will help you maintain ideal inventory levels.
Data-driven management
Having the right amount of raw material stocked when needed is only possible by collecting data from your sales, production lines, and anywhere else on your supply chain. It is possible to do it with inefficient spreadsheets. However, it can be difficult to make constant manual updates.
Costing
You might know how to calculate the value of your raw materials, but that doesn’t mean you can accurately track how much it costs to manufacture your products.
Other costs you need to track include manufacturing overheads and labor used in production. Due to various factors, these costs often change (meaning items in your inventory don’t have the same value as others). Tracking these costs alone will be extremely time-consuming and difficult.
Many manufacturers turn to ERP manufacturing software to help automate and track their raw materials inventory.
Use raw material management software
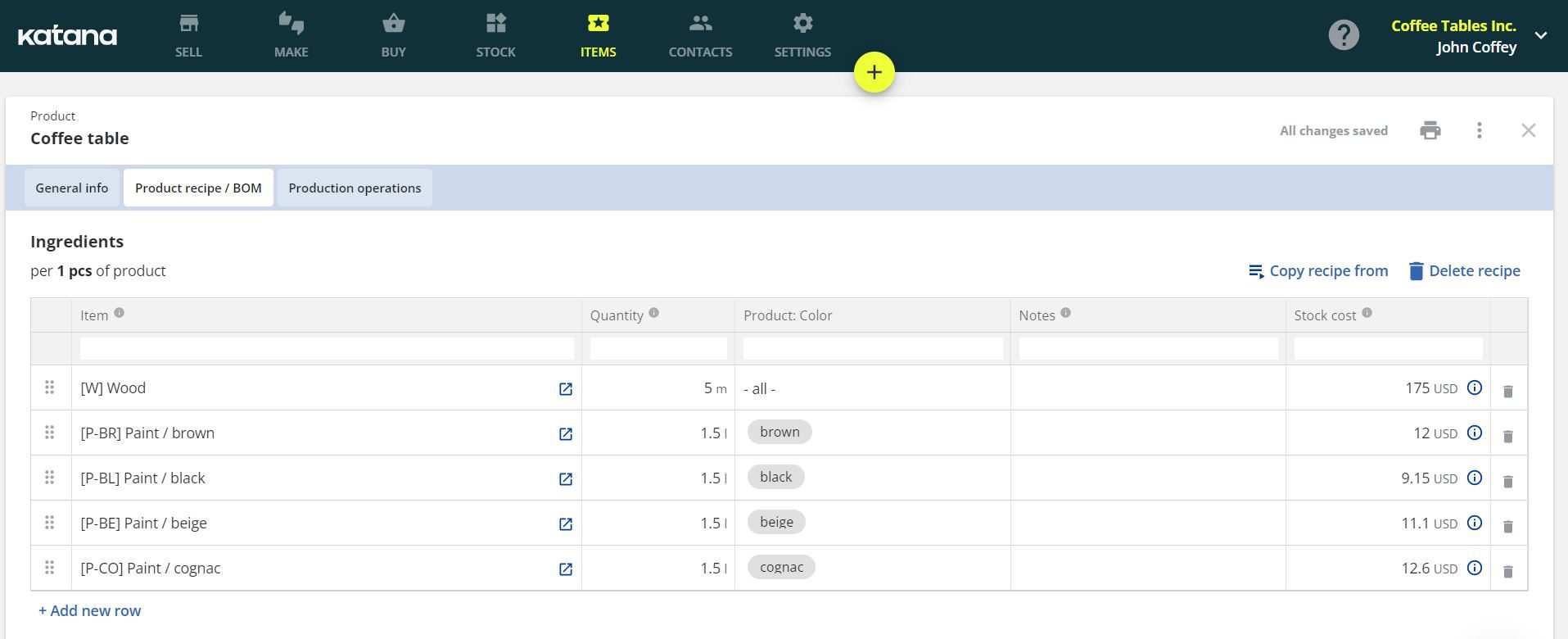
You could have the best managerial mind in the world.
Your industry knowledge could be second to none. But your business could still be dead in the water if you don’t have the right tools. Managing raw materials inventory in a scaling business without dedicated software will be an uphill battle.
A dedicated cloud inventory software like Katana can greatly boost your business’ growth by:
- Getting orders out the door and to the customer faster
- Calculating raw materials used for optimal reorder points
- Automating repetitive tasks so you aren’t bored out of your mind counting buttons
In addition, Katana makes it easy to:
- Manage your manufacturing processes
- Follow your production quality control checklist
- Integrate with your favorite business tools
- Manage your inventory in real time
- And much more
To see how you can easily track the costs of your materials and products, check out the video below.
Don’t let the cost of keeping raw material stock destroy your margins. Try out complete raw materials inventory management that lowers your costs.
Raw materials inventory FAQs
What is an example of a raw material inventory?
A raw material inventory refers to the stock of basic materials that a company holds, which are eventually processed into finished products. An example could be an automotive manufacturer holding a raw material inventory of metal, leather, and bolts. These materials are essential for the production process but have not yet been transformed into finished goods.
How do you record raw materials inventory?
Raw materials inventory is recorded in a company’s financial records as a current asset. When raw materials are purchased, they are recorded at their purchase cost. As materials are used in production, their cost is transferred to a work-in-progress inventory account, and subsequently to finished goods inventory once the manufacturing process is complete.
This process is often tracked using inventory management software or systems like perpetual or periodic inventory systems.
What are the types of raw materials?
Raw materials can be broadly classified into two categories:
- Direct materials — Materials that directly become part of the finished product and can be easily traced. For example, stones in jewelry inventory that are used for jewelry manufacturing or fabric in textile production.
- Indirect materials — Materials used in the production process but do not become part of the finished product. Examples include lubricants for machinery and cleaning supplies for factory equipment.
Do raw materials count as inventory?
Yes, raw materials do count as inventory. They are considered a type of inventory known as raw materials inventory, which is an essential component of a company’s total inventory. This inventory represents the first stage in the manufacturing process before materials are processed into work-in-progress and, finally, finished goods.
Table of contents
Inventory management guide
More content from Katana
Get visibility over your sales and stock
Wave goodbye to uncertainty with Katana Cloud Inventory — AI-powered for total inventory control