Good manufacturing practices to ensure constant high quality standards
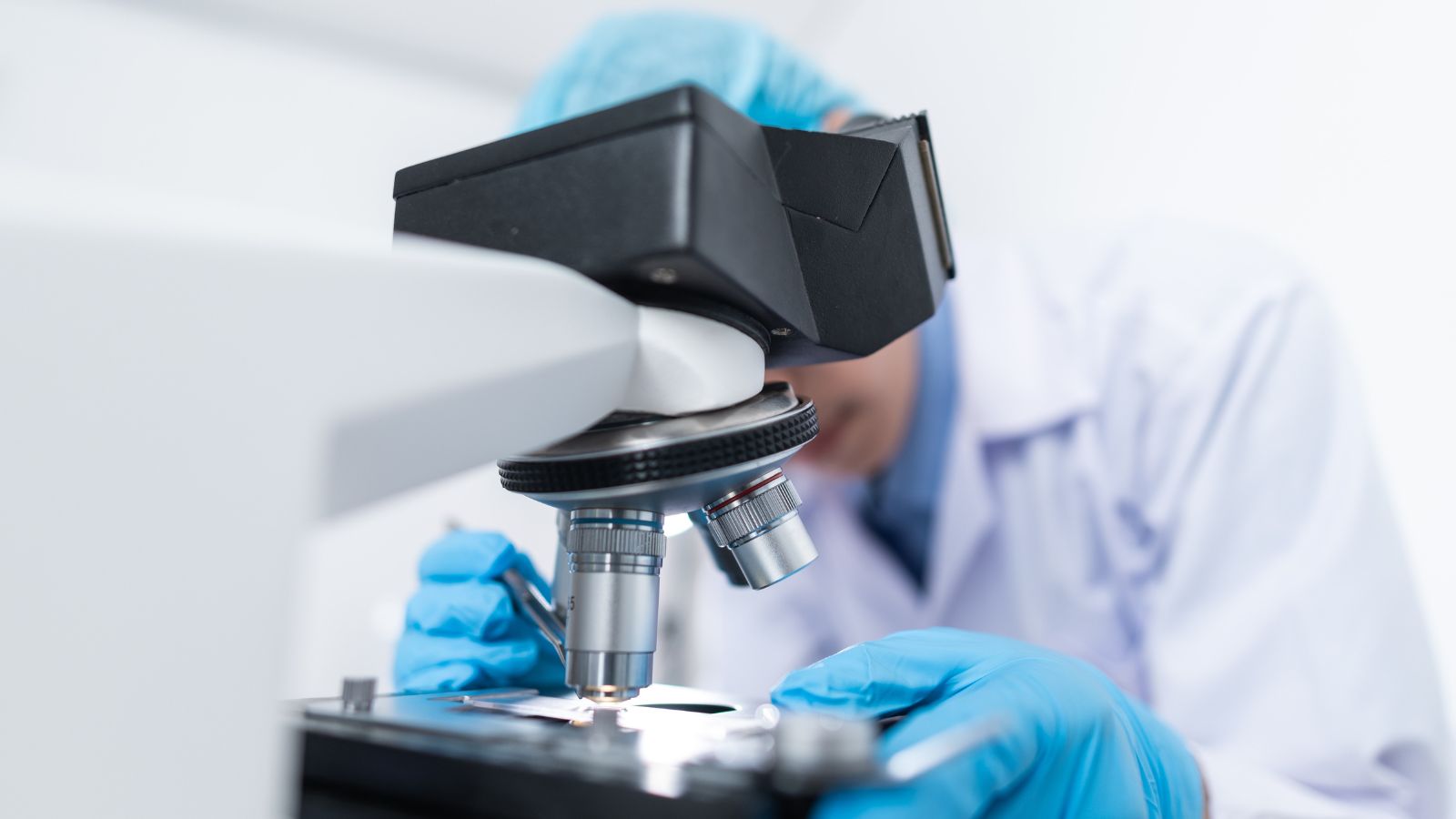
In 1968, WHO started working on the good manufacturing practices (GMP) draft document.
But what are good manufacturing practices, why do good manufacturing practices exist, and who is WHO? The World Health Organization (WHO) says that “good manufacturing practice is a system for ensuring that products are consistently produced and controlled according to quality standards.”
In this article, we will explore GMPs in-depth — what they are, why you need to know what they are, WHO’s involvement in all of this, and if you need to spend resources on implementing them.
What is GMP in manufacturing?
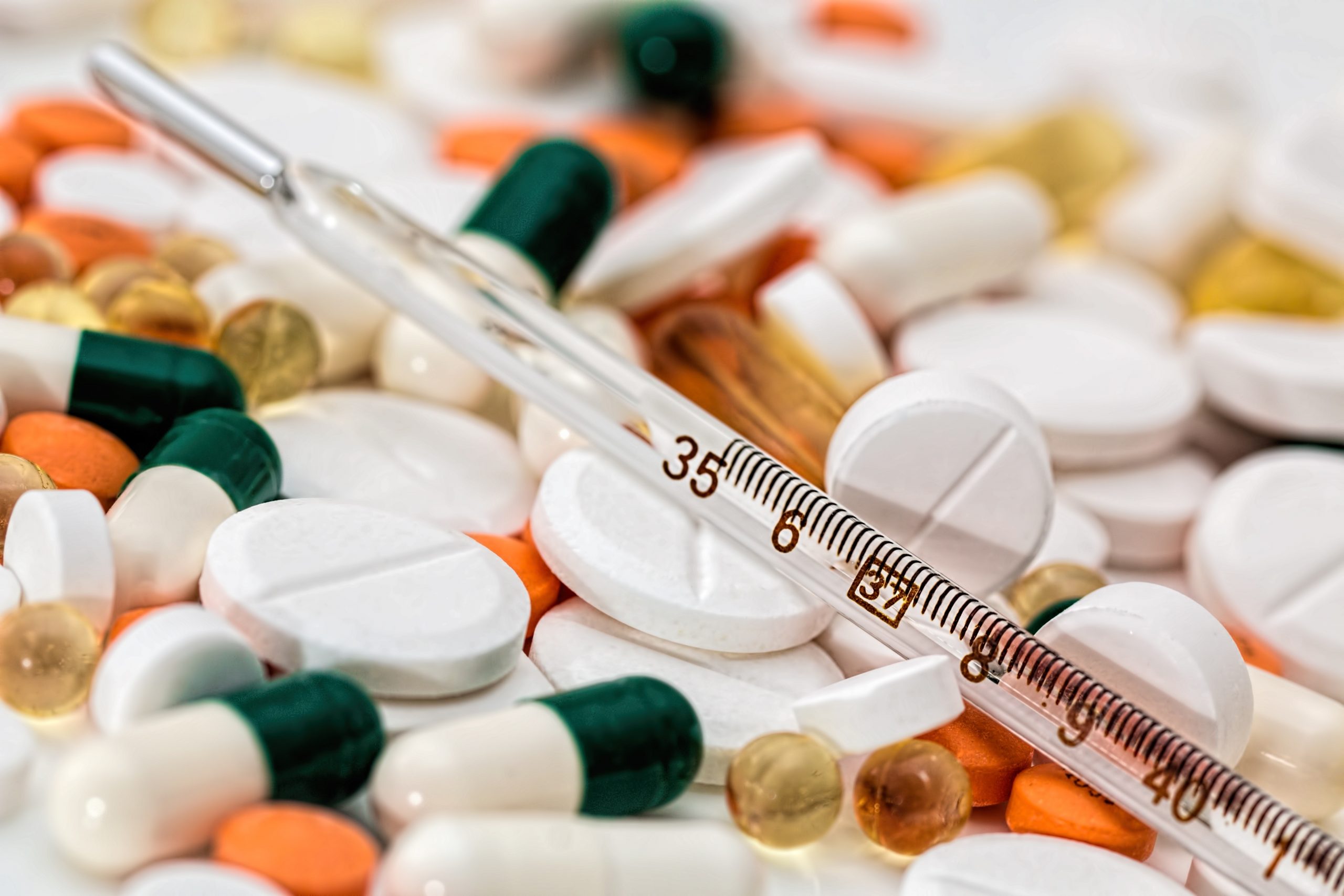
Good manufacturing practices (GMPs) are a set of guidelines that provide a framework for manufacturing processes and quality control procedures. GMPs are designed to ensure that products are safe, consistent, and effective.
WHO wrote the global definition of GMPs in the late 1960s to advise medical manufacturers on how to manufacture their products safely.
The quality of medicines is important not only for therapeutic effects but also to avoid harm. WHO’s GMP requirements help ensure that the quality of medicines is acceptable and safe for human use. WHO’s GMP covers every aspect of production, including raw materials, facilities, equipment, and the training and personal hygiene of staff.
GMPs are essential for ensuring the quality of medicine and certain other products that we’ll talk about a bit later.
They help ensure that medicines are safe for human use and meet the required quality standards. GMPs are based on a set of internationally recognized principles that provide guidance on how to manufacture medicines safely and effectively.
WHO itself does not enforce the GMP requirements but provides guidance and support to countries that wish to implement them.
When it comes to enforcing the requirements, WHO works closely with national authorities responsible for regulating medicines, like the US Food and Drug Administration (FDA).
Manage quality control and compliance tasks
Read how pharmaceutical manufacturing software helps you stay focused.
GMP for pharmaceuticals
The original GMP guidelines, published in 1968, were aimed at drug manufacturers. These guidelines have been revised several times over the years and are now widely used by manufacturers of pharmaceutical products all over the world.
Pharmaceuticals were originally defined as drugs that were used to treat or prevent disease. Today, the term also includes vaccines, blood products, antiallergenics, cell and gene therapies, etc.
The GMP requirements for pharmaceuticals are laid out in WHO’s “Quality assurance of pharmaceuticals: A compendium of guidelines and related materials”. This compendium provides guidance on all aspects of pharmaceutical quality assurance, from the starting materials used in production to the finished product.
GMP in the food industry
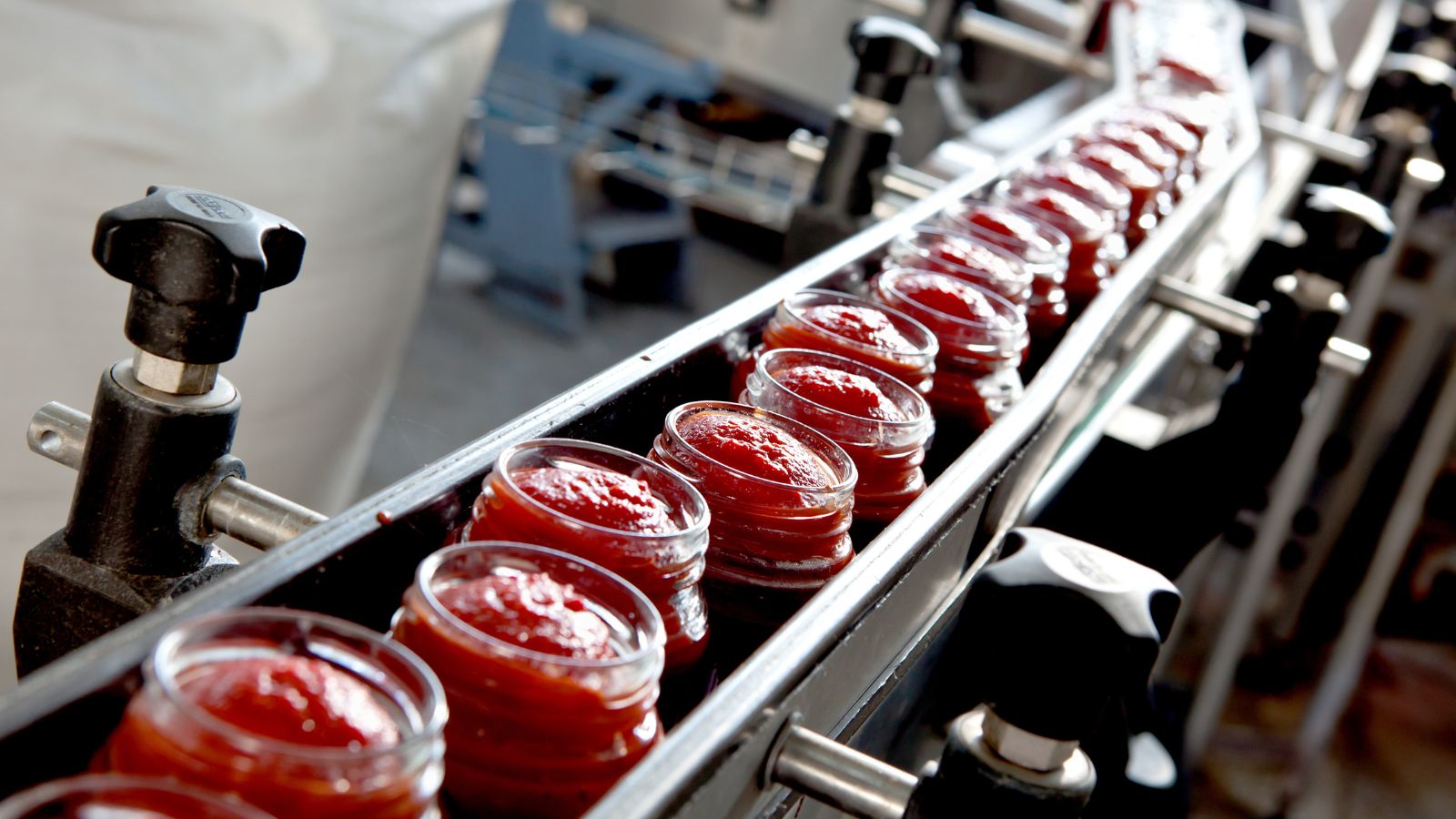
Besides the pharmaceutical industry, GMP also needs to be followed by the food industry.
The food industry is one of the most regulated industries in the world. In the United States, the Food and Drug Administration is responsible for regulating food products. The FDA has established a set of GMP regulations that apply to all aspects of food production, from farming and food processing to storage of food inventory and food distribution.
The FDA’s GMP regulations for the food industry are known as the Food Safety Modernization Act (FSMA).
The FSMA was enacted in 2011 in response to many reports of food-born illnesses, such as the 2007 recall of pet food contaminated with melamine. The FSMA requires food manufacturers to implement comprehensive quality control and food safety systems. These systems must be designed to prevent food contamination and address potential hazards at every stage of the food production process.
In addition to the FSMA, food manufacturers in the United States are also subject to GMP regulations from the U.S. Department of Agriculture (USDA).
The USDA’s GMP regulations are known as the Hazard Analysis and Critical Control Point (HACCP) system. The HACCP system is a preventative approach to food safety that focuses on identifying and controlling potential hazards throughout the food production process. Food manufacturers who wish to sell their products in the United States must implement a HACCP plan that meets the USDA’s requirements.
Why are GMPs important?
That’s a lot of rules and regulations that must be followed, but is that all really necessary?
GMPs are important because they help to ensure the quality of products that have the potential to cause significant harm if they are not effective or safe. They help ensure that these are safe for human use and meet the required quality standards.
GMPs also help to ensure that manufacturing processes are consistent and reproducible and that products are made to the same high standards every time.
The fall of Theranos
The infamous health technology company Theranos decided to blatantly ignore GMPs and is now paying the price for it. Had they implemented GMPs for their “revolutionary” rapid blood tests, they might have avoided bankruptcy and all the lawsuits.
Theranos had plenty of world-class scientists, business savants, and experienced health officials on their team, but the company’s leaders decided to ignore GMPs.
They decided to focus primarily on marketing and eventually shamed the health industry in general. Former CEO of Theranos, Elizabeth Holmes, faces up to 20 years in federal prison, plus potentially millions of dollars in compensations and fines, and is currently scheduled for sentencing on November 18th, 2022.
Difference between GMPs and cGMPs
When reading about GMPs, you may come across the initialism cGMPs. Let’s briefly look at the differences:
- GMPs — A set of principles that provide guidance on how to manufacture medicines safely and effectively
- cGMPs — A set of regulations that detail the specific requirements that must be met in order to comply with the GMP principles
In the United States, the FDA is responsible for enforcing cGMP regulations. These regulations must be followed by businesses in the regulated manufacturing industries like pharmaceutical, medical device, beverage, and food industries.
Now let’s take a look at the requirements for GMPs.
GMP requirements
The specific requirements for GMPs vary from country to country, but some common elements are usually included. These common elements are:
- Detailed, written procedures for each process that could affect the quality of the finished product
- Systems to provide documented evidence that correct procedures are consistently followed at each step in the manufacturing process
- Training and personal hygiene of staff
- Premises and equipment that are suitable for the manufacture of medicines
- Control of starting materials, packaging materials, and finished products
In order to ensure compliance with GMP requirements, manufacturers must establish quality control systems. These systems should cover all aspects of production, from the selection of starting materials to the finished product.
Quality control systems should include procedures for ensuring that all products meet the required quality standards. They should also include procedures for investigating and correcting any problems that arise during production.
GMPs are an important part of ensuring the quality of medicines. By following these principles, manufacturers can help to ensure that their products are safe and effective.
See how Katana can help you follow GMPs
Katana offers end-to-end traceability, which is essential for companies in highly regulated industries like food and pharmaceuticals.
Benefits of following GMPs
Following good manufacturing practices in your industry is an investment.
You can think of GMPs as an insurance process to avoid recalls, confiscated products, and even potential lawsuits. In addition, following these practices usually leads to increased product quality. This is due to the fact that when all members of your team are working with the same guidelines, it’s easier to avoid mistakes.
It can also lead to increased efficiency and even happier employees. After all, when people know what’s expected of them and they have the resources they need to do their jobs well, they’re more likely to be satisfied with their work.
Implementing good manufacturing practices at your company also diminishes the risk of adulteration.
Did you know? If a pharmaceutical manufacturer skips FDA’s current good manufacturing practice regulations, all their drugs are considered “adulterated”. This doesn’t mean that there is necessarily something wrong with the quality of the drug if it works as advertised.
FDA keeps a database of drugs that they approve, and they also have a database of companies that do not comply with GMPs. Non-compliant drug manufacturers should know that FDA will keep a closer eye on them and may sometimes conduct inspections if they have reason to believe that the drug manufacturing process is prone to mistakes.
Also, suppose a drug has too few active pharmaceutical ingredients. In that case, the FDA requests the company to recall the drug if the company has not done so already after receiving negative feedback. If a company refuses to recall a drug, FDA warns the public and seizes the drug.
There aren’t many manufacturers who march through product seizures without taking a hit to their reputation. Cutting corners with GMPs is a dangerous game of chess with regulatory agencies.
There are many benefits to following GMPs, but ultimately it comes down to protecting your company, your industry, and the general public.
Quality control for GMP manufacturing
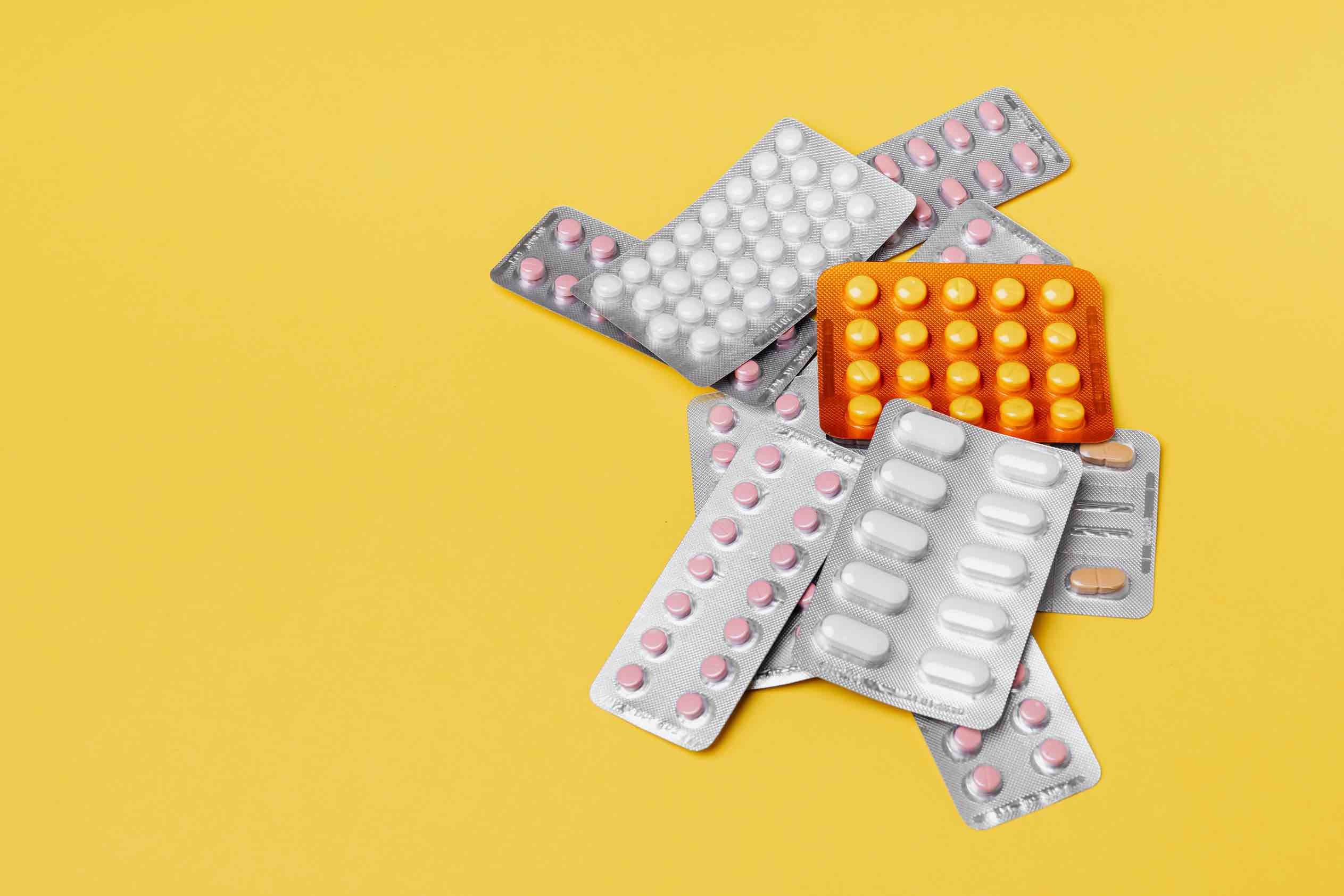
GMP guidelines require that finished products meet pre-determined specifications for quality.
In order to ensure compliance, manufacturers must establish quality control systems. These systems should cover all aspects of production, from the selection of starting materials to the finished product. Quality control systems should include procedures for ensuring that all products meet the required standards of quality.
They should also include procedures for investigating and correcting any problems that arise during production. In general, quality control systems should address four main elements:
- Product specifications — Should be based on market needs and customer requirements. They should be comprehensive enough to cover all aspects of quality that are important to customers
- Product testing — Essential for ensuring that products meet all the required specifications. Manufacturers should have procedures in place for testing raw materials, finished products, and in-process materials
- Product release — Should only be released for sale or distribution if they meet all the relevant quality specifications. Manufacturers must have procedures in place for approving products for release
- Corrective action — If a problem is found with a product, manufacturers should have procedures in place to take corrective action. These procedures should include steps for identifying the root cause of the problem and implementing corrective measures to prevent it from happening again
Manufacturing software to monitor all your production processes
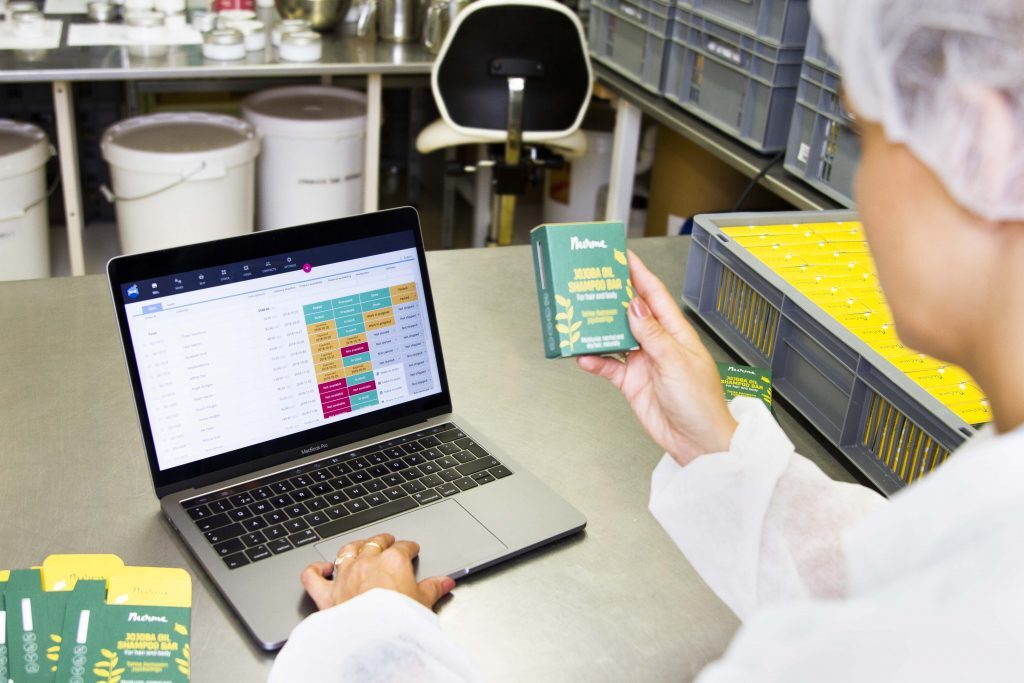
GMP guidelines and regulations address the following areas:
- Quality management
- Raw materials
- Equipment
- Manufacturing facilities
- Staff
- Documentation
- Qualification and certification
- Feedback both positive and negative
- Audits and inspections
Some old-school manufacturers use legacy systems and basic spreadsheets to collect data in these areas. However, you can do better by using modern manufacturing traceability software.
Katana ERP has essential features for manufacturers in the pharmaceutical industry and food and beverages industries, such as tracking expiration dates and barcode scanning.
You can track batches for products and materials by assigning batch numbers to items, giving you full traceability from purchasing raw materials to manufacturing and sales. Assigning expiry dates to batches gives you full control over the shelf life of your items.
Besides the built-in features, Katana also offers seamless integrations with the most popular business tools to ensure your data is kept up-to-date across all platforms.
With Katana, you can take your business to the next level with an intuitive manufacturing ERP that tracks every material, product, and order in one place. ERP gives you the tools to get a complete overview of your production processes and manufacturing facilities.
See Katana’s lot tracking software in action by booking a demo and see how it can help you follow GMPs effortlessly.
Table of contents
Manufacturing guide
More on manufacturing
Get visibility over your sales and stock
Wave goodbye to uncertainty by using Katana Cloud Inventory for total inventory control
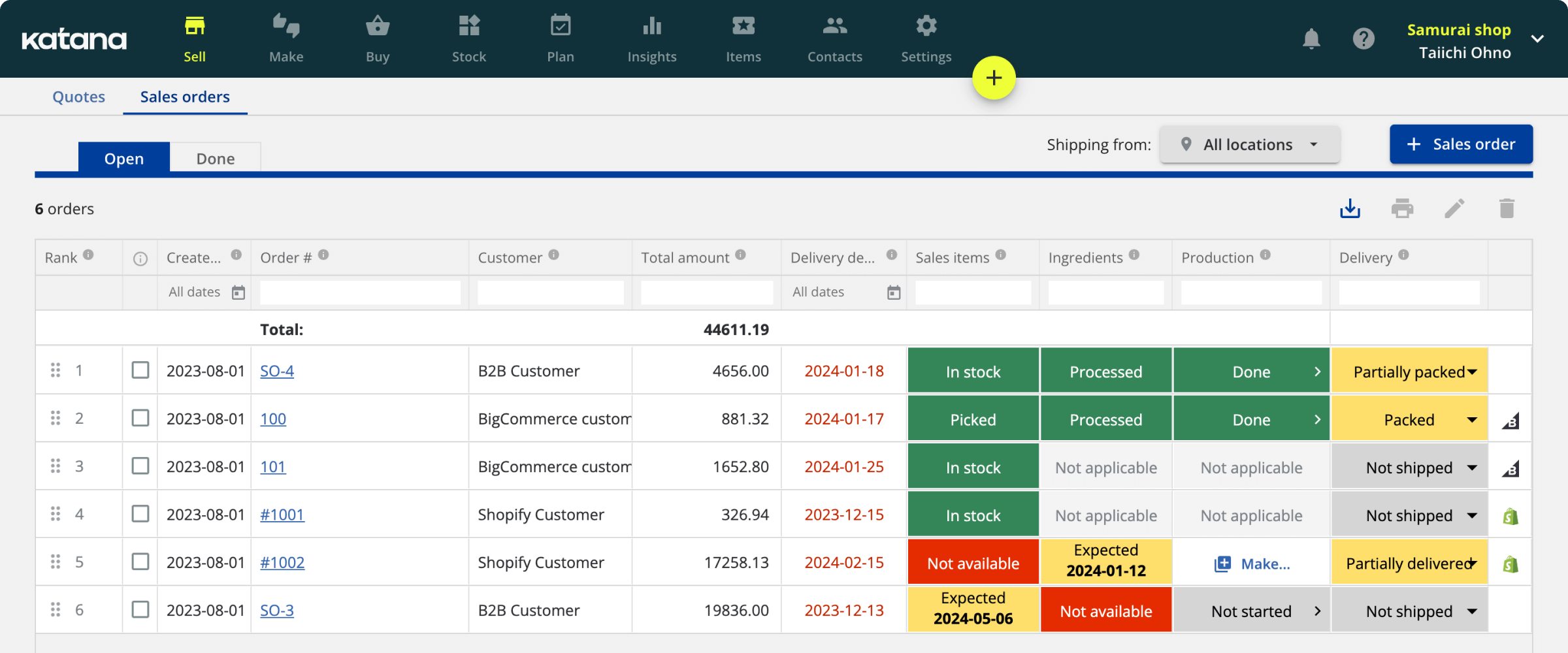