9 essential tips to reduce manufacturing waste
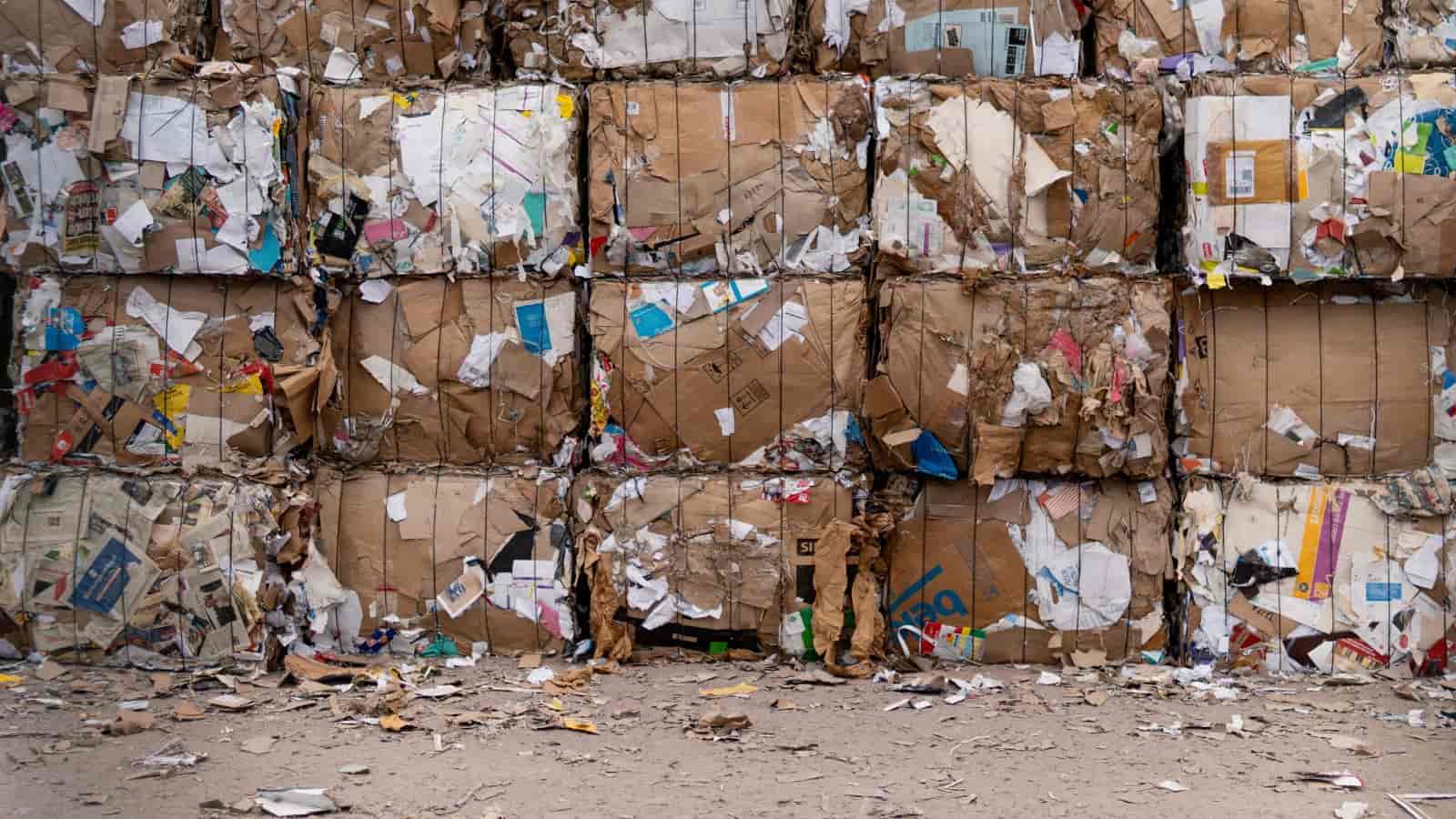
Manufacturing waste can mean different things in different industries. Regardless of specific definitions, reducing waste in manufacturing translates to higher efficiency. Fortunately, we have come a long way in understanding the different types of manufacturing waste and how to reduce it.
In this article, we’ll take a look at the different types of manufacturing waste, how to recognize it, and what strategies you can use to reduce it.
But first, let’s go over the basics and define what we mean by manufacturing waste.
What is manufacturing waste?
By one definition, manufacturing waste refers to any materials or resources discarded or not used in manufacturing. Some manufacturing waste examples include excess raw materials, scrap materials, broken or defective products, and energy or water used in production.
These types of waste can have negative environmental and economic impacts, and many manufacturers aim to reduce or eliminate waste to improve efficiency and sustainability.
With the introduction of lean manufacturing, the perception of manufacturing waste management changed significantly.
Lean principles encoded the idea of eliminating waste from the process of manufacturing. The lean manufacturing principles require you to define value and then classify your processes into two depending on whether they provide value to your business and customers. This process allows you to identify and systematically reduce waste in manufacturing.
The 7 types of manufacturing waste
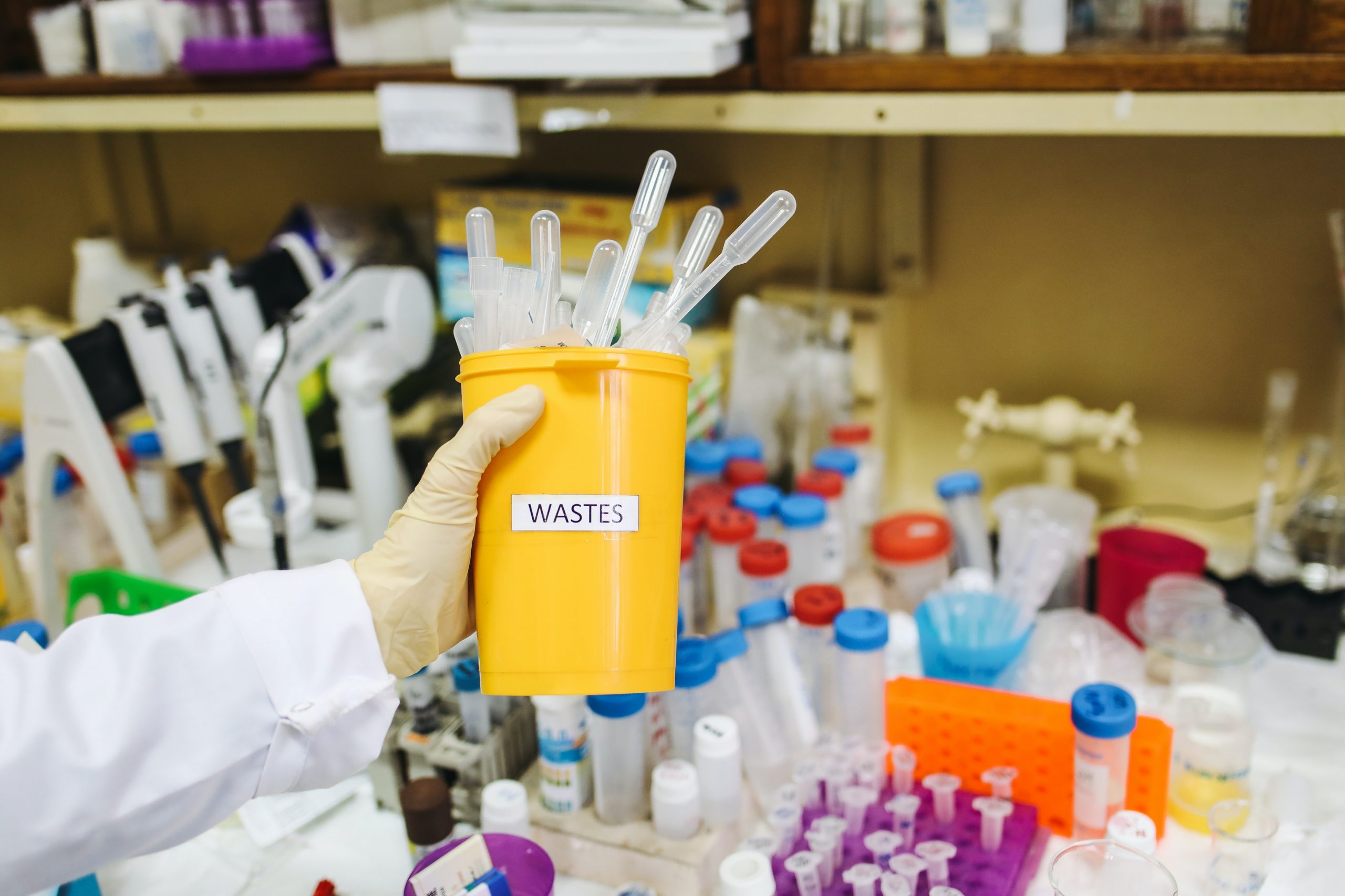
Knowing and identifying the type of waste your manufacturing workflows create helps you to tackle it better.
Lean principles categorize the different types of lean manufacturing waste in the following way:
- Overproduction — Producing more than what is needed, simply to store it
- Waiting — Idle machines and technicians, bottlenecks in your production
- Transport — Moving parts and products multiple times
- Processing — Performing unnecessary processing steps in the production of your products
- Inventory — Overstocking supplies leads to manufacturing overheads in storage and inventory management
- Motion — Inefficient workflows leading to unnecessary movement of people, machinery, or equipment
- Correction — Producing defective products or employing a process that produces a lot of scraps
Unrealized potential is often considered the eighth type of waste in lean manufacturing. Underutilizing the skills of your workforce is probably the most important and, at the same time, the most challenging form of waste to minimize.
How to reduce waste and boost manufacturing productivity?
With the above classification, you can understand the kind of waste you generate the most, regardless of your industry.
Of course, the specifics differ from industry to industry. For instance, material waste can come from your perishable inventory expiring in the food manufacturing business. Whereas in textile and metal manufacturing, waste comes from scraps. However, mapping out your waste streams and classifying the type of waste you generate is the first step.
Once you have that clear, you can move on to the various things you can do to reduce waste.
9 Tips to reduce waste in manufacturing
Regardless of the sector, here are nine tips that outline how to reduce waste in lean manufacturing.
1. Set a waste management goal
Once you have defined and understood the waste you generate, your next step should be to set a waste management goal and commit to it. Don’t worry — it will not be a waste of time.
Setting a goal can help you and your team to stay on track and assess how well your company is cutting excess waste. For instance, you could set a goal of reducing waste by 25% in the upcoming quarter. Developing a plan allows you to quantify the progress that you are making toward the goal.
This step also involves getting your entire company on board with the goal and contributing enthusiastically.
Can you strive for perfection in reducing waste?
Let’s use the above example, setting a goal of reducing 25% more waste every quarter. At the end of the year, your company will produce close to 70% less waste.
If only life was that simple. Certainly, you can aim to remove every wasteful thing from your production lines. Unfortunately, it’s impossible — instead, the goal is to perfect your business value continuously.
2. Minimize overstocking and overproduction
The overheads that come from overstocking and overproduction can lead to a significant waste of resources.
An effective way to combat this is by establishing a pull-based system so you only manufacture products when needed in a just-in-time fashion. Such a production system lets you focus on making your workflows more efficient.
3. Stay on top of your inventory
Eliminating excess stock can be a challenging goal to achieve.
Your workflows might often require you to maintain certain levels of stock. In such cases, you need total inventory control. A batch of expired products can throw off your entire production schedule and delay your orders.
An effective inventory tracking system can ensure you use your products well before they go bad.
4. Set up a preventive maintenance schedule
Machines that break down in the middle of production add unnecessary delays in your manufacturing process and additional operating expenses in the form of repairs.
As they say, prevention is better than cure. So, a preventive maintenance schedule that allows you to perform regular maintenance activities can prevent the unexpected breakdown of your machinery — ensuring that your production process continues uninterrupted.
5. Optimize your shop floor
Imagine your shop floor staff not knowing about the modifications requested by the customer.
In the worst case, this could mean that the product ends up in the trash, and you have to make a new one all over again. A paper-based communication system could lead to mistakes and waste like these. Or imagine a technician having to walk around the shop floor looking for a specific tool to complete a job.
This delays order fulfillment and frustrates your workforce, leading to higher attrition rates.
Having effective and fast communication on the shop floor can unlock value and prevent waste.
6. Reduce packaging
Revisiting how you pack and ship your products could lead you to reduce waste significantly as well. After all, plastic is for life, and reducing its use, can greatly benefit your business and the environment.
For example, Apple decided to ship only a cable but not the adapter with its iPhones, starting with the iPhone 12. This allowed it to pack the new iPhones in smaller boxes. This controversial move reduced packaging waste significantly and reportedly increased Apple’s profits by a whopping $6.5 billion.
This shows that at large volumes, even small changes could lead to immense gains in terms of profit and sustainability. So, to wrap it up, simple tweaks like switching to recyclable materials or reducing packaging can go a long way.
7. Perform a professional waste audit
A waste audit allows you to analyze your waste streams and find different ways to reduce waste.
Although you can do it yourself, an external audit can set you on a path toward obtaining green certification. So, hiring a professional waste auditing firm might be a worthwhile investment to get the certificate.
8. Invest in processes that can bring about a circular economy
There is a growing movement toward designing eco-friendly products and processes with a large focus on reuse, repair, refurbishing, and recycling. This ensures that your products have a long lifecycle, at the end of which they can be repurposed — preventing them from ending up in a landfill.
You could aim high and invest in production processes that produce zero waste and promote this idea of a circular economy.
9. Get creative
Some byproducts of your manufacturing process that you might deem a waste are probably still valuable. There could be an opportunity to repurpose waste — let’s look at an example.
The dairy and cheese industry used to consider whey to be a waste product up until the 1950s. Often large dairy processing plants would pay to dispose of the excess whey. Then came whey protein, the boom of weight-lifting as a sport, and large-scale market adoption. So, what was earlier considered a waste product is now the raw material for a multi-billion dollar protein supplement industry.
Waste during holidays
While considering the nine items in our list above, you also need to take into account the moments in the year when your business is most at risk of higher wastage — the holidays. These are the significant sale events where you’ll see rapidly increasing orders and sky-high demand for faster service at a lower price. If you’ve got your waste management in order, you’ll be off to a good start, but if you’re not well-prepared, the sales might hurt your bottom line instead of helping it.
Let’s look at the different phases of the year when the holidays come along.
Early year holidays
Beyond potential New Year sales, Valentine’s Day, and days related to your parents, there aren’t many big banner sale moments in the first part of the year. For some businesses, these won’t even make a dent in day-to-day life, but if you’re making greeting cards or novelty gifts, they’re big moments.
Make sure you have waste goals set, and look at trends from previous years to help predict your requirements for stock and production so you don’t overdo it, but you’re not hit by a dreaded stockout either.
Black Friday
It comes a month before perhaps the biggest shopping event of the year, but Black Friday is starting to give Christmas a run for its money. With huge sales across nearly every industry, Black Friday is event shoppers anticipate. It’s an event when items hit a great price, and people are ready to yell, “Shut up and take my money!” But for manufacturers, Black Friday is a significant waste risk.
If you’re not fully prepared for Black Friday, it can be a chaotic and hectic time of year.
You might look to produce enough stock to meet demand and accidentally overshoot this. Or perhaps worse, undershoot and be frantically reordering to fulfill awaiting orders. Either way, you’re in a mess. This is where we return to forecasting demand and optimizing your shop floor to meet orders quickly.
It’s crucial to make a surplus of popular products before Black Friday but not to go overboard so you’re left holding stock that may never sell.
And a final consideration, which could bring an advantage, is the proximity to Christmas. A month after Black Friday, you can still sell some of that excess stock. You can also use kitting to create attractive holiday gift boxes, or further reductions could help clean your storage space and reduce inventory to a normal level.
Manufacturing waste statistics
- In the EU, an average of 4.8 tonnes of waste were generated per inhabitant in 2020
- 39.2% of waste was recycled in the EU in 2020
- An average dump is made up of approximately one-third of packaging material
- In the US, only 1% of plastic and aluminum products are recycled
Christmas
Christmas is arguably the most significant annual holiday we have globally. Planning for Christmas should start months in advance, and with smart waste planning, you can make it smooth for you and your business. It’s a moment when it’s almost a necessity for people to buy, and meeting people at the right price can see products soar off the shelves.
Perhaps it’s worth planning your waste audit for early January to reflect on your holiday performance and prepare well for the year ahead. And make sure when Christmas comes around, you aren’t wasting precious time on waste that should be for meaningful work and wonderful family time.
Want to see Katana in action?
Book a demo to get all your questions answered regarding Katana’s features, integrations, pricing, and more.
How to use lean inventory management software to reduce waste
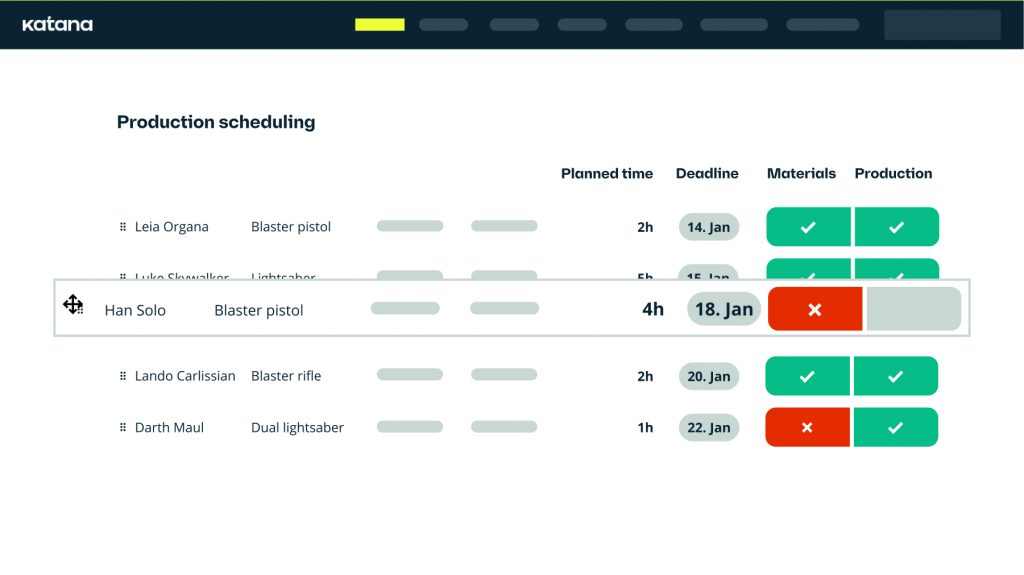
One way to ensure you’re business runs as efficiently as possible and keeps waste minimal is by implementing manufacturing software.
Katana’s manufacturing ERP software offers all the features needed for end-to-end traceability, including purchase order management, batch tracking, and expiry date tracking to help you streamline your inventory management.
With Katana, you also get forecasting and production planning capabilities which are highly effective in reducing waste from excess inventory. And Katana’s Shop Floor App lets you add notes to manufacturing orders and track time spent on tasks to optimize the shop floor processes.
Sign up now to get a demo and find out how thousands of manufacturers use Katana to optimize their business operations and minimize waste.
Table of contents
Manufacturing guide
More on manufacturing
Get visibility over your sales and stock
Wave goodbye to uncertainty by using Katana Cloud Inventory for total inventory control
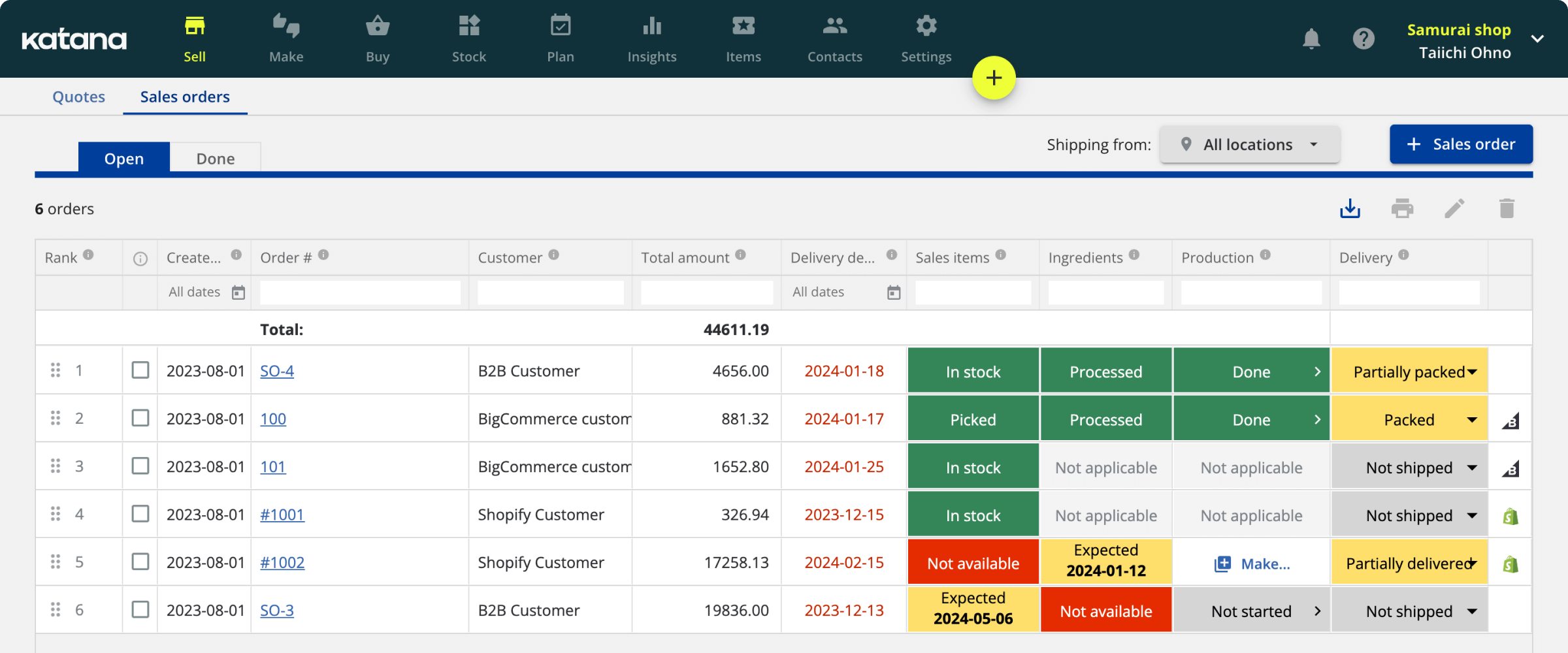